Economy & Market
Cement Industry: Forging ahead despite odds
Published
13 years agoon
By
admin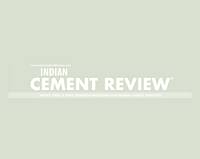
Indian cement industry is growing at a brisk pace of 9-10 per cent, in spite of the fact that it is saddled with excess capacity, and buffeted by slowing economy. However, the prospects of the industry remains bright as the high level of housing deficit in India and the infrastructure sector growth will drive the industry’s growth going forward.The cement industry in India is the second largest market after China with a total capacity of over 300 m tonnes (MT) as of financial year ended 2011-12. The industry has gone through a consolidation phase due to which the top three players alone control over a third of the total capacity. However, due to large number of players, the balance capacity remains quite fragmented.During the last decade, the Indian cement industry has registered a decent growth of about 9 per cent to 10 per cent. However, the per capita consumption of cement still remains quite low when compared with the world average. When compared with China’s per capita consumption of 1,380 kg in 2010, India’s per capita consumption at 230 kg is abysmally poor. The positive thing is that low per capita consumption indicates that there is huge scope for growth in the Indian cement industry.Cement industry in India is largely divided into five main regions, viz. north, south, west, east and the central region. This is because cement being a bulk commodity its transportation over long distances is uneconomical. In the last on year, capacity additions have happened at a faster rate than the growth in demand, due to which prices of cement have remained subdued.The principal growth driver for the cement industry is residential housing. However, with the government’s thrust on the infrastructure sector, this sector is likely to emerge as the next growth driver.ConcernsThe cement industry has been facing quite a few challenges due to adverse investment environment and rising fuel prices. Investment in cement plants is always on a long-term basis due to the long gestation period. Also, with interest rates at a high, the capital costs are high too. Licensing of coal and limestone reserves, supply of power from the state grid, etc. are controlled by the government, so the cement companies have no option but to buy from the state. The shortage of coal and the volatile fuel prices have forced the producers to rely on captive power. There is tough competition amongst the players, which also takes a toll on the company’s profitability.The Reserve Bank of India’s policy measures to increase interest rates aimed at curbing inflationary pressures resulted in credit crunch thereby adversely impacting real estate, infrastructure and other construction projects. The vagaries of monsoons and logistical bottlenecks slowed down construction work and, as a result, average industry capacity utilisation at one point fell to as low as 70 per cent. The low cement demand dented average realizations, while additional capacities exacerbated the oversupply situation. On the other hand, rising input and fuel costs hurt the margins of cement players, while export markets saw sluggish growth due to the slowdown in the global economy, especially the sagging construction activity in the Gulf region.ProspectsRising inflation, high interest rates, high prices of commodities and fuels have slowed down Indian economy and since the cement industry’s prospects are linked to the prospects of the economy, the cement industry would face an uphill task ahead. The housing sector consumes almost 60-70% of the country’s cement and if the slowdown in real estate persists for an extended period, it would adversely impact the consumption of cement.Despite the overcapacity situation in the cement industry, several major capacity additions on the anvil in the next few years in anticipation of rise in cement demand. As a result, the supply overhang would persist for the next two-three years, putting pressure on realizations. The demand for cement is likely to grow at around 8-9 per cent due to the government’s thrust on infrastructure and housing.ACCCement House, 121, Maharshi Karve Road, Mumbai – 400 020Phone: +91-22-33024321 Fax: +91-22-66317440 www.acclimited.comKuldip K Kaura, CEO & MDACC is India’s foremost manufacturer of cement and concrete. ACC’s operations are spread throughout the country with 16 modern cement factories with installed capacity of about 30 mn tonnes p.a., more than 40 Ready Mix Concrete plants, 21 sales offices, and several zonal offices. It has a workforce of about 9,000 persons and a countrywide distribution network of over 9,000 dealers.The house of Tata was associated with ACC upto 2000. Between 999 and 2000, the Tata group sold all 14.45 per cent of its shareholding in ACC in three stages to subsidiary companies of Gujarat Ambuja Cements (later called Ambuja Cement), who then became the largest single shareholder in ACC. In January 2005, Holcim Group of Switzerland announced its plans to enter into a long-term strategic alliance with the Ambuja Group by acquiring a majority stake in Ambuja Cements India (ACI), which at the time held 13.8 per cent equity stake in ACC. Holcim, along with ACI, also made an open offer to ACC shareholders, through Holdcem Cement and ACI, to acquire a majority shareholding in ACC. Consequently, ACI’s equity stake in ACC increased to 34.69 per cent after which ACI declared itself as a promoter of ACC.Ambuja CementsElegant Business Park, MIDC Cross Road ‘B’, Off Andheri-Kurla Road., Andheri (E), Mumbai 400059Tel : 022 – 40667000 www.ambujacement.comOnne van der Weijde, Managing DirectorAmbuja Cements Ltd (ACL) is one of the leading cement manufacturing companies in India. The company, initially called Gujarat Ambuja Cements, was founded by Narottam Sekhsaria in 1983 with a partner, Suresh Neotia. The company commenced cement production in 1986. The global cement major Holcim acquired management control of ACL in 2006. Holcim today holds little over 46% equity in ACL. The Company is currently known as Ambuja Cements. ACL’s current cement capacity is about 25 million tonnes. The company has five integrated cement manufacturing plants and eight cement grinding units across the country. ACL is one of the most efficient cement manufacturers in the world. ACL is the first Indian cement manufacturers to build a captive port with three terminals along the country’s western coastline to facilitate timely, cost effective and environmentally cleaner shipments of bulk cement to its customers. The company has its own fleet of ships. ACL has also pioneered the development of the multiple bio-mass co-fired technology for generating greener power in its captive plants.Bagalkot CementStadium House, Block No.1, 6th Floor, Veer Nariman Road, Churchgate, Mumbai – 400 020.Tel : 022-22023841, 22023897 Fax : 022-22022884 www.bagalkotcement.comAjay Kanoria, Chairman & MD,Bagalkot Cement and Industries (BCIL) is a Kanoria Group Initiative that was incorporated in 2007 to acquire the cement division of Bagalkot Udyog. BCIL manufactures two classes of cement – BAGALKOT SHAKTI and BAGALKOT SUPREME with four decades of technical expertise, innovation, quality control and professionalism. It is one of the many cement manufacturing units in the North Karnataka. The cement factory started in 1955 with the wet process kiln of 300-tpd capacity. It was converted to a dry process kiln in 1982. Currently the plant manufactures 297,000 TPA of Cement.Binani CementMercantile Chambers, 2nd Floor, 12 JN Heredia Marg, Ballard Estate, Mumbai – 400 001Tel : 022-22690506-10 Fax : 022-22690001, 22690003 www.binaniindustries.comBraj Binani, ChairmanFollowing the restructuring of the Braj Binani Group, between 1996 and 2004, Binani Industries (BIL) was founded to serve as the holding company for Binani Cement, Binani Zinc, Goa Glass Fibre and BT Composites. After establishing its footprint firmly in India, China and Dubai, the Braj Binani Group is now envisioning to explore newer global horizons. Setting its sights on emerging markets like South Africa, East Africa and Mauritius, the Group is endeavouring to establish a strong network of Binani Cement presence across the globe. The Braj Binani Group’s focused continual improvement has been recognised with internationally accepted certifications for its various ventures.Birla Corporation14, Government Place (East), Kolkata 701 069Tel: 033-22483131(D), 22481111 Fax: 033-22486960, 4572 www.birlacorporation.comHarsh V. Lodha, Chairman,Birla Corporation is the flagship company of the M.P. Birla Group. Incorporated as Birla Jute Manufacturing Company in 1919, the late chairman Madhav Prasad Birla transformed it from a manufacturer of jute goods to a leading multi-product corporation with widespread activities. Under the chairmanship of Priyamvada Birla, the company crossed the Rs 1300-crore turnover mark and the name was changed to Birla Corporation in 1998. After the demise of Priyamvada Birla, the late Rajendra S. Lodha, became the chairman of the M.P. Birla Group. Harsh V Lodha is currently the chairman of the company. Birla Corporation has products ranging from cement to jute goods, PVC floor covering, as well as auto trims (jute felt-based car interiors).Cement Corporation of IndiaScope Complex, Core No. 5, 7, Lodhi Road, New Delhi – 110 003.Tel : 011-24360005/ 24360099 Fax : 011-24360464/ 24364555 www.cementcorporation.co.inR. P. Tak, Chairman & MD,Cement Corporation of India (CCI) is a company established in 1965 and wholly owned by Government of India. CCI is a multi unit organisation at present having ten units spread over eight states with a total annual installed capacity of 38.48 lakh MT. In line with the advancement in cement technology CCI had been adopting the latest one with one million tonne plants at Tandur and Nayagaon. CCI manufactures various types of cements like Portland Pozzolana Cement (PPC), Portland Slag Cement (PSC) & Ordinary Portland Cement (OPC) of varying grades viz. 33, 43,53 and 53S (special grade cement for manufacture of sleepers for Indian Railways) grades. under strict quality control with the brand name of CCI Cement. CCI has a strong work-force of 988 employees.Cement Manufacturing Company
281, Deepali, Pitampura, New Delhi – 110 034Tel: 011-27033821/22/27 Fax: 011-27033824 www.cmcl.co.inSajjan Bhajanka, Vice Chairman & MDCement Manufacturing Company (CMC) is the largest cement manufacturer in north east India. The company’s plant is spread across 40 acres of land in the idyllic town of Lumshnong, a strategic location at Meghalaya that ensures easy availability of high-grade limestone. Its brand "Star Cement" has established itself as the most accredited brand of the region. CMCL’s product range includes Ordinary Portland Cement (OPC 43-Grade) and (OPC 53-Grade) and Portland Pozzolana Cement (PPC) in line with evolving customer needs. Presently, CMCL is marketing clinker to different grinding units located in India, Nepal & Bhutan, along with cement of 3 types. The company’s institutional customers comprise L&T, NHPC, PWD, Indian Railways and Ministry of Defence.Chettinad Cement CorporationRani Seethai Hall Building, 603, Anna Salai, Chennai – 600 006Tel : 044-28292727, 28292040 Fax : 044-28291558 www.chettinad.comM.A.M.R. Muthiah, Managing DirectorChettinad Cement is operating its cement business spanning three generations. Since its establishment in 1962 with a wet process cement plant at Puliyur near Karur, Chettinad cement has been expanding and making itself versatile in the field of cement products. Major supplier of Southern India’s cement needs, Chettinad Cement supplies cement for many residential, commercial and engineering projects. Chettinad Cement has established its position in the southern market by innovatively aligning its products and services to the needs of cement users. Its ‘Builders Choice’ brand offers extensive range of bagged products, including Ordinary Portland cements and blended cements to suit most building and construction applications.Dalmia Cement (Bharat)11th & 12th Floors, Hansalaya Building, 15, Barakhamba Road, New Delhi – 110 001Tel : 011-23310121 Fax : 011-23313303 www.dalmiacement.comPuneet Dalmia, Managing DirectorFounded in 1935 by Jaidayal Dalmia; the cement division of DCBL was established in 1939 and enjoys 70 years of expertise and experience. The company has cement plants in southern states of Tamil Nadu (Dalmiapuram & Ariyalur) and Andhra Pradesh (Kadapa), with a capacity of 9 million tonnes per annum. The company is a pioneer in super specialty cements used for oil wells, railway sleepers and air strips. The company holds a stake of 45.4% in OCL India, a major cement player in the eastern region, and now control a cement capacity of 14.3 million tonnes and has a strong presence in southern and eastern regions of the country. With the plant located close to its source of raw materials, the company keeps its freight and transport costs low, giving it an edge over competition.Gujarat Sidhee CementNKM International House, 178, Backbay Reclamation, Mumbai – 400 020Tel : 022-66365444, 32955563 Fax : 022-66365445 www.hathi-sidheecements.comM.S. Gilotra, Managing DirectorGujarat Sidhee Cement (GSC), a part of the Mehta Group, markets cement under the brand name ‘Sidhee’. The company manufacturers Oridanary Portland Cement (OPC) 53 grade, 43 grade, Portland Pozzolana Cement (PPC) types of cement and clinker. GSCL is one of the first Indian cement company to get 53 grade license. GSC is a recognized Export House and has won the Indian cement industry’s prestigious National Productivity Awards thrice in succession .The Indian arm of the Mehta Group comprises of "Saurashtra Cement " (SC), marketing cement under the brand name "Haathi". Saurashtra Cement manufacturers Portland Pozzolana Cement (PPC), Ordinary Portland Cement (OPC 53 grade, 43 grade), SRPC types of cement and clinker. SCL is a recognized Export House and has won the Indian cement industry’s prestigious national award for ‘Energy Efficiency.’Heidelberg Cement India9th Floor, Tower-C, Infinity Towers, DLF Cyber City, Phase-II, Gurgaon – 122 002, HaryanaTel : 0124-4503700 Fax : 0124-4147692 www.mycemco.comAshish Guha, Managing DirectorHeidelberg Cement India (MCL), a Heidelberg Cement Group Company, was promoted in 1958 by a Karnataka-based industrialist in technical and financial collaboration with Kaisers of USA as a Public Limited Company. Pursuant to the Share Subscription and Share Purchase Agreement and Escrow Agreement Cementrum I B.V.(subsidiary of Heidelberg Cement AG) acquired equity shares from the S.K. Birla Group and its affiliates. In addition, further equity shares were acquired under the open offer giving Cementrum I B.V. 54.89 per cent shareholding in Heidelberg Cement India. Heidelberg Cement Group, with its core products being cement, ready mixed concrete, aggregates and related activities, is one of the leading producers of building materials worldwide, and it employs around 54,000 people in more than 40 countries.India Cements"Coromandel Towers" 93,Santhome High Road, Karpagam Avenue, Raja Annamalai Puram, Chennai – 600 028Tel : 044-28524004 Fax : 044-28520702 www.indiacements.co.inN. Srinivasan, Vice Chairman & MD,India Cements was established in 1946 and the first plant was setup at Sankarnagar in Tamilnadu in 1949 . Since then it has grown to seven plants spread over Tamil Nadu and Andhra Pradesh. The capacities as on March 2010 have reached 14.05 mtpa. The company is the largest producer of cement in South India with its plants well spread with three in Tamil Nadu and four in Andhra Pradesh which cater to all major markets in South India and Maharashtra. The company is the market leader with a market share of 28% in the South. The company has access to huge limestone resources and plans to expand capacity by debottlenecking and optimisation of existing plants as well as by acquisitions. The company has a strong distribution network with over 10,000 stockists of whom 25 per cent are dedicated. The company has well established brands- Sankar Super Power, Coromandel Super Power and Raasi Super Power.Jaiprakash AssociatesSector-128 NOIDA – 201 304 (U.P.) Tel : 0120-4609000, 2470800, 4609002 (D) Fax : 0120-460964, 460946 www.jalindia.comSunny Gaur, Managing Director (Cement)Jaypee Group is the 3rd largest cement producer in the country. The group produces special blend of Portland Pozzolana Cement under the brand name ‘Jaypee Cement’ (PPC). Its cement division currently operates modern, computerized process control cement plants with an aggregate capacity of 28 MTPA. The company is in the midst of capacity expansion of its cement business in Northern, Southern, Central, Eastern and Western parts of the country and is slated to be 35.90 MTPA by FY13 (expected) with captive thermal power plants totaling 672 MW.JK CementsKamla Tower, Kanpur, Uttar Pradesh.Tel : 0512-2371478-81 Fax : 0512-2399854, 2394250 www.jkcement.comYadupati Singhania, MD & CEOThe company’s cement operations commenced commercial production in May 1975 at its first plant at Nimbahera in the state of Rajasthan. Today, JK Cement is one of the largest cement manufacturers in north India. The company is also the second largest white cement manufacturer in India by production capacity. While the grey cement is primarily sold in the northern India market, the white cement enjoys demand in the export market including countries like South Africa, Nigeria, Singapore, Bahrain, Bangladesh, Sri Lanka, Kenya, Tanzania, UAE and Nepal.JK Lakshmi CementNehru House, 4th Floor, 4, Bahadurshah Zafar Marg, New Delhi – 110 002.Tel : 011-23311112 Fax : 011-23722251, 23712680 www.jklakshmi.comVinita Singhania, Managing Director,One of the established names in the cement industry, JK Lakshmi Cement has state-of-the-art plant at Jaykaypuram, district Sirohi, Rajasthan. With the capacity expansion and further commissioning of split location grinding units at Motibhoyan, Kalol (Gujarat) & Bajitpur, Jhajjar (Haryana) the combined capacity of the company today stands at 5.30 mn. MTPA. The company uses the latest technology from Blue Circle Industries and modern equipments from Fuller International of USA.Kalyanpur CementsMaurya Centre, 1, Fraser Road, Patna – 800 001Tel : 0612-2225819 Fax : 0612-2239884 www.kalyanpur.comAnant Prakash Sinha, Managing Director,Kalyanpur Cements is a leading cement manufacturer in eastern India. It runs the only integrated cement manufacturing facility in Bihar and markets its cement in Bihar, Jharkhand and Uttar Pradesh. Kalyanpur was established in 1938 and markets its cement under the popular KC Super, KC Special and Castcrete brands.KCPRamakrishna Buildings, 2, Dr. P.V. Cherian Crescent, Egmore, Chennai 600 008Tel : 044-66772609/10 Fax : 044-66772680 www.kcp.co.inV.L. Indira Dutt, Jt. Managing DirectorKCP, one of the country’s oldest cement producers, has a strong presence in the south India market. KCP strategically chose the greenfield plant located at Ramakrishnapuram, Muktyala Village, Jaggayyapet Mandal in Krishna district of Andhra Pradesh because it is close to large limestone reserves and provides easy access to the key markets of Andhra Pradesh, Tamil Nadu, Karnataka and Orissa. The company’s energy-efficient plant has an annual capacity of 1.52 million tonnes. Its cement plant at Macherla in Andhra Pradesh is India’s first dry process kiln and was installed in 1958 by HUMBOLDT, Germany even while it was still a prototype in Europe.Kesoram IndustriesP.O. Basantnagar – 505 187, Dist. Karimnagar (A.P.).Tel : 033-22435453, 22429454, 22135121; 08728-228123(D) Fax : 08728-228160, 228444 www.kesocorp.comK.C. Jain, Wholetime Director,Kesoram Industries has two units manufacturing under two brand names, viz Vasavadatta Cement and Kesoram Cement. While Vasavadatt unit is located at Sedam in Gulbarga district of Karnataka, Kesoram unit is located at Basantnagar in Karimnagar district of Andhra Pradesh. The installed capacity of Sedam unit is 57.5 lakh metric tonnes, the installed capacity of Basantnagar unit is 15 metric tonnes. The performance of cement division has been quite good during FY 11-12, with the company’s income from cement division rising from Rs 1852 crore in 2010-11 to Rs 2060 crore in 2011-12. The operating profit from the cement division jumped from Rs 274 crore in FY2010-11 to Rs 439 crore in FY2011-12NCL Industries7th Floor, Raghava Ratna Towers, Chirag Ali Lane, Abids, Hyderabad 500001Phone: 040-23201146, 23203637 www.nclind.comK Ravi, Managing DirectorNCL Industries, the flagship company of the NCL group of industries, has been serving the construction industry of Andhra Pradesh for the past 25 years with its cement under the brand name ‘Nagarjuna Cement’, which is an established premium brand in the coastal districts of Andhra Pradesh. The company expanded the capacity of the cement plant by stages from 200 TPD to 900 TPD. The company which is now operating two units and has expanded its capacity of 2,000 MT per day to 6,000 MT per day and is poised to have a capacity of two million tonnes per annum.Penna Cement IndustriesPlot No. 705, No. 8-2-268/A/1/5/1, Road No. 3 Banjara Hills, Hyderabad 500 034Phone: 040-44565100 Fax No. 040-23328073, 23355941, 23353947 www.pennacement.comP. Prathap Reddy, Managing DirectorPenna Cement Industries (PCI) was formed in year 1991 by Prathap Reddy. First plant was commissioned in 1994 at Talaricheruvu village in Tadipatri Mandal of Ananthapur district of Andhra Pradesh with initial capacity of 0.2 MTPA. Penna Cement has operational plants and with plans for setting up grinding units and packing units at various locations with total installed capacity of 7 MTPA. Penna Cement manufactures a wide range of cement including Ordinary Portland Cement (OPC 53grade and 43 grade), Portland Pozzolana Cement (PPC), Portland Slag Cement (PSC).Prism CementRahejas, Main Avenue, Vallabhai Patel Road, Santacruz (W), Mumbai 400 054.Tel: 91 22 6675 4142/3/4. Fax: 91 22 2600 1304. www.prismcement.comManoj Chhabra, Managing DirectorPrism Cement commenced its production in August 1997 and manufactures Portland Pozzollana Cement with the brand name ‘Champion’ and Ordinary Portland Cement (OPC). It has the highest quality standards due to efficient plant operations with automated controls. It caters mainly to markets of UP, MP and Bihar, with an average lead of 340-370 km of its plant at Satna, MP. It has integrated building materials company with a wide range from cement, ready-mixed concrete, tiles, and bath products to kitchens. The company has three Divisions, viz. Prism Cement, H & R Johnson (India), and RMC Readymix (India). Prism Cement Limited also has a 74% stake in Raheja QBE General Insurance Company Limited, a JV with QBE Group of Australia.UltraTech Cement
"B" Wing, 2nd floor, Ahura Centre, Mahakali Caves Road, Andheri (East), Mumbai 400 093.Tel: 91-22-66917800; Fax: 91-22-66928109 Website: www.ultratechcement.comO. P. Puranmalka, Whole-Time Director,UltraTech Cement is the ultimate 360? building materials destination, providing an array of products ranging from grey cement to white cement, from building products to building solutions and an assortment of ready mix concretes catering to varied needs and applications. UltraTech’s products include Ordinary Portland cement, Portland Pozzolana cement and Portland blast-furnace slag cement. UltraTech is India’s largest exporter of cement clinker spanning export markets in countries across the Indian Ocean, Africa, Europe and the Middle East. The company exports over 2.5 million tonnes per annum, which is about 30 per cent of the country’s total exports. UltraTech and its subsidiaries have a presence in 5 countries through 11 integrated plants, 1 white cement plant, 1 clinkerisation plant, 15 grinding units, 2 rail and 3 coastal terminals and 101 RMC plants.
You may like
Concrete
Shree Cement reports 2025 financial year results
Published
7 days agoon
June 17, 2025By
admin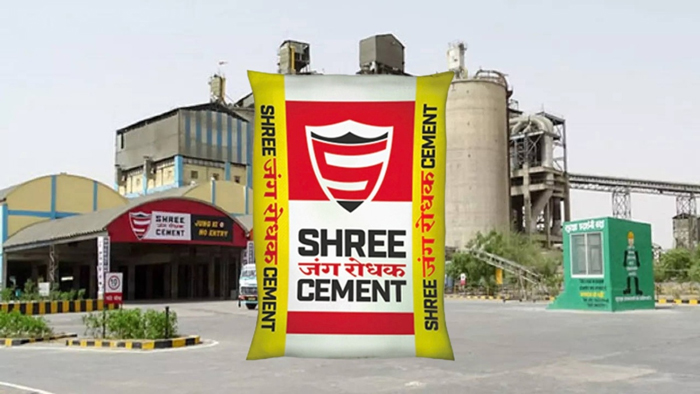
Shree Cement posted revenue of US$2.38 billion for FY2025, marking a 5.5 per cent decline year-on-year. Operating costs rose 2.9 per cent to US$2.17 billion, resulting in an EBITDA of US$528 million—down 12 per cent from the previous year. Net profit fell 50 per cent to US$141 million. The company reported cement sales of 9.84Mt in Q4 FY2025, a 3.3 per cent increase from 9.53Mt in Q4 FY2024, with premium products making up 16 per cent of total sales.
Image source:https://newsmantra.in/
Concrete
Rekha Onteddu to become director at Sagar Cements
Published
7 days agoon
June 17, 2025By
admin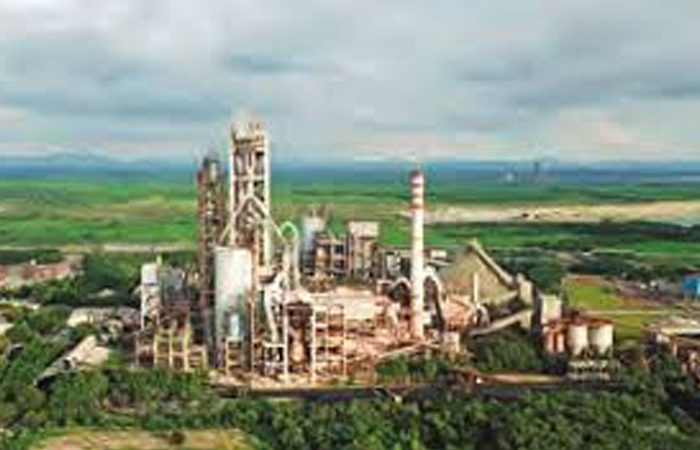
Sagar Cements has announced the appointment of Rekha Onteddu as a non-executive independent director, effective 30 June 2025. According to People in Business News, Rekha Onteddu is currently serving in a similar capacity at Andhra Cements, the parent company of Sagar Cements.
Image source:https://sagarcements.in/
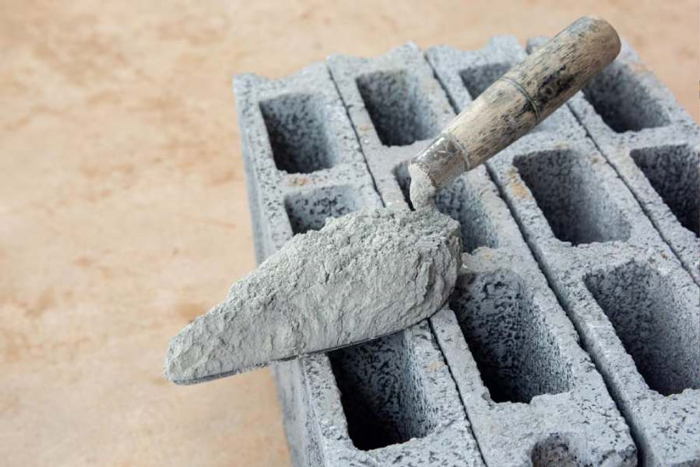
According to a Moody’s report, India’s cement consumption is projected to rise by 50 per cent over the next five years, increasing from 445 million metric tons per annum (MMTPA) in FY24 to 670 MMTPA by 2030. This growth is expected to be driven by government infrastructure spending and rising housing demand, with an anticipated annual growth rate of 6-7 per cent. To meet this demand, major cement companies are likely to continue acquiring smaller, less profitable firms.
Image source:https://www.telegraphindia.com/

Star Cement launches ‘Star Smart Building Solutions’

Nuvoco Vistas reports record quarterly EBITDA

UltraTech Cement increases capacity by 1.4Mt/yr

Shree Cement reports 2025 financial year results

Rekha Onteddu to become director at Sagar Cements

Star Cement launches ‘Star Smart Building Solutions’

Nuvoco Vistas reports record quarterly EBITDA

UltraTech Cement increases capacity by 1.4Mt/yr

Shree Cement reports 2025 financial year results
