Concrete
Smart Bags for Cement
Published
1 year agoon
By
admin
The cement bagging and packaging processes have taken a new turn in recent times, with eco-friendly practices taking centrestage. ICR looks at the strategic importance of packaging in enhancing product integrity and logistical efficiency.
Cement bagging and packaging play a pivotal role in the cement industry, ensuring the safe transportation, storage, and delivery of cement products to consumers. Proper packaging is essential not only for protecting the integrity of the cement but also for maintaining its quality and extending its shelf life.
In the Indian cement industry, various packaging methods are employed to meet the diverse needs of consumers and industries. Traditional paper bags have long been used for cement packaging due to their cost-effectiveness and ease of handling. However, with advancements in technology and increasing demand for durable packaging solutions, polypropylene bags and jumbo bags have gained popularity for their superior strength and resistance to moisture and external elements.
Dhananjay Singh Parmar, Senior Manager – Packing Plant, Udaipur Cement Works, says, “Our commitment to delivering a superior product is reflected in the meticulous selection of packaging materials at UCWL. For premium products, we employ high-quality laminated paper-based bags, while for other products, we opt for HDPE bags that adhere to industry standards. The choice of materials is carefully curated to guarantee durability and integrity during transportation and storage. To further ensure the strength of our bags, we conduct random sampling and drop tests, reaffirming our dedication to delivering a reliable and superior product to our customers.”
Each packaging method offers unique advantages and is chosen based on factors such as transportation requirements, storage conditions and customer preferences. Cement manufacturers carefully select the appropriate packaging method to ensure that their products reach consumers in optimal condition, thus maintaining customer satisfaction and upholding industry standards.
GLOBAL OVERVIEW
According to the report Cement Packaging Market – Global Industry Analysis and Forecast (2023-2029) by Maximize Market Research, the cement packaging market size was valued at US$ 343.9 Bn. in 2022 and the total revenue is expected to grow at
3.9 per cent through 2023 to 2029, reaching nearly US$ 449.6 Bn. he growing demand for environmentally friendly cement packaging bags is propelling the cement packaging industry forward. Cement packaging is a critical aspect for any cement manufacturing organisation as well as cement marketers. It should be stored in such bags or sacks that help prevent
the cement from becoming moist. The bags or sacks used to package the cement are made of paper and plastic.
The report’s geographical analysis of the market states that the cement packaging solutions are most expected to become more popular in emerging countries across Asia Pacific and the Middle East and Africa. Polypropylene is the most used cement packing material in nations like India and China.
Because of the increasing demand for the product from developing countries, Asia-Pacific dominates the cement packaging industry. Furthermore, during the forecast period, the growth of the cement packaging market in the area will be aided by the expansion of construction and infrastructure activities. Because of rising urbanisation, the cement packaging market in North America is expected to rise significantly.
MATERIALS AND QUALITY STANDARDS
Polypropylene is the chosen material for cement bags. The benefits of using this material are protection from moisture and strength to packaging. There are various categories of polypropylene bags available with coatings, linings etc.
PP Plain Woven Bags: These are simple bags made of plastic, stitched at the ends to hold cement in them.
PP Lined Woven Bags: These bags have an extra lining under the plastic outside that prevents cement from encountering moisture.
Laminated PP Bags: These bags have an extra poly film layer over the polypropylene. They have a higher strength than the regular PP woven bags and provide a greater resistance from air that meets the bags. These also give way to better branding of the product when it is stored in uncovered settings.
BOPP Laminated Bags: The Biaxially Oriented Polypropylene (BOPP) laminated bags have a superior quality than other bags. An extra added layer enhances the durability of these bags and makes them more attractive for branding as well as prevent wear, tear, and wastage while handling.
Cement makers, for the sake of sustainability, have been contemplating switching to paper bags. However, PP woven bags have various advantages when put in use for storing cement. They are highly chemical and weather resistant. They have high tear strength, which enables it to carry heavyweight materials. PP woven bags are 100 per cent reusable and have high durability making it the less pollutant product compared to other packaging bags. The element of recyclability and waste prevention because of the sturdiness of PP woven bags, they are the chosen material for cement packaging.
Quality control for cement packaging is very important. The BIS (Bureau of Indian Standards) has set norms for cement packaging. As per Cl 9.2 of IS 455: 1989, the average net mass of cement per bag shall be 50 kg. The average net mass of cement per bag may also be 25 kg subject to tolerances and packed in suitable bags as agreed to between the purchaser and the manufacturer. Similarly, as per Cl 10.2 of IS 1489 (Part 1): 1991 and IS 1489 (Part 2): 1991, the average net mass of cement per bag shall be 50 kg. The average net mass of cement per bag may also be 25 kg subject to tolerances and packed in suitable bags as agreed to between the purchaser and the manufacturer. Also, as per IS 8112: 1989, the average net mass of cement per bag may also be 25 kg, 10 kg, 5 kg, 2 kg, or 1 kg, subject to tolerances and packed in suitable bags as agreed to between the purchaser and the manufacturer.
SUSTAINABILITY AND TECHNOLOGY
In the domain of cement bagging and packaging, sustainability and technology are converging to reshape industry practices and drive positive environmental outcomes.
Cement manufacturers are increasingly opting for eco-friendly packaging materials such as biodegradable paper bags, recycled plastics, and compostable coatings. These choices minimise environmental impact and align with global sustainability goals.
Embracing circular economy principles, the industry is investing in recycling infrastructure to recover and reuse packaging materials. Initiatives like the collection and recycling of plastic bags and jumbo bags promote resource efficiency and reduce waste.
“With growing awareness about sustainability and the need to improve the environment, the cement industry has become more accepting of re-processed materials. This would mean that they also use bags made from re-processed materials,” says Alpesh Patel, Director, Knack Packaging.
“Some of our bags are manufactured with repurposed materials and have been placed at some cement plants for trials. However, we believe that it is the need of the hour for the world to bring more and more sustainability to every manufacturing process and facility,” he adds.
Sustainable packaging practices not only address waste management but also contribute to energy savings, reduced greenhouse gas emissions, and conservation of natural resources. By
minimising packaging waste and optimising logistics, cement manufacturers can mitigate their environmental footprint.
The symbiotic relationship between sustainability initiatives and technological advancements is revolutionising the way cement products are packaged and distributed. Embracing a holistic approach to sustainability, cement manufacturers are integrating eco-friendly packaging materials and innovative technologies into their operations. From the selection of biodegradable paper bags to the adoption of recycled plastics and compostable coatings, the industry is committed to minimising its environmental footprint while meeting the demands of a rapidly evolving market.
Moreover, technological innovations such as automation, robotics, and smart packaging solutions play a pivotal role in enhancing efficiency, precision, and resource optimisation. These advancements not only streamline packaging processes but also provide valuable insights into product quality, supply chain visibility and environmental impact. By harnessing the power of digitalisation and data analytics, manufacturers can optimise packaging operations, reduce waste, and drive continuous improvement. This synergy between sustainability and technology not only fosters operational excellence but also reinforces the industry’s commitment to environmental stewardship and sustainable development.
The convergence of sustainability and technology in cement bagging and packaging represents a paradigm shift towards more responsible and efficient practices. By embracing sustainable packaging solutions and leveraging cutting-edge technologies, the industry can enhance competitiveness, meet evolving consumer demands, and contribute to a greener and more sustainable future.
CHALLENGES IN BAGGING AND PACKAGING
Despite significant advancements in technology and practices, the Indian cement industry grapples with several challenges in the domain of bagging and packaging.
Limited infrastructure and inadequate transportation networks in certain regions of India result in logistical challenges for cement manufacturers. Ensuring timely delivery of packaged cement to remote areas remains a persistent challenge, affecting market reach and customer satisfaction.
Maintaining consistent product quality and integrity throughout the packaging process is crucial for cement manufacturers. However, ensuring uniformity in bagging and packaging standards across multiple production facilities and distribution channels poses a challenge, leading to variations in product quality and customer complaints.
Stringent environmental regulations and compliance standards mandate the adoption of sustainable packaging practices in the cement industry. Balancing regulatory requirements with operational efficiency and cost considerations presents a challenge for manufacturers, particularly in implementing eco-friendly packaging solutions and waste management practices.
The disposal and recycling of packaging materials, such as paper bags, polypropylene bags and jumbo bags, present logistical and environmental challenges for cement manufacturers. Developing efficient waste management strategies and promoting recycling initiatives require investment in infrastructure and collaboration with stakeholders across the supply chain.
The Indian cement industry faces multifaceted challenges in the areas of bagging and packaging, encompassing logistical constraints, quality control, environmental regulations, cost pressures, waste management, and consumer preferences. Overcoming these challenges requires collaborative efforts, technological innovation and strategic planning to enhance efficiency, sustainability, and competitiveness in the packaging of cement products.
CONCLUSION
Cement bagging and packaging stand as critical components within the Indian cement industry, ensuring the safe delivery and storage of cement products while meeting the diverse needs of consumers and industries. While the industry has made significant strides in adopting advanced technologies and sustainable practices, it continues to grapple with challenges ranging from logistical constraints to environmental regulations and shifting consumer preferences. Moving forward, concerted efforts from stakeholders across the supply chain will be essential to address these challenges, drive innovation, and foster sustainability in cement packaging practices. By embracing technological advancements, implementing eco-friendly solutions, and prioritising quality control, the Indian cement industry can navigate the evolving landscape of bagging and packaging while fostering efficiency, reliability and environmental stewardship.
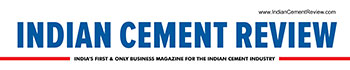
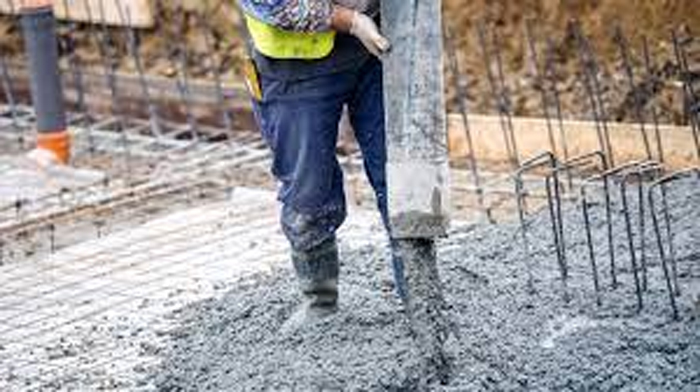
Tamil Nadu is set to host one of India’s five national carbon capture and utilisation (CCU) testbeds, aimed at reducing CO2 emissions in the cement industry as part of the country’s 2070 net-zero goal, as per a news report. The facility will be based at UltraTech Cement’s Reddipalayam plant in Ariyalur, supported by IIT Madras and BITS Pilani. Backed by the Department of Science and Technology (DST), the project will pilot an oxygen-enriched kiln capable of capturing up to two tonnes of CO2 per day for conversion into concrete products. Additional testbeds are planned in Rajasthan, Odisha, and Andhra Pradesh, involving companies like JK Cement and Dalmia Cement. Union Minister Jitendra Singh confirmed that funding approvals are underway, with full implementation expected in 2025.
Image source:https://www.heavyequipmentguide.ca/
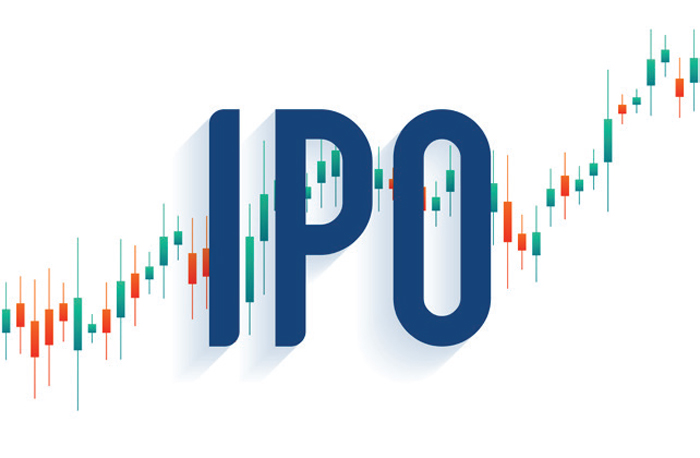
JSW Cement has set the price range for its upcoming initial public offering(IPO) at US$1.58 to US$1.67 per share, aiming to raise approximately US$409 million. As reported in the news, around US$91 million from the proceeds will be directed towards partially financing a new integrated cement plant in Nagaur, Rajasthan. Additionally, the company plans to utilise US$59.2 million to repay or prepay existing debts. The remaining capital will be allocated for general corporate purposes.
Concrete
Cement industry to gain from new infrastructure spending
Published
1 month agoon
July 24, 2025By
admin
As per a news report, Karan Adani, ACC Chair, has said that he expects the cement industry to benefit from the an anticipated US$2.2tn in new public infrastructure spending between 2025 and 2030. In a statement he said that ACC has crossed the 100Mt/yr cement capacity milestone in April 2025, propelling the company to get closer to its ambitious 140Mt/yr target by the 2028 financial year. The company’s capacity corresponds to 15 per cent of an all-India installed capacity of 686Mt/yr.
Image source:https://cementplantsupplier.com/cement-manufacturing/emerging-trends-in-cement-manufacturing-technology/