Concrete
Smart Motion Systems Power Cement Plants
Published
1 month agoon
By
admin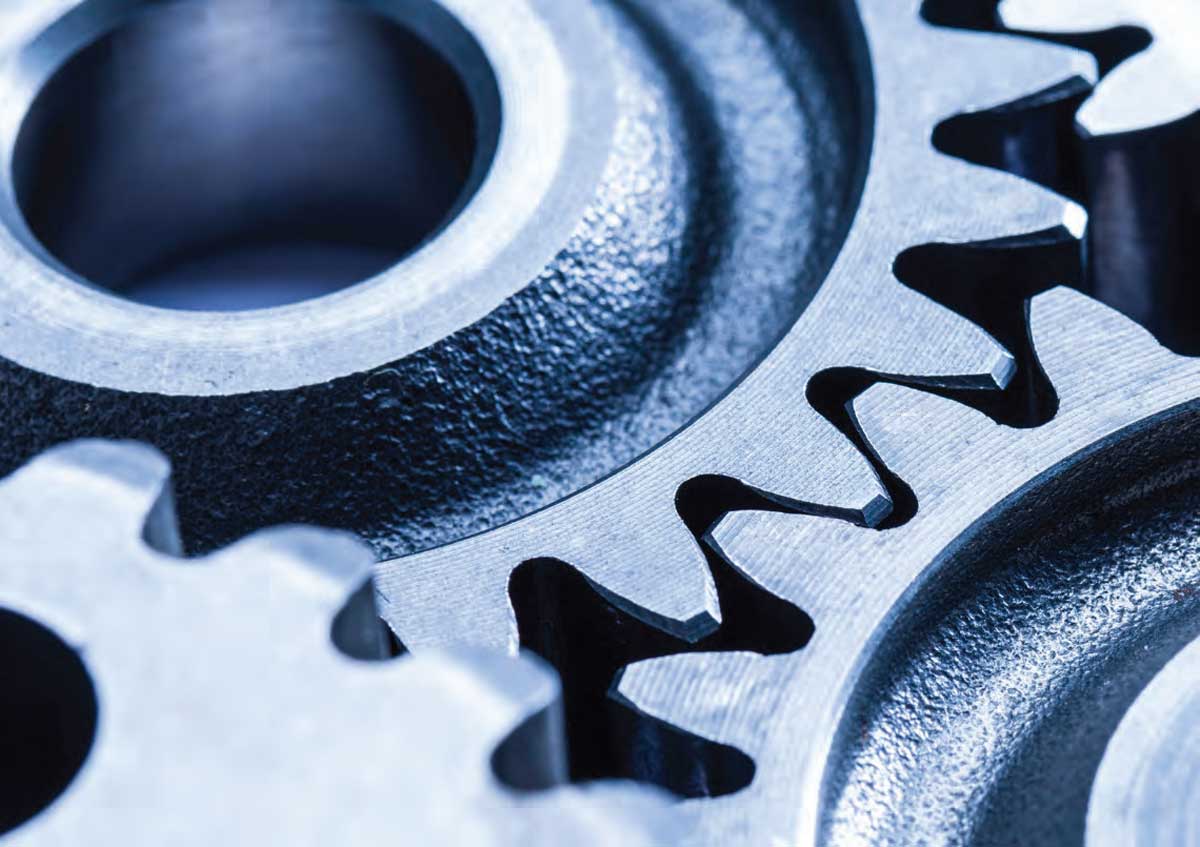
ICR explores how advanced gears, drives, and motors are transforming cement manufacturing by enhancing reliability, reducing energy use, and enabling predictive maintenance. With digitalisation, electrification, and sustainability at the forefront, motion systems now play a strategic role in driving operational excellence and Net Zero goals.
Gears are the unsung workhorses of cement plants, critical to the operation of equipment ranging from crushers and conveyors to milling units and kilns. Built to endure heavy-duty conditions—dust, heat, shock and continuous load—they are often made from carburised, electro-welded steel, precision-ground to withstand high torque and ensure longevity. The failure of a single girth gear or pinion can halt an entire production line, emphasising the importance of quality-focused design and maintenance.
In grinding applications, such as those involving ball mills and vertical roller mills (VRMs), gearboxes play a pivotal role in power transmission. For instance, ring gears and planetary gear systems manage loads up to 8?MW, balancing efficiency with structural resilience. While planetary drives may add a 5 per cent –15 per cent premium over conventional girth-drive systems, their improved lifecycle, reduced maintenance and enhanced control often justify the higher upfront cost.
Gears also facilitate the precise rotation of kilns. Dual-drive systems, each powering pinions on opposite sides of the kiln, ensure balanced torque delivery and smooth operation. This configuration reduces shell distortion, mechanical stress, and vibration, extending component life and reducing unplanned downtime. Regular maintenance, alignment checks and vibration monitoring underpin the reliability of these high-capacity systems.
Innovation continues to advance gear performance. Companies like MAAG Gear and others have embraced high-strength materials, optimised tooth profiles and modular gearbox architectures to improve serviceability and energy efficiency. The coexistence of traditional weld-and-grind gearboxes and modern planetary or gearless drives reflects the balance between proven reliability and future readiness in cement plant design.
Lifecycle costs and return on investment
In capital-intensive industries like cement, the upfront cost of gears, motors and drives is only one piece of the financial puzzle. What truly matters over time is the total cost of ownership (TCO)—including maintenance, energy use, downtime losses and equipment lifespan. High-efficiency gearboxes or premium VFDs may appear costlier initially, but they often deliver far superior ROI through reduced power consumption and longer operational life. For example, using a high-efficiency IE4 motor can save up to 30 per cent in energy costs over a decade compared to IE1-rated models.
Modern procurement is increasingly driven by this lifecycle approach. Maintenance teams, once focused on price, now calculate costs over a 10–15-year horizon. A planetary gearbox with precision-machined gears and sealed lubrication may offer double the life of a conventional pinion system, with 40 per cent fewer breakdowns. When downtime in a cement plant can cost lakhs per hour, these savings become significant. The ability to track and predict maintenance intervals using sensor-based diagnostics only improves financial predictability.
Pradip Kalra, CEO, Stotz Gears, says, “Kiln shells, like other critical cement plant components, are manufactured in accordance with international quality standards. These standards are set by OEMs and well-known across the cement industry. I believe the foundation of delivering high-quality products lies in honesty—honesty towards quality standards, material procurement, and the will to achieve excellence. Personally, I have always repeated to myself: I must achieve it, I must achieve it. That self-motivation and conviction have taken me a long way. Every kiln shell we produce reflects that commitment. We source certified raw materials, maintain stringent manufacturing controls, and ensure precision across every stage. The final product not only meets OEM specifications but also earns the long-term trust of our clients.”
Additionally, energy audits and drive optimisation programs have become key tools in ROI evaluation. By measuring baseline power usage and simulating post-retrofit performance, plant heads can make data-backed investment decisions. For instance, the ROI period for installing VFDs on ID fans or mill motors has dropped from 3 years to under 18 months in many Indian plants, thanks to energy savings and extended motor life.
Some cement companies are also entering into performance-based contracts with OEMs—where vendors guarantee uptime, energy efficiency, or availability, with penalties and bonuses linked to performance. This shifts the focus from product cost to value delivered, and aligns all stakeholders toward plant profitability. Lifecycle thinking is no longer optional—it’s a strategic lens for both capital budgeting and operational optimisation.
Drives and motors: Energy efficiency and control
Electric motors and drives constitute one of the largest operational cost centres in cement manufacturing—accounting for as much as 75 per cent of electrical energy usage. Motors power crushers, grinders, fans, pumps and conveyors. Without precise speed control, these systems operate inefficiently, especially under partial load conditions. As the industry strives to reduce energy intensity—currently averaging 4.69?GJ/t of clinker with a 0.69?GJ/t potential improvement—the role of drives is critical.
Variable Frequency Drives (VFDs) or Variable Speed Drives (VSDs) optimise motor operation by adjusting speed to load. Since power consumption follows a cubic relationship with speed, even a 10 per cent reduction in fan speed can yield up to 27 per cent energy savings. ABB estimates VSD adoption can cut fan energy use by up to 60 per cent, and similar savings apply to pumps and conveyors. Additionally, soft-start capabilities reduce mechanical wear and electricity demand.
Medium-voltage drives are increasingly favoured in kilns and mills, offering efficient and controlled propulsion for large motors (>375?kW). These include design variants like scalar, vector and direct torque control, each enhancing process stability and reliability. Smart motor-control centres and digital monitoring add predictive maintenance capabilities, lowering downtime and protecting components from damage.
Digitalisation helps further boosts efficiency. Sensors track vibration, temperature and torque, sending alerts when anomalies appear—allowing proactive intervention. Coupled with cloud-enabled dashboards, these systems give plant managers real-time operational visuals. Emerging strategies include motor-driven kilns, optimised compressor control and regenerative braking in conveyors—all promising integrated energy savings and system longevity.
Maintenance and digital condition monitoring
Robust gear and motor performance depends as much on diligent maintenance as on quality hardware. Cement plants operate in abrasive environments, where dust ingress and heat accelerate wear on gearboxes and bearings. Traditional preventive schedules are being enhanced with condition-based monitoring (CBM), employing vibration, oil quality and thermal sensors to detect anomalies before breakdowns occur.
“The products we manufacture are primarily made from 42CrMo4 alloy steel, which is well-known for its strength and durability. This type of steel is highly resistant to corrosion and mechanical stress, which is essential in an environment like a cement plant. We also advise our customers to use protective covers while the machines are operating to further reduce environmental wear and tear. As for material performance, the tensile strength of the steel we use is around 900 N/mm². In comparison, many competitor products fail at around 600 N/mm². This shows that we never compromise on material quality, even if it means our costs are higher. Our philosophy is to prioritise long-term durability over short-term price reductions, and this approach has helped us build a strong reputation for reliability,” says Dheepan Ramalingam, Managing Director, Ringfeder Power Transmission (I).
CBM-enabled gearboxes report early signs of wear—uneven vibration, tooth damage, or gearbox play—well in advance of delays. Remote monitoring allows engineers to schedule maintenance during planned shutdowns, reducing unplanned downtime. This approach is especially valuable for critical components like kiln pinions or mill drives, where failures can stall production lines for hours or
even days.
For motors, performance data such as current fluctuations, temperature rise, and RPM deviations are tracked. Alerts flag performance drift or impending failure, triggering targeted maintenance and preventing catastrophic breakdowns. Coupled with operator training, these data-driven tools build a maintenance culture that extends asset longevity and optimises operational costs.
As plants scale in complexity, digital twins are gaining traction. By simulating gear stresses and motor behaviours under load scenarios, engineers can anticipate and resolve potential issues. Predictive analytics, powered by AI, further enhance reliability, enabling asset care programs that are cost-effective and aligned with safety and sustainability objectives.
Safety, reliability and compliance standards
In heavy industries like cement, safety and compliance are non-negotiable—and the gear and drive systems play a central role in risk prevention. Gear failures can result in catastrophic downtime or physical hazards such as shattered components or oil fires. Similarly, motor overheating, shaft misalignment, or electrical surges can pose serious threats to personnel and equipment. Therefore, selecting systems that comply with international standards like ISO 9001, IEC 60034, ISO 6336, or OSHA guidelines is critical.
Many high-performance drives now come equipped with built-in safety features: torque limiting, electronic braking, soft-start functions, thermal overload protection, and arc-flash prevention systems. These features not only protect the drive system itself but also safeguard connected equipment and operators. For example, a kiln drive motor with real-time torque monitoring can alert operators before any mechanical over-torque incident occurs, reducing the risk of accidents or
gear damage.
Regulatory compliance is another layer cement manufacturers cannot afford to overlook. Indian plants, especially those supplying to government or infrastructure projects, are now required to submit compliance records for emissions, energy consumption, and equipment safety. Components like drives and motors are increasingly scrutinised for CE marking, RoHS conformity, and BIS certification. This has elevated the importance of sourcing from certified vendors who can provide full documentation and after-sales support.
Training is also part of the safety ecosystem. OEMs and drive manufacturers now offer onsite and digital certification programs for plant technicians, enabling them to detect faults, align motors and gearboxes correctly, and safely shut down systems when needed. The result is not just improved compliance—but also a more resilient and skilled maintenance workforce, better equipped to manage evolving plant demands.
Sustainability impact and energy savings
Driven by climate targets and energy cost pressures, the cement industry is elevating energy efficiency as a sustainability imperative. Cement plants are working to reduce their energy-intensity—both in electricity (e) and thermal—through advanced drives, efficient gears, and digital controls. They aim to reduce electrical use toward 4?GJ/t and overall energy consumption below global best-practice levels.
The switch to VSD-equipped fans, pumps, and kilns reduces CO2 emissions and energy expenses. For example, a kiln fan retrofitted with VFDs at a Chinese plant lowered annual energy consumption by 10 per cent, saving US?$124,000. In India,
embracing dry-process technology and VSDs has helped most plants meet or outperform PAT-II efficiency benchmarks.
Gear innovations also contribute to sustainability. High-efficiency planetary and helical gear systems reduce friction losses and require less frequent oil changes and part replacements. Gearboxes designed with optimised tooth profiles and high-strength alloys, such as carburised steel, cut mechanical drag and electrical demand. Brands are also exploring low-lubricant and sealed gearbox systems to reduce environmental contamination.
Energy savings compound when drives and gears are integrated with alternative energy sources. Waste Heat Recovery (WHR) systems supply power to drives, reducing grid load. Solar/battery systems and kinetic energy recovery (e.g., regenerative braking) help close the efficiency loop. Together, these measures support the industry’s decarbonisation ambition toward Net Zero by 2070.
Smart factories, electrification trends
As Industry 4.0 gains momentum, gears, motors, and drives are no longer just mechanical components—they are becoming intelligent nodes in the cement plant’s digital nervous system. The integration of sensors, IoT-enabled monitoring and cloud-based analytics is turning static assets into dynamic, responsive systems.
Today, predictive maintenance dashboards allow engineers to visualise gearbox temperature trends, motor vibration or torque fluctuations in real time—enabling proactive interventions and optimising asset life.
Ramalingam exemplifies, “One of the most exciting developments is the integration of electronic feedback systems into our product lines. This represents a step toward smart technology, where products can provide real-time performance data. We are currently working on embedding sensors and feedback modules into our systems, which can give users predictive insights and maintenance alerts.”
One major trend is the emergence of digital twins—virtual replicas of physical systems that simulate their behaviour under real-world conditions. In cement applications, digital twins can model gearbox loads, monitor motor efficiency curves, and forecast failure modes. Paired with machine learning algorithms, they enable optimisation of process parameters, drive tuning, and asset scheduling without physical trials—cutting downtime and testing costs.
Another exciting development is the shift toward fully electrified drive systems, especially in rotary kilns and large vertical mills. While traditional hydraulic or mechanical drive systems still dominate in many plants, high-torque electric drives are gaining adoption due to their precision, lower maintenance, and ability to integrate with control systems. These drives also support energy recovery strategies—such as regenerative braking—enabling significant reductions in net power consumption.
Looking ahead, innovations like sensorless motor control, self-healing gear coatings, and edge AI processors for real-time condition assessment will redefine how cement plants view motion systems. These advancements won’t just boost uptime—they will provide the agility, traceability, and efficiency required for the future-ready, low-carbon smart
cement plant.
Conclusion
In cement manufacturing, gears, drives and motors serve as the backbone of plant operations—ensuring continuous, controlled motion across critical processes like crushing, grinding, kiln rotation and material handling. Today, these systems are evolving rapidly, with high-efficiency gearboxes, VFD-integrated motors and digital condition monitoring helping plants improve uptime, reduce energy use and extend equipment life.
Keeping up with the changing needs of the cement sector is mandatory for component providers. Kalra states, “Challenges are constant, especially in engineering and manufacturing. One of the biggest challenges is the increasing demand for precision and reliability from cement plants. Every year, the expectations rise. Clients demand tighter tolerances, better materials and longer-lasting components—even if the products we supplied years ago are still running without a single complaint.”
As India’s cement industry scales up capacity while pushing for sustainability and operational excellence, investing in reliable, customisable, and digitally enabled motion systems is no longer optional—it’s strategic. Whether it’s through localised innovation, safety compliance, or predictive maintenance, the performance of gears, drives, and motors will remain central to meeting future efficiency and Net
Zero goals.
– Kanika Mathur
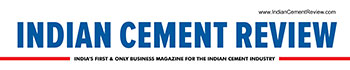
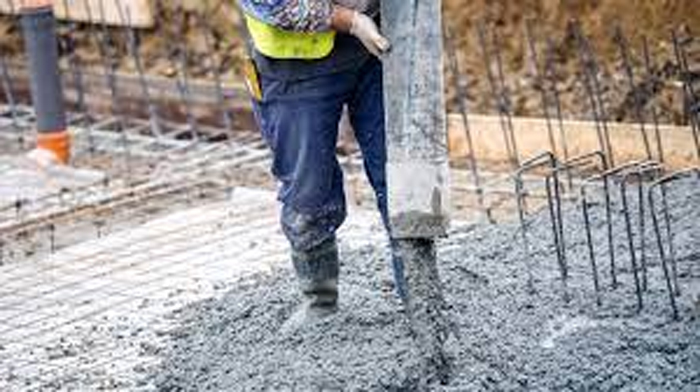
Tamil Nadu is set to host one of India’s five national carbon capture and utilisation (CCU) testbeds, aimed at reducing CO2 emissions in the cement industry as part of the country’s 2070 net-zero goal, as per a news report. The facility will be based at UltraTech Cement’s Reddipalayam plant in Ariyalur, supported by IIT Madras and BITS Pilani. Backed by the Department of Science and Technology (DST), the project will pilot an oxygen-enriched kiln capable of capturing up to two tonnes of CO2 per day for conversion into concrete products. Additional testbeds are planned in Rajasthan, Odisha, and Andhra Pradesh, involving companies like JK Cement and Dalmia Cement. Union Minister Jitendra Singh confirmed that funding approvals are underway, with full implementation expected in 2025.
Image source:https://www.heavyequipmentguide.ca/
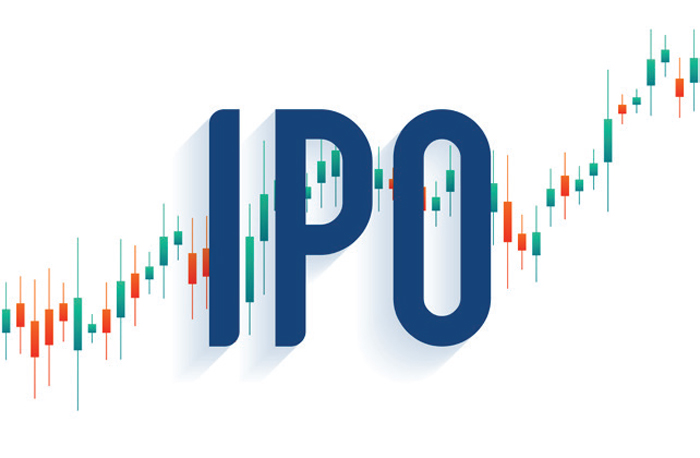
JSW Cement has set the price range for its upcoming initial public offering(IPO) at US$1.58 to US$1.67 per share, aiming to raise approximately US$409 million. As reported in the news, around US$91 million from the proceeds will be directed towards partially financing a new integrated cement plant in Nagaur, Rajasthan. Additionally, the company plans to utilise US$59.2 million to repay or prepay existing debts. The remaining capital will be allocated for general corporate purposes.
Concrete
Cement industry to gain from new infrastructure spending
Published
1 month agoon
July 24, 2025By
admin
As per a news report, Karan Adani, ACC Chair, has said that he expects the cement industry to benefit from the an anticipated US$2.2tn in new public infrastructure spending between 2025 and 2030. In a statement he said that ACC has crossed the 100Mt/yr cement capacity milestone in April 2025, propelling the company to get closer to its ambitious 140Mt/yr target by the 2028 financial year. The company’s capacity corresponds to 15 per cent of an all-India installed capacity of 686Mt/yr.
Image source:https://cementplantsupplier.com/cement-manufacturing/emerging-trends-in-cement-manufacturing-technology/