Concrete
Charting a Cleaner Future
Published
2 years agoon
By
admin
The Indian cement industry’s commitment to carbon neutrality with the use of carbon capture, utilisation and storage (CCUS) technology is commendable. But it still has ‘miles to go’ before it achieves its sustainability goals. ICR looks at the various aspects of CCUS, and the challenges and opportunities it presents to the cement sector.
In an era where the imperative to combat climate change has become increasingly urgent, the cement industry finds itself at the crossroads of innovation and environmental responsibility. At the heart of this transformative journey lies Carbon Capture, Utilisation, and Storage (CCUS), a suite of technologies designed to intercept carbon dioxide emissions at their source, repurpose them for various applications, and securely store them away from the atmosphere. This paradigm shift in industrial practices is not merely a technological evolution; it represents a conscientious commitment to mitigating the environmental footprint of one of the most significant contributors to global greenhouse gas emissions.
Defining the trifecta of Carbon Capture, Utilisation, and Storage involves a nuanced understanding of each element›s role in reshaping the landscape of industrial sustainability. Carbon capture technologies strive to intercept and capture CO2 emissions at their genesis, preventing their release into the atmosphere. Utilisation ventures beyond mere containment, exploring innovative ways to repurpose captured carbon for constructive applications, fostering a circular economy. Meanwhile, the storage component addresses the crucial need to safely sequester captured carbon, ensuring it remains dormant and harmless.
Dr Paula Carey, Co-Founder & Chief Scientific Officer, Carbon8 says, “The amount of Carbon Dioxide that is captured is limited by the amount of residue available, but the economics of our system means that a profit can be made for every tonne of CO2 captured without the need for subsidies, or large energy penalties or the use of expensive toxic chemicals such as amines. The process results in the sustainable management of an industrial residue that might otherwise be destined for landfill and produces a low carbon product for the construction industry reducing the need for the extraction of natural aggregate.”
The significance of CCUS in addressing climate change cannot be overstated. With the cement industry being a notable contributor to carbon emissions globally, the adoption of CCUS stands as a pivotal step towards achieving climate goals. According to Delhi-based think tank Centre for Science and Environment’s Decarbonising India: Cement sector report, CCUS could be one of the recommended pathways for reducing emissions in the Indian cement sector in the long run but not by 2030, especially after witnessing the slow progress on CCUS in the Indian cement sector.
CCUS TECHNOLOGIES
As the global imperative to combat climate change continues to gain momentum, industries are turning their focus towards innovative solutions to reduce carbon emissions. The cement sector, known for its significant environmental footprint, stands poised for a revolutionary transformation through the adoption of Carbon Capture, Utilisation, and Storage (CCUS) technologies. In this segment, we delve into the intricate realm of CCUS technologies, presenting an insightful overview of the diverse approaches aimed at capturing and managing carbon emissions at cement plants.
According to the Annual Global Climate Report 2023 by National Centers for Environmental Information, the year 2023 was the warmest year since global records began in 1850 at 1.18°C (2.12°F) above the 20th century average of 13.9°C (57.0°F). This value is 0.15°C (0.27°F) more than the previous record set in 2016. The 10 warmest years in the 174-year record have all occurred during the last decade (2014–2023). Of note, the year 2005, which was the first year to set a new global temperature record in the 21st century, is now the 12th-warmest year on record. The year 2010, which had surpassed 2005 at the time, now ranks as the 11th-warmest year on record.
The landscape of carbon capture technologies is a dynamic tapestry of innovation, with various methods vying for prominence in the quest for sustainability. From post-combustion capture, where CO2 is extracted from flue gasses after the combustion process, to pre-combustion capture, which intervenes in the fuel conversion stage, and oxy-fuel combustion, where fossil fuels are burned in oxygen-rich environments—each approach brings its unique set of advantages and challenges. This article endeavors to unravel this technological tapestry, providing a comprehensive understanding of the strengths and limitations inherent in different carbon capture methodologies, and their applicability to the intricacies of cement production.
According to Max Tschurtschenthaler: Global Business Unit Manager, Cement, Process Industries, ABB and Joonas Rauramo: CEO, Coolbrook, “There are huge costs associated with decarbonising the cement industry. According to the Council on Energy, Environment and Water (CEEW), given that the cumulative CO2 emissions from manufacturing 337 Mt of cement were estimated to be around 218 Mt in 2018-19, India will need approximately $334 billion in capital expenses and another $3 billion in annual operating costs to decarbonise the existing cement production in the country.”
As a result, the IEA has called for dedicated efforts to reduce carbon emissions in the cement industry, which could include the reduction of clinkerto- cement ratio (including through greater uptake of blended cement) as well as adopting pathbreaking technologies such as electric kilns, carbon capture, utilisation and storage (CCUS) and clinkers made from alternative raw materials” they add.
The adoption of CCUS in cement plants represents a critical juncture in the industry›s evolution towards sustainability. Cement production, notorious for its substantial carbon emissions, now stands on the precipice of change, with CCUS offering a lifeline to curb its environmental impact. By exploring the current landscape of CCUS adoption in cement plants, this article seeks to showcase the tangible efforts and strides made by the industry towards aligning with global climate objectives. From pilot projects to large-scale implementations, the cement sector is poised to redefine its narrative, proving that responsible production practices and environmental stewardship can indeed go hand in hand.
CHALLENGES IN CCUS
As the sector grapples with the imperative to reduce its carbon footprint, a host of technical hurdles loom on the path to seamless integration of CCUS technologies. From the complexities of retrofitting existing cement plants to the energy-intensive nature of certain capture processes, the technical challenges inherent in this paradigm shift require a meticulous examination. This segment aims to dissect the nuanced obstacles that confront the cement industry on its quest for sustainable practices, offering a glimpse into the labyrinth of hurdles that must be navigated to embrace CCUS wholeheartedly.
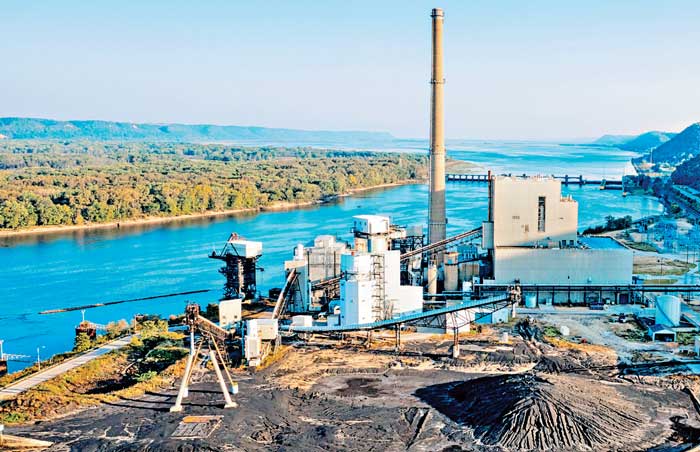
However, the landscape is not one solely marked by impediments; it is equally defined by the spirit of innovation and the relentless pursuit of solutions. As the cement industry strives to overcome the technical challenges posed by the adoption of CCUS, a wave of innovative solutions and technological advancements is sweeping through the sector. From breakthroughs in capture efficiency to the development of more costeffective storage methods, this article sheds light on the cutting-edge developments that promise to revolutionise the way cement plants approach carbon management. The symbiosis of challenges and solutions forms the crucible in which the future of sustainable cement production is forged, showcasing the industry›s resilience and determination to surmount obstacles on its journey toward a greener tomorrow.
According to the report An affordable, reliable, competitive path to net zero by McKinsey & Company, the net-zero transition and economic empowerment are urgent and simultaneous goals. But there are several ways that the net-zero transitions, if not executed well, could make energy, materials, and other products less affordable than traditional alternatives. Even though wind and solar generate electricity more cheaply than fossil fuels do, they will require additional spending as their share in the overall generation mix rises—for storage; other “firming capacity,” which is electricity that can be used at times when solar and wind are not providing enough energy; and grid infrastructure.
If the costs of technologies, such as batteries, do not decline as expected, or if grids are not designed thoughtfully, the delivered cost of electricity could rise. For materials, decarbonising the production of steel, aluminum, and cement could increase production costs by 15 per cent or more by 2050. If costs of energy and other products were to rise, economic growth could suffer, posing a particular problem for developing countries. And as we mentioned above, the scale of spending needed for the transition could stretch public finances.
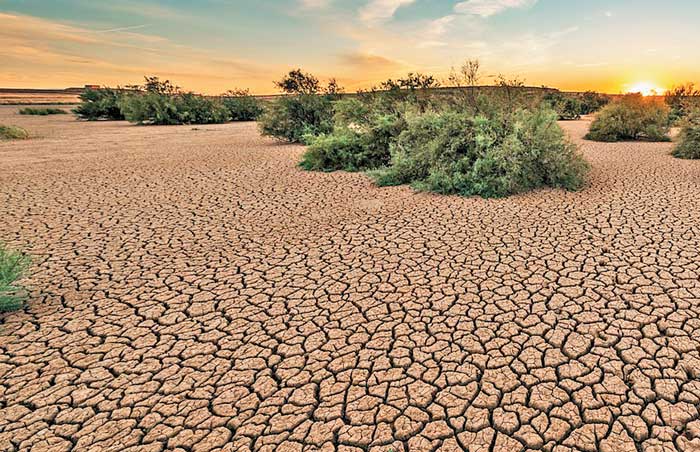
ECONOMIC VIABILITY
As the global community intensifies its focus on environmental sustainability, the cement industry finds itself at a pivotal juncture, where economic viability converges with ecological responsibility through the lens of Carbon Capture, Utilisation, and Storage (CCUS). Central to this paradigm shift is a meticulous examination of the economic landscape, exploring the cost implications of integrating CCUS into the intricate tapestry of cement production. This segment delves into a comprehensive cost analysis, deciphering the financial intricacies that cement manufacturers must navigate on their journey towards a more sustainable and carbon-conscious future.
Implementing CCUS in cement production is not merely a technological endeavor; it is an economic calculus that demands scrutiny. From the capital investments required for retrofitting existing facilities to the operational costs associated with capturing, utilising, and storing carbon emissions, a nuanced understanding of the economic implications is essential. This article aims to unravel the complexities, providing insights into the direct and indirect costs that shape the economic viability of CCUS adoption in the cement industry.
Amidst these financial considerations, the landscape is punctuated by a beacon of support in the form of financial incentives and government backing. Recognising the pivotal role that industries play in achieving climate goals, governments worldwide are championing initiatives to encourage CCUS adoption. From tax incentives to grants and subsidies, this article explores the various avenues of financial support that cement manufacturers can leverage, underscoring the collaborative effort required between private enterprises and governments to make sustainable practices not only environmentally sound but economically feasible. The convergence of economic viability and environmental stewardship is a narrative that unfolds in the realm of CCUS, illustrating the profound impact of responsible industry practices on the global stage.
ENVIRONMENTAL IMPACT
In the ever-evolving discourse on environmental conservation, the cement industry finds itself at the forefront of a transformative narrative, catalysed by the integration of Carbon Capture, Utilisation, and Storage (CCUS) technologies. Central to this narrative is a profound examination of the environmental impact, where the echoes of reduced carbon emissions reverberate through the concrete jungles of manufacturing. This segment embarks on a journey into the heart of sustainability, exploring the tangible reductions in carbon emissions achieved through the implementation of CCUS in cement production. As the cement industry grapples with its status as a significant contributor to global carbon emissions, the promise of substantial reductions becomes a beacon of hope in the fight against climate change. CCUS not only intercepts carbon emissions at their source but actively seeks to mitigate their release into the atmosphere. This article unfolds the environmental benefits, presenting a comparative analysis that illuminates the stark contrast between conventional cement production and the greener landscape sculpted by CCUS. From decreased atmospheric pollution to a measurable reduction in the industry’s overall carbon footprint, the environmental impact of CCUS stands as a testament to its potential as a transformative force in achieving sustainable manufacturing practices.
Within this exploration lies a broader question: What if the cement industry were to continue its trajectory without the integration of CCUS? The comparison draws a vivid contrast between a future marked by unrestrained carbon emissions and the alternative reality of a more sustainable industry, embracing CCUS as a cornerstone of its environmental responsibility. Through this lens, the environmental impact of CCUS emerges not merely as a reduction in numbers but as a profound shift towards a future where industry and ecology coexist harmoniously, proving that the pursuit of progress need not come at the cost of our planet›s well-being.
CARBON UTILISATION
In the dynamic landscape of Carbon Capture, Utilisation, and Storage (CCUS), the spotlight extends beyond the mere interception and storage of carbon emissions. It converges upon the transformative concept of Carbon Utilisation, an innovative frontier where captured carbon becomes a valuable resource rather than a mere byproduct. This segment embarks on an exploration into the realm of possibilities, unraveling the myriad ways in which captured carbon can be harnessed to not only enhance sustainability in cement production but also create tangible value across diverse industries.
Traditionally viewed as an environmental challenge, carbon emissions are now being reimagined as a resource with the potential for multifaceted applications. Within the confines of cement production, the concept of carbon utilisation extends beyond containment, exploring how captured carbon can be integrated into the very fabric of manufacturing processes. This article delves into the intricacies of utilising captured carbon within cement production, examining how it can enhance the efficiency and reduce the environmental impact of this critical industry.
Moreover, the canvas of carbon utilisation extends beyond the boundaries of cement plants, presenting a myriad of opportunities to create value in other industries. From the production of synthetic fuels to the development of innovative building materials, the captured carbon becomes a versatile asset with the potential to revolutionise various sectors. This exploration not only unveils the technical possibilities but also underscores the economic incentives for industries to actively participate in the carbon utilisation revolution. The integration of carbon utilisation within the CCUS framework transcends the narrative of mitigation; it becomes a testament to the transformative power of innovation, where environmental responsibility converges with economic opportunity to redefine the landscape of sustainable industry practices.
STORAGE OPTIONS
As the cement industry endeavors to mitigate its carbon footprint through the adoption of Carbon Capture, Utilisation, and Storage (CCUS), the spotlight turns towards the crucial facet of carbon storage—a process that extends beyond mere capture and demands a thoughtful consideration of methods, sites, and safety protocols. This segment delves into the nuanced realm of storage options, unveiling the diverse methods employed to securely sequester captured carbon and emphasising the paramount importance of site evaluation and safety considerations in ensuring the success of CCUS initiatives.
The myriad methods of carbon storage present a mosaic of possibilities, ranging from geological storage in depleted oil and gas reservoirs or deep saline formations to enhanced oil recovery where captured carbon is injected to extract additional hydrocarbons. This article embarks on an exploration of these storage options, dissecting their unique strengths, limitations, and the factors that influence their applicability in the context of the cement industry. Each method represents a piece of the puzzle in the broader CCUS framework, contributing to the collective effort to safely and effectively manage the carbon emissions intercepted at their source.
Amidst the technical intricacies of storage methods, the critical importance of site evaluation and safety considerations emerges as a paramount concern. Identifying suitable storage sites involves a comprehensive assessment of geological, hydrological, and environmental factors to ensure the long-term stability and containment of captured carbon. Safety considerations, both in terms of the integrity of storage structures and the potential environmental impact, become the linchpin of successful CCUS implementation. This article navigates through the intricacies of site selection and safety protocols, underscoring the industry’s commitment to not only mitigating carbon emissions but doing so with the utmost responsibility and adherence to rigorous safety standards. In the dynamic landscape of CCUS, carbon storage becomes the silent guardian, ensuring that captured emissions find a secure and sustainable sanctuary beneath the Earth›s surface.
CONCLUSION
In the evolution towards a sustainable future, the integration of Carbon Capture, Utilisation, and Storage (CCUS) in the cement industry marks a transformative paradigm shift. Through overcoming technical challenges, navigating economic considerations, and prioritising environmental impact, the industry demonstrates a commitment to responsible innovation. The reduction in carbon emissions and the repurposing of captured carbon showcase the tangible benefits of this shift. With a focus on secure storage solutions and safety considerations, the cement industry is not just mitigating its environmental impact but actively shaping a narrative of resilience and progress. As CCUS becomes a cornerstone of industry practices, it reflects a collective effort towards a greener, more harmonious coexistence between industrial progress and environmental stewardship.
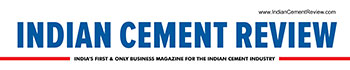
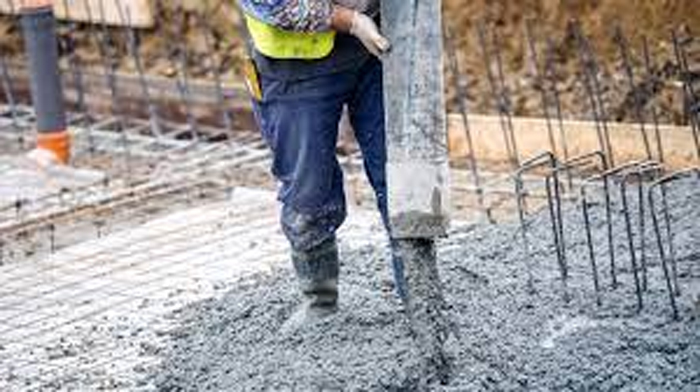
Tamil Nadu is set to host one of India’s five national carbon capture and utilisation (CCU) testbeds, aimed at reducing CO2 emissions in the cement industry as part of the country’s 2070 net-zero goal, as per a news report. The facility will be based at UltraTech Cement’s Reddipalayam plant in Ariyalur, supported by IIT Madras and BITS Pilani. Backed by the Department of Science and Technology (DST), the project will pilot an oxygen-enriched kiln capable of capturing up to two tonnes of CO2 per day for conversion into concrete products. Additional testbeds are planned in Rajasthan, Odisha, and Andhra Pradesh, involving companies like JK Cement and Dalmia Cement. Union Minister Jitendra Singh confirmed that funding approvals are underway, with full implementation expected in 2025.
Image source:https://www.heavyequipmentguide.ca/
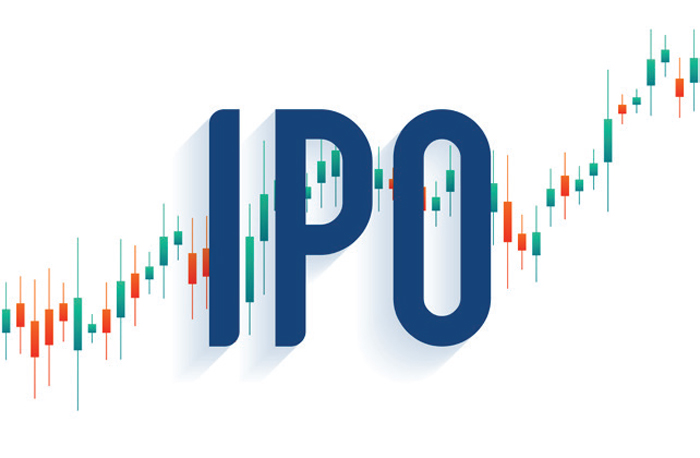
JSW Cement has set the price range for its upcoming initial public offering(IPO) at US$1.58 to US$1.67 per share, aiming to raise approximately US$409 million. As reported in the news, around US$91 million from the proceeds will be directed towards partially financing a new integrated cement plant in Nagaur, Rajasthan. Additionally, the company plans to utilise US$59.2 million to repay or prepay existing debts. The remaining capital will be allocated for general corporate purposes.
Concrete
Cement industry to gain from new infrastructure spending
Published
1 month agoon
July 24, 2025By
admin
As per a news report, Karan Adani, ACC Chair, has said that he expects the cement industry to benefit from the an anticipated US$2.2tn in new public infrastructure spending between 2025 and 2030. In a statement he said that ACC has crossed the 100Mt/yr cement capacity milestone in April 2025, propelling the company to get closer to its ambitious 140Mt/yr target by the 2028 financial year. The company’s capacity corresponds to 15 per cent of an all-India installed capacity of 686Mt/yr.
Image source:https://cementplantsupplier.com/cement-manufacturing/emerging-trends-in-cement-manufacturing-technology/