Concrete
Refractories: ‘Tech’ing Up!
Published
3 years agoon
By
admin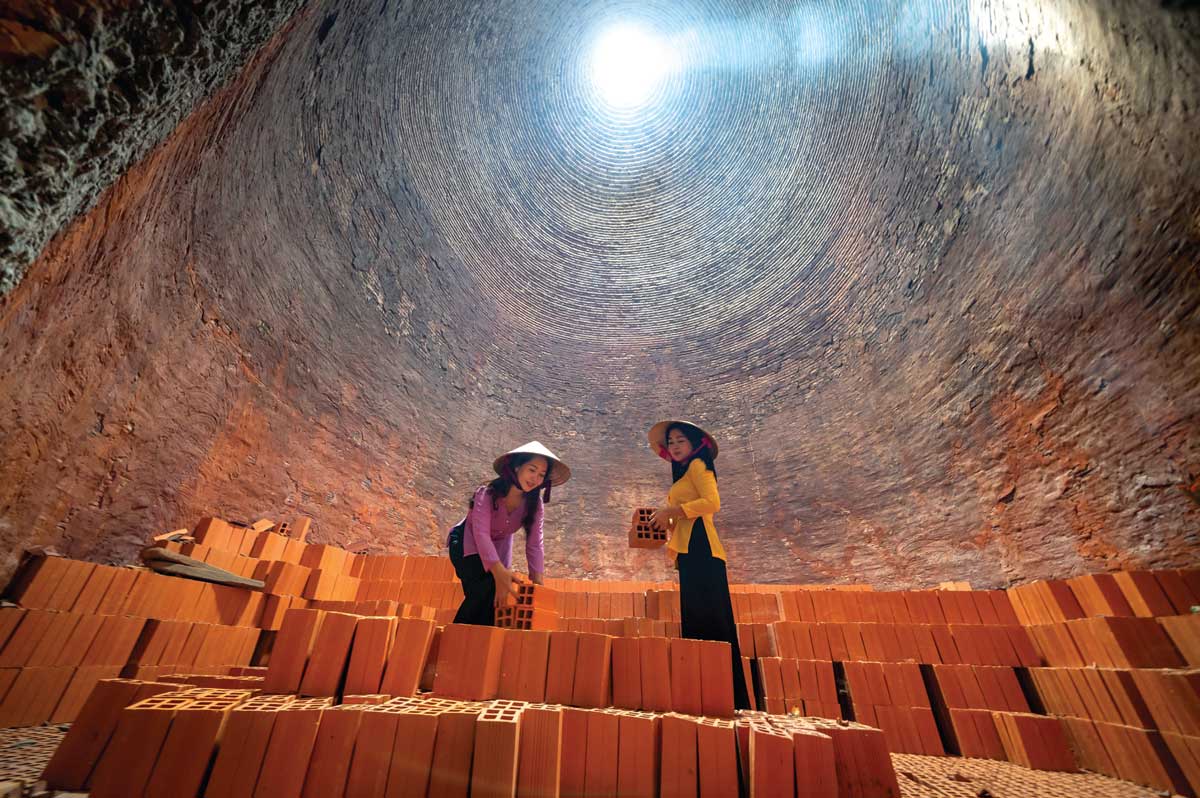
Refractory failure is considered the most critical upset in a kiln operation. Considering the importance of refractories in the cement making process, ICR delves into the various types of refractories, their operations, challenges and the efforts taken by cement manufacturers in keeping up with innovations and automation of refractories for more efficient processes.
Cement is the most consumed man-made product across the globe. The modern civilisation owes a lot to the contribution of cement and concrete as a building material for construction of bridges, buildings, roads, dams, tunnels, and tall structures which are being used by the people everywhere in every walk of life. Manufacturing process of cement involves high temperatures. The combustion of limestone, clay or other materials to form clinker is an extremely energy intensive and temperature intensive process. This high-temperature reaction takes place inside a reactor called a kiln.
To contain the temperature inside the kiln on a continuous basis and to make the manufacturing possible on an industrial scale, Refractories play a very important role. A refractory lining inside the reactor maintains the temperature range of the reactor metal structure within a tolerable limit. This lining, also known as refractory, also inhibits the heat flow from inside of the reactor to outside. Thus, it helps in conserving the energy, which makes the cement manufacturing process productive and profitable.
There are two major purposes of refractories in a cement manufacturing unit:
To contain the high temperature or heat generated during pyroprocessingTo insulate the reactor and prevent the heat from dissipating in the environment
The special demands of cement manufacturing have always required specialised refractories – especially now, when more and more alternative fuels are used.
Types of Refractories
The special demands of cement manufacturing have always required specialised refractories – especially now, when more and more alternative fuels are used. There are two main types of refractories: castable and brick, each with distinct advantages and disadvantages.
Castable Refractory: This refractory comes in a powder form and is mixed with water on-site. Before the mixture can be put in place, anchors are installed. These Y-shaped anchors are similar to rebar in cement; they help give the castable lining its strength. Once these anchors are in place, the cement-like mixture is pumped into the lining of the rotary kiln, and allowed to cure for several days.
Brick Refractory: Brick is fired in a furnace under tightly controlled conditions that allow it to achieve better properties than a similar composition castable refractory.
Castable refractory has a similar material cost to brick. However, brick installation is much more labor intensive, as each brick is individually installed. This makes the overall cost of a brick lining more expensive than castable. While brick refractories are slightly more expensive than castable refractories, bricks do not require anchors, and their quality is superior. When processing a highly abrasive material, brick refractory is advisable most of the time, as castable does not have the durability to stand up against abrasive materials as well as brick.
Besides lower overall cost, the advantage to using a castable refractory in a rotary kiln is that it is usually easily patched when a problem is encountered. Down time is typically minimal, because the problem area can be cut out and new refractory poured into the cavity.
The disadvantage to using a castable refractory in a rotary kiln is that it is very susceptible to installation problems. When a castable refractory is expertly installed, it can nearly match the quality of brick.
But if installed incorrectly, there can be a considerable difference in quality, and the life of the refractory can be severely compromised.
The disadvantage to brick refractory is that it is kept in place much like a roman arch: bricks are held in place by the pressure of the other bricks pushing against each other. When a problem is encountered, typically the failed brick needs to be replaced, but when one brick is relying on the bricks around it to hold it in place, often one cannot replace just one brick, and whole sections of the refractory must be replaced. Unlike castable refractory, the repair of a failure in brick refractory is much more involved.
Need and Function of Refractory in a RotaryKiln
Cement rotary kilns are kilns that conduct pyroprocessing. It is a machinery in the cement manufacturing plant that is used to heat materials to high temperatures in a continuous process. The kiln body is a cylinder vessel with a certain degree of tilt to the horizontal level. Raw materials are fed into the vessel from the upper end and moved to the lower end, being stirred and mixed relying on the inclination and rotation of the kiln. The kiln burner produces a lot of heat by burning fuel. This kind of heat is usually transferred to materials through flame radiation, hot gas convection, kiln brick conduction, etc., which causes the chemical reaction between raw materials and finally forms a clinker.
Rotary kilns can be divided into cement kilns, metallurgical and chemical rotary kilns, lime rotary kilns and so on. Cement rotary kilns are used for calcining cement clinkers in the cement plant, which can be divided into dry cement kilns and wet cement kilns. Metallurgical and chemical rotary kilns are mainly applied in the metallurgical industry. As for the lime rotary kiln, it is the main equipment for calcining active lime and light burned dolomite used in iron and steel plants, ferroalloy plants, calcium carbide plants, and magnesium metal plants.

The cement rotary kiln is mainly composed of a cylinder, supporting device, drive gear, refractory lining, catch-wheel device, kiln head sealing device, kiln tail sealing device, kiln hood, and other components. On the cylinder, there is a large gear ring fixed with a spring plate near the kiln tail; some pinions below are engaged with it, jointly forming the drive gear. In normal operation, the main drive motor will transfer power to this gear device through a reducer to run a rotary kiln. The raw material usually enters the rotary kiln from the upper end and moves slowly to another end along with the chamber as it rotates. In this process, raw materials will be heated by high temperature and then decompose and produce chemical reactions so that their state finally changes. Under normal conditions, the heat source of indirect fired rotary kilns is supplied from the kiln burner outside the kiln. This kind of way protects the integrity of raw materials, while the heat source of the direct-fired rotary kiln is inside the kiln. Besides, the rotation speed and temperature of the cylinder are tightly controlled and changed according to different desired processes and material applications. After the calcination is completed, the clinker will be pre-cooled in the chamber and then be sent into the cooler for further cooling.
With the continuous progress of the cement industry, rotary kilns, as the core cement equipment of the cement production line, is developing towards a large scale. Compared with the traditional rotary kiln, its technology is more complex, and the requirements for rotary kiln design and accessories are higher. The rotary kiln refractory lining is a layer of refractory material installed inside the kiln cylinder, which plays a protective role in many aspects, and is an important part of cement rotary kiln.
To protect the shell of the kiln from the high temperatures of the feed and combustion gases, a brick lining is used. Refractories play a critical role in both the rotary kiln lining, and the lining of the high-volume static equipment areas that comprise a modern pre-calciner kiln system.
Refractories require an insulating coating or lining further helping its function of preventing heat from escaping the kiln. Some of the key features that this coating material must have are:
- High adhering potential to the lining and bricks
- Mouldable to various shapes and sizes to fill in the gaps and holes of the brick lining
- Acts as a protective layer against corrosion from flames and molten substances
- Provides thermal spalling
- Improves surface resistance to erosions and voids.
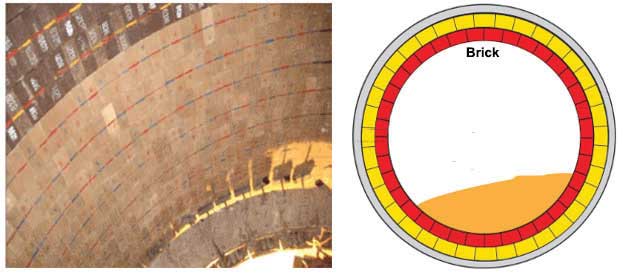
Layers of Refractories
Refractory is a customisable part of the rotary kiln and can be designed to suit the requirement of the desired clinker and subsequently, the end product of the process, cement. It can be tailored with multiple layers to meet the demands of a given application.
A refractory mostly has two layers, the working layer and the insulating layer and the combined thickness of the two ranges from 4.5 inches to 12 inches. They are made with materials that can withstand the high temperature process that takes place in the cement manufacturing process.
Working layer is designed with durable materials designed to withstand the heat within the rotary kiln as it comes directly in contact with the materials and raw mix being processed. It also goes through constant abrasion as it comes in contact with the materials.
An insulating layer is required beneath the working layer of the refractory to prevent the heat from slipping out to the shell of the kiln. This would be both dangerous as well as would lead to loss of efficiency and productivity of the process. It would also lead to damage of the kiln shell.
Typically, the working layer and the insulating layer are made of the same material (ie. brick or castable), with varying chemistries. The working layer tends to be a higher density, stronger material that is more conductive. The insulating layer does not need these qualities, and tends to be softer, lighter, and less conductive, therefore more insulating. These two layers often vary in thicknesses, determined by the needs of the rotary kiln and what material is being processed. In some cases, such as when temperatures are low, or when efficiency is not a concern, a single working layer may be all that is needed.
In contrast, when insulation is extremely critical, an optional third layer of ceramic fibre backing may be used. This thin, but very efficient layer is like fibreglass insulation found in a house, but it is much more compressed. The decision to employ this layer comes with some responsibility. Should a crack in the refractory occur and go unnoticed, it is possible for the high heat inside the rotary kiln to reach this backing and burn it up. This would create a gap between the refractory and the shell of the rotary kiln, which would cause disastrous problems. Due to this potential of increased risk, this third layer is not always appropriate.
Refractory Materials
A refractory is made of inert inorganic solid materials like oxides, carbides, nitrides, and borides of aluminium, silicon, alkaline earth metals, and transition metals. The key requirements of the materials from which a refractory is built are to be stable at high temperatures and to retain their original physical shape when they are exposed to corrosive solid, liquid or gaseous materials. Out of all these materials, very few qualify to be used in industrial scale, because of their instability under normal atmospheric conditions or because of the rare availability and high cost.
“Cement manufacturing is an energy intensive process. Burning alkaline raw materials (reactive) combined with smaller constituents of metals and abrasive raw materials at very high temperature is a major challenge. Therefore, a good refractory that can withstand high temperatures while retaining required strength and that is resistant to chemical properties of the alkaline raw materials is crucial. Besides, chemical attacks from sulphates or chlorine from the kiln feed, fuel or alternative fuels there are other factors that need to be factored in,” says Prabhat Singh Parihar, Vice President Technical Head, Mangrol Plant, JK Cement.
The source of the raw materials can be natural or synthetic. The raw materials used for refractory manufacturing are mainly naturally occurring minerals like bauxite, magnesite, clay etc., which are mined and processed before being used for refractory manufacturing. Some synthetic materials like mullite (3Al2O3.2SiO2), fused alumina (Al2O3), silicon carbide (SiC), spinel (MgO.Al2O3) etc., are also being used widely in refractories for the cement industry.
Operating Condition for Refractories
According to a report – Refractories Selection for Cement Industry, August 2020 published by IN Chakraborty, Ace Calderys Limited, Nagpur, refractory selection is the most important step for the maximisation of its performance.

areas that comprise a modern pre-calciner kiln system.
The major deciding factors for refractory selection are the working environment where the refractory would be used. The working environment, in general, is defined by the following parameters:
- Operating temperature
- Chemical condition
- Chemical nature of solid or liquid, i.e., acidic, or basic, in contact with the refractory
- Characteristic of the gaseous environment
- Thermal shock
- Mechanical stress
- Abrasion
Refractory selection is the most important step for the maximisation of its performance. The major deciding factor for refractory selection is the working or operating environment where the refractory would be used. The working environment, in general, is defined by the following parameters:
Identification of critical parameters for a given working environment is vital for refractory life maximisation at optimal cost. Once the critical operating parameters are identified, the refractory should be so selected that it can withstand the operating condition for the stipulated lifespan. In the context of the refractory life in the cement rotary kiln, the lining design as well as the quality of refractory installation play a very critical role.
As a function of the cement manufacturing process, a raw meal i.e., a mix of limestone, quartz, clay and some lateritic material is fed in the kiln. This operating condition in this kiln is not severe except for in the burning zone where temperature can go up to 1450oC and the liquid content of the feed material falls in the range of 25 per cent to 27 per cent
By the time the raw mix attains a temperature of 900oC, the limestone present in the raw material is decomposed and quartz undergoes polymorphic transformation and cement constituents like C2S and C3A start forming. None of these have an adverse effect on the refractory. As the temperature rises to 1400oC, the liquid phase forms. At the maximum operating temperature, approximately 1450oC, the liquid phase concentration is about 25 per cent. On cooling down the C3S and C4AF precipitate out from the melt. As the clinker cools down, the reactivity of the mass reduces, i.e., the refractory is not chemically affected. However, the cold clinker becomes abrasive and may cause erosions on the refractory.
This operating condition of the kiln is of moderate severity from the chemical reactions point of view. The temperature in the non-burning zone part of the kiln system is not high enough for a chemical reaction between the aluminous refractory and the lime bearing raw material of the clinker.
This situation, however, becomes severe when alternative fuels are used. It is their alkali and chlorine concentrations that are significantly high compared to the conventional fuels. The melting points of these alkali compounds are lower than the maximum operating temperature of the kiln, hence, they evaporate in the kiln and travel along with the flue gas towards the kiln inlet areas whereas the rest escape in the kiln system by combining with the clinker. This alkali bearing gas then gets deposited on the incoming raw meal at the corresponding feeding point of these alkali compounds. The alkali enriched raw meal travels back to the kiln and the process repeats.

has either been entirely lost or has become too thin.
The chloride compounds have a lower melting point than the sulphates. They have the ability to travel further back in the kiln system, compared to sulphur bearing compounds. Owing to this cycling process, the kiln environment becomes richer in alkalis as compared to their concentration in the raw meals. Owing to the self-enrichment phenomenon, raw meal chemistry does not indicate the true chemical environment of the kiln.
Properties of Refractories
Refractories are characterised by their chemical and physical properties and are used to correlate its behaviour in actual high-temperature application.
Apparent Porosity: Refractories contain pores; some of the pores are open and connected and some are closed. The total volume of a refractory body is the sum of the volume of the matter, volume of the open pores and the volume of closed pores. The apparent porosity of a refractory is expressed in percentage and is defined as a percentage of the volume of open pores against the total volume.
It is a very important property and influences the mechanical strength, corrosion resistance, and thermal conductivity of a refractory. Porosity and bulk density of a refractory are inversely related. The lower the apparent porosity, the more will be the bulk density, mechanical strength, thermal conductivity, and corrosion resistance of the body. Besides total pore volume, the pore sizes are also very important to influence the corrosion resistance and thermal conductivity of the refractory. The smaller the pore sizes, the better is the corrosion resistance and the lower is the thermal conductivity.
Permeability: It is the measure of flow of gases through pores within the refractory body, and it indicates the extent of pore linkage. Permeability of refractories gives an indication on how well the Refractory will stand up to molten slag, a melt or to a gas penetration.
“The apparent porosity or open porosity (oPo) is the volume of the open pores, into which a liquid can penetrate, as a percentage of the total volume of the refractory. This property is important when the refractory is in contact with molten charge. A low apparent porosity prevents molten material from penetrating into the refractory, it makes a materialto- material bond and develops a good and stable coating on refractory / bricks, which enhances its life and its resistance to corrosion,” says Pradeep Kumar Chouhan, General Manager – Quality Control & Environment, Udaipur Cement Works Limited.
“The permeability of refractories is a governing factor in the deterioration of linings by liquids and gases. The permeability of any refractory material is defined as the volume of the gas or air, which passes through a cubic centimetre of material under a pressure of 10 mmWG per seconds” he adds.
Bulk Densities: It is the mass of the material per unit volume including pores. For the same kind of refractory, the bulk density can vary. The higher is the bulk density, the lesser will be the porosity and normally more will be the mechanical strength.
Specific Gravity: All different refractory minerals have different densities. They can be identified by their specific gravities. The specific gravity of a refractory can be determined by making powder of the sample of a specific size and using a specific gravity bottle and a balance.
Refractories are subjected to extreme temperatures and conditions. This is also a test of their mechanical properties. Some of the key mechanical properties of a refractory are:Cold Crushing StrengthModulus RuptureModulus of ElasticityFractureAbrasion Resistance
Factors Affecting the Maintenance of Refractories
Among kiln operators, refractory failure is considered the most critical upset in a kiln operation. Refractory failure inside the rotary kiln is indicated when the kiln shell becomes red hot because the refractory lining has either been entirely lost or has become so thin in an area that the kiln shell becomes overheated.
In most instances, however, damage can be avoided if the kiln is shut down for lining replacement as soon as the shell starts to show a large red spot.
Replacement of the kiln lining, especially in the burning zone, is unfortunately a frequent necessity, exerting a large strain on the operating budget and on production schedules.
Many plants have found that refractory life is often directly proportional to the number of kiln shutdowns that were experienced while the refractory was in the kiln. The more shutdowns and kilns stop, the shorter the life. The danger of damaging the refractory is directly related to the rate of cooling of the kiln, the danger being the greatest when cooling is too rapid.
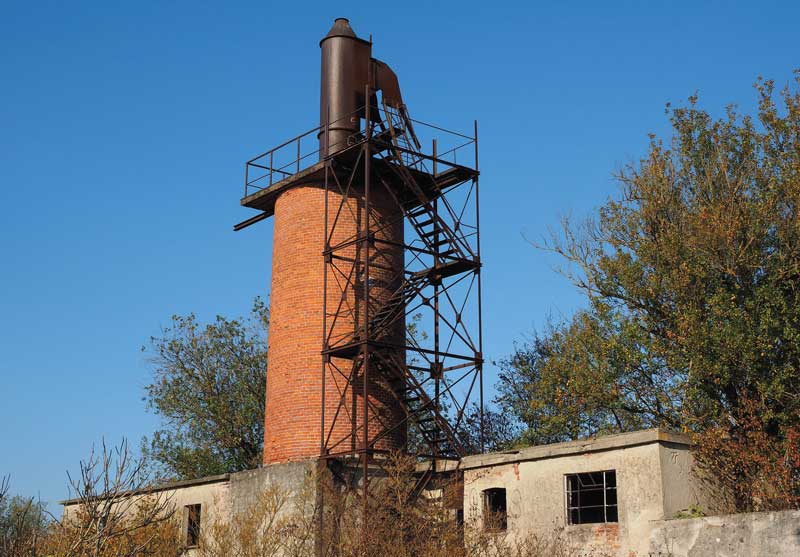
The first step in preventing this situation is to eliminate shutdowns by operating the kiln more efficiently on a continuous basis. The second step is to make sure that cooling is slow and uniform when the kiln is shut down. Cooling time should be a minimum of 8 hours or longer. Placing a large guillotine damper to seal the kiln exit (back-end) helps to conserve heat inside the kiln and retards cooling during a shutdown. Another method of ensuring slow cooling of the refractory in the kiln is to shut the draft fan immediately when the fire is taken out of the kiln.
The primary air fan should be left running only for such a time as needed to protect the burner pipe from heat during the early period of kiln cooling.
As rapid cooling can cause damage to the refractory, so can rapidly heating it. Heating up the refractory quickly can cause thermal deterioration of the brick. Governed partly by the concept of thermal conductivity of the refractory, the kiln shell expansion takes place slower than the bricks. Because of this, the heating process should be for a minimum of 16 hours and should be gradually built up.
Another important factor to be considered for the longevity of the refractory life is to avoid overheating it. This can be ensured by constant monitoring of the kiln temperature and taking corrective action if the temperature rises beyond the threshold.
Having the refractory installed uniformly and in a shapely manner as per the kiln and end product requirement prevents its wear and tear when exposed to high temperature and erosive conditions. Kiln managers should also select the right type of refractories for each location of the kiln which is easier said than done.
Building the right refractory is a key process in the cement manufacturing process as this protective layer of the kiln withstands high temperature and handles the process of converting limestone to clinker and its cooling. Having the right shape, size and composition of refractory in the manufacturing unit increases the overall productivity and efficiency of the cement manufacturing process, thus, also increasing the profitability of the organisation at large. Paying keen attention to its installation and maintenance is important and must be done on a regular basis under expert guidance.
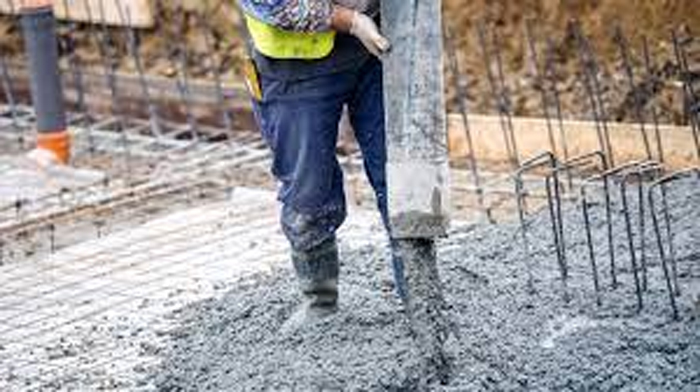
Tamil Nadu is set to host one of India’s five national carbon capture and utilisation (CCU) testbeds, aimed at reducing CO2 emissions in the cement industry as part of the country’s 2070 net-zero goal, as per a news report. The facility will be based at UltraTech Cement’s Reddipalayam plant in Ariyalur, supported by IIT Madras and BITS Pilani. Backed by the Department of Science and Technology (DST), the project will pilot an oxygen-enriched kiln capable of capturing up to two tonnes of CO2 per day for conversion into concrete products. Additional testbeds are planned in Rajasthan, Odisha, and Andhra Pradesh, involving companies like JK Cement and Dalmia Cement. Union Minister Jitendra Singh confirmed that funding approvals are underway, with full implementation expected in 2025.
Image source:https://www.heavyequipmentguide.ca/
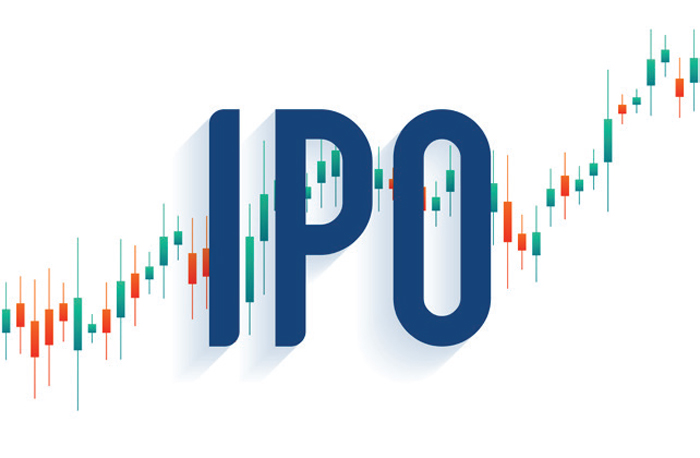
JSW Cement has set the price range for its upcoming initial public offering(IPO) at US$1.58 to US$1.67 per share, aiming to raise approximately US$409 million. As reported in the news, around US$91 million from the proceeds will be directed towards partially financing a new integrated cement plant in Nagaur, Rajasthan. Additionally, the company plans to utilise US$59.2 million to repay or prepay existing debts. The remaining capital will be allocated for general corporate purposes.
Concrete
Cement industry to gain from new infrastructure spending
Published
1 month agoon
July 24, 2025By
admin
As per a news report, Karan Adani, ACC Chair, has said that he expects the cement industry to benefit from the an anticipated US$2.2tn in new public infrastructure spending between 2025 and 2030. In a statement he said that ACC has crossed the 100Mt/yr cement capacity milestone in April 2025, propelling the company to get closer to its ambitious 140Mt/yr target by the 2028 financial year. The company’s capacity corresponds to 15 per cent of an all-India installed capacity of 686Mt/yr.
Image source:https://cementplantsupplier.com/cement-manufacturing/emerging-trends-in-cement-manufacturing-technology/