Concrete
From Grey to Green
Published
2 years agoon
By
admin
Green cement is no longer the future of the industry; it is the present. Manufacturing green cement is a complex process and the technical, economic and regulatory challenges involved are impregnable. However, they also provide the industry with a significant opportunity for innovation. ICR looks at the stumbling blocks and growth paths in the processing of green cement.
Green cement is a type of cement that is manufactured using eco-friendly and sustainable practices, with a focus on reducing carbon emissions and environmental impact. It is made by incorporating waste materials such as fly ash, slag and silica fumes, which are by-products of industrial processes, into the cement mixture. This process not only reduces the amount of waste that ends up in landfills but also reduces the carbon footprint of the cement manufacturing process.
In addition to reducing waste and carbon emissions, green cement also has other benefits over traditional cement. It has a lower water demand and a longer lifespan, which means it can be used for longer periods without needing to be replaced. Additionally, it can be manufactured using renewable energy sources such as solar and wind power, further reducing its environmental impact.
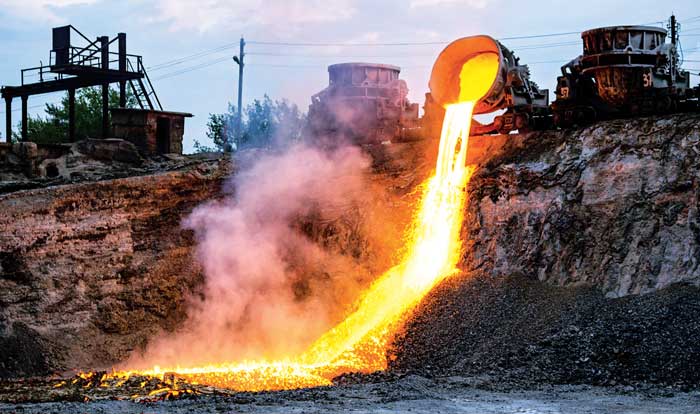
Waste from one industry is wealth for another as can be seen in the use of by-products such as fly ash, slag and silica fumes by the cement companies.
ROLE OF ALTERNATIVE FUELS
Alternative fuels play an important role in the cement manufacturing industry as they offer a more sustainable and eco-friendlier alternative to traditional fossil fuels such as coal and petroleum coke.
Alternative fuels, such as biomass, waste materials, and industrial by-products, have lower carbon content than traditional fossil fuels. By using these fuels, cement manufacturers can significantly reduce their carbon emissions and mitigate their impact on the environment. India is heavily dependent on imports for its fossil fuel requirements. By using alternative fuels, cement manufacturers can reduce their reliance on fossil fuels, which helps to promote energy security and reduce the country’s dependence on imports.
Cement manufacturers in India are using waste materials such as municipal solid waste, agricultural residues and industrial by-products as alternative fuels. This not only helps to reduce waste that would otherwise end up in landfills but also promotes a circular economy by utilising waste materials as a resource. Alternative fuels are often cheaper than traditional fossil fuels. By using alternative fuels, cement manufacturers can improve their
cost competitiveness and potentially lower their operating costs.
Kiran D Patil, Managing Director, Wonder Cement, says, “Our company is aligned with the country’s Net Zero policy and working towards achieving the targets through various initiatives such as using renewable energy, improving energy efficiency, and usage of industrial waste. Additionally, we are continuously working to reduce the environmental impact of our manufacturing process, including reducing water usage, minimising waste generation, and ensuring responsible sourcing of raw materials. We understand that sustainability is critical to the long-term success of our business and to the health of our plant. We are committed to doing our part to achieve a sustainable future. Our plan for the future is to use electrically operated vehicles for our plant operations.”
The use of alternative fuels in cement manufacturing in India offers numerous benefits, both in terms of sustainability and cost competitiveness. As such, the trend towards using alternative fuels is likely to continue and expand in the coming years.
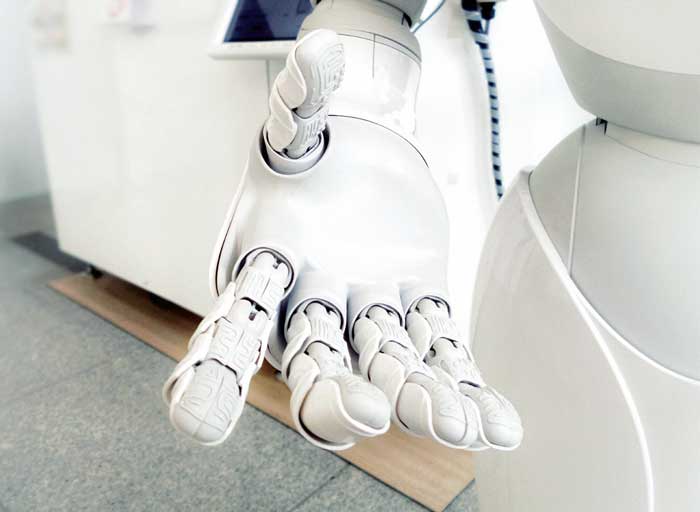
SUPPLEMENTARY CEMENTITIOUS MATERIALS
Supplementary Cementitious Materials (SCMs) can make cement more environmentally friendly and lower in carbon content in several ways:
- Reduced clinker content: Clinker, the primary component of cement, is responsible for a significant amount of carbon emissions during the manufacturing process. By replacing a portion of the clinker with SCMs, such as fly ash, slag, or silica fume, the overall carbon footprint of cement can be reduced.
“Reduction in Clinker to Cement Ratio through greater uptake of blended cement in all the key consumption segments – housing, government projects, precast cement products and ready-mix concrete. This involves developing new blended cement to suit the requirements in segments where OPC is still preferred for specific reasons, and to adopt a higher percentage of alternative fuels in the process,” says D L Kantham, Director – Technical, Penna Cement. - Improved workability: SCMs can improve the workability of cement, which reduces the need for additional water or chemical admixtures. This not only improves the performance of the concrete but also reduces the carbon emissions associated with the production of these additives.
- Increased durability: SCMs can improve the durability of concrete by reducing the porosity and increasing the strength of the material. This reduces the need for maintenance and repairs, which in turn reduces the carbon emissions associated with these activities.
- Reduced waste: SCMs are often industrial by-products or waste materials that would otherwise be disposed of in landfills. By using these materials as a partial replacement for clinker, cement manufacturers can reduce waste and promote a circular economy.
- Improved thermal performance: SCMs can improve the thermal performance of concrete, which reduces the need for additional insulation and reduces the energy consumption associated with heating and cooling.

Indian cement industry is committed to reducing its CO2 emissions intensity by 35 per cent by 2030, compared to 2005 levels
The use of supplementary cementitious materials in cement manufacturing can significantly reduce the carbon footprint of the cement and promote sustainable practices. By using these materials, cement manufacturers can reduce waste, improve the durability and workability of the concrete and promote a circular economy.
ROLE OF AUTOMATION AND TECHNOLOGY
Automation and technology can play a significant role in manufacturing eco-friendly cement by reducing the energy consumption and carbon emissions associated with traditional cement production processes.
Dr S B Hegde, Professor, Jain University and Visiting Professor, Pennsylvania State University, USA, in his article Using AI to Achieve Operational Excellence mentions, “AI will be essential in achieving environmental sustainability goals, not just in terms of reducing emissions but also in terms of energy management and optimisation. As a result, operating costs and profit margins will immediately improve, and new business models for high-tech, low-CO2 cements will be possible.”
“Tying analytics and APC together will enable re-modelling and tuning in an automated way and optimising additional variables. Many technology suppliers are also working on utilising data collected through cement information management systems to address challenges that have not yet been tackled such as cement quality prediction,” he adds.
One way that automation and technology can achieve this is through the use of alternative fuels and raw materials. For example, the use of waste materials such as fly ash, slag and rice husk ash can significantly reduce the amount of CO2 emitted during cement production. Automation can help to monitor and control the process of adding these materials to the cement mix, ensuring consistent quality and reducing waste.
Additionally, automation can be used to optimise the cement manufacturing process, reducing the energy consumption and CO2 emissions associated with traditional methods. This can include using advanced sensors and control systems to monitor and adjust the temperature, pressure, and other key parameters in the production process, optimising the use of energy and resources.
Another way that automation and technology can contribute to eco-friendly cement production is through the use of digital tools such as machine learning and artificial intelligence. These tools can help to predict and prevent equipment failures, optimise energy usage, and improve overall process efficiency.
“Data Analytics has been there in the cement industry for quite some time. The industry is quite standardised with different product lines. The overall process is extremely complex: you have mines, conveyor belts moving raw materials, stockyards, kilns, grinding and so on. Various customers, especially the big players, have had solutions in place to
provide data analytics,” says Manish Chordia, Regional Sales Manager – Cement, South Asia and Africa, ABB.
“When you move to the next step of AI, we have solutions relating to assets and asset reliability. We collect various data like device temperatures, loading patterns, ambient temperatures and the happenings inside the cabinets to do AI-based analytics,”
he adds.
Overall, automation and technology have the potential to have a significant effect on the production of eco-friendly cement, reducing the environmental impact of this important industry while also improving efficiency and quality.
NET ZERO JOURNEY
The Indian cement industry is one of the largest and most energy-intensive industries in the country, accounting for around seven per cent of the world’s total cement production. Cement manufacturing is a highly carbon-intensive process that involves burning fossil fuels, emitting large amounts of CO2 and other GreenHouse Gases. However, the Indian cement industry has been making significant efforts towards achieving Net Zero carbon emissions and promoting green cement.
The Net Zero journey of the Indian cement industry started with the launch of the Cement Sustainability Initiative (CSI) by the World Business Council for Sustainable Development (WBCSD) in 2002. The initiative aimed to reduce CO2 emissions from cement production by improving energy efficiency, using alternative fuels, and developing low-carbon cements.
In 2018, the Indian cement industry committed to reducing its CO2 emissions intensity by 35 per cent by 2030, compared to 2005 levels, through the use of alternative fuels, waste heat recovery, and other innovative technologies. This commitment was made under the Cement Sustainability Initiative’s ‘Getting the Numbers Right’ (GNR) framework.
Dr Arvind Bodhankar, Executive Director, ESG and CRO, Dalmia Bharat, says, “Dalmia Cement has been doing its part and is the pioneer in setting up the target of Net Zero in the industry. We announced that we will become carbon negative by 2040.
We are the first cement company globally to have such an ambitious target. And, we have been working in all spheres of its subject to meet our five-year interim targets.”
“So far, we have been progressing well and ahead of our carbon negative roadmap targets. As compared to the target of 485 NetKgCO2/tonne of cementitious, we have already achieved 463 kgCO2/tonne of cementitious in FY23, which is more than 4.5 per cent reduction below the carbon negative target. All this has been taking place voluntarily without any regulatory push,” he adds.
To achieve this target, the Indian cement industry has been implementing various measures, such as use of alternative fuels, energy efficiency, carbon capture and utilisation and more.
The Indian cement industry’s efforts towards Net Zero carbon emissions and promoting green cement have gained significant momentum in recent years. Several cement companies in India, such as Dalmia Cement, ACC and UltraTech Cement, have set ambitious targets for achieving Net Zero carbon emissions by 2050.
GOVERNMENTAL REGULATIONS
The Indian government has introduced various regulations and policies to promote sustainable practices and reduce carbon emissions and waste in the cement manufacturing industry. Here are some of the key regulations that cement manufacturers in India need to comply with:
- PAT Scheme: The Perform, Achieve and Trade (PAT) Scheme is a market-based mechanism that aims to improve energy efficiency in energy-intensive industries such as cement manufacturing. Under this scheme, cement manufacturers are required to meet specific energy consumption targets, failing which they may have to pay penalties.
- National Action Plan on Climate Change: The National Action Plan on Climate Change (NAPCC) aims to mitigate the impacts of climate change by reducing greenhouse gas emissions. The cement manufacturing industry is included in this plan, and cement manufacturers are required to reduce their carbon emissions and implement sustainable practices.
- Solid Waste Management Rules: The Solid Waste Management Rules (2016) require industries to promote the principles of reduce, reuse, and recycle in their operations. Cement manufacturers are required to use alternative fuels such as biomass, agricultural waste, and municipal solid waste as a fuel source in their kilns.
- Cement Industry Standards: The Bureau of Indian Standards (BIS) has introduced standards for cement manufacturing, including requirements for energy consumption, quality, and emissions. Cement manufacturers are required to comply with these standards to ensure that their operations are sustainable and eco-friendly.
- Emission Standards for Cement Plants: The Ministry of Environment, Forest and Climate Change has introduced emission standards for cement plants, including requirements for particulate matter, sulphur dioxide and nitrogen oxides emissions. Cement manufacturers are required to comply with these standards to minimise their impact on the environment.
- The Indian government has introduced a range of regulations and policies to promote sustainable practices in the cement manufacturing industry, including reducing carbon emissions and waste. Cement manufacturers are required to comply with these regulations to ensure that their operations are sustainable and eco-friendly.
In conclusion, green cement has emerged as a crucial solution to address the environmental impact of cement production, which is one of the most carbon-intensive industrial processes. The use of alternative fuels and alternative raw materials, along with the implementation of carbon capture and utilisation technologies, are some of the key strategies that are being adopted by the cement industry to reduce its carbon footprint. Government policies and regulations aimed at promoting the use of green cement and achieving Net Zero emissions are expected to play a critical role in accelerating this transition. As the global demand for cement continues to rise, the adoption of sustainable and eco-friendly practices such as green cement will become increasingly important to ensure a more sustainable future for the construction industry.
-Kanika Mathur
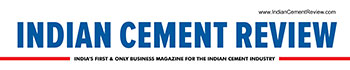
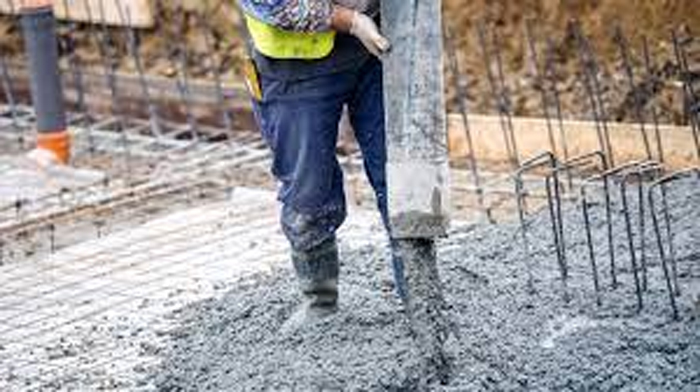
Tamil Nadu is set to host one of India’s five national carbon capture and utilisation (CCU) testbeds, aimed at reducing CO2 emissions in the cement industry as part of the country’s 2070 net-zero goal, as per a news report. The facility will be based at UltraTech Cement’s Reddipalayam plant in Ariyalur, supported by IIT Madras and BITS Pilani. Backed by the Department of Science and Technology (DST), the project will pilot an oxygen-enriched kiln capable of capturing up to two tonnes of CO2 per day for conversion into concrete products. Additional testbeds are planned in Rajasthan, Odisha, and Andhra Pradesh, involving companies like JK Cement and Dalmia Cement. Union Minister Jitendra Singh confirmed that funding approvals are underway, with full implementation expected in 2025.
Image source:https://www.heavyequipmentguide.ca/
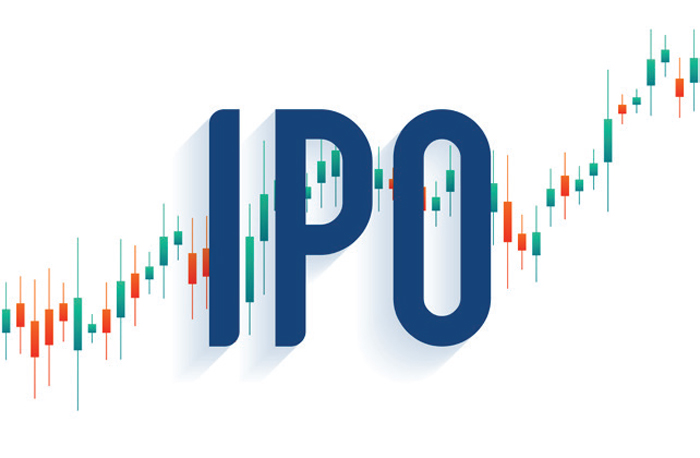
JSW Cement has set the price range for its upcoming initial public offering(IPO) at US$1.58 to US$1.67 per share, aiming to raise approximately US$409 million. As reported in the news, around US$91 million from the proceeds will be directed towards partially financing a new integrated cement plant in Nagaur, Rajasthan. Additionally, the company plans to utilise US$59.2 million to repay or prepay existing debts. The remaining capital will be allocated for general corporate purposes.
Concrete
Cement industry to gain from new infrastructure spending
Published
1 month agoon
July 24, 2025By
admin
As per a news report, Karan Adani, ACC Chair, has said that he expects the cement industry to benefit from the an anticipated US$2.2tn in new public infrastructure spending between 2025 and 2030. In a statement he said that ACC has crossed the 100Mt/yr cement capacity milestone in April 2025, propelling the company to get closer to its ambitious 140Mt/yr target by the 2028 financial year. The company’s capacity corresponds to 15 per cent of an all-India installed capacity of 686Mt/yr.
Image source:https://cementplantsupplier.com/cement-manufacturing/emerging-trends-in-cement-manufacturing-technology/