Concrete
Sustainability is a core priority for us
Published
1 year agoon
By
Roshna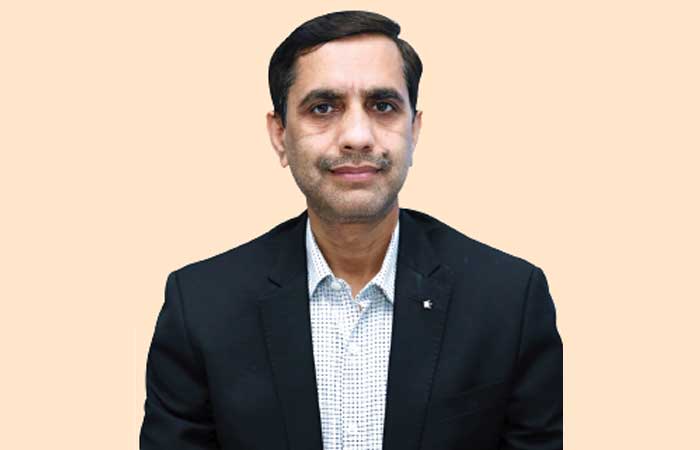
Arun Shukla, President and Director, JK Lakshmi Cement, reveals how their digital transformation initiatives have helped them set new benchmarks.
How has the implementation of IT initiatives transformed your operations and processes in the cement industry?
At JK Lakshmi Cement, we have embarked on a comprehensive digital transformation journey, leveraging cutting-edge technologies to revolutionise our operations and processes. This strategic approach has yielded significant results across several key areas.
We have implemented Dataiku, a leading data science and machine learning platform. This has resulted in a remarkable 60-70 per cent reduction in operational task execution times. Additionally, report generation has skyrocketed by over 300 per cent. This empowers our teams with real-time visibility into crucial metrics encompassing sales, logistics, manufacturing and procurement, ultimately transforming decision-making across the organisation.
By harnessing data from diverse sources, we can now provide customers with near-flawless delivery time predictions at the point of invoicing. This translates to a demonstrably higher level of customer satisfaction and reinforces their trust in our data-driven capabilities. We have made substantial investments in both Internet of Things (IoT) and automation technologies to optimise our operations. IoT is strategically leveraged for tasks like fleet management, supply chain optimisation, and water conservation. Furthermore, a machine learning platform automates essential logistics and supply chain processes, leading to significant cost savings and enhanced operational efficiency.
We have meticulously built robust data analytics capabilities. This includes the utilisation of descriptive analytics, real-time dashboards, and predictive modelling. This empowers our leadership team to make informed, data-driven decisions that positively impact our financial performance.
Environmental sustainability is paramount to JK Lakshmi Cement. We are a proud member of the RE100 initiative, pledging to achieve 100 per cent reliance on renewable energy by 2040. We’ve also deployed green LNG trucks for transportation, further minimising our environmental footprint.
By strategically investing in digital technologies and data-driven initiatives, JK Lakshmi Cement has not only transformed its operations and elevated customer experience, but we have also solidified our position as a frontrunner in the cement industry’s digital transformation.
Can you discuss how your organisation is adopting Industry 4.0 technologies and the benefits you are experiencing?
At JK Lakshmi Cement, we have been proactively embracing Industry 4.0 technologies to drive operational excellence and enhance customer experience. Some of the key initiatives we have undertaken include:
Digitalisation and automation: We have implemented advanced process control systems, smart sensors, and data analytics across our manufacturing facilities to optimise production, improve quality, and reduce energy consumption. For example, JK Lakshmi Cement has been awarded the best EGS performance in community engagement and empowerment at various platforms and has committed to multiple memberships such as SBTi, RE100 and EP 100, which meets its sustainability goals and reduces its carbon footprint.
Supply chain optimisation: We have leveraged technologies like IoT, blockchain, and predictive analytics to enhance our logistics and distribution network. This has allowed us to rationalise our procurement, material handling and transportation, leading to significant cost optimisation.
Customer-centric innovation: To better serve our customers, we have developed a suite of digital tools and services. This includes a mobile app for order placement, delivery tracking, and technical support, as well as an e-commerce platform for seamless online transactions. These digital interventions have greatly improved customer convenience and satisfaction.
Sustainability and efficiency: Sustainability is a core priority for us, and we have adopted Industry 4.0 technologies to drive energy efficiency and reduce our environmental footprint. For instance, we have deployed green LNG trucks for transportation, making us the first cement company in India to do so.
What specific automation technologies have you implemented, and how have they improved efficiency and productivity in your cement plants?
We are at the forefront of leveraging Industry 4.0 solutions to achieve operational excellence. Here are some key highlights:
IoT-powered fleet management and supply chain optimisation: We have deployed a comprehensive IoT ecosystem across our transportation network. This provides real-time visibility into vehicle location, driver behaviour and fuel efficiency. Coupled with our AI-powered logistics platform from FarEye, this has resulted in a 3-4 per cent reduction in logistics costs and a double digit improvement in on-time delivery rates.
Predictive maintenance with AI/ML: We’ve harnessed the power of AI and ML to create predictive maintenance models for our plant equipment. By analysing sensor data and historical maintenance records, these models anticipate potential failures before they occur. This proactive approach has led to a decrease in unplanned downtime and a significant improvement in overall equipment effectiveness.
Automated manufacturing processes: We have embraced automation across critical production stages, including material handling, kiln operations, and packaging. For instance, our state-of-the-art German technology for Autoclaved Aerated Concrete (AAC) blocks boasts innovative features like ‘Green Separation’ and ‘Horizontal Autoclaving,’ ensuring unmatched product consistency and quality.
Data-driven decision making: Underpinning these automation initiatives is a robust data analytics and business intelligence (BI) platform. We have developed advanced data models and real-time dashboards
that provide comprehensive insights into key performance indicators (KPIs) across sales, logistics, manufacturing and finance. This empowers us to make data-driven decisions that optimise operations and drive continuous improvement.
How are predictive analytics and maintenance technologies being utilised in your operations to minimise downtime and optimise maintenance schedules?
We are pioneering a data-driven approach to achieve industry-leading operational excellence. Our powerful synergy between advanced analytics and AI-powered solutions is transforming our business.
We have gone beyond basic forecasting by building robust AI and machine learning models. These models leverage a comprehensive data landscape, including historical production data, real-time sensor
readings from our Industrial Internet of Things (IIoT) network, and even external market trends. This holistic approach empowers us to generate highly accurate predictions that guide critical decisions across the entire value chain.
For instance, our predictive maintenance program, powered by IIoT sensors and cutting-edge analytics, continuously monitors equipment health. By identifying potential issues early, these models enable proactive maintenance interventions, drastically reducing unplanned downtime and maximising equipment effectiveness.
Similarly, our sales forecasting models, fueled by machine learning, meticulously analyse market dynamics, customer behaviour patterns
and a multitude of other factors to predict future demand with exceptional precision. This allows us to optimise production planning, logistics and inventory management, ensuring we meet customer needs efficiently while minimising waste and operational inefficiencies.
Our commitment to continuous improvement is resolute. The positive impact of these investments is undeniable. Our data models currently boast an excellent example of growth and commitment
and have been on an upward trajectory. By embracing these cutting-edge solutions, JK Lakshmi Cement is well-positioned to solidify its leadership position within the industry. We are driven to achieve operational excellence, superior competitiveness, and ultimately deliver exceptional value to both our customers and shareholders.
What are the challenges and advantages of integrating data across various systems in your cement manufacturing process?
Integrating data across various systems in our cement manufacturing process presents both challenges and advantages. One of the key challenges we face is the lack of real-time data connectivity, which can hinder efficient decision-making and agility within the organisation. To address this, we have implemented Oracle Cloud Solutions, which provide advanced analytics and real-time data connectivity, enabling us to have access to accurate and timely information for better decision-making and operational effectiveness.
Another challenge is the lack of integration among our systems, which can lead to inefficiencies, data duplication, and errors. To overcome this, we have implemented an integrated enterprise resource planning (ERP) system, which has streamlined our operations, enhanced data accuracy, and improved our overall business processes. This integration has also promoted streamlined processes and data integration, leading to enhanced efficiency and productivity through automation, data centralisation and improved communication with stakeholders.
One of the key advantages of integrating data across our systems is the ability to have a more transparent, agile, and integrated supply and logistics chain. With the implementation of Oracle Logistics Management Solution, we have been able to overcome challenges related to consignment locations and truck movements, providing real-time visibility into our operations. This has also led to operational efficiency improvements and the ability to predict consignment delivery times, which we share with our customers, enhancing their experience.
Furthermore, the integration of our systems has allowed us to create a more holistic technology landscape, enabling us to act faster and be more predictive. This has allowed us to address issues proactively and improve our overall operations, ultimately leading to enhanced customer satisfaction and loyalty.
How are IT initiatives contributing to sustainability efforts and reducing the environmental impact of your cement production?
JK Lakshmi Cement is leveraging innovative IT initiatives to drive sustainability and reduce the environmental impact of its cement production operations. By harnessing the power of digital technologies, the company is optimising its processes and enhancing resource efficiency across the
value chain.
One key IT-enabled initiative is the implementation of advanced analytics and predictive modeling. The company has deployed sophisticated data analytics tools to gain real-time visibility into energy consumption, emissions, and resource utilisation across its manufacturing facilities. This data-driven approach allows JK Lakshmi Cement to identify optimisation opportunities, implement targeted efficiency measures, and track the impact of its sustainability efforts with precision.
Furthermore, the company has invested in cutting-edge automation and control systems to enhance operational efficiency. Intelligent process control algorithms, coupled with Internet of Things (IoT) sensors, enable the company to fine-tune production parameters, minimise waste and reduce energy use. This intelligent automation has resulted in significant improvements in energy efficiency and a lower carbon footprint for JK Lakshmi Cement’s cement manufacturing operations.
To foster a culture of sustainability, the company has also developed robust digital platforms for employee engagement and knowledge sharing. Interactive dashboards and mobile applications empower employees to track sustainability metrics, participate in green initiatives, and share best practices
across the organisation. This digital ecosystem facilitates cross-functional collaboration and drives continuous improvement in the company’s environmental performance.
Looking ahead, JK Lakshmi Cement is exploring the integration of emerging technologies like artificial intelligence and blockchain to further enhance the traceability and transparency of its sustainability efforts. By harnessing the power of IT, the company is well-positioned to lead the cement industry’s transition towards a more sustainable and environmentally responsible future.
With the increasing digitisation of operations, what steps are you taking to ensure cybersecurity and protect sensitive data?
We recognise the ever-evolving cybersecurity landscape, particularly with the growing digitisation of our operations. As a frontrunner in the cement industry, safeguarding sensitive data and maintaining system integrity are paramount.
We leverage a multi-layered cybersecurity approach, featuring industry-leading anti-spam and anti-phishing solutions to combat advanced threats. This aligns seamlessly with our core business goals, where we actively implement ‘security by design’ principles to build inherent resilience within our systems.
Data protection remains a cornerstone of our strategy. We have deployed robust Data Loss Prevention (DLP) controls to guarantee sensitive information security. Furthermore, we continuously elevate employee preparedness through regular cybersecurity awareness training and simulated phishing exercises, fostering a keen ability to recognise and react to potential threats.
Beyond established protocols, JK Lakshmi Cement embraces cutting-edge technology. We utilise smart link neutralisation to assess URL reputation and leverage sandboxing to analyse suspicious files in a secure environment. This layered approach ensures comprehensive threat mitigation.
Moreover, we’ve fostered a strong cybersecurity culture that empowers our employees to actively participate in our defense strategy. Through continuous monitoring of our security posture, investment in skilled personnel, and collaboration with industry experts, JK Lakshmi Cement is well-positioned to navigate the dynamic digital landscape. This ensures the protection of our sensitive data and strengthens stakeholder trust in our commitment to cybersecurity.
What future IT trends do you foresee having the most significant impact on the cement industry, and how is your organisation preparing to embrace these trends?
The cement industry stands on the precipice of a transformative era, driven by the integration of cutting-edge IT solutions. At JK Lakshmi Cement, we are not just keeping pace; we are actively shaping the future by embracing these trends and unlocking their full potential.
One such transformative force is the widespread adoption of cloud computing. By leveraging cloud-native applications like Oracle’s Logistics Management Solution, we have achieved a 25 per cent increase in supply chain transparency and a 10 per cent reduction in logistics lead times). This translates to real-time visibility into operations, allowing us to optimise consignment locations, streamline truck movements, and ultimately, enhance our overall operational efficiency.
Another game-changer is Augmented Reality (AR). We envision AR revolutionising the way we approach construction projects. By creating detailed 3D models and immersive virtual tours, AR empowers stakeholders to gain a comprehensive understanding of a project’s environmental impact, sustainability measures, and overall feasibility – all before construction even begins. This technology also holds immense potential for improving site safety through virtual training and ensuring construction accuracy with BIM (Building Information Modeling) integration.
Machine learning and advanced analytics are poised to further propel the industry forward. By harnessing these powerful tools, we aim to become more proactive. Predictive maintenance, optimised production processes and data-driven decision-making are just a few of the benefits we anticipate. This translates to a significant competitive edge, allowing us to stay ahead of the curve and deliver superior value to our stakeholders.
At JK Lakshmi Cement, our commitment to technological innovation is unwavering. We are actively investing in building a robust IT infrastructure that seamlessly integrates with our ambitious growth plans, which include expanding our manufacturing base, introducing new product lines, and venturing into new markets. To achieve these goals, we’re fostering a culture of continuous improvement and building a holistic technology landscape that empowers a truly connected and intelligent ecosystem.
By embracing these transformative trends, JK Lakshmi Cement is positioned to be a leader in the next generation of cement production. We envision an industry characterised by greater efficiency, enhanced safety standards, and an unwavering focus on providing an exceptional customer experience. Our unwavering commitment to innovation and agility will ensure we remain at the forefront of this exciting transformation.
– Kanika Mathur
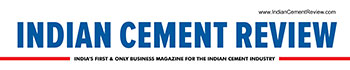
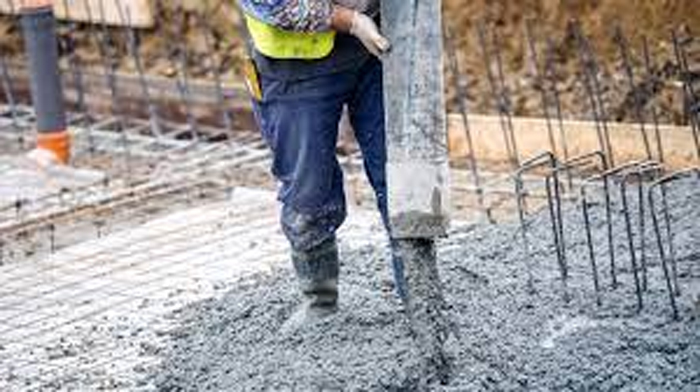
Tamil Nadu is set to host one of India’s five national carbon capture and utilisation (CCU) testbeds, aimed at reducing CO2 emissions in the cement industry as part of the country’s 2070 net-zero goal, as per a news report. The facility will be based at UltraTech Cement’s Reddipalayam plant in Ariyalur, supported by IIT Madras and BITS Pilani. Backed by the Department of Science and Technology (DST), the project will pilot an oxygen-enriched kiln capable of capturing up to two tonnes of CO2 per day for conversion into concrete products. Additional testbeds are planned in Rajasthan, Odisha, and Andhra Pradesh, involving companies like JK Cement and Dalmia Cement. Union Minister Jitendra Singh confirmed that funding approvals are underway, with full implementation expected in 2025.
Image source:https://www.heavyequipmentguide.ca/
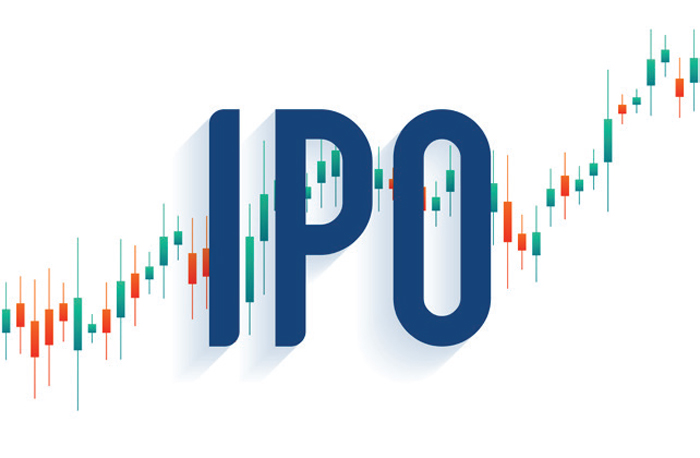
JSW Cement has set the price range for its upcoming initial public offering(IPO) at US$1.58 to US$1.67 per share, aiming to raise approximately US$409 million. As reported in the news, around US$91 million from the proceeds will be directed towards partially financing a new integrated cement plant in Nagaur, Rajasthan. Additionally, the company plans to utilise US$59.2 million to repay or prepay existing debts. The remaining capital will be allocated for general corporate purposes.
Concrete
Cement industry to gain from new infrastructure spending
Published
1 month agoon
July 24, 2025By
admin
As per a news report, Karan Adani, ACC Chair, has said that he expects the cement industry to benefit from the an anticipated US$2.2tn in new public infrastructure spending between 2025 and 2030. In a statement he said that ACC has crossed the 100Mt/yr cement capacity milestone in April 2025, propelling the company to get closer to its ambitious 140Mt/yr target by the 2028 financial year. The company’s capacity corresponds to 15 per cent of an all-India installed capacity of 686Mt/yr.
Image source:https://cementplantsupplier.com/cement-manufacturing/emerging-trends-in-cement-manufacturing-technology/