Process
Metso has years of know-how in different solutions for sand crushing and classification
Published
4 years agoon
By
admin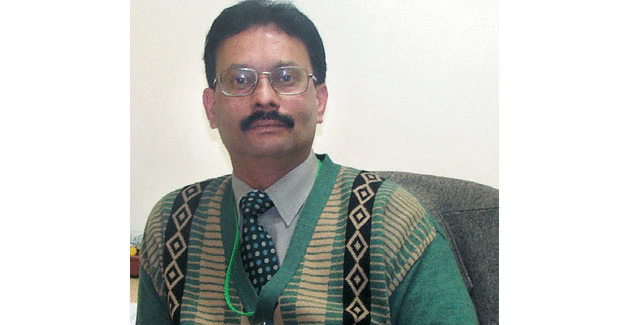
Niraj Srivastava Vice President, Technical Support, South East Asia, Japan and Korean, Metso
A factory-made product used in urban areas, the importance of manufactured sand is beyond doubt. From users? perspective, it is necessary for them to know the properties of the material and where it differs from natural sand. Through a conversation with Niraj Srivastava, Vice President, Technical Support, South East Asia, Japan and Korean of a multinational company Metso, a prominent suppliers of vertical shaft impactors, which produces artificial sand, ICR brings readers this information.
Why go for M sand when you can get natural sand?
The noticeable effects on environment and the eco-system caused by sand mining, together with the growing demand of aggregates to fulfill the construction requirements of the urban world has made it imperative to look for alternate solutions to the concern. That?s the reason; operators now wish to produce high-quality manufactured sand.
Manufactured sand is defined as a purpose-made crushed fine aggregate produced from a suitable source material. Production generally involves crushing, screening and separation into discrete fractions, recombining and blending may be necessary. Manufactured sand has a more predictable product consistency than natural sand variation. There are two main drivers.
Firstly, there is a lack of natural sand reserves. Urban expansion, local legislation and environmental constraints have made the extraction of natural sand and gravel an expensive activity. Application processes for greenfield sand and gravel extraction are often long, expensive affairs with a high chance of site applications being rejected. The increasing difficulty in extraction has had a negative effect on the bottom line for many producers. In many regions of the world, the extraction of sand and gravel is heavily taxed or banned completely, to try to preserve remaining deposits. The industry must find alternatives to meet the growing demand for fine aggregates.
The second driver is purely economic. A growing number of quarry operators have found that processed, high-quality manufactured sand can improve their bottom line and significantly reduce the percentage of waste and low value by-products.
Customer requirements for production less than 20 mm, especially for 5/20 mm, mean that significant amounts of 0/5 mm are produced as a by-product.
By utilising the correct process equipment, low value crusher dust can be processed into a high value, premium product. Concrete, mortar and asphalt sand production possibly depend on the material characteristics and regional regulations.
Manufactured sand shape, smooth surface texture, and grading have a significant effect on the performance of fresh concrete. Aggregate when blends with well-shaped, rounded, and smooth sand particles require less paste for a given slump than blends with flat, elongated, angular and rough particles, reduces inter-particle friction in the fine aggregate component of the concrete mix grading. Optimised manufactured sand with uniform grading results in aggregate blends with high packing and with low water demand. As a result, they are less expensive and will have less durability problems caused by the paste such as heat generation, porosity, and drying shrinkage.
The benefits of this process are two-fold: the producer secures new product offerings and reduces low value products; and the customer has access to a secure supply of sand with a stable grading curve.
What is the present status? What are the various options available?
Rising concerns about the alarmingly negative environmental impact, has seen strict measures making their way in the country. After banning mining of river sand and other minor minerals without the mandatory environment clearance, the National Green Tribunal (NGT) has also banned beach sand mining or removal of sand from river beds across the country without an environmental clearance. Yet, news about illegal sand mining keeps making its way to the national and regional dailies every now and then. The figure reported to have accounted for loss of minerals through such practices have run into multi-million tonnes.
In fact, the 2011 sand policy encourages establishment of manufactured sand units by giving top priority while allotting quarries. So, manufactured sand is the option. As natural sand is not replenished at the rate it is being used, the government has begun to promote manufactured sand. Experts vouch that manufactured sand is not only a viable alternative to natural sand, but is superior in many ways. Tests have revealed that characteristics of mortars and concrete using manufactured sand as fine aggregate are superior when compared to the natural sand as fine aggregate. Demand for manufactured fine aggregates for making concrete is increasing day-by-day as river sand cannot meet the rising demand. Because of its limited supply, the cost of natural river sand has sky rocketed and its consistent supply cannot be guaranteed. Under these circumstances, use of manufactured sand becomes inevitable.
What products do you are offering for making sand, capacities, product specifications, etc.?
Metso has years of know-how in different solutions for sand crushing and classification, and a good portfolio of related equipment to produce a high quality manufactured sand.
Sand crushing solutions from Metso: Shape is a major issue. This is where the crushing equipment?s role is critical to ensure an acceptable shape and size. Cone crushers, like the Metso Nordberg? HP Series???and GP Series??? enable the production of finer products together with coarser aggregates. They also lower the initial capital investment and save energy, due to the fewer crushing stages. They gives the producers high energy efficiency and capacity, good product gradation, a high reduction ratio and low sensitivity to rock hardness. Cavity design for cone crushers should be optimised to ensure that crushing occurs along the full length of the crushing zone between the liners. This causes inter-particle crushing to occur, leading to the highest possible generation of the required fines and cubically shaped products. Advances in high-speed cones with high clamping forces offer the opportunity to produce well-graded and shaped <20 mm product including well graded manufactured sand.
Studies show that the best end product for various purposes can be achieved with high-velocity impact crushing. The Metso Barmac? VSI vertical shaft autogenous impactor improves the soundness and shape of the material and produces a quality that is very close to natural sand. Unlike cones, VSI shaping is not influenced by the closed side setting (CSS), and shaping occurs throughout the product curve. The sand produced from rock-on-rock crushing is proven to have sound performance in concrete and mortar products. Such sand is well known for its cubical shape and consistent gradation. The gradation and quality of the product from the VSI does not tail off with increased wear on parts. This leads to the highest possible quality of performance in concrete and mortar mixes leading to reduced production costs. Sand classification solutions from Metso: Screens and classifiers are then used to remove the needed amount of fine particles and dust. Metso?s Triple Slope Screen (TS Screen) is used for final screening for manufactured sand as well as for plaster sand to take 2.36 mm down product. Metso Air Classifiers, which are environmentally friendly and economical to use, produce consistent sand quality.
Dual bearing TS screen ensures capacity and efficiency due to multi-slope profile with elliptical vibrating motion, which has 20-40 per cent more capacity compared to conventional inclined screen. Elliptical motion toward at feed end and backward at discharge end – particle retention time on screening surface more for efficient screening. Superior for aggregate and fines screening. Screening area varies from 7.6 to 25 sq m in double and triple deck option.
Metso?s air classification technology offers dry classification solutions to produce manufactured sand. The dry separation process separates fine and coarse particles. This allows a reduced percentage of super fines in manufactured sand. Classified manufactured sand for concrete has particles of equi-dimensional shape, an ?even? type particle size distribution. Thereby meeting specifications and achieving quality products.
Metso offers two classifier options to aggregate producers. The gravitational inertial classifier is typically fed 0/4 mm or less and makes separations between 300 microns (50#) and 63 microns (230#). These units are ideal for use in the manufacturing of concrete and asphalt sands that typically require a reduction in the amount of 63 microns (230#) present. It is designed with an internal re-circulating function that allows the efficiency of the separation to be adjusted depending on the desired grading curve. When finer separations are required, the centrifugal classifier can make separations of between 100 microns (140#) and 20 microns (625#). Making it suitable for production of very fine products such as lime, fly ash and fertilisers.
How is the process carried out once you identify the rock?
Geologist conduct geological survey and estimate the aggregate reserves and their quality; mining engineers mine that aggregate and bring it to the surface; while process engineers beneficiate mined aggregate by utilising controlled and optimised size reduction process with the help of crushing, screening and classification equipment in some cases to produce manufactured sand.
Reliability, performance and capacity wise, Metso crushing, screening and classifying equipment are already proven, as per IS383-1970 (Reaffirmed 2002). The quality of manufactured sand is classified in four categories – Zone 1, Zone 2 Zone 3 and Zone 4 depending upon purpose of use. Manufactured sand must follow these Zones. (Table 1) Higher the Zone numbers finer the gradation. In crushing and screening plant at second last stage, impact crusher, mainly a shaping machine produces cubical sand particle with smooth surface texture. To meet the above Zone, thus manufactured sand need to be classified with help of classifier.
List some of the users in India.
Mostly all three stage plants are supplied by Metso with Jaw + Cone + Barmac, produce Barmac sand along with other aggregate fractions. There are almost 18 air classifier AC 30 units installed/operational India by below named customers for producing classified sand.
Dilip Buildcon
Larsen & Toubro
Thriveni Earth Movers Ltd (TEMPL)
SEW Construction
VLS Rock Sand P Ltd
Ramky Infra
SGP Shrii Ent.
Beach Minerals Co
United Infra
Thomsun Granites
Table 1: Comparison of River Sand and Manufactured Sand
Properties | River Sand | Manufactured Sand | "Advantages of Manufactured Sand" |
---|---|---|---|
Shape | Spherical particle | Cubical Particle | "Higher cohesion and Compressive Strength" |
Gradation | Can not be controlled | Can be controlled | "Reduction in Void sand Higher strength" |
"Particles passing 75 microns" | "Up to 3 %( IS 383-1970)" | "Up to 15 %( IS 383-1970)" | Refer note below |
"Clay and Organic Impurities" | Likely to be present, retard the setting & compressive strength, Absent, Better Concrete Quality | Absent | Better Concrete Quality |
"Grading zone IS-383" | "Mostly conforms to Zone II and III" | "Manufactured to conforms to Zone II Sand" | "Zone II Sand is ideal for concrete" |
You may like
Process
Price hikes, drop in input costs help cement industry to post positive margins: Care Ratings
Published
4 years agoon
October 21, 2021By
admin
Region-wise,the southern region comprises 35% of the total cement capacity, followed by thenorthern, eastern, western and central region comprising 20%, 18%, 14% and 13%of the capacity, respectively.
The cement industry is expected to post positive margins on decent price hikes over the months, falling raw material prices and marked drop in overall production costs, said an analysis of Care Ratings.
Wholesale and retail prices of cement have increased 11.9% and 12.4%, respectively, in the current financial year. As whole prices have remained elevated in most of the markets in the months of FY20, against the corresponding period of the previous year.
Similarly, electricity and fuel cost have declined 11.9% during 9M FY20 due to drop in crude oil prices. Logistics costs, the biggest cost for cement industry, has also dropped 7.7% (selling and distribution) as the Railways extended the benefit of exemption from busy season surcharge. Moreover, the cost of raw materials, too, declined 5.1% given the price of limestone had fallen 11.3% in the same aforementioned period, the analysis said.
According to Care Ratings, though the overall sales revenue has increased only 1.3%, against 16% growth in the year-ago period, the overall expenditure has declined 3.2% which has benefited the industry largely given the moderation in sales.
Even though FY20 has been subdued in terms of production and demand, the fall in cost of production has still supported the cement industry by clocking in positive margins, the rating agency said.
Cement demand is closely linked to the overall economic growth, particularly the housing and infrastructure sector. The cement sector will be seeing a sharp growth in volumes mainly due to increasing demand from affordable housing and other government infrastructure projects like roads, metros, airports, irrigation.
The government’s newly introduced National Infrastructure Pipeline (NIP), with its target of becoming a $5-trillion economy by 2025, is a detailed road map focused on economic revival through infrastructure development.
The NIP covers a gamut of sectors; rural and urban infrastructure and entails investments of Rs.102 lakh crore to be undertaken by the central government, state governments and the private sector. Of the total projects of the NIP, 42% are under implementation while 19% are under development, 31% are at the conceptual stage and 8% are yet to be classified.
The sectors that will be of focus will be roads, railways, power (renewable and conventional), irrigation and urban infrastructure. These sectors together account for 79% of the proposed investments in six years to 2025. Given the government’s thrust on infrastructure creation, it is likely to benefit the cement industry going forward.
Similarly, the Pradhan Mantri Awaas Yojana, aimed at providing affordable housing, will be a strong driver to lift cement demand. Prices have started correcting Q4 FY20 onwards due to revival in demand of the commodity, the agency said in its analysis.
Industry’s sales revenue has grown at a CAGR of 7.3% during FY15-19 but has grown only 1.3% in the current financial year. Tepid demand throughout the country in the first half of the year has led to the contraction of sales revenue. Fall in the total expenditure of cement firms had aided in improving the operating profit and net profit margins of the industry (OPM was 15.2 during 9M FY19 and NPM was 3.1 during 9M FY19). Interest coverage ratio, too, has improved on an overall basis (ICR was 3.3 during 9M FY19).
According to Cement Manufacturers Association, India accounts for over 8% of the overall global installed capacity. Region-wise, the southern region comprises 35% of the total cement capacity, followed by the northern, eastern, western and central region comprising 20%, 18%, 14% and 13% of the capacity, respectively.
Installed capacity of domestic cement makers has increased at a CAGR of 4.9% during FY16-20. Manufacturers have been able to maintain a capacity utilisation rate above 65% in the past quinquennium. In the current financial year due to the prolonged rains in many parts of the country, the capacity utilisation rate has fallen from 70% during FY19 to 66% currently (YTD).
Source:moneycontrol.com
Process
Wonder Cement shows journey of cement with new campaign
Published
4 years agoon
October 21, 2021By
admin
The campaign also marks Wonder Cement being the first ever cement brand to enter the world of IGTV…
ETBrandEquity
Cement manufacturing company Wonder Cement, has announced the launch of a digital campaign ‘Har Raah Mein Wonder Hai’. The campaign has been designed specifically to run on platforms such as Instagram, Facebook and YouTube.
#HarRaahMeinWonderHai is a one-minute video, designed and conceptualised by its digital media partner Triature Digital Marketing and Technologies Pvt Ltd. The entire journey of the cement brand from leaving the factory, going through various weather conditions and witnessing the beauty of nature and wonders through the way until it reaches the destination i.e., to the consumer is very intriguing and the brand has tried to showcase the same with the film.
Sanjay Joshi, executive director, Wonder Cement, said, "Cement as a product poses a unique marketing challenge. Most consumers will build their homes once and therefore buy cement once in a lifetime. It is critical for a cement company to connect with their consumers emotionally. As a part of our communication strategy, it is our endeavor to reach out to a large audience of this country through digital. Wonder Cement always a pioneer in digital, with the launch of our IGTV campaign #HarRahMeinWonderHai, is the first brand in the cement category to venture into this space. Through this campaign, we have captured the emotional journey of a cement bag through its own perspective and depicted what it takes to lay the foundation of one’s dreams and turn them into reality."
The story begins with a family performing the bhoomi poojan of their new plot. It is the place where they are investing their life-long earnings; and planning to build a dream house for the family and children. The family believes in the tradition of having a ‘perfect shuruaat’ (perfect beginning) for their future dream house. The video later highlights the process of construction and in sequence it is emphasising the value of ‘Perfect Shuruaat’ through the eyes of a cement bag.
Tarun Singh Chauhan, management advisor and brand consultant, Wonder Cement, said, "Our objective with this campaign was to show that the cement produced at the Wonder Cement plant speaks for itself, its quality, trust and most of all perfection. The only way this was possible was to take the perspective of a cement bag and showing its journey of perfection from beginning till the end."
According to the company, the campaign also marks Wonder Cement being the first ever cement brand to enter the world of IGTV. No other brand in this category has created content specific to the platform.
Process
In spite of company’s optimism, demand weakness in cement is seen in the 4% y-o-y drop in sales volume. (Reuters)
Published
4 years agoon
October 21, 2021By
admin
Cost cuts and better realizations save? the ?day ?for ?UltraTech Cement, Updated: 27 Jan 2020, Vatsala Kamat from Live Mint
Lower cost of energy and logistics helped Ebitda per tonne rise by about 29% in Q3
Premiumization of acquired brands, synergistic?operations hold promise for future profit growth Topics
UltraTech Cement
India’s largest cement producer UltraTech Cement Ltd turned out a bittersweet show in the December quarter. A sharp drop in fuel costs and higher realizations helped drive profit growth. But the inherent demand weakness was evident in the sales volumes drop during the quarter.
Better realizations during the December quarter, in spite of the 4% year-on-year volume decline, minimized the pain. Net stand-alone revenue fell by 2.6% to ?9,981.8 crore.
But as pointed out earlier, lower costs on most fronts helped profitability. The chart alongside shows the sharp drop in energy costs led by lower petcoke prices, lower fuel consumption and higher use of green power. Logistics costs, too, fell due to lower railway freight charges and synergies from the acquired assets. These savings helped offset the increase in raw material costs.
The upshot: Q3 Ebitda (earnings before interest, tax, depreciation and amortization) of about ?990 per tonne was 29% higher from a year ago. The jump in profit on a per tonne basis was more or less along expected lines, given the increase in realizations. "Besides, the reduction in net debt by about ?2,000 crore is a key positive," said Binod Modi, analyst at Reliance Securities Ltd.
Graphic by Santosh Sharma/Mint
What also impressed analysts is the nimble-footed integration of the recently merged cement assets of Nathdwara and Century, which was a concern on the Street.
Kunal Shah, analyst (institutional equities) at Yes Securities (India) Ltd, said: "The company has proved its ability of asset integration. Century’s cement assets were ramped up to 79% capacity utilization in December, even as they operated Nathdwara generating an Ebitda of ?1,500 per tonne."
Looks like the demand weakness mirrored in weak sales during the quarter was masked by the deft integration and synergies derived from these acquired assets. This drove UltraTech’s stock up by 2.6% to ?4,643 after the Q3 results were declared on Friday.
Brand transition from Century to UltraTech, which is 55% complete, is likely to touch 80% by September 2020. A report by Jefferies India Pvt. Ltd highlights that the Ebitda per tonne for premium brands is about ?5-10 higher per bag than the average (A cement bag weighs 50kg). Of course, with competition increasing in the arena, it remains to be seen how brand premiumization in the cement industry will pan out. UltraTech Cement scores well among peers here.
However, there are road bumps ahead for the cement sector and for UltraTech. Falling gross domestic product growth, fiscal slippages and lower budgetary allocation to infrastructure sector are making industry houses jittery on growth. Although UltraTech’s management is confident that cement demand is looking up, sustainability and pricing power remains a worry for the near term.

Star Cement launches ‘Star Smart Building Solutions’

Nuvoco Vistas reports record quarterly EBITDA

UltraTech Cement increases capacity by 1.4Mt/yr

Shree Cement reports 2025 financial year results

Rekha Onteddu to become director at Sagar Cements

Star Cement launches ‘Star Smart Building Solutions’

Nuvoco Vistas reports record quarterly EBITDA

UltraTech Cement increases capacity by 1.4Mt/yr

Shree Cement reports 2025 financial year results
