Concrete
AFR can provide economic and environmental benefits
Published
6 months agoon
By
admin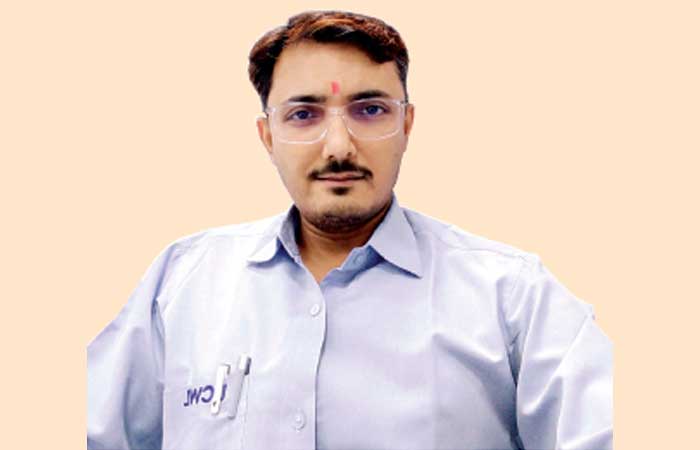
Tushar Khandhadia, General Manager – Production, Udaipur Cement Works, in conversation with Kanika Mathur about the impact of AFR on efficiency and quality.
As the cement industry moves towardmore sustainable practices, alternative fuels and raw materials (AFR) play a crucial role in reducing carbon emissions and enhancing resource efficiency. In this exclusive interview, Tushar Khandhadia, General Manager – Production at Udaipur Cement Works, shares insights on how the company integrates AFR into its production process, the challenges involved, and the latest innovations driving sustainable cement manufacturing.
Which AFR does your company currently use in cement production?
Our organisation employs a variety of AFR to enhance sustainability and reduce our carbon footprint. These include:
- Alternative fuels: Waste-derived fuels such as municipal solid waste (MSW), tire-derived fuel (TDF), biomass, and industrial waste, waste mix for co-incineration LCV.
- Alternative raw materials: Industrial by-products like fly ash, f.f slag, jarosite chemical gypsum, granulated slag, bf dust, chemical sludge (waste water treatment, ETP sludge – solid, spent carbon, waste mix (solid)).
How do alternative fuels impact the efficiency and quality of cement?
While alternative fuels can provide economic and environmental benefits, they must be carefully managed to ensure that the final quality of the cement is not compromised. The key to optimising the impact of alternative fuels on cement production lies in the selection of the right types of fuels, proper blending, and controlling combustion conditions to maintain both efficiency and high-quality output.
Fuel characteristics
- Energy content: Alternative fuels (such as biomass, waste-derived fuels, or industrial by-products) often have lower energy content compared to traditional fuels like coal or pet coke. This means that more of the alternative fuel is required to achieve the same level of heat generation. As a result, more fuel needs to be burned, potentially increasing the overall heat consumption of
the kiln. - Moisture and volatile matter: Some alternative fuels have higher moisture content or volatile substances, requiring additional energy to evaporate the moisture or combust these volatile compounds. This can lead to a higher heat consumption during the combustion process.
- Burning efficiency: combustion characteristics: Different alternative fuels may burn at different rates or temperatures compared to traditional fuels, which could affect the kiln’s efficiency. Incomplete combustion of some alternative fuels might cause heat losses and thus increase the energy needed to maintain kiln operation.
- Clinker formation: Alternative fuels may affect the formation of clinker (the solid material produced in the kiln). If the composition or combustion characteristics of the alternative fuel cause uneven heating or changes in clinker quality, additional energy may be needed to stabilise the temperature or improve the quality of the clinker.
- Operational adjustments: process optimisation: When switching to alternative fuels, adjustments are often required to optimise the kiln’s operational parameters (like air flow, temperature control, etc.). Until these adjustments are fully optimised, the kiln may operate less efficiently, leading to higher heat consumption.
Impact on quality:
- Chemical composition: Some alternative fuels, such as those derived from industrial waste or hazardous materials, may introduce chemical compounds that can alter the final properties of cement. However, proper fuel management ensures that any potential adverse effects on cement quality are minimised.
- Clinker quality: The quality of the clinker, which is the key ingredient in cement, can be affected by the composition of the alternative fuels. Some alternative fuels may introduce impurities (such as chlorine or sulphur), which could lead to clinker quality issues, such as instability or the formation of undesirable compounds.
- Consistency in product: The use of alternative fuels can cause variations in the combustion process, which may lead to slight fluctuations in temperature and material composition. These inconsistencies could impact the final cement quality, though careful fuel selection and blending can mitigate these risks.
- Environmental impacts on quality: One of the advantages of using alternative fuels is their potential to reduce the carbon footprint of cement production. The reduction of CO2 emissions and other pollutants indirectly benefits the overall quality of the end product, as it promotes sustainability and cleaner production processes.
Environmental and sustainability considerations
- Lower CO2 emissions: By using alternative fuels, the cement industry can reduce its reliance on fossil fuels, thereby decreasing CO2 emissions. The use of waste materials like municipal solid waste or biomass can result in a carbon-neutral or lower-carbon cement production process.
- Waste reduction: AFR helps recycle waste materials, reduce landfill use and promote circular economy practices, which indirectly enhances the sustainability of the cement industry.
What challenges do you face in sourcing and utilising AFR?
Sourcing and utilising AFR in cement production comes with several challenges that must be addressed to ensure that the transition is both effective and sustainable. Below are the key challenges typically faced:
Fuel quality variability
- Inconsistent properties: AFRs such as waste materials, biomass or industrial by-products can vary significantly in their chemical composition, energy content, moisture levels and combustion characteristics. This inconsistency can complicate kiln operations, as cement plants are optimised for burning specific fuels like coal or petcoke. Variability in AFR can lead to issues with combustion efficiency, temperature control, and process stability.
- Contaminants: Some AFRs may contain unwanted contaminants (e.g., plastics, heavy metals, chlorine, or sulfur) that could affect both the kiln’s performance and the quality of the final product. These contaminants can increase emissions or cause equipment corrosion and premature wear.
Supply chain and availability
- Logistical complexity: Sourcing AFR requires a robust and reliable supply chain, as many alternative fuels come from waste streams that may not be consistently available. This variability in supply can lead to fluctuations in fuel availability, which may impact production schedules.
- Sourcing reliability: The availability of certain types of AFRs may be limited by geographic location, government regulations, or competing demands (e.g., the use of biomass for other industries or energy production). This can make it difficult to secure a stable and consistent supply of AFR, particularly in regions where waste recycling infrastructure is underdeveloped.
Storage and handling
- Storage issues: Some AFRs, especially organic or biomass-based fuels, may require specialised storage facilities to prevent degradation, moisture absorption, or contamination. Proper storage is necessary to maintain fuel quality and prevent losses due to spoilage.
- Handling challenges: Different AFRs require different handling techniques, such as shredding, drying or sorting, before they can be used in the kiln. This adds complexity to the operational process and may require investment in new infrastructure and equipment.
Regulatory and environmental concerns
- Compliance with regulations: The use of certain AFRs may be subject to stringent environmental regulations, particularly regarding emissions, waste management and fuel quality standards. Compliance with these regulations may require additional monitoring, testing and reporting, increasing operational costs and complexity.
- Emission control: Some alternative fuels may lead to higher levels of certain pollutants (e.g., dioxins, furans, or particulate matter) if not properly managed. Cement plants must invest in additional air pollution control technologies (e.g., scrubbers, electrostatic precipitators) to mitigate these emissions.
Technical adaptation of kilns and equipment
- Modification of existing systems: Cement plants may need to retrofit or upgrade their existing equipment (e.g., burners, air systems, or fuel handling systems) to efficiently utilise AFR. These modifications can be costly, time-consuming, and may require downtime.
- Impact on kiln efficiency: The combustion characteristics of AFR differ from those of traditional fuels, and improper adaptation can lead to inefficient burning, lower kiln temperatures and lower overall kiln throughput. Continuous monitoring and optimisation of the kiln operation are essential to ensure efficient use of AFR.
Cost and economic viability
- Initial investment: While AFRs can provide cost savings in the long term (especially if they are locally sourced or cheaper than conventional fuels), the upfront cost of modifying equipment, establishing fuel handling processes, and meeting regulatory requirements can be significant.
- Price fluctuations: The cost of alternative fuels can fluctuate based on market conditions, waste availability, and local competition for resources. Such variability in pricing may make it difficult to predict savings over time and could affect the economic feasibility of using AFRs.
Quality control of cement
- Impact on product consistency: The chemical composition of AFRs can affect the clinker quality and, in turn, the final cement product. Variations in the AFR may result in inconsistent burning conditions in the kiln, which can lead to variations in clinker mineral composition and final cement properties.
- Blending and optimisation: To ensure that product quality remains consistent, cement producers must carefully manage the blending of alternative fuels with traditional fuels. Finding the right balance and ensuring stable quality control requires detailed analysis and optimisation.
Public perception and social acceptance
- Concerns about waste incineration: In some regions, the use of waste-derived fuels in cement kilns may face resistance due to public concerns about the environmental and health impacts of burning waste. These concerns can affect the social acceptance of AFR use, particularly if local communities are not fully educated about the benefits of AFR in reducing waste and emissions.
- Brand reputation: Cement companies must also be mindful of their brand reputation when using waste-derived fuels. Public perception can play a significant role in the company’s market standing, especially in more environmentally conscious regions.
Long-term sustainability of AFR supply
- Sustainability of fuel sources: The long-term availability of certain types of AFR, such as biomass or waste-derived fuels, may be subject to factors like changing waste management practices, government policies, and market demand. Over-reliance on a single source of AFR could lead to supply chain disruptions or sustainability concerns in the future.
Strategies to overcome these challenges
To overcome these challenges, cement producers often adopt several strategies:
- Diversification of AFR sources: Relying on a mix of different AFR types (e.g., industrial by-products, biomass, municipal waste) can help mitigate supply risks and fuel quality issues.
- Partnerships and collaboration: Collaborating with waste management companies, municipalities, and regulatory bodies can help secure a reliable AFR supply and ensure compliance with regulations.
- Technology and monitoring: Investing in advanced combustion technologies, sensors, and control systems can help optimise AFR utilisation in the kiln, ensuring efficient combustion and minimising emissions.
- Training and skill development: Ensuring that staff are well-trained in handling and utilising AFRs can help minimise operational challenges and improve overall kiln efficiency.
While there are many challenges associated with sourcing and utilising AFR, many of them can be addressed with proper planning, technology, and management. The long-term benefits of using alternative fuels, including environmental sustainability and cost savings, often outweigh the challenges, especially with ongoing improvements in fuel handling and kiln optimisation.
How does AFR adoption contribute to cost savings and sustainability?
The adoption of AFR) in cement production can significantly contribute to both cost savings and sustainability. Here’s how:
Cost Savings
- Reduced reliance on expensive fossil fuels: Traditional fuels like coal or petcoke can be subject to volatile price fluctuations due to geopolitical factors or market changes. AFRs, such as industrial by-products, biomass, or waste materials, are often less expensive than conventional fuels. By switching to AFRs, cement producers can lower their overall fuel costs.
- Utilising waste streams: Many AFRs are waste products from other industries or municipal waste. Using these materials instead of purchasing new fuels reduces the cost of sourcing energy, as companies may even receive subsidies or payments for taking certain waste materials off their hands (e.g., biomass, plastics, tires).
- Reduced disposal costs: Cement plants can help reduce the cost of waste disposal for municipalities and industries by accepting waste streams as alternative fuels. Waste management and disposal can be expensive, and cement producers may receive financial incentives for taking in these materials.
- Operational efficiency: Local sourcing of AFRs can cut down transportation costs compared to importing traditional fuels from distant sources. If waste materials are available locally, their use in cement production can result in both cost savings and a smaller carbon footprint due to reduced transportation emissions.
- Energy efficiency gains with optimised kiln operations: AFRs, when properly integrated into cement production, can lead to more efficient energy usage. Some AFRs burn hotter or more efficiently than traditional fuels, improving the energy output per unit of fuel used. This means that the cement plant might be able to produce the same amount of clinker with less energy.
Reduction in carbon emissions
- Lower greenhouse gas emissions: One of the most significant benefits of AFR adoption is the reduction in CO2 emissions. Many alternative fuels have a lower carbon footprint than traditional fossil fuels. For instance, biomass can be considered carbon-neutral since the CO2 released during its combustion is roughly equivalent to the CO2 absorbed during the plant’s growth. Using waste materials that would otherwise decompose in landfills (producing methane, a potent greenhouse gas) also helps to reduce the overall carbon impact.
- Reduced reliance on fossil fuels: By replacing fossil fuels with renewable or waste-derived alternatives, cement producers reduce their overall consumption of non-renewable resources, helping to lower their carbon footprint and contribute to global sustainability goals.
Waste diversion
- Waste-to-energy: By using waste materials as fuel, cement plants contribute to waste diversion from landfills and incinerators. This process transforms waste into a valuable resource, helping to reduce the environmental impact associated with landfill usage and waste incineration, both of which are significant sources of pollution.
- Circular economy contribution: AFR adoption is an example of a circular economy model, where waste is transformed into valuable resources rather than being discarded. This contributes to the reduction of environmental pollution and promotes sustainability within industries.
- Resource conservation: By using alternative fuels instead of coal, oil, or gas, cement plants help preserve natural resources. Fossil fuels are finite, and their extraction can cause environmental degradation. By utilising AFRs, companies help reduce the pressure on extracting and depleting natural reserves.
- Reduced landfill impact: The cement industry can help alleviate the growing challenge of managing waste by using materials that might otherwise end up in landfills. For instance, tire-derived fuels, plastics, and even certain types of municipal solid waste can be repurposed in cement kilns, decreasing the amount of waste needing disposal and contributing to a reduction in landfill waste volume.
- Energy efficiency and lower resource consumption: Many AFRs, like biomass or waste oils, may have similar or higher calorific values than conventional fuels, contributing to better energy efficiency in the kiln process. This optimised energy use leads to a reduced need for fossil fuels and less overall consumption of resources, which contributes to sustainability efforts.
The adoption of AFRs in cement production delivers clear benefits in terms of cost savings (through reduced fuel and disposal costs, and energy efficiencies) and sustainability (by lowering emissions, reducing waste, conserving resources, and supporting a circular economy). While the transition to AFRs may require upfront investments in technology and infrastructure, the long-term economic and environmental benefits make it a key strategy for the cement industry to align with global sustainability goals, reduce operational costs, and enhance its competitive edge in an increasingly eco-conscious market.
Are there any recent innovations your company has implemented in AFR usage?
Yes, we have done several major projects for utilisation of AFR in our kiln.
Development of robust AFR handling systems: Innovations in AFR handling systems are enabling the safe and efficient use of various waste materials. Technologies such as pipe conveyors and precise metering systems ensure that different types of AFR can be fed into the kiln without environmental impact. These systems are designed to accommodate the varying characteristics of alternative fuels, providing comprehensive support from planning through operation to service and optimisation measures.
Real-time monitoring and quality assessment: Systems enable continuous monitoring of AFR quality, detecting anomalies and ensuring consistent fuel quality. This real-time analysis allows for immediate adjustments to the combustion process, optimising AFR utilisation.
Combustion optimisation through ML: Machine learning algorithms analyse kiln data to optimise combustion processes, ensuring complete fuel combustion and minimising waste. This leads to reduced fuel consumption, lower emissions and enhanced energy efficiency.
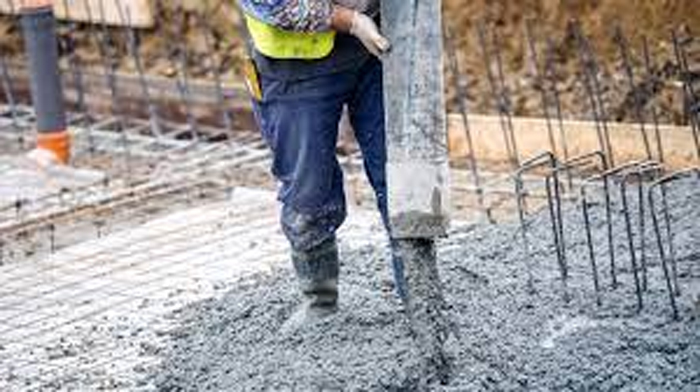
Tamil Nadu is set to host one of India’s five national carbon capture and utilisation (CCU) testbeds, aimed at reducing CO2 emissions in the cement industry as part of the country’s 2070 net-zero goal, as per a news report. The facility will be based at UltraTech Cement’s Reddipalayam plant in Ariyalur, supported by IIT Madras and BITS Pilani. Backed by the Department of Science and Technology (DST), the project will pilot an oxygen-enriched kiln capable of capturing up to two tonnes of CO2 per day for conversion into concrete products. Additional testbeds are planned in Rajasthan, Odisha, and Andhra Pradesh, involving companies like JK Cement and Dalmia Cement. Union Minister Jitendra Singh confirmed that funding approvals are underway, with full implementation expected in 2025.
Image source:https://www.heavyequipmentguide.ca/
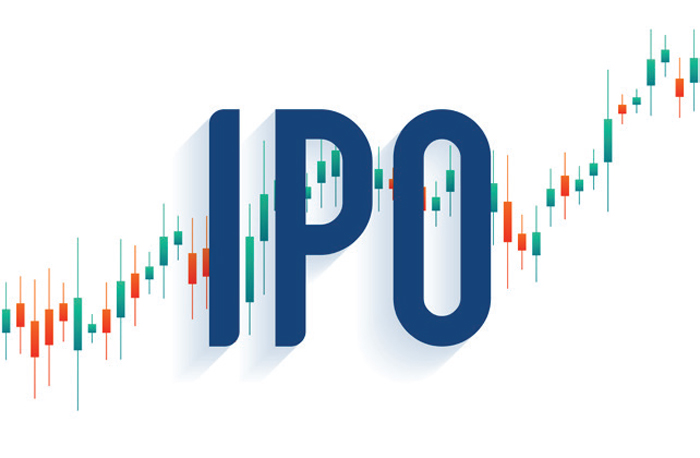
JSW Cement has set the price range for its upcoming initial public offering(IPO) at US$1.58 to US$1.67 per share, aiming to raise approximately US$409 million. As reported in the news, around US$91 million from the proceeds will be directed towards partially financing a new integrated cement plant in Nagaur, Rajasthan. Additionally, the company plans to utilise US$59.2 million to repay or prepay existing debts. The remaining capital will be allocated for general corporate purposes.
Concrete
Cement industry to gain from new infrastructure spending
Published
1 month agoon
July 24, 2025By
admin
As per a news report, Karan Adani, ACC Chair, has said that he expects the cement industry to benefit from the an anticipated US$2.2tn in new public infrastructure spending between 2025 and 2030. In a statement he said that ACC has crossed the 100Mt/yr cement capacity milestone in April 2025, propelling the company to get closer to its ambitious 140Mt/yr target by the 2028 financial year. The company’s capacity corresponds to 15 per cent of an all-India installed capacity of 686Mt/yr.
Image source:https://cementplantsupplier.com/cement-manufacturing/emerging-trends-in-cement-manufacturing-technology/