Concrete
Renewable energy is a cornerstone of our strategy
Published
11 months agoon
By
admin
MM Rathi, Joint President – Power Plants, Shree Cement, speaks about their comprehensive approach to sustainability, which includes renewable energy and cutting-edge technologies.
Can you provide an overview of your company’s current initiatives and strategies to enhance energy efficiency in cement production?
At Shree Cement, we are committed to advancing energy efficiency in cement production through a comprehensive and forward-thinking strategy. We recognise that energy efficiency is crucial not only for reducing operational costs but also for minimising our environmental impact. To this end, we have undertaken several initiatives and adopted innovative strategies to enhance energy efficiency across our cement production processes. We have progressively integrated the use of alternative fuels, such as biomass and waste-derived fuels, into our production process. This not only reduces our dependence on traditional fossil fuels but also lowers greenhouse gas emissions.
Moreover, at the project stage itself, we select and implement energy-efficient drives and key equipment, including fans, compressors and
other critical components, to optimise performance and reduce overall energy consumption. Through advanced data analytics and real-time monitoring, we have optimised key processes such as clinker production, raw material grinding and cement milling, which has led to significant reductions in specific energy consumption.
We conduct Computational Fluid Dynamics (CFD) analysis for our plants right before project execution as a best practice to optimise energy efficiency and ensure informed decision-making in our energy-saving initiatives. We also implement regular energy audits to continuously assess and optimise our energy consumption. These audits help identify areas for improvement, track progress and ensure that our energy efficiency measures are effective.
We are proud to have achieved a renewable energy share of 55.9 per cent in FY 23-24, the highest among Indian cement industries. This achievement underscores our commitment to reducing our carbon footprint and reliance on non-renewable energy sources. Our total power generation capacity is 1 GW, with 50 per cent derived from solar, wind and Waste Heat Recovery (WHR), 30 per cent from Independent Power Producers (IPP), and the remaining 20 per cent from coal-based captive power plants. We have invested in Waste Heat Recovery (WHR) systems with a total capacity of 245 MW across several of our plants. These systems capture waste heat from the production process and convert it into electrical energy, reducing our overall energy consumption and enhancing efficiency. Further, we are exploring emerging technologies i.e. battery energy storage, pumped hydro energy storage, electric trucks etc.
As part of our long-term sustainability goals, we have joined the RE100 initiative, pledging to achieve 100 per cent renewable electricity by 2050. This commitment reflects our dedication to leading the industry in transitioning to a low-carbon future. In alignment with global climate goals, we have set ambitious targets to reduce our Scope 2 emissions by ~27-28 per cent and Scope 1 emissions by ~12-13 per cent by 2030, compared to 2019 levels. These targets highlight our proactive approach to mitigating climate change.
What are the key challenges your company faces in implementing energy-efficient practices in the cement manufacturing process?
While we are committed to enhancing energy efficiency, a few challenges persist. For example, the use of alternative fuels is impacted by supply chain issues and resource availability. Fluctuations in alternative fuel supply (quantity and quality) can disrupt the consistent implementation of energy-efficient practices. Also, upgrading infrastructure to incorporate energy-efficient technologies, including the higher costs of battery and pump storage systems, requires substantial capital investment. There could also be technological constraints related to compatibility and operational disruptions when integrating new, energy-efficient technologies into existing plants. Addressing these challenges requires a thorough approach to enhance energy efficiency throughout the cement manufacturing process, which our engineers are constantly endeavoring to find solutions to.
How do advancements in technology contribute to improving energy efficiency in your cement plants? Can you provide some examples?
Technological advancements are crucial for improving energy efficiency at our cement plants. We leverage Industry 4.0 technologies, including centralised data servers and remote data monitoring, to optimise operations. These technologies provide real-time insights and control over plant performance, enabling precise energy management and reducing downtime. Also, ISO 50001-certified energy management systems provide a structured approach to continuous energy performance improvements.
Additionally, our manufacturing plants leverage the latest and state-of-the-art equipment such as waste heat recovery systems, MVDs/VFDs, IE4 motors, centrifugal compressors, etc. Our meticulous planning and adoption of energy-efficient technologies have helped us overachieve the targets that were notified under the various Perform, Achieve and Trade
(PAT) schemes.
What role does renewable energy play in your overall strategy for energy efficiency, and how is it integrated into your cement manufacturing operations?
Renewable energy is a cornerstone of our strategy for energy efficiency and sustainability at Shree Cement. Our commitment to integrating renewable energy is reflected in our energy mix, where renewable sources account for 55.9 per cent of our total energy consumption. This significant share has enabled us to avoid 0.94 million tons of CO2 emissions, demonstrating our impact on reducing greenhouse gasses. Our total power generation capacity is 1 GW, with 50 per cent derived from renewable sources, including solar, wind and WHR.
WHR systems, with a capacity of 245 MW, capture and reuse heat generated during production, converting it into electricity. This integration supports our goal of transitioning away from non-renewable fossil fuels and aligns with our commitment to achieve 100 per cent renewable electricity by 2050.
Our energy management strategy leverages renewable energy to stabilise and optimise our energy supply. We are exploring advanced energy storage solutions, such as battery and pump storage systems, to manage the variability of renewable sources and ensure a consistent energy supply. Renewable energy is pivotal in achieving our sustainability targets, including substantial reductions in Scope 1 and Scope 2 emissions. By increasing our renewable energy share, we have significantly lowered our carbon footprint and contributed to global climate goals.
Can you discuss any specific projects or upgrades your company has undertaken to reduce energy consumption and increase efficiency in your cement production facilities?
Shree Cement has undertaken several strategic projects to reduce energy consumption and enhance efficiency in its cement production facilities. A key focus has been the integration of alternative fuels and raw materials into the production processes. The company has made notable progress by utilising hazardous waste, Municipal Solid Waste (MSW) in the form of Refuse Derived Fuel (RDF), and biomass waste such as crop residue. We have been steadily increasing our replacement of fossil fuels with agro-waste and have replaced over +300 billion kCal in FY24. This shift significantly reduces reliance on traditional fossil fuels and promotes the use of renewable resources in cement manufacturing.
We are the pioneers within the cement industry in implementing WHR system to capture waste heat and convert it into usable electricity. Having proven its success, as a policy, Shree Cement is implementing WHR systems across all the existing and upcoming kilns.
Further, Shree Cement manufactures blended cement by incorporating fly ash and ground granulated blast-furnace slag (GBF slag), replacing clinker. This approach not only reduces the demand for clinker but also conserves essential natural resources, such as limestone, and lowers fossil fuel consumption, aligning with our sustainability goals. Additionally, we have focused on improving energy efficiency in our operations. We have successfully reduced clinker energy use by approximately 12 to 18 Kcal/kg clinker produced.
How do you measure and monitor energy efficiency in your cement manufacturing processes, and what metrics are most critical for your company?
To effectively measure and monitor energy efficiency in our cement manufacturing processes, Shree Cement employs several critical metrics. The primary metric is Specific Energy Consumption (SEC), which quantifies the energy required per unit of cement produced, typically expressed in kWh per ton. Reducing SEC is a fundamental objective for enhancing energy efficiency.
Thermal energy consumption is also closely monitored, focusing on the energy required for pyro processes, especially in the kiln. This helps identify opportunities to improve fuel efficiency and optimise Pyro process. Similarly, electrical energy consumption is tracked across various plant components, such as grinding mills, process fans pumps and conveyors. Monitoring this metric helps identify potential areas for improvement in electrical energy use. Another metric is cooler efficiency, which measures how effectively cooling air is utilised back in the
pyro processing, which is crucial for lowering operational costs.
Additionally, WHR systems are evaluated for their effectiveness in capturing and reusing waste heat, as higher recovery rates from these systems can significantly reduce overall energy consumption.
Lastly, monitoring CO2 emissions per tonne of cement provides insight into the environmental impact of our production activities and helps us align with our sustainability goals.
What partnerships or collaborations has your company engaged in to promote and enhance energy efficiency within the cement industry?
Shree Cement has adopted a proactive approach in promoting and enhancing energy efficiency within the cement industry through various strategic partnerships and collaborations.
One of the key avenues has been our partnership with leading technology providers and equipment suppliers to integrate advanced energy-efficient technologies into our production processes. These partnerships enable us to access the latest innovations in energy management, process optimisation, and waste heat recovery systems. Besides teaming up with tech companies, we engage with government agencies and regulatory bodies to stay informed about and contribute to energy efficiency regulations and policies. Our participation in public consultations and policy development helps shape industry standards and supports our compliance with energy efficiency mandates.
Shree Cement is part of various sustainability networks and forums that focus on energy efficiency and environmental impact reduction. These networks provide opportunities to learn from peers, share experiences and collaborate on industry-wide sustainability projects.
We are also actively involved in industry associations such as the Cement Manufacturers’ Association (CMA) and the Confederation of Indian Industry (CII). Through these platforms, we participate in knowledge-sharing, best practice exchange and collaborative efforts on energy efficiency and sustainability initiatives across the cement sector. Shree Cement has also joined the RE100 initiative, a global platform of businesses committed to achieving 100 per cent renewable electricity. This collaboration aligns with our goal to transition to renewable energy sources and drives collective action toward sustainability in the cement industry.
These strategic alliances are instrumental in advancing our sustainability goals and driving industry-wide improvements.
How does your company balance the need for energy efficiency with maintaining high production levels and meeting market demands?
At Shree Cement, balancing energy efficiency with high production levels and market demands involves a multifaceted approach. One of the methods is process optimisation. We continuously refine our manufacturing processes using advanced control systems and data analytics. This approach enhances our operational efficiency while maintaining our production capacity, allowing us to meet market needs effectively. Additionally, Shree Cement has established strong energy management systems that monitor energy consumption in real time. This helps us identify areas for savings and reduce waste while sustaining production levels, ensuring optimal energy use.
Furthermore, Shree Cement also invests in innovation by adopting new technologies such as more efficient clinker coolers which enhance energy efficiency and production levels. To manage energy costs and support high production levels, we run our cement mills during the day when our solar plants are operational. For the remaining energy demand, we plan to meet it during off-peak times of the day (TOD). This strategic energy use helps us optimise energy costs while maintaining efficient production.
Looking ahead, what are your company’s strategic priorities for further improving energy efficiency, and how do you plan to address future energy challenges in the cement industry?
Shree Cement is focused on several key strategic priorities to enhance energy efficiency and address future energy challenges in the cement industry. We plan to expand our investments in solar and wind energy projects to further increase our renewable energy capacity, enhance our reliance on clean energy sources and reduce our overall carbon footprint. To ensure a stable and reliable supply of renewable energy, we are exploring solar plants integrated with battery storage systems. This will enable us to store excess solar power and use it during periods of low sunlight, improving energy efficiency and continuity.
We are also exploring the development of pump hydro storage plants as a means to balance energy supply and demand. This technology will help us manage fluctuations in renewable energy generation and enhance our overall energy resilience.
To reduce emissions from our logistics operations, we are looking at electric trucks, which will decrease our reliance on fossil fuels for transportation and contribute to our sustainability goals.
Further, we are making investments to establish a comprehensive, end-to-end solid waste feeding system for the consumption of municipal solid waste to substantially enhance the thermal substitution rate through a pilot at one of the locations. Upon success, this shall be replicated in other units as well.
– Kanika Mathur
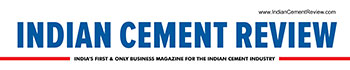
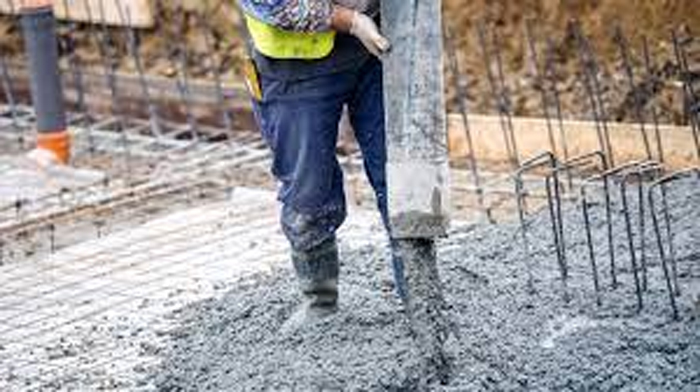
Tamil Nadu is set to host one of India’s five national carbon capture and utilisation (CCU) testbeds, aimed at reducing CO2 emissions in the cement industry as part of the country’s 2070 net-zero goal, as per a news report. The facility will be based at UltraTech Cement’s Reddipalayam plant in Ariyalur, supported by IIT Madras and BITS Pilani. Backed by the Department of Science and Technology (DST), the project will pilot an oxygen-enriched kiln capable of capturing up to two tonnes of CO2 per day for conversion into concrete products. Additional testbeds are planned in Rajasthan, Odisha, and Andhra Pradesh, involving companies like JK Cement and Dalmia Cement. Union Minister Jitendra Singh confirmed that funding approvals are underway, with full implementation expected in 2025.
Image source:https://www.heavyequipmentguide.ca/
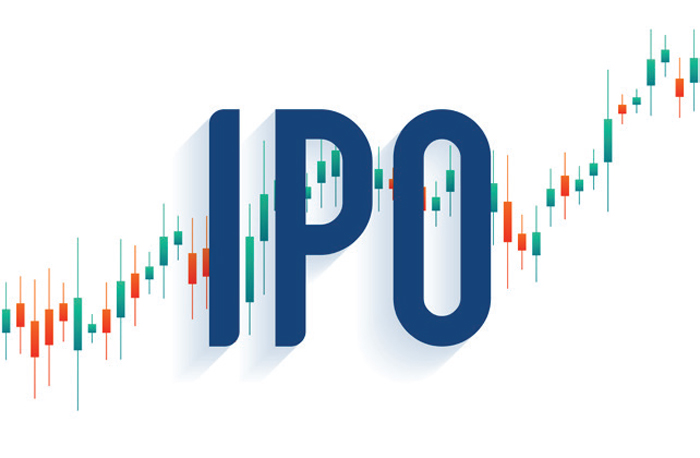
JSW Cement has set the price range for its upcoming initial public offering(IPO) at US$1.58 to US$1.67 per share, aiming to raise approximately US$409 million. As reported in the news, around US$91 million from the proceeds will be directed towards partially financing a new integrated cement plant in Nagaur, Rajasthan. Additionally, the company plans to utilise US$59.2 million to repay or prepay existing debts. The remaining capital will be allocated for general corporate purposes.
Concrete
Cement industry to gain from new infrastructure spending
Published
1 month agoon
July 24, 2025By
admin
As per a news report, Karan Adani, ACC Chair, has said that he expects the cement industry to benefit from the an anticipated US$2.2tn in new public infrastructure spending between 2025 and 2030. In a statement he said that ACC has crossed the 100Mt/yr cement capacity milestone in April 2025, propelling the company to get closer to its ambitious 140Mt/yr target by the 2028 financial year. The company’s capacity corresponds to 15 per cent of an all-India installed capacity of 686Mt/yr.
Image source:https://cementplantsupplier.com/cement-manufacturing/emerging-trends-in-cement-manufacturing-technology/