Concrete
Water management has recently undergone a paradigm shift
Published
3 years agoon
By
admin
Anil Kumar Jain, Assistant Vice President, Corporate Head – Environment and Sustainability, JK Cement, talks about the various sources of water harvesting at their cement manufacturing unit, and the steps taken to reduce its water footprint.
Tell us about the use of water in the cement manufacturing process.
Cement production requires water for dust suppression in mining activity (wet drilling, crusher and haul road spray etc.), making raw material sufficiently moist in raw material storage area to avoid growing of fugitive emission during handling of dry materials (crushed limestone, additives and coal etc.), cooling heavy equipment, power generation (CPP and WHRS), grinding mills (size reduction of raw materials), cooling of process gases, spray on kuccha roads to control the dust emission, plantation and domestic consumption.
What is the dry process? What kind of impact does it have on water positivity for cement manufacturers?
The traditional practice of cement manufacturing was water intensive, owing to the wet manufacturing processes. In the last two decades, the Indian cement industry has almost fully transitioned to the dry manufacturing processes supplemented by air cooling and multiple dust control technologies/practices and reduced water consumption about 50 to 60 per cent.
Present cement plants mostly fulfil their water requirement from the rain water harvesting systems and maintaining ZLD. Modern plants are highly water positive and have a positive impact on society. Presently, almost 99 per cent of installed cement manufacturing capacity in India uses dry process. A water positive dry process plants withdraw minimal water from ground and surface sources, consume 100 per cent self-generated waste water and put more fresh water into the aquifer by implementing the effective rain water harvesting and ground water recharge system in and around the plant and in the mining area. As a result, the surrounding water level improved. The positive benefit of this is that the society that lives around the plant gets water in better quality and quantity from their own sources and the cement industry also supplies to meet their domestic and agriculture purpose, which also improves the community relationship. Additionally, it has reduced the risk of productivity loss due to water scarcity.
I would say that the dry process cement plant with water positivity technologies will remain sustainable and will take full care of the society
and business.
Tell us about the various sources of water harvesting within the premises of your cement manufacturing unit.
JK Cement has both integrated cement manufacturing units with mining and standalone cement grinding units.
All of our sites understand the importance of water conservation and implemented various steps for harvesting of water such as construction of storm water drains and ponds within premises for collection of rainwater, artificial ground water aquifer recharge structures to improve the groundwater level and collection of rainwater in mine-pits. Our rainwater harvesting activities are not only made to benefit our organisation but also to the communities around our plants. We have constructed water ponds and other structures in village areas around our plant’s vicinity, which are filled with rainwater collected in our mine pits to meet the water requirement for agriculture, livestock and domestic etc.
Our vision and mission are to stay away from lack of water and worry of water scarcity by reducing the dependency on ground water and fresh water as well. We utilise our own treated domestic sewage water and city sewage water for plantation. We believe that our dependency on recycled/harvested water is high and the importance will continue to remain.
I am delighted to share that one of our integrated cement plant at Muddapur in Karnataka is India’s only Integrated Cement Factory, which has been awarded this year FY2022 with most prestigious CII GreenCO Platinum Award for implementation of world’s best practices and best available technologies in decarbonisation, process optimisation, clean energy, waste management, biodiversity and water stewardship.
This plant uses 100 per cent rainwater and no ground water in plant operation, maintaining ZLD, use of more than 80 per cent clean and green power which doesn’t consume water. Similarly, our other integrated cement plants are also switching towards using rainwater to reduce dependency on ground water sources. The Mangrol plant in Rajasthan is the second integrated plant which has received prestigious CII GreenCO Gold award this year FY2022 for implementation of best practices for a sustainable future including water stewardship.
Moreover, the same complex has been awarded with the CII National Award for Excellence in Water Management, 2022. Our Nimbahera Integrated complex has also implemented the best practices for water harvesting and consuming about 80 per cent rain water including domestic use. This all happened because we have developed sufficient rainwater collection systems within our premises, which is cost effective as well as sustainable and win-win deal with respect to availability, quality, no special treatment required and generate very less reject water, which is fit for another utility.
Elaborate the steps taken by your organisation to reduce its water footprint.
We believe that reducing our dependence on natural resources is sustainable and beneficial for business. We have our vision, mission, and culture to use natural resources at lower scale and to utilise waste as much as possible. Our focus is to reduce the fresh water consumption, recycle the discharge in process and reuse the waste water of others as well so that our natural and pure water wealth can be saved, which could be used by us and society in difficult times. This is our way of reducing the business and social risk.
JK Cement has a 100 per cent dry process manufacturing operation. A minimal quantity of water is used in the process to maintain the required moisture in raw materials to avoid dust emission, cooling of heavy equipment, makeup water for steam generation in WHRS to produce green power, plantation and domestic consumption.
Our focus is on implementation of water efficient practices and technologies in all the operations. Our operations are not water intensive in terms of quality and quantity and we accept all types of water because there is no such thing as waste in our business model and any waste, if it can be useful in our operations, is a sustainable resource for us.
We are a zero liquid discharge company and ensure that most of our operational requirements are addressed through rainwater harvested and recycled water. Fresh water or good quality water is only required for domestic purposes. Hence, we don’t foresee any changes in our dependency on good quality freshwater in future.
At JK Cement, we have employed various technological interventions to minimise our water consumption. Our endeavours in this direction are summarised as under:
- To get rid of ground water resources, firstly we connected all the mine pits at Nimbahera Chittorgarh in Rajasthan with a plant for which we laid the pipeline and installed the latest water filter plant to make it fit for domestic and industrial consumption. The same setup is also being installed for Mangrol plant in Chittorgarh, Rajasthan for domestic purposes.
- All our power generation plants (CPP and WHRS) are operated on air cooled condenser technology except one WHRS at Nimbahera, which is under final stage of commissioning, and as soon as it starts our water consumption will be reduced by 90 per cent in power generation and 50 per cent in overall complex consumption.
- Replaced water-cooled reciprocating compressor with air cooled screw compressors.
- Replacement of raw material grinding with dry grinding roller press.
- Replacement of old underground pipelines with new overhead pipelines.
- Repaired / replaced old water storage tanks and pipelines to arrest the leakages.
- Replaced ball valves with push type taps to reduce leakage.
- Laid pipeline to lift rainwater collected in mines pits to reduce use of ground water consumption in plants.
- Treatment of sewage water for utilisation in plantation.
- Use of RO and water treatment reject water in mill spray.
- Use of city sewage water for plantation. Recently, we started to develop a 50 ha Biodiversity Park in our Ahirpura Limestone Mine at Nimbahera Chittorgarh Rajasthan to improve the ecological footprints of quarry and to develop safe/secure habitat for local flora and fauna.
- Installation of drip irrigation system for effective use of water in plantation.
- Concreting roads, covered storage and vacuum sweeping to reduce the water consumption in dust suppression generated due to transportation.
- Switching towards renewable energy in place of fossil fuel based CPP, which consumes water.
- Commissioned a high-speed overland belt conveyor for replacement of fleet to transport limestone from mines to plant and saved the water which was being sprayed on road.
- Installed dry fog system at crusher unloading point and fully automated mist system for maintaining dust free haul.
In FY 2022, we have achieved water positivity as 4.6 times and further we are working with CII for feasibility beyond the fence to enhance our
water positivity.
Tell us about the norms followed by your organisation for conservation of water.
Water conservation has been at the forefront of our sustainability journey. Being a global member of the GCCA we follow the best practices and sustainable interventions being implemented by the member companies globally. The major cement production units are located in water scarcity regions. We have a social obligation and business goal in managing our water impact in a responsible way.
We have framed water policy keeping in view the central and state government rules and guidelines, best practices being adopted by the peers, benchmarking, local water scenario and social need and we follow it completely.
In our water management, we have set up a water management cell to monitor (physical and remote), review, implement latest water efficient technology, conduct awareness programmes, and communicate for withdrawal and judicious consumption of water. By implementing the best water practices and water efficient technologies, we have reduced specific water consumption from 0.162 to 0.137 KL/T of cementitious material (cement plant, power generation, mining and domestic).
Has your organisation achieved many milestones with respect to water positivity?
JK Cement works continuously towards limiting our water usage and improving water recharge as well as raising awareness among our stakeholders about its optimal use. All our manufacturing facilities are zero-water discharges that treat and reuse
all domestic and industrial wastewater generated on-site.
We have reached a water positivity of 4.6 times in FY2022 from 3.2 in FY2020 by investing in water efficient technologies and working to meet the SDG goal of 5 times water positive by FY2030.
How do communities surrounding your plant contribute towards your water footprint?
JK Cement Limited is continuously limiting water usage and improving the water recharge reserves. We are also raising awareness about water conservation in the surrounding communities. In our beyond the fence endeavours to improve the water positivity, we are working with CII to improve the nearby community water aquifer with the help of nearby residents. We have constructed a water pond in nearby village Karunda in Chittorgarh, which is filled with our mine water and is used for domestic purposes and to recharge the nearby water aquifers.
How do you measure water positivity and what are the ideal benchmarks?
JK Cement follows the guidelines of Central Ground Water Authority, Government of India to calculate recharge quantum, and thereafter water positivity is calculated as per the GCCA, India water positivity tool (Debit/Credit) policy. Presently JKCL has reached a water positivity of 4.6 times in FY22.
We have implemented measures based on the impact analysis of the LCA study, which include the minimal water consumption in cement manufacturing process and maintaining ZLD. Our approach to minimising the use of natural resources and reduction of impact on the environment has been acknowledged and our blended grey cement has been certified with the prestigious CII GreenPro Ecolabel certificate in FY2022.
Tell us about the major challenges your organisation faces with water consumption and optimum utilisation.
Water management has recently undergone a paradigm shift in our cement businesses as water scarcity is increasingly becoming a major concern because most of our operations are in dry, water-scarce areas. We work continuously towards limiting our water usage and improving our water recharge as well as raising awareness among our stakeholders about its optimal use. All our manufacturing facilities are zero-water discharge plants that treat and reuse all domestic and industrial wastewater generated on-site.
How do you foresee your organisation in terms of achieving water positivity and further optimising its consumption?
JK Cement understands its responsibility towards the environment and minimising consumption of resources. Water positivity reduces the business risk, improves the social relations and makes the business sustainable. Currently we are 4.6 times water positive and our target is to become 5 times water positive by 2030. As we increase water positivity, we make our operations water efficient and produce more cement with less water. Water positivity also increases the water availability for the society, so as our productivity increases, nearby communities do not get harmed, rather, farm productivity increases and such efforts bring happiness in their lives.
In the end, I take pride in telling our stakeholders that JK Cement is 4.6 times water positive, working to increase 5 times water positivity, maintaining all the operations with dry process and operating highly water efficient plants, recycling and reusing 100 per cent of wastewater and implementing the aquifer recharge system to increase the water availability for the community, which is helping to increase prosperity among the society.
-Kanika Mathur
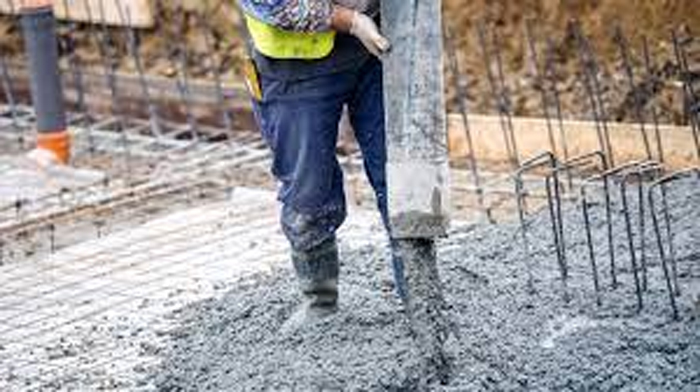
Tamil Nadu is set to host one of India’s five national carbon capture and utilisation (CCU) testbeds, aimed at reducing CO2 emissions in the cement industry as part of the country’s 2070 net-zero goal, as per a news report. The facility will be based at UltraTech Cement’s Reddipalayam plant in Ariyalur, supported by IIT Madras and BITS Pilani. Backed by the Department of Science and Technology (DST), the project will pilot an oxygen-enriched kiln capable of capturing up to two tonnes of CO2 per day for conversion into concrete products. Additional testbeds are planned in Rajasthan, Odisha, and Andhra Pradesh, involving companies like JK Cement and Dalmia Cement. Union Minister Jitendra Singh confirmed that funding approvals are underway, with full implementation expected in 2025.
Image source:https://www.heavyequipmentguide.ca/
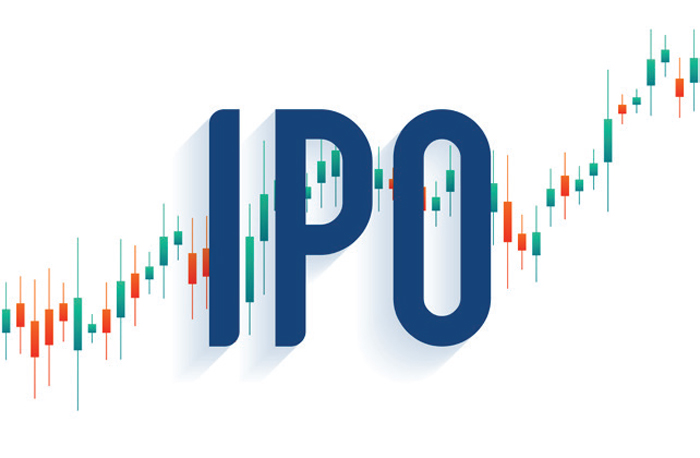
JSW Cement has set the price range for its upcoming initial public offering(IPO) at US$1.58 to US$1.67 per share, aiming to raise approximately US$409 million. As reported in the news, around US$91 million from the proceeds will be directed towards partially financing a new integrated cement plant in Nagaur, Rajasthan. Additionally, the company plans to utilise US$59.2 million to repay or prepay existing debts. The remaining capital will be allocated for general corporate purposes.
Concrete
Cement industry to gain from new infrastructure spending
Published
1 month agoon
July 24, 2025By
admin
As per a news report, Karan Adani, ACC Chair, has said that he expects the cement industry to benefit from the an anticipated US$2.2tn in new public infrastructure spending between 2025 and 2030. In a statement he said that ACC has crossed the 100Mt/yr cement capacity milestone in April 2025, propelling the company to get closer to its ambitious 140Mt/yr target by the 2028 financial year. The company’s capacity corresponds to 15 per cent of an all-India installed capacity of 686Mt/yr.
Image source:https://cementplantsupplier.com/cement-manufacturing/emerging-trends-in-cement-manufacturing-technology/