Concrete
Today, managing energy is a full time job
Published
3 years agoon
By
admin
Jamshed N Cooper, Managing Director, HeidelbergCement India Ltd. and Zuari Cement, looks at energy consumption across various areas of cement production while emphasising the need to measure energy usage in terms of consumption vis-a-vis the cost per unit.
What kind of innovations in the area of energy consumption do you wish to see in the cement industry?
In cement manufacturing process, maximum energy is consumed at the clinkering stage. Electrical energy ranges from 50 to 80 units and thermal energy ranges from 2.9 to 3.25 GigaJoule per tonne. Therefore, clinkering stage is the one that becomes the focus of attention when it comes to adopting new technologies. Cement companies are always on a lookout for energy efficient kilns that are capable of operating with a combination of fuel mix and low on energy consumption. Resultant benefit also flows in by way of low CO2 generation.
To achieve economies of scale, mass continuous production needs to be achieved. For example, a million tonne kiln in today’s time is termed as an energy guzzler. As a thumb rule, a kiln of 5500 TPD is now the entry level. The general trend is to flog kilns of 5,000 TPD to deliver 6,000 TPD at the same time keeping MTBF (Mean Time Between Failure) at maximum, one would be able to optimise energy consumption.
Significant development has happened during the years and now we have fourth generation cross bar coolers which are energy efficient. Another potential area to reduce energy is by deploying VFDs in an optimal manner. Since VFDs are costly, payback analysis on case to case basis should be taken up and replacement of direct drives to be prioritised with a goal to do away with less efficient equipment.
Post clinkering, it’s the grinding stage that consumes a good amount of electrical energy. The industry has worked upon this area and have succeeded in implementing solutions to reduce energy consumption.
At one point of time, cement grinding used to take up to 50 to 60 units of power. The latest energy efficient mills we separator are able to grind clinker consuming as low as 20 to 25 units of energy.
Deployment of vertical roller mills (VRM) and prepress roller mills have led to productivity enhancement and reduced energy consumption on per ton output.
Use of AFR (Alternative Fuel Resource), is yet another avenue available to the cement industry to reduce its thermal energy cost and reduce CO2 footprint. Although, the heat requirement for the pyro-process remains the same, energy substituted from AFR has good potential in reducing costs. Power generation from waste heat recovery (WHR). has come a long way and the cement industry has wisely adopted this technology gainfully.
The drive to reduce energy consumption by the cement industry is now compelling us to embrace digital technology. Digitalisation is fast catching up in the cement industry and is becoming the harbinger in the area of energy optimisation and reduction of CO2 footprint.
How does automation and technology help in optimising the use of energy in cement plants?
Talking about automation, earlier we used to have a significant human interface for plant operations. For example, highly skilled workmen called “Burners” were required for operating kilns. These workmen used their experienced based judgement for controlling the kiln fuel to the kiln by watching the condition of the flame. Today, all of this is controlled from the Central Control Room (CCR) using state of the art digital technology making it possible to monitor plant operations with deft accuracy and speed At HeidelbergCement, we use Px Trends – a system that gathers system data and does trend analysis based on which it provides solutions to the operators for controlling various equipment. The big data gathered over the years offers immense potential to deploy Artificial Intelligence (AI) engines and optimise various operating parameters in real time automatically. Cement manufacturing deals with large volumes of raw materials and this compromises accuracy when it comes to measurement in real time. Given the volumes processed every minute, it’s humanly not possible to regulate their flows with accuracy nor easy to predict accurately the quality of raw materials being mined. By digitalising, we have created processes and methodologies custom built by HeidelbergCement that facilitate optimisation of fuel and energy.
HeidelbergCement Group has also invested in IT companies with a long term aim to digitalise its operations and become future ready. Our Group is relentlessly working to deploy digital technology as we believe that it holds the key to a better future. Remote management of our cement mills is one such example deployed in India to achieve improved productivity and control of the processes.
What is the energy consumption in one cycle of cement manufacturing process? Which process is the most energy intensive?
On average, the electrical energy consumption for producing a tonne of cement ranges from 60 units to 90 units and is dependent on the type of cement produced and the technology deployed. In the same company, there could be multiple kilns and processes installed over different time horizons and the energy consumption for the same would not be similar. The latest technologies bank on large production lines that deliver optimal energy efficiency and would consume about 60 to 65 units.
What are the major challenges your organisation faces in managing the energy needs of the cement manufacturing process?
In today’s times and especially since the fuel prices have more than tripled, managing energy has become a fulltime job. Energy which used to constitute about 30 per cent of the manufacturing cost has now become close to 45 per cent. Therefore, managing our energy needs becomes one of the bigger challenges for us and the industry as well. HeidelbergCement has developed several ways to manage its energy needs and deploy customised systems that have been developed by the Group.
Energy consumed to manufacture a tonne of cement is measured in Kcal or Giga Joules but more relevant is how do we achieve the lowest cost per Kcal or Gj. It therefore becomes prudent to manage the fuel mix based on its landed cost at the plant. To be able to optimise the energy consumption and its cost, we constantly evaluate and keep altering our fuel recipes.
On one hand is the cost of various fuels and on the other is its consumption. In the cement manufacturing process, a lot of heat is lost if thermal radiation is not contained. “Heat Contained is Heat Saved”. Periodic and astute maintenance schedules not only hold the key to improve plant availability but go a long way in reducing energy consumption.
We constantly endeavor to replace fossil fuels with AFR and maximise power generation from WHR. Replacing high cost grid power with low cost renewable power such as solar and wind have remained in sharp focus for HeidelbergCement India. Over a period of the last few years, we have been able to reduce our energy consumption by upgrading the plant and machinery in our plants.
How does energy conservation impact the profitability of the organisation? What impact does it have on the productivity of the process?
As I mentioned, reduction in energy consumption results in reduction of manufacturing costs as well and adds to the bottom line. Replacing high cost conventional energy sources with WHR and low renewable energy sources helps us save enough to be able to invest and adapt to newer technologies. It’s a self-fulfilling cycle that improves the competitive advantage which in the Indian context is a necessity for survival and growth.
Productivity and Energy efficiency go hand in hand and every employee in our organisation understands this. Drop in productivity of any equipment gets reflected in terms of higher energy consumption per unit of cement produced. For example, a kiln of 5,000 TPD if operated to deliver an output of 5800 TPD clinker, the incremental energy requirement will be marginally higher in relation to the energy consumed when operated at 5000 TPD.
With oil prices shooting through the roof, what has been its impact on the cement industry?
Escalated fuel cost has dealt a severe blow to the cement industry. Fuel related costs have added the most to our woes. The costs have gone up by 20 per cent to 30 per cent during the last two years and continue to rise unabated. Due to overhang of capacity and intense competition, the cement industry has not been able to pass on the price increases to the consumers.
In December 2020, pet coke prices were about $50 per tonne. Today the same is close to US$ 220 which makes the increase 3x of what it was. Today imported coal is hovering in the range of US$195 to $200 per tonne. Looking at the geopolitical situation and the state of economies across the globe, it does not seem that fuel prices would relent much in the coming year or so.
While industry continues to strive and contain its costs by deploying efficient technologies, it has its limitations. The cost savings thus achieved fall significantly short when it comes to matching the pace at which raw material costs have been increasing.
The recent past declared quarterly financial results of cement companies, makes it obvious that if the industry fails to pass on the cost increases to the customers, it could have a debilitating effect on the foreseeable future of the industry.
What are the major compliances and standards for efficiently handling fuel and energy in the organisation?
The statutory compliances to be fulfilled by cement manufacturers are well defined by the respective Government agencies. When it comes to improving energy efficiencies, we have to achieve the targets under the PAT cycle. We have been witnessing over the years as to how the PAT cycle has shaped the industry’s approach to becoming energy efficient.
A few of the environmental compliances in India are more stringent than those applicable in developed economies. Nevertheless, the Indian Cement Manufacturers have time and again demonstrated their commitment to meet all the norms and standards laid down by the MoEF. As a good corporate citizen, we at HeidelbergCement take pride in ensuring total compliance with the laws of the land and the industry.
How often are audits done to ensure optimum use of energy and what is the suggested duration for the same?
We undertake all requisite audits periodically and file our reports as required under the law. As a responsible corporate, we do our own energy audits as well.
We believe in the philosophy of “Continuous Improvement”. Besides our internal standards, we benchmark our performance with our past best achievements and also that of our competitors and replicate the same. We strive to become better than the previous year.
At our India operations, we pursue a target to achieve a two-degree lower ambient temperature in our plants compared to than prevailing a Km away.
This journey we commenced in 2014 and now two of our cement plants have achieved the goal and the remaining ones are close to emerging winners. The average reduction for all our units operating in India now stands at 1.4 degree Celsius lower. This act of ours has led to creation of a cooler work environment and is resulting in higher productivity.
How have been the carbon emission norms for the cement industry in India vis-à-vis the World? What percentage of your carbon emission reduction target are you set to achieve by 2030?
The CO2 emission by the cement industry worldwide in 2018-19 reduced to 640 kg per tonne of cement from 760 kg per tonne in 1990 thereby recording a significant reduction of 16 per cent. At our India operations, we take pride in having achieved 585 kg CO2 per tonne of cement in 2018-19 from a level of 800 kg per tonne in 1990.
During FY 2021, CO2 emissions for our India operations stood at 570 kg per tonne of cement and now we strive to further reduce it to 550 kg by 2025. By 2030, we have the ambition to touch 534 kg CO2. In Central India, we manufacture 100 per cent blended cement with a CO2 footprint of 510 kg per tonne of cement pursuing a target to further reduce it to 495 kg by 2030. The group is pushing us to achieve this target and compete at Global levels.
CO2 emissions while manufacturing Cement is inevitable. When we say that we are going to achieve carbon neutrality, it implies that going forward deploying carbon capture or utilisation will come into play.
HeidelbergCement Group is poised to emerge as a pioneer in the cement industry as it continues to build the first of its king state of art carbon capture units in Norway. A delegation comprising members of DPIIT and NCCBM, visited the establishment to witness the same.
HeidelbergCement Group is working on close to eight carbon capture technologies which are at various Technological Readiness Levels (TRLs).
These include processes like post combustion, oxy fuel, lilac technology, direct separation, micro algae, hydrogen burning and kiln electrification. These pioneering efforts of our Group are poised to become a boon for the cement industry and the society as well.
Our slogan “Materials to Build Our Future” energises us day after day to renew our commitment to “making the world a wonderful place to live for our generations to come”.
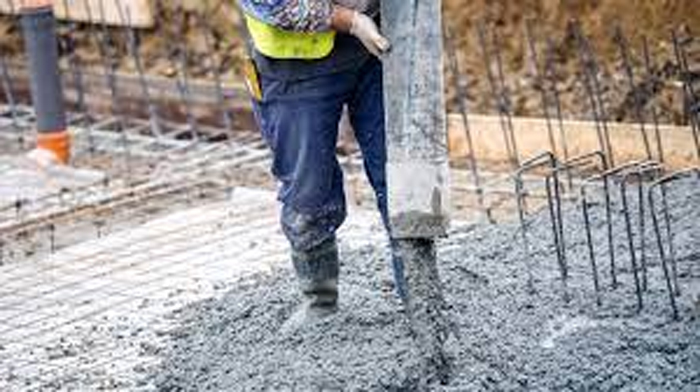
Tamil Nadu is set to host one of India’s five national carbon capture and utilisation (CCU) testbeds, aimed at reducing CO2 emissions in the cement industry as part of the country’s 2070 net-zero goal, as per a news report. The facility will be based at UltraTech Cement’s Reddipalayam plant in Ariyalur, supported by IIT Madras and BITS Pilani. Backed by the Department of Science and Technology (DST), the project will pilot an oxygen-enriched kiln capable of capturing up to two tonnes of CO2 per day for conversion into concrete products. Additional testbeds are planned in Rajasthan, Odisha, and Andhra Pradesh, involving companies like JK Cement and Dalmia Cement. Union Minister Jitendra Singh confirmed that funding approvals are underway, with full implementation expected in 2025.
Image source:https://www.heavyequipmentguide.ca/
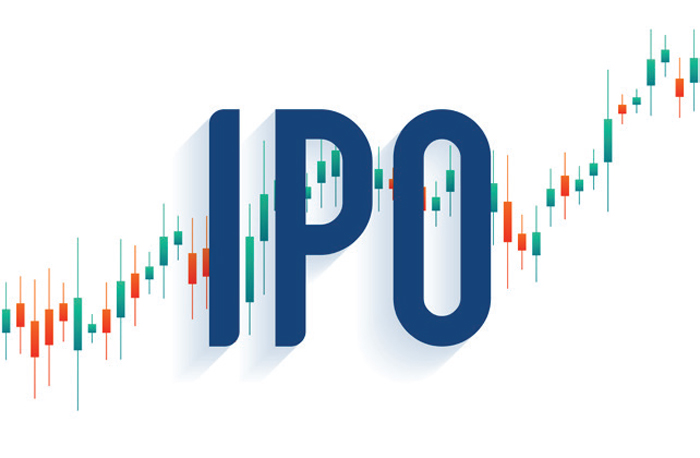
JSW Cement has set the price range for its upcoming initial public offering(IPO) at US$1.58 to US$1.67 per share, aiming to raise approximately US$409 million. As reported in the news, around US$91 million from the proceeds will be directed towards partially financing a new integrated cement plant in Nagaur, Rajasthan. Additionally, the company plans to utilise US$59.2 million to repay or prepay existing debts. The remaining capital will be allocated for general corporate purposes.
Concrete
Cement industry to gain from new infrastructure spending
Published
1 month agoon
July 24, 2025By
admin
As per a news report, Karan Adani, ACC Chair, has said that he expects the cement industry to benefit from the an anticipated US$2.2tn in new public infrastructure spending between 2025 and 2030. In a statement he said that ACC has crossed the 100Mt/yr cement capacity milestone in April 2025, propelling the company to get closer to its ambitious 140Mt/yr target by the 2028 financial year. The company’s capacity corresponds to 15 per cent of an all-India installed capacity of 686Mt/yr.
Image source:https://cementplantsupplier.com/cement-manufacturing/emerging-trends-in-cement-manufacturing-technology/