Concrete
Boosting Productivity
Published
1 year agoon
By
admin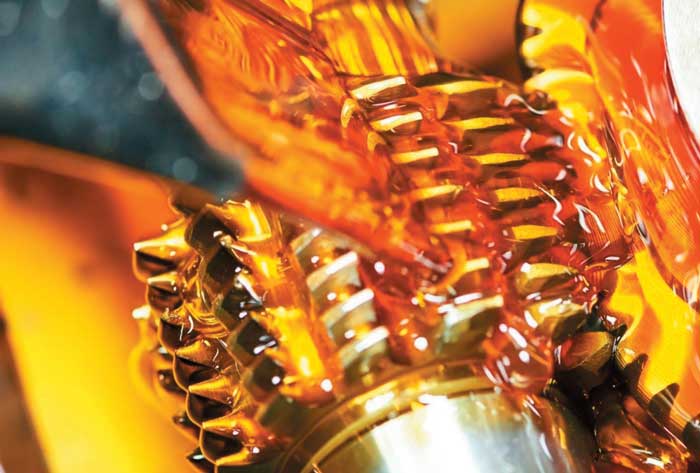
ICR delves into how advanced industrial lubricants are changing the game for the cement sector by enhancing the performance and longevity of heavy machinery and improving the productivity of cement plants.
Lubricants play a pivotal role in the cement industry, ensuring the smooth and efficient operation of machinery involved in the production process. Cement manufacturing is a rigorous process that involves heavy machinery operating under extreme conditions such as high temperatures, heavy loads, and dusty environments. Effective lubrication is critical to maintain the functionality and longevity of this equipment.
Fortune Business Insights states that the global industrial lubricants market was valued at US$ 71.55 billion in 2023 and is projected to be worth US$ 74.05 billion in 2024 and reach US$ 96.93 billion by 2032, exhibiting a CAGR of 3.3 per cent during the forecast period. Lubricants that are used for industrial applications are considered industrial lubricants.
According to Custom Marketing Insights, India Industrial Lubricants Market is valued at US$ 13,045 million in 2024 and is expected to reach US$ 20,715 million by 2033, at a CAGR of 4.12 per cent during the forecast period 2024- 2033.
One of the primary functions of lubricants in the cement industry is to reduce friction between moving parts. This reduction in friction minimises wear and tear, thus extending the lifespan of machinery and reducing the frequency and cost of repairs. Lubricants also help in dissipating heat generated by friction, which is crucial for preventing overheating and potential damage to equipment.
In addition to reducing friction and heat, lubricants provide a protective barrier against contaminants such as dust and moisture. This protection is essential in the cement industry, where the dusty environment can lead to abrasive wear and corrosion if machinery is not adequately lubricated.
Proper lubrication also enhances the efficiency of machinery. Well-lubricated equipment operates more smoothly, leading to improved performance and reduced energy consumption. This efficiency not only lowers operational costs but also contributes to the overall productivity of the cement plant.
“We evaluate the cost-effectiveness of different lubricants through a comprehensive analysis. Factors considered include performance metrics, longevity, environmental impact, and overall operational efficiency. Our purchasing decisions prioritise value without compromising on quality or sustainability. Our goal is to strike a balance between cost-effectiveness and performance excellence,” says Amit Mehta, Vice President – Operations, Wonder Cement.
Moreover, advancements in lubricant technology have led to the development of specialised lubricants designed to meet the specific needs of the cement industry. These include high-temperature lubricants, synthetic oils, and environmentally friendly options that offer superior performance and sustainability benefits.
Types of lubricants
Gear oils: They are essential in the cement industry for lubricating the gears found in heavy machinery such as crushers, mills, and kilns. These oils are formulated to withstand high pressures and loads, ensuring smooth and efficient gear operation. They often contain additives to enhance performance under extreme conditions, reducing friction and wear, and providing a protective film that extends the life of gear components.
Hydraulic oils: These are used in the hydraulic systems of cement plants, which power equipment such as conveyors, crushers, and kiln drives. These oils are designed to provide efficient power transfer, corrosion protection, and optimal viscosity under varying temperatures. High-quality hydraulic oils help in minimising wear and tear on system components, reducing the risk of system failures and downtime.
Grease: It is widely used for lubrication in the cement industry due to its ability to stay in place and provide long-lasting protection. It is particularly useful in applications where liquid lubricants might not be retained, such as bearings, seals and gears. Grease is formulated to withstand extreme temperatures, heavy loads and environmental contaminants, making it ideal for the harsh conditions in cement manufacturing.
Specialty lubricants: They include a range of products designed for specific high-performance applications within the cement industry. These can include high-temperature lubricants for kiln operations, synthetic lubricants that offer superior stability and protection, and bio-based lubricants that provide environmentally friendly alternatives. Specialty lubricants are tailored to meet the unique challenges of different processes, ensuring optimal machinery performance and longevity.
Synthetic lubricants: They are engineered to provide enhanced performance over traditional mineral oils. They offer superior thermal stability, oxidation resistance, and protection against wear, making them suitable for the demanding environments of cement manufacturing. Synthetic lubricants are often used in critical applications where equipment reliability and efficiency are paramount, such as in gearboxes, compressors and high-temperature areas.
Each type of lubricant plays a crucial role in ensuring the seamless operation and maintenance of machinery within the cement industry. By selecting the appropriate lubricant for each application, cement plants can achieve greater efficiency, reduced downtime, and extended equipment life.
Lubrication technology and management system
Lubrication technology has advanced significantly, providing the cement industry with sophisticated solutions to enhance equipment performance and longevity. Modern lubricants are formulated with high-quality base oils and advanced additives that improve their ability to reduce friction, dissipate heat, and protect against wear and corrosion. Innovations such as synthetic lubricants offer superior stability and performance under extreme conditions, while bio-based lubricants present environmentally friendly alternatives. Additionally, high-performance additives enhance lubricant capabilities, ensuring optimal operation of machinery under heavy loads and high temperatures typical in cement manufacturing.
A lubrication management system is crucial for ensuring the efficient use of lubricants and the optimal performance of machinery. This system involves regular monitoring and analysis of lubricant conditions, scheduled maintenance, and the strategic application of lubricants to critical components. By implementing a robust lubrication management system, cement plants can predict and prevent equipment failures, reduce downtime, and extend the lifespan of machinery. Advanced systems may include automated lubrication systems that deliver precise amounts of lubricant at controlled intervals, minimising human error and ensuring consistent lubrication.
KB Mathur, Founder and Director, Global Technical Services, says, “A basic requirement is to maintain quality of lubricants and greases manufactured by standard and reputed oil companies. The specification of the oil is therefore to be maintained and oil to be kept in clean condition to avoid any contamination with dust, dirt or moisture. This contamination has to be kept under control for good mechanical maintenance. Any breakdown in cement plant operation is very costly, affecting production.”
“Therefore, it is essential for cement plants to invest in good lubrication practices by having dedicated manpower, doing lubrication, keeping oil clean by use of filtration machines, oil testing laboratory at site, to ensure quality of oil as per specifications and take corrective action, when required,” he adds.
Effective maintenance practices are integral to successful lubrication management in the cement industry. These practices include routine inspections, timely lubrication, and the use of proper techniques and tools. Maintenance staff should be trained to recognise signs of lubricant degradation and machinery wear, and to understand the specific lubrication requirements of different equipment. Predictive maintenance, facilitated by condition monitoring technologies, allows for the early detection of potential issues, enabling preemptive actions to avoid unplanned outages. Regular oil analysis and lubrication audits help in assessing the effectiveness of the lubrication programme and making necessary adjustments to improve performance and reliability.
Together, advanced lubrication technology, a comprehensive lubrication management system, and diligent maintenance practices form the backbone of efficient and reliable operations in the cement industry, leading to enhanced productivity and reduced operational costs.
High performance additives
High-performance additives are essential components in modern lubricants, enhancing their functionality and effectiveness in demanding applications such as those found in the cement industry. These additives are chemical compounds formulated to improve various properties of the base oil, allowing the lubricants to meet specific performance requirements and extend the operational lifespan of machinery.
Lisa Marston, Regional Technical Service Engineer, Cortec Corporation, says, “Cortec has products that serve various needs in lubricating systems. One major category of products is oil additives with contact and vapour phase corrosion inhibitors that are designed to provide enhanced corrosion protection in addition to the lubricating oil itself during long term storage and intermittent operating conditions for gearboxes, steam turbines, pumps, etc. Cortec also offers greases that are formulated with vapour phase corrosion inhibitors, some of which are derived from renewable resources. Additionally, Cortec manufactures general purpose lubricants with corrosion inhibitors that can be used on valve bushings, fasteners, and packing glands, as a few examples. The addition of contact and vapour phase corrosion inhibitors in these products ensures consistent corrosion protection throughout the equipment, even when components may not be in direct contact with the lubricant.”
- Anti-wear additives: These additives form a protective film on metal surfaces, reducing friction and preventing wear and tear under high-pressure conditions. This is crucial in extending the life of gears and bearings in cement machinery.
- Extreme pressure (EP) additives: EP additives are designed to provide additional protection under extreme load conditions. They react with metal surfaces to create a protective layer that prevents welding and scoring of metal parts, ensuring smooth operation in heavy-duty equipment.
- Anti-oxidants: These additives prevent the oxidation of the lubricant, which can lead to the formation of sludge and varnish. By inhibiting oxidation, antioxidants help maintain the lubricant’s viscosity and performance over extended periods, even in high-temperature environments.
- Corrosion inhibitors: Corrosion inhibitors protect metal surfaces from rust and corrosion caused by exposure to moisture and other corrosive agents. This is particularly important in the cement industry, where machinery is often exposed to harsh environmental conditions.
- Detergents and dispersants: These additives keep engines and machinery clean by preventing the formation of deposits and sludge. Detergents neutralise acids formed during the combustion process, while dispersants keep particles suspended in the lubricant, preventing them from clumping together and causing blockages.
- Viscosity index improvers: These additives help the lubricant maintain its viscosity across a wide temperature range. This ensures that the lubricant performs effectively in both high and low temperatures, providing consistent protection and performance.
By incorporating these high-performance additives, lubricants can deliver enhanced protection, efficiency and durability. In the cement industry, where equipment operates under extreme conditions, the use of such advanced lubricants is critical for maintaining operational efficiency, reducing downtime and prolonging the lifespan of expensive machinery.
Sustainability and lubrication
Sustainability has become a critical focus in the cement industry, including the realm of lubrication. Sustainable lubrication practices involve using high-performance, environmentally friendly lubricants, optimising lubricant usage, and ensuring proper disposal and recycling of used lubricants. These practices help minimise environmental impact, improve energy efficiency and reduce waste, aligning with global sustainability goals.
Proper disposal and recycling of used lubricants are essential for minimising environmental pollution and conserving resources. The cement industry, with its substantial lubricant usage, must implement robust procedures for handling used lubricants.
Used lubricants can contain harmful contaminants that pose environmental risks if not disposed of correctly. Cement plants should follow stringent regulations and guidelines for the safe disposal of used lubricants. This typically involves collecting the used lubricants in designated containers and ensuring they are handled by licensed waste management companies that specialise in hazardous waste disposal. These companies treat the used lubricants to neutralise harmful substances before safe disposal, preventing soil and water contamination.
Recycling used lubricants is an effective way to reduce environmental impact and promote sustainability. The recycling process involves collecting used lubricants and subjecting them to re-refining, which removes impurities and restores the lubricants to a usable state. Re-refined lubricants can perform comparably to new lubricants, making them a viable option for reuse in various applications.
The cement industry can contribute to lubricant recycling efforts by partnering with certified recycling facilities. These facilities use advanced technologies to clean and purify used lubricants, converting them into high-quality products that can re-enter the market. This not only reduces the demand for virgin lubricant production but also minimises waste and conserves natural resources.
Incorporating sustainable lubrication practices, including the proper disposal and recycling of used lubricants, helps the cement industry reduce its environmental footprint, enhance operational efficiency, and align with broader sustainability initiatives. By doing so, the industry can contribute to a healthier environment and more sustainable future.
Conclusion
Effective lubrication is essential for the cement industry, ensuring the efficient and reliable operation of machinery under demanding conditions. The use of advanced lubrication technology, including high-performance synthetic and bio-based lubricants, significantly enhances equipment performance and longevity. Implementing a comprehensive lubrication management system, coupled with effective maintenance practices, allows cement plants to minimise downtime, reduce operational costs and extend the lifespan of their machinery.
Sustainability is also a key consideration in lubrication practices. The proper disposal and recycling of used lubricants are crucial for minimising environmental impact and conserving resources.
By following stringent regulations and partnering with certified recycling facilities, the cement industry can effectively manage waste and promote a circular economy. These efforts contribute to a reduced environmental footprint, aligning with global sustainability goals and fostering a healthier environment.
In conclusion, embracing advanced lubrication technology, robust management systems, and sustainable practices not only improves the operational efficiency of cement plants but also supports their commitment to environmental responsibility. By prioritising these aspects, the cement industry can achieve greater productivity and sustainability, paving the way for a more efficient and eco-friendly future.
– Kanika Mathur
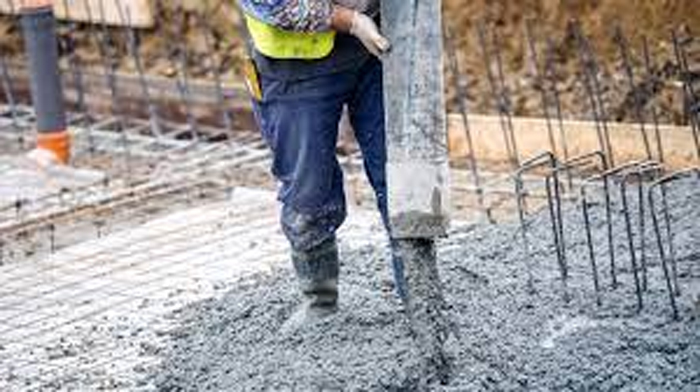
Tamil Nadu is set to host one of India’s five national carbon capture and utilisation (CCU) testbeds, aimed at reducing CO2 emissions in the cement industry as part of the country’s 2070 net-zero goal, as per a news report. The facility will be based at UltraTech Cement’s Reddipalayam plant in Ariyalur, supported by IIT Madras and BITS Pilani. Backed by the Department of Science and Technology (DST), the project will pilot an oxygen-enriched kiln capable of capturing up to two tonnes of CO2 per day for conversion into concrete products. Additional testbeds are planned in Rajasthan, Odisha, and Andhra Pradesh, involving companies like JK Cement and Dalmia Cement. Union Minister Jitendra Singh confirmed that funding approvals are underway, with full implementation expected in 2025.
Image source:https://www.heavyequipmentguide.ca/
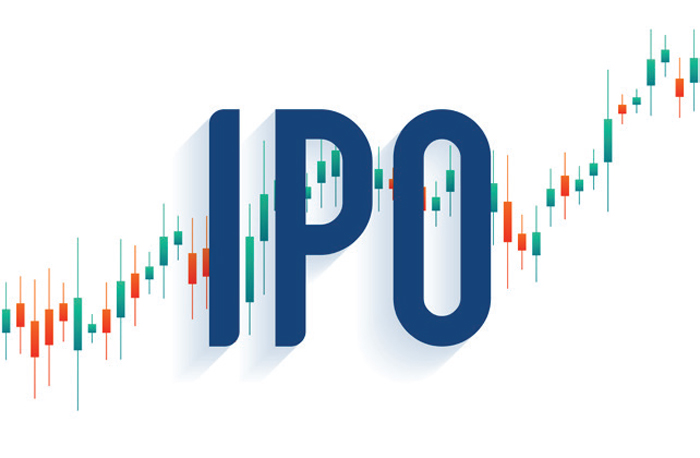
JSW Cement has set the price range for its upcoming initial public offering(IPO) at US$1.58 to US$1.67 per share, aiming to raise approximately US$409 million. As reported in the news, around US$91 million from the proceeds will be directed towards partially financing a new integrated cement plant in Nagaur, Rajasthan. Additionally, the company plans to utilise US$59.2 million to repay or prepay existing debts. The remaining capital will be allocated for general corporate purposes.
Concrete
Cement industry to gain from new infrastructure spending
Published
1 month agoon
July 24, 2025By
admin
As per a news report, Karan Adani, ACC Chair, has said that he expects the cement industry to benefit from the an anticipated US$2.2tn in new public infrastructure spending between 2025 and 2030. In a statement he said that ACC has crossed the 100Mt/yr cement capacity milestone in April 2025, propelling the company to get closer to its ambitious 140Mt/yr target by the 2028 financial year. The company’s capacity corresponds to 15 per cent of an all-India installed capacity of 686Mt/yr.
Image source:https://cementplantsupplier.com/cement-manufacturing/emerging-trends-in-cement-manufacturing-technology/