Concrete
Science and Application of Grinding Aids
Published
7 months agoon
By
admin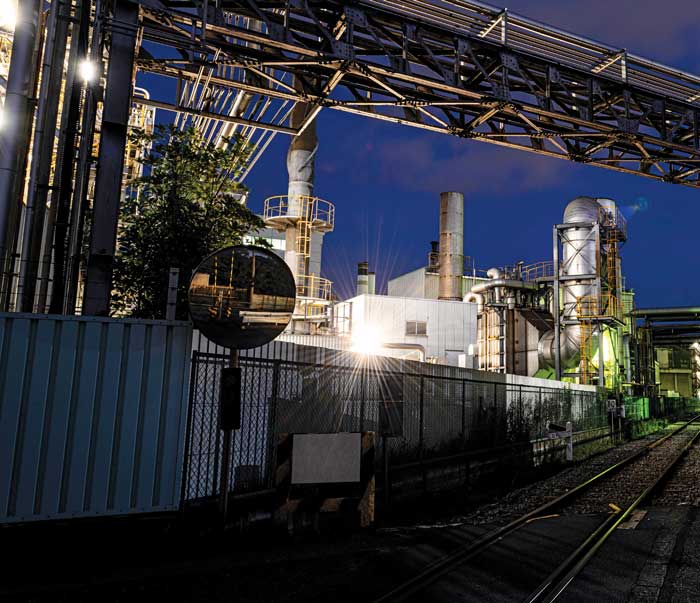
Dr SB Hegde discusses the importance of grinding aids as essential chemical additives that enhance cement grinding efficiency, reduce energy consumption and improve overall cement quality.
Grinding aids are chemical additives used in the manufacturing of cement to improve the grinding efficiency and performance of the material. These additives have become a critical component of the cement industry, playing a significant role in optimising mill output, reducing energy consumption, and enhancing the quality of cement. However, the adoption of grinding aids varies significantly across regions, influenced by cost considerations, regulatory frameworks, and technical awareness.
Despite their utility, grinding aids remain underutilised in certain regions. For instance, Europe has achieved over 80 per cent penetration of grinding aids due to stringent energy efficiency norms and advanced technologies, while India lags at around 30 per cent penetration, primarily due to cost sensitivity and limited technical expertise. Additionally, inconsistent quality and improper dosing often lead to suboptimal performance, underlining the need for stringent quality control and process optimisation.
The global market for grinding aids is expanding, projected to reach $ 1.2 billion by 2030, with a CAGR of 5.5 per cent. In India, the market is currently valued at `500 crore (2024). Innovations in the chemistry of grinding aids and the push for sustainable, bio-based additives are opening new avenues for adoption. Moreover, real-time monitoring and digital integration in cement plants are poised to revolutionise grinding aid applications by ensuring precise dosing and performance optimisation.
This article delves into the science, chemistry, and application of grinding aids, exploring their role in improving milling efficiency, quality control, and concrete performance. It further addresses market dynamics, challenges in adoption, and the path forward for maximising the benefits of grinding aids in cement manufacturing.
Chemistry of Grinding Aids
Grinding aids are chemical compounds specifically designed to improve the efficiency of the cement grinding process. Their effectiveness arises from their ability to modify the physical and chemical interactions between cement particles during grinding, thereby reducing agglomeration and improving the flowability of the material. This section delves into the nomenclature, chemistry, and scientific characteristics of grinding aids, providing an advanced understanding of their role in cement manufacturing.
2.1. Nomenclature and Classification
Grinding aids are generally categorised based on their chemical composition and functional groups. The most common types include:
1. Amine-based Compounds:
- Triethanolamine (TEA)
- Diethanolamine (DEA)
- Monoethanolamine (MEA)
2. Glycol-based Compounds:
- Ethylene glycol (EG)
- Diethylene glycol (DEG)
- Polyethylene glycol (PEG)
3. Other Organic Compounds:
- Lignosulfonates
- Hydroxycarboxylic acids (e.g., citric acid)
4. Hybrid Formulations:
- Combinations of amines and glycols for enhanced performance
- Additives with functionalised polymers provide multiple benefits, such as improving hydration kinetics and early strength development.
These compounds are often blended with performance enhancers, such as surfactants or dispersants, to achieve desired operational and material properties.
2.2. Chemical Mechanism of Action
Grinding aids operate at the molecular level by modifying surface properties and reducing inter-particle forces. The primary mechanisms include:
1. Reduction of Surface Energy:
- Cement particles exhibit high surface energy due to fracture during grinding. Grinding aids adsorb onto particle surfaces, reducing their surface energy and preventing agglomeration.
2. Electrostatic Neutralisation:
- Many grinding aids neutralise electrostatic charges that cause particles to attract each other, thus improving dispersion.
3. Lubrication Effect:
- Glycol-based grinding aids act as lubricants at the contact points between particles and grinding media, reducing friction and energy consumption.
4. Improved Particle Size Distribution (PSD):
- Grinding aids influence PSD by stabilising fine particles and preventing the re-agglomeration of smaller fractions, resulting in improved cement quality.
2.3. Scientific Characteristics and Properties
The effectiveness of grinding aids depends on their physicochemical properties and interactions with cement clinker phases.
1. Molecular Weight and Structure:
- Low molecular weight compounds, such as TEA, are highly effective in reducing agglomeration but may increase water demand in the final cement.
- High molecular weight compounds, such as PEG, provide additional benefits like workability and slump retention.
2. Hydrophilicity and Hydrophobicity:
- Hydrophilic compounds, such as DEG, enhance water compatibility, while hydrophobic additives improve the grinding of clinker with high limestone content.
3. pH and Ionic Strength:
- Most grinding aids function optimally within a specific pH range (typically 7-9) to ensure effective adsorption on clinker particles.
- Ionic strength plays a critical role in the interaction of grinding aids with calcium ions present in the clinker.
4. Thermal Stability:
- The thermal decomposition of grinding aids during the grinding process can influence their effectiveness. For example, amine-based compounds degrade at temperatures above 200°C, whereas glycol-based compounds remain stable under similar conditions.
2.4. Advanced Chemical Interactions with Clinker Phases
Grinding aids interact differently with the primary clinker phases—C3S (alite), C2S (belite), C3A (tricalcium aluminate), and C4AF (ferrite).
1. C3S (Alite):
- Glycol-based compounds enhance the grinding of alite due to their ability to reduce crystalline hardness.
- TEA has been shown to accelerate the hydration of C3S, improving early strength.
2. C2S (Belite):
- Grinding aids have limited direct interaction with belite but indirectly improve its grinding efficiency by stabilising the fine particles in the cement mix.
3. C3A (Tricalcium Aluminate):
- Amine-based grinding aids are highly effective in modifying the hydration kinetics of C3A, thereby influencing setting time and workability.
4. C4AF (Ferrite):
- Ferrite phases are less reactive, but grinding aids reduce the grinding energy required for these phases, indirectly contributing to overall mill efficiency.
2.5. Examples of Performance Variation
Performance variations of grinding aids depend on clinker composition, mill type, and operating conditions. For instance:
- A study revealed that the use of TEA in ball mills improved the grinding efficiency by 15 per cent, while the same compound exhibited a 20 per cent improvement in vertical roller mills.
- Glycol-based aids showed superior performance with clinker containing higher SO3 content, improving Blaine fineness by 10 per cent compared to amine-based aids.
- Customised formulations combining TEA and PEG reduced specific power consumption by eight per cent in a cement plant in South India.
2.6. Quality Control and Standardisation
To ensure consistent performance, grinding aids undergo rigorous quality control tests, including:
1. Fourier Transform Infrared Spectroscopy (FTIR): Used to identify functional groups and confirm chemical composition.
2. Gas Chromatography-Mass Spectrometry (GC-MS): Determines the purity and presence of byproducts in grinding aid formulations.
3. Thermogravimetric Analysis (TGA): Assesses thermal stability and decomposition characteristics.
4. Surface Area and PSD Analysis: Evaluates the impact of grinding aids on cement particle size distribution and specific surface area.
5. Mill Trials: Performance is validated under real-world conditions by assessing mill output, specific power consumption, and cement quality metrics like Blaine fineness and compressive strength.
Performance Evaluation of Grinding Aids
The performance evaluation of grinding aids is crucial in determining their efficiency and overall contribution to cement manufacturing processes. A systematic assessment involves analysing key performance indicators (KPIs) such as energy consumption, mill output, and particle size distribution, while also evaluating their impact on cement hydration, setting time, and compressive strength. These evaluations, carried out both in laboratories and real-world industrial settings, provide critical insights into the effectiveness of grinding aids.
3.1. Key Performance Indicators (KPIs)
Energy consumption serves as a primary metric for evaluating grinding aids, as their primary objective is to reduce the energy required for grinding. Studies have revealed that grinding aids can lower specific energy consumption by five to 25 per cent, contingent upon factors such as cement type, mill configuration, and operating parameters. For instance, a South Indian cement plant achieved an eight per cent reduction in specific power consumption with a glycol-based grinding aid in a ball mill, equating to considerable cost savings.
Mill output is another essential parameter. Grinding aids enhance material flowability and reduce agglomeration, leading to increased throughput. For example, polycarboxylate ether (PCE)-based grinding aids have been shown to boost mill output in vertical roller mills by 10 to 15 per cent compared to traditional amine-based formulations. This improvement is due to the superior dispersion and grinding efficiency offered by PCE-based formulations.
Particle size distribution (PSD) is significantly impacted by grinding aids, as they help achieve a finer and more uniform grind. This results in improved packing density and reduced voids in the cement matrix. Laboratory tests with triethanolamine (TEA)-based grinding aids have demonstrated a 12 per cent increase in Blaine fineness, alongside a notable reduction in oversize particles (>45 microns).
3.2. Laboratory Testing Methods for Grinding Aids
To comprehensively evaluate grinding aids, laboratory testing under controlled conditions is indispensable. Standardised methods include:
Grinding Efficiency Tests: Laboratory ball mills simulate industrial grinding conditions. The addition of grinding aids is assessed by measuring power draw, material flow rate, and specific residue levels. These tests provide quantifiable data on grinding efficiency improvements.
Hydration Studies: Techniques like isothermal calorimetry and X-ray diffraction (XRD) monitor hydration kinetics and phase formation. Amine-based grinding aids accelerate calcium silicate
hydrate (C-S-H) formation, contributing to early strength development.
Rheology and Flowability Tests: Grinding aids improve flowability, evaluated using rheometers and flowability indices. Glycol-based additives typically enhance flow properties by 15 to 20 per cent, reducing clogging and promoting smoother mill operations.
Compressive Strength Testing: Cement mortars incorporating grinding aids are subjected to compressive strength tests at various curing ages (e.g., 1, 3, 7, and 28 days). TEA-based grinding aids exhibit a 10 to 15 per cent improvement in early compressive strength, while PCE-based formulations deliver balanced strength gains across all curing ages.
3.3. Effect of Grinding Aids on Cement Hydration, Setting Time, and Compressive Strength Development
Grinding aids play a pivotal role in influencing cement hydration. Amine-based formulations, such as TEA and diethanolamine (DEA), enhance alite (C3S) hydration, leading to accelerated setting and early strength gain. However, excessive dosages can retard ettringite formation, thereby delaying setting time.
Glycol-based additives improve particle dispersion, ensuring uniform hydration. This results in enhanced compressive strength development at all ages. For instance, laboratory experiments demonstrated an eight per cent increase in 28-day compressive strength with ethylene glycol-based grinding aids compared to untreated cement.
Polycarboxylate ether-based grinding aids represent a modern advancement, offering dual benefits of improved grinding efficiency and compatibility with chemical admixtures like superplasticisers. This synergy optimises hydration, resulting in superior strength development. Studies have shown a 12 per cent increase in 28-day compressive strength for PCE-based grinding aids in cement containing supplementary materials like fly ash and slag.
3.4. Examples of Performance Variations with Specific Grinding Aids
Performance variations among grinding aids are influenced by their chemical compositions and the specific characteristics of the grinding process.
For example:
- A North American cement plant achieved a 15 per cent increase in mill throughput and a 10 per cent reduction in specific energy consumption after transitioning from TEA-based to hybrid amine-glycol grinding aids.
- Comparative trials revealed that diethylene glycol (DEG) is more effective in reducing grinding energy for clinker with high C3A content, while TEA offers superior performance for clinker with low gypsum levels.
- A European cement manufacturer observed significant quality improvements with PCE-based grinding aids, particularly for blended cements containing up to 30 per cent fly ash. These cements exhibited narrower PSD and enhanced durability characteristics.
Challenges in Grinding Aid Adoption
Grinding aids, despite their proven benefits in enhancing milling efficiency and improving cement quality, face several challenges in widespread adoption. Understanding these challenges requires a detailed analysis of operational, environmental, and regulatory factors at both global and regional levels, including India. This section delves into the barriers to the extensive use of grinding aids, with a focus on technical, logistical, and market-driven aspects.
4.1. Reasons for Limited Popularity in Some Regions and Plants
The limited adoption of grinding aids in certain regions and plants often stems from economic constraints and lack of awareness. In emerging markets, the upfront cost of grinding aids may deter smaller or cost-sensitive cement producers. For example, in India, many mid-sized plants operate on tight profit margins and prioritise short-term cost reductions over long-term efficiency gains. Globally, smaller plants in Africa and Southeast Asia also exhibit lower adoption rates due to financial constraints and limited technical knowledge about the benefits of grinding aids.
Additionally, plant operators may hesitate to incorporate grinding aids due to the perception that these additives increase operational complexity. Variations in clinker composition and grinding equipment across plants often necessitate customised formulations of grinding aids, which can create challenges in consistency and effectiveness. For instance, cement plants using vertical roller mills (VRMs) often require different grinding aid formulations compared to those with ball mills, leading to variability in performance and discouraging adoption.
4.2. Impact of Raw Material Variability on Grinding Aid Effectiveness
The variability of raw materials, including clinker and gypsum, presents a significant challenge to the consistent performance of grinding aids. Differences in chemical composition, mineralogy, and moisture content of raw materials can influence the reactivity and efficacy of grinding aids. For example, clinkers with high levels of alite (C3S) and belite (C2S) require different formulations compared to those with elevated free lime or alkali content.
In India, raw material variability is particularly pronounced due to the use of diverse limestone sources and blended cements containing fly ash, slag, or other supplementary cementitious materials (SCMs). A study conducted by a leading Indian cement producer revealed that grinding aids optimised for clinker-based cement exhibited suboptimal performance when used for fly ash-blended cement, resulting in inconsistent strength development and mill throughput.
Globally, similar issues arise in regions where raw material quality is inconsistent. Cement plants in Southeast Asia, for instance, frequently encounter challenges due to high moisture content in limestone and clay, which affects grinding efficiency and necessitates frequent adjustments in grinding aid dosage.
4.3. Concerns Over Operational and Maintenance Issues in Cement Mills
Operational and maintenance challenges in cement mills also contribute to the limited adoption of grinding aids. Excessive use of grinding aids can lead to unwanted side effects, such as excessive coating of grinding media and mill internals, which can reduce grinding efficiency and increase maintenance costs. For example, ethylene glycol-based grinding aids, when used at high dosages, may lead to the formation of sticky residues, necessitating frequent cleaning of mill components.
Furthermore, some plant operators report issues related to the compatibility of grinding aids with chemical admixtures or process conditions. In certain cases, the use of amine-based grinding aids has been linked to increased foaming in water-recirculating systems, leading to operational disruptions and higher water treatment costs.
Additionally, the adoption of grinding aids in plants using VRMs is often hindered by the sensitivity of these mills to operating parameters. Variations in grinding aid dosage or clinker properties can significantly affect mill vibrations and stability, creating operational challenges.
4.4. Environmental and Regulatory Challenges Related to Grinding Aids
Environmental concerns and regulatory restrictions represent another significant barrier to the widespread adoption of grinding aids. Many grinding aids contain volatile organic compounds (VOCs), which are subject to stringent environmental regulations in developed markets such as Europe and North America. For instance, amine-based formulations, including triethanolamine (TEA) and diethanolamine (DEA), are classified as hazardous substances in some regions, limiting their usage.
In India, while environmental regulations are less restrictive, there is growing pressure from policymakers and environmental organisations to minimise the carbon footprint of cement manufacturing. Grinding aid manufacturers face the challenge of developing eco-friendly formulations that meet performance requirements while adhering to environmental standards. This has spurred interest in biodegradable and low-VOC grinding aids, although their higher cost remains a deterrent.
Additionally, regulatory approval processes for new grinding aid formulations can be time-consuming and costly, particularly in regions with strict compliance standards. This limits the introduction of innovative products in markets such as the EU, where REACH (Registration, Evaluation, Authorisation, and Restriction of Chemicals) compliance is mandatory.
About the author:
Dr SB Hegde, a global cement industry leader with over 30 years of experience, is a Professor at Jain College of Engineering, India, and a Visiting Professor at Pennsylvania State University, USA. Recipient of the ‘Global Visionary’ award, Dr Hegde advises India’s think tank CSTEP on hydrogen usage in cement and consults for major cement companies. He also serves on expert panels of key industry bodies and journals globally.
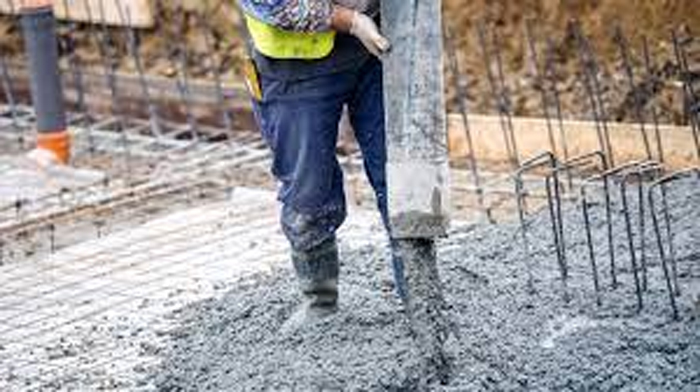
Tamil Nadu is set to host one of India’s five national carbon capture and utilisation (CCU) testbeds, aimed at reducing CO2 emissions in the cement industry as part of the country’s 2070 net-zero goal, as per a news report. The facility will be based at UltraTech Cement’s Reddipalayam plant in Ariyalur, supported by IIT Madras and BITS Pilani. Backed by the Department of Science and Technology (DST), the project will pilot an oxygen-enriched kiln capable of capturing up to two tonnes of CO2 per day for conversion into concrete products. Additional testbeds are planned in Rajasthan, Odisha, and Andhra Pradesh, involving companies like JK Cement and Dalmia Cement. Union Minister Jitendra Singh confirmed that funding approvals are underway, with full implementation expected in 2025.
Image source:https://www.heavyequipmentguide.ca/
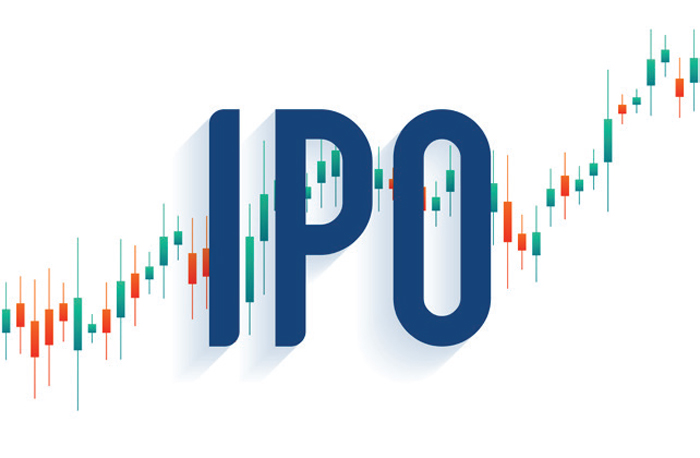
JSW Cement has set the price range for its upcoming initial public offering(IPO) at US$1.58 to US$1.67 per share, aiming to raise approximately US$409 million. As reported in the news, around US$91 million from the proceeds will be directed towards partially financing a new integrated cement plant in Nagaur, Rajasthan. Additionally, the company plans to utilise US$59.2 million to repay or prepay existing debts. The remaining capital will be allocated for general corporate purposes.
Concrete
Cement industry to gain from new infrastructure spending
Published
1 month agoon
July 24, 2025By
admin
As per a news report, Karan Adani, ACC Chair, has said that he expects the cement industry to benefit from the an anticipated US$2.2tn in new public infrastructure spending between 2025 and 2030. In a statement he said that ACC has crossed the 100Mt/yr cement capacity milestone in April 2025, propelling the company to get closer to its ambitious 140Mt/yr target by the 2028 financial year. The company’s capacity corresponds to 15 per cent of an all-India installed capacity of 686Mt/yr.
Image source:https://cementplantsupplier.com/cement-manufacturing/emerging-trends-in-cement-manufacturing-technology/