Concrete
A Quest for Green Energy
Published
2 years agoon
By
admin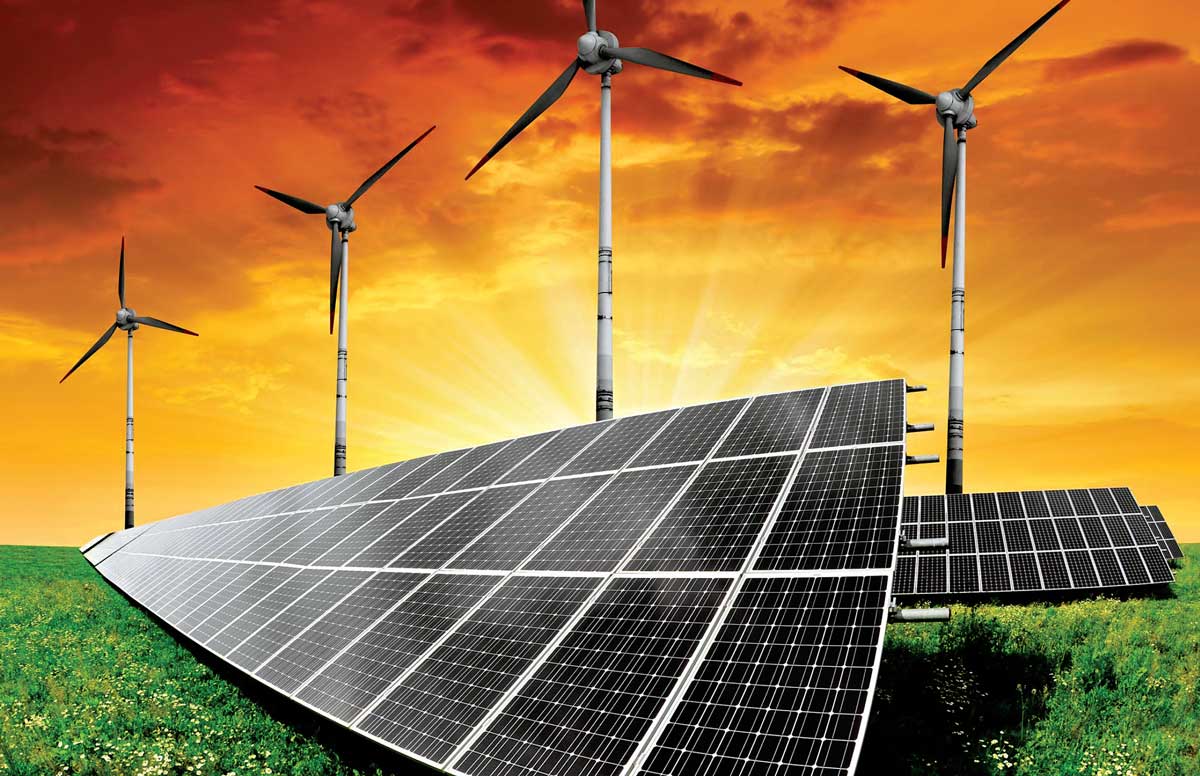
Efforts to mitigate the environmental impact of cement production have led companies to look for innovative solutions. ICR delves into challenges and opportunities of energy-efficiency in the cement industry, and the pivotal role it plays in the broader drive towards a greener future.
The world is in a transition phase and energy is central to it. India has been responsible for almost 10 per cent of the increase in global energy demand since the year 2000. India’s energy demand in this period has almost doubled, pushing the country’s share in global demand up to 5.7 per cent in 2013 from 4.4 per cent at the beginning of the century.
The demand is expected to increase to about 1250 million tonnes of oil equivalent (Mtoe), as estimated by the International Energy Agency, to 1500 Mtoe (estimated in the Integrated Energy Policy Report) in 2030. India’s energy consumption is expected to grow rapidly.
Yet the increase in domestic energy production is far below India’s consumption needs. By 2040, more than 40 per cent of primary energy supply will be imported, up from 32 per cent in 2030. It may also be noted that no country in the world has been able to achieve a Human Development Index of 0.9 or more without an annual energy supply of at least 4 toe per capita. Consequently, there is a large latent demand for energy services that needs to be fulfilled in order for people to have reasonable incomes and a decent quality of life.
As per the Central Electricity Authority (CEA) as on May 2023, the Installed Generation Capacity is 4,17,668 MW of which 56.8 per cent is derived from fossil fuels and 43 per cent is derived from non-fossil fuel sources. The electricity generation target for the year 2023-24 was fixed at 1750 BU consisting of 1324.110 BU Thermal; 156.700 BU Hydro; 46.190 Nuclear; 8 BU Import from Bhutan and 215 BU RES (Excl. Large Hydro).
The Government of India has undertaken a two-pronged approach to cater to the energy demand of its citizens while ensuring minimum growth in CO2 emissions, so that the global emissions do not lead to irreversible damage to the earth system. The Energy Conservation Act (EC Act) was enacted in 2001 with the goal of reducing the energy intensity of the Indian economy. The Bureau of Energy Efficiency (BEE), a statutory body under the Ministry of Power, is responsible for spearheading the improvement of energy efficiency in the economy through various regulatory and promotional instruments.
Sanjay Joshi, Chief Manufacturing Officer, Nuvoco Vistas Corp, says, “Nuvoco’s Integrated cement plants are covered under the Perform, Achieve, and Trade (PAT) scheme of the Bureau of Energy Efficiency (BEE) by the Ministry of Power, Government of India for reducing its specific energy consumption year on year. We have a dedicated energy manager in each of our units who is certified to monitor the plant’s energy use and continuously improve it.”
“Nuvoco is committed to adherence to rigorous compliance and standards that prioritise energy use and efficiency, exemplified by our sustainability agenda – Protect Our Planet,” he adds.
ENERGY IN THE CEMENT INDUSTRY
The cement industry is known for its high energy consumption, primarily due to the energy-intensive processes involved in manufacturing cement. Energy is used in various stages of cement production, and its efficient utilisation is crucial for both economic and environmental reasons.
It starts with the energy required for mining and quarrying raw materials like limestone and clay. Subsequent stages involve crushing, grinding, and preheating the raw materials, all of which demand significant electrical energy. The most energy-intensive step is clinker production, where raw materials are heated to extremely high temperatures in rotary kilns, necessitating the use of fossil fuels like coal or natural gas. Cement grinding, another electricity-intensive phase, involves finely grinding clinker with gypsum.
“We use fossil fuels as the energy source for manufacturing needs. This includes coal, oil, and natural gas, which are burned in kilns to generate the heat necessary for the production process. We are also utilising alternative fuels to reduce usage of fossil fuels and promote sustainable practices. These alternative fuels can include RDF, biomass, such as rice/mustard husk or agricultural waste as well as waste materials like shredded tires or sewage sludge. By using these alternative fuels, we are not only progressing towards carbon neutrality but also contributing to waste management efforts,” said Sameer Kumar Pujari, Senior General Manager,JK Cement.
Even the packing and shipping stages require energy for material handling and transportation. To mitigate its environmental impact and operational costs, the cement industry is actively adopting strategies such as the use of alternative fuels, energy-efficient equipment, waste heat recovery and process optimisation to reduce energy consumption and carbon emissions while maintaining product quality.
In 2022, the size of the global cement market reached US$ 363.4 billion, and it is expected to grow at a CAGR of 5.4 per cent during 2023 – 2028 to reach US$ 498.23 billion by 2028. Being the second largest cement producer in the world after China, India contributes over 8 per cent to the global installed capacity in cement production. India has potentially rich deposits of limestones in different regions of the country essentially required for cement production. In terms of installed capacity, India’s Southern region (33 per cent) has the largest market share in cement production followed by North (22 per cent), East (19 per cent), West (13 per cent) and Central (13 per cent).
The energy sector aims to achieve an ambitious target of 450 GW of solar and wind in 2030 as it has pledged to reach carbon neutrality by 2070. What makes this target seem achievable is that the renewable capacity of the Indian energy sector (excluding large hydro) overtook 100 GW in 2021. While three quarters of the energy requirement is still met by fossil fuels, the overall consumption of energy has gone down by 5 per cent in 2021.
Cement plays a vital role in building the economy of a nation. The sector is largely dominated by players with large manufacturing capacities, making the cement industry one of the largest in the country and one that is energy intensive. The Perform Achieve and Trade (PAT) scheme of the Ministry of Power, Government of India has so far covered 126 numbers of cement plants in India targeting to reduce specific energy consumption since its inception from 2012 onwards.
The Bureau of Energy Efficiency states that based on the threshold defined, 85 numbers of cement plants were included as DCs and their cumulative energy consumption was 15.01 million Mtoe in PAT Cycle-1. Based on their specific energy consumption level, these DCs were given SEC target reduction of an average 5.43 per cent resulting in 0.815 Mtoe energy consumption reduction in absolute terms. The cement sector constituted 12.19 per cent of the overall energy saving target under PAT Cycle-1.
The total savings achieved by the cement sector covering 75 numbers of designated consumers in PAT Cycle-1 is 1.48 Mtoe, which is 0.665 Mtoe in excess of the target. At present, the energy consumption of these cement units as designated consumers is 23.246 Mtoe. The target given for them from PAT Cycle –II onwards is 0.94 million tonnes of oil equivalent.
AUTOMATION AND TECHNOLOGY
Automation and technology play a pivotal role in the cement sector’s pursuit of energy efficiency. These innovations are instrumental in optimising processes, reducing energy consumption and enhancing overall sustainability. Technology works in many ways to help the cement industry achieve energy efficiency.
Advanced process control (APC) systems use sensors, data analytics, and machine learning algorithms to continuously monitor and adjust production processes in real-time. These systems optimise parameters like kiln temperature, fuel combustion, and material flow to ensure efficient clinker production while minimising energy waste.
Internet of Things (IoT) technology is employed to gather data from various sensors placed throughout the production line. This data is then analysed to identify energy inefficiencies and areas for improvement. For instance, temperature and pressure sensors help maintain optimal conditions, reducing energy consumption during the clinker production process.
Energy Management Systems (EMS) and software helps cement plants monitor and manage their energy consumption. It provides insights into energy use patterns, identifies anomalies, and enables proactive energy-saving measures. EMS can also forecast energy demand and integrate renewable energy sources into the grid.
Predictive maintenance systems utilise sensors and data analysis to predict equipment failures before they occur. By preventing unexpected breakdowns and optimising maintenance schedules, these systems reduce downtime and ensure that machinery operates at peak energy efficiency.
Automation assists in the efficient management of alternative fuels and raw materials. Automated systems control the feeding and combustion of alternative fuels like biomass or waste-derived fuels, ensuring a stable and efficient energy source while reducing reliance on fossil fuels.
The adoption of energy-efficient machinery, such as high-efficiency motors, variable frequency drives (VFDs) and advanced kiln designs, significantly reduces energy consumption during the cement production process.
Automated waste heat recovery systems capture and reuse excess heat generated during clinker production. This recovered heat can be used for preheating raw materials or generating electricity, further improving energy efficiency.
Cement plants are increasingly adopting digital twin technology, which creates a virtual replica of the physical plant. This allows for simulations and testing of process improvements before implementation, reducing the risk of energy-inefficient changes.
Automation can manage the integration of renewable energy sources like solar panels and wind turbines into cement plant operations, maximising the use of clean energy and reducing dependence on fossil fuels.
Automation provides real-time energy monitoring and reporting tools that enable cement plants to track energy performance and identify opportunities for optimisation. This data-driven approach facilitates continuous improvement in energy efficiency. By embracing these technological advancements and incorporating automation into their operations, cement plants can achieve substantial energy savings, reduce greenhouse gas emissions.
According to the details on energy efficiency shared by Adani Cement, automation and technology play an instrumental role in optimising energy utilisation within cement plants. These advancements contribute to enhanced productivity and heightened system reliability, creating a stable manufacturing environment. The harmonious synergy between automation and technology facilitates the most efficient allocation of energy resources, minimising wastage and enhancing overall energy efficiency. In line with this, Adani Cement has implemented High-Level Control (HLC) systems for each kiln and cement mill circuit. These technologies not only streamline operations but also empower the company to respond proactively to energy consumption patterns.
EFFICIENCY IN ENERGY USE
Efficiency improvements in the cement industry are diverse and crucial for both sustainability and competitiveness. Energy management is a
primary focus, achieved through alternative fuels like biomass and waste-derived sources, coupled
with waste heat recovery during clinker production. Process optimisation, enabled by advanced control systems and predictive maintenance, fine-tunes operations like kiln and grinding processes, while upgrading to energy-efficient equipment further curtails energy consumption.
The adoption of alternative energy sources in the cement industry reduces carbon emissions but also enhances sustainability and helps cement companies meet environmental regulations and industry sustainability goals. However, the feasibility of using specific alternative energy sources may vary depending on the location, available resources and regulatory constraints.
Srivatsan Iyer, Global CEO, Hero Future Energies, presented his thoughts on the expectations from the G20 Summit in terms of Energy Transition Outlook: “At the upcoming G20 summit, we anticipate the reinforcement of a collective determination to quicken the pace of energy transition globally. It is absolutely critical that the G20 nations accelerate efforts in sharing advanced technologies and ensuring access to affordable financing from multilateral development banks and international finance institutions, especially for emerging economies. As we move towards a net-zero future, the critical role of new technologies like electrolysers, battery storage and carbon capture will become even more apparent.”
“We look forward to increased technological collaboration among G20 nations, establishing more resilient and open global markets, particularly in the emerging sector of green hydrogen. Our hope is for consensus, actionable strategies and a commitment to these crucial imperatives.”
CONCLUSION
The journey toward achieving energy efficiency in the cement industry is not merely a pursuit of environmental responsibility; it is a pathway to long-term sustainability and economic viability. As we confront the challenges posed by climate change and the imperative to reduce carbon emissions, the cement sector stands at a critical crossroads.
As the world moves toward a greener, more sustainable future, the cement industry’s dedication to energy efficiency not only safeguards the environment but also secures its place as a responsible and forward-thinking player in the global industrial landscape. It is a commitment that benefits not only the industry itself but also future generations and the planet we all call home.
- Kanika Mathur
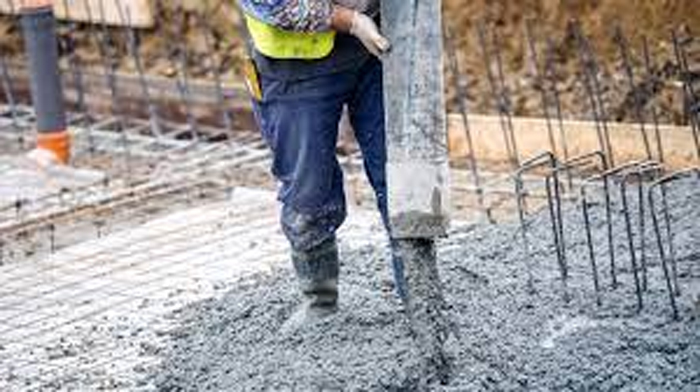
Tamil Nadu is set to host one of India’s five national carbon capture and utilisation (CCU) testbeds, aimed at reducing CO2 emissions in the cement industry as part of the country’s 2070 net-zero goal, as per a news report. The facility will be based at UltraTech Cement’s Reddipalayam plant in Ariyalur, supported by IIT Madras and BITS Pilani. Backed by the Department of Science and Technology (DST), the project will pilot an oxygen-enriched kiln capable of capturing up to two tonnes of CO2 per day for conversion into concrete products. Additional testbeds are planned in Rajasthan, Odisha, and Andhra Pradesh, involving companies like JK Cement and Dalmia Cement. Union Minister Jitendra Singh confirmed that funding approvals are underway, with full implementation expected in 2025.
Image source:https://www.heavyequipmentguide.ca/
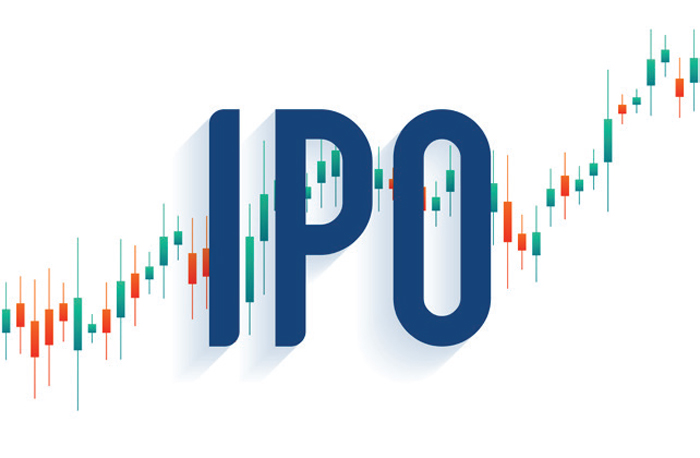
JSW Cement has set the price range for its upcoming initial public offering(IPO) at US$1.58 to US$1.67 per share, aiming to raise approximately US$409 million. As reported in the news, around US$91 million from the proceeds will be directed towards partially financing a new integrated cement plant in Nagaur, Rajasthan. Additionally, the company plans to utilise US$59.2 million to repay or prepay existing debts. The remaining capital will be allocated for general corporate purposes.
Concrete
Cement industry to gain from new infrastructure spending
Published
1 month agoon
July 24, 2025By
admin
As per a news report, Karan Adani, ACC Chair, has said that he expects the cement industry to benefit from the an anticipated US$2.2tn in new public infrastructure spending between 2025 and 2030. In a statement he said that ACC has crossed the 100Mt/yr cement capacity milestone in April 2025, propelling the company to get closer to its ambitious 140Mt/yr target by the 2028 financial year. The company’s capacity corresponds to 15 per cent of an all-India installed capacity of 686Mt/yr.
Image source:https://cementplantsupplier.com/cement-manufacturing/emerging-trends-in-cement-manufacturing-technology/