Concrete
The Framework of Sustainable Mining
Published
3 years agoon
By
admin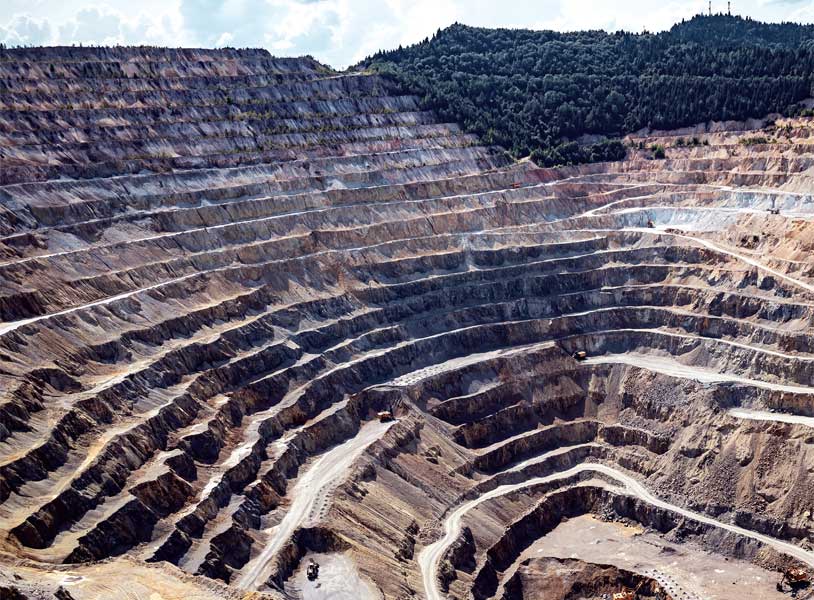
Reducing the environmental impact of mining is a key driver for the Indian cement fraternity today, with a holistic approach and well-planned strategies to ensure lesser carbon emissions.
Mining, the process of extracting from the bed of the earth, is a key process in the making of cement. The raw materials for making cement such as limestone, clay, bauxite and other minerals are sourced from the bed of the earth through the process of mining. The source of energy for cement plants, coal, is also drawn from its mines.
India’s limestone deposits can be found throughout the country. In India, total limestone reserves or resources of all types and grades are estimated to be 203,224 million tonnes. Karnataka has the most limestone reserves, with about 28 per cent, followed by Andhra Pradesh and Rajasthan, each with about 11 per cent limestone reserves. Gujarat, Meghalaya, and Telangana have 10 per cent, 9 per cent, and 8 per cent of the population, respectively. In terms of annual extraction volume, limestone ranks first among non-fuel solid mineral deposits in India.
The mining industry in India contributes significantly to the economy, amounting to around 10 to 11 per cent to the industrial sector. This industry took a modern turn post the economic reforms of 1991, and the 1993 Mining Policy further helped its growth. India has a rich reserve of mineral and non-mineral ores distributed in five mineral belts across the length and breadth of the country. The geographical distribution of mineral belts are the North Eastern Peninsular Belt, Central Belt, Southern Belt, South Western Belt and North Western Belt. The index of mineral production of the mining and quarrying sector for November 2021 stood at 111.9, which was 5 per cent higher than the level in November 2020.
Mining in India falls under the legal and constitutional framework. Governed by the Indian Bureau of Mines, its primary mission is to promote systematic and scientific development of mineral resources of the country (both onshore and offshore), through regulatory inspections of the mines, approval of mining plans and environment management plans to ensure minimal adverse impact on the environment.
Mining operations are regulated under the Mines and Minerals (Development and Regulation) [MMDR] Act of 1957. The State Governments, as owners of minerals, grant mineral concessions and collect royalty, dead rent and fees as per the provisions of MMDR Act. These revenues are held in the Consolidated Fund of State Government until the state legislature approves their use through budgetary processes. The MMDR Act was enacted to provide for the regulation of mines and development of minerals under the control of the Union. The Act has been amended in 1972, 1986, 1994 and 1999 in keeping with changes in the policy on mineral development. In 2015, the act was amended with the intention of removing discretion and introducing more transparency in the grant of mineral concessions. The amendments now made to the MMDR Act, 1957 provide that mineral concessions will be granted only on the basis of bidding at an auction, for the prospecting stage or mining stage on a case to case basis.
According to Make in India – Mining Achievements, the grade conformity of coal has jumped to 69 per cent in 2022-23 (till Nov’ 22) as against 51 per cent in 2017-18. The National Mineral Exploration Trust (NMET) has approved 187 exploration projects with a total cost of Rs 895.72 crore up to 31st December 2019. Among this total 69 projects have already been completed and 118 projects are ongoing. The Government of India has handed over 52 Geological Survey of India (GSI) approved mine blocks to 15 State Governments. An E-portal of an accreditation scheme for Mineral exploration has been launched to increase transparency and ease of doing business.

only to water and land flora and fauna but also to the
ecosystem in and around the mining area.
IMPACT OF MINING ON THE ENVIRONMENT
The Indian cement industry is one amongst the largest in the world, the production is high and so is the demand for raw material and energy. Regardless of the scale of mining, the extraction of rocks and minerals has an impact on the environment at various stages of mining, processing, and utilisation.
The severity of environmental issues is determined by the extent of mining and the mining site’s ecological sensitivity. Denudation of forests, water depletion, pollution of water, soil, and air, loss of natural flora and fauna, reduction in biodiversity, erosion of soil, instability of soil and rock masses, changes in the landscape and degradation of agricultural land are just a few of the obvious environmental consequences of limestone mining. Both terrestrial and aquatic ecosystems are impacted, with long-term consequences that may extend beyond the mining area’s boundaries.
Lowering of water tables, habitat destruction, waste encroachment into agricultural land, building destruction due to cracks, pollution of rivers, loss of biodiversity, destruction of crops, unclean rainwater harvested from roofs, and health issues such as inhalation of dust resulting in respiratory tract infections are just a few of the consequences.
Manish Toshniwal, Vice President and Mines Head, JK Cement, says, “The availability of natural resources is limited and mining leads to depletion of natural resources. It is quite important that on the one hand we meet the needs of the present, and on the other we conserve natural resources to meet future needs.”
“Mining can become more sustainable by developing and integrating practices that ensure cost effective mining, reduce the environmental impacts of mining operations, improve socio economic development of people, and comply with statutory obligations. Massive plantations have been taken up for conservation of flora and fauna in the mines. So far, the plantation drive in mines involves planting 4,07,294 saplings covering an area of 158.07 hectares. The development of bio diversity park, to create safe and secure habitat for local flora and fauna to improve the ecological footprint of the mine, spreads over an area of 50.0 hectares. The park will be developed in three phases with a total of 50,000 saplings and is targeted to be complete by FY 2024-25” he adds.
Mining and metals operations, local communities and others all depend on clean air, water, land and energy. Securing fair access to these shared resources increasingly depends on demonstrating responsible stewardship and recognising the needs of others. Failure to effectively manage the potential adverse impacts of mining on these shared resources can result in the deterioration of environmental resources and have adverse consequences for human health.
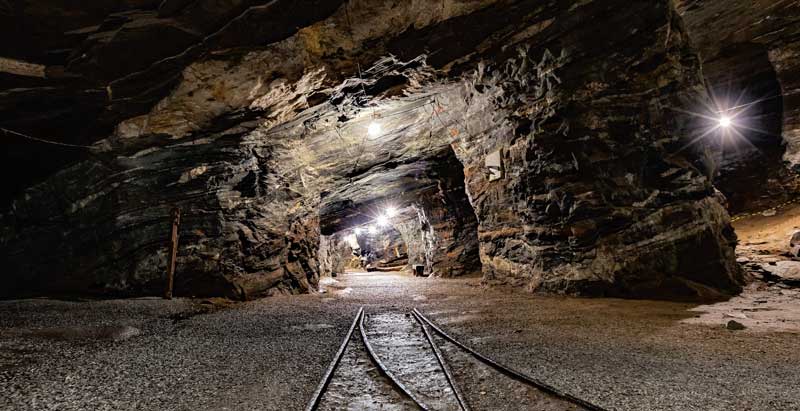
MINING AND THE CEMENT INDUSTRY
Cement manufacturers mine and process raw materials and put them through a chemical reaction process to create cement. They need to understand the chemical composition of the raw materials so that the reaction in their process takes place correctly and they make good, high-quality cement that will eventually be used to make concrete by contractors and ‘ready-mix’ companies. Mining is an integral part of the cement making process. It is the first step in obtaining the key raw material – limestone – from quarries to make the final product. Limestone is obtained from the deposits or rock by blasting or mechanical excavation depending on the hardness of the rock. It is then crushed into smaller chunks. After crushing the stone is sorted into different fractions by screening, after which it is processed further. In the grinding process, the limestone is ground to a fine powder.
Limestone is one of the key minerals used in cement making. Limestone is a sedimentary rock composed mostly of the calcium carbonate (CaCO3) and comprises about 15 per cent of the Earth’s sedimentary crust. Surface mining is the general excavation method. There are a few underground limestone mines, but most are pits on the surface. Most of the limestone is obtained from open quarries. The extraction is carried out by open cast method on both small and large scales. The small-scale extraction of limestone is done manually by individuals using minimal machinery. The limestone beds are drilled for blast holes using drilling machines, after which the rocks undergo blasting. The limestone rocks undergo manual sizing, in order to obtain rock pieces of suitable sizes for easy transportation and processing.
For cement, limestone mining takes place on a large scale by the underground mining method. The basic operations in underground mining are drilling, blasting, loading and hauling, scaling and roof bolting. Drilling equipment includes horizontal drills and down hole track drills. This equipment results in much smaller blast holes and a lower volume of rock produced with each blast. Other equipment required in the underground mine includes powder loaders, which are used to blow ammonium nitrate–fuel oil mixtures into the blast holes. Scaling rigs, which are used to remove loose rocks from the ribs and roof of the mine, and roof-bolting equipment may also be required in an underground mine.
“Hydraulic excavators, wheel loaders, backhoe loaders, bulldozers, dump trucks, tippers, graders, rock breakers, vibratory compactors, cranes, fork lifts, dozers, off-highway dumpers (20T to 240T), drills, scrapers, motor graders, rope shovels, etc. are just a few examples of the machinery that falls under the category of mining equipment deployed for limestone mining. They carry out a range of tasks, including ground preparation, excavation, material haulage, dumping/laying in a specific way, material handling, haul road building, etc. Shovels, surface miners, dumpers and drills are the primary production tools used in opencast mining for hauling, drilling, and excavating,” says Pukhraj Sethiya, Chief Operating Office, ReVal Consulting.
“While a wide variety of mining equipment with various capacities is being used in India, the most popular fleet is made up of hydraulic excavators with 3 to 10 Cu.m bucket capacities and dumpers with 35 to 100 T capacities. Surface miners are also frequently used in the mining of soft and thin seams in softer strata like coal and limestone (in a few locations, such as western Gujarat), which eliminates the need for blasting in coal and ultimately contributes to lowering greenhouse gas emissions,” he adds.
Cement making is an energy intensive process and coal provides for 90 per cent of the energy consumed by cement plants around the world. India is one of the largest producers and consumers of coal, with the cement sector dominating its consumption. The Coal India Limited (CIL) is the state-owned miner for the country and accounts for over 80 per cent of domestic coal production. CIL coal production target for India is set to 1 billion tonnes by FY2020. However, the cement industry gets about 5 per cent of coal from within the country, and the rest of its coal demand is met through imports. The combustion process results in the emission of carbon dioxide, which is a prominent reason for air pollution.
There are four types of coal available in India, namely, peat, lignite, bituminous coal and anthracite coal. The most consumed amongst these are lignite and bituminous. The cement industry mainly uses non-coking bituminous coal and lignite in small quantities in plants in Tamil Nadu and Rajasthan. Specifically, the coal used by the cement companies is of grade G4, G5, G6, G7, G8 and G9.
The Ministry of Coal has the overall responsibility of determining policies and strategies in respect of exploration and development of coal and lignite reserves, sanctioning of important projects of high value and for deciding all related issues. Under the administrative control of the Ministry, these key functions are exercised through the Public Sector Undertakings, namely, Coal India Ltd. and its subsidiaries and Neyveli Lignite corporation India Limited (NLCIL). Other than Coal India Ltd and Neyveli Lignite Corporation India Ltd, the Ministry of Coal also has a joint venture with the Government of Telangana called Singareni Collieries Company Limited. The Government of Telangana holds 51 per cent equity and Government of India holds 49 per cent equity.
The industry is constantly looking for alternative solutions to replace coal and reduce the carbon emission by substituting it with other energy giving materials. This is a conscious effort taken by all large players in the cement industry.
“The demand for coal in the Asian markets has increased in the last two years. Due to this increase in demand, prices have increased dramatically and look on the upper side in the next two quarters. Indonesian miners are trying to cope with the demand but due to logistics constraints and harsh weather conditions, they are facing issues to manage the supply. The demand for Indonesian coal has increased in Europe as well,” says Vishal Uberoi, Director, KTP Exports, Indonesia.

million tonnes of solid wastes related to mining is
generated in India every year
TECHNOLOGY IN MINING
Technology has played a large role in making mining as a process more efficient, productive and sustainable. These technologies have heavily contributed to the growth and progression of the mining operations, leading to more significant mineral commodities and overall productivity.

that mining moves into sustainability terrain real fast.
Artificial intelligence (AI) solutions in mining use smart data and machine learning to improve mining production, efficiency, and safety. These technologies allow companies to generate data in half the time than what has been previously seen in the field, enabling companies to improve decision-making with faster and more accurate data-driven insights. As a result, the AI technologies’ machine-learning capabilities are heavily influencing how mines make decisions for the future. By helping miners locate sites, precise position and in some cases self-driving vehicles or operating machines has made let to minimised costs, reduce environmental impact, and improved safety and reliability.
Automation in excavators and other machinery has also led to making mining a more cost effective and reduced waste process. Thus, making mining sustainable. Technologies like GPS, GIS systems, drones etc., are key to effective mining.
SUSTAINABLE MINING
Mining has its own set of pros and cons.
The planet has bestowed us with minerals and rocks that have properties to make materials that are valuable to human kind. Limestone, other minerals and coal are the key materials that are mined for the cement industry.
Various technologies and methods have been adopted by cement manufacturers and miners to make mining a sustainable process that does not harm the environment. From planting trees to harvesting water, controlling dust and rehabilitating villagers close to the mines, many efforts have been taken to safeguard the environment. Carbon emission is also another factor that is taken care of by the miners.
Anurag Bagaria, Director – Sales & Mining Head, KK Bagaria Group and Anurag Bagaria Group, says, “We incorporate sustainability into our mining process by using renewable energy sources, such as solar and wind power, to power our operations. We also use water recycling systems to reduce water consumption and minimise our environmental impact. Additionally, we use advanced technologies to reduce our carbon footprint and minimise our waste output. Finally, we strive to ensure that our operations are conducted in a responsible manner that respects the local environment and communities. Sustainable mining is an essential element – not only in recovering from the latest mining slump but also for the industry’s long-term survival”.
According to the Indian Bureau of Mines, it is estimated that well over 170 million tonnes of solid wastes related to mining are generated in India every year. This is expected to rise substantially to 300 million tonnes with the increase in production of various minerals. Due to shortages of some minerals in the natural reserves and depletion of high-grade ores, leaner grade ores are being mined which generate a large amount of waste. Adding to this, the preferred method of mining for industries is the open cast method for its high productivity, economic viability and safety aspects, which leads to large volumes of waste generation.
This rock waste generated cannot be immediately back filled due to geological constraints and has to be planned and phased out. This results in stacking of this waste externally creating a mining waste dump.
While this waste is an unavoidable damage to the land, there are many ways of rehabilitating the area where the waste is dumped. The design of the waste should accommodate progressive rehabilitation to ensure a minimum area is disturbed at any given time. This waste can also be used in alternative jobs, like construction or landfills, to put it to good use and reduce the stacking and dumping of the same.
It must be ensured that a proper drainage channel is created from the waste dump in case heavy rainfall is expected in the area. This shall prevent the nearby land from getting contaminated with the waste residues. Proper rehabilitation of tailings must be planned in order to avoid contamination of water sources around the dump area.
Rehabilitation of the mining waste dump areas should aim to establish a vegetative cover and increase rainfall infiltration. Dumps with higher salt content must be screened with overburden of the lowest salt content.
The cement industry consumes mined materials for their varied processes, and its volume has the potential to change the game for the environment. Shifting practices towards sustainable means can lead to a greener country with cleaner air. With advanced technology and better planning, this is an achievable feat. Influential players in the cement industry are taking efforts to help heal the environment and create mining processes that do more good than harm.
-Kanika Mathur
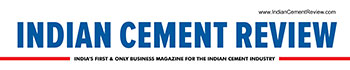
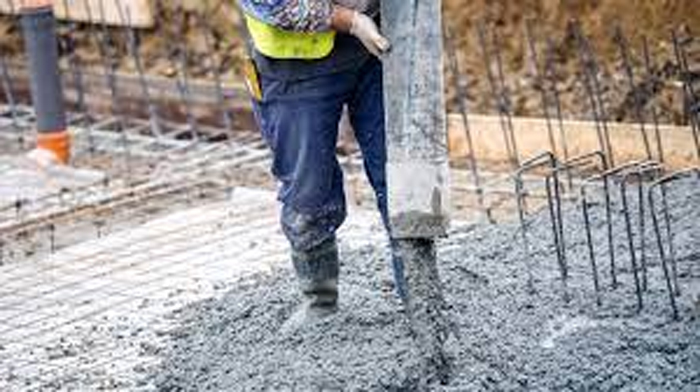
Tamil Nadu is set to host one of India’s five national carbon capture and utilisation (CCU) testbeds, aimed at reducing CO2 emissions in the cement industry as part of the country’s 2070 net-zero goal, as per a news report. The facility will be based at UltraTech Cement’s Reddipalayam plant in Ariyalur, supported by IIT Madras and BITS Pilani. Backed by the Department of Science and Technology (DST), the project will pilot an oxygen-enriched kiln capable of capturing up to two tonnes of CO2 per day for conversion into concrete products. Additional testbeds are planned in Rajasthan, Odisha, and Andhra Pradesh, involving companies like JK Cement and Dalmia Cement. Union Minister Jitendra Singh confirmed that funding approvals are underway, with full implementation expected in 2025.
Image source:https://www.heavyequipmentguide.ca/
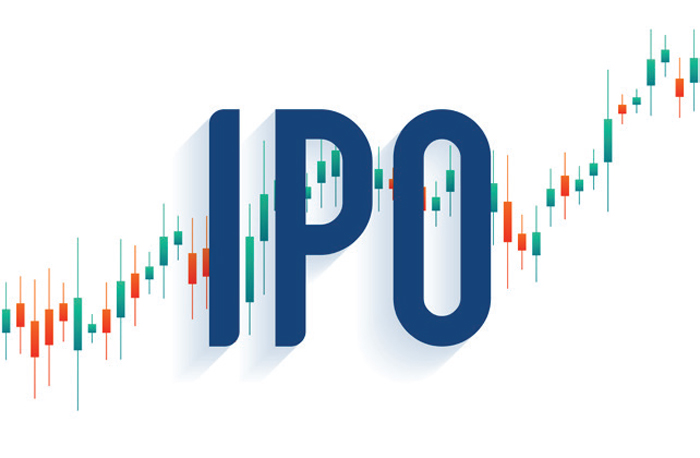
JSW Cement has set the price range for its upcoming initial public offering(IPO) at US$1.58 to US$1.67 per share, aiming to raise approximately US$409 million. As reported in the news, around US$91 million from the proceeds will be directed towards partially financing a new integrated cement plant in Nagaur, Rajasthan. Additionally, the company plans to utilise US$59.2 million to repay or prepay existing debts. The remaining capital will be allocated for general corporate purposes.
Concrete
Cement industry to gain from new infrastructure spending
Published
3 weeks agoon
July 24, 2025By
admin
As per a news report, Karan Adani, ACC Chair, has said that he expects the cement industry to benefit from the an anticipated US$2.2tn in new public infrastructure spending between 2025 and 2030. In a statement he said that ACC has crossed the 100Mt/yr cement capacity milestone in April 2025, propelling the company to get closer to its ambitious 140Mt/yr target by the 2028 financial year. The company’s capacity corresponds to 15 per cent of an all-India installed capacity of 686Mt/yr.
Image source:https://cementplantsupplier.com/cement-manufacturing/emerging-trends-in-cement-manufacturing-technology/