Concrete
Bridging the Skill Gap in Manufacturing
Published
5 months agoon
By
admin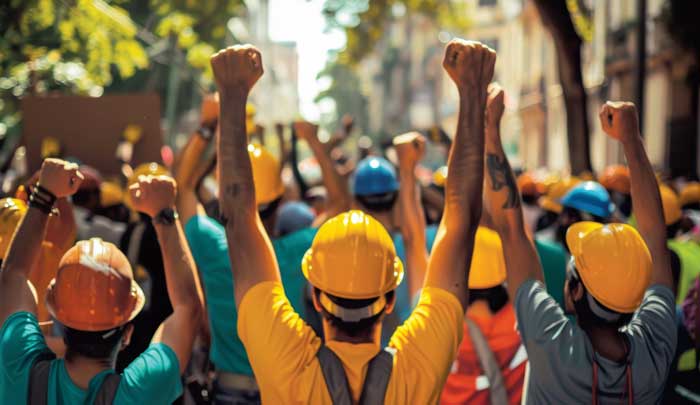
Dr SB Hegde analyses the changing trend in the cement industry as it faces a growing skill gap as ageing workers retire and new talent turns away, threatening efficiency and sustainability.
Cement is the backbone of roads, buildings and cities worldwide. In 2023, the world produced 4.1 billion tonnes of cement, and that number could grow to 4.7 billion tonnes by 2030 (US Geological Survey, 2024). However, there’s a big problem — the cement workforce is ageing and not enough young workers have the skills to operate modern machines or meet new environmental standards. This skill gap — the difference between what the industry needs and what workers can do — is growing quickly. It’s a hidden threat that could slow down construction projects and
hurt economies.
Cement drives development worldwide, but countries like India are feeling the pressure the most. In 2022, India produced 410 million tonnes of cement, making it the second-largest producer after China (Statista, 2024a). With major infrastructure plans for roads and railways, India needs skilled workers more than ever. However, many cement plants are struggling to find workers who understand modern tools or environmentally friendly methods.
This article explores why this skill gap exists, how it impacts the industry, and what can be done to fix it—both globally and in India. With updated statistics and real-world examples, it sends a clear message: cement companies must take action before the problem gets worse.
The hidden crisis
The skill gap in the cement industry is a growing problem that’s not always easy to see. Across the world, experienced workers who have spent decades mastering cement production are retiring. A 2023 report shows that 30 per cent of them are over 50, and new workers aren’t stepping in fast enough, especially in Europe and the US (World Cement Association, 2024).
At the same time, cement plants are becoming more advanced, using technology like smart sensors, automated systems and robots. These systems require workers with technical and computer skills—not just physical strength and basic knowledge.
India is also feeling the heat. With the capacity to produce 690 million tonnes of cement yearly, the industry employs over 1 million people (IBEF, 2024). But according to a 2024 study, 65 per cent of plant managers report not having enough skilled workers to handle modern machinery (CII, 2024). This problem is even worse in southern India, where too many plants compete for limited talent, and low wages push skilled workers to better-paying city jobs.
This skill shortage affects the industry in several ways:
- Higher maintenance costs: Without skilled workers, machines break down more often.
- Reduced cement quality: Poorly operated machinery affects the consistency and quality of cement.
- Increased production costs: Inefficiencies lead to higher operational costs.
The crisis is reshaping how cement is made and forcing companies to rethink their strategies. If the industry doesn’t tackle this problem soon, it could face severe setbacks in productivity, quality and profitability.
From skill to crisis
Cement production used to rely heavily on hands-on skills. Workers learned through experience—breaking rocks, firing kilns and mixing materials. But today, machines handle most of that work. Around 80 per cent of the world’s cement now comes from dry processes, which require less labour but more technical expertise (Rhodium Group, 2024).
The older generation of workers, who mastered traditional methods, often struggle to adapt to modern systems. Meanwhile, younger workers are not being trained quickly enough to fill the gap. This shift is making the industry less efficient and more vulnerable.
India is a prime example of this transformation. Small cement plants once thrived on local skills and traditional methods. But now, large companies like UltraTech, which produces 79 million tonnes of cement annually, are using advanced technologies like waste heat recovery systems (WHRS) to save energy and reduce emissions (IBEF, 2024).
However, a 2023 survey by the National Skill Development Corporation (NSDC) revealed that only 20 per cent of cement workers in India are capable of handling these modern systems (NSDC, 2024). This lack of expertise leads to several problems:
- Inefficiencies in production: Poorly operated technology slows down manufacturing.
- Reduced sustainability efforts: Without skilled workers, eco-friendly systems like WHRS are not fully effective.
- Higher operating costs: More downtime and maintenance result from improper handling of equipment.
The old craftsmanship is fading, leaving the industry at a crossroads. Without immediate action, this skill shortage could severely impact cement production’s ability to meet growing demands and adopt sustainable practices.
Technology’s double-edged sword
Technology is both a solution and a challenge for the cement industry. Around the world, new tech is making cement production faster, cleaner and more efficient. For example, Cemex tested solar-powered cement in 2023, aiming for eco-friendly production, while Heidelberg invested €450 million in carbon capture technology in Belgium (World Cement Association, 2024). These innovations are part of why the global cement market could reach $686 billion by 2032 (Fortune Business Insights, 2025).
However, the catch is that these high-tech solutions require skilled workers who understand how to operate and maintain advanced systems—not just traditional manual labour.
India is also riding the wave of automation. Cement plants are now getting 20–25 per cent of their power from WHRS, which save energy and reduce costs (World Cement, 2025). When Adani acquired Sanghi Industries for $606.5 million in 2023, it added more advanced technology to its operations. But the problem remains: local workers often lack the skills needed to handle this new machinery effectively.
While technological advancements have helped India produce 375 million tonnes of cement in 2023, they are also creating a divide within the workforce. The industry is splitting into two groups:
- Tech-savvy workers: A small group trained to handle automation, digital systems and advanced equipment.
- Traditional workers: A much larger group lacking the skills needed to work with modern technology.
This divide leads to several challenges:
- Underutilised technology: Many high-tech systems are not fully used due to a lack of trained operators.
- Increased operational costs: Companies spend more on training and maintenance when technology is poorly managed.
- Job insecurity: As automation grows, workers with outdated skills face the risk of being left behind.
The cement industry must find a balance between adopting new technologies and ensuring workers have the skills to operate them effectively. Without doing so, the push for efficiency and sustainability could leave a large part of the workforce struggling to keep up.
Why is the young talent avoiding the cement industry?
Young people are not interested in working in the cement industry. Globally, only about 5 per cent of engineering graduates from the US and Europe consider manufacturing jobs, according to a 2023 report (McKinsey, 2023). They see cement jobs as dirty, boring and outdated compared to high-paying tech jobs with modern offices and exciting projects.
India faces the same problem. Although the cement industry contributes around 6 per cent to the country’s economy, it struggles to attract fresh talent. In 2023, the IT sector hired 1.5 million graduates, while the cement industry managed to recruit only about 50,000 (NSDC, 2024). Cities like Bengaluru, known for their booming tech hubs, lure young engineers who prefer coding jobs over working in hot, dusty cement plants in places like Rajasthan.
The perception problem is real. A 2024 survey revealed that 70 per cent of Indian engineering students described cement work as ‘dull’ and ‘unappealing,’ even though starting salaries can be quite competitive, ranging from `8 to Rs.12 lakh per year (CII, 2024). They don’t see cement as a modern, innovative field with growth opportunities.
Beyond the factory floor
The skill shortage in the cement industry isn’t just a factory problem—it’s a major issue for big construction projects worldwide. When cement plants struggle to find skilled workers, everything slows down, causing costly delays.
In the US, the $1.2 trillion infrastructure plan aimed at upgrading roads, bridges and railways is already feeling the pressure. Cement shortages caused by untrained workers are holding back progress (Fortune Business Insights, 2025).
Africa faces a similar problem. Cement demand on the continent is expected to grow by 77 per cent by 2030. But without skilled workers, meeting that demand will be nearly impossible, stalling economic growth and infrastructure development (World Cement Association, 2024).
India is feeling the pinch more than most. The country’s $14.59 billion infrastructure plan, which includes building highways, smart cities and bullet train projects, heavily relies on cement (IBEF, 2024). One of the most ambitious projects, the Mumbai-Ahmedabad Bullet Train, requires a staggering 20,000 cubic metres of cement daily. But skill shortages are disrupting supply, leading to delays.
The problem isn’t just limited to mega-projects. For example, Chennai’s metro expansion faced major delays in 2023 because local cement plants couldn’t meet demand on time. The skill gap is directly impacting the speed and quality of these projects.
What’s at risk?
- Job creation: India’s construction boom is expected to create around 1 million jobs, but if the cement industry can’t keep up, those opportunities will be lost.
- Economic growth: Infrastructure development contributes significantly to GDP. Delays in cement supply can slow down the entire economy.
- Global competitiveness: If India and other countries can’t resolve this skill gap, their ability to compete on a global scale will be compromised.
Bridging the gap
The skill gap in the cement industry isn’t impossible to fix—new training models worldwide are making a difference. Countries and companies are trying out fresh ideas to build a skilled workforce.
In Germany, a dual education system that combines classroom learning with hands-on factory training is producing 60,000 skilled workers every year (IEA, 2023). It’s a practical approach where students gain real-world experience while studying, making them job-ready from day one.
Companies are also stepping up. Holcim introduced virtual reality (VR) training in 2024, allowing workers to practice operating complex cement plants in a simulated environment. This approach saves time, money, and reduces accidents during training.
India is making efforts too. UltraTech’s skill centres trained 10,000 workers in 2023, focusing on areas like automation, machine handling, and safety (IBEF, 2024). The company is trying to bridge the skill gap by equipping workers with modern technical skills.
Collaborations are also happening. Shree Cement has partnered with IIT Kharagpur, producing 500 skilled engineers annually since 2022. This initiative aims to bring fresh talent into the industry, particularly in high-tech areas.
The National Skill Development Corporation (NSDC) and Ambuja Cement have even bigger plans. They aim to train 50,000 young people by 2029, with a special focus on green technologies and sustainable manufacturing.
Why this matters:
- Reducing the skill gap: If these training programmes expand successfully, India’s 65 per cent skill shortage could be significantly reduced by 2030.
- Improving productivity: Better-trained workers mean fewer machine breakdowns, improved cement quality and reduced costs.
- Boosting economic growth: Skilled workers are essential for completing big infrastructure projects on time, directly supporting economic development.
Sustainability at risk
Achieving sustainability in cement production isn’t just about technology—it’s about having skilled workers who can operate and maintain green systems. The cement industry is responsible for 6–8 per cent of the world’s CO2 emissions, pushing companies to find eco-friendly solutions (IEA, 2023).
In 2024, a plant in the UK managed to cut its emissions by 85 per cent by adopting advanced technologies. But here’s the catch: running these systems needs highly trained workers who understand how to use and maintain them.
India is also striving for greener cement production. Major companies like JK Cement have set ambitious targets, aiming to use 50 per cent biomass fuel by 2030. However, only 15 per cent of the workforce currently has the necessary skills to handle this transition effectively (CII, 2024).
Ambuja Cement’s Concrete Futures Lab is one initiative trying to close the skill gap by training 2,000 workers each year in eco-friendly cement production. But compared to the scale of the industry, that’s not nearly enough.
Why this matters:
- Carbon-neutral goals at risk: India’s target of achieving carbon-neutral cement production by 2050 is in danger if the workforce isn’t adequately skilled.
- Need for better training programmes: Without widespread and advanced training programmes, green technologies will remain underutilised, slowing down the progress toward sustainability.
- Global impact: What’s true for India is true for the world—if we don’t bridge the skill gap, the dream of reducing cement’s carbon footprint may stay out of reach.
- The solution is clear: We need more training centres, better courses, and partnerships between companies, educational institutions, and the government to make green cement production a reality.
The global skill gap
The skill gap in cement manufacturing is a worldwide problem, but it looks different depending on where you are.
In the US, which produced 91 million tonnes of cement in 2023, the main issue is a shortage of workers with digital skills to operate advanced systems (World Cement, 2025).
In Africa, the problem is more basic. The industry lacks trained workers altogether, which could severely impact its cement demand expected to rise by 77 per cent by 2030 (World Cement Association, 2024).
India faces a mixed challenge. Northern cement plants struggle to find workers with the technical expertise to handle modern, automated systems. In contrast, southern plants have a surplus of workers, but their skills are outdated or irrelevant. NSDC trains around 50,000 workers annually, but that’s far too little compared to the rapidly growing demand (World Cement, 2025).
In China, the government takes a proactive approach, training 200,000 workers each year through organised programmes to support its massive production of 2.1 billion tonnes in 2022 (Statista, 2024b).
Why this matters:
- India’s demand boom: Cement demand in India is projected to increase by 42 per cent by 2030, but without the right skills, meeting that demand will be difficult.
- Learning from others: Countries need to collaborate, sharing training models and technologies to address skill shortages effectively.
- Bridging the gap: Without the right skillsets, the cement industry’s growth and sustainability goals are at serious risk worldwide.
The urgent need to address the skill shortage
Time is running out. By 2024, the world will have a surplus of 1 billion tonnes of cement, but only skilled workers can make sure it’s used properly (World Cement Association, 2024). In India, the demand for cement could grow by 7–8 per cent every year through 2027, needing $14.89 billion in new plants (CRISIL, 2024). But without the right skills, this growth is at risk.
Here’s the hard truth for cement companies: current efforts aren’t enough. Training 10,000 workers, like UltraTech did, is a good start, but India needs 500,000 more skilled workers by 2030 to keep up with demand. Globally, companies are hoarding technology but aren’t sharing the necessary training, leaving developing regions behind. In India, companies often focus more on profits than on developing talent. Southern plants, for example, lower wages instead of investing in training, causing skilled workers to leave for better-paying jobs in IT. As for sustainability? Many green projects are just for show unless workers have the skills to run them.
So, what’s the solution? Companies need to think bigger. Globally, the cement industry should pool resources and create an industry fund for training, like the oil industry does for research and development. They should share training tools, like virtual reality, to help regions like Africa catch up. In India, companies like UltraTech and Adani should take the lead by partnering with all engineering colleges—not just the top ones—and offering scholarships to attract young talent. Rural plants should raise wages to compete with city jobs. Governments can help too, like India’s 2025 budget could offer tax cuts to companies that train workers, similar to Germany’s model.
But here’s the tough reality: many cement companies resist change. They prefer to squeeze more out of their current workforce rather than investing in new talent. That approach won’t work. If they don’t act now—really act—plants will shut down, projects will be delayed, and sustainability goals will fail. The choice is clear: build a skilled future or watch everything collapse. Which path will you take?
Conclusion
The skill shortage in cement manufacturing is a serious issue, both globally and in India, and it can’t be ignored any longer. As older workers retire, technology is taking over, but young people aren’t interested in cement jobs. This is causing growth to slow down and impacting green initiatives worldwide. In India, with its massive cement production of 410 million tonnes a year and big plans for the future, the situation is even more critical—65 per cent of plants lack skilled workers, putting jobs and infrastructure at risk.
However, there’s hope. New training programmes, like UltraTech’s centres or global VR training tools, show progress, but these efforts aren’t enough yet. Companies must act quickly, share ideas and invest more in training their workforce. If India makes the right moves, it could boost its production to 599.7 million tonnes by 2032 (IMARC Group, 2024). The global cement industry can also thrive with the right investment in skills.
Ignoring the skill gap means risking the foundation of the cement industry—and the future of construction worldwide. Cement companies must decide now: invest in skilled workers and grow, or let the industry’s progress crumble.
References
1. Confederation of Indian Industry (CII). (2024). Skill shortages in Indian manufacturing: A sector-wise analysis. New Delhi: CII.
2. CRISIL. (2024). Cement sector to invest US$ 14.89 billion as capex by FY27. Mumbai: CRISIL Ratings.
3. Fortune Business Insights. (2025). Cement market size, share & trends: Growth report [2032].
4. India Brand Equity Foundation (IBEF). (2024). Indian cement industry analysis.
5. International Energy Agency (IEA). (2023). Cement: Reducing CO2 emissions while meeting demand.
6. IMARC Group. (2024). India cement market size, share, demand & growth – 2032.
7. McKinsey & Company. (2023). The future of manufacturing: Talent trends in 2023.
8. National Skill Development Corporation (NSDC). (2024). Skill gap assessment in the Indian cement sector. New Delhi: NSDC.
9. Rhodium Group. (2024). The global cement challenge.
10. Statista. (2024a). India’s cement production volume 2008–2022.
11. Statista. (2024b). China’s cement production volume 2010–2023.
12. Statista. (2025). Cement production global 2023.
13. US Geological Survey. (2024). Major countries in worldwide cement production in 2023.
14. World Cement Association. (2024). Global cement industry outlook: Trends and forecasts.
15. World Cement. (2025). India in focus: A comprehensive analysis of the Indian cement industry.
About the author:
Dr SB Hegde is a Professor with the Department of Civil Engineering, Jain College of Engineering and Technology, Hubli, India and a Visiting Professor at Pennsylvania State University, USA. He is a globally recognised cement industry expert and academic leader with over three decades of experience. He has held senior positions in leading cement companies and has authored over 235 research papers, holds 10 patents and guided 2 PhDs.
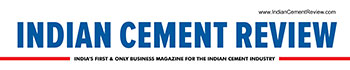
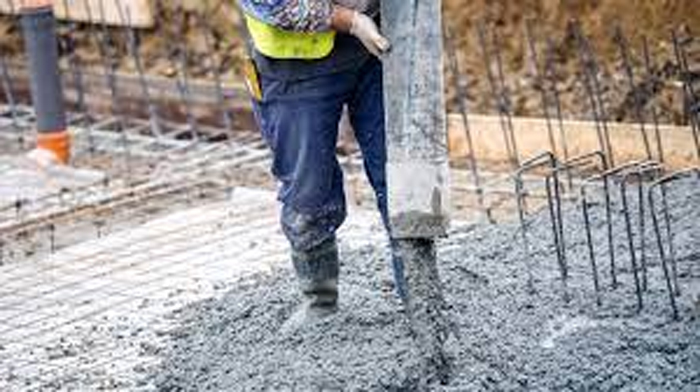
Tamil Nadu is set to host one of India’s five national carbon capture and utilisation (CCU) testbeds, aimed at reducing CO2 emissions in the cement industry as part of the country’s 2070 net-zero goal, as per a news report. The facility will be based at UltraTech Cement’s Reddipalayam plant in Ariyalur, supported by IIT Madras and BITS Pilani. Backed by the Department of Science and Technology (DST), the project will pilot an oxygen-enriched kiln capable of capturing up to two tonnes of CO2 per day for conversion into concrete products. Additional testbeds are planned in Rajasthan, Odisha, and Andhra Pradesh, involving companies like JK Cement and Dalmia Cement. Union Minister Jitendra Singh confirmed that funding approvals are underway, with full implementation expected in 2025.
Image source:https://www.heavyequipmentguide.ca/
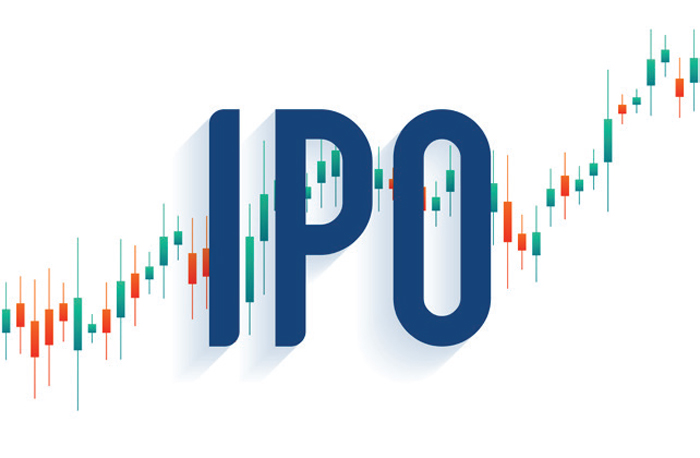
JSW Cement has set the price range for its upcoming initial public offering(IPO) at US$1.58 to US$1.67 per share, aiming to raise approximately US$409 million. As reported in the news, around US$91 million from the proceeds will be directed towards partially financing a new integrated cement plant in Nagaur, Rajasthan. Additionally, the company plans to utilise US$59.2 million to repay or prepay existing debts. The remaining capital will be allocated for general corporate purposes.
Concrete
Cement industry to gain from new infrastructure spending
Published
1 month agoon
July 24, 2025By
admin
As per a news report, Karan Adani, ACC Chair, has said that he expects the cement industry to benefit from the an anticipated US$2.2tn in new public infrastructure spending between 2025 and 2030. In a statement he said that ACC has crossed the 100Mt/yr cement capacity milestone in April 2025, propelling the company to get closer to its ambitious 140Mt/yr target by the 2028 financial year. The company’s capacity corresponds to 15 per cent of an all-India installed capacity of 686Mt/yr.
Image source:https://cementplantsupplier.com/cement-manufacturing/emerging-trends-in-cement-manufacturing-technology/