Concrete
Pyroprocessing and Kiln Operation
Published
3 years agoon
By
admin
Dr SB Hegde, Professor, Jain University, Bangalore, talks about pyroprocessing and the role of preheater, rotary kiln and clinker cooler in the cement manufacturing process. In the concluding part of the two-part series, we will learn more about the various factors aiding pyroprocessing.
False Air in Pyro Processing
India is the second largest cement producer in the world in terms of cement capacity. Therefore, it is deciphered that the amount of energy being consumed in cement production process and its wastage attributed to non-availability of proper technology to plug the leakages.
There are several research papers/case studies discussing the effect of different factors on energy consumption in cement manufacturing and are well documented. There are some studies that discuss this issue with the help of mathematical models. However, all studies reveal the fact that the ‘false air’ may be one of the factors for higher energy consumption in cement plants. Further, based on the several studies in the field of operational audit, it can be concluded that production level can be improved and energy consumption reduced by reduction of ‘false air’.
False air is any unwanted air entering into the process system. The exact amount of false air is difficult to measure. However, an indicator of false air can be increase of per cent of oxygen between two points (usable for gas streams containing less than 21 per cent of oxygen). Due to unwanted air, the power consumption increases and the system’s temperature decreases. Therefore, to maintain the same temperature fuel consumption has to be increased.

Impact of False Air in a Cement Plant
• Increase of power consumption
• Increase the fuel consumption
• Unstable operation
• Reduction in productivity
• Higher wear of fans
False Air Ingress Points
In cement plants, generally false air intrudes in the kiln section through the kiln outlet, inlet seal, TAD slide gate, inspection doors and flap box. Similarly, in mill section false air intrudes through rotary feeder at mill inlet, mill body, mill door, flaps, expansion joints, holes of ducts and tie rod entry point. In the power sector, as margin is very less, cost- effectiveness plays an important role. Generally false air intrudes in the CPP section through air pre-heater casing, boiler main door, fan casing, inspection doors, ESP main doors, ESP hopper doors, expansion bellows and ducts. Similarly, in the GPP section false air intrudes through main holes, hammering, bellows, rotary air locks, damper casing, expansion bellow, etc.

Checking of Heat balance
Heat balance on a kiln can offer extremely useful information on the thermal performance of the system. Heat balance shows where or how the fuel heat is consumed based on the simple principle of input = output.
Unnecessary energy losses can be easily detected, the principle of heat balance may be easily transferred to another system such as preheater, cooler and drying system. Various reasons or circumstances may cause a need for a heat balance measurement. The following situations may justify a heat balance:
- Performance test,
- Recoding of kiln performance before/after a modification,
- Unusually high heat consumption or abnormal kiln operational data,
- Kiln optimisation endeavours.
Although the specific heat consumption proper could also be determined by measuring nothing but fuel heat and clinker production, a complete heat balance does offer considerably more information and security.
The consistency of the measured data is proved much better, and the balance shows clearly where the heat is consumed. A heat balance is obviously a very efficient tool assessment of thermal efficiency. A heat balance does not only mean calculation of heat balance items.
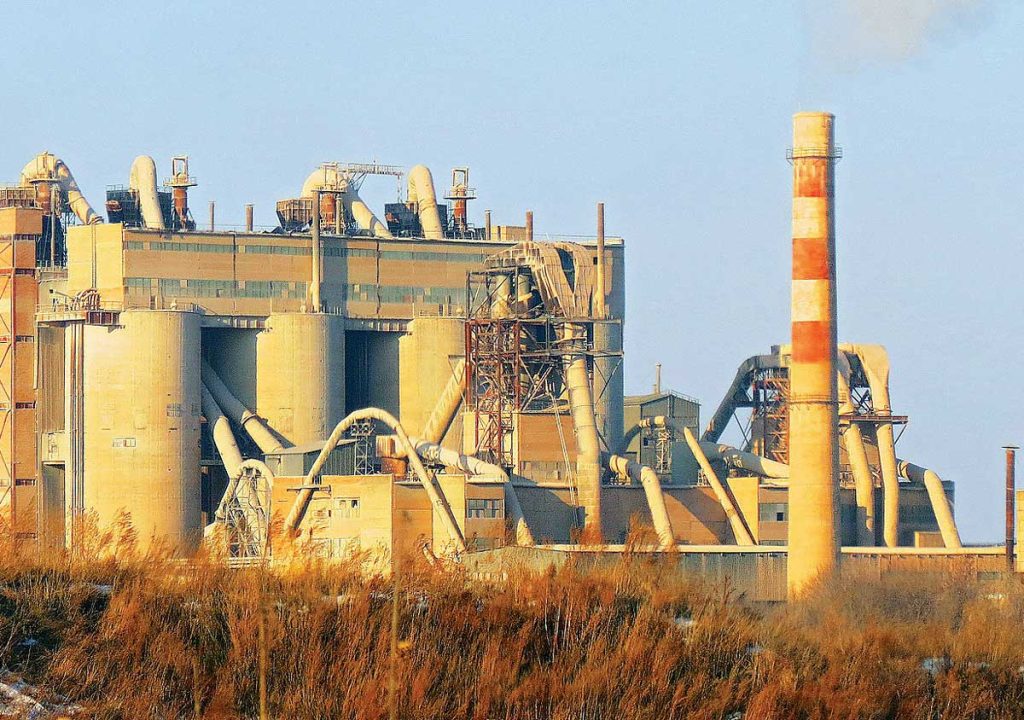
Kiln Operation Problems Using Pet Coke
- The consequence of using pet coke is dusty conditions and a kiln inlet ring. Even though there is no CO (carbon monoxide) in the kiln inlet, the large amount of SO3 introduced by the pet coke may not be properly balanced by alkalis (Na2O and K2O) in the kiln feed. This will result in a high SO3 re-circulation and a reduction of the liquid phase surface tension and viscosity. This will produce poor clinker nodulation and a corresponding increase in the dust load in the kiln and rings near the kiln inlet.
- The possible solutions are:
- Ensure that the high SO3 input is balanced with the appropriate percentage of alkalis.
- Optimise the burnability of the raw meal in order to reduce the burning zone temperature.
- Optimise the flame shape to reduce the length of the burning zone.
- Increase the O2 at the kiln inlet even more to ensure enough oxygen is present to remove the increased amount of alkali sulphates from the kiln.
If chloride levels are high in the raw materials this can react preferentially with the alkalis in the bottom cyclones, reducing the percentage of alkalis available to remove SO3 from the kiln. In this case the only practical solution is to try and reduce the chloride input.
Pet coke sometimes needs more O2 at the kiln inlet than required. It is common in some plants to have to run with 6-8 per cent O2 at the kiln inlet to keep SO3 recirculation down to an acceptable level. Remember that just having a small excess of O2 in the kiln inlet (sufficient to ensure zero CO) may not be enough to control the high sulphur input from pet coke.
2K2O + 2SO2 + O2 = 2K2SO4
2CaO + 2SO2 +O2 = 2CaSO4
The molecular weight s is
2SO2 = 128
O2 = 32
Therefore, every 4 tonne of SO2 needs 1 tonne of O2 to be converted to SO4-2, no matter if there are sufficient alkalis or not. Calculate the percent of O2 required at the kiln inlet from the total input of SO2 from pet coke and the gas flow rate at the kiln inlet.
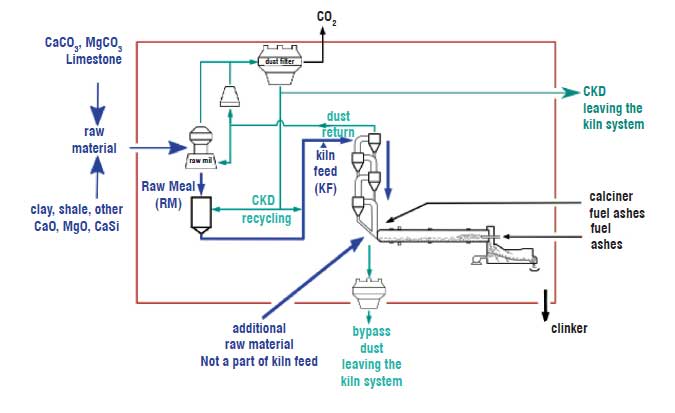
Burning softer (i.e., lower litre weight) is a good idea because it uses less fuel and lowers the sulphur input. Softer burning will reduce the sulphur volatilisation in the burning zone (ensuring oxidising conditions in the burning zone is critical since CaSO4 is more susceptible to thermal decomposition under slightly reducing conditions than alkali sulphates.).
Traditionally it is known that an excess SO3 content of some 300-700 gm per 100 kg clinker can be tolerated in the kiln system. Lower limit will be valid for hard to burn raw materials while the upper one refers to easy burnable raw meals. Apart from adjustment of the sulphur/alkali ratio it is possible by operational means to substantially reduce the sulphur evaporation in the burning zone. One can consume 1000 gm SO3 per 100 kg clinker by the following changes in burning operation.
- High Oxygen – levels in the kiln (around 5 per cent O2)
- High Flame Momentum
- Short residence time in the burning zone
- Improve chemical burnability
- Finer grinding of raw mix and pet coke
Significance of Liquid Content in Clinker
Liquid content of clinker is the fraction of the kiln feed that melts between the upper transition and burning zone. The liquid content has a critical role in clinker nodulisation and clinker phase development and properties. In the absence of liquid, the conversion of C2S and free lime to C3S would be almost impossible in the kiln.
Plant chemists and CCR operators are usually more concerned with the amount of liquid rather than with the rheological properties of the liquid. The latter is more important during clinkering reactions than the former.
Amount of liquid Content
The raw mix consists of only 4 oxides, i.e., CaO, SiO2, Al2O3 and Fe2O3, it would start melting at 1,338 degree C, the so-called eutectic temperature for the system C-S-A-F.
Industrial raw mixes contain impurities such as MgO, Na2O, K2O and SO3. At certain concentrations, these impurities reduce the eutectic temperature of the system to 1,280 degree C, thus promoting clinker formation. These oxides act as fluxes in the kiln, forming liquid as far up in the calcining zone.
Liquid percentage at 1,450 C=3XA+2.25XF+MgO+K2O+Na2O+SO3 (MgO<2).
For most commercial clinkers, the amount of liquid content is in the range of 26-29.5 per cent. Higher values can be damaging to most refractory bricks in the absence of stable coating. As the brick is infiltrated and saturated with liquid, its elastic modulus increases and so does its tendency to spall off.
The tendency to coating formation or the coataibility of clinker increases with the amount of liquid. However, more coating does not necessarily mean better coating. Coating refractoriness, texture and stability are by far more important than the amount of coating deposited on the lining.
Significance of liquid content
The most important clinker phase is C3S (alite) which requires the presence of liquid for its formation. In the absence of liquid, alite formation is extremely slow and it would render clinkering impossible. This fact also explains why alite is formed essentially in the burning zone, where the amount of liquid is at a maximum.
To understand why alite formation requires
liquid content, one must first understand the alite formation mechanism:
- C2S and free CaO dissolves in the clinker melt.
- Calcium ions migrate towards C2S through chemical diffusion
- C3S is formed and crystallised out of the liquid.
Without liquid phase the diffusion of Ca ions towards C2S would be extremely slow, and that of C2S almost impossible at clinkering temperature. It is important to mention that Na2O and K2O decrease the mobility of Ca ions, whereas MgO and sulphates considerably increase it. That is why addition of gypsum in the raw mix promotes alite formation.
Properties of liquid phase Viscosity
Temperature has the most pronounced effect on liquid phase viscosity. Low viscosity liquid infiltrates the refractory lining faster, leading to its premature failure. MgO, alkali sulphates, fluorides and chlorides also reduce liquid phase viscosity.
Free alkali and phosphorous increase liquid phase viscosity, but this effect is offset by MgO and SO3. Only clinkers with S/A ratio lower than 0.83, low in MgO, would experience the negative effects of high liquid viscosity.
The liquid content viscosity increases linearly with A/F ratio. For a given burning temperature, high C3A clinkers tend to nodulise better than low C3A clinkers. Moreover, the liquid phase is considerably less damaging to the refractory lining when the liquid is viscous.
Another important property of the liquid phase is its surface tension, or its ability to ‘wet’ the lining. The surface tension has a direct impact on clinker fineness, coating adherence to the lining and clinker quality.
High surface tension values would favour nodule formation and liquid penetration through pores of the nodules. The resulting clinker contains less dust (fraction below 5 or 10 mm) and lower free lime content. A liquid phase with high surface tension has less tendency to adhere to the brick surface, therefore, reducing clinker coatibility or adherence to the lining.
Alkali, MgO and SO3 reduce liquid surface tension. So does temperature. Sulphur and potassium have the strongest effects, followed by sodium and magnesium. Therefore, MgO, SO3 and K2O to a certain concentration, are good coating promoters.
Unfortunately, the liquid properties that induce C3S formation are detrimental to the refractory lining and to clinker nodulisation.
Although the amount of liquid phase in the burning zones of the kiln is important to clinker formation and brick performance, the rheological properties of the melt are even more important. The rheological properties of the clinker melt control parameters such as clinker mineral formation, clinker coatability, clinker fineness, cement strength and refractory depth of infiltration.
It is then very important to keep fuel, raw material properties and flame temperature as steady as possible. Whenever introducing drastic changes in the raw material or fuel properties, the refractory lining must be changed accordingly to meet the differences in clinker coatability and burnability.
Material Balance of a Pyro Processing in Clinker Production
The following diagram illustrates an example of the mass flows in a cement plant and the mass balance of a kiln system from raw meal (RM) to clinker.
Figure 1: Schematic diagram of material and dust flows in a cement plant
The reporting of CO2 emissions from the calcination of raw materials depends on the principle choice of the method for determining the mass balance: from the input side (raw meal consumption).
Accordingly, we need to consider the reporting of the mass flows bypass dust, cement
kiln dust leaving the kiln system (and crossing the red boundary in the diagram) and additional raw materials), which are not part of the normal kiln feed, as follows:
Simple input method and detailed input method: The actual amount of raw meal consumed for clinker production can be determined by weighing the kiln feed and subtracting the dust return.
- Bypass dust leaving the kiln system is accounted for in the amount of raw meal consumed. Additional calculations may be required if the bypass dust is only partially calcined. This is implemented only in the detailed input method:
- CKD recycling remains within the mass balance and therefore does not need additional reporting.
- CKD leaving the kiln system (and crossing the red boundary in the diagram) needs to be quantified and requires additional reporting in the input methods.
- Additional raw materials (ARM), which are not part of the kiln feed are not accounted for by the amount of raw meal consumed. Thus, they require additional reporting in the input methods. However, the necessary calculations are only implemented in the detailed input method. The simple input method (A1) should therefore not be used if ARM is relevant for the complete reporting of the CO2 emissions.
Simple output method and detailed output method: The amount of clinker production can be determined from calculating the clinker mass balance or by direct weighing.
- Bypass dust leaving the kiln system requires separate reporting:
- CKD recycling remains within the mass balance. Thus, it does not need additional reporting.
- The mass flow of CKD leaving the kiln system (and crossing the red boundary in the diagram) needs to be accounted for additionally.
- Additional raw materials (ARM) do not need to be accounted for additionally in the output methods, which are based on the clinker production.
Conclusions
Pyro-processing in a cement plant comprises a preheater, rotary kiln and clinker cooler. Pyro-processing section is considered to be the heart of a cement plant as actual cement clinker production takes place in kilns.
The size of a cement plant is determined based on the pyro-processing section and the sizes of all other equipment are determined to match pyro-processing. Cyclones are basic units in a preheater system. Pressure drop and change of temperature of gas across each stage determines the efficiency of cyclones.
Introduction of Low Pressure drop (LP) cyclones has brought the pressure drop across each stage to around 50 mm WG from around 150 mm WG in conventional cyclones. This has resulted in more and more plants adopting 5 or 6 stages of preheater.
A typical 6 stage preheater with LP cyclones will have a preheater exhaust gas temperature of around 250°C and draught of around 500 mm WG. This in turn led to decrease in preheater fan
power consumption.
The reduced temperatures at preheater exhaust contribute to environmental improvement. Cyclone separators are used in preheaters on cement plants to separate the raw material for gases. Very tall preheater means more power is required to operate the plant.
It is always desired for a minimum preheater height to operate the plant economically. Due to the preheater arrangement and layout design, cyclones decide the height of the preheater. Pressure drop-in cyclones plays an important role in determining the cost of operation of a cyclone separator. High pressure drop means more power required to operate the cyclone.
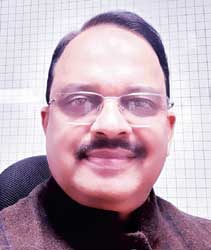
ABOUT THE AUTHOR
Dr SB Hegde is currently a Professor at Jain University, Bangalore, Karnataka, and a Visiting Professor at Pennsylvania State University, United States of America. He has more than 30 years of experience in cement manufacturing both in India and abroad. He has occupied the ‘Leadership positions’ in reputed major cement companies both in India and overseas. He is also a recipient of ‘Global Visionary Award’ instituted by Gujarat Chambers of Commerce and Industry, Ahmedabad in 2020.
Concrete
Cement industry to gain from new infrastructure spending
Published
1 week agoon
July 24, 2025By
admin
As per a news report, Karan Adani, ACC Chair, has said that he expects the cement industry to benefit from the an anticipated US$2.2tn in new public infrastructure spending between 2025 and 2030. In a statement he said that ACC has crossed the 100Mt/yr cement capacity milestone in April 2025, propelling the company to get closer to its ambitious 140Mt/yr target by the 2028 financial year. The company’s capacity corresponds to 15 per cent of an all-India installed capacity of 686Mt/yr.
Image source:https://cementplantsupplier.com/cement-manufacturing/emerging-trends-in-cement-manufacturing-technology/

The American Cement Association projects a nearly 1Mt annual increase in US cement demand over the next three years, driven by the surge in AI data centres. Consumption by data centres is expected to grow from 247,000 tonnes in 2025 to 860,000 tonnes by 2027. With over 5,400 AI data centres currently operating and numbers forecast to exceed 6,000 by 2027, the association cautions that regulatory hurdles and labour shortages may impact the industry’s ability to meet demand.
Image source:https://img-s-msn-com.akamaized.net/tenant/amp/entityid/AA1zOrih.img?w=2000&h=1362&m=4&q=79

GoldCrest Cement will build a greenfield integrated plant with a 3.5Mt/yr clinker capacity and 4.5Mt/yr cement capacity. GoldCrest Cement appointed Humboldt Wedag India as engineering, procurement and construction contractor in March 2025 and targets completion by March 2027. It has signed a 40-year supply agreement with Gujarat Mineral Development Corporation for 150Mt of limestone from its upcoming Lakhpat Punrajpur mine in Gujarat.