Environment
Composite cement helps conserve our natural resources
Published
7 years agoon
By
admin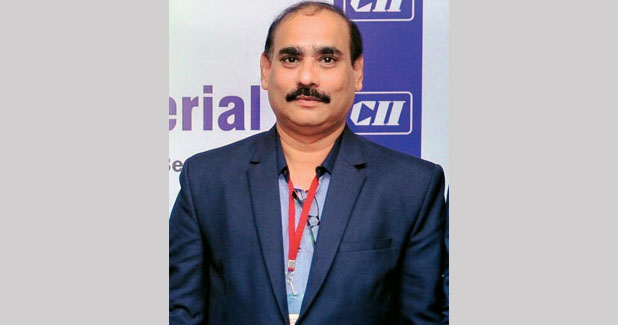
Do you still see a preference for OPC in certain segments of the cement market such as institutional or in certain geographies? How do you deal with these national preferences?
Yes. OPC cement commands preference in certain geographic markets and institutional segment in comparison to trade segment. This preference is predominantly in institutional segment due to faster setting time and better compressive strength over PPC/PSC cement. OPC Grade 43 / 53 are more preferred in infrastructure projects and have emerged as the top choice of engineers and engineering companies engaged in construction of mega projects – such as national highways, bridges, transmission lines, power plants, industrial and residential structures. Also in major infrastructure projects OPC Grade 43 / 53 is approved through central/State Government/local governing bodies/institutions over PPC/PSC, making OPC preferred product in institutional segment.
Another reason why OPC is preferred over PPC / PSC is because in certain geographies or markets availability/supply of fly ash and slag is a constraint due to location of power and steel plant because of which supply of PPC/PSC cement is very limited hence people go for OPC cement more. Some of its properties like higher strength and faster setting the consumers consider that OPC cement is better over PPC and PSC.
What is your company’s overall product mix – OPC, PPC and PSC? To what extent is this mix is influenced by market preferences and to what extent by availability of fly ash and/or slag?
At Nuvoco, we are committed to sustainability and hence our product mix is skewed towards PPC and PSC cement than OPC. The product mix is primarily based on the preferences of the consumer as well as geographic locations. In certain market consumer preferences are driven by color of cement thought it does not have an impact on its properties. In some markets consumers prefer to use darker cement i.e. PPC while in other market they opt for PSC cement as it is lighter in shade. Whereas in certain market consumer prefer OPC cement. Simultaneously, the customer prefer to go with a particular type of cement be it OPC, PSC or PPC based on the supply / availability in that particular market because if the customer is building his own house then he would not like to wait for a particular type thereby increasing the wait time.
Availability of fly ash and slag is another factor, which affects the availability of various cement grades. Basis the location of steel and power plants, fly ash and slag is available. Not only this cement plants should also be strategically located so that both these materials are readily available to manufacture PPC and PSC cement. To overcome this hurdle many cement companies are entering into long term supply agreement with various steel and power plants to get an uninterrupted supply of these raw materials.
How do you view the historical growth rates of PSC & PPC in your markets? How do you project this growth in coming five years?
Historically ever since government allowed blending of cement with OPC there has been continuous growth in the sales of PSC / PPC cement. There has been a very good penetration of blended cements in the market. Earlier OPC used to be the market leader in India. However, today, it represents only about 20-25 per cent of the market share. In this context, it is encouraging to note that nearly 75 per cent of cement production in India at present is in the form of blended cement of various types, as against only 30 per cent in 1999-2000. We are committed towards the preservation of natural resources and in that context we have put major thrust on using blended cements like PPC and PSC.
In order to promote a sustainable future, cement companies should pass on cost benefits and the government must provide incentives along with compulsory use of blended cement in all government projects. Since blended cement uses factory waste, a by-product, as its raw material, it is important for environmental reasons that we maximize the use of PPC / PSC and move towards a greener path.
Major companies are migrating from traditional OPC (approximately 95 per cent clinker) towards alternative types of cements such as fly ash based (approximately 75 per cent clinker) or recently growing composite cement which is a mixture of slag as well as fly ash (approximately 65 to 70 per cent clinker) thus not only reducing the carbon emission due to manufacturing process of clinker but also using materials, which were earlier disposed from carbon intensive sectors like power and steel. With the growing awareness towards environmental issues and the internal target of large cement manufacturers to increase the share of alternative fuels, the share of alternative fuels would increase to around 10 per cent and contribution from traditional fuels is going down.
What are the applications or regions where you would recommend use of PPC/PSC to your customers and why?
Selection of a particular grade of cement is almost always based on the type of concrete, which will be used for construction so as to ensure durability of the structure. Thus, making wise choice of cement type for particular construction site prevents structure from deteriorating and saves much repair and rehabilitation cost later.
PSC and PPC cement is suitable for high rainfall areas and coastal areas as these offer higher longevity of structures. As PSC / PPC are left with very little lime after complete hydration reaction they offer highest resistance against sulphate and chloride attacks and environmental pollutants.
Applications of Portland Slag Cement (PSC) – It is OPC + granulated slag cement. It gives low heat of hydration. The slag should be more than 50 per cent and up to 70 per cent. It is used for:
Marine and off shore structures – very high chloride and sulphate resistant.
Sewage disposal treatments works
Water treatment plants
Constructions which are expected to be attacked by dissolved chlorides and sulphate ions.
Should be mainly used for all future structures.
Applications of Portland Pozzolana Cement (PPC) – It gives low heat of hydration and reduces the leaching of calcium hydroxide. Thereby PPC is prone to fewer cracks and reduced shrinkage, better workability and finishing (as fly ash based cement are spherical in shape and finer in size). It is used for:
Hydraulic structures – dams, retaining walls
Marine structures
Mass concrete works – like bridge footings
Under aggressive conditions
Masonry mortar and plastering
We have heard a lot about peculiar customer perceptions about colour and smell of cement in some markets? Have you experienced this phenomenon? Are these related to presence of slag/fly ash in cement? How do you deal with such idiosyncratic ideas?
Yes, customers in different geographies of our country have peculiar understanding towards the colour and smell of cement, however both has nothing to do with the quality of cement.
Colour of cement varies from dark to light due to the cementitous blends (fly ash / slag). Fly ash – a by-product from thermal power plant is used in producing PPC. This fly ash consists of traces of unburnt carbon and other impurities hence PPC is darker in colour. GGBS (Ground Granulated Blast furnace Slag) is off white in colour, which is used in producing PSC. Hence the colour of PSC is lighter. In certain geography lighter colour has advantages as darker colour and vice versa.
The colour of PPC containing fly ash as pozzolana will invariably be of slightly different colour than that of OPC, depending on the colour of the pozzolonic fly ash that is used in the manufacture. However, the colour of cement, whether it is PPC / PSC or be any other grade, has no relationship with the quality of cement. The colour of the cement is gauged by its C4AF content and the pozzolonic material used. The higher the C4AF the darker the cement will be. Similarly, the lighter the colour of pozzolonic material, the lighter the shade of the cement. As such, there is no governing specification for the colour of cement. One cannot gauge the quality of cement by looking at its colour. The quality of cement can be assessed only by testing its physical and chemical properties.
Traditionally basis availability of PPC / PSC cement and its usage, end user/mason/engineers have developed the perception that cement quality is dependent upon colour which is a myth. Basis our PPC / PSC product availability in different market, we conduct lots of customer engagement programmes, mason/engineers/architect meets to create awareness on the quality of product. We provide sampling at customer site and after sales service to resolve complains (if any). Our innovative product are tested at our research centre, i.e., CIDC and we provide customer with our quality test reports to convince them on the quality of cement.
Recently BIS have permitted composite cements to be manufactured and sold in India. What is your strategy for introducing this product in the market and what are the manufacturing and marketing challenges involved in this?
Composite cement is covered under IS: 16415-2015 and is best suited cement to produce high strength concrete, which is highly durable. Composite cement is a mixture of high quality clinker, fly ash, granulated slag and gypsum.
Composite cement offers better opportunity to conserve natural resources in terms of limestone by replacing higher percentage of clinker, having lower carbon footprint without compromising on concrete properties in green and hardened state. The finding of this study might be useful to accept composite cement for different concrete applications in construction.
Plants that are already making blended cements can easily and conveniently make composite cements. For example, those that are making PPC can add a hopper and feeder for limestone powder. Those that are making PPC can arrange to add slag, and vice versa. The proportions of the third component to be added, whether slag, fly ash or limestone, have to be decided in consultation with research institutes and in accordance with prevailing (or forthcoming) standards for composite cements.
The major challenge is making arrangements to store the different types of cement manufactured in a single plant. Configuration of mills making these cements and corresponding silos for storage would have to be worked out carefully, taking into account the volume and consistency of demand for each type of cement produced. For small and infrequent demands a multi-compartment silo could be used to store different types of cement. Again, factors like: dispatches by road and or rail and their respective volumes, dispatched in bag or in bulk would have to be taken into account in planning the overall layout of cement grinding, storage, and dispatch sections. Thus a layout would have to be worked out specifically for each plant to meet its requirements. These are the current challenges in aligning different activities for production of composite cement.
On marketing front awareness and acceptability with customer pose immediate challenges. However we understand these could be addressed by different activities we conduct to build the connection with our customers. Other challenge will be to get the product approved from different government agencies and passing the quality test.
The supply chain of both fly ash and slag has now become an integral part of cement manufacturer. In the light of this how do you see the current demand and supply scenarios of these two commodities. Fly ash and slag? What are the price movements of these two commodities? Are you recommending any regulatory help in ensuring more liberal supply of fly ash?
Coal/lignite based thermal power generation has been the backbone of power capacity addition in the country. Indian coal is of low grade with ash content of the order of 30-45 per cent in comparison to imported coals which have low ash content of the order of 10-15 per cent.
Several number of coal/lignite based thermal power plant is setup for providing electric to rapidly growing industrial as well as agriculture sectors. 70 percent of the electricity generated in India is from coal based thermal plant. The generation of coal fly ash is anticipated to increase for many more years, as a result of the increasing reliance on coal-fired power generation. Large quantity of ash is, thus being generated at coal/lignite based thermal power stations in the country, which not only requires large area of precious land for its disposal but is also one of the sources of pollution of both air and water. To reduce the problem caused by production of fly ash, it is now mandatory to use fly ash based products like cement.
Steel slag, a by-product of steel making, is produced during the separation of the molten steel from impurities in steel-making furnaces. The slag occurs as a molten liquid melt and is a complex solution of silicates and oxides that solidifies upon cooling. Virtually all steel is now made in integrated steel plants using a version of the basic oxygen process or in specialty steel plants (mini-mills) using an electric arc furnace process. The open hearth furnace process is no longer used. There has been continuous growth in steel industry due to increase demand in infrastructure development, real estate industry, etc.
With the increase in generation of by product from these industries, there dumping has always been an issue for these industries. Both by products are used in blending of cement to produce PPC and PSC cement. Logistics movement of both the by-product has been a challenge. Hence cement plant is ideally set up near to these industries. Logistics cost for movement of clinker is always lower compared to cost for movement of fly ash and slag. Cement industry go for a long term association with these industries for continuous supply of by-products.
You may like
-
It is equally important to build resilient building structures
-
Efficient Processes for a Better Tomorrow
-
Stud technology has proven to be a boon for the industry
-
Brand differentiation happens at every touch point
-
Achieving Net Zero goals is a complex and long-term process
-
The consistent goal in the cement industry is to use fewer natural resources
Concrete
India donates 225t of cement for Myanmar earthquake relief
Published
3 months agoon
June 17, 2025By
admin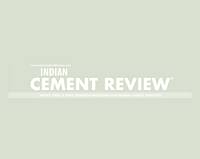
On 23 May 2025, the Indian Navy ship UMS Myitkyina arrived at Thilawa (MITT) port carrying 225 tonnes of cement provided by the Indian government to aid post-earthquake rebuilding efforts in Myanmar. As reported by the Global Light of Myanmar, a formal handover of 4500 50kg cement bags took place that afternoon. The Yangon Region authorities managed the loading of the cement onto trucks for distribution to the earthquake-affected zones.
Concrete
Reclamation of Used Oil for a Greener Future
Published
3 months agoon
June 16, 2025By
admin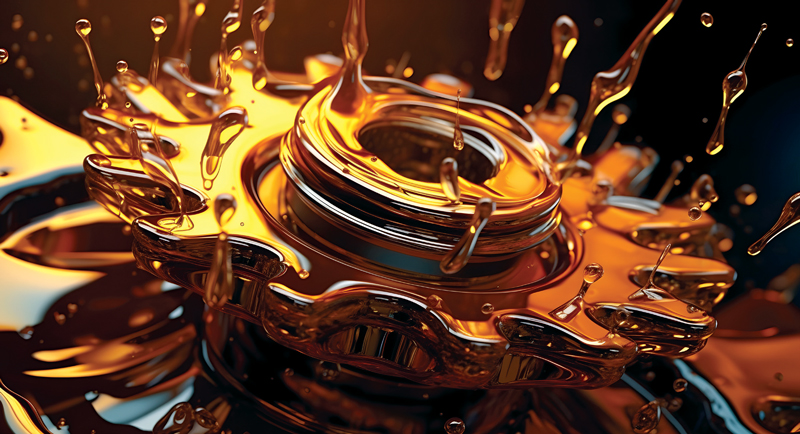
In this insightful article, KB Mathur, Founder and Director, Global Technical Services, explores how reclaiming used lubricants through advanced filtration and on-site testing can drive cost savings, enhance productivity, and support a greener industrial future. Read on to discover how oil regeneration is revolutionising sustainability in cement and core industries.
The core principle of the circular economy is to redefine the life cycle of materials and products. Unlike traditional linear models where waste from industrial production is dumped/discarded into the environment causing immense harm to the environment;the circular model seeks to keep materials literally in continuous circulation. This is achievedthrough processes cycle of reduction, regeneration, validating (testing) and reuse. Product once
validated as fit, this model ensures that products and materials are reintroduced into the production system, minimising waste. The result? Cleaner and greener manufacturing that fosters a more sustainable planet for future generations.
The current landscape of lubricants
Modern lubricants, typically derived from refined hydrocarbons, made from highly refined petroleum base stocks from crude oil. These play a critical role in maintaining the performance of machinery by reducing friction, enabling smooth operation, preventing damage and wear. However, most of these lubricants; derived from finite petroleum resources pose an environmental challenge once used and disposed of. As industries become increasingly conscious of their environmental impact, the paramount importance or focus is shifting towards reducing the carbon footprint and maximising the lifespan of lubricants; not just for environmental reasons but also to optimise operational costs.
During operations, lubricants often lose their efficacy and performance due to contamination and depletion of additives. When these oils reach their rejection limits (as they will now offer poor or bad lubrication) determined through laboratory testing, they are typically discarded contributing to environmental contamination and pollution.
But here lies an opportunity: Used lubricants can be regenerated and recharged, restoring them to their original performance level. This not only mitigates environmental pollution but also supports a circular economy by reducing waste and conserving resources.
Circular economy in lubricants
In the world of industrial machinery, lubricating oils while essential; are often misunderstood in terms of their life cycle. When oils are used in machinery, they don’t simply ‘DIE’. Instead, they become contaminated with moisture (water) and solid contaminants like dust, dirt, and wear debris. These contaminants degrade the oil’s effectiveness but do not render it completely unusable. Used lubricants can be regenerated via advanced filtration processes/systems and recharged with the use of performance enhancing additives hence restoring them. These oils are brought back to ‘As-New’ levels. This new fresher lubricating oil is formulated to carry out its specific job providing heightened lubrication and reliable performance of the assets with a view of improved machine condition. Hence, contributing to not just cost savings but leading to magnified productivity, and diminished environmental stress.
Save oil, save environment
At Global Technical Services (GTS), we specialise in the regeneration of hydraulic oils and gear oils used in plant operations. While we don’t recommend the regeneration of engine oils due to the complexity of contaminants and additives, our process ensures the continued utility of oils in other applications, offering both cost-saving and environmental benefits.
Regeneration process
Our regeneration plant employs state-of-the-art advanced contamination removal systems including fine and depth filters designed to remove dirt, wear particles, sludge, varnish, and water. Once contaminants are removed, the oil undergoes comprehensive testing to assess its physico-chemical properties and contamination levels. The test results indicate the status of the regenerated oil as compared to the fresh oil.
Depending upon the status the oil is further supplemented with high performance additives to bring it back to the desired specifications, under the guidance of an experienced lubrication technologist.
Contamination Removal ? Testing ? Additive Addition
(to be determined after testing in oil test laboratory)
The steps involved in this process are as follows:
1. Contamination removal: Using advanced filtration techniques to remove contaminants.
2. Testing: Assessing the oil’s properties to determine if it meets the required performance standards.
3. Additive addition: Based on testing results, performance-enhancing additives are added to restore the oil’s original characteristics.
On-site oil testing laboratories
The used oil from the machine passes through 5th generation fine filtration to be reclaimed as ‘New Oil’ and fit to use as per stringent industry standards.
To effectively implement circular economy principles in oil reclamation from used oil, establishing an on-site oil testing laboratory is crucial at any large plants or sites. Scientific testing methods ensure that regenerated oil meets the specifications required for optimal machine performance, making it suitable for reuse as ‘New Oil’ (within specified tolerances). Hence, it can be reused safely by reintroducing it in the machines.
The key parameters to be tested for regenerated hydraulic, gear and transmission oils (except Engine oils) include both physical and chemical characteristics of the lubricant:
- Kinematic Viscosity
- Flash Point
- Total Acid Number
- Moisture / Water Content
- Oil Cleanliness
- Elemental Analysis (Particulates, Additives and Contaminants)
- Insoluble
The presence of an on-site laboratory is essential for making quick decisions; ensuring that test reports are available within 36 to 48 hours and this prevents potential mechanical issues/ failures from arising due to poor lubrication. This symbiotic and cyclic process helps not only reduce waste and conserve oil, but also contributes in achieving cost savings and playing a big role in green economy.
Conclusion
The future of industrial operations depends on sustainability, and reclaiming used lubricating oils plays a critical role in this transformation. Through 5th Generation Filtration processes, lubricants can be regenerated and restored to their original levels, contributing to both environmental preservation and economic efficiency.
What would happen if we didn’t recycle our lubricants? Let’s review the quadruple impacts as mentioned below:
1. Oil Conservation and Environmental Impact: Used lubricating oils after usage are normally burnt or sold to a vendor which can be misused leading to pollution. Regenerating oils rather than discarding prevents unnecessary waste and reduces the environmental footprint of the industry. It helps save invaluable resources, aligning with the principles of sustainability and the circular economy. All lubricating oils (except engine oils) can be regenerated and brought to the level of ‘As New Oils’.
2. Cost Reduction Impact: By extending the life of lubricants, industries can significantly cut down on operating costs associated with frequent oil changes, leading to considerable savings over time. Lubricating oils are expensive and saving of lubricants by the process of regeneration will overall be a game changer and highly economical to the core industries.
3. Timely Decisions Impact: Having an oil testing laboratory at site is of prime importance for getting test reports within 36 to 48 hours enabling quick decisions in critical matters that may
lead to complete shutdown of the invaluable asset/equipment.
4. Green Economy Impact: Oil Regeneration is a fundamental part of the green economy. Supporting industries in their efforts to reduce waste, conserve resources, and minimise pollution is ‘The Need of Our Times’.
About the author:
KB Mathur, Founder & Director, Global Technical Services, is a seasoned mechanical engineer with 56 years of experience in India’s oil industry and industrial reliability. He pioneered ‘Total Lubrication Management’ and has been serving the mining and cement sectors since 1999.
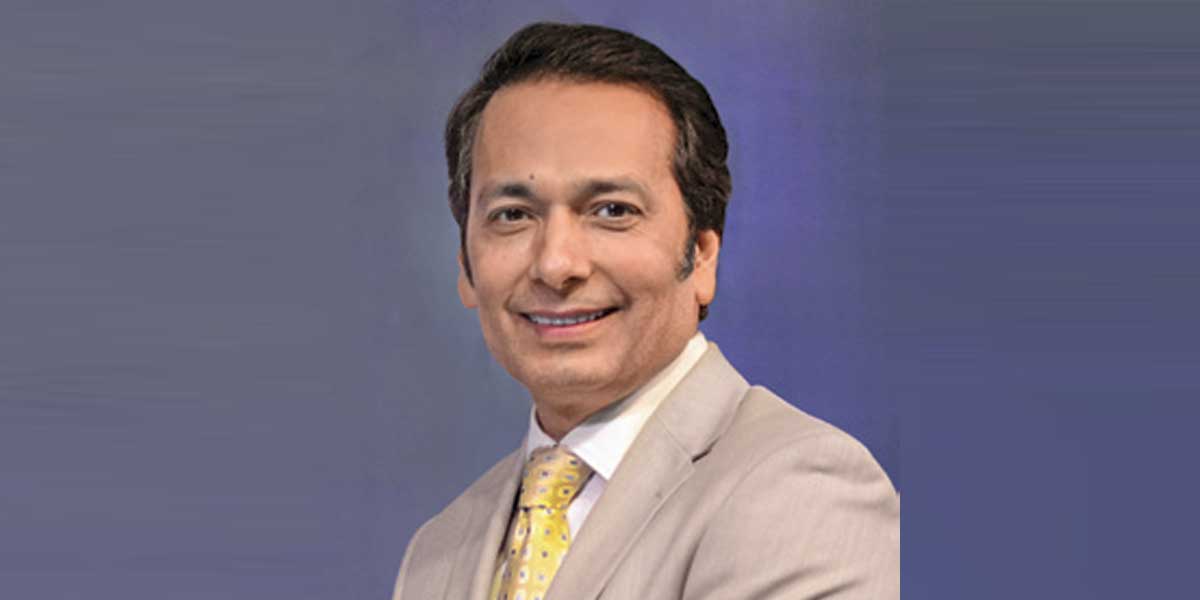
The Indian cement industry has reached a critical juncture in its sustainability journey. In a landmark move, the Ministry of Environment, Forest and Climate Change has, for the first time, announced greenhouse gas (GHG) emission intensity reduction targets for 282 entities, including 186 cement plants, under the Carbon Credit Trading Scheme, 2023. These targets, to be enforced starting FY2025-26, are aligned with India’s overarching ambition of achieving net zero emissions by 2070.
Cement manufacturing is intrinsically carbon-intensive, contributing to around 7 per cent of global GHG emissions, or approximately 3.8 billion tonnes annually. In India, the sector is responsible for 6 per cent of total emissions, underscoring its critical role in national climate mitigation strategies. This regulatory push, though long overdue, marks a significant shift towards accountability and structured decarbonisation.
However, the path to a greener cement sector is fraught with challenges—economic viability, regulatory ambiguity, and technical limitations continue to hinder the widespread adoption of sustainable alternatives. A major gap lies in the lack of a clear, India-specific definition for ‘green cement’, which is essential to establish standards and drive industry-wide transformation.
Despite these hurdles, the industry holds immense potential to emerge as a climate champion. Studies estimate that through targeted decarbonisation strategies—ranging from clinker substitution and alternative fuels to carbon capture and innovative product development—the sector could reduce emissions by 400 to 500 million metric tonnes by 2030.
Collaborations between key stakeholders and industry-wide awareness initiatives (such as Earth Day) are already fostering momentum. The responsibility now lies with producers, regulators and technology providers to fast-track innovation and investment.
The time to act is now. A sustainable cement industry is not only possible—it is imperative.