Technology
It’s not just about the bag!
Published
8 years agoon
By
admin
A correctly selected air pollution control system will not only control air emissions successfully, but also contribute to the cement plant’s overall efficiency.
It is a fact that emission limits in the cement industry have become and will continue to get more stringent. Although there are some differences, depending on which part of the world one looks at, the limits are undoubtedly heading downwards. A direct implication of this is that the dust control activities of cement manufacturers will have to be improved globally.
In cement plants across the world, cyclones, electrostatic precipitators (ESPs), and baghouses, either alone or in combination, are widely used dust control technologies, each with their own benefits. The well-known and established ESP technology is capable of handling dust emission limits of 5- 10 mg/Nm3.
ESPs in the cement industry can be operated up to a service temperature of around 450?C, so there is no cooling of the gas needed for kiln exit gases and those of the clinker cooler. In the case of bypass filters, depending on the kiln exit temperature, cooling of the gases with air or water may be required. One of the most compelling arguments for an ESP installation is that ESPs are very easy to operate.
Moreover, maintenance is relatively simple and the cost reasonable, due to fewer components involved as compared to a baghouse, for example. On the other hand, the space requirements for an ESP filter are huge and, if one wants to lower the dust emissions even further, the filter becomes very large, and the consumption of electricity very extensive. The extension of an ESP to meet new emission limits could imply higher fixed costs and increased operating costs.
In most cases, the option of expanding the ESP filter is not available, as space is often the limiting factor in existing facilities. However, depending on the desired lower emission targets, ESP technology may not even be able to reach those new levels.
Other options
Time and again, changes in regulations and lower emission limits have forced the cement industry to look for other solutions. Lower emissions, in the range of about 3-5 mg/Nm3, can be achieved with baghouses, which also have a much smaller footprint than ESPs. No wonder that one of the industry’s responses to the challenge was the conversion of an existing ESP installation, either in full or in part, into a baghouse with a fabric filter. This type of filter conversion has become common practice in the cement industry, and with new limits in place, many more retrofits are expected worldwide in the coming years. However, the right implementation is crucial to reaping the benefits of such a retrofit. Some of the problems encountered can be traced back to fundamental differences between the two technologies. Two of these basic differences are the direction of flow of the flue gases and the operating temperature. An ESP filter requires a horizontal flow of the flue gases going through the collecting plates. In a baghouse, the flue gases go through the vertically hanging bags.
Therefore, in a baghouse filter, the gas flow should be vertical. An ESP installation can be operated at approximately 450?C, whereas in the case of a baghouse, the temperature is limited by the kind of filter media used. Maximum continuous operating temperatures for fabric filters are 250-260?C; cooling of the flue gases is therefore required. The actual filter media may be a fabric cloth made of either a needle felt or a woven fibre glass. Both fabrics could be equipped with an expanded polytetrafluorethylene (ePTFE) membrane material. Due to the very small pore size of the membrane (1 – 2 ?m), lower emission rates of about 3-5 mg/Nm3 can be achieved.
The crystallite melting point of PTFE material is 327?C and a potential active continuous service temperature of 288?C seems possible. However, practical continuous filtration operating tempe-ratures are between a maximum of 250-260?C. In order to protect the fabric filtration media, valuable heat energy has to be wasted due to the cooling of the flue gas. In many cases, where cooling is done by air, about 30-50 per cent of the air going through a fabric filter baghouse is the air required for cooling the flue gas to a desired temperature.
Cooling of flue gas can be avoided, if the filter medium can withstand higher temperatures, presenting a number of opportunities:
The volume of air can be reduced, which saves electricity costs on the fan motor. Increased production capacity may become possible without having to scale up the ID fan capacity. The clean gases are higher in temperature and therefore do not need to be heated for potential SCR NOx reduction treatment. This will save on fuel consumption and therefore on cost.
The thermal energy from the clean hot gases can be reused as thermal energy for drying raw material or coal. Those clean hot gases could also be used to generate electricity.
The use of latest state-of-the-art high efficiency pollution control equipment like ESPs and bag filters has made it possible for the cement industry to be well within the particulate emission norms. The recently prescribed norms for PM, SO2 and NOx are at par with the stringent EU norms. However, Indian cement plants need adequate time to implement measures in order to comply with the norms (particularly with SO2 and NOX) in a gradual phased manner, given the fact that there is a need for availability of good quality coal, ammonia, equipment design modifications and concerns on health hazards associated with use of ammonia in NOx reduction technologies.
Emission Monitoring
The cement industry has installed Continuous Emission Monitoring Systems (CEMS) in most of the kiln stacks and opacity monitors in most of process stacks. CEMS facilitates tracking of SO2 and NOX emissions in real time on a continuous basis and enhance the accuracy of reporting. It also helps to identify the base line emissions and deviations from expected regu-latory norms with a view to take corrective measures wherever necessary.
Various types of Air Pollution Control Equipments (APCEs) are used in cement plants to control the particulate emission to the atmosphere such as cyclone and multi-cyclones, wets crubbers, ESPs, fabric filters/bag filters or gravel bed filters.
The use of more advanced technologies, such as pulse jet bag houses, has been extended in manufacturing units of cement industry. The methods employed for fugitive dust control in cement industry includes water spray system, green cover, tree plantation, exhaust ventilation system and proper house-keeping. Filter bags are a critical component in assuring that the fabric filter will be able to meet environmental regulations and plant process demand. Though filter bags are usually the first place plant personnel look when problems occur, there are other areas to consider. The bag house equipment design, such as how the bags are cleaned and how the dust is removed from the bags are equally important.
The maintenance practices such as filter bag installation, start-up and shutdown procedures are important to attain optimal performance. One of the biggest issues that cement plants face with fabric filters is the ability to distribute gas equally to all of the compartments without causing high velocity problems, which can quickly cause filter bags to break.
Expert knowledge
To ensure the fabric filter meets operational goals and complies with environmental regulations, it needs the support of associated services, inclu-ding qualified technical support, filter training, lab testing, spare parts, make and hold agreements, and ongoing customer service. This requires an experienced solution provider who has both operational know-how and technological manufac-turing competencies. Filter bag engineers should be able to evaluate all process conditions, including gas temperature, air flow, volume, and more.
Here, FLSmidth Airtech has engineered the best design to meet these challenges head on by utilising an exclusive design of gas distribution screens and side inlet that reduces velocity and allows dust to pass directly into the hopper. This contributes directly towards longer filter bag life.
The feature of equalised and low velocity gas streams provides extremely important benefits for the cement plant such as cost reductions in the compressed air energy used for filter bag cleaning.
The kiln
Fiberglass is the most common media for filter bags in kiln filters for good reason. Its temperature resistance of up to 260?C (500?F) can withstand the hot gases of the kiln, providing flexibility to plant operations as higher temperature ratings allow for improved throughput and production.
However, fiberglass bags are relatively fragile and must be handled very carefully, especially during installation. Consequently, it is recom-mended that installation of fiberglass bags is left to experienced, qualified personnel.
A potential drawback of fiberglass bags is their relative inability to withstand ‘overpulsing’ or excessive cleaning. Here, efficient and careful cleaning of the bags is an important factor in preventing failure. An excessive amount of cleaning pulses will often lead to premature failure, so it is necessary to find the optimal frequency to ensure the longest possible service. Qualified fabric filter technicians can provide best-practice recommendations.
Clinker cooler
The typical media for clinker cooler filters is aramid. This sets a maximum temperature limit of 204?C (400?F) and a constant of 190?C (375?F) since above this, aramid bags will fail. Bag failures can lead to unnecessary stoppages of the clinker cooler, because the defective bags need to be located and exchanged. A particularly useful device is a broken bag detector that can alert the plant operators in the event of a broken bag as well as pinpoint the location.
This minimises production loss and provides better conditions for finding and replacing the bags efficiently and safely. In addition, if fabric filter performance is not cost effective, several filter media upgrades are available.
Finish mill
In finish mill filters, polyester is one of the most widely used media because of its high availability and low cost. However, hydrolysis is a common problem for this process. Polyester becomes brittle when exposed to moisture and temperatures around dew point, approximately 100?C (215?F). A better option is an acrylic filter bag because it operates well in high moisture applications. Other benefits of acrylic filter media are good resistance to moist mineral and most acids as well as an excellent resistance to organic solvents.
Coal mill
Typical filter media for coal mill dust collectors include polyester, acrylic and aramid. With a stainless steel scrim, these new and improved media replace the traditional, blended fabric with carbon fibres, also known as epitropic filters. The conductive scrims dissipate static consistently throughout the filter bag at a lower cost. Static electricity in the coal mill filter could ignite coal dust and cause a fire or explosion. Safety measures preventing static electricity discharge therefore need to be in place to reduce the potential for explosions and fires. These measures include using stainless steel or copper grounding wires sewn to the filter bag or semiconductor filter bags.
Secondary dedusting
It is not uncommon to see undersised dust collectors in applications such as silos, pack houses, belt transport and conveying systems. High differential pressure issues in these units, designed for a specific grain loading, are usually caused by system overloading as production expands. The issue can be solved by retrofitting the design, increasing the size of the collector or using a pleated filter bag design instead. This last option can be the most cost effective because the same housing and other components are used.
Filter monitoring
Although particulate monitoring systems are generally purchased to monitor environmental emissions, many users also utilise these instruments as preventative maintenance tools. The ability to predict when a filter is likely to fail and to be able to identify which row or chamber is at fault has provided users with a proven method to not only reduce the environmental impact and clean-up costs associated with large-scale emission events but also to make significant savings in spares, maintenance times and lost production.
To achieve this, the selected monitoring technique must be able to accurately track the very dynamic dust emissions created during a bag filter cleaning cycle. To these ends UK-based PCME recommends Electrodynamic units in preference to Optical or Triboelectric systems.
As a filter is reverse jet cleaned, any defects in the filter membranes are exposed resulting in relatively high dust peaks. By monitoring these peaks in real time using the Predict software package, it is possible to identify potential problems within the filter before they result in breaches of environmental limits.
The cleaning signature of the bag house is made easily identifiable by the input to the monitor of the filters cleaning pulses via Auxiliary Input Modules. Additionally further outputs maybe taken from pressure sensors within the bag house to assess the caking of the filter elements, thereby allowing the operator to reduce bag wear and compressed air usage and allowing the optimisation of the filter system.
Predict provides the possibility to observe filter problems remotely and check maintenance work to ensure correct performance of the filter. The use of Predict has proven the ability of a monitor not only to be used for environmental compliance but also to be used as a significant aid to plant maintenance and to also enable users to greatly reduce the instances of catastrophic filter failure.
These two complimentary monitoring tech-niques are used as they offer the best monitoring solutions in the widely different conditions found in these two locations. Electrodynamic sensors have a proven capability to monitor the extremely high dust loads found Pre-filter, providing a reliable, rugged monitoring solution whereas Optical sensors are chosen for chosen for use.
Post filter as a result of their capability to measure extremely low dust levels (0.1 mg/m3 utilising pro-scatter techniques) and their low maintenance requirements. The ability to observe in real time the perfor-mance of the filter allows the operator to adjust operating parameters to optimise not only filter efficiency, but also reduce operating costs, extend the filters operating life and decrease the environmental impact of the process.
Economy & Market
Hindalco Buys US Speciality Alumina Firm for $125 Million
Published
2 months agoon
June 25, 2025By
admin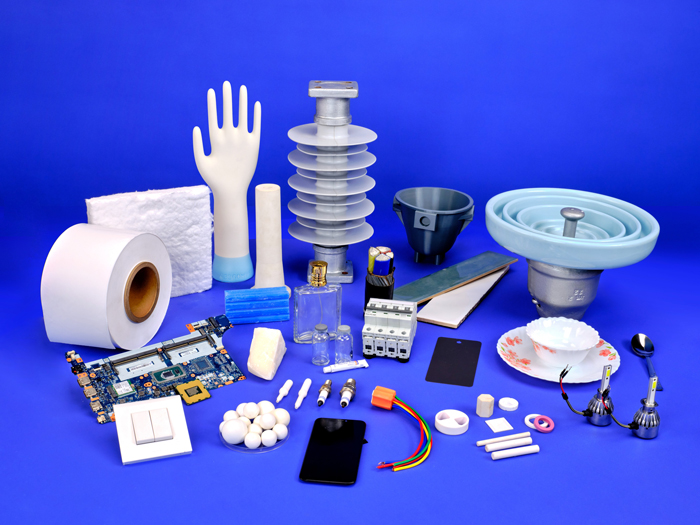
This strategic acquisition marks a significant investment in speciality alumina, a key step by Aditya Birla Group’s metals flagship towards becoming future-ready by scaling its high-value, technology-led materials portfolio.
Hindalco Industries, the world’s largest aluminium company by revenue and the metals flagship of the $28 billion Aditya Birla Group, has announced the acquisition of a 100 per cent equity stake in US-based AluChem Companies—a prominent manufacturer of speciality alumina—for an enterprise value of $125 million. The transaction will be executed through Aditya Holdings, a wholly owned subsidiary.
This acquisition represents a pivotal investment in speciality alumina and advances Hindalco’s strategy to expand its high-value, technology-led materials portfolio.
Hindalco’s speciality alumina business, a key pillar of its value-added strategy, has delivered consistent double-digit growth in recent years. It has emerged as a high-growth, high-margin vertical within the company’s portfolio. As speciality alumina finds expanding applications across electric mobility, semiconductors, and precision ceramics, the deal positions Hindalco further up the innovation curve, enabling next-generation alumina solutions and value-accretive growth.
Kumar Mangalam Birla, Chairman of Aditya Birla Group, called the acquisition an important step in their global strategy to build a leadership position in value-added, high-tech materials.
“Our strategic foray into the speciality alumina space will not only accelerate the development of future-ready, sustainable solutions but also open new pathways to pursue high-impact growth opportunities. By integrating advanced technologies into our value chain, we are reinforcing our commitment to self-reliance, import substitution, and building scale in innovation-led businesses.”
Ronald P Zapletal, Founder, AluChem Companies, said the partnership with Hindalco would provide AluChem the ability and capital to scale up faster and build scale in North America.
“AluChem will benefit from their world-class sustainability and safety standards and practices, access to integrated operations and a consistent, reliable raw material supply chain. Their ability to leverage R&D capabilities and a talented workforce adds tremendous value to our innovation pipeline, helping drive market expansion beyond North America.”
An Eye on the Future
The global speciality alumina market is projected to grow significantly, with rising demand for tailored solutions in sectors such as ceramics, electronics, aerospace, and medical applications. Hindalco currently operates 500,000 tonnes of speciality alumina capacity and aims to scale this up to 1 million tonnes by FY2030.
Commenting on the development, Satish Pai, Managing Director, Hindalco Industries, said the deal reinforced their commitment to innovation and global expansion.
“As alumina gains increasing relevance in critical and clean-tech sectors, AluChem’s advanced chemistry capabilities will significantly enhance our ability to serve these fast-evolving markets. Importantly, it deepens our high-value-added portfolio with differentiated products that drive profitability and strengthen our global competitiveness.”
AluChem adds a strong North American presence to Hindalco’s portfolio, with an annual capacity of 60,000 tonnes across three advanced manufacturing facilities in Ohio and Arkansas. The company is a long-standing supplier of ultra-low soda calcined and tabular alumina, materials prized for their thermal and mechanical stability and widely used in precision engineering and high-performance refractories.
Saurabh Khedekar, CEO of the Alumina Business at Hindalco Industries, said the acquisition unlocked immediate synergies, including market access and portfolio diversification.
“Hindalco plans to work with AluChem’s high performance technology solutions and scale up production of ultra-low soda alumina products to drive a larger global market share.”
The transaction is expected to close in the upcoming quarter, subject to customary closing conditions and regulatory approvals.

As India’s cement industry heads for unprecedented growth, the importance of smart, sustainable and strategic lubrication is gaining ground. From reducing downtime and enhancing energy efficiency to enabling predictive maintenance, lubricants are transforming plant performance. ICR explores how advanced lubrication solutions are becoming critical enablers of reliability, resilience and environmental stewardship in the cement sector.
The Indian cement industry, a cornerstone of the nation’s infrastructure development, is experiencing significant growth. In 2023, India’s cement production reached 374.55 million tonnes, marking a 6.83 per cent year-on-year growth. Projections indicate that the market size will expand from 3.96 billion tonnes in 2023 to 5.99 billion tonnes by 2032, reflecting a compound annual growth rate (CAGR) of 4.7 per cent during 2024-32. This expansion underscores the increasing demand for efficient and sustainable operations within the sector.
In cement manufacturing, equipment such as kilns, crushers, vertical mills, ball mills, conveyors and fans operate under extreme temperatures, heavy loads and high dust exposure. These demanding conditions make proper lubrication not just essential, but mission-critical. Selecting the right type of lubricant and maintaining an effective lubrication regime can drastically improve machine uptime, reduce maintenance costs, and enhance plant safety. In many cases, lubricant-related failures account for a significant proportion of unplanned downtime, underscoring the value of a well-structured lubrication strategy.
The Indian cement sector is also undergoing a technological transformation, with increasing emphasis on automation, predictive maintenance and energy efficiency. In this evolving landscape, lubricants are no longer just consumables—they are enablers of performance, longevity and sustainability. With the growing availability of advanced lubricants and condition-monitoring technologies, Indian cement plants have the opportunity to optimise their lubrication practices in line with global standards. Additionally, tightening environmental regulations and sustainability goals are driving the shift toward eco-friendly lubricants and responsible usage practices, making lubrication management a key factor in both operational and environmental performance.
As the industry moves forward, there is a growing realisation that lubrication excellence can be a competitive differentiator. This article explores the critical role of lubricants in cement manufacturing, the latest technological advancements, the environmental considerations shaping lubricant use, and the challenges and opportunities for cement producers in India aiming to maximise equipment reliability and operational efficiency.
The role of lubricants in cement manufacturing
Cement manufacturing involves heavy-duty machinery operating under extreme conditions—high temperatures, heavy loads and continuous operations. Lubricants are essential in minimising friction, reducing wear and tear, and preventing equipment failures. Proper lubrication ensures that components such as kilns, crushers and grinding mills function optimally, thereby reducing downtime and maintenance costs.
Moreover, the integration of advanced lubrication technologies has enabled predictive maintenance strategies. By monitoring lubricant conditions, operators can anticipate equipment issues before they escalate, allowing for timely interventions and uninterrupted production cycles.
“Lubricants play a crucial role in enhancing the efficiency and reliability of cement plant operations. High-performance lubricants reduce friction and wear in critical machinery such as crushers, kilns, mills, and conveyors, ensuring smoother operation and extending equipment life. By minimising mechanical breakdowns and unplanned downtime, they contribute to consistent production and lower maintenance costs. Additionally, specialised lubricants designed to withstand high temperatures, heavy loads, and dusty environments help maintain optimal performance under demanding conditions. Proper lubrication also improves energy efficiency by reducing power loss due to friction. In essence, the right lubrication strategy not only enhances equipment reliability and operational uptime but also supports overall cost-effectiveness and productivity in cement manufacturing,” says Hiten Ved, Sales Head, Royal Petro Specialities.
In addition to enhancing equipment longevity, lubricants are pivotal in ensuring uninterrupted production cycles. Cement manufacturing is a 24/7 operation, and any unexpected downtime due to mechanical failure can lead to significant financial losses. Lubricants with high thermal stability and oxidation resistance prevent the breakdown of oil films under intense heat, especially in applications like rotary kilns, vertical roller mills and clinker coolers. By reducing the likelihood of equipment seizures or breakdowns, these lubricants act as silent enablers of plant reliability and uptime.
Gaurav Mathur, Director and Chief Executive Officer, Global Technical Services, says, “Wall paintings in tombs show workers using water to move statues, indicating early recognition of lubrication. By 1400 BC, animal fat was used to lubricate chariot axles, ever since then mankind has been relentlessly working to improvise the efficiency of lubricants. Tribological advancements have propelled industrialisation in the world. Machines working in demanding environment need better performance, however merely just better lubricant that is made from highly refined base oils is not good enough. Mineral and synthetic base oils and advanced additives chemistry have given birth to advanced lubricants. These lubricants have better performance characteristics and longer service life.”
“However, the way lubrication is done is more critical and if lubrication is not performed in a proper way, highest performing lubricants would also under perform compared to the lowest specification product. Total Lubrication Management has to be implemented for better machine reliability, equipment availability and lower down time. Implementation of TLM has paid rich dividends in the industry. Pillars of TLM being, contamination free lubrication, regular testing of lubricants to access the lubricant and machine condition and regeneration of lubricants,” he adds.
Lubricants contribute directly to energy efficiency. Friction losses within rotating equipment can account for up to 30 per cent of the total energy consumption in certain plant areas. Advanced synthetic lubricants, with low traction coefficients and superior film strength, reduce this internal resistance, thus improving mechanical efficiency and lowering the plant’s overall energy footprint. As Indian cement plants pursue energy benchmarking and ISO 50001 certifications, the use of high-performance lubricants becomes an integral strategy in achieving energy conservation goals.
“The cement industry has many lubrication points that require NLGI Grade 2 grease that can be used in high temperature applications. These may include bearings on vibrating screens and roller mills; rotating joints on grinding units; and various shafts, pivots, and metal to metal contact points found throughout the plant. CorrLube™ VpCI® Lithium EP Grease has a dropping point of 360 °F (182 °C), allowing it to be used in a broad range of temperatures. For areas that need a slightly harder grease of NLGI Grade 3, EcoLine® Biobased Grease offers a
similar dropping point of 365 °F (185 °C), explain Julie Holmquist, Marketing Content Writer,
Cortec Corporation.
Market dynamics: growth and trends
The Indian industrial lubricants market was valued at $13.05 billion in 2024 and is projected to reach $ 20.72 billion by 2033, growing at a CAGR of 4.12 per cent. This growth is driven by the expanding industrial sector, increased mechanisation, and the adoption of advanced machinery requiring specialised lubricants.
In the cement sector specifically, the demand for high-performance lubricants is rising. The lubricants for cement market are estimated to be $ 2.5 billion in 2024 and is expected to reach $ 3.9 billion by 2033, at a CAGR of 5.3 per cent from 2026 to 2033. This surge is attributed to the need for lubricants that can withstand harsh operating conditions and enhance equipment reliability.
Advancements in lubrication technology
Recent years have witnessed significant advancements in lubrication technology tailored for the cement industry. Synthetic lubricants, known for their superior thermal stability and longer service life, are increasingly being adopted. These lubricants perform effectively under extreme temperatures and heavy loads, common in cement manufacturing processes.
Additionally, the development of bio-based lubricants offers environmentally friendly alternatives without compromising performance. These lubricants, derived from renewable sources, reduce the environmental footprint and align with global sustainability goals. Their biodegradability and low toxicity make them suitable for applications where environmental considerations are paramount.
Smart lubrication systems are another breakthrough in the cement industry. These systems use IoT-enabled sensors and controllers to monitor lubricant condition in real time—tracking parameters such as viscosity, temperature, contamination levels and usage. This data is integrated into plant maintenance software to automate lubricant replenishment and alert operators to potential failures. Predictive lubrication ensures that each component receives the right amount of lubricant at the right time, minimising waste, reducing manual intervention, and extending machinery life.
“Many VpCI® products can be applied to surfaces with minimal pre-cleaning, and the protective VpCI® layer typically does not need to be removed before equipment is put back into service. VpCI® ‘s save significant labor, time, and associated costs compared to methods that require extensive surface preparation (e.g., sandblasting) and post-application cleaning or degreasing. This allows for faster startup after maintenance,” elaborates Ana Juraga, Content Writer, Cortec Corporation.
Furthermore, Original Equipment Manufacturers (OEMs) and lubricant suppliers are collaborating to develop application-specific lubricants tailored to the unique operating conditions of cement manufacturing units. For example, gear oils designed for high-load kilns or open gear systems now come with superior Extreme Pressure (EP) additives and anti-wear properties to cope with shock loading and variable speed operations. These co-developed solutions not only enhance mechanical reliability but also ensure compatibility with diverse materials used in modern cement equipment, ensuring peak performance in both greenfield and brownfield plants.
Sustainability and environmental considerations
The cement industry is under increasing pressure to reduce its environmental impact. Lubricants contribute to this goal by enhancing energy efficiency and reducing emissions. High-quality lubricants decrease friction, leading to lower energy consumption and, consequently, reduced greenhouse gas emissions.
Furthermore, the use of long-life lubricants minimises the frequency of oil changes, thereby reducing waste generation and disposal issues. The shift towards bio-based and recyclable lubricants also supports circular economy principles, promoting resource efficiency and environmental stewardship.
A report by Klüber Lubrication India suggests that sustainability continues to be a key focus for industries, the Securities and Exchange Board of India (SEBI) has mandated Business Responsibility and Sustainability Reporting (BRSR) for the top 1,000 listed companies. This framework requires organisations to disclose their environmental, social and governance (ESG) initiatives, including energy conservation, emission reductions and resource optimisation. Beyond compliance, BRSR reporting allows companies to showcase their sustainability leadership and build investor confidence. Organisations that proactively address sustainability challenges are better positioned to attract long-term investors, secure financing, and maintain a competitive advantage in an evolving regulatory landscape.
The report also states that their high-performance synthetic lubricants play a crucial role in helping cement manufacturers meet these regulatory requirements by enhancing energy efficiency and reducing CO2 emissions in critical machinery such as vertical roller mills (VRMs) and main gearboxes. By adopting our energy-efficient solutions, companies can strengthen their BRSR compliance while achieving tangible operational benefits.
An emerging trend in the lubricant industry is the formulation of biodegradable lubricants specifically tailored for heavy industries like cement manufacturing. These eco-friendly alternatives are made from renewable base stocks and are designed to degrade naturally without leaving behind harmful residues. In environmentally sensitive zones or operations with high spill risk, such as open gear applications or hydraulic systems exposed to the elements, biodegradable lubricants offer a sustainable solution that aligns with stricter environmental regulations and the growing emphasis on corporate social responsibility (CSR) in India’s industrial sector.
KB Mathur, Founder and Director, Global Technical Services, says, “In the world of industrial machinery, lubricating oils while essential; are often misunderstood in terms of their life cycle. When oils are used in machinery, they don’t simply ‘DIE’. Instead, they become contaminated with moisture (water) and solid contaminants like dust, dirt and wear debris. These contaminants degrade the oil’s effectiveness but do not render it completely unusable. Used lubricants can be regenerated via advanced filtration processes/systems and recharged with the use of performance enhancing additives hence restoring them. These oils are brought back to ‘As-New’ levels. This new fresher lubricating oil is formulated to carry out its specific job providing heightened lubrication and reliable performance of the assets with a view of improved machine condition. Hence, contributing to not just cost savings but leading to magnified productivity, and diminished environmental stress.”
Lubricant manufacturers are increasingly focusing on circular economy principles, offering oil analysis, filtration and recycling services that extend lubricant life and minimise waste. Used oil regeneration programs not only reduce disposal costs but also help cement plants meet regulatory norms under the Hazardous Waste Management Rules of India. This closed-loop approach not only lowers the environmental burden but also enhances economic efficiency—making sustainability a dual benefit for operational and ecological performance. As cement companies work towards science-based targets and carbon neutrality, lubricant selection and management play a more strategic role in meeting these broader sustainability commitments.
Challenges and opportunities
Despite the benefits, the adoption of advanced lubricants in the Indian cement industry faces challenges. These include the higher initial costs of synthetic and bio-based lubricants and a lack of awareness about their long-term benefits. Additionally, the integration of lubrication management systems requires investment in training and infrastructure.
However, these challenges present opportunities for innovation and collaboration. Manufacturers
can work closely with lubricant suppliers to develop customised solutions that meet specific operational needs. Moreover, government incentives and regulatory frameworks promoting sustainable practices can accelerate the adoption of advanced lubrication technologies.
Another key challenge is the limited awareness and technical training available at the plant level regarding proper lubrication practices. Many maintenance teams still rely on outdated methods such as manual greasing or fixed-interval lubrication schedules, which often lead to over-lubrication, under-lubrication or lubricant contamination. This results in premature equipment wear and higher operating costs. There is a growing need for skill development programmes and collaboration with lubricant suppliers to train technicians on best practices, condition-based monitoring, and the use of smart lubrication systems.
“Oil in the machine is like blood in the human body. There is no rotating machine that works without lubricants (liquid, semi liquid or solid). Based on the machine component, type of lubricant is used to minimise the mechanical changes in the machine. Lubricant being the product that separates two or more materials under movement. With modern machines being more and more sophisticated and tolerances being finer than before, cleanliness of Lubricants is critical, would the source of contamination be internal wear or external contamination. These contaminations rupture and compromises lubricant film, contamination particles when come in-between the fine tolerances, become cause of catastrophic failure,” expounds Gaurav Mathur.
At the same time, the industry is witnessing an opportunity to leverage digitalisation in lubrication management. Advanced lubrication tracking tools, coupled with ERP and maintenance software, can now offer real-time visibility into lubricant consumption, scheduling and health diagnostics. Integration of AI-powered analytics helps predict equipment failure based on lubricant data, enabling a shift from reactive to predictive maintenance. For Indian cement manufacturers aiming to digitise plant operations as part of Industry 4.0, lubrication is an ideal entry point that delivers immediate ROI and long-term gains in efficiency, asset life and sustainability.
Conclusion
As the Indian cement industry continues its trajectory of growth, the role of high-performance lubricants in ensuring operational reliability, energy efficiency and cost savings cannot be overstated. From kilns and crushers to ball mills and gearboxes, modern lubrication solutions are critical in
reducing downtime and maximising equipment lifespan. With rising demand and increased production pressures, cement plants must adopt a proactive approach to lubrication management—viewing it not as a routine maintenance task, but as a strategic pillar of plant performance.
Recent advancements in lubricant technology, such as synthetic formulations, nano-additives, and smart dispensers, have opened new avenues for boosting equipment efficiency and longevity. Digital tools and IoT-based systems now allow plant operators to monitor lubricant condition in real time, enabling predictive maintenance and minimising the risk of failure. As cement manufacturers increasingly pursue digital transformation and automation under Industry 4.0 frameworks, lubrication systems must be seamlessly integrated into broader asset management strategies.
At the same time, sustainability imperatives are reshaping lubrication choices. There is growing emphasis on biodegradable lubricants, optimised lubricant consumption, and environmentally responsible disposal practices. Overcoming challenges such as limited awareness, inconsistent maintenance practices, and cost sensitivity will require collaboration between lubricant manufacturers, OEMs and cement producers. The opportunities, however, are substantial—by aligning lubrication strategies with efficiency, digitalisation and sustainability goals, the Indian cement industry can significantly enhance its competitiveness and resilience in the years ahead.
– Kanika Mathur
Concrete
We consistently push the boundaries of technology
Published
4 months agoon
April 18, 2025By
admin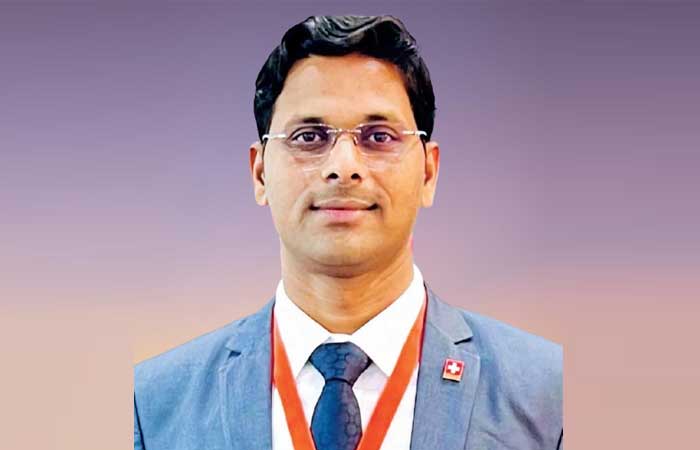
Swapnil Jadhav, Director, SIDSA Environmental, discusses transforming waste into valuable resources through cutting-edge technology and innovative process solutions.
SIDSA Environmental brings decades of experience and expertise to the important niche of waste treatment and process technologies. As a global leader that is at the forefront of sustainable waste management, the company excels in recycling, waste-to-energy solutions and alternative fuel production. In this conversation, Swapnil Jadhav, Director, SIDSA Environmental, shares insights into their advanced shredding technology, its role in RDF production for the cement industry and emerging trends in waste-to-energy solutions.
Can you give us an overview of SIDSA Environmental’s role in waste treatment and process technologies?
SIDSA is a leading innovator in the field of waste treatment and process technologies, dedicated to delivering sustainable solutions that address the growing challenges of waste management.
SIDSA is a more than 52-year-old organisation with worldwide presence and has successfully realised over 1100 projects.
Our expertise is in the engineering and development of cutting-edge systems that enable the conversion of waste materials into valuable resources. This includes recycling technologies, waste-to-energy (W2E) systems, and advanced methods for producing alternative fuels such as refuse derived fuel (RDF). The organisation prioritises environmental stewardship by integrating energy-efficient processes and technologies, supporting industrial sectors—including the cement industry—in reducing their carbon footprint. Through our comprehensive approach, we aim to promote a circular economy where waste is no longer a burden but a resource to be harnessed.
How does SIDSA Environmental’s shredding technology contribute to the cement industry, especially in the production of RDF?
SIDSA’s shredding technology is pivotal in transforming diverse waste streams into high-quality RDF. Cement kilns require fuel with specific calorific values and uniform composition to ensure efficient combustion and operational stability, and this is where our shredding systems excel. In India, we are segment leaders with more than 30 projects including over 50 equipment of varied capacity successfully realised. Some of the solutions were supplied as complete turnkey plants for high capacity AFR processing. Our esteemed client list comprises reputed cement manufacturers and chemical industries. Our technology processes various types of waste—such as plastics, textiles and industrial residues—breaking them down into consistent particles suitable for energy recovery.
Key features include:
- High efficiency: Ensures optimal throughput for large volumes of waste.
- Adaptability: Handles mixed and heterogeneous waste streams, including contaminated or complex materials.
- Reliability: Reduces the likelihood of operational disruptions in RDF production. By standardising RDF properties, our shredding technology enables cement plants to achieve greater energy efficiency while adhering to environmental regulations.
What are the key benefits of using alternative fuels like RDF in cement kilns?
The adoption of RDF and other alternative fuels offers significant advantages across environmental, economic and social dimensions:
- Environmental benefits: Cement kilns using RDF emit fewer greenhouse gases compared to those reliant on fossil fuels like coal or petroleum coke. RDF also helps mitigate the issue of overflowing landfills by diverting waste toward energy recovery.
- Economic savings: Alternative fuels are often more cost-effective than traditional energy sources, allowing cement plants to reduce operational expenses.
- Sustainability and resource efficiency: RDF facilitates the circular economy by repurposing waste materials into energy, conserving finite natural resources.
- Operational flexibility: Cement kilns designed to use RDF can seamlessly switch between different fuel types, enhancing adaptability to market conditions.
What innovations have been introduced in waste-to-energy (W2E) and recycling solutions?
SIDSA’s machinery is meticulously engineered to handle the complex requirements of processing hazardous and bulky waste.
This includes:
- Robust construction: Our equipment is designed to manage heavy loads and challenging waste streams, such as industrial debris, tires and large furniture.
- Advanced safety features: Intelligent sensors and automated controls ensure safe operation when dealing with potentially harmful materials, such as chemical waste.
- Compliance with standards: Machinery is built to adhere to international environmental and safety regulations, guaranteeing reliability under stringent conditions.
- Modular design: Allows for customisation and scalability to meet the unique needs of various waste management facilities.
How does your organisation customised solutions help cement plants improve sustainability and efficiency?
We consistently push the boundaries of technology to enhance waste management outcomes.
General innovations and new product development focus on:
- Energy-efficient shredders: These machines consume less power while maintaining high throughput, contributing to lower operational costs.
- AI-powered sorting systems: Utilise advanced algorithms to automate waste classification, increasing material recovery rates and minimising errors.
- Advanced gasification technologies: Convert waste into syngas (a clean energy source) while minimising emissions and residue.
- Closed-loop recycling solutions: Enable the extraction and repurposing of materials from waste streams, maximising resource use while reducing environmental impact.
What future trends do you foresee in waste management and alternative fuel usage in the cement sector?
Looking ahead, several trends are likely to shape the future of waste management and alternative fuels in the cement industry:
- AI integration: AI-driven technologies will enhance waste sorting and optimise RDF production, enabling greater efficiency.
- Bio-based fuels: Increased use of biofuels derived from organic waste as a renewable and low-carbon energy source.
- Collaborative approaches: Strengthened partnerships between governments, private industries and technology providers will facilitate large-scale implementation of sustainable practices.
- Circular economy expansion: The cement sector will increasingly adopt closed-loop systems, reducing waste and maximising resource reuse.
- Regulatory evolution: More stringent environmental laws and incentives for using alternative fuels will accelerate the transition toward sustainable energy solutions.
(Communication by the management of the company)