Concrete
Water conservation is vital in our mining operations
Published
10 months agoon
By
admin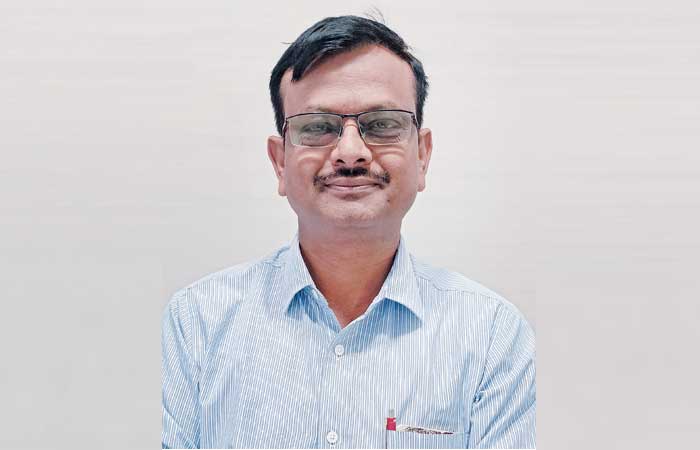
Pankaj Agarwal, Vice President – Mines, Shree Cement, discusses the company’s commitment to sustainable mining through innovative practices like reducing diesel consumption, integrating recycled materials and implementing advanced digital technologies, all aimed at minimising environmental impact.
Sustainable mining practices are becoming increasingly important for the cement industry. How is your company ensuring that mining operations for raw materials like limestone align with sustainable development goals?
At Shree Cement, we are deeply committed to sustainable mining practices, ensuring that our mining operations for raw materials like limestone align with global sustainable development goals. We have comprehensive mine operation and closure plans in place for all active sites. Our approach emphasises maximising efficiency through advanced structural mapping, which allows us to plan operations with minimal wastage and ensure optimal recovery of limestone. This includes reserve estimation and daily planning, which are crucial for sustainable resource management.
A key part of our sustainability efforts focuses on reducing diesel consumption in our mining equipment, with several notable initiatives already in place. For example, at our Nawalgarh mine, we strategically placed the crusher 70 meters deep within the limestone quarry, which has eliminated the need for upgradient transportation and is projected to save approximately 3.84 lakh litres of diesel annually over the mine’s lifetime. Similarly, the introduction of optimised and automated high-pressure drill machines at our Ras, Nawalgarh, and Raipur mines is helping to save an estimated 7.91 lakh litres of diesel each year. Additionally, by replacing traditional dumpers with tippers for overburden transportation at Nawalgarh, we anticipate saving around 21 million litres of diesel throughout the lifespan of the mine.
We’ve also implemented an Operator Independent Truck Dispatch System (OITDS) at our Ras and Raipur sites, which has significantly reduced idle time for trucks, resulting in an annual diesel savings of 7.27 lakh litres. These initiatives not only demonstrate our commitment to reducing our carbon footprint but also serve as a model for sustainable mining operations. Given the success of these efforts, we are actively exploring the possibility of rolling out similar initiatives at other locations wherever feasible.
What initiatives has your organisation implemented to reduce the environmental impact of quarrying activities for cement production, particularly in terms of land rehabilitation and biodiversity conservation?
We are committed to minimising the environmental impact of quarrying activities through a proactive approach centred on land rehabilitation and biodiversity conservation. Prior to the commencement or expansion of any project, we conduct thorough Environmental Impact Assessments (EIA) to evaluate potential risks related to biodiversity, water resources, and other environmental factors. These assessments are tailored to each site and include adjacent areas within a 10-kilometer radius of our operations. Any identified risks are addressed by implementing location-specific conservation plans that align with our overarching goal of achieving a ‘Net Positive Impact’ on biodiversity.
To ensure we uphold the highest standards of environmental stewardship, we avoid operating in world heritage sites, ecologically sensitive zones, protected areas, or regions with high biodiversity value. Our mitigation strategy is comprehensive, following a hierarchy of avoid, minimise, restore, and offset. This approach allows us to systematically address any negative impacts on local ecosystems.
While we have not yet closed any mines, we have detailed mine closure plans in place for every active site. These plans emphasise progressive mine rehabilitation, which involves restoring mined-out areas through afforestation, re-vegetation, or converting these sites into water bodies, as appropriate. Our goal is to enhance local biodiversity by reintroducing native plant species, ultimately restoring the natural ecosystem. This long-term commitment reflects our dedication to responsible mining practices that prioritise the preservation and restoration of natural landscapes for future generations.
In terms of reducing carbon emissions, how is your company approaching the challenge of sustainable mining, and what technologies or methods are you using to minimise your carbon footprint during material extraction?
Reducing our carbon footprint is central to our sustainable mining efforts. We have implemented a range of innovative technologies and strategies to lower fuel consumption and minimise emissions during material extraction. For instance, we have optimised material transportation systems across our sites, such as strategically placing crushers within limestone quarries to minimise haulage distances. This has significantly reduced diesel consumption. Additionally, our mines are equipped with automated high-pressure drill machines, enhancing operational efficiency and lowering fuel use.
We have also replaced conventional dumpers with more fuel-efficient tippers for overburden removal, further reducing diesel reliance. Advanced systems like the Operator Independent Truck Dispatch System (OITDS) are in place to streamline logistics, curbing truck idle time and contributing to substantial fuel savings across key locations. To further reduce our reliance on fossil fuels, we have installed solar-powered lighting systems within our mine premises.
Moreover, we actively use Condition-Based Monitoring (CBM) to ensure that our equipment operates efficiently and with minimal environmental impact. This involves regular fuel consumption analysis, CO emission checks, and engine calibration to optimise fuel use and extend the life of our machinery. These practices help reduce emissions while ensuring the sustainable operation of our mining activities.
Our efforts to optimise blasting techniques also play a key role in reducing our carbon footprint. We have adopted non-electric true bottom initiation systems and incorporated polymer beads with ammonium nitrate to minimise explosive consumption. These techniques help lower the impact of blasting on the environment by reducing ground vibrations, sound, and dust, further contributing to our goal of sustainable and responsible mining. Through these initiatives, Shree Cement continues to lead by example, demonstrating how the cement industry can successfully balance operational efficiency with environmental stewardship.
Water conservation is critical in mining operations. How is your organisation managing water use in your quarries, and what steps are being taken to ensure sustainable water management in the cement production supply chain?
Water conservation is vital in our mining operations, and we take a comprehensive approach to managing water use throughout the cement production supply chain. Recognising that water is a shared and precious resource, we have developed sustainable solutions to ensure judicious consumption and minimal wastage. Our operations rely on surface water, groundwater, and third-party supplied water, and with several of our integrated and grinding units located in water-stressed areas, we have implemented prudent management plans to mitigate the impact on local water resources.
One of our key initiatives is ensuring that all our manufacturing locations operate as Zero Liquid Discharge (ZLD) facilities, where 100 per cent of wastewater generated is treated, recycled, and reused. This initiative not only reduces water wastage but also supports responsible water usage across our sites. We also regularly conduct training programs for our internal stakeholders, raising awareness about the importance of water conservation and encouraging reduced water consumption across the board.
In terms of specific water usage, our freshwater consumption within cement operations stood at 65.1 litres per tonne of cement production during the current year, a slight increase from the previous year’s 64.8 litres per tonne. We are continuously exploring alternative water sources to further reduce our reliance on freshwater, particularly in our operations in water-stressed areas. One such alternative is the use of municipal sewage treatment plant (STP) treated water at our Beawar and Nawalgarh facilities, and we have established agreements with local municipalities to meet our water needs. In FY 2023-24, STP-treated water supplied 253.4 million litres for our processes, significantly reducing the demand for fresh water.
Additionally, we have undertaken several rainwater harvesting initiatives both within our premises and in nearby villages to enhance water availability. Our limestone mining operations are strategically planned to maximise the collection and storage of rainwater in mine pits. To combat evaporation losses due to rising global temperatures, we’ve introduced a biodegradable chemical called EVALOCK in our mine’s water harvesting pits, which has helped save approximately 30 per cent of water that would otherwise have been lost to evaporation.
As a result of our collective water conservation efforts, we have achieved more than seven times water positivity, harvesting a total of 16,234 million litres of rainwater compared to our freshwater consumption of 2,228 million litres. This ensures that our operations do not impact water availability for local communities, and it strengthens our commitment to sustainable water management. By optimising water usage, treating and recycling wastewater, and expanding rainwater harvesting initiatives, we have made significant progress in safeguarding this critical resource.
How is your company integrating recycled materials or industrial by-products to reduce dependence on natural resources through mining?
At Shree Cement, we recognise the critical importance of reducing our reliance on finite natural resources and have made significant strides in integrating recycled materials and industrial by-products into our cement production processes. In FY 2023-24, 24.41per cent of the total raw materials we used were sourced from alternative materials, including fly ash, granulated blast furnace slag (GBFS), and chemical gypsum, among others, amounting to 11.39 million tonnes. These materials, which are by-products of other industries, play a pivotal role in reducing the extraction pressure on natural resources such as limestone, and help us mitigate the environmental impact of waste disposal.
Our commitment to fostering a circular economy is further highlighted by our innovative use of synthetic gypsum, which we produce through a patented process involving the use of low-grade limestone and spent acid, an industrial waste product. This initiative not only decreases our consumption of natural gypsum but also addresses industrial waste management, leading to cost savings and a more sustainable production cycle.
Furthermore, this practice extends the lifespan of natural resources while promoting waste-to-wealth solutions that have tangible environmental benefits. Despite cement production relying heavily on non-renewable materials, we continuously strive to optimise the use of alternative resources to reduce environmental degradation and build a more sustainable industry. The introduction of synthetic gypsum exemplifies our forward-thinking approach, as it helps reduce our overall carbon footprint and enhances our resource efficiency in the long term.
What role does digitalisation or Industry 4.0 play in improving the efficiency and sustainability of your mining operations for cement production?
Digitalisation and Industry 4.0 technologies have revolutionised the way Shree Cement conducts its mining operations, significantly improving both operational efficiency and sustainability. Our integration of advanced technologies such as artificial intelligence (AI), data analytics, and automation enables us to optimise the extraction of raw materials, minimise waste, and enhance resource utilisation. By utilising cutting-edge mining software like ‘DATAMINE,’ we can conduct highly accurate reserve estimations and daily planning, which allows for precision in resource management, helping us recover the maximum amount of mineral resources while minimising the environmental impact of our operations.
In addition to advanced planning tools, we have implemented the Operator Independent Truck Dispatch System (OITDS), which increases operational efficiency by reducing idle times, improving fuel consumption, and maximising the utilisation of our fleet. This level of automation helps reduce greenhouse gas emissions by optimising the performance of our vehicles and machinery. Real-time monitoring of limestone quality through cross-belt analysers ensures that we are using our resources efficiently, reducing wastage, and maintaining consistent feed quality during cement production.
The use of these digital tools not only streamlines our operational processes but also enables us to make data-driven decisions that enhance our environmental stewardship. By integrating these Industry 4.0 technologies, Shree Cement ensures that its mining operations align with both efficiency and sustainability goals, contributing to a significant reduction in our overall carbon footprint. As we continue to embrace digital transformation, we are committed to leveraging these innovations to drive sustainability across the entire value chain of our cement production process.
Looking ahead, how does your organisation plan to further innovate and improve mining practices to align with the future goals of achieving net-zero emissions in cement production.
Our commitment towards national goals and SDGs drives us to continuously innovate and improve our mining practices. Our strategy involves enhancing resource management and optimising the use of alternative materials. Currently, we have successfully integrated 24.41per cent alternative raw materials into our production process, which allows us to decrease our dependence on conventional resources.
In addition to incorporating alternative materials, we are focused on implementing energy-efficient technologies across our operations. This includes ongoing initiatives to optimise diesel consumption in our mining equipment, which is crucial for reducing our overall carbon footprint. One exciting avenue we are exploring is the use of bio-diesel in our mining machinery. By adopting bio-diesel, we can minimise our reliance on fossil fuels and significantly
lower greenhouse gas emissions associated with our operations.
Moreover, we are committed to continuous improvement and innovation. We actively seek out new technologies and methodologies that can enhance the efficiency of our mining practices while reducing environmental impacts. This comprehensive approach ensures that we are not only meeting our immediate sustainability goals but also paving the way for a greener, more responsible future in the cement industry. Through these efforts, we are dedicated to leading the way toward sustainable mining practices in line with our environmental commitments.
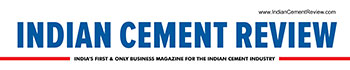
Concrete
Cement industry to gain from new infrastructure spending
Published
1 week agoon
July 24, 2025By
admin
As per a news report, Karan Adani, ACC Chair, has said that he expects the cement industry to benefit from the an anticipated US$2.2tn in new public infrastructure spending between 2025 and 2030. In a statement he said that ACC has crossed the 100Mt/yr cement capacity milestone in April 2025, propelling the company to get closer to its ambitious 140Mt/yr target by the 2028 financial year. The company’s capacity corresponds to 15 per cent of an all-India installed capacity of 686Mt/yr.
Image source:https://cementplantsupplier.com/cement-manufacturing/emerging-trends-in-cement-manufacturing-technology/

The American Cement Association projects a nearly 1Mt annual increase in US cement demand over the next three years, driven by the surge in AI data centres. Consumption by data centres is expected to grow from 247,000 tonnes in 2025 to 860,000 tonnes by 2027. With over 5,400 AI data centres currently operating and numbers forecast to exceed 6,000 by 2027, the association cautions that regulatory hurdles and labour shortages may impact the industry’s ability to meet demand.
Image source:https://img-s-msn-com.akamaized.net/tenant/amp/entityid/AA1zOrih.img?w=2000&h=1362&m=4&q=79

GoldCrest Cement will build a greenfield integrated plant with a 3.5Mt/yr clinker capacity and 4.5Mt/yr cement capacity. GoldCrest Cement appointed Humboldt Wedag India as engineering, procurement and construction contractor in March 2025 and targets completion by March 2027. It has signed a 40-year supply agreement with Gujarat Mineral Development Corporation for 150Mt of limestone from its upcoming Lakhpat Punrajpur mine in Gujarat.