Concrete
Green Cements and Potential Challenges
Published
2 years agoon
By
admin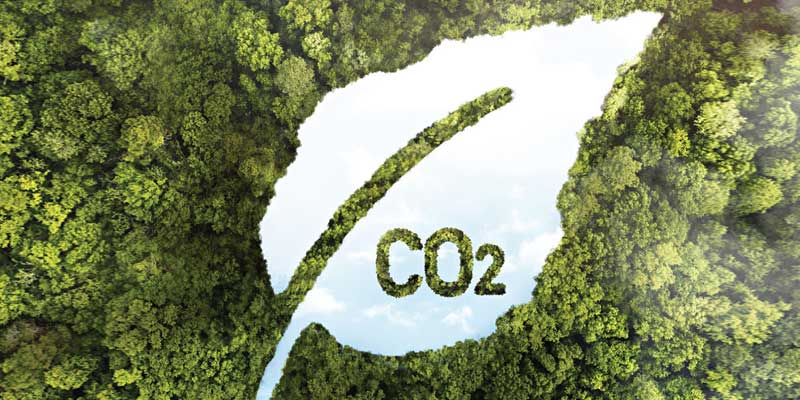
Dr SB Hegde, Professor, Jain University, Karnataka State, India, and Visiting Professor, Pennsylvania State University, USA, discusses the varieties of eco-friendly cements and their key components while evaluating the difficulties in manufacturing them.
Today, cement is the commodity item that is used most widely, and each person uses about half a tonne of cement annually.
Cement, however, has a significant negative impact on the environment despite the important role it plays in society. Currently, the production of cement consumes 3 per cent of the energy used worldwide and contributes to 4.5 per cent of greenhouse gas emissions (GHGs) and as the demand for cement rises, so does its impact on climate change.
For the world to achieve its goal of keeping global warming to 1.5°C in order to avoid the worst effects of climate change, it is imperative to find ways to reduce emissions from the cement sector, but this industry has proven to be obstinately challenging to decarbonise. Today, a crucial chemical process known as calcination is responsible for between fifty percent and two thirds of all emissions from cement manufacturing. Escaping these emissions is challenging.
In order to bring the cement industry to comply with the Paris Climate Agreement, annual emissions must decrease by at least 16 per cent by 2030. This implies that efforts along the entire value chain, from demand management to increasing process efficiency to utilising cutting-edge technologies and solutions in the manufacture of cement and concrete, will be crucial. However, directly addressing the process emissions will have the biggest impact.

It is anticipated that using CCUS technology to decarbonise the cement industry will increase costs by more than $100 per tonne of cement
Types of Main Green or Low Carbon Cements
Green cement is a product that is friendly to the environment and reduces the carbon footprint of cement production. A variety of green cement types have been created after numerous attempts to produce green cements.
The majority of these are based on technological developments, such as new cement formulations, geopolymers, carbon-negative cements, and new concrete products. These include energy-efficient, low carbon production techniques. Additionally, the production of green cement reduces the consumption of cement, and its primary raw materials include fly ash and blast furnace slag, industrial waste.
Examples of green cement include Ekkomaxx cement, magnesium oxychloride cement, geopolymer cement, ferrocrete, calcium sulfoaluminate cement and sequestrated carbon cement. While some of these products have been commercialised and used in numerous projects, some of these cements have not yet been widely used in construction projects despite having significant potential.
Ekkomaxx Cement
It is a kind of green cement made by the American company Ceratech, and it contains 5 per cent liquid renewable additives and 95 per cent fly ash. This cement, made by Ceratech Company, has almost no carbon footprint based on standards like the International Code Council and United States Green Building Council.
Along with a 95 per cent reduction in the use of virgin materials, the process of making cement also requires 50 per cent less water.
High early strength, resilience, crack resistance, low chloride permeability, resistance to sulphate attack, durability and corrosion resistance that is more than three times that of conventional cement, and greater resistance to freezing and thawing than that of standard cement are the main characteristics of Ekkomax cement.
Ferrocrete Cement
By combining silica and iron, which are leftover byproducts from the steel and glass industries, ferrocrete cement is created. This material mixture is then CO2-cured, potentially resulting in the creation of carbon-negative material. Ferrocrete was created by researchers at the Pennsylvania State University, USA.
Sequestrated Carbon Cement
The Calera Corp. cement in California produced cement from seawater or brine mixed with CO2 that may be used as a Portland cement substitute. In this cement production process, CO2Â rich gases are filtered through seawater.
In order to create cement that can be used in place of Portland cement, the Calera Corp. cement plant in California mixed brine or seawater with CO2. Seawater is used to filter CO2 rich gases used in the cement manufacturing process.
Cement Produced with Superheated Steam
The process of superheated steam can be used to change the cement particles in order to make them more reactive. In this process, the emitted CO2 can be captured after it has been separated.
Magnesium oxychloride Cement (MOC)
Magnesium oxide (MgO) powder and a concentrated solution of magnesium chloride are the two main components of magnesium oxychloride cement (MOC), environmentally friendly and carbon-neutral cement (MgC12). These are byproducts of the mining of magnesium.
The MOC has great compressive strength and sets quickly and MgO absorbs CO2 from the atmosphere, but water can reduce its strength considerably. However, this weakness of MOC can be tackled to certain extent by introducing 15 per cent of fly ash and the same amount of silica fume.
These additives fill the pore structure in MOC, which makes the concrete denser. Consequently, both strength and durability of concrete is improved considerably. Furthermore, it is required to add phosphoric acid and soluble phosphates to improve the resistance of this type of green cement against warm water.
This cement causes steel to corrode – it cannot be used to build reinforced concrete structures unless this issue is resolved.
Geopolymer Cement
Alkali-activated cement, also known as geopolymer, is made from aluminosilicates rather than the more environmentally hazardous calcium oxide.
The aluminosilicates are made from by-products of industry, such as fly ash. The performance and price of the geopolymer cement are comparable to those of regular Portland cement, and it emits 95 per cent less CO2 overall.
Potential Challenges
Technology for carbon capture, utilisation, and storage (CCUS) offers one potential answer to these challenging process emissions. In CCUS, CO2 is extracted from cement manufacturing facilities’ exhaust gases and either used as a raw material for the production of valuable chemicals and fuels or stored deep underground in geological formations. Up to 90 per cent of all emissions from cement manufacturing could be eliminated by CCUS. However, there are a number of significant obstacles to overcome before the technology can be scaled up to meet sector demands. The challenges are as follows:

Clinkerisation is the most carbon intensive process in cement making and manufacturers are targeting this process mainly for carbon reduction.
A. CO2 Content
Compared to other industrial processes targeted by CCUS, cement production emits flue gas with a CO2 concentration of less than 20 per cent. Because of this, CO2 capture from cement plants is expensive. The efficiency and economics of the capture process could be improved with the use of creative kiln designs that separate exhaust gases, but doing so would require significant investment and plant redesign.
B. Geographic Limitations
Plants must be located close to an appropriate geological formation for carbon storage, which is neither common nor evenly distributed throughout the world. The cost of storing and transporting the captured CO2 in conjunction with a low-value product like cement poses a significant obstacle to the widespread use of this technology.
C. Capital Expenditure
The deployment of CCUS technology at scale is still a long way off and remains an expensive option. Although it is possible to capture cement plant emissions for about $100 per tonne of CO2, the costs are still higher than for other hard-to-abate industries like steel and fertiliser production.
D. Influence the Customers
It is anticipated that using CCUS technology to decarbonise the cement industry will increase costs by more than $100 per tonne of cement. This entails increasing the cost of cement from its current average of about $ 80-90 120 per tonne by a factor of two and consequently raising the cost of concrete by a factor of about 30 per cent. In a market where prices are so sensitive, this is a significant barrier.
Although CCUS technology is well-positioned to contribute to the decarbonisation of the cement industry, these difficulties make it unlikely that it will solve all problems and difficulties.
Low-Carbon or Green Cement – The Real Solution
Low-carbon cement can reduce process emissions by 10 to 100 per cent when compared to conventional ordinary Portland cement (OPC), which emits 0.6 tonnes of CO2 equivalent per tonne of cement and contains more than 90 per cent clinker. The most energy- and carbon-intensive step in the cement manufacturing process, the ‘clinker’, is directly targeted by low-carbon cement in order to reduce carbon emissions. There are numerous approaches to accomplish this, including:
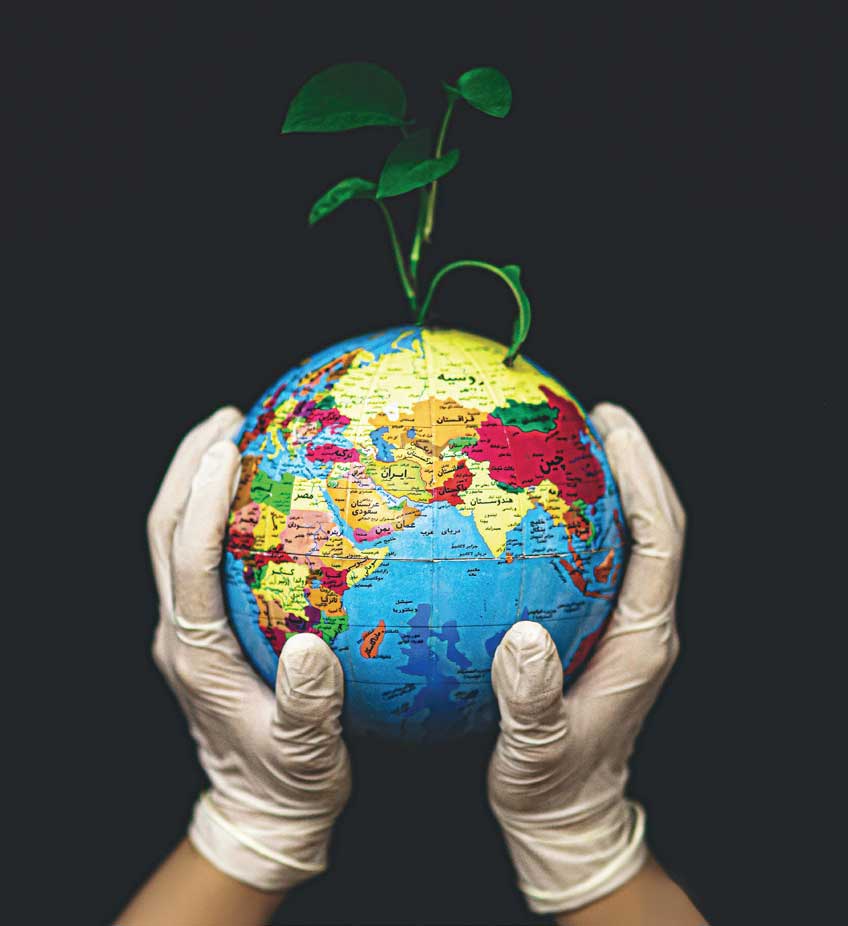
Green cement is a product that is friendly to the environment and reduces the carbon footprint of cement production.
- Reducing the amount of clinker used in cement by substituting a portion of it with alternatives called supplementary cementitious materials, or SCMs
- Readjusting the way clinker is made by reducing the amount of limestone in feedstocks or modifying the calcination process
- Reformulating cement chemistries by developing new binders based on novel materials and low-carbon processes.
Supply-Side Restrictions Stranded Resources
It costs between $200 million and $300 million to build a plant that can produce one million tonnes of ordinary Portland cement, the most widely used type of cement. Since there are currently more than 2,000 cement kilns in use, the industry is very resistant to any solution that calls for a redesign of manufacturing facilities.
Raw Material Availability
Cement is a low-value product that is consumed in enormous quantities, so the raw inputs need to be cheap, reliable and plentiful.

Efficiency of carbon capture process can be Improved with creative kiln designs.
Sales-Marketing Barriers Customer Unrest
Because safety is typically the top priority for engineers, architects and contractors, they prefer to use a reliable and well-known product. Low-carbon cements could differ from conventional OPC in terms of their setting times or early strength. This may lead to the perception that these products are risky, expensive or challenging to use.
Broken Value Chain
Numerous players participate in the construction industry at various stages of the project. This further discourages the use of alternative products by reinforcing the desire to use standardised, predictable and consistent products.
Testing Standards
Current testing standards for cements and concrete are highly prescriptive, often dictating the exact composition required for specific applications. These standards have been designed for OPC and may not be suitable for assessing the true performance of cements based on new chemistries. Setting new standards can take decades, and adoption by customers can be even slower.
Way Forward for Low Carbon or Green Cement
Low-carbon cements are a crucial way to significantly reduce emissions from cement production, despite these legitimate worries. Although there has never been a market for low-carbon cements, large corporations, government organisations, and real estate developers are all demanding solutions to lower the carbon footprints of their infrastructure and buildings, which is mandating pilot scale studies and venture capital interest in this field.
Conclusion
The potential of low-carbon cement cannot be made successful by only cement and concrete manufactures alone. Scaling innovation will require support from and collaboration among a diverse set of people like, cement manufacturers, builders, government and investors, whose input will be crucial at different stages of this project.
ABOUT THE AUTHOR:
Dr S B Hegde is a Professor at Jain University, Karnataka, India and also a Visiting Professor of Pennsylvania State University, United States of America. He had occupied ‘Leadership Positions’ in major and top cement companies in India and overseas. He has published more than 150 research papers in national and international journals. Dr Hegde is a recipient of the ‘Global Visionary’ Award in 2020.
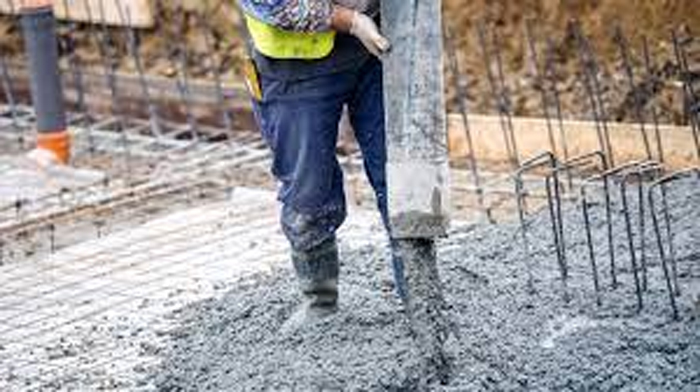
Tamil Nadu is set to host one of India’s five national carbon capture and utilisation (CCU) testbeds, aimed at reducing CO2 emissions in the cement industry as part of the country’s 2070 net-zero goal, as per a news report. The facility will be based at UltraTech Cement’s Reddipalayam plant in Ariyalur, supported by IIT Madras and BITS Pilani. Backed by the Department of Science and Technology (DST), the project will pilot an oxygen-enriched kiln capable of capturing up to two tonnes of CO2 per day for conversion into concrete products. Additional testbeds are planned in Rajasthan, Odisha, and Andhra Pradesh, involving companies like JK Cement and Dalmia Cement. Union Minister Jitendra Singh confirmed that funding approvals are underway, with full implementation expected in 2025.
Image source:https://www.heavyequipmentguide.ca/
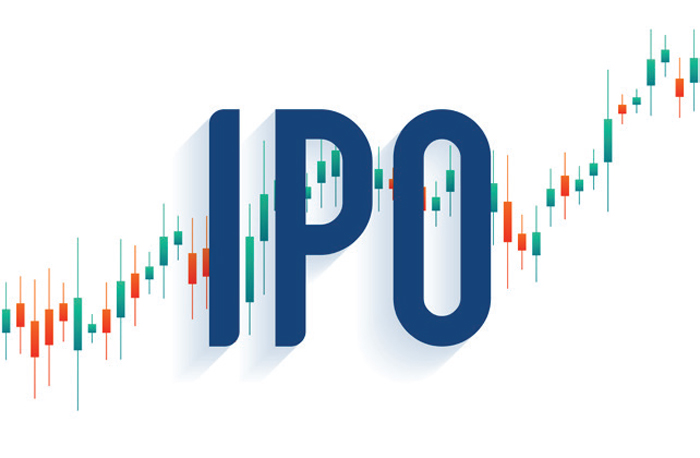
JSW Cement has set the price range for its upcoming initial public offering(IPO) at US$1.58 to US$1.67 per share, aiming to raise approximately US$409 million. As reported in the news, around US$91 million from the proceeds will be directed towards partially financing a new integrated cement plant in Nagaur, Rajasthan. Additionally, the company plans to utilise US$59.2 million to repay or prepay existing debts. The remaining capital will be allocated for general corporate purposes.
Concrete
Cement industry to gain from new infrastructure spending
Published
1 month agoon
July 24, 2025By
admin
As per a news report, Karan Adani, ACC Chair, has said that he expects the cement industry to benefit from the an anticipated US$2.2tn in new public infrastructure spending between 2025 and 2030. In a statement he said that ACC has crossed the 100Mt/yr cement capacity milestone in April 2025, propelling the company to get closer to its ambitious 140Mt/yr target by the 2028 financial year. The company’s capacity corresponds to 15 per cent of an all-India installed capacity of 686Mt/yr.
Image source:https://cementplantsupplier.com/cement-manufacturing/emerging-trends-in-cement-manufacturing-technology/