Environment
Improving energy efficiency in cement manufacturing
Published
7 years agoon
By
admin
The Indian government announced PAT, an innovative, market-based trading scheme, in 2008 under its National Mission on Enhanced Energy Efficiency (NMEEE) in the National Action Plan on Climate Change (NAPCC).
The industry has reduced its overall specific electrical energy consumption (SEC – Electricity), in cement production from 80 kilowatt hour/tonne of cement (kWh/t cement) in 2010 to 76 kWh/t cement in 2017. The steady increase in the production of blended cement (72 per cent) in 2016 and 2017 and improvements in the clinker factor have mostly driven this reduction. A decrease in clinker quantity in cement implies lower energy consumption for grinding. Despite increased use of petcoke and alternative fuels, frequent stop-starts due to market conditions and low capacity utilisation, the specific electrical energy use of clinkerisation (kWh/t clinker) decreased by nearly 1 kWh/t clinker compared to the baseline (2010).
The thermal SEC increased to 744 kcal/kg clinker in 2017 compared to 725 kcal/kg clinker in 2010. The increase in thermal SEC can be attributed to increased petcoke use, increases in alternative fuel use and frequent start/stops due to low market demand.
Market changes & improvements observed From 2010-2017, we have observed the following sectoral dynamics with respect to electrical and thermal energy-efficiency improvements.
Preheater and kilns: companies made a number of improvements in preheaters and kilns, such as the installation of platforms and alternative fuel feeding systems, nitrogen oxides (NOx) control systems, waste heat recovery from kiln shell radiation, energy-efficient blowers for kiln and calciner coal feeding systems and optimizing phase density, the pre-mixing of fuel and raw meal to improve heat transfer and reduce NOx, and modifications in cyclones based on computational fluid dynamics (CFD). The installation of alternative fuel feeding systems and NOx control systems results in increases in SEC.
Latest generation high-efficiency clinker coolers: improvements include the installation of high-efficiency clinker coolers by certain plants, recirculation systems to maximise cooler recuperation efficiency and excess power generation through WHRS installed on the cooler side, heat shields to improve cooler recuperation efficiency and the installation of latest generation efficient cooler grates.
Grinding systems: improvements include secondary classification in the grid cone, the use of CFD to improve classification efficiency, multi-drive systems, vibration-based sensors for filling control, the adoption of high-pressure grinding rollers (HPGR) instead of vertical roller mills (VRM) for slag and cement grinding, the optimization of air flow by providing angular flow channels below rollers, and the installation of latest generation classifiers.
Process fans: the major improvements observed are the installation of high-efficiency fans, preheater systems with fan SEC as low as 4 kWh/t clinker, and the use of slide gates instead of dampers for major fans with variable frequency drives (VFD).
Auxiliary equipment: auxiliary equipment such as vertical conveyors, tri-lobe blowers, three-phase transformers for increased collection efficiency in electrostatic precipitators, lower head pumps to cool water circuits with booster pumps for specific application, aluminum piping to reduce the pressure drop, water-cooled condenser coils for packaged air conditioning and the installation of screw chillers instead of compression chillers.
The Indian government announced PAT, an innovative, market-based trading scheme, in 2008 under its National Mission on Enhanced Energy Efficiency (NMEEE) in the National Action Plan on Climate Change (NAPCC). PAT aims to improve energy efficiency in industries by trading in energy-efficiency certificates in energy-intensive sectors.
Under the PAT scheme, designated consumers (DCs) are assigned targets for reducing their specific energy consumption. The target reduction for each DC is based on its energy-efficiency quotient during the baseline year (2010), such that energy-efficient DCs have a lower percentage reduction target compared to those that are less energy efficient.
The first PAT cycle period ran from 2012 to 2015 and included 85 cement plants. The target allocated to these plants was to reduce energy consumption by 0.815 million tonnes of oil equivalent (MTOE). The plants in PAT cycle 1 surpassed the energy saving targets and achieved savings of 1.48 MTOE, which is around 81 per cent higher than the savings target.
Under the PAT scheme, energy from alternative fuels is accounted for as zero. During PAT cycle 1, the most significant contributions were from the use of alternative fuels and waste heat recovery. PAT has further enhanced energy efficiency in the cement sector and, as a result, the sector is currently among the best globally. Some of the key measures that cement manufacturers have taken in India to achieve their PAT targets include: the installation of co-processing platforms and pre-processing systems to feed-in alternative fuels, resulting in reductions in carbon emissions; and the upgrading of conventional clinker cooler systems with latest generation ones.
PAT cycle 2 will cover 111 cement plants. The average reduction target for the sector in cycle 2 remains similar to that in cycle 1 (4-5 per cent). It will be challenging for the sector to achieve these targets since most of the easy changes have already been made. The appropriate pricing of Energy Saving Certificates (ESCerts) is crucial to ensuring the continued effectiveness of the PAT scheme.
Challenges to implementation
Over the last seven years (2010-2017, Indian cement companies reported several technical, financial and regulatory barriers to the adoption of technological advancements to improve electrical and thermal energy efficiency. Factors such as layout constraints, high moisture content in limestone and the burnability index of raw mix pose technical barriers for preheaters and kilns.
One of the major limitations in the installation of high-efficiency clinker coolers is the uncertainty around estimating the guaranteed benefits for retrofit installations. Additional shutdown time requirements for retrofits is another. In financial terms, incremental costs for new installations and overall costs for retrofit installations are also a challenge.
In terms of technology, there are still a few challenges, such as the capacity limitations of a roller press, whereas possibilities of higher efficiency are by voltage regulator module. Retrofitting costs to upgrade grinding technology are very high and have long payback periods, i.e., 6 -10 years (if only energy savings are considered). Challenges associated with retrofitting uniflow burners with advanced multi-channel burners include high costs and long payback periods. We have observed that many plants have installed the latest energy-efficient burners, which have shown good reductions in NOx generation and primary air consumption as low as 3.5 per cent.
In terms of energy-efficiency improvements in process fans, a few technical challenges are associated with layout in facilities where the ideal duct system cannot be accommodated. Moreover, the cost of retrofitting in certain cases could be high. Higher investment and operating costs for the latest auxiliary equipment could be a deterrent.
Examples of energy-efficiency improvements with the latest technological interventions:
The Indian cement industry is a pioneer in adopting the latest technologies to improve productivity and energy efficiency.
A plant in Madhya Pradesh has upgraded its conventional clinker cooler with the latest generation energy-efficient clinker cooler. This has resulted in reductions of 15-20 kcal/kg of clinker in specific heat consumption. The power consumption of the cooler section was also reduced by 0.59 kWh/t of clinker.
A company in Chhattisgarh has commissioned a new clinkersation line of 10,000 tonnes per day (tpd) with a six-stage preheater. The new clinkerisation unit is a state-of-the-art plant that is highly automated and has a latest generation energy-efficient clinker cooler. The specific heat consumption of the kiln is 697 kcal/kg clinker and the specific energy consumption of the kiln section is 13.0 kWh/t clinker.
A plant in Rajasthan has installed a medium voltage variable frequency drive (VFD) instead of a grid rotor resistance (GRR) for a kiln hybrid bag house fan, which has resulted in savings of around 160 kW. The investment incurred was Rs 6 million, with a simple payback period of 10 months.
SOURCE: Excerpts from the Low Carbon Technology Roadmap for the Indian Cement Sector: Status Review 2018, published by World Business Council for Sustainable Development (WBCSD).
Concrete
India donates 225t of cement for Myanmar earthquake relief
Published
4 weeks agoon
June 17, 2025By
admin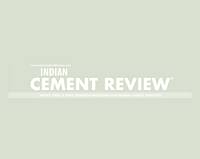
On 23 May 2025, the Indian Navy ship UMS Myitkyina arrived at Thilawa (MITT) port carrying 225 tonnes of cement provided by the Indian government to aid post-earthquake rebuilding efforts in Myanmar. As reported by the Global Light of Myanmar, a formal handover of 4500 50kg cement bags took place that afternoon. The Yangon Region authorities managed the loading of the cement onto trucks for distribution to the earthquake-affected zones.
Concrete
Reclamation of Used Oil for a Greener Future
Published
4 weeks agoon
June 16, 2025By
admin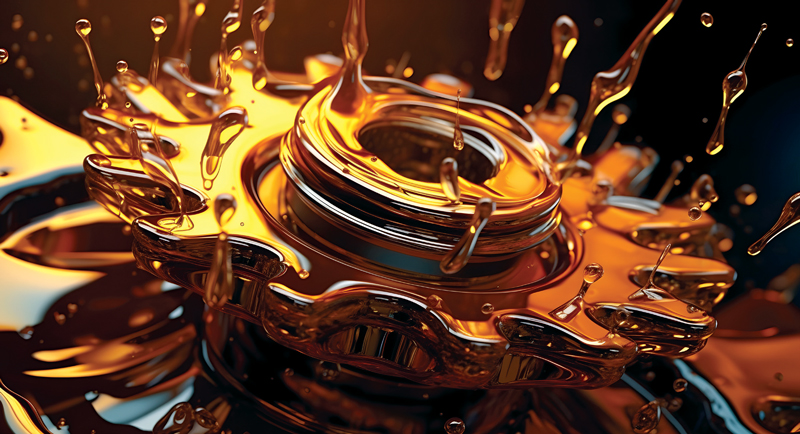
In this insightful article, KB Mathur, Founder and Director, Global Technical Services, explores how reclaiming used lubricants through advanced filtration and on-site testing can drive cost savings, enhance productivity, and support a greener industrial future. Read on to discover how oil regeneration is revolutionising sustainability in cement and core industries.
The core principle of the circular economy is to redefine the life cycle of materials and products. Unlike traditional linear models where waste from industrial production is dumped/discarded into the environment causing immense harm to the environment;the circular model seeks to keep materials literally in continuous circulation. This is achievedthrough processes cycle of reduction, regeneration, validating (testing) and reuse. Product once
validated as fit, this model ensures that products and materials are reintroduced into the production system, minimising waste. The result? Cleaner and greener manufacturing that fosters a more sustainable planet for future generations.
The current landscape of lubricants
Modern lubricants, typically derived from refined hydrocarbons, made from highly refined petroleum base stocks from crude oil. These play a critical role in maintaining the performance of machinery by reducing friction, enabling smooth operation, preventing damage and wear. However, most of these lubricants; derived from finite petroleum resources pose an environmental challenge once used and disposed of. As industries become increasingly conscious of their environmental impact, the paramount importance or focus is shifting towards reducing the carbon footprint and maximising the lifespan of lubricants; not just for environmental reasons but also to optimise operational costs.
During operations, lubricants often lose their efficacy and performance due to contamination and depletion of additives. When these oils reach their rejection limits (as they will now offer poor or bad lubrication) determined through laboratory testing, they are typically discarded contributing to environmental contamination and pollution.
But here lies an opportunity: Used lubricants can be regenerated and recharged, restoring them to their original performance level. This not only mitigates environmental pollution but also supports a circular economy by reducing waste and conserving resources.
Circular economy in lubricants
In the world of industrial machinery, lubricating oils while essential; are often misunderstood in terms of their life cycle. When oils are used in machinery, they don’t simply ‘DIE’. Instead, they become contaminated with moisture (water) and solid contaminants like dust, dirt, and wear debris. These contaminants degrade the oil’s effectiveness but do not render it completely unusable. Used lubricants can be regenerated via advanced filtration processes/systems and recharged with the use of performance enhancing additives hence restoring them. These oils are brought back to ‘As-New’ levels. This new fresher lubricating oil is formulated to carry out its specific job providing heightened lubrication and reliable performance of the assets with a view of improved machine condition. Hence, contributing to not just cost savings but leading to magnified productivity, and diminished environmental stress.
Save oil, save environment
At Global Technical Services (GTS), we specialise in the regeneration of hydraulic oils and gear oils used in plant operations. While we don’t recommend the regeneration of engine oils due to the complexity of contaminants and additives, our process ensures the continued utility of oils in other applications, offering both cost-saving and environmental benefits.
Regeneration process
Our regeneration plant employs state-of-the-art advanced contamination removal systems including fine and depth filters designed to remove dirt, wear particles, sludge, varnish, and water. Once contaminants are removed, the oil undergoes comprehensive testing to assess its physico-chemical properties and contamination levels. The test results indicate the status of the regenerated oil as compared to the fresh oil.
Depending upon the status the oil is further supplemented with high performance additives to bring it back to the desired specifications, under the guidance of an experienced lubrication technologist.
Contamination Removal ? Testing ? Additive Addition
(to be determined after testing in oil test laboratory)
The steps involved in this process are as follows:
1. Contamination removal: Using advanced filtration techniques to remove contaminants.
2. Testing: Assessing the oil’s properties to determine if it meets the required performance standards.
3. Additive addition: Based on testing results, performance-enhancing additives are added to restore the oil’s original characteristics.
On-site oil testing laboratories
The used oil from the machine passes through 5th generation fine filtration to be reclaimed as ‘New Oil’ and fit to use as per stringent industry standards.
To effectively implement circular economy principles in oil reclamation from used oil, establishing an on-site oil testing laboratory is crucial at any large plants or sites. Scientific testing methods ensure that regenerated oil meets the specifications required for optimal machine performance, making it suitable for reuse as ‘New Oil’ (within specified tolerances). Hence, it can be reused safely by reintroducing it in the machines.
The key parameters to be tested for regenerated hydraulic, gear and transmission oils (except Engine oils) include both physical and chemical characteristics of the lubricant:
- Kinematic Viscosity
- Flash Point
- Total Acid Number
- Moisture / Water Content
- Oil Cleanliness
- Elemental Analysis (Particulates, Additives and Contaminants)
- Insoluble
The presence of an on-site laboratory is essential for making quick decisions; ensuring that test reports are available within 36 to 48 hours and this prevents potential mechanical issues/ failures from arising due to poor lubrication. This symbiotic and cyclic process helps not only reduce waste and conserve oil, but also contributes in achieving cost savings and playing a big role in green economy.
Conclusion
The future of industrial operations depends on sustainability, and reclaiming used lubricating oils plays a critical role in this transformation. Through 5th Generation Filtration processes, lubricants can be regenerated and restored to their original levels, contributing to both environmental preservation and economic efficiency.
What would happen if we didn’t recycle our lubricants? Let’s review the quadruple impacts as mentioned below:
1. Oil Conservation and Environmental Impact: Used lubricating oils after usage are normally burnt or sold to a vendor which can be misused leading to pollution. Regenerating oils rather than discarding prevents unnecessary waste and reduces the environmental footprint of the industry. It helps save invaluable resources, aligning with the principles of sustainability and the circular economy. All lubricating oils (except engine oils) can be regenerated and brought to the level of ‘As New Oils’.
2. Cost Reduction Impact: By extending the life of lubricants, industries can significantly cut down on operating costs associated with frequent oil changes, leading to considerable savings over time. Lubricating oils are expensive and saving of lubricants by the process of regeneration will overall be a game changer and highly economical to the core industries.
3. Timely Decisions Impact: Having an oil testing laboratory at site is of prime importance for getting test reports within 36 to 48 hours enabling quick decisions in critical matters that may
lead to complete shutdown of the invaluable asset/equipment.
4. Green Economy Impact: Oil Regeneration is a fundamental part of the green economy. Supporting industries in their efforts to reduce waste, conserve resources, and minimise pollution is ‘The Need of Our Times’.
About the author:
KB Mathur, Founder & Director, Global Technical Services, is a seasoned mechanical engineer with 56 years of experience in India’s oil industry and industrial reliability. He pioneered ‘Total Lubrication Management’ and has been serving the mining and cement sectors since 1999.
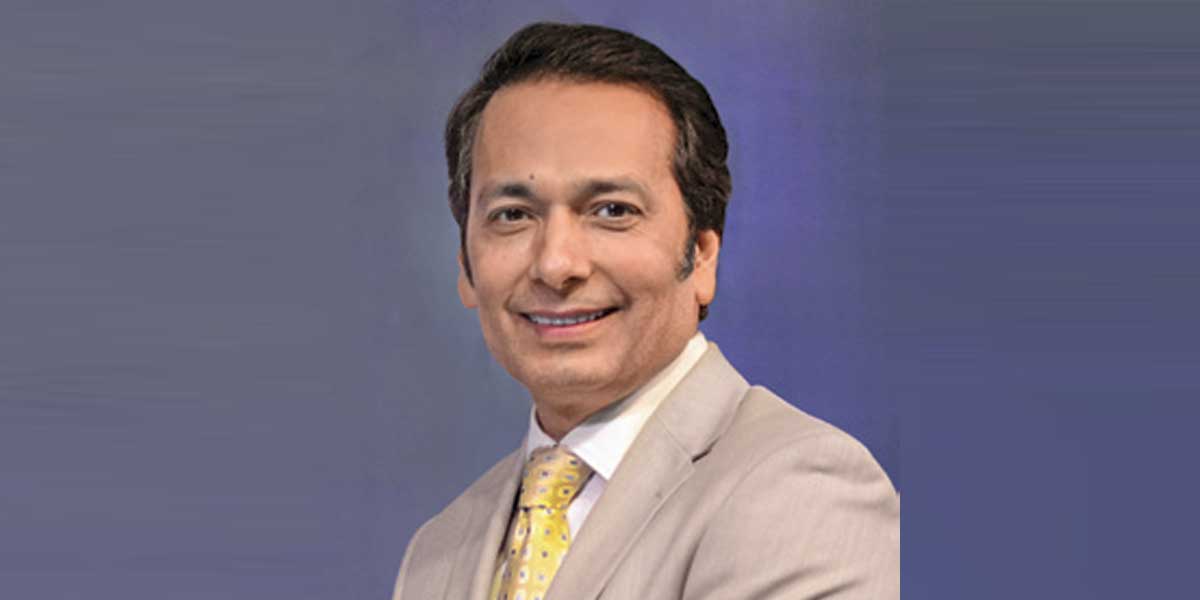
The Indian cement industry has reached a critical juncture in its sustainability journey. In a landmark move, the Ministry of Environment, Forest and Climate Change has, for the first time, announced greenhouse gas (GHG) emission intensity reduction targets for 282 entities, including 186 cement plants, under the Carbon Credit Trading Scheme, 2023. These targets, to be enforced starting FY2025-26, are aligned with India’s overarching ambition of achieving net zero emissions by 2070.
Cement manufacturing is intrinsically carbon-intensive, contributing to around 7 per cent of global GHG emissions, or approximately 3.8 billion tonnes annually. In India, the sector is responsible for 6 per cent of total emissions, underscoring its critical role in national climate mitigation strategies. This regulatory push, though long overdue, marks a significant shift towards accountability and structured decarbonisation.
However, the path to a greener cement sector is fraught with challenges—economic viability, regulatory ambiguity, and technical limitations continue to hinder the widespread adoption of sustainable alternatives. A major gap lies in the lack of a clear, India-specific definition for ‘green cement’, which is essential to establish standards and drive industry-wide transformation.
Despite these hurdles, the industry holds immense potential to emerge as a climate champion. Studies estimate that through targeted decarbonisation strategies—ranging from clinker substitution and alternative fuels to carbon capture and innovative product development—the sector could reduce emissions by 400 to 500 million metric tonnes by 2030.
Collaborations between key stakeholders and industry-wide awareness initiatives (such as Earth Day) are already fostering momentum. The responsibility now lies with producers, regulators and technology providers to fast-track innovation and investment.
The time to act is now. A sustainable cement industry is not only possible—it is imperative.

Hindalco Buys US Speciality Alumina Firm for $125 Million

Star Cement launches ‘Star Smart Building Solutions’

Nuvoco Vistas reports record quarterly EBITDA

UltraTech Cement increases capacity by 1.4Mt/yr

Shree Cement reports 2025 financial year results

Hindalco Buys US Speciality Alumina Firm for $125 Million

Star Cement launches ‘Star Smart Building Solutions’

Nuvoco Vistas reports record quarterly EBITDA

UltraTech Cement increases capacity by 1.4Mt/yr
