Concrete
The main task in cement production is improving sustainability
Published
3 years agoon
By
admin
Prakhar Shrivastava, Head – Corporate Quality, JK Cement Limited, discusses the smart use of supplementary cementitious materials to improve cement production and make cement manufacturing more integral to a circular economy.
What are supplementary cementitious materials? Tell us more about their nature
of origin.
Supplementary Cementitious Materials (SCM) are materials that are obtained from other industrial waste as by-product and none have their own/individually hardened properties but contribute by grinding with clinker or blending with Ordinary Portland Cement (OPC) through hydraulic and/or pozzolanic activity. These waste products are used as supplementary cementitious materials so that the maximum utilisation of wastes is possible. SCM play a significant role in increasing the workability of the product and enhance the serviceability or durability, thus, decreasing the permeability, aiding in pumpability and finishability.
Typical SCM are flyash, slag, silica fume, natural ashes, rice husk ash, burnt shale, metakaolinite, calcined clay and natural pozzolana i.e., volcanic glass, etc. Among them, flyash and slag are widely used by cement industries for production of PPC and PSC.
Flyash or pulverised fuel ash is formed during combustion of coal from coal-fired electric and steam generating plants and obtained by electrostatic or mechanical precipitation of dust like particles from the flue gases. Earlier, it was recognised as an industrial waste but now has become an important industrial by-product.

Steel slag, a by-product of steel industries, formerly referred to as ground, granulated blast-furnace slag, is a glassy, granular material formed when molten, iron blast-furnace slag is rapidly chilled – typically by water sprays or immersion in water – and subsequently ground to cement fineness.
Tell us about the supplementary cementitious materials and their composition used by your organisation?
Supplementary cementitious materials are soluble siliceous, alumina-siliceous or calcium alumina-siliceous powders used as partial replacements of clinker in cements or as partial replacements of portland cement in concrete mixtures.
At JK Cement, we manufacture Portland Pozzolana Cement (PPC) from all our plants with addition of flyash up to 35 per cent and PPC in premium category with 20 per cent flyash to promote usage of only blended cement to fulfil customer requirements by achieving equivalent strength properties of OPC (Ordinary Portland Cement). At our south India plant in Muddapur, we also manufacture Portland Slag Cement (PSC) with the addition of slag at approximately 65 per cent, meeting all the internal product quality norms.
In our plants, flyash is sourced from different thermal power plants in accordance to the quality, cost and suitability criteria of the plants. Similarly, slag is sourced from steel plants located in Karnataka and Goa. The typical chemical composition and quality requirements as per Indian standards of flyash and slag are mentioned in the table:

Does the use of supplementary cementitious materials impact the process of cement manufacturing?
Impact of SCM can be categorised in two aspects i.e., challenges and benefits. Below are the few challenges faced during the process of cement manufacturing.


- Major SCM are available across the country, such as, dry flyash and pond ash; however, less availability of dry flyash directly connected with thermal power plants (TPP) operation.
- Though there is abundance of pond ash, the major concern in its usage is the high moisture content and coarser size, which creates constraint of jamming, leading to lower production, higher power consumption, blended cement quality and slower production.
- Additional feeding systems are required.
- Challenges of further grinding of abrasive/harder to grind materials such as coarser pond ash, GGBS, copper slag.
- It may increase the cost of the product especially where some SCM are more expensive than cement. i.e., the availability of SCM.
- SCM used for the clinkerisation process required high grade limestone to maintain the desired quality of clinker which affects the mine life.
What are the key advantages of using supplementary cementitious materials in the cement manufacturing process?
The key advantages of using supplementary cementitious materials are:
- Increased clinker substitution; reduces CO2 emission per ton of cement production.
- Reduces use of fossil fuel per ton of cement production.
- Increases the life of limestone mines.
- Reduces consumption of thermal and electrical energy.
- Reduces water consumption.
- Reduces generation of garbage materials at the location, which in turn leads to clean India.
How does the use of supplementary materials increase the profitability of the cement manufacturing for your organisation?
SCM play a vital role in increasing the profitability of the cement manufacturing; with the addition of SCM during cement production, it enhances the overall cement capacity. All our plants are using SCM which are available nearby to plant location. We are investing a lot at locations where SCM are available at a lower cost value and hence reducing the overall cost of cement as compared to clinker cost. Also, these SCM help in reducing the power consumption per ton of cement due to increase in cement volume. Another benefit is the increased cement volume that results in intangible benefit by increasing limestone mine life and conserving natural resources of compendious materials.
Tell us about the quality standards and checks implemented for the final product made using supplementary materials.
The Indian standards have been framed to define the quality of SCM by BIS. Each SCM has a specific Indian standard with specific quality norms like for pulverised fuel ash (IS 3812 Part-1), slag (IS 12089), calcined clay pozzolana (IS: 1344-1981 (Part-II) etc. According to IS specification; internal quality standards have been specified to monitor the SCM quality and these quality specifications are specified in the purchase order for vendor reference. A structured and systematic approach is made to check the SCM quality by the quality control department and all test results are recorded in SIT formats.
In order to make different grade products following checks have been implemented
- Has established a distinct location/yard/silo for proper storage of SCM and to avoid contamination.
- Different hoppers are assigned for each type of material storage and to introduce during the manufacturing process.
- For controlled and calculated addition; weigh feeders are installed.
- For each process or step, quality norms have defined and organised the monitoring and testing in stipulated frequency as per IS requirement.
- Prior to dispatch and release of product in market or to customer the prescribed quality testing performed for quality reassurance.
Tell us about the role of technology in deciding the proportions of supplementary cementitious materials.
Today, the main task in cement production is improving sustainability by reducing emissions. This is achieved by promoting the use of green fuels that lower the conventional fuel consumption and by utilising the alternative raw materials i.e. SCM while producing reliable products at a competitive cost for the construction industry. Less clinker and more SCM is the challenge for the cement industry. The control and optimisation of clinker and cement reactivity is one important key to reach these targets. A problem today is that clinker and cement reactivity are not quantified at cement plants, except by slow and indirect methods like compressive strength testing.
XRF and XRD studies are valuable to understand the composition. However, quantitative XRD does not directly assess the reactivity of SCM. Recently isothermal heat flow calorimetry techniques have been suggested as a new analytical tool for process control and deciding the proportion of SCM in cement.
Recently, the beneficiation or processing of flyash has become hugely important. Flyash Beneficiation Technology or process converts waste from coal-fired power stations (pulverised fuel ash or flyash) by separating the constituent minerals to generate a range of sustainable, environment-friendly products with unique physical and chemical characteristics.
What are the major challenges you face while using supplementary materials for cement manufacturing?
The major concern is availability in terms of quality and quantity; the second factor is cost because the overall cost depends on the distance between the generation unit to the cement manufacturing plant which eventually impacts the cost of cement.
Constantly the SCM demand is increasing and the availability of good quality SCM is very limited and on high cost, the high moisture content of slag and pond ash creates operational challenges. The quality of SCM, largely influenced by the existence of high quartz, heavy metals, alkalis and the fineness that determine the quality of cement. Indian flyash is more crystalline compared to what is generated in other countries and the ratio of formers (SiO2,+Al2O3+Fe2O3) to network modifiers (Na2O+K2O+CaO+MgO) in the Indian flyash is very high and imbalanced.
Depending on the source of coal that varies from mine to mine impacts the composition of flyash like bituminous coals, sub-bituminous and lignite coal determine the flyash colour, fineness and other radicals. Among all SCM, flyash is mostly used in cement plants and as thermal power plants (TPP) are the source of flyash, the present availability of coal and its high cost is a major concern for TPP operations that is affecting the flyash generation. The availability and sources of slag in India are limited, which are affecting its usage in blended cement. Except for flyash and slag, other SCM availability is very less and not too economical.
How does the use of cement made of supplementary materials impact its carbon footprint?
We have committed to achieving our SBTi goal by cutting our GHG emissions according to climate science and as a Global Member of GCCA, by pledging for UNFCCC’s ‘Race to Zero Campaign’ to achieve Net Zero Carbon by 2050.
Clinker manufacturing is responsible for 80 per cent of the carbon emissions and supplementary cementitious materials reduce the clinker content in cement to a great extent without compromising the quality of the product. JK Cement’s green vision is to deliver a sustainable product to meet the stakeholder’s demands while taking several measures that can reduce CO2 emissions in the clinker manufacturing process. This can be achieved by using different types of alternative fuels, RDF/MSW, biomass fuels etc. and various industrial waste such as raw mix components like red mud, GCP dust, iron sludge, zinc slag etc.
Supplementary cementitious materials such as flyash, slag, waste gypsum and industrial waste are the crucial components of JK Cement’s business strategies for conservation of the mineral resources which enables us to produce sustainable construction materials in terms of low embodied carbon at a competitive cost. This has transformed our operations by setting up a benchmark for achieving the best sustainable business practices in the industries and producing Green Certified Cement.
Tell us about the impact of cement made with supplementary materials on the construction and allied industries.
As the construction sector is incessantly challenged by the growing societal demands for safer and cost-effective infrastructures, more and more environment-friendly products and processes must be developed and adopted into our industrial practice. Although supplementary cementitious materials are one of the most used construction materials worldwide, there are still some major concerns about their sustainability and durability.
Firstly, the production of concrete is releasing large volumes of carbon dioxide into the atmosphere, one of the greenhouse gases attributable to
climate change. Secondly, even though cementitious materials are very versatile and robust they may suffer from various deteriorative processes, leading to shortened service life, and consequently, intrusive or expensive costs for maintenance and repair.
To meet the expectations of consumers, demanding more durable, less labour and service intensive materials at a competitive price, numerous new composite materials and technologies have been developed over the last couple of decades including blended cements with Supplementary Cementitious Materials (SCM).
Some of the positive impacts are summarised as follows:
- The use of supplementary cementitious materials in construction not only improves the mechanical property of cement matrix but also reduces its impacts on the environment.
- Blended cement helps to reduce the damage to the concrete from alkali-silica reaction and provides higher resistance to chloride ingress thus reducing the risk of reinforcement corrosion.
- Mitigating sulphate phase formation, which takes place when sulphates found in seawater and some soils react with tricalcium aluminate in concrete.
- Some of the allied industries have started making limestone bricks, AAC blocks, hollow blocks, flyash bricks which are not only considered as green products but also reduce the cost of construction works.
How do you foresee the future of the global cement industry in terms of using alternative materials for cement manufacturing and running the race of decarbonisation?
The production of Ordinary Portland Cement (OPC) is continuously declining, with a simultaneous increase in the production of blended cement like PPC, PSC, and Composite Cement based on flyash and granulated blast furnace slag. SCM are increasingly used to minimise cement-related CO2 emissions and increase plant efficiency from an economic and environmental perspective.
At present, blended cements have a greater share (73 per cent) in comparison to ordinary portland cement (27 per cent). Other cement formulations such as Portland Limestone Cement (PLC) and Limestone Calcined Clay Cement (LC3) are also at different stages of development in India.
In recent years, globally and in India several research has been conducted for the development of environment-friendly and less CO2 emission cement i.e., Calcium Sulfo-Aluminate Cement, Reactive Belite Cement, Alkali Activated Cement etc., that is found to be more energy-saving, less carbon intensive and optimises waste-utilisation. Further studies were carried out on carbon capture storage and usage, zero emission mining, oxyfuel combustion in kiln etc. If these solutions become economically viable, they may contribute to a considerable reduction in CO2 output from the cement industry.
–Kanika Mathur
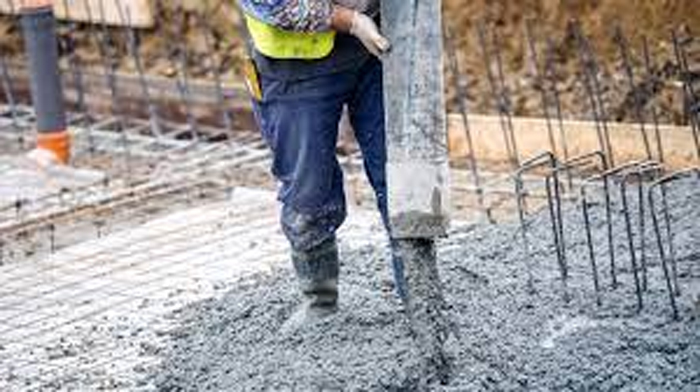
Tamil Nadu is set to host one of India’s five national carbon capture and utilisation (CCU) testbeds, aimed at reducing CO2 emissions in the cement industry as part of the country’s 2070 net-zero goal, as per a news report. The facility will be based at UltraTech Cement’s Reddipalayam plant in Ariyalur, supported by IIT Madras and BITS Pilani. Backed by the Department of Science and Technology (DST), the project will pilot an oxygen-enriched kiln capable of capturing up to two tonnes of CO2 per day for conversion into concrete products. Additional testbeds are planned in Rajasthan, Odisha, and Andhra Pradesh, involving companies like JK Cement and Dalmia Cement. Union Minister Jitendra Singh confirmed that funding approvals are underway, with full implementation expected in 2025.
Image source:https://www.heavyequipmentguide.ca/
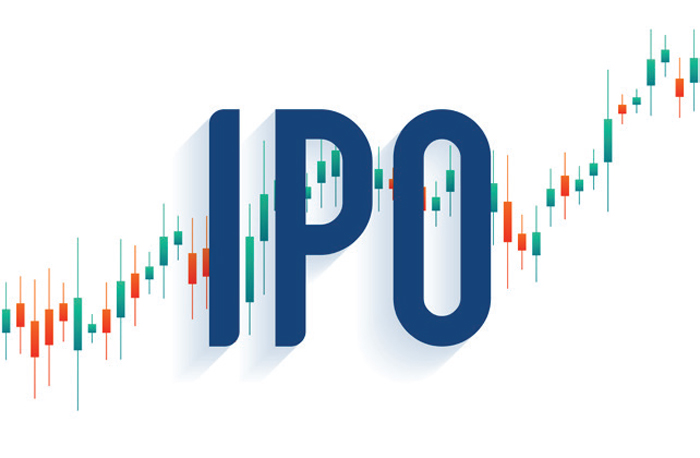
JSW Cement has set the price range for its upcoming initial public offering(IPO) at US$1.58 to US$1.67 per share, aiming to raise approximately US$409 million. As reported in the news, around US$91 million from the proceeds will be directed towards partially financing a new integrated cement plant in Nagaur, Rajasthan. Additionally, the company plans to utilise US$59.2 million to repay or prepay existing debts. The remaining capital will be allocated for general corporate purposes.
Concrete
Cement industry to gain from new infrastructure spending
Published
1 month agoon
July 24, 2025By
admin
As per a news report, Karan Adani, ACC Chair, has said that he expects the cement industry to benefit from the an anticipated US$2.2tn in new public infrastructure spending between 2025 and 2030. In a statement he said that ACC has crossed the 100Mt/yr cement capacity milestone in April 2025, propelling the company to get closer to its ambitious 140Mt/yr target by the 2028 financial year. The company’s capacity corresponds to 15 per cent of an all-India installed capacity of 686Mt/yr.
Image source:https://cementplantsupplier.com/cement-manufacturing/emerging-trends-in-cement-manufacturing-technology/