Concrete
Integrating Sustainable Processes
Published
3 years agoon
By
admin
Primary and secondary packaging of cement is one of the most crucial stages of the manufacturing process, given the nature of the product. Faulty or cheap packaging can result in the cement turning solid due to moisture, by the time it is delivered on the site. At the turn of the century, the functionality of cement bags was not the only parameter to consider. Cement companies turned to innovation and recycling to implement sustainable bagging and packaging of their product. ICR looks at the current options available in the market and how cement brands can improve their packaging processes to reduce their carbon footprint.
Cement is a widely consumed and produced product. Its packaging, therefore, holds a lot of importance and needs to be done with care and precision. With the ongoing infrastructural development in the country, the demand for cement is ever rising. Similarly, India also exports a significant amount of cement.
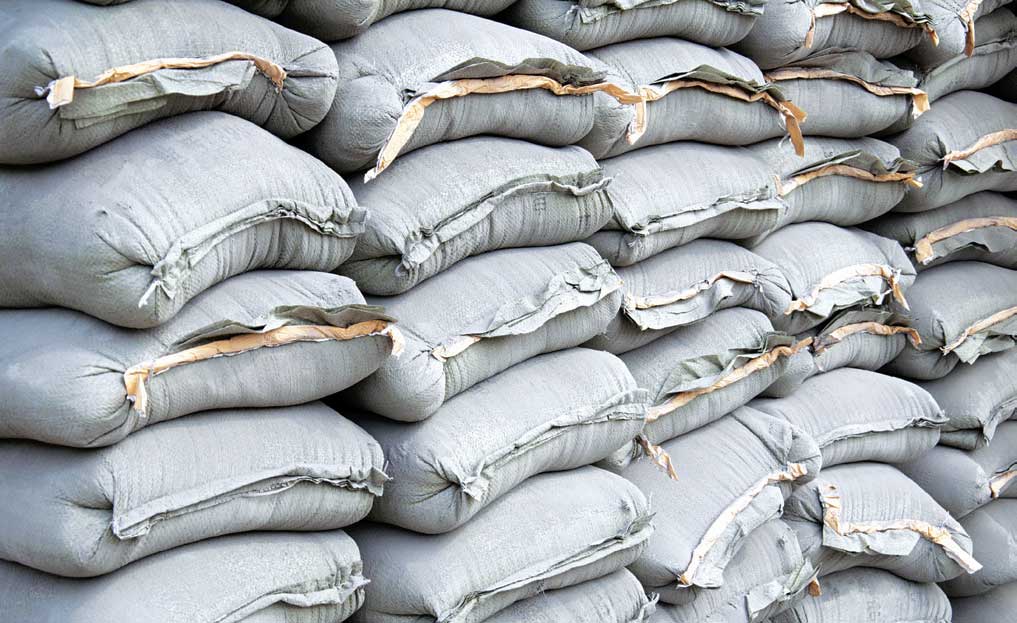
high durability making it the less pollutant product
compared to other packaging bags.
Packaging of cement plays a crucial role in the process of taking it from the makers to the consumers. Manufacturer’s source highest grade technology and packaging material to protect their product from damage, wastage and to reach the end user in an unharmed manner.
The process of packaging is at the last leg of the cement manufacturing process at the plant. Cement is extracted from the silo bottom by aeration and transported to electronic packing machines by air slides and bucket elevators. When it comes to filling cement bags at plants with valve fillers, the process is automated but the technicality is not simple. The product is pressed into the bag, while bags are made round so the maximum amount of product with air can be put inside. Then the bags are flattened so the air can escape through the many holes in the bag, and the bags can be stacked on a pallet. But this process does not work well with a closed plastic bag. The air leaving the product causes air to come in that cannot escape.
Materials and Quality Standards
Polypropylene is the chosen material for cement bags. The benefits of using this material are protection from moisture and strength to packaging. There are various categories of polypropylene bags available with coatings, linings etc.
- PP Plain Woven Bags: These are simple bags made of plastic, stitched at the ends to hold cement in them.
- PP Lined Woven Bags: These bags have an extra lining under the plastic outside that prevents cement from coming in contact with moisture.
- Laminated PP Bags: These bags have an extra poly film layer over the polypropylene. They have a higher strength than the regular PP woven bags and provide a greater resistance from air that comes in contact with the bags. These also give way to better branding of the product when it is stored in uncovered settings.
- BOPP Laminated Bags: The Biaxially Oriented Polypropylene (BOPP) laminated bags have a superior quality than other bags. An extra added layer enhances the durability of these bags and makes them more attractive for branding as well as prevent wear, tear and wastage while handling.
Cement makers, for the sake of sustainability, have been contemplating switching to paper bags. However, PP woven bags have various advantages when put in use for storing cement. They are highly chemical and weather resistant. They have high tear strength, which enables it to carry heavyweight materials. PP woven bags are 100 per cent reusable and have high durability making it the less pollutant product compared to other packaging bags. The element of recyclability and waste prevention because of the sturdiness of PP woven bags, they are the chosen material for cement packaging.
“Bags made of polypropylene can easily sustain harsh environments. Usually, we do not need to add any additives to retain the properties of the bags as in a normal case, cement is consumed within one to two months after it is produced and packed. But if there is a need to have longevity, we can add certain additives to the master batch to retain the properties of the bag. These additives allow the bags to sustain harsh conditions and environments, if exposed,
for up to a year,” says Nitesh Sharma, Director, ShriMaa Group.
Quality control for cement packaging is very important. The BIS (Bureau of Indian Standards) has set norms for cement packaging. As per Cl 9.2 of IS 455: 1989, the average net mass of cement per bag shall be 50 kg. The average net mass of cement per bag may also be 25 kg subject to tolerances and packed in suitable bags as agreed to between the purchaser and the manufacturer. Similarly, as per Cl 10.2 of IS 1489 (Part 1): 1991 and IS 1489 (Part 2): 1991, the average net mass of cement per bag shall be 50 kg. The average net mass of cement per bag may also be 25 kg subject to tolerances and packed in suitable bags as agreed to between the purchaser and the manufacturer. Also, as per IS 8112: 1989, the average net mass of cement per bag may also be 25 kg, 10 kg, 5 kg, 2 kg or 1 kg, subject to tolerances and packed in suitable bags as agreed to between the purchaser and the manufacturer.
Technology of Cement Packaging
Packing and bagging of cement is the last leg of the cement manufacturing process, after which the end product is loaded into its transport and sent across for sales and distribution. This process of packaging is mechanised and precision needs to be maintained to attain uniform results in packaging.
The packing machines can be classified as a fixed type and a rotary type. The fixed type usually has 1 to 4 cement discharging nozzles while the rotary type machine has 6 to 14 nozzles, which operates in a rotating way for automated cement bag filling.
With this machinery, cement bags are filled continuously through the discharging mouth by the impeller running at high speed. A weight is set for the filling and when the cement reaches that set weight, a signal is transmitted to the main system and the filling is stopped. This process is electronically controlled; however, bags of the desired size are manually fed to the machine. Automation of the bag filling process has various advantages like
having a stable operation, giving uniformity and structure to the bags, clean and hygienic filling of cement bags, ease of maintenance and lesser mechanical faults.
Growth of the Packaging Market
According to research conducted by Future Market Insights, the cement packaging market is expected to record a CAGR of 3.9 per cent during the forecast period 2022-2032, up from US$ 344.5 Billion in the year 2022 to reach a valuation of US$ 488.4 Billion by 2032. This growth shall be credited to the increasing demand from construction industry, surging application of paper bags as it provides ease of printability and replacement of conventional plastic bags. On the other hand, evolution of advanced products will further create new and ample opportunities for the growth of cement packaging market in the above-mentioned forecast period. This will also be seen in the sustainable packaging solutions vertical over the years to come as that demand is growing in most sectors related to cement.
Moreover, the market is flooded with duplicated and adulterated construction materials. So, the manufacturers of cement are aiming to reduce instances of counterfeiting by incorporating sophisticated branding impressions on their packaging solutions. These factors are expected to drive the sales of cement packaging solutions in the global industrial packaging market.
Sustainability in Packaging

Decision makers of the cement industry have taken conscious steps towards sustainability in their manufacturing process. Cement bags and packaging also play a crucial role as they eventually become waste by-products of cement and end up in landfills or waterbeds.
According to Nitin Vyas, Managing Director and CEO, Beumer India, “Looking at the larger picture and speaking about sustainability, our cement bags are a problem. They have a high porosity. The only two countries using these bags are India and China, where China will stop using these bags going forward as they are huge pollutants. When the bag is thrown, a lot of dust is generated. The cement industry needs to become responsible and not look at saving a miniscule amount of money per bag and rather look at the bigger picture and save the environment. Approximately Rs 2 per 50 kg bag needs to be spent to improve the quality, which will result in a better environment and better health conditions for the loader as well.”
“There are no hard policies for packaging. There are no strict regulations on what kind of bags need to be used for packaging, what is the pollution limit in a packing plant etc. Sustainability is treated as fashion in today’s time, but it needs to be looked at more seriously, especially in the packaging and logistics domain,” he adds.
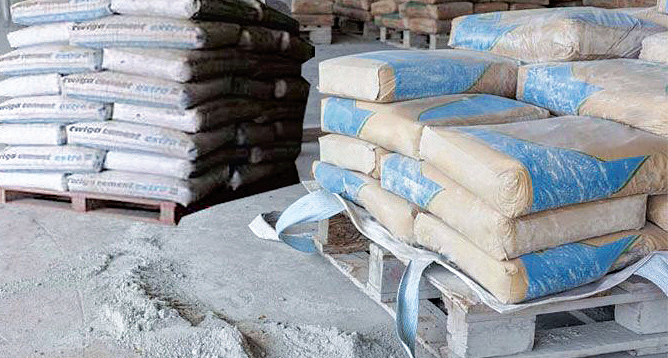
the approach towards sustainability and eventually
become waste by-products of cement and end up in
landfills or wat
Recycling of cement bags has been taken up as a major step towards the conservation of resources and prevention of wastage. Primarily made of polypropylene or plastic, there are two product outcomes while recycling cement sacks, i.e., recycled polymer (polypropylene) and calcium carbonate (CaCo3). The most common method of cleaning the sacks is by water; this allows agglomeration of cement (lumps) that is left in the bag. Hence, 80-85 per cent of recycled polypropylene is churned out in grey (not white) and the remaining 15-20 per cent is calcium carbonate formed from the cement already available in the sack. While washing with air is another option, it is not widely used given its high cost. The output is the same-coloured polymer and less calcium carbonate. The reason behind these polymers being coloured is due to the use of masterbatch or UV coating while making them.
The recycled polymers are sent to regions where the blow-moulding industry is predominant for conversion. In India, Dhoraji, Ahmedabad in Gujarat is the recycling ‘hub’ for all plastic scrap. Other regions include Aurangabad in Maharashtra and Hyderabad in Telangana. Nearly 30 per cent of the cement sacks are cleaned and re-used by farmers and small-scale industry manufacturers to collect/pack manure, waste, by-product, scrap etc.
The Bureau of Indian Standards (BIS) allows 15 per cent calcium carbonate and only 10 per cent recycled polymers while making cement sacks. The reason for lesser use of recycled polymer is because the handling system in India is mostly manual involving 8-10 people across the supply chain. This increases the scope for breakage and tearing. There is a bursting system that indicates the number of cement sacks that can be stacked atop of one cement sack; its breakage is tested depending on the number of sacks that are stacked before the bottom sack could burst. In China, the bursting standards are 7:1 i.e., 7 cement sacks stacked upon 1 whereas in India it is 5:1. Baling of cement sacks would spread the risk of breakage.
Cement industry in India and globally is growing. And so is the requirement of its bagging and packaging. This comes with its own set of challenges; however, the advancing automation and technology is making the process precision and waste free. Recycling of the polypropylene bags has been identified as a key solution to avoid wastage and pollution of the environment. Efforts are being made by the industry to make their brand stand out with quality packaging as well as in the direction of sustainability to build a better tomorrow.
-Kanika Mathur
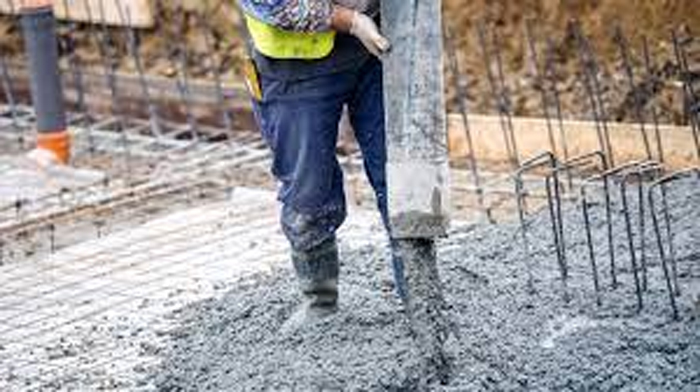
Tamil Nadu is set to host one of India’s five national carbon capture and utilisation (CCU) testbeds, aimed at reducing CO2 emissions in the cement industry as part of the country’s 2070 net-zero goal, as per a news report. The facility will be based at UltraTech Cement’s Reddipalayam plant in Ariyalur, supported by IIT Madras and BITS Pilani. Backed by the Department of Science and Technology (DST), the project will pilot an oxygen-enriched kiln capable of capturing up to two tonnes of CO2 per day for conversion into concrete products. Additional testbeds are planned in Rajasthan, Odisha, and Andhra Pradesh, involving companies like JK Cement and Dalmia Cement. Union Minister Jitendra Singh confirmed that funding approvals are underway, with full implementation expected in 2025.
Image source:https://www.heavyequipmentguide.ca/
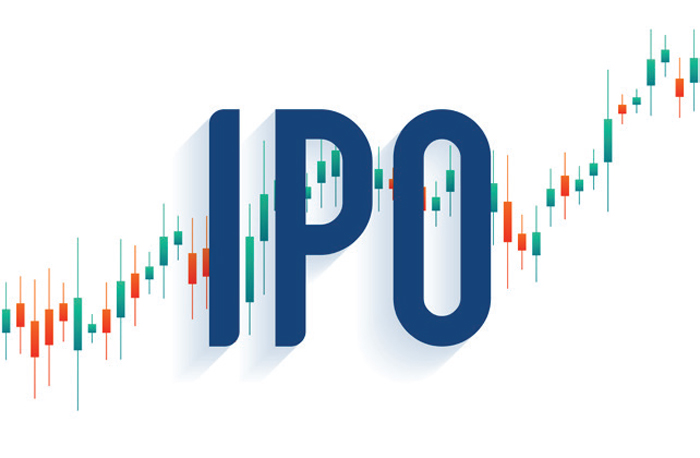
JSW Cement has set the price range for its upcoming initial public offering(IPO) at US$1.58 to US$1.67 per share, aiming to raise approximately US$409 million. As reported in the news, around US$91 million from the proceeds will be directed towards partially financing a new integrated cement plant in Nagaur, Rajasthan. Additionally, the company plans to utilise US$59.2 million to repay or prepay existing debts. The remaining capital will be allocated for general corporate purposes.
Concrete
Cement industry to gain from new infrastructure spending
Published
1 month agoon
July 24, 2025By
admin
As per a news report, Karan Adani, ACC Chair, has said that he expects the cement industry to benefit from the an anticipated US$2.2tn in new public infrastructure spending between 2025 and 2030. In a statement he said that ACC has crossed the 100Mt/yr cement capacity milestone in April 2025, propelling the company to get closer to its ambitious 140Mt/yr target by the 2028 financial year. The company’s capacity corresponds to 15 per cent of an all-India installed capacity of 686Mt/yr.
Image source:https://cementplantsupplier.com/cement-manufacturing/emerging-trends-in-cement-manufacturing-technology/