Concrete
Revolutionising Material Movement
Published
2 years agoon
By
admin
Streamlining material transportation at cement plants vastly affects productivity, cost-effectiveness and environmental compliance. ICR looks at how automation has transformed the way cement plants manage, store and transport materials, as a vital step towards modernising the manufacturing process.
Material handling in a cement manufacturing plant setup refers to the various processes and equipment used to transport, store, control, and manage raw materials, intermediate products, and finished cement within the plant. Effective material handling is crucial for ensuring the efficient and safe operation of the cement manufacturing process.
In the process of cement manufacturing, materials go through several touch points as they are transformed from raw materials into the final product.
The process begins with the extraction of raw materials, primarily limestone, clay and silica, from quarries or mines. Large equipment such as bulldozers and dump trucks are used to handle and transport these materials from the quarry to the cement plant. Once the raw materials are extracted, they are transported to crushers where they are crushed
into smaller pieces to facilitate further processing. The crushed materials are then blended in
precise proportions to create a raw mix, ensuring a consistent composition.
The raw mix is conveyed to a raw mill, where it is finely ground into a powder. The mill may use rollers, ball mills, or other grinding equipment to achieve the desired particle size. The finely ground raw meal is then preheated and pre-calcined in a preheater tower or cyclone system. This reduces the moisture content and initiates the chemical reactions necessary for cement production. The preheated and pre-calcined raw meal is fed into a rotary kiln, where it is heated to extremely high temperatures, typically around 1,450o C. This process transforms the raw materials into clinker, a nodular material.
After exiting the rotary kiln, the clinker is cooled and then finely ground in a cement mill. Gypsum is often added to control the setting time of the resulting cement. The ground clinker and gypsum mixture is known as Portland cement. The final cement product is stored in silos or bins before being packaged in bags or bulk containers for distribution to customers. Material handling equipment like conveyors, bucket elevators, and packing machines are used at this stage. Cement products are transported by trucks, rail, or ships to distribution centers or directly to construction sites, where they are used in various construction applications.
Throughout the entire cement manufacturing process, careful control and handling of materials are essential to ensure the quality and consistency of the final product. Automation and monitoring systems are often employed to maintain precise control over these touchpoints and optimise the efficiency of the process.
“Cement plants are notorious for clogging problems. Accumulations in ducts, chutes, and vessels often choke the movement of materials, causing bottlenecks that create expensive impediments to plant performance, process efficiency, productivity, and profitability. This means build-ups need to be manually cleared with alarming regularity unless the right technology is employed to keep things flowing smoothly,”
says Anup Nair, Managing Director, Martin Engineering India.
“The biggest single improvement when it comes to safety and efficiency in preheater performance is the use of air cannons, employed in a number of applications in cement production, from unclogging chutes and hoppers to moving super-heated material through the cooling process,” he adds.
MATERIAL TRANSPORTATION ENABLERS
In a cement manufacturing plant, various types of equipment and systems are used for the transportation of materials from quarries to the plant, within the plant, and for moving finished products from the plant to the dispatch points. Here are the key equipment and systems used at each stage of material transportation:
- Quarry to plant transportation
Heavy-duty trucks and haulage equipment are commonly used to transport raw materials from quarries or mines to the cement plant. These vehicles can carry bulk quantities of materials such as limestone, clay, and shale. - Within the plant transportation
• Conveyor belts: Conveyor systems are extensively used within the plant to move raw materials from one process to another. They are especially critical for transporting raw materials from storage areas to processing equipment.
• Bucket elevators: Bucket elevators are used to vertically transport bulk materials such as clinker, cement, and additives within the plant. They consist of buckets attached to a rotating belt.
• Pneumatic conveying systems: These systems use air pressure to transport powdered or granular materials through pipelines. They are often used for transporting cement and fly ash.
• Screw conveyors: Screw conveyors are used for transporting materials horizontally or at an incline. They are commonly employed in cement
plants to move materials like cement clinker and granular additives.
• Palletisers and robotic systems: Automated systems are used for palletising cement bags or other packaging containers before dispatch.
• Rail and Tram Systems: In larger plants, railroads or trams may be used to transport materials over longer distances within the facility. - Finished product from plant to despatch
• Belt conveyors: Conveyor belts are used to transport the final cement product from the cement
mill to storage silos and from silos to the
packaging area.
• Silo storage: Silos are used to store cement before packaging or dispatch. They often have aeration systems to prevent material caking.
• Truck loadout systems: Loading systems are used to load cement into trucks for distribution. These systems often have weighing scales to ensure accurate loading.
• Railcar loadout systems: In some cases, cement may be transported in railcars. Loadout systems for railcars are used to fill them efficiently.
• Bulk handling equipment: For bulk cement transport, specialised equipment like bulk tanker trucks, bulk ship loaders and pneumatic conveyors may be used for large-scale transportation.
MATERIAL TRANSPORTATION AND EFFICIENCY
Efficient material transportation is integral to the effectiveness and production output of a cement plant. It exerts a direct influence on various facets of plant operations, and its proficiency can have a ripple effect on overall production. Firstly, the timely and dependable supply of raw materials from quarries or mines to the plant ensures a steady production flow. Any disruptions or delays in material delivery can disrupt production schedules, leading to downtime and a decrease in efficiency. Furthermore, material transportation is instrumental in preserving the quality and uniformity of raw materials, a critical factor in achieving the desired properties of the cement product. Proper blending and mixing of these materials, made feasible by streamlined transport systems, are essential.
“We have a process of quality checking for every belt that is manufactured at our end. The key to maintaining quality is inspection of every belt that is dispatched from our company. Our in-house laboratory helps us keep a check on quality maintenance,” says AP Singh, Executive Director, Continental Conveyors Private Limited.
“Maintenance of the belts or requirement of change depends from plant to plant. If the establishment is good and follows all protocols, the requirement for changing the belts is lesser. If the maintenance of systems and processes are not good, then the requirement of changing or getting maintenance done for the belts is high as they are made of softer materials and may be classified as one of the weakest materials in the cement plants,” he adds.
Energy consumption also ties closely to material transportation efficiency. Inefficient systems, such as long conveyor belts with excessive friction or poorly designed pneumatic conveying setups, can lead to wasteful energy consumption and increased operational costs. Additionally, the time it takes for raw materials to traverse various processing stages within the plant hinges on effective material transportation. Faster, more dependable transport systems can shorten processing times, increase throughput, and enhance overall production efficiency. Efficient material handling also ensures that processing equipment, including crushers, mills, and kilns, receive a consistent supply of raw materials at the required rates, minimising equipment downtime due to shortages or blockages.
Effective material transport also facilitates inventory management, reducing the likelihood of excess or insufficient stockpiles of raw materials, which can lead to inefficiencies, storage complications, and extra expenses. Quality control is another key aspect, as material transportation impacts the quality of the final cement product. Proper handling,
blending, and storage of clinker and additives are vital for achieving the desired cement quality and minimising waste. Furthermore, efficient dust and emission control measures are necessary for environmental compliance and avoiding regulatory issues.
Lastly, operational costs, encompassing maintenance, energy and labour expenses, are profoundly affected by material transportation efficiency. Optimising these processes can reduce these costs and bolster overall operational efficiency. Additionally, a well-designed and maintained material handling system contributes to a safe working environment, promoting plant safety.
AUTOMATION IN MATERIAL TRANSPORTATION
The implementation of material transportation and handling automation in cement plants offers a multitude of benefits that contribute to the overall efficiency and effectiveness of operations.
Firstly, automation significantly enhances efficiency by eliminating human errors and optimising processes, resulting in increased operational efficiency and higher throughput rates. Secondly, it leads to substantial cost reductions as it reduces labour costs,
minimises energy consumption, and lowers maintenance expenses, thus improving the plant’s financial viability.
Furthermore, automation prioritises safety by removing workers from potentially hazardous environments and minimising the risk of accidents. This not only ensures the well-being of plant personnel but also safeguards the plant’s reputation and productivity. Additionally, automation plays a pivotal role in maintaining consistent product quality.
Precise control over material handling processes guarantees that the final cement product adheres to stringent quality standards, ultimately satisfying customer expectations.
Lastly, automation in material transportation and handling aligns with environmental compliance efforts. By effectively controlling emissions and mitigating dust, it helps cement plants adhere to environmental regulations, contributing to sustainability and minimising the plant’s environmental
footprint. In essence, these benefits underscore the significance of material transportation and handling automation as a fundamental aspect of modern cement plant operations.
CONCLUSION
The efficient handling and transportation of materials in cement manufacturing plants are vital for their productivity, cost-effectiveness and environmental compliance. Automation technologies have emerged as key enablers in this context, offering a range of benefits. These include improved operational efficiency, cost reduction, enhanced safety, consistent product quality and environmental compliance. Automation has revolutionised the way cement plants manage materials, making them more competitive, sustainable, and efficient in an increasingly demanding industry. Embracing automation in material handling is not just a trend; it is a necessity for cement plants to thrive in the modern era.
–Kanika Mathur
You may like
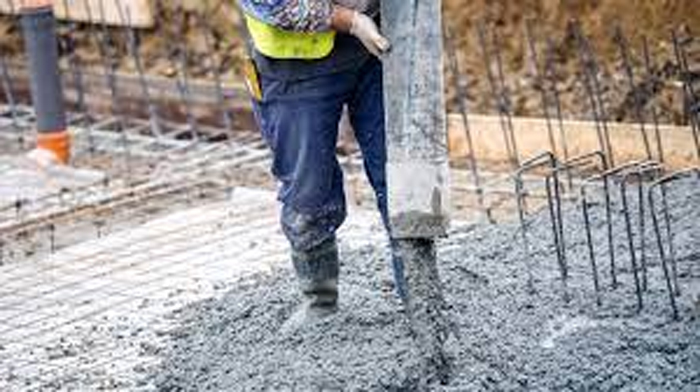
Tamil Nadu is set to host one of India’s five national carbon capture and utilisation (CCU) testbeds, aimed at reducing CO2 emissions in the cement industry as part of the country’s 2070 net-zero goal, as per a news report. The facility will be based at UltraTech Cement’s Reddipalayam plant in Ariyalur, supported by IIT Madras and BITS Pilani. Backed by the Department of Science and Technology (DST), the project will pilot an oxygen-enriched kiln capable of capturing up to two tonnes of CO2 per day for conversion into concrete products. Additional testbeds are planned in Rajasthan, Odisha, and Andhra Pradesh, involving companies like JK Cement and Dalmia Cement. Union Minister Jitendra Singh confirmed that funding approvals are underway, with full implementation expected in 2025.
Image source:https://www.heavyequipmentguide.ca/
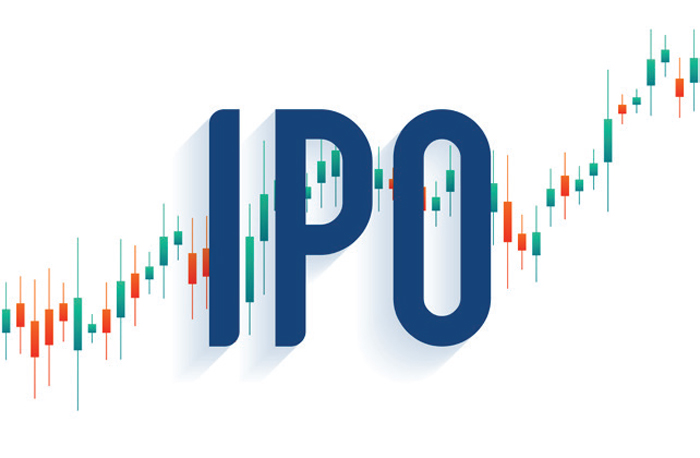
JSW Cement has set the price range for its upcoming initial public offering(IPO) at US$1.58 to US$1.67 per share, aiming to raise approximately US$409 million. As reported in the news, around US$91 million from the proceeds will be directed towards partially financing a new integrated cement plant in Nagaur, Rajasthan. Additionally, the company plans to utilise US$59.2 million to repay or prepay existing debts. The remaining capital will be allocated for general corporate purposes.
Concrete
Cement industry to gain from new infrastructure spending
Published
1 month agoon
July 24, 2025By
admin
As per a news report, Karan Adani, ACC Chair, has said that he expects the cement industry to benefit from the an anticipated US$2.2tn in new public infrastructure spending between 2025 and 2030. In a statement he said that ACC has crossed the 100Mt/yr cement capacity milestone in April 2025, propelling the company to get closer to its ambitious 140Mt/yr target by the 2028 financial year. The company’s capacity corresponds to 15 per cent of an all-India installed capacity of 686Mt/yr.
Image source:https://cementplantsupplier.com/cement-manufacturing/emerging-trends-in-cement-manufacturing-technology/