Concrete
Greener energy has a positive impact on manufacturing
Published
2 years agoon
By
admin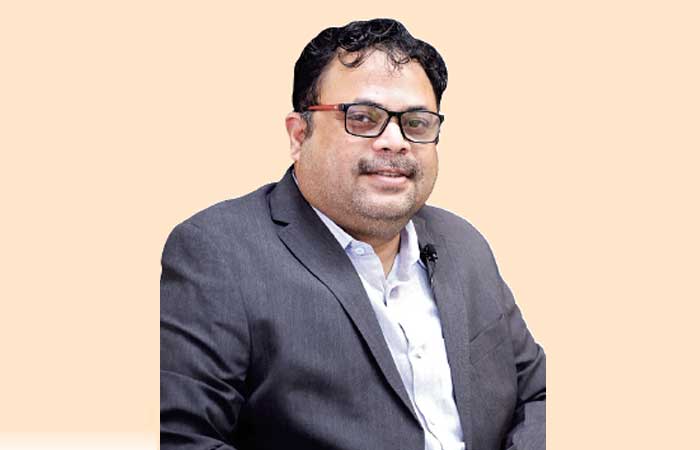
Sameer Kumar Pujari, Senior General Manager, JK Cement, elaborates on the role played by technology, alternative raw materials, cost, infrastructure and local regulations in making cement manufacturing process more energy efficient.
Tell us about the role of energy in the manufacturing of cement? What is the volume of your organisation’s energy consumption?
The role of energy in the manufacturing of cement is significant as it is one of the most energy-intensive industries globally. The production of cement involves several energy-intensive processes, from the extraction and crushing of raw materials to production of clinker and finally converting it into cement.
The production of cement consumes large quantities of energy in the form of thermal and electrical. This requires approximately 3.2 GJ to 5.0 GJ of energy per tonne of clinker produced. As an energy intensive industry, thermal energy used in the cement industry accounts for about 20–25 per cent of the production cost. The typical electrical energy consumption of a modern cement plant is about 70 KWh to 80 KWh per tonne of cement. In the manufacturing process, thermal energy is used mainly during the burning process, while maximum share of electrical energy is used for cement grinding.
Our SEC is approximately 61.8KWH/T cement and specific thermal energy is 3.18 GJ/tonne of cement. We are proud to share that our IU at Muddapur Karnataka and GU at Jhajjar, Haryana, are national leaders in energy and have been awarded by renowned organisations like Confederation of Indian Industry (CII). The source of energy in cement manufacturing is fossil fuels (coal, oil and natural gas) and alternative fuels (biomass/waste material/municipal waste etc.).
Other than above, we also use renewable energy solar/wind, WHRS and grid power to produce cement.
What are the various modes of energy sources used by your organisation for its manufacturing needs?
We use fossil fuels as the energy source for manufacturing needs. This includes coal, oil, and natural gas, which are burned in kilns to generate the heat necessary for the production process. We are also utilising alternative fuels to reduce usage of fossil fuels and promote sustainable practices. These alternative fuels can include RDF, biomass, such as rice/mustard husk or agricultural waste as well as waste materials like shredded tires or sewage sludge. By using these alternative fuels, we are not only progressing towards carbon neutrality but also contributing to waste management efforts.
We are using solar, wind and WHRS, too. We are procuring renewable energy through open access. Our capacity in WHRS is 62 MW, solar is 20 MW and we are progressing towards the goal of green cement by 2030. Our Muddapur, Karnataka, plant has achieved 100 per cent renewable energy uses at zero grid consumption through open access.
Which of the said energy sources yields maximum productivity for the plant and which yields the least?
The productivity of different energy sources for cement plants can vary depending on various factors such as technology being used, availability, cost, infrastructure and local regulations. Here are some examples:
Fossil fuels (e.g., coal, oil, and natural gas): Traditionally been the primary energy source for cement production due to their high energy content. However, they contribute significantly to carbon emissions and are considered non-renewable resources.
Biomass: Biomass, such as agricultural residues or dedicated energy crops, can be used as an alternative fuel source in cement production. Its productivity can vary depending on the availability and sustainability of biomass feedstock.
Waste materials: Certain waste materials, such as shredded tires or municipal solid waste, can be used as alternative fuels in cement kilns. The productivity of waste materials as an energy source depends on their calorific value, availability, and proper waste management practices.
Renewable energy sources: Renewable energy sources like solar, wind or geothermal power can be utilised to generate electricity for cement plants. Their productivity depends on factors such as location, resource availability and the ability to integrate them into the plant’s
energy infrastructure.
It is important to note that each cement plant may have unique circumstances and considerations when choosing an energy source. The optimal solution often involves a combination of different energy sources and technologies to achieve maximum productivity while minimising environmental impact.
What are the alternative energy sources that are being adapted by the cement industry and your organisation?
Generally fossil fuels such as coal, petroleum coke and natural gas provide the thermal energy required for the cement industry. With increasing economic benefits in usage of alternative fuel (AF) over conventional fuels gives high thrust on usage of AF. Other factors, which give a push to usage of AF, are limited resources of fossil fuel and environmental concerns. AF covers all non-fossil fuels and waste from other industries including tire-derived fuels, biomass residues, sewage sludge and different commercial wastes. The kiln used in cement manufacturing is able to burn a wide range of materials due to the long exposure time at high temperatures (up to 1400oC), intrinsic ability of clinker to absorb and lock contaminants into the clinker and the alkalinity of the kiln environment. Materials like waste oils, plastics, waste tires and sewage sludge are being adopted as alternative fuels by the cement industries. Biomass waste and spent pot linings produced in aluminium smelters are also identified as potential alternative fuels for the cement industry.
Our organisation uses almost all kinds of plastic wastes, non-hazardous and hazardous waste, and biomass. We have a dedicated AFR feeding system in our plants. We initially focused on using plastic waste, shredded RDF. Slowly and gradually, we increased our capacity and started using hazardous materials also. For the processing of hazardous waste, we needed impregnation material like biomass such as rice husk, saw dust, wood chips, etc. So, we started utilising them in smaller proportions. And with the experience so far, now we are consuming around 20 per cent to 25 per cent of hazardous solid waste, 40 per cent to 50 per cent MSW/RDF waste, and up to 25 per cent non-hazardous solid wastes.
What is the impact of greener energy sources on the productivity and cost of cement manufacturing?
Greener energy has a positive impact on manufacturing, including commercial and technical aspects. Here are some potential impacts:
• Productivity: Greener energy sources have a positive impact on the productivity of cement manufacturing. For example, using alternative fuels like biomass or waste materials can
provide a reliable and consistent source of heat for kilns, ensuring a stable production process. This can help reduce downtime and improve overall productivity.
• Cost: The cost implications of using greener energy sources in cement manufacturing can also vary. In some cases, alternative energy sources may be more cost-effective compared to traditional fossil fuels as AF gives additional revenue to consumers of AF. Additionally, utilising waste materials as alternative fuels can reduce waste disposal costs for cement plants.
• Energy efficiency: Greener energy sources often promote energy efficiency in cement manufacturing. For example, using renewable energy sources like solar or wind power can reduce reliance on fossil fuels and decrease energy consumption. This can result in cost savings and improved overall efficiency.
• Environmental impact: One of the key benefits of greener energy sources in cement manufacturing is the reduction in environmental impact. By transitioning to alternative fuels or renewable energy sources, cement plants can significantly reduce greenhouse gas emissions and air pollution associated with traditional fossil fuel combustion. This can contribute to environmental sustainability goals and help meet regulatory requirements.
It is important to note that the specific impact on productivity and cost will depend on the individual circumstances of each cement organisation, including factors such as location, availability of resources, technological capabilities and government policies or incentives.
How does automation and technology help in optimising the use of energy in cement plants?
Automation and technology play a pivotal role in optimising the use of energy in cement plants. We are using VFD, Smart MCC, Sensors, Integrated Load Management System, Energy Monitoring System and Smart Lighting System for effectively optimising the use of energy in our organisation.
Here are some ways which helps to reduce the energy:
• Energy monitoring and control: Automation systems can continuously monitor energy consumption in various parts of the cement plant, such as kilns, mills, and crushers. This real-time data allows operators to identify pilferage processes or equipment and optimise energy usage.
• Process optimisation: Advanced control systems and predictive analytics can optimise the cement manufacturing process to minimise energy consumption. By analysing data from various sensors and instruments, these technologies can identify opportunities for energy savings and automatically adjust parameters to achieve optimal efficiency.
• Energy management systems: Automation systems can integrate with energy management systems to provide a holistic view of energy usage across the entire plant. This allows operators to track energy performance and accordingly set targets, and implement energy-saving measures effectively.
• Load management: Automation systems can optimise the scheduling and sequencing of equipment to ensure a balanced load distribution, reducing peak demand and improving overall energy efficiency. For example, by coordinating the operation of kilns, mills, and other machinery, the system can minimise energy wastage during periods of low demand.
• Energy recovery: Automation technology can facilitate the implementation of energy recovery systems in cement plants. For instance, waste heat from kilns can be captured and used to generate electricity or provide heat for other processes, reducing the reliance on external energy sources.
• Equipment optimisation: Automation systems can monitor the performance of individual equipment and identify inefficiencies or malfunctions that may contribute to excessive energy consumption. By providing real-time alerts and diagnostics, operators can take corrective actions promptly, ensuring optimal equipment performance and energy usage.
Overall, automation and technology enable cement plants to have better visibility, control and optimisation of energy usage. This leads to improved energy efficiency, cost savings and reduced environmental impact.
What are the major challenges your organisation faces in managing the energy needs?
We are facing challenges of imposition of power curtailment from grid mostly at our Rajasthan-based plants:
• Grid disturbances and power outages
• There is high volatile market and heavy fluctuations in fuel sourcing
• Energy cost volatility: Cement production is highly energy-intensive, and the cost of energy can fluctuate significantly. This makes it challenging to plan and budget for energy needs effectively an increase in the prices of fossil fuel
would adversely impact the industry, leading to an increase in production costs, however we focused on driving optimisation of fuel mix, energy efficiency and use of alternative fuel to mitigate this
• Ageing infrastructure: To upgrade or replace the ageing infrastructure/ systems can be expensive and may require significant downtime. However, we have completed the brownfield modernisation of our Nimbahera Line-3, with the kiln now capable of producing 6,500 TPD, against the earlier capacity of 5,000 TPD. The brownfield projects that have been undertaken over the past few years have been delivering greater efficiencies in the form of reduced power and fuel consumption and increased WHR.
Tell us about the compliance and standards followed by you to maintain energy use and efficiency in the organisation.
Some of the key regulations and standards include:
• ISO 50001: This international standard provides a framework for organisations to establish, implement, maintain, and improve an energy management system. We are ISO 50001 certified company and regularly enhance our energy performance, identify energy-saving opportunities and comply with energy management requirements.
• PAT Compliance: PAT is a mechanism for improvements in energy efficiency of energy intensive industries. Specific high energy intensive industries are identified as Designated Consumers (DC) within certain key sectors, who are required to appoint an energy manager, file energy consumption returns every year and conduct mandatory energy audits regularly. The key tasks in the PAT mechanism is to set the methodology for deciding the Specific Energy Consumption (SEC) norms for each designated consumers in the baseline year and in the target years, devise verification process for SEC, finding ways of issuing the Energy Savings Certificates, operationalisation of the trading process for ESCert in addition to the compliance and reconciliation process for ESCert.
To ensure compliance with these regulations and standards, JK Cement regularly monitors our energy consumption, implements energy management systems, conducts energy audits, invests in energy-efficient technologies, and reports the emissions and energy performance to relevant authorities. Additionally, we collaborate with industry associations, research institutions and government agencies to stay
updated on evolving regulations and best practices in energy management.
How often are audits done to ensure optimum use of energy? What is the suggested duration for the same?
• We conduct energy audits every year as a part of energy management practices. This allows us to assess the energy performance, identify
areas for improvement and implement energy-saving measures.
• We have formed internal management teams across our plants where we closely monitor
our energy consumption on a daily basis. We fix our best targets across the locations
and further compare and revise our targets to further optimisation.
What kind of innovations in the area of energy consumption do you wish to see in the cement industry?
Some potential innovations in the area of energy consumption that we may wish to see in the cement industry:
• Alternative fuel sources: Increased utilisation of alternative fuels, such as biomass, waste materials, or renewable energy sources, can reduce reliance on fossil fuels and lower carbon emissions.
• Energy-efficient technologies: The adoption of advanced technologies, such as more efficient kilns, improved heat recovery systems, and optimised grinding processes, can help reduce energy consumption in cement production.
• Carbon capture and utilisation: Implementing carbon capture, storage, and utilisation (CCUS) technologies can help capture and store carbon dioxide emissions from cement plants or utilise them in other industrial processes.
• Process optimisation through AI: Continuous process optimisation through AI data analytics, machine learning, and automation can identify areas of inefficiency and enable real-time adjustments to optimise energy consumption.
• Circular economy practises: Adopting circular economy principles, such as recycling and reusing waste materials or by-products from cement production, can reduce resource consumption and minimise environmental impact.
• Collaborative research and development: Encouraging collaboration between industry stakeholders, researchers and governments can drive innovation in energy-efficient cement production technologies and practices.
• We want to innovate to produce entirely green cement with sustainability and to achieve our net zero target by 2030.
• Cement manufacturing with an alternative of fly ash and lesser water curing requirements also plants with less heat consumption during clinker production such as in LC3 cement.
-Kanika Mathur
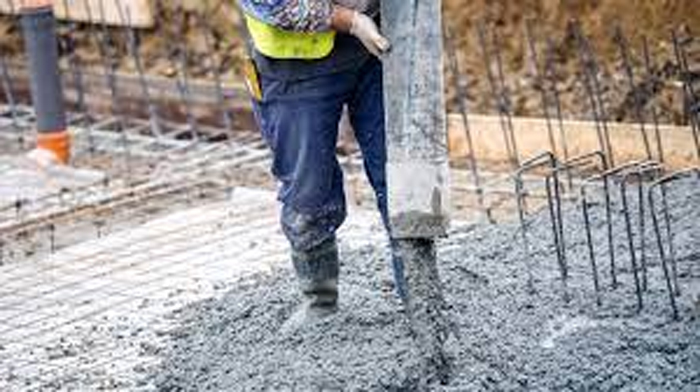
Tamil Nadu is set to host one of India’s five national carbon capture and utilisation (CCU) testbeds, aimed at reducing CO2 emissions in the cement industry as part of the country’s 2070 net-zero goal, as per a news report. The facility will be based at UltraTech Cement’s Reddipalayam plant in Ariyalur, supported by IIT Madras and BITS Pilani. Backed by the Department of Science and Technology (DST), the project will pilot an oxygen-enriched kiln capable of capturing up to two tonnes of CO2 per day for conversion into concrete products. Additional testbeds are planned in Rajasthan, Odisha, and Andhra Pradesh, involving companies like JK Cement and Dalmia Cement. Union Minister Jitendra Singh confirmed that funding approvals are underway, with full implementation expected in 2025.
Image source:https://www.heavyequipmentguide.ca/
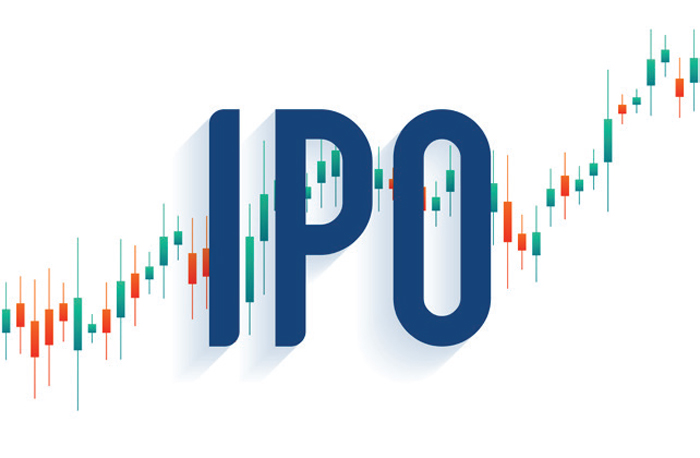
JSW Cement has set the price range for its upcoming initial public offering(IPO) at US$1.58 to US$1.67 per share, aiming to raise approximately US$409 million. As reported in the news, around US$91 million from the proceeds will be directed towards partially financing a new integrated cement plant in Nagaur, Rajasthan. Additionally, the company plans to utilise US$59.2 million to repay or prepay existing debts. The remaining capital will be allocated for general corporate purposes.
Concrete
Cement industry to gain from new infrastructure spending
Published
4 weeks agoon
July 24, 2025By
admin
As per a news report, Karan Adani, ACC Chair, has said that he expects the cement industry to benefit from the an anticipated US$2.2tn in new public infrastructure spending between 2025 and 2030. In a statement he said that ACC has crossed the 100Mt/yr cement capacity milestone in April 2025, propelling the company to get closer to its ambitious 140Mt/yr target by the 2028 financial year. The company’s capacity corresponds to 15 per cent of an all-India installed capacity of 686Mt/yr.
Image source:https://cementplantsupplier.com/cement-manufacturing/emerging-trends-in-cement-manufacturing-technology/