Concrete
The mark of a good refractory is its ability to remain inert
Published
3 years agoon
By
admin
Prabhat Singh Parihar, Vice President (Technical Head), Mangrol Plant, JK Cement, talks about the challenges faced by cement plants in maintaining refractories and the important properties of refractories that ensure smooth functioning of the processes.
Explain the types of refractories you have in your manufacturing unit. What are their respective purposes?
At JK Cement’s MGR plant, the following types of refractories are used:
- Acid Refractories: Any type of alumina silicate refractories (like fire bricks, alumina brick, high alumina bricks) and silica refractories are called acid refractories. Our manufacturing facilities use alumina bricks in all our kilns, PH, and coolers.
- Kiln Refractory: In the kiln we use DALSINT A (70 per cent alumina and 2 per cent Fe), DALSINT B (70 per cent alumina and 2.5 per cent Fe) and alumina 40 per cent bricks in the respective kiln zones.
- Purpose: Alumina bricks are especially used because these bricks resist acidic flux. Alumina bricks have good thermal stability, high refractoriness that is more than 1770oC and lower thermal conductivity resulting in less heat loss. Alumina bricks are also cost effective when compared to basic bricks.
- Castable: Various grades of castable are used for better service life of the kiln inlet and outlet sectors, burner pipe and coolers. As sintered clinker is very abrasive in nature, Castables such as SiC base, mullite base and CRC- BP for burner pipe are preferred. Castables are best suited for surfaces where brick lining installation is not-possible or is not suitable, as it is easy to mould and there is no chance of falling out like bricks.
- Calcium Silicate Blocks: The challenge with pyro-section is its high operating temperature, resulting in high surface heat losses to ambient surroundings. To overcome this, calcium silicate blocks are installed throughout with refractory, with increment in thickness of insulation blocks. This results in a significant decrease in surface temperature and heat loss.
- Mortar: Alumina/Mullite based mortars are generally used for adhering bricks. As it also shrinks at high temperatures a limited quantity (1.5 to 2 mm) should be applied.
- Ceramic Blankets / Paper / Wool: Like all materials, refractory also expands when heated. Typically, a newly installed refractory would expand anywhere between 1.5 per cent to 2 per cent initially. To avoid adding extra mechanical stress to the refractory, a gap is provided along a certain length. This is generally packed with glass-wool as it gets compressed when the refractory expands. Glass can be easily fitted in any slot or gap as it can be compressed. The dimension for the brick lining is typically 600×600 mm for castable panels, with the axial height of 1000 mm.
What are the key materials used in building a refractory lining to the kiln in your organisation?
For kiln refractory lining, a major portion consists of refractory bricks, castable for kiln inlet and outlet sector, mortar, ceramic paper, shim plate and anchors.
- Refractory bricks: In a rotary kiln, the majority of the refractory type is brick refractory. Various grades of 40 per cent, 60 per cent and 70 per cent alumina bricks (DALSINT-A, B and C) are used. VDZ type bricks are generally used. Kiln lining is done by both layering and jack.
- Castable are used for kiln inlet and outlet sectors to improve better service life. Since, sintered clinker is cooled just after the liquid phase as the sintered phase reaches a high temperature (1450oC) and is very abrasive in nature. Castable that is SiC base and CRC- BP is usually preferred.
- Anchors: Temperature of both extremities are high, to hold castable, and provide structural strength to castable, SS-310 anchors are used. Anchors are welded and capped to prevent breakage from metallic expansion.
- Ceramic Blankets / Paper / Wool: To provide expansion provision for brick lining and castable panel for kiln sector (10 to 18 panel), ceramic paper of 3 mm applied.
- Mortar: Alumina/Mullite based mortars are generally used for adhering bricks. As it also shrinks at high temperature and can loosen the arch causing refractory failure, a minimum and only justified amount of mortar should be used in kiln lining.
What are the key properties of a refractory that support the cement making process?
Cement manufacturing is an energy intensive process. Burning alkaline raw materials (reactive) combined with smaller constituents of metals and abrasive raw materials at very high temperature is a major challenge. Therefore, a good refractory that can withstand high temperatures while retaining required strength and that is resistant to chemical properties of the alkaline raw materials is crucial. Besides, chemical attacks from sulphates or chlorine from the kiln feed or fuel or alternative fuels are other factors that need to be factored in.
Major refractory properties that contribute to cement manufacturing are:
Thermal properties
- Refractories are materials that can withstand very high temperatures and mechanical stresses of dead load. Key parameters for considering a good refractory are its service temperature which is the maximum temperature at which refractory can withstand stresses applied to it at a given temperature.
- Refractory Under Load (RUL) and Pyrometric Cone Equivalent (PCE) are defined as the most important properties of refractory, i.e., resisting or withstanding high temperature. Refractory under load can be defined as the temperature at which refractory can withstand without deformation. Pyrometric Cone Equivalent (PCU) is the temperature at which refractory starts to form an amorphous phase.
- Resistance to thermal shock or spalling: As refractory is heated or cooled it tends to expand or shrink respectively a sudden cooling or heating can cause refractory to lose its strength or can dislocate its position during the heating and cooling cycle resulting in refractory failure.
- Reducing heat losses: Refractories have a lower heat conductivity, thus, the heat transfer rate due to conduction is reduced.
Chemical properties
Refractory material is exposed to high temperature and reactive components of kiln feed, fuel, and alternative fuels. The major reactive components are the metal sulphates or chlorides that can penetrate through the pores of the refractory and get deposited at the core. The cold face of the refractory causes’ loss of strength of refractory material. The mark of a good refractory is its ability to remain inert.
Physical properties
Bulk density is an important property of refractories. A higher bulk density material means that it has a minimum porosity which minimises chemical attacks on the refractory.
Porosity can be defined as the percentage of open pore space in the overall volume of refractory. Pores on a refractory material, provides a site for absorption to the alkali sulphates or chlorides which get absorbed from the hot face side to under refractories and erodes and loses strength from the core of refractories. That is why a good refractory shall have a minimum apparent porosity of 0.2 per cent.
Cold crushing strength: As refractories must withstand a certain mechanical load. The load of itself and the mechanical stress generated due to expansion (radial and axial). A high cold crushing strength means that it would have less breakage while installing, with a good RUL and along comes the draw-back of brittleness
of refractory.
Thermal expansion or permanent linear change. Like all materials, refractory also expands at high temperatures. While a newly installed refractory expands to upto 2 per cent, the permanent expansion and thermal expansion shrinkage cycle deteriorates the strength and service life of the refractory.
Tell us more about the porosity and permeability of the refractory.
Porosity is the volumetric ratio occupied by pores present in refractory material. Porous material is not suitable for refractory application as it has low bulk density and low cold crushing strength.
Apparent Porosity: The ratio of the total volume of the open pores in a porous body to its bulk volume expressed as percentage, of the bulk volume is apparent porosity.
The significance of apparent porosity is as follows:
- Lower the better as it influences chemical resistance.
- Related to BD or compactness.
- Affects cold crushing strength.
- Higher the porosity, lower the thermal conductivity. This means lower heat loss because of more entrapped air inside the refractory structure. Hence, higher porosity refractory may be used to save heat loss in the area where there is lesser risk of abrasion and lower possibility of alkali penetration.
- Very low porosity affects thermal shock resistance.
- 15 per cent to 20 per cent common value for most refractories made by machine pressing.
- For hand moulded shapes 25 per cent to 35 per cent may be the range
- Higher the porosity, more will be the alkali penetration. Generally, alkali salts are solidified at a temperature range between 750 to 850oC directly from vapour. Hence, a more porous refractory can be easily used in the area where the application temperature is less than 750oC.
Closed Porosity: The ratio of the total volume of the closed pores in a porous body to its bulk volume expressed as a percentage of the bulk volume is closed porosity.
True Porosity: The sum of the apparent porosity and the closed porosity is true porosity.
Permeability: It is the measure of flow of gases through pores within the refractory body, and it indicates the extent of pore linkage. Permeability of refractories gives an indication on how well the refractory will stand up to molten slag, a melt or to a gas penetration.
Permeability of refractory is directly influenced by refractory material and apparent porosity of the refractory. As the apparent porosity of the refractory increases it provides a more active site for absorption of volatile sulphates or chlorides into the refractory.
Typical cases of permeability are:
- Alkali Salt Infiltration: As the pores on the refractory surface absorb the volatile metallic sulphates and chloride. They seep through refractory to core and cold face of refractory where they condense to solid form.
- Anchor Corrosion: The alkali salts that seep through the castable reacts with anchors causing corrosion, hence, castable loses its structural strength causing refractory failure.
What is the maximum temperature that a refractory can withhold? How does its strength differ from ambient temperature to high temperature?
There are four key parameters for defining the maximum temperature a refractory can
withhold are:
- Service Temperature: This is the temperature at which refractory can withstand without any failure or losing strength. With increase in active refractory ingredients, the refractory service temperature increases.
- Refractory Under Load (RUL): It is the minimum temperature at which a sample will deform by 0.6 per cent under a constant load. Cylindrical sample that is 50 mm in diameter and 50 mm in height is tested. Constant load of 2 kg/cm2 is maintained on the specimen. The rate of temperature rise is maintained at 15oC or a minimum up to 1000oC and 8oC/min beyond that. Temperature is measured either by thermocouple or optical pyrometer. The expansion or contraction while reading is measured by a dial gauge. As a thumb rule, RUL of brick should be at least 200oC more from its application temperature.
- Pyro metric Cone Equivalent (PCE): It is the temperature at which refractory material gets softened, or it indicates the range of melting point. Sample cones are made by using ~1 per cent alkali free dextrin. Standard cone (German Standard Seger cone or ASTM standard orton cone) along with sample cone are placed on a plaque at an angle of 82o inside. After that this plaque is placed inside the furnace where temperature rise is 35oC/min up to 1560oC and 2-3oC/min beyond that.
- Cold Crushing Strength (CCS): In this test, the cube of a specific dimension cut from the brick sample is subjected to increasing load, until it gets crushed and the test result is reported as the value load per unit area. It indicates the adequacy of firing temperature, for shaped Refractory products, required for proper sintering and to develop the required microstructure and the quality of hydraulic or chemical bond in case of unshaped refractories. In the unshaped products, the CCS does not remain the same after heat treatment, and it decreases or increases with the temperature of heat treatment. The good cold crushing strength of shaped refractories protects them from damages during handling and from mechanical abuses in service.
PCE > RUL > Service Temperature > Operating Temperature
As a thumb rule PCE temperature is about 15 to 20oC more than RUL, whereas RUL should be about 150 to 200oC more than service temperature.
Service temperature is decided in such a manner that at any given time it is always higher than operating temperature (operating temperature + temperature increase in case of process fluctuation).
Numerous inert or non-refractory materials can decrease the service temperature as they form a new eutectic point with an active refractory compound. It is a common practice to make small panels of refractory by installing extra retainers to hold the dead weight of refractories.
Tell us about the installation and operating process of refractories in the kiln.
The lining of refractory material in the rotary kiln is almost exclusively made up of refractory bricks. Refractory castables are used in part only in the kiln inlet and outlet. The bricks work creates an arch in the kiln that is self-supporting and which correctly fits with the kiln shell.
Due to lack of anchoring, the lining must be supported during installation. Two type of bricks installation in a kiln are:
Installation with rotation of kiln – Spindle Method: The spindle method or jacking method is a classic procedure for lining rotary kilns. The bricks are placed in the lower half of the kiln, then the wall segment is supported with spindles so that the kiln can be rotated. After a quarter turn the next segment is lined and so on. The spindle method is a cost-effective method and can achieve excellent results. However, the kiln must be rotated again and again because the individual sections cannot be more than five metre in length. Moreover, the spindle method is suitable only up to a kiln diameter of 4.4 metres.
Installation without rotation of the kiln – Brick Lining Machine: A method in which the rotary kiln must not be rotated while lining (and cannot be rotated) work based on the same principle i.e., first, the lower half of the kiln is provided with the refractory bricks, because no support is required in this area and then brick lining machine will be installed for the remaining upper half area and each ring is supported by a hydraulic jack of brick lining machine until its completion.
What are the standards set for refractories in a cement kiln?
For a kiln, the following types of refractories are used: Refractory Brick, Castable and SS Anchor.
The refractory bricks for the kiln brick lining, high alumina ISO bricks of 40 per cent, 60 per cent and 70 per cent alumina are used. Abrasive resistant castables have a high service temperature and are desired such as grade- LC-60, 90 SiC and CRC as the quenching/cooling zone of the kiln handles the hot and abrasive sintered clinker. SS310 anchors are preferred over SS304 only for kiln and burner pipe.
The main standards that a refractory supplier must meet are:
- Bulk Density: A very crude and crucial standard. A higher bulk density means the refractory bricks are cooked properly and have an active refractory ingredient present. Brick with low brick density indicates low active refractory ingredients.
- Alumina/Active Refractory Content: Alumina content of bricks should not be less than specified value as it is the active refractory ingredient.
- Iron/Ferrite: Iron content of refractory should be below 2.5 per cent as the increase in iron content decreases the PCE and RUL values.
- Apparent Porosity: The value of the refractory should be kept below 0.25 as it increases the alkali salt permeability, anchor corrosion, and decreases the core crushing strength of refractory.
- Cold Crushing Strength (CCS): This strength of the refractory is a must compliant property of a refractory to withhold any mechanical load that is applied to it. Typical CCS value for a fireclay with high alumina is 450kN/cm2 and 650 kN/cm2.
Refractory Under Load (RUL) for refractories it typically between 1400oC to 1500oC
Permanent Linear Change (PLC) is an expansion of a newly installed refractory. This generates an excessive mechanical load on refractory. PLC for refractory should be less than 1.5 per cent.
Pyrometric Cone Equivalent (PCE) for a refractory should be around 35 degree Orton.
Spalling Resistance are the numbers of heating and cooling cycles that a refractory can hold without any failure. Spalling resistance for refractory is desired to be above 30.
Geometry of the refractory is mostly important and no compromise can be made with it, albeit a tolerance of 1.5 to 2 mm can be considered. Same applies for the SS anchors.
What is the role of technology and automation in refractories for cement kilns?
Since the refractory work is very bulky and time consuming, lots of skilled man-hours are spent, which makes it one of the most cost and time intensive jobs. Shutdown even for a small duration of the plant is a major challenge. The introductions of new technology will help to ultimately overcome the refractory application cost and the installation time.
To overcome the above challenges, new processes/technology that are being implemented.
Brick Lining Machine: Before brick lining machine, the refractory applications required manpower for the transportation of refractory, installation of refractory and using jack for holding arch. All these procedures require a large manpower, both skilled and unskilled. In addition to that, it also takes a long time for installation.
The use of brick lining machines and portable belt conveyor, refractory materials are easily conveyed in a convenient way without any unnecessary stockpile lying around in the way of work. Since all brickwork can be done without rotation with the brick lining machine, the time lost in between tightening and loosening the jack and evacuating the manpower from the kiln while rotating is eliminated. A huge advantage is the completion of this process without the requirement of a huge manpower. A small team of skilled manpower can execute the work in a very precise manner and in a limited time.
Gunning/ShotCreting: For castable application in gunning, a batch of dry castable and binder or water are conveyed through a compressed air line to the mixing nozzle where they mix and get applied at application site. Conventional castable application requires a mandatory castable shuttering with material poured over and a vibrator needle, to set it in the right place. This makes it very time-consuming and chances of the castable not being placed properly is there which will take enormous time and manpower to rectify the application. For a shuttering that is not set properly it needs to be broken and new castable will be reapplied hence increasing cost of breaking and re-applying.
For a point place where huge quantum of castable must be applied, Gunning is preferred as it has its advantages such as:
- No need of carpenter or mason or helpers for shuttering frame, making and application of castable.
- Chances of castable not setting properly is eliminated.
- Refractory application rate can be achieved up to 5 TPH.
- Since, failure of setting occurs and application are lesser than conventional method, wastage of castable is minimum with rebound losses for gunning of are about 2 per cent.
- Precast Pre-Fired Refractory: A modern and modular way for refractory application is the Precast Pre-Fired Refractory, which are pre casted to defined required geometrical shapes and can be applied simply bolting, anchoring, and hanging to roof channel support. The key advantages of the new concept are less dependency on skilled manpower, availability of refractory is already casted and only need to be installed.
What tests are employed to check the refractory for defects and at what intervals are these tests done?
There is only a limited number of methods available for a condition diagnosis of the refractory material. In practice, the following are used:
- Measurement of shell temperatures.
- Visual inspection from inside and outside (example: inspection of expansion joints, friction comp.)
- Non-destructive measurement of residual
- brick thickness
- Drill holes and chiselling out of windows
- Quality measurement and surveying the kiln axis
Measurement of shell temperatures: The chronological development of the maximum, average and minimum temperatures on the shell of the rotary kiln allows for conclusion to be drawn for the ratio between lining and coating build-up. Based on the velocity of the temperature changes, further development can be estimated. For example, if maximum temperature rises sharply while the average temperature remains the same or changes slightly, then this pertains to a limited, localised eruption and not overheating of the relevant kiln zone. One preferable option would be to continually check the kiln shell temperature by measuring infrared radiation.
Visual inspection from outside: Inspection or detecting peculiarities on the entire kiln plant are part of the routine task of the kiln personnel. Sudden changes in the surface colours due to increased shell temperatures are clear signs of damage in the lining. But most of the time, even more serious damage is already present. The visual diagnostic procedure therefore ranks last among potential tools, and it is primarily used to prevent further damage to machines.
The condition of the cyclone and vaulted ceilings should be checked regularly through the inspection openings in the ceilings to see if the transition between the brick masonry and the skin is flush. In addition, skin temperature should be compared to earlier measurements in order to gain information about the current refractory status.
Easily accessible part of the cooler, burner pipe or the kiln can also be inspected visually via inspection openings or kiln/cooler cameras. Such an inspection is especially suitable during sort down times as easy inspection measures.
Non-destructive measurements of residual brick thickness: The brick thickness can be measured relatively quickly using a residual thickness metre. But experience shows that generally no reliable measurement signals are provided. Residual thickness metres work with sensitive probe systems that can send and record high frequency electrical impulses. The metallic rotary kiln shell serves as a reflector to determine the residual wall thickness. This device also allows for the different electromagnetic properties of different refractory bricks and infiltration to be recorded.
Drill holes and chiselling out of windows: The residual brick height of the refractory material is determined along the rotary kiln by drilling with a brick drill (9-10 mm). The procedure and results are recorded in a drilling protocol. Brick damage is not always detected with the drilling samples. Using core drilling or chiselling of windows in critical spots, it is possible to detect crack formation or alkali filtration in addition to the residual brick height. However, the subsequent closure of the masonry is unsatisfactory with this method if the residual brick height is low.
What are the major challenges your organisation comes across with the refractory kiln?
- Spalling of bricks in the burning zone: We use ISO type of bricks in the burning zone in kilns. Refractories develop the spalling because of the mismatch of thermal expansion or contraction in between hot face and cold face during heating – cooling cycle and as a result, cracks are developed in the brick. This crack propagates every time and ultimately some portion of the brick gets spelled out from the position.
- Kiln bricks failure near second tyre: Due to mechanical loading as well as thermal loading, bricks failure occurs near kiln 2nd tyre area. Whenever this failure happens, then in this area brick lining is done with a manual jack method
- Tip casting failure: Kiln tip casting failure occurs every 3 to 4 months of continuous running of kiln. Earlier shuttering panel was 400×400 mm as the first kiln outlet retainer was just after 400 mm from the kiln outlet. After modification, outlet retainer shifted towards inlet about 400 mm, i.e., now tip casting shuttering increased to 800×800 mm. It gives us a maximum tip casting life of about 11 months.
What innovations in the refractory sector do you expect to see in the near future that will help better it?
The two main innovations that we foresee are:
AFR friendly refractory: Due to the increasing fuel cost and focus on sustainable ways of operations, the use of alternative fuels in cement industries is essential. Though, the use of alternative fuels is limited because of the high concentration of chlorine and sulphates which are susceptible to coating formation. Therefore, coating resistant refractories that are less prone to chlorine and sulphate attacks will increase the use of alternative fuels with a good refractory life. Moreover, with the enhanced use of AFR, we require good quality AFR friendly castable near AFR feeding zones.
Insulating Bricks: Refractories with low thermal conductivity and low radiation emissivity can help to save the heat losses that ultimately leads to saving fuel, instead of increasing refractory thickness. While by increasing the refractory thickness a loss of volume in pyro-equipment may affect the production capability of the system. Therefore, we required high alumina with low thermal conductivity refractory bricks to save the radiation loss.
–Kanika Mathur
You may like
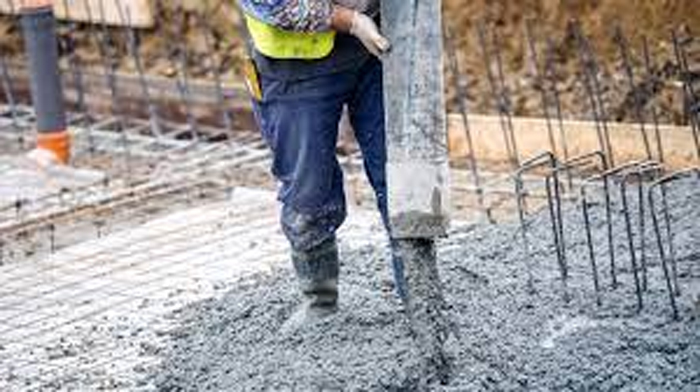
Tamil Nadu is set to host one of India’s five national carbon capture and utilisation (CCU) testbeds, aimed at reducing CO2 emissions in the cement industry as part of the country’s 2070 net-zero goal, as per a news report. The facility will be based at UltraTech Cement’s Reddipalayam plant in Ariyalur, supported by IIT Madras and BITS Pilani. Backed by the Department of Science and Technology (DST), the project will pilot an oxygen-enriched kiln capable of capturing up to two tonnes of CO2 per day for conversion into concrete products. Additional testbeds are planned in Rajasthan, Odisha, and Andhra Pradesh, involving companies like JK Cement and Dalmia Cement. Union Minister Jitendra Singh confirmed that funding approvals are underway, with full implementation expected in 2025.
Image source:https://www.heavyequipmentguide.ca/
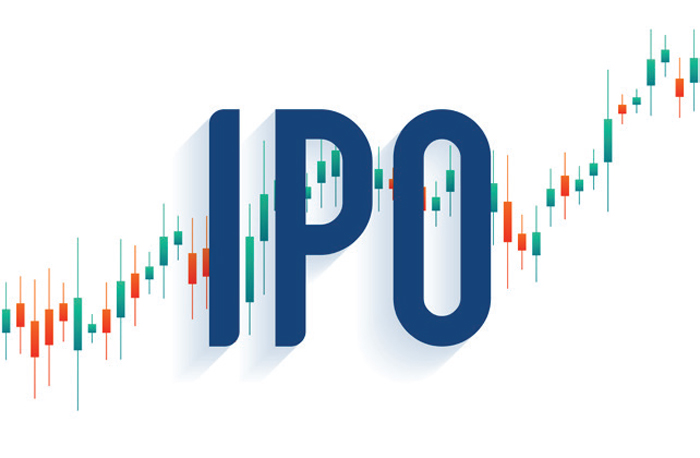
JSW Cement has set the price range for its upcoming initial public offering(IPO) at US$1.58 to US$1.67 per share, aiming to raise approximately US$409 million. As reported in the news, around US$91 million from the proceeds will be directed towards partially financing a new integrated cement plant in Nagaur, Rajasthan. Additionally, the company plans to utilise US$59.2 million to repay or prepay existing debts. The remaining capital will be allocated for general corporate purposes.
Concrete
Cement industry to gain from new infrastructure spending
Published
1 month agoon
July 24, 2025By
admin
As per a news report, Karan Adani, ACC Chair, has said that he expects the cement industry to benefit from the an anticipated US$2.2tn in new public infrastructure spending between 2025 and 2030. In a statement he said that ACC has crossed the 100Mt/yr cement capacity milestone in April 2025, propelling the company to get closer to its ambitious 140Mt/yr target by the 2028 financial year. The company’s capacity corresponds to 15 per cent of an all-India installed capacity of 686Mt/yr.
Image source:https://cementplantsupplier.com/cement-manufacturing/emerging-trends-in-cement-manufacturing-technology/