Concrete
Building the Future
Published
1 year agoon
By
admin
In the rapidly evolving landscape of Indian infrastructure, specialised construction projects stand at the forefront of innovation and development. In this article, we look into the transformative role of cement as India builds its infrastructural dreams, ensuring they stand the test of time and contribute towards sustainable, economic growth.
Specialised construction projects encompass a diverse range of endeavours that demand unique expertise, advanced techniques, and tailored materials to address specific challenges and achieve exceptional outcomes. In India, these projects play a crucial role in shaping the country’s infrastructure and urban landscape, contributing to economic growth and societal advancement. Specialised projects include bridges, dams, metro rail systems, tunnels etc.
India is home to a multitude of bridges spanning rivers, valleys and urban landscapes. These structures vary in complexity and scale, from small pedestrian bridges to iconic cable-stayed bridges like the Bandra-Worli Sea Link in Mumbai or the Signature Bridge in Delhi. With its vast network of rivers and reservoirs, India relies on dams for water storage, flood control and hydroelectric power generation The metro rail systems are vital components of urban transportation infrastructure, providing efficient, sustainable mobility solutions for millions of commuters. Projects like the Delhi Metro, Mumbai Metro and Bengaluru Metro exemplify the integration of modern engineering and construction techniques in urban environments. Tunnels are essential for providing transportation connectivity through challenging terrain, such as mountains and dense urban areas.
ROLE OF CEMENT IN SPECIALISED CONSTRUCTION
Cement stands as the cornerstone of specialised construction projects, offering unparalleled versatility, durability, and strength crucial for these ventures’ success. Its significance lies in its ability to bind various construction materials together, providing structural integrity and longevity to complex infrastructures. Cement’s primary role in specialised projects extends beyond mere adhesion; its chemical and physical properties make it indispensable for a multitude of applications. Notably, its hydraulic properties enable it to harden and set underwater, making it indispensable for projects like dams and underwater structures.
Pritam Chivukula, Vice President, CREDAI-MCHI, and Co-Founder and Director, Tridhaatu Realty, says, “Developers look at the strength, durability, sustainability, local availability of materials and storage of these materials among other properties while selecting a product. It can affect the project and maintenance cost to a large extent. Strength is the most important aspect while selecting construction materials. It reveals the ability to withstand stresses such as compression, tension and shear. For instance, steel is graded according to its strength. If the building does not have to bear large loads, then low steel grade can be used and vice versa.”
“Durability helps in a structure with a long-life span without considerable maintenance cost. Sustainability helps in reducing the carbon footprint and addresses the industry and home buyer demand. Local availability of materials is important as it affects both the construction cost and schedule. Handling and storage of materials is another factor that must be considered because it affects construction time, requirements for labour and equipment for handling and construction cost,” he adds.
Furthermore, cement’s adaptability allows for the formulation of specialised mixes tailored to meet specific project requirements, whether it is achieving high compressive strength in high-rise buildings or enhancing durability in bridges subjected to harsh environmental conditions. Moreover, cement’s compatibility with various additives and admixtures facilitates the development of concrete with desired characteristics, such as rapid strength gain, self-healing properties, and resistance to chemical corrosion. In essence, cement serves as the bedrock of specialised construction, providing the foundation upon which monumental structures and infrastructures are built, ensuring longevity, safety, and resilience in the face of diverse challenges.
Prashant Sharma, President, NAREDCO, Maharashtra, says, “In choosing construction materials, developers focus on key attributes like strength for load bearing, durability against decay and weathering, cost-effectiveness, and environmental sustainability. Material weight influences structural design and engineering, while thermal properties affect energy efficiency and comfort. Fire resistance is crucial for withstanding high temperatures and enhancing building safety.”
TYPES OF CEMENT USED
In the realm of specialised construction projects in India, a diverse array of cement types finds application, each tailored to meet specific project requirements and environmental conditions. Portland Cement serves as the backbone of many projects due to its versatility and reliability, delivering high compressive strength and durability ideal for various applications ranging from high-rise buildings to bridges and dams. Blended cements, such as Portland Pozzolana Cement (PPC) and Portland Slag Cement (PSC), are gaining prominence for their enhanced performance and sustainability benefits. PPC, incorporating pozzolanic materials like fly ash, offers improved workability, reduced heat evolution, and increased resistance to chemical attack, making it suitable for marine structures and underground constructions. PSC, blended with granulated blast furnace slag, exhibits superior resistance to sulfate and chloride attacks, making it an ideal choice for structures exposed to aggressive environments, such as coastal areas and industrial sites.
Moreover, specialty cement formulations, including High-Early Strength Cement (HESC), Low-Heat Cement (LHC), and Sulphate-Resistant Cement (SRC), address specific challenges encountered in specialised projects while contributing to sustainability efforts by reducing carbon emissions and resource consumption. Engineered cementitious materials like Self-Compacting Concrete (SCC) and High-Performance Concrete (HPC) offer superior workability, durability, and mechanical properties, further advancing sustainability goals in the construction sector.
“To curb sustainability issues, adopting alternative materials to traditional cement is crucial for reducing its usage, enhancing production efficiency, and leveraging concrete carbonation to lower emissions. Innovations in concrete mixtures with reduced cement content or carbon capture technology are essential. Sustainable design principles that reduce material use and incorporate natural resources also lessen the construction industry’s environmental footprint. Furthermore, utilising Building information modelling (BIM) improves material specification accuracy, minimising over ordering and construction waste. For instance, fly ash is a byproduct of burning pulverised coal in electric power generating plants. There are multiple advantages like the cement content can be reduced by 25 per cent by mixing ash in the concrete. This concrete mix generates low heat of hydration. It also reduces requirements of clay, sand, limestone in cement manufacturing and hence conserves natural resources,” says Sharma.
“Secondly, autoclaved aerated concrete (AAC) blocks, being 3 to 4 times lighter than traditional bricks, simplify and lower transportation costs.
Their lighter weight reduces a building’s structural load by up to 60 per cent, allowing for more design flexibility and less reinforcement. AAC blocks offer high fire resistance, improving a building’s fire safety. Their production is more sustainable, generating less waste and using fewer resources, and they are environmentally friendly due to their non-toxic materials and lower energy consumption. The quick construction benefits of AAC blocks make them ideal for fast-paced projects without sacrificing quality or durability,” he adds.
By leveraging this diverse range of cement types, specialised construction projects in India can achieve optimal performance and durability, meeting the evolving needs of the built environment while ensuring the success and longevity of monumental undertakings.
TAILORING CEMENT FOR SPECIALISED CONSTRUCTION
In specialised construction projects, cement formulations play a crucial role in meeting specific demands such as strength, durability, and environmental considerations. To achieve desired strength characteristics, engineers can modify cement compositions by incorporating supplementary materials like silica fume or metakaolin.
Durability can be enhanced through the use of blended cements containing pozzolanic materials or slag, which improve resistance to chemical degradation and reduce permeability. Moreover, advancements in admixture technology allow for precise control over concrete properties, ensuring tailored solutions for intricate architectural elements or logistical challenges during construction.
Additionally, innovations in cement chemistry aim to improve environmental sustainability by reducing carbon emissions and energy consumption associated with production. By continuously refining cement formulations, stakeholders can ensure that specialised projects meet structural, durability, and sustainability requirements, addressing the evolving needs of the construction industry.
ADVANCEMENTS IN CEMENT TECHNOLOGY
Recent technological breakthroughs have transformed cement’s role in specialised construction projects, enhancing performance and sustainability. High-performance concrete (HPC) offers superior strength and durability, crucial for challenging environments. Self-healing concrete, integrating microorganisms or encapsulated agents, autonomously repairs cracks, prolonging structural integrity.
Sustainable alternatives like fly ash and ground granulated blast furnace slag (GGBFS), coupled with carbon capture and utilisation (CCU) technologies, reduce the environmental impact of cement production. Digital tools like Building Information Modeling (BIM) optimise mix designs and construction processes, ensuring efficiency and quality. These innovations promise a future where specialised projects are not only robust but also environmentally conscious, meeting the demands of modern construction sustainably.
“The real estate sector in India is evolving and demand is growing for sustainable developments. This brings into play the need to increase the use of green and sustainable building materials in the construction process which has minimal impact on our environment and considerably lowers carbon footprint. These materials conserve natural resources, reduce waste and energy usage,” says Chivukula.
“One innovative approach gaining traction in the concrete industry is carbon capture and utilisation (CCU). This technology captures CO2 emissions from concrete plants and converts them into usable products. For example, captured CO2 can be chemically converted into calcium carbonate, which can then be used as an ingredient in concrete production. This not only reduces CO2 emissions but also improves the concrete’s strength and durability,” he adds.
FUTURE OUTLOOK
Looking ahead, the future of cement usage in specialised construction projects in India holds promising prospects, driven by emerging technologies, evolving market dynamics, and increasing sustainability considerations.
Emerging technologies, such as advanced concrete formulations and digital construction tools, are expected to revolutionise the way specialised projects are conceptualised, designed, and executed. High-performance concrete (HPC) and self-healing concrete will become increasingly prevalent, offering enhanced durability and resilience to structures. Furthermore, digital tools like Building Information Modelling (BIM) and real-time monitoring systems will enable greater efficiency, precision, and sustainability throughout the construction process.
Market dynamics are also evolving, with a growing emphasis on sustainable construction practices and materials. The demand for eco-friendly cement alternatives, such as fly ash, slag, and calcined clays, is expected to rise, driven by regulatory pressures and environmental consciousness among stakeholders. Additionally, the adoption of carbon capture and utilisation (CCU) technologies will play a crucial role in reducing the carbon footprint of cement production, aligning with global sustainability goals.
In conclusion, the future of cement usage in specialised construction projects in India hinges upon continuous innovation and collaboration within the industry. By embracing emerging technologies, market dynamics, and sustainability considerations, stakeholders can ensure that specialised projects meet the evolving needs of the construction sector while minimising environmental impact. Continuous innovation and collaboration will be paramount in driving the industry forward, ensuring that specialised construction projects in India remain at the forefront of excellence and sustainability.
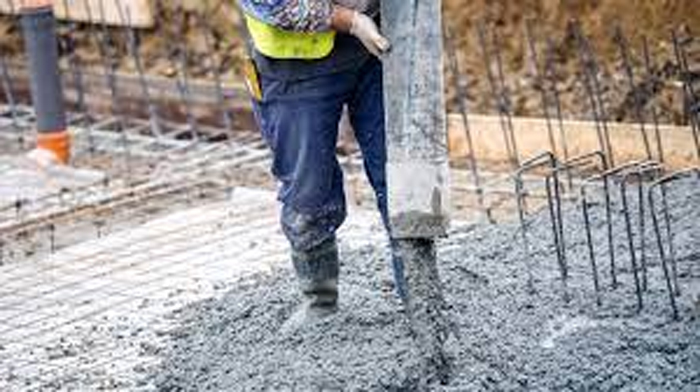
Tamil Nadu is set to host one of India’s five national carbon capture and utilisation (CCU) testbeds, aimed at reducing CO2 emissions in the cement industry as part of the country’s 2070 net-zero goal, as per a news report. The facility will be based at UltraTech Cement’s Reddipalayam plant in Ariyalur, supported by IIT Madras and BITS Pilani. Backed by the Department of Science and Technology (DST), the project will pilot an oxygen-enriched kiln capable of capturing up to two tonnes of CO2 per day for conversion into concrete products. Additional testbeds are planned in Rajasthan, Odisha, and Andhra Pradesh, involving companies like JK Cement and Dalmia Cement. Union Minister Jitendra Singh confirmed that funding approvals are underway, with full implementation expected in 2025.
Image source:https://www.heavyequipmentguide.ca/
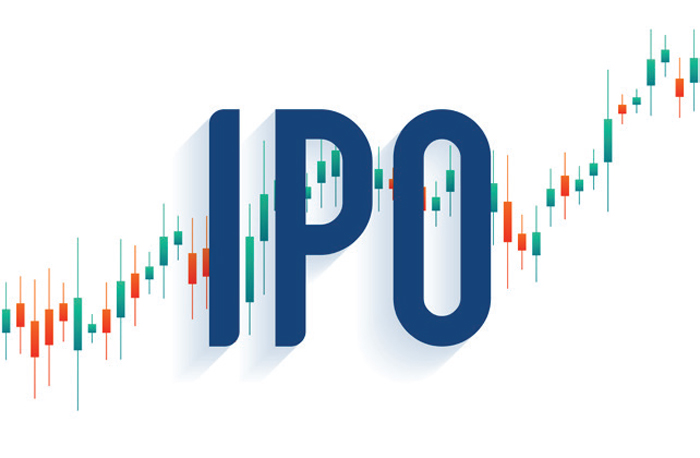
JSW Cement has set the price range for its upcoming initial public offering(IPO) at US$1.58 to US$1.67 per share, aiming to raise approximately US$409 million. As reported in the news, around US$91 million from the proceeds will be directed towards partially financing a new integrated cement plant in Nagaur, Rajasthan. Additionally, the company plans to utilise US$59.2 million to repay or prepay existing debts. The remaining capital will be allocated for general corporate purposes.
Concrete
Cement industry to gain from new infrastructure spending
Published
1 month agoon
July 24, 2025By
admin
As per a news report, Karan Adani, ACC Chair, has said that he expects the cement industry to benefit from the an anticipated US$2.2tn in new public infrastructure spending between 2025 and 2030. In a statement he said that ACC has crossed the 100Mt/yr cement capacity milestone in April 2025, propelling the company to get closer to its ambitious 140Mt/yr target by the 2028 financial year. The company’s capacity corresponds to 15 per cent of an all-India installed capacity of 686Mt/yr.
Image source:https://cementplantsupplier.com/cement-manufacturing/emerging-trends-in-cement-manufacturing-technology/