Concrete
How Energy-Efficient Are We?
Published
3 years agoon
By
admin
As the cement sector moves towards a sustainable future, energy conservation takes centrestage. ICR looks at the efforts taken and challenges faced in achieving energy-efficient manufacturing processes
The power or energy generation in India is shared between national public utilities (around 40 per cent), state utilities and private companies (around 30 per cent each). This management sector of energy is split between several ministries: the Ministry of Power (MoP) for electricity and the coordination of energy conservation programmes; the Ministry of Petroleum and Natural Gas (MoPNG); the Ministry of Coal; and, finally, the Ministry of New and Renewable Energy (MNRE).
According to the India Energy Report, 2021 by Enerdata, the total energy consumption per capita remained around 0.7 tonne of oil equivalent (toe) in 2021, which was about half of the Asian average consumption. Electricity consumption per capita reached 970 kWh in 2021, about a third of the Asian average. Total energy consumption reached 927 Mtoe in 2021 (+4.7 per cent), which was still 1.2 per cent below the 2019 level. It had increased rapidly over 2010-2019 (4 per cent per year). Coal is the country›s top energy source with a share of 44 per cent in 2021, followed by oil (24 per cent) and biomass (22 per cent). Natural gas covered 6 per cent and primary electricity (hydro, nuclear, solar, and wind) was at 4 per cent.
The energy sector aims to achieve an ambitious target of 450 GW of solar and wind in 2030 as it has pledged to reach carbon neutrality by 2070. What makes this target seem achievable is that the renewable capacity of the Indian energy sector (excluding large hydro) overtook 100 GW in 2021. While three quarters of the energy requirement is still met by fossil fuels, the overall consumption of energy has gone down by 5 per cent in 2021.
Cement plays a vital role in building the economy of a nation. The sector is largely dominated by players with large manufacturing capacities, making the cement industry one of the largest in the country and one that is energy intensive.
The Perform Achieve and Trade (PAT) scheme of the Ministry of Power, Government of India has so far covered 126 numbers of cement plants in India targeting to reduce specific energy consumption since its inception from 2012 onwards.

The Bureau of Energy Efficiency states that based on the threshold defined, 85 numbers of cement plants were included as DCs and their cumulative energy consumption was 15.01 million MTOE in PAT Cycle-1. Based on their specific energy consumption level, these DCs were given SEC target reduction of an average 5.43 per cent resulting in 0.815 million TOE energy consumption reduction in absolute terms. The cement sector constituted 12.19 per cent of the overall energy saving target under PAT Cycle-1.
The total savings achieved by the cement sector covering 75 numbers of designated consumers in PAT Cycle-1 is 1.48 million MTOE which is 0.665 million MTOE in excess of the target. At present, the energy consumption of these cement units as designated consumers is 23.246 million tonnes of oil equivalent. The target given for them from PAT Cycle –II onwards is 0.94 million tonnes of oil equivalent.
The cement sector is highly energy-intensive, consuming approximately 7 per cent of global industrial energy consumption each year. The manufacturing process is carried out in stages. From grinding of raw material in raw mill grinders, to pyroprocessing and clinkerisation and then grinding of clinker in roller press mills, vertical mills, balls mills etc., to obtain the final product, cement. Each stage consumes a significant amount of energy and organisations are constantly looking at solutions, technology, automation and better equipment to optimise the quantum of energy consumed in the process.
Pictorial depiction of cement manufacturing process.
Given the significant impact that the manufacturing industry has on global sustainability and considering the increasing economic pressure introduced by a competitive market and the reduction of available energy resources, optimising the energy efficiency of production systems has become a primary concern.
According to the Technological Energy Efficiency Improvements in Cement Industries Report, 2021 published at MDPI, energy consumption in the cement industry is provided by electricity and fuels.
Over 90 per cent of fuels used are consumed in the production of clinker. Electric energy, on the other hand, is used for about 39 per cent for the finishing process, for around 28 per cent for both processing the raw materials and burning the clinker, and for less than 5 per cent for other operations.
“An area where energy is majorly consumed is the grinding stage of cement manufacturing. Here is where there is a large scope of reduction of the same. The industry has worked upon the same and come up with solutions to make that happen. At one point of time, cement grinding used to take up to 50 units to 60 units of power. With the new, energy efficient mills we are able to grind clinker while using 20 units to 25 units of energy and this is a major benefit that the industry has been able to derive of the vertical roller mills or the pre-pressed grinding mills,” says Jamshed Cooper, Managing Director, HeidelbergCement India Ltd. and Zuari Cement Ltd.
“With the use of EFR and alternative fuels also the industry can save on energy. These are not directly energy efficient. Yes, the quantum of heat generation requirement for the clinkerisation process will be the same, but that can be substituted with alternative sources. Also, recycling the waste heat with the Waste Heat Recovery (WHR) unit is also a great way to save energy and use it for further processes,” he adds.

Automation and Technology
The world is moving towards digitalisation. From switching on your home lights to a manufacturing unit, the controls are moving from human to digital across the board. Technological advancement in the area of cement manufacturing has led to a lot of advancement in its functioning and has led towards achieving the goal of energy conservation by reducing its usage in the operations.
“The role of automation in the cement industry is very high. If we look back, the cement plants in the later part of 1970 or early 1980s used to have local substations or local control systems. But today with automation, plants are operated and controlled from a single location (CCR). The control room operator can see the entire plant operation from a single monitor. Functions like start or stop, alarms, process interlocks etc., are major benefits of automation that a cement plant experiences” says Kiran Patil, Managing Director, Wonder Cement.
“Furthermore, industries have used robotics in the plant, and Wonder Cement is one of the cement plants to have robotics for quality control. In this digital world, we cannot be behind and so, we are working towards the implementation of digitalisation in operation and maintenance to get better efficiency” he adds.
The cement industry is realising the importance of process control and automation to achieve their goals of energy efficiency and for a trouble free continuous operation leading to improved productivity at optimal energy levels. Automation also takes care of optimal operation in mining and hence longer life of mines and consistent desired cement quality is assured. Instrumentation and control logic can also be used effectively for taking care of human and equipment safety and to monitor equipment health and implement preventive maintenance in the manufacturing facility.
Organisations are continuously analysing and seeking advanced technical equipment that help streamline their processes and align them with the goals of achieving a similar or higher productivity level with a lower amount of energy input. This not only saves on their costs and enhances profitability for the organisation but also helps achieve their sustainability targets by reducing direct or indirect emissions caused by the cement manufacturing unit’s energy requirement.
While the input of energy is optimised by technology and automation, audits support the need of constant monitoring of the performance of the units individually as well as on a group level. A dedicated professional, certified in the area of energy consumption is stationed at every unit with the key goal of monitoring everyday consumption. Audits play a key role in achieving this goal.
Energy management bodies like Centre for Mining, Environment, Plant Engineering and Operations (CME), under the National Council for Cement and Building Materials (NCCBM), run programmes that offer technical services related to Energy Audits and WHR feasibility studies to cement plants of India.
Their services include energy audit studies in cement plants including captive power plants, management, monitoring and target setting, heat and gas balance studies, identification of potential for thermal and electrical energy savings and recommendations for remedial measures and Techno economic feasibility studies for waste heat recovery system (WHRS) in cement plants.
These audits are conducted by means of site visits and data collection, preliminary data analysis and detailed data analysis. Post which a detailed report and recommendations on economic viability is presented to the organisation in audit.
Hitesh Sukhwal, Dy General Manager – Environment, Udaipur Cement Works, says, “Our company is covered under PAT scheme. We are an ISO 50001 certified company under energy management. We have a dedicated resource under the designation of ‘energy manager,’ who is qualified to keep a check on the energy consumption of the plant and continuously optimise the same.” A periodic energy audit (once in three years) as per EC Act is done. Half yearly internal audits and external audits once a year are performed under energy management. Moreover, power monitoring reports are discussed on an everyday basis during the desktop production meeting” he adds.
Many cement producers have lowered energy costs up to 20 per cent by adopting a holistic approach to industrial energy management. The Petroleum Conservation Research Association lists some key areas where cement manufacturing units can work upon for having a more energy efficient plant:
Use improved insulating bricks/blocks in kilns and preheaters.Use energy efficient equipment like high efficiency fans, improved ball mill internals etc.
- Recover waste heat from the preheater and use it for cogeneration of power.
- Prevent idle running of equipment by providing The interlocking arrangement and operating with PLC system. Generate daily reports on idle running of equipment, also in terms of monetary losses.
- Optimise the fuel mix and raw mix by including alternative fuels and supplementary cementitious materials.
- Establish an efficient management information system for identifying various important parameters for efficient operation of the equipment and taking timely remedial measures.
- Regularly monitor and calibrate flow metres.
Carry out regular audits.
Other areas that it focuses on apart from the main manufacturing process are the various overheads and other operations where energy is consumed in smaller quantities but when clubbed together can be a large value of consumption.

“The cement industry affects climate change as it contributes 7 per cent to 8 per cent to the global carbon pool. To curtail this, stakeholders that include members of the United Nations Principal of Responsible Investment and such have begun to reach out to cement industry players across the globe to come up with solutions to cut down on CO2 emissions to see investments flow in.” says Dr Arvind Bodhankar, Executive Director, ESG & CRO, Dalmia Bharat Limited.
“Dalmia Bharat are leading the pack with commitments that encourage the circular economy. Global visionaries such as our honourable Prime Minister, Narendra Modi, have also stated that India will become a carbon-neutral country by 2070 and committed to 520 GW of renewable energy by 2030.
This has helped ease new policies as far as renewable energy is concerned and enabled sector leaders such as us to stay the course to meet our goal of becoming carbon negative by 2040,” he adds.
Alternative sources of energy like solar power plants and Waste Heat Recovery (WHR) are also a key in achieving energy efficiency and sustainability goals for every cement organisation. UltraTech has imbibed Sustainable Development Goals (SDGs) as a business objective and is working towards reducing its energy consumption and carbon emissions. It was one of the first in the Indian cement industry to embrace the technology of WHRS. Waste heat recovery has proved to be an inexpensive energy source in addition to moderating the carbon footprint.
This has enhanced energy security (accounting for 20 per cent of power needs) for the company. UltraTech Cement has an aggregate capacity of about 59 MW in waste heat recovery systems.
In a report published at SAUR Energy International, May 2022, a major issue in the cement industry is the very high particulate matter (PM) emissions from production processes. The pollutants commonly emitted by cement plants are dust or particulate matter, NOx, SOx, carbon oxides and methane and others. Energy consumption is also an issue, with the approximate required per tonne of cement, roughly two thirds of which is used for particle size reduction.
About 65 per cent of the total electrical energy used in a cement plant is utilised for the grinding of coal, raw materials and clinker.
Some of the key players are adaption to alternative sources of energy. Ultratech Cement has a power generation capacity of 156 MW through waste heat recovery systems. The waste heat recovery capacity is expected to reach 302 MW by FY2024. In the area of renewable energy, the firm professes plans to invest in solar power generation for captive usage.
This is in addition to existing contract capacity of 148 MW renewable energy plants. UltraTech is committed to increase the share of green energy in its electricity mix to 34 per cent by 2024 from the current level of 13 per cent.
Utilising its waste heat recovery plants, and solar and wind power plants, Shree Cement boasts a renewable energy portfolio of over 234 MW. Consequently, during FY 2019-20, 45 per cent of the total energy needs of the company was fulfilled by renewable energy. The firm has a 62 kW Solar PV Power Plant at Beawar.
In 2021, Ambuja Cement and ACC announced investments in Waste Heat Recovery Systems (WHRS) across six sites in India to reduce 5.61 lakhs tons of CO2 emissions per year. ACC committed to reducing scope 1 GHG emissions by 21.3 per cent per tonne of cementitious material and scope 2 GHG emissions by 21.3 per cent per tonne of cementitious material by 2030.
Dalmia Bharat’s carbon footprint is 40 per cent lower than the global average for a cement company which places it at the top, globally in the race of decarbonising the cement sector. Dalmia Cement has been progressively producing cement with ‘greener’ alternatives.
Energy is key to the cement sector, however, the time has come to re-look at the conventional sources and to tap into the more readily available alternative sources of energy. With advancement of technology and automation across the globe, there are various equipment and machinery that make these alternative sources more effective and affordable for the cement manufacturers. It is a conscious choice that the industry shall have to make to safeguard the environment for the future generations to come in terms of availability of energy sources and the quality of surroundings they leave behind.
You may like
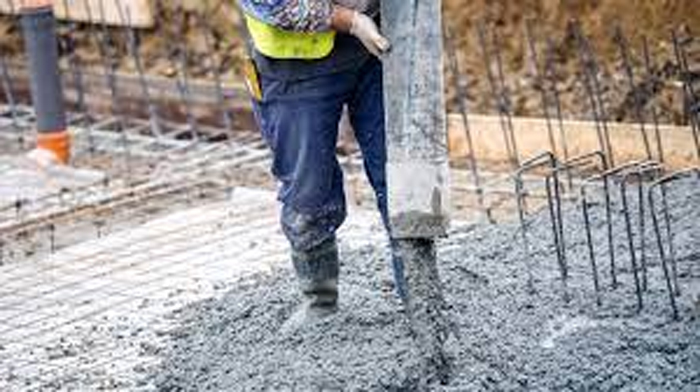
Tamil Nadu is set to host one of India’s five national carbon capture and utilisation (CCU) testbeds, aimed at reducing CO2 emissions in the cement industry as part of the country’s 2070 net-zero goal, as per a news report. The facility will be based at UltraTech Cement’s Reddipalayam plant in Ariyalur, supported by IIT Madras and BITS Pilani. Backed by the Department of Science and Technology (DST), the project will pilot an oxygen-enriched kiln capable of capturing up to two tonnes of CO2 per day for conversion into concrete products. Additional testbeds are planned in Rajasthan, Odisha, and Andhra Pradesh, involving companies like JK Cement and Dalmia Cement. Union Minister Jitendra Singh confirmed that funding approvals are underway, with full implementation expected in 2025.
Image source:https://www.heavyequipmentguide.ca/
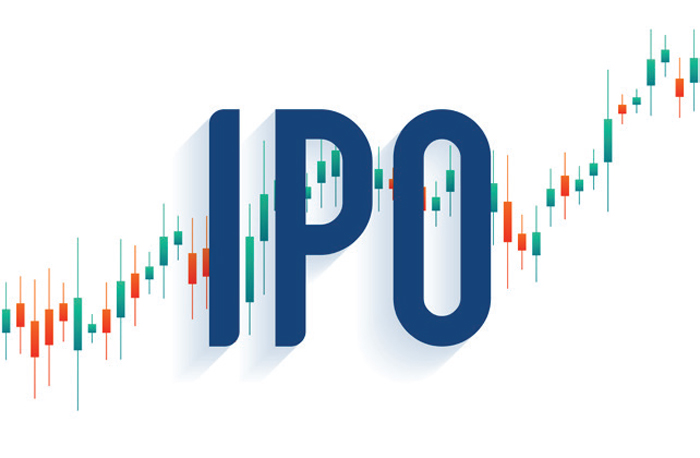
JSW Cement has set the price range for its upcoming initial public offering(IPO) at US$1.58 to US$1.67 per share, aiming to raise approximately US$409 million. As reported in the news, around US$91 million from the proceeds will be directed towards partially financing a new integrated cement plant in Nagaur, Rajasthan. Additionally, the company plans to utilise US$59.2 million to repay or prepay existing debts. The remaining capital will be allocated for general corporate purposes.
Concrete
Cement industry to gain from new infrastructure spending
Published
1 month agoon
July 24, 2025By
admin
As per a news report, Karan Adani, ACC Chair, has said that he expects the cement industry to benefit from the an anticipated US$2.2tn in new public infrastructure spending between 2025 and 2030. In a statement he said that ACC has crossed the 100Mt/yr cement capacity milestone in April 2025, propelling the company to get closer to its ambitious 140Mt/yr target by the 2028 financial year. The company’s capacity corresponds to 15 per cent of an all-India installed capacity of 686Mt/yr.
Image source:https://cementplantsupplier.com/cement-manufacturing/emerging-trends-in-cement-manufacturing-technology/