Concrete
Battling Emissions
Published
2 years agoon
By
admin
Initiatives such as carbon capture, sustainable sourcing and technological substitutes aim to achieve net-zero emissions, reducing environmental impact by curbing greenhouse gases and resource consumption. ICR delves into the endeavours undertaken by cement companies to mitigate emissions and the role of technology plays in the scheme of things.
The cement industry exerts a substantial environmental impact primarily through its emissions. Its production processes are energy-intensive and result in the release of significant amounts of carbon dioxide (CO2), contributing to global warming and climate change. This industry also generates air pollutants, including sulphur dioxide (SO2), nitrogen oxides (NOx), and particulate matter, which adversely affect air quality and human health.
Regulations and emission standards aim to limit the cement industry’s emissions and promote sustainability, but the environmental concerns remain significant and require ongoing attention. The environment has been a concern on the rise for a very long time. According to the World Air Quality Report 2023, India ranks eighth in the most polluted countries in the world amongst 131 countries with a population weighted average PM2. 5 level of 53.3 µg/m3 in 2022. The WHO guideline for annual PM2.5 levels is 5 µg/m3.
Particulate matter, in the form of fine particles, harms respiratory health and settles on ecosystems, impacting soil and water bodies. Moreover, cement production entails the extraction of raw materials through quarrying and mining, which disrupts ecosystems, leads to habitat destruction, and causes soil erosion and water pollution.
Water consumption for cooling and raw material preparation further strains local resources. To mitigate these environmental issues, the cement industry is adopting alternative fuels, improving energy efficiency, exploring carbon capture and utilisation (CCU) and storage (CCS) technologies and focusing on sustainable sourcing and recycling.
Vehicular emissions, industrial waste, smoke from cooking, construction activities, crop burning and power generation are among the biggest sources of air pollution in India. The country’s dependence on coal, oil and gas due to rampant electrification makes it the world’s third-largest polluter, contributing over 2.65 billion metric tonnes of carbon to the atmosphere every year.
Mitigating environmental emissions is top priority for cement manufacturers and innovative methods are the primary goal of their R&D departments. Ajay Sharma, Deputy Manager – Environment, Udaipur Cement Works Limited (UCWL), states, “Technology plays a crucial role in curbing emissions and improving the environment, allowing optimisation and cost saving. The installed pollution control equipment is connected with real time monitoring systems, which, in case of process failure of the interlocked facility, automatically tip/stop the plant operation to control environmental emissions.”
AN ENERGY INTENSIVE PROCESS
Energy consumption in cement plants is a critical aspect of the industry’s operations, and it is closely linked to emissions, primarily CO2 emissions. Cement manufacturing requires a significant amount of energy for various processes, including crushing, grinding, heating and clinker production. This energy typically comes from fossil fuels, such as coal, natural gas, and to a lesser extent, oil. To achieve their sustainability goals and to safeguard the environment, the industry uses alternative fuels like biomass, waste materials, and non-recyclable plastics in the plants to reduce their reliance on fossil fuels.
Raman Bhatia, Founder and Managing Director, Servotech Power Systems says, “Cement manufacturing indeed requires a significant amount of energy, which comes from carbon-emitting sources. However, by integrating Servotech’s on-grid solar system, the cement manufacturing process can be supported with clean and renewable energy. This sustainable energy source not only reduces the carbon footprint but also lowers operational costs, making the entire process more environmentally friendly and economically viable.”
A high intensity of heat generation is required for the process of clinkerisation, which is key to the process of cement making. This high energy intensity is a major driver of carbon emissions associated with cement manufacturing. The primary environmental concern related to energy consumption in cement plants is the release of CO2 emissions. When fossil fuels are burned to provide the necessary heat for clinker production, carbon dioxide is released into the atmosphere. This CO2 accounts for a significant portion of the industry’s total greenhouse gas emissions.
Automation plays a major role in managing the energy demands of the cement sector.
Manish Chordia, Regional Sales Manager-Cement (South Asia and Africa), ABB India, elaborates, “Efforts to reduce energy demands, by using higher efficiency equipment and substituting fuels and raw materials, are important to lower production costs. These changes introduce constraints that must be managed to secure the required quality and productivity of the plant.”
“There can be no flaws or failures in cement composition or entire structures could disintegrate. Advanced measuring, information and optimisation systems are needed as never before to monitor and correct any deviations in quality standards – from quarry to dispatch. Automation systems minimise material and energy use in complex processes,”
he adds.
SUBSTITUTION FOR ENVIRONMENT PROTECTION
Efforts are underway in the cement industry to mitigate these environmental harms. These include the use of alternative fuels and raw materials, energy efficiency improvements, carbon capture and utilisation/storage technologies, and sustainable sourcing of raw materials. The industry is also adhering to stricter environmental regulations and emissions standards are being put in place to limit the industry’s impact on the environment and promote more sustainable practices.
As India is part of the Paris Agreement and has aligned itself with its goal of achieving net zero by 2070 as announced in the Glasgow Climate Summit, it is in the race to achieve carbon neutrality by the said deadline. Thus, the industry has turned its focus on the use of alternative fuels and raw materials for the cement manufacturing process. This use of alternatives in the manufacturing process not only has significant ecological benefits of conserving non-renewable resources, the reduction of waste disposal requirements and reduction of emissions, but is also of an economic benefit for the industry.
The cement industry is actively exploring and adopting various substitutes and technologies to achieve net-zero emissions and reduce its environmental impact. One significant approach is the use of alternative fuels, such as biomass (e.g., wood chips, rice husks), waste-derived fuels (e.g., municipal solid waste, tire-derived fuels), and non-recyclable plastics. Substituting traditional fossil fuels with these alternatives reduces greenhouse gas emissions and resource consumption.
As large consumers of energy, transitioning to renewable energy sources, like wind, solar, and hydropower, to meet some of the energy needs of cement plants can significantly reduce carbon emissions. Implementing energy-efficient technologies and practices can reduce energy consumption and emissions. This includes optimising kiln design, heat recovery systems and upgrading equipment.
“Our highly efficient On-Grid Solar System is designed to provide solar energy to cement manufacturing plants seamlessly. The process begins with the installation of solar panels, which capture sunlight and convert it into electricity. The energy generated is then fed into the plant’s electrical grid. This solar-generated electricity effectively powers various operations within the cement manufacturing process, reducing the plant’s reliance on conventional energy sources and lowering its electricity costs. This transition to solar energy not only makes cement production more sustainable but also contributes to reduced operational expenses, ultimately benefiting the environment and making the entire process cost-efficient,” Bhatia adds.
CIRCULAR ECONOMY
The cement industry can make significant contributions to the circular economy, thereby reducing its environmental impact and emissions. Embracing circular economy practices can lead to more sustainable cement production by minimising waste, conserving resources, and reducing the carbon footprint.
The cement industry can incorporate various industrial byproducts into its production processes. For example, steel slag, coal, fly ash and silica fumes can be used as supplementary cementitious materials, reducing the environmental impact of these waste materials. Wastes from various industries like bio-waste, non-usable rubber, plastic etc. can be used as fuel. This would prevent the said waste from accumulating in the land and ocean beds, thus harming land fertility and creating water body pollution.
Besides the use of waste as fuels and raw materials, waste heat from cement production processes can be captured and repurposed to provide additional energy for the plant or for other industrial processes, reducing the industry’s energy consumption and emissions. The captured CO2 emissions from cement plants can be utilised in other processes or industries, such as the production of synthetic fuels, chemicals, or building materials. This not only reduces emissions but also creates value from a waste product.
Old concrete structures can be recycled and crushed to produce recycled aggregates, which can be used in new concrete production. This conserves natural resources and reduces the need for quarrying and mining.
According to a report published by McKinsey, ‘The Circular Cement Value Chain: Sustainable and Profitable, October 2023, the cement value chain is well positioned to create closed loops, or automatically regulated systems, for carbon dioxide, materials and minerals and energy. This entails circular economies, which are based on the principles of eliminating waste and pollution, circulating products and materials and regenerating nature. Circularity can work jointly with reducing carbon emissions in cement production because circular technologies follow the paradigm of three crucial decarbonisation strategies: redesign, reduce and repurpose.
Addressing the total volume of materials needed — or redesigning materials, buildings, and infrastructure — can play a critical role in changing how industry leaders approach projects. Next, shifting from fossil to alternative fuels can help reduce emissions of materials. Finally, repurposing, repairing, and refurbishing existing assets and infrastructure can help limit the need for new products by utilising captured carbon dioxide emissions and reinserting them into the value chain.
According to estimates, and expected carbon prices, each of these circularity technologies will be value-positive by 2050, with some already more profitable than today’s business-as-usual solutions. That said, a few solutions were not factored into our analysis despite being critical to reaching net-zero emissions, including the reduction of clinker in cement through substitutes and low binder intensity, the reduction of cement in concrete through less overspecification by design, and the overall reduction of concrete in the built environment through alternative building materials. Thus, these solutions should be considered part of a broader definition of circularity.
By adopting these circular economy practices, the cement industry can reduce waste generation, conserve resources, lower energy consumption, and minimise carbon emissions. This not only benefits the environment but also enhances the long-term sustainability and resilience of the industry itself, helping it align with global efforts to address climate change and environmental challenges.
FUTURE OF ENVIRONMENT AND EMISSION
“The future of emissions in the cement industry is likely to be marked by efforts to reduce carbon emissions. The pace of change will depend on a variety of factors, including technological advancements, regulatory policies, and the level of commitment from industry stakeholders. The industry is expected to continue its journey towards lower emissions, driven by a growing awareness of the environmental impact and the importance of sustainable practices. The cement industry shall continue to invest in and adopt carbon reduction technologies, such as carbon capture and storage (CCS) and CCUS to capture and sequester CO2 emissions from cement production. These technologies may become more widespread as the industry seeks to reduce its carbon footprint,” says Sharma.
“Use of alternative materials and blends like slag, fly ash, calcined clay and limestone, is expected to be increased. These materials can help reduce the clinker content in cement, lowering emissions during production. The industry is also paving a path towards transitioning to renewable energy sources for power generation at cement plants, such as solar, wind and hydropower, which will reduce carbon emissions associated with energy use in cement production,” he adds.
Environmental protection is at the core of the cement industry. With the race to net zero, decarbonisation and sustainability are at the forefront of the cement industry. Experts from all fields of the industry are involved in research and development to reduce their emissions. Various technological advancements and latest machinery and equipment tech are getting incorporated by players of the industry as an effort to safeguard the environment. The future of the cement industry in India holds the potential for significant improvements in environmental sustainability and emissions reduction. However, realising this potential will require a concerted effort by the industry, government, and other stakeholders to adopt and implement sustainable and low-carbon technologies and practices.
- –Kanika Mathur
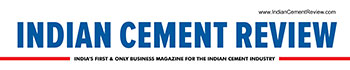
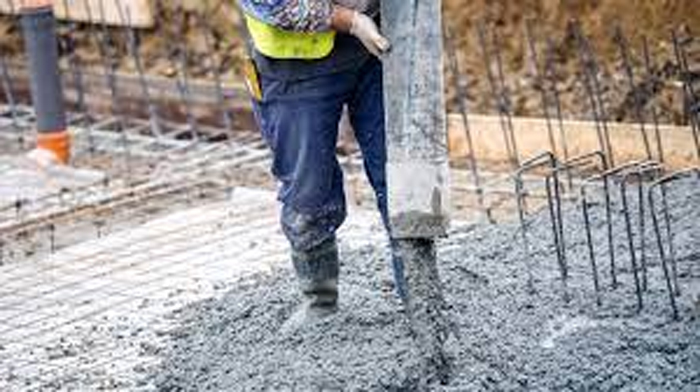
Tamil Nadu is set to host one of India’s five national carbon capture and utilisation (CCU) testbeds, aimed at reducing CO2 emissions in the cement industry as part of the country’s 2070 net-zero goal, as per a news report. The facility will be based at UltraTech Cement’s Reddipalayam plant in Ariyalur, supported by IIT Madras and BITS Pilani. Backed by the Department of Science and Technology (DST), the project will pilot an oxygen-enriched kiln capable of capturing up to two tonnes of CO2 per day for conversion into concrete products. Additional testbeds are planned in Rajasthan, Odisha, and Andhra Pradesh, involving companies like JK Cement and Dalmia Cement. Union Minister Jitendra Singh confirmed that funding approvals are underway, with full implementation expected in 2025.
Image source:https://www.heavyequipmentguide.ca/
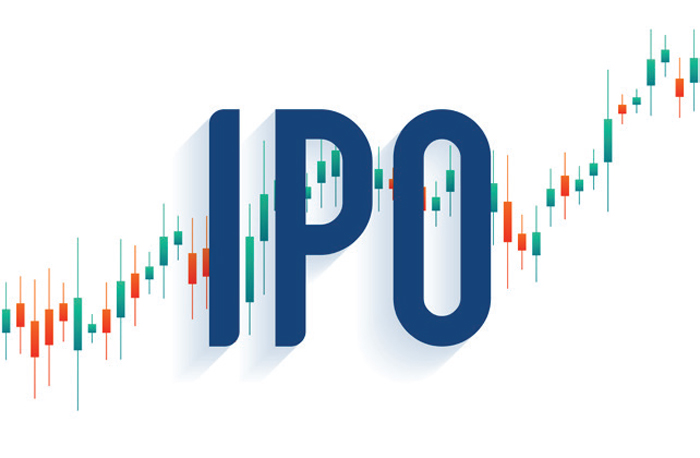
JSW Cement has set the price range for its upcoming initial public offering(IPO) at US$1.58 to US$1.67 per share, aiming to raise approximately US$409 million. As reported in the news, around US$91 million from the proceeds will be directed towards partially financing a new integrated cement plant in Nagaur, Rajasthan. Additionally, the company plans to utilise US$59.2 million to repay or prepay existing debts. The remaining capital will be allocated for general corporate purposes.
Concrete
Cement industry to gain from new infrastructure spending
Published
1 month agoon
July 24, 2025By
admin
As per a news report, Karan Adani, ACC Chair, has said that he expects the cement industry to benefit from the an anticipated US$2.2tn in new public infrastructure spending between 2025 and 2030. In a statement he said that ACC has crossed the 100Mt/yr cement capacity milestone in April 2025, propelling the company to get closer to its ambitious 140Mt/yr target by the 2028 financial year. The company’s capacity corresponds to 15 per cent of an all-India installed capacity of 686Mt/yr.
Image source:https://cementplantsupplier.com/cement-manufacturing/emerging-trends-in-cement-manufacturing-technology/