Concrete
Milestone Trends in Indian Cement Industry
Published
2 years agoon
By
admin
KHD charts its green footprints on the road to low carbon emissions.
India is the second largest cement producer in the world and accounted for over 8 per cent of the global installed capacity. Of the total capacity, 98 per cent lies with the private sector and the rest with the public sector. The top 20 companies account for around 70 per cent of the total cement production in India. Having the high quantity and quality of limestone deposits throughout the country, the cement industry has promised huge potential for growth since 1914. In the past five years, the industry has witnessed a CAGR of approximately 5.5 per cent driven by demands in roads, urban infrastructure and commercial real estate. The cement sector has received good investments and support from the Government in the recent past.
In this growing trend, the industry has witnessed ups and downs, technological changes, import-export crisis, increased fuel prices, environment load, alternate solutions, mergers and acquisitions, market strategies, fierce competition and above all sustainability. Various trends were witnessed, which called for solutions that have a global approach particularly low carbon emissions. Due to the incessant changing technology and requirements of cement industry, KHD being a responsible partner is steadily delivering and contributing its best for more than 160 years presenting a sterling example in fulfilling the responsibility as a prime technology supplier. Continual development based on the need from the industry, guided the technology providers to think ahead and gear up to provide the cement industry with the latest state of art technology integrating the innovations, which are leading to the sustainability of the plants in long run. With the depleting resources, concerns for growing greenhouse emissions and sustainable practices, KHD with its long vision approach worked out that for the growth to be consistent the principle, which will form the basis should be derived on the sustainable life cycle. The coming sections will discuss the number of trends witnessed by industry in the past decades.
Trends for an efficient pyroprocessing system: In the past few decades, the basic nature of pyroprocessing has not changed. A little that had changed happened about twenty or thirty years ago, which was the transition from wet to semi-dry and semi-dry to dry processes. Post that, most of the processes have become more and more efficient, but have not changed fundamentally. It›s the continuous evolution of technologies from good to better to best like Preheaters Development in terms of increased efficiency, reduced pressure drops, lower exit temperatures and reduced emissions. For instance, the top stage twin cyclones as supplied by KHD are designed with highest dust collection efficiency of > 96 per cent, low exhaust gas temperatures up to 260oC and low pressure drop as low as 350 mmWG (Fig 1). Another development goes into the calciner series wherein the calciner was developed over a time for usage of alternate fuels of varying degree and quality. The developments were made keeping in view the requirement of industry to use more of alternate fuels than the noble nonrenewable fuel sources (Fig 2). Today the trend stands for the more and more usage of alternate fuels up to 90 per cent in the pyroprocessing system thus, decreasing the load on mother nature and contributing towards the ‘2050 Climate Ambition’.
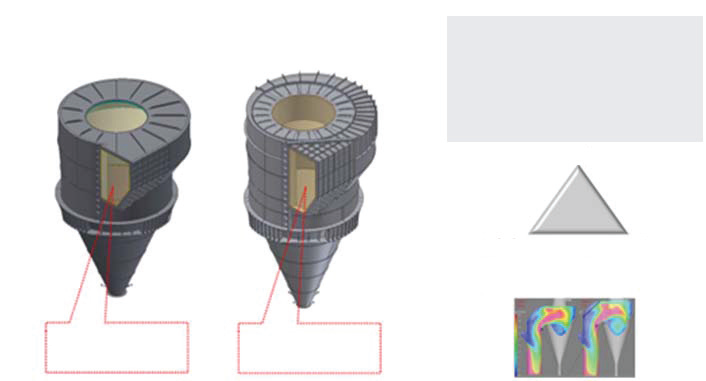
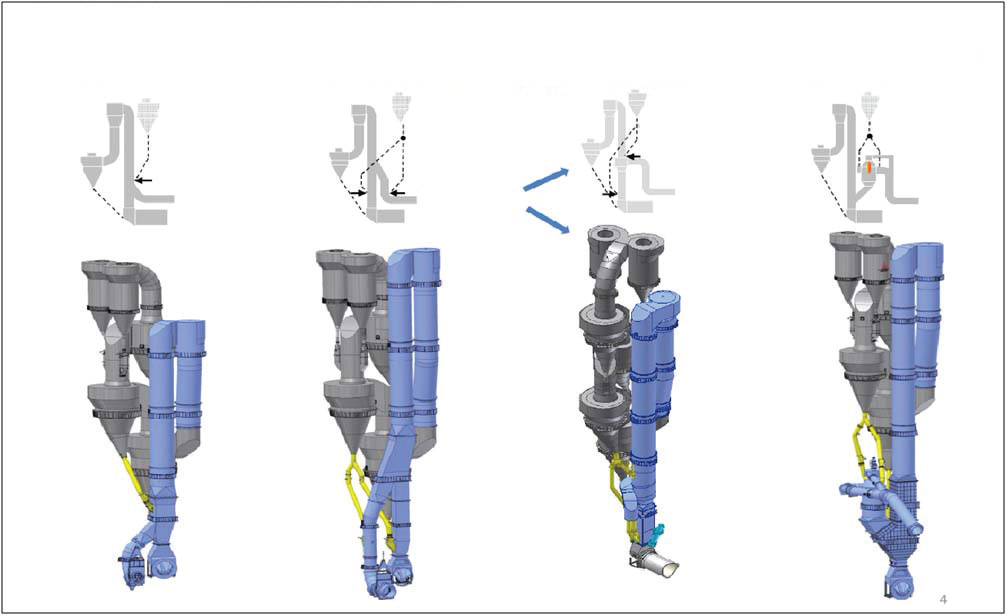
Another trend is for decreased thermal energy consumption, which is addressed by developing the preheater cyclones and calciner by KHD. To arrest the radiation losses in the system KHD is doing proper insulation in the preheater and ducts along with special aluminum-based paints to retain the heat within the system and increase the availability for intrinsic processes. We will deal with more of the global mandates in coming sections on environment trends.
Cooling solutions have always played a major role in any clinkerisation line. The earlier generations of coolers like the rotary cooler, satellite coolers were replaced by grate coolers in the eras of 90 and later walking floor coolers. Further, developments were made in these coolers as better features like KHD further developed its clinker cooler ‘Static Inlet’ with state-of-art features. Latest generation clinker cooler ‘Static Grate’ is designed with ‘Horse Shoe’ for optimal clinker distribution on the static grate with high specific cooling air to achieve the benefits of highest recuperation efficiency, excellent clinker distribution across cooler width, minimum ‘Snowman’ formation and low clinker temperature at beginning of moving grate. For the cooling zone section, low maintenance-high efficiency grate plates are being offered. The salient features of these patented plates are autogenous wear protection and reduced pressure drop due to optimally designed aeration slots. Also, the fall through of dust was eliminated by the development of better sealing arrangements (Fig 3).
Another upcoming trend in the cement industry is the generation of power from exhaust. As known India is amongst the few G20 countries to be on track to meet its Nationally Determined Contributions (NDCs) committed under the Paris Agreement. According to the Ministry of New and Renewable Energy (MNRE), the Indian Cement Industry has the highest potential (amongst identified sectors) to generate energy from waste. However, potential also lies in providing the technologies, which can provide the maximum waste heat. For instance, KHD coolers have high potential to provide more of the exhaust heat from its midpoint in order to be captured by the boiler after hot air recirculation
Also providing an intermediate crusher has an advantage of increasing the midair temp. Similarly in preheaters more of the exhaust gases are captured to generate more power. Recently one of the plants operating with KHD Preheater and cooler has generated approx. 15 MW gross from a potential 8000 tpd clinkerisation unit.
One more additional trend upcoming in the pyro system is the use of alternate raw materials to produce clinker without compromising on the quality and parameters. Selected waste and by-products containing useful minerals such as calcium, silica, alumina and iron can be used as raw materials in the kiln, replacing raw materials such as clay, shale and limestone. Even to some extent 3 per cent slag can be used in the raw material replacing some of the traditional raw material. In one of the KHD plants in Novotroitsk, Russia, copper slag, which is a byproduct from nearby industry, replaced up to 30 per cent of raw material for clinker production.
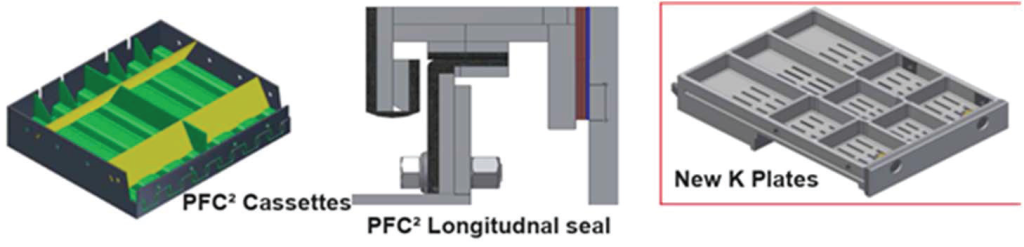
This iron corrective component (Martin Slag) material not only acts as alternate raw material but also produces heat and fulfils the heat content requirement of the process. This has led to the World Record of specific heat consumption of only 600 kCal/kg clinker (Fig 5).
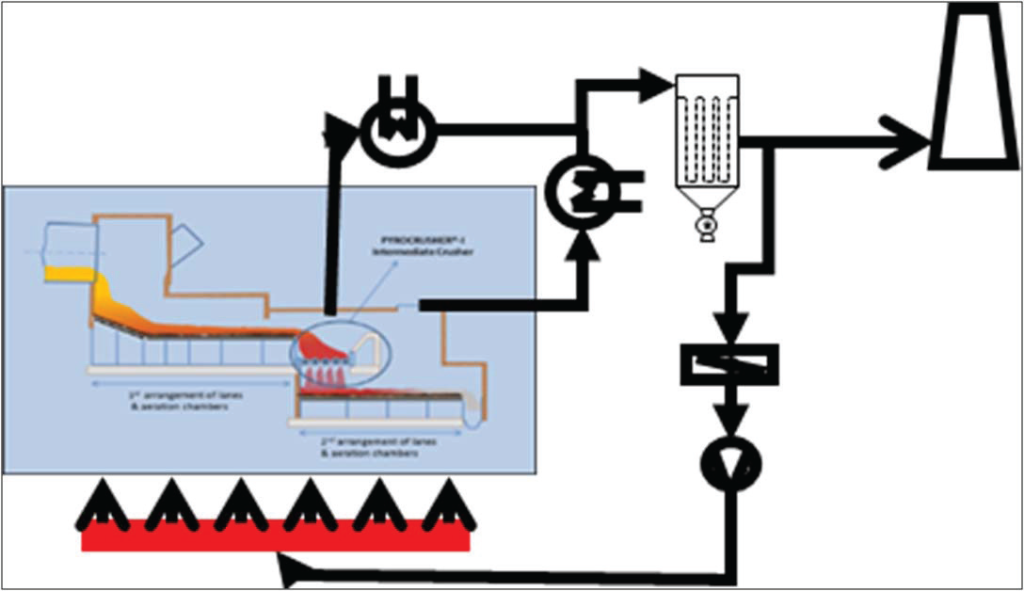
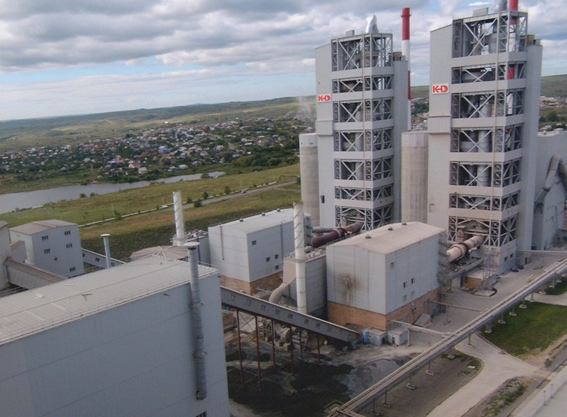
ENVIRONMENT IMPACT ASSESSMENT AND TRENDS
The Indian Cement Industry has a lot of potential to use alternate fuel in the manufacture of cement with benefit in terms of conservation of natural resources and prevention of environmental hazards including mitigation of greenhouse gas emission, all of which serves the goal of sustainable growth and development in India. Today, many cement plants are exploring to collect all the municipal waste of the area, process it and use it as an alternate fuel. Keeping in view all these, long time back KHD has rolled down equipment to use alternate fuels of varying degree. One such example is the combustion chamber.
KHD Combustion chamber is especially designed to burn the material, which is lumpy and coarse in nature as well as difficult to ignite. An optimised flow pattern of the gas-meal-fuel suspension within the vessel is necessary to accomplish that without creating excessive calciner dimensions. The Calciner design is based on the requirements of Creation of subsequent zones with dedicated functions for a controlled process of NOx reduction, staged combustion and mixing zone for a reliable final oxidisation on CO-remains.
KHD Pyrorotor® is a unique rotary combustion reactor that sustainably co-processes waste materials. Within the range of modular solutions from KHD for co-processing of alternative fuels in the clinker production process, the Pyrorotor® covers the demands for highest TSR rates of least pre-processed AF. Due to the high temperature process and longer residence time, it is suitable for nearly all types of coarse solid fuels. Tertiary air is used as combustion air for burning of fuels. (Fig 6).
Emissions are released from cement kilns, coming from the physical and chemical reactions of the raw materials and from the combustion of fuels. There is a system consisting of equipment to draw, condition and analyse the flue gas sample and provide a permanent record of emissions and process parameters continuously on a real time basis and is called “Continuous Emission Monitoring System (CEMS)”. It is of vital importance to install the CEMS system as the source can be controlled after measuring the emissions. However, some of the cement manufacturers in India have not installed the CEMS in their cement plants. It must be a collaborative effort of cement manufacturers, suppliers, consultants and Government to achieve the objective of emission control. KHD is trying to ensure that all the plants equipped with KHD technology get CEMS implemented to protect the environment.
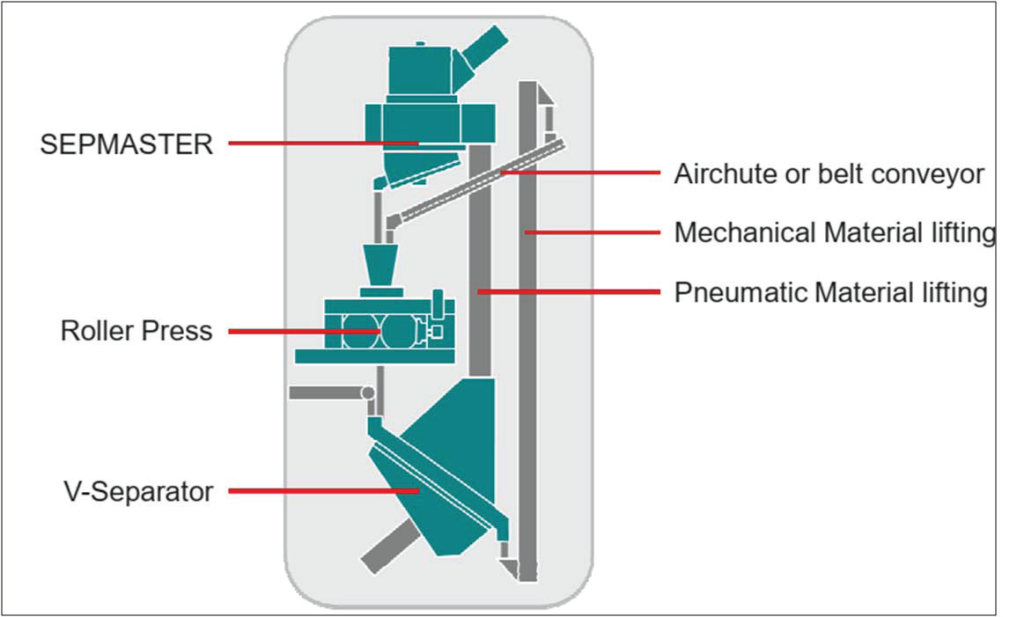
with RP: COMFLEX
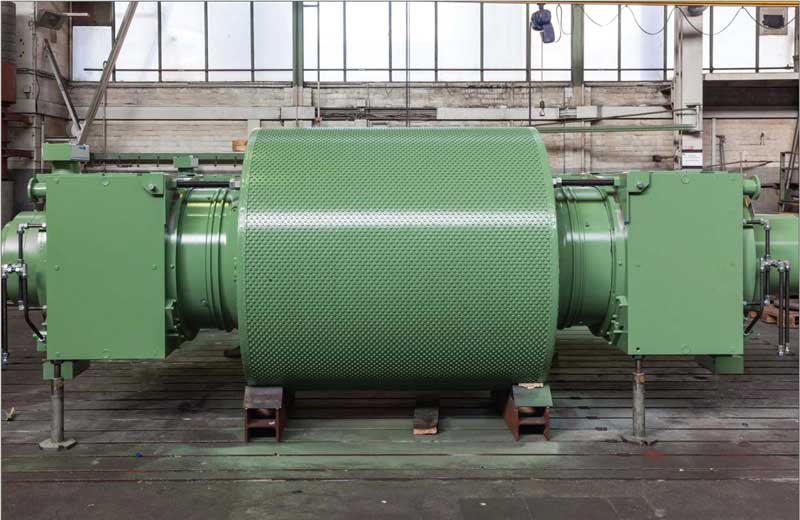
An example equipment from KHD for reducing the emissions at source is the Low NOx burner (Pyro-Jet® Burner). The most imperative features of the burner are the Low NOx emissions, low primary air, and flame (stable and uniform) characteristics. The flame of the PYRO-JET® burner has both an internal recirculation zone and a long external one which results in considerable NOx reduction.
Pyroclon®-R Low NOx AF is the special design calciner, which attains retention time that is desired for complete burnout of the fuel. Another prominent solution from KHD for reducing the NOX emissions is the PYROREDOX® system where the NOx coming from the kiln gets further reduced and formation of Fuel NOx is suppressed.
TRENDS IN GRINDING TECHNOLOGY
The buzz word for grinding systems remains from decades is Electrical Energy Consumption. This is because nearly 65 per cent of the energy consumed in cement plants is attributable to grinding systems. Roller Presses are the solution for grinding circuits. Comflex Grinding system from KHD (Fig 6) consumes less energy compared to other process circuits and is a proven fact for raw material and slag grinding. In case of clinker grinding application also, less specific power is established with roller press in finish mode operations as compared to other technologies available at present. Some of the operating results, which are shared in the next section depict the energy efficiency of a roller press.
Dust Free Circuits: Today most of the plants face the problem of fugitive emissions as well as point source dust spillage. It is well known that the KHD COMFLEX grinding circuits are dust free circuits with no belt conveyors in the grinding and separation group. Also, due the compact arrangement the system has less vibration and hence less noise level. Air chutes avoid mechanical conveying in the grinding circuit and can take feed of more than 1000 tons per hour and accept even coarse and moist fresh feed. The air chute consists of an inlet- and outlet section, each with air lock, the standard sections, the air supply, and venting. From its dimensions the housing is similar to an air slide. Wear protection plates are used instead of cloth for low maintenance operation. Simple air-slide fans are used to introduce ambient air or hot air, if moist materials are conveyed.
Water consumption in cement plants is a necessity, which plays a role as process water, recirculation water and potable water. In the context of the grinding systems vertical raw mills require additional water for bed stabilisation and water sprays into cement mills for temperature control by evaporative cooling. This is not the case in a roller press as water requirement is very insignificant, max 1 m3/hr in comparison to VRM Requirement of 8-10m3/hr. When a cement plant is located in a desert environment the process has to be specifically designed to have low water consumption. Hence, KHD Roller Presses come in picture as the best water conserving machines.
On any grinding surface lowest wear rates are achieved, if the ground material itself provides the wear protection. This is reached by profiling the surface in a way that it is partly covered with ground material. KHD’s patented STUD-Lining (Fig 8), consists of extremely wear resistant carbide cylinders inserted in the roller surface. More than 70 per cent of the roller surface is covered with ground material, acting as autogenous wear protection. Wear rate of rollers/table in VRM is higher than Roller Press and this can be well attributed to the stud surfaces as offered by KHD.
Moreover, KHD is under near offering of high chrome surfaces, which will be more in terms of availability and reliability due to extended wear life.
With the trend of more low clinker to cement ratio this one and foremost step for reduced carbon print, is already in place in the cement industry. Today, India is one of the cement industries, which is moving very fast toward this aspect of green cover. PSC, PPC, Composite cements are the up going curves. Cement Industry is well versed with the utilisation and manufacturing of Blended Cement. KHD is one of the key suppliers for providing energy efficient technologies, viz a roller press grinding for the production of blended cement. It is estimated that decreasing the clinker ratio in production of cement contributes nearly 37 per cent CO2 reduction targeted. By promoting PPC and PSC cement in India, more than 85 per cent cement is produced as blended cement / composite cement (which has come into existence during the last 3-5 years). PPC allows 35 per cent fly-ash usage at present, whereas PSC allows 55 per cent to 65 per cent granulated slag in clinker. Increase of Pozzolona (fly-ash) usage in PPC up to 45 per cent can reduce the carbon footprint further, which has a permissible limit up to 55 per cent in some European countries.
MODERNISATION AND UPGRADATION TRENDS
Apart from building new production lines to increase the capacity, there is a rising trend for upgradation and modernisation of existing set-ups. Utilisation of existing kilns to its maximum potential is an art. This concept not only enhances clinker production but also significantly contributes in improving the overall operational efficiency. The reduced thermal and electrical energy demands will aid in reducing the carbon footprint of existing plants.
To cater market demands in this area, KHD, offers extensive modernisation solutions, which includes PH cyclones modification, optimised dip tubes, suitable riser ducts, high efficiency top cyclones, new generation clinker cooler, cooler plates, state-of-art Low NOx-AF calciner solutions etc. in Pyro section and latest generation separators, milling parts etc. in grinding section. KHD’s experience in this area is unparalleled and hence established as one of the leading technological solution providers to modernise existing cement plants.
In the last few years, KHD has implemented new technologies to modernise the number of existing plants with the prime objective of achieving enhanced productivity, improved energy efficiency and reduced emissions. The results from these plants are quite satisfactory and paved the way for more such projects from various customers globally.
OPERATION AND MAINTENANCE TRENDS
Best operating practices, efficient and reliable equipment and plant availability are the parameters, which define the efficiency of a cement plant. The detailed designing of the equipment play a critical role in the reliability of the equipment e.g. the cylindrical roller bearing for the rollers due its shape and radial load carrying capacity doesn’t suffer skewing in the roller bearing housing and are easy for sealing and safer, too. Similarly, upside equipment like rod sizer, metal detector, magnetic separators are some of the equipment, which are protecting and ensuring the long operating hours and smooth operation flow of the major equipment. The robust kiln shell and tires, low wear and tear of coolers calls up for very less maintenance over years. This leads to nearly full time availability of the system throughout the year. Also, machinery suppliers such as KHD take over annual maintenance contracts of the plant to improve the reliability of machines thus enhancing overall productivity.
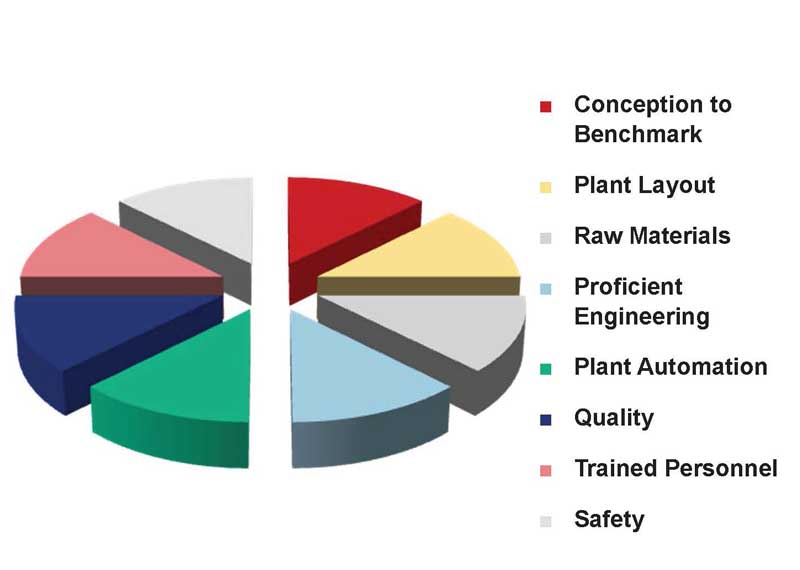
DIGITISATION AND AUTOMATION TRENDS
The path forward for the industry is clear: embrace digitisation and sustainability. Putting these two trends at the core of planning for the future will help cement players catch up to those in other heavy industries and achieve considerable productivity gains. In an industry where regaining lost revenues can take years, it is crucial to kick off now to both recover from the impact of pandemic and make cement players more resilient to future disruptions.
Indeed, the cement plant of the future will operate in a drastically different way than today’s plants. It will achieve considerably lower operating costs and higher asset value through higher energy efficiency, yield, and throughput. More targeted and effective maintenance lengthens the lifetime of equipment. Each plant’s environmental footprint is minimised, securing its licence to operate across locations and jurisdictions. The plant meets customer demand by dynamically adjusting production and logistics according to real-time customer data. Excited, engaged employees focus on value-added activities, and all non-value-added tasks are automated. Real-time information is available for managers remotely at all levels to make better decisions. Digital twins simulate and optimise the overall impact of external variability in operations ranging from complex processes such as burning to more structured activities such as maintenance.
Fewer workers are required to be on-site continuously, and interactive online dashboards allow managers to remotely collaborate, solve problems, and quickly make informed decisions with the rest of the team. Maintenance engineers are alerted of faults in equipment or of opportunities for maintenance immediately, and they receive step-by-step instructions on how to repair with the aid of augmented reality. This will cater to one of the main concerns of safety of individuals avoiding frequent proximity of accidental areas and occupational hazards.
CONCLUSION
Today there are identified levers, which are shaping the industry to reach the highest point of the curve of sustainability vs time period. Cement manufacturers are taking a big leap for achieving the goals as established by various associations and global bodies. Although the trend is more towards the decarbonisation of the industry, capacity utilisations, productivity enhancements and controlled emissions are big watchers. The Indian cement industry has been working on the issue of its GHG emissions and has brought down the CO2 emission factor considerably. However, it has to work more to achieve the goals of Cement and Concrete Roadmap 2050 for the Net Zero Concrete. The leading cement and concrete companies in India have accepted the goal to achieve Net Zero Concrete by 2050 and committed to fully contribute to building the sustainable world of tomorrow. However, the industry needs to work more on newer technologies like Renewable Energy, Novel Cements, Carbon Capture and Storage/Utilisation. Cement technology suppliers are doing their work and are in the process of rolling out these technologies with the main plants. KHD has done advanced work in this field and has solutions like LC cement. As part of the Made in India concept KHD is also promoting more manufacturing in Indian workshops with improved quality, which can aim at improved reliability of the equipment. All these steps are keen steps to make the Indian cement industry cherish and flourish achieving the roadmaps of carbon reduction, increased capacity to meet the demands and go in liasoning of government plans.
Authors: A K Dembla, Sandeep Zutshi and Deepti Varshney
Concrete
Star Cement launches ‘Star Smart Building Solutions’
Published
4 weeks agoon
June 17, 2025By
admin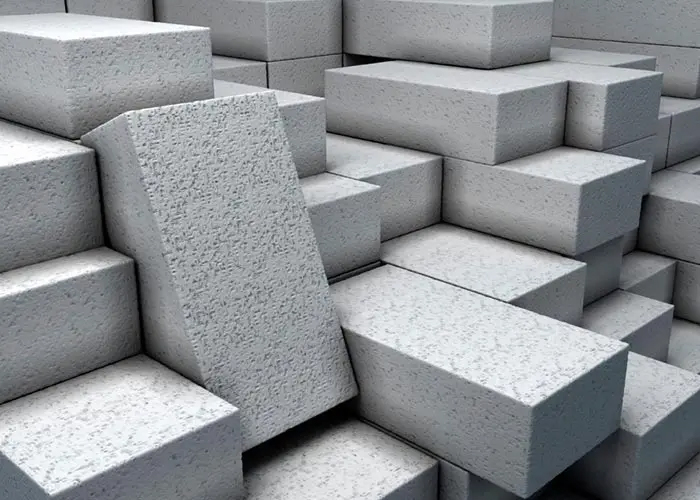
Star Cement has launched ‘Star Smart Building Solutions,’ a new initiative aimed at promoting sustainable construction practices, as per a recent news report. This venture introduces a range of eco-friendly products, including tile adhesives, tile cleaners and grouts, designed to enhance durability and reduce environmental impact. The company plans to expand this portfolio with additional value-added products in the near future. By focusing on sustainable materials and innovative building solutions, Star Cement aims to contribute to environmentally responsible construction and meet the evolving needs of modern infrastructure development.
Image source:https://www.starcement.co.in/
Concrete
Nuvoco Vistas reports record quarterly EBITDA
Published
4 weeks agoon
June 17, 2025By
admin
Nuvoco Vistas reported its highest-ever quarterly consolidated EBITDA of Rs.556 crore in Q4 FY25, with annual EBITDA at Rs.1,391 crore. Cement sales reached 19.4 MMT in FY25, with Q4 contributing 5.7 MMT. Revenue rose 4 per cent YoY to Rs.3,042 crore in Q4. Net debt reduced by Rs.390 crore to Rs.3,640 crore. The company received NCLT approval for acquiring Vadraj Cement, targeting 31 MMTPA capacity by FY27. Key marketing initiatives, expanding RMX and MBM businesses, and a focus on sustainability (457 kg CO2/tonne) drove performance. Nuvoco remains focused on premiumisation, operational efficiency, and market expansion.
Image source:nuvoco.com
Concrete
UltraTech Cement increases capacity by 1.4Mt/yr
Published
4 weeks agoon
June 17, 2025By
admin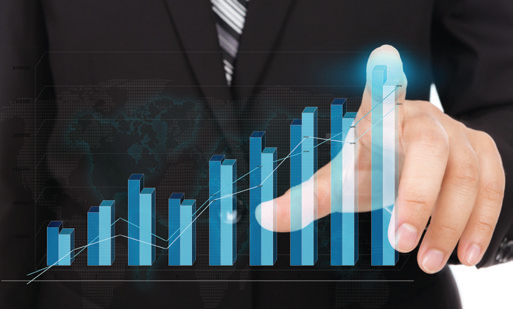
UltraTech Cement has expanded its production capacity by 1.4 million tonnes per annum (Mt/yr) through a combination of debottlenecking efforts and operational efficiency upgrades across several of its plants. The enhancements include an addition of 0.6Mt/yr in grinding capacity at the Nagpur facility in Maharashtra and a combined 0.8Mt/yr at the Panipat and Jhajjar units in Haryana. With these upgrades, the company’s total domestic grey cement capacity has risen to 184.8Mt/yr, while its global capacity now stands at 190.2Mt/yr.

Hindalco Buys US Speciality Alumina Firm for $125 Million

Star Cement launches ‘Star Smart Building Solutions’

Nuvoco Vistas reports record quarterly EBITDA

UltraTech Cement increases capacity by 1.4Mt/yr

Shree Cement reports 2025 financial year results

Hindalco Buys US Speciality Alumina Firm for $125 Million

Star Cement launches ‘Star Smart Building Solutions’

Nuvoco Vistas reports record quarterly EBITDA

UltraTech Cement increases capacity by 1.4Mt/yr
