Environment
We challenge conventional packaging for a sustainable future.
Published
4 years agoon
By
admin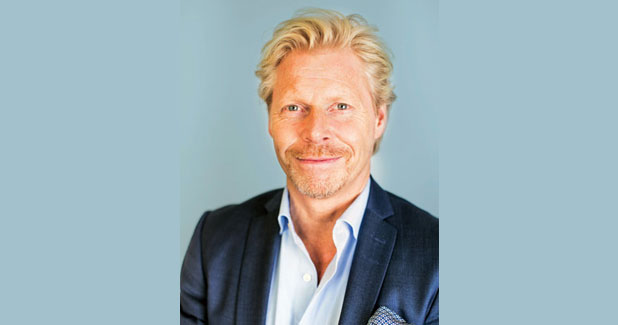
Johan Nellbeck, Senior Vice President Packaging Paper, BillerudKorsn?s AB
Worldwide trend is to use paper bags for packing cement. However in India it is the other way. BillerudKorsn?s AB one of the largest suppliers of sack paper has entered India and trying it?s hand on cement sector. ICR is in conversation with Johan Nellbeck, ?enior Vice President Packaging Paper, BillerudKorsn?s AB
Introduce your company and speak about its Indian operations for our readers. Give us an idea of your product portfolio…..
BillerudKorsn?s is one of the world?s leading suppliers of high-quality packaging materials that are made from the high strength, long fibres of Scandinavian trees. Our raw material – wood, comes from sustainably managed forests and our manufacturing processes are resource-efficient.
The manufacture of pulp, paper and board takes place at BillerudKorsn?s? eight production units in Sweden, Finland and the UK. Our five units in Sweden are integrated mills and all the eight units in ?weden, Finland and UK hold quality and environmental certification.
We have been servicing the Indian market for some time now; we realise the potential of the Indian market and offer the best product with high level of service to this market. We now have a representative office in India, so that we are with the customers whenever they need us.
Give us a brief on your product ?Sack Paper? for the cement industry. In what colors is it available?
Our sack papers are produced from high quality northern pine trees, the fibre from these trees gives our paper a superior quality and high strength. The production process adds to the porosity of the paper and as a result what we have is a high strength with high porosity paper, most suitable for powdered products and especially cement. The filling is efficient, clean and dust free.
Our sack paper is available in white (bleached) and brown. The paper can have full body printing and so it can serve the Indian market well. In India cement sacks are generally coloured, bright colours like yellow/green and so on. Good branding on white paper sacks will make the brand stand out.
HDPE or LDPE are all plastics, these sacks have micro pores, which leads to cement loss and pilferage. Also these plastics sacks are neither biodegradable nor environmentally friendly.
Which are the most important properties of a paper sack? How do these compare with sacks made with other materials (Laminated bags or HDPF, LDPE bags)?
The most important property of paper for cement sacks is high strength with high porosity. Due to porosity, while filling deaeration happens on its own and therefore no perforations are required. Since the sacks have no perforations the strength of the kraft paper remains intact.
Woven and laminated sacks have an open structure or are perforated, allowing large amounts of cement to escape; we?ve measured up to 300 gm per sack. This cement wastage costs money, damages the environment and the health of workers and customers. If one calculates this loss for the whole Indian cement industry, using cement production of 280 million tonnes, 80 per cent sack use and $100 per tonne, one arrives at the astounding loss of 1.5 million tonnes of cement, $150 million in turnover and additional carbon footprint of one million tonnes of CO2.
When compared to LDPE/HDPE, in paper bags, there is no wastage while filling, no pilferage during logistics, clean working and handling for the workers. Besides this it brings value to the brand – the brand is visible on the sacks, its clean, dust free and environment friendly. Paper degrades in soil in less than three months As a caution we suggest that hooks should be avoided for loading and unloading.
Does the user of these sacks require controlled humidity and temperature for storage of paper? Does it have limited shelf life?
Both the paper and the paper sacks, well packaged, can be stored in normal warehouses without the need for a controlled atmosphere. The shelf life of cement in paper sacks is adequate for the value chain; however, we recommend proper stock management to ensure sack performance and to minimise storage costs and working capital.
What are your strategies for popularising paper sacks in India since it is a very minor share of the market at present?
Paper sacks made of strong, high-porous paper like QuickFill, are the preferred, cost-efficient choice of cement companies in many Asian countries such as Indonesia, Thailand, Malaysia and the Philippines. We believe that producers of cement in India are very interested in switching to clean and strong paper sacks but are held back by their cost focus paradigm. They know that paper sacks create value by solving the problems of plastic pollution, cement waste, health hazards and poor branding due to the dusting of WPP sacks. Our strategy is to shift this paradigm to a "value" focus approach by creating awareness of the lost value.
We support these efforts by sharing success from other markets, offering pilot projects with full project management and, most importantly, supporting the projects with continuous and competent technical support. The activities mostly start with one-on-one consultations with cement producers and we guarantee confidentiality should a company require this. In India, we are working closely with a few cement brand owners, and Ms Madhvi, India representative for sack solution, is taking the projects forward.
Branding is also a very important part of this initiative so we have branded the product Quickfill Clean – "Quickfill" due to the high performance of the packaging and "Clean" due to the dustless nature of the sack. The "Clean" clearly communicates the elimination of cement losses and damage to nature and health.
Share with our readers a few success stories on packing of cement for brand enhancement and as a solution provider for reducing dust emission.
QuickFill sacks with a strong white QuickFill as outer ply is used by producers wishing to enhance their branding and at the same time offer their customers clean, dust free product with an appealing presentation. Cement companies in Russia, South Africa and China are among those having made this choice. We share our success stories on our website but only if given permission by the brand owner. Readers should visit our website: http://www.billerudkorsnas.com/Our-Offer/?olution-Services/?ack-?olutions/ Our most recent success story is one in South Africa where Sephaku switched their outer ply to white paper in order to differentiate themselves from their competitors. The new construction which also contained an extra high porous paper in the inner ply to solve filling problems related to high ash content, has resulted in increased brand recognition, assisting the company in achieving their sales and marketing goals.
Recently in Vietnam, a company ordered the first commercial volumes of QuickFill Clean sacks to replace WPP-based sacks. The company is fully satisfied with the performance of the Quickfill Clean sacks and is switching to paper for branding and differentiation purposes. They also like the much improved product presentation and better friction properties which provide stable and safer stacking of cement sacks. In India we currently have three projects running which are progressing very well.
On the commercial side, how do the costs of a paper and plastic sack compare?
When comparing the unit cost of a QuickFill Clean paper sack and a WPP plastic sack, the paper sack is usually higher in price. But then, so is its value! When making a total cost analysis, including the high loss of cement, higher maintenance costs, costs of pilferage, revenue loss and reduced goodwill due to poor image and pollution, then the paper sack is clearly the logical and economical choice.
Two aspects which are difficult to quantify are damage to the health of people exposed to the cement dust and the damage to the environment. Given the state of our planet and the clear and present danger of global warming, cement producers have a moral responsibility to take this into account and must make every effort to eliminate this unnecessary extravagance.
Give us some information on WWF Environmental Paper Company Index 2015 (EPCI). What has been your performance on the Paper Company Index? What is your road ahead?
I was very pleased that we were recognized by WWF this autumn for leadership in transparency, which is in how we disclose our ecological footprint in the WWF Environmental Paper Company Index 2015 (EPCI). Transparency for us is an important tool for promoting sustainability in the value chain. It is also a tool in providing stakeholders information for their evaluation of the company?s performance. We scored 78 per cent for transparency as shown by reporting and environmental management systems. In the product category – Packaging, BillerudKorsn?s achieved 70.6 per cent, which is an improvement compared to the last survey. The company was especially acknowledged for the substantial decrease in greenhouse gas emissions.
What is your take on COP21?
It was very pleasing to see the world?s leaders come to a new, ambitious global climate agreement in Paris. Our contribution to reaching these goals will be participation in the Swedish government?s climate initiative, "Fossil Free Sweden", with the aim of achieving a fossil-free society. We have been pursuing a reduction in fossil fuels for many years now, resulting in a fossil fuel consumption of only 2.6 per cent in 2015. Within the scope of Science Based Targets, we have taken the definitive step of developing new, scientifically based climate goals of our own. Replacing fossil based packaging with renewable fibre-based materials is part of the solution and we will play a part in stepping up the pace of this much-needed transition in the global society.
Tell us about some innovations you have been carrying out in other product categories? Where is the industry heading?
If we can stay in the paper sack industry for a moment, I?m very proud to tell you about our latest development, the disappearing sack or D-Sack?. We developed this innovation together with LafargeHolcim in France. This cement sack performs the same as a normal paper cement sack, but has the amazing ability to disintegrate completely in the cement mixer and to integrate itself with the cement or mortar without any detrimental effect on the properties of the cement or mortar! One simply puts the whole cement sack into the mixer and it is gone – we like to think of it as the perfect packaging – packaging which disappears on use!
BillerudKorsn?s? mission is to challenge conventional packaging for a sustainable future in all our product categories. Renewable, recyclable and compostable wood fibre-based packaging can successfully substitute a lot of fossil-based plastic packaging. We have for example developed FibreForm, a paper which is possible to shape and form to replace for example plastic clam-shells, trays and other 3-dimensional packaging. Another initiative BillerudKorsn?s has taken is to develop a paper bottle meeting the demands of carbonated drinks.
People believe that using paper causes deforestation; could you give us some facts on this?
This is a huge misconception. Deforestation is mostly caused by farmers clearing land to produce food for the world?s ever growing population. The legislation governing the management of forests in Sweden is very strict and was promulgated in the early 1800?s when the people understood that resources must be managed on a sustainable basis. One important law requires foresters to replace every felled tree with three to four new ones. As a result, the forests in Sweden are growing, both in the amount of wood and in surface area. It is important to understand that these forests bind carbon as they grow, reducing carbon dioxide and releasing oxygen which we humans breathe. We like to call them the earth?s lungs, which is why we look after them so carefully.
We go to great lengths to ensure that all our papers are made from sustainably managed forests. Another great advantage of paper based packaging is that paper disintegrates in few months, whereas plastic lasts basically forever, polluting the earth, causing catastrophes such as floods and ending up in our oceans, our food chain and eventually our children. Paper is definitely environment friendly.
You may like
-
Who’s gonna bag it
-
India cement industry bosses expect to import more high-sulphur petcoke Sudarshan Varadhan
-
Dalmia Bharat Q4 profit jumps over 2-fold to Rs 264 cr
-
Top level changes at Refratechnik Cement
-
Kerala govt may expedite award of teminal project
-
Jagdish Jaiswal, Owner, Titan Ceramic and Cement Centre (TC&CC)
Concrete
India donates 225t of cement for Myanmar earthquake relief
Published
3 months agoon
June 17, 2025By
admin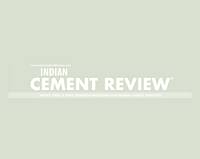
On 23 May 2025, the Indian Navy ship UMS Myitkyina arrived at Thilawa (MITT) port carrying 225 tonnes of cement provided by the Indian government to aid post-earthquake rebuilding efforts in Myanmar. As reported by the Global Light of Myanmar, a formal handover of 4500 50kg cement bags took place that afternoon. The Yangon Region authorities managed the loading of the cement onto trucks for distribution to the earthquake-affected zones.
Concrete
Reclamation of Used Oil for a Greener Future
Published
3 months agoon
June 16, 2025By
admin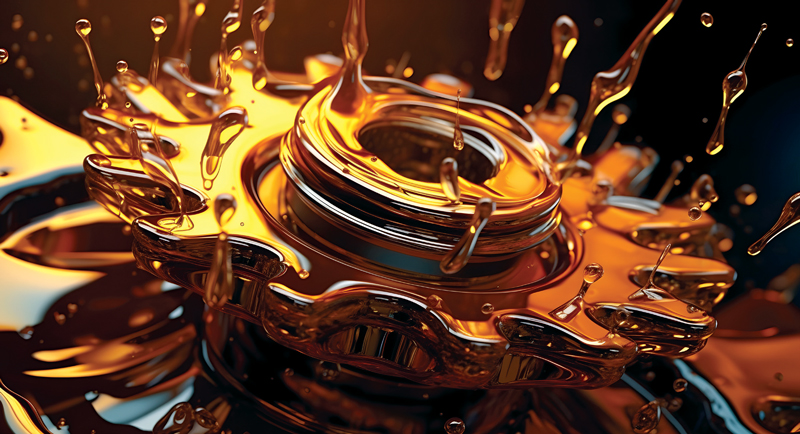
In this insightful article, KB Mathur, Founder and Director, Global Technical Services, explores how reclaiming used lubricants through advanced filtration and on-site testing can drive cost savings, enhance productivity, and support a greener industrial future. Read on to discover how oil regeneration is revolutionising sustainability in cement and core industries.
The core principle of the circular economy is to redefine the life cycle of materials and products. Unlike traditional linear models where waste from industrial production is dumped/discarded into the environment causing immense harm to the environment;the circular model seeks to keep materials literally in continuous circulation. This is achievedthrough processes cycle of reduction, regeneration, validating (testing) and reuse. Product once
validated as fit, this model ensures that products and materials are reintroduced into the production system, minimising waste. The result? Cleaner and greener manufacturing that fosters a more sustainable planet for future generations.
The current landscape of lubricants
Modern lubricants, typically derived from refined hydrocarbons, made from highly refined petroleum base stocks from crude oil. These play a critical role in maintaining the performance of machinery by reducing friction, enabling smooth operation, preventing damage and wear. However, most of these lubricants; derived from finite petroleum resources pose an environmental challenge once used and disposed of. As industries become increasingly conscious of their environmental impact, the paramount importance or focus is shifting towards reducing the carbon footprint and maximising the lifespan of lubricants; not just for environmental reasons but also to optimise operational costs.
During operations, lubricants often lose their efficacy and performance due to contamination and depletion of additives. When these oils reach their rejection limits (as they will now offer poor or bad lubrication) determined through laboratory testing, they are typically discarded contributing to environmental contamination and pollution.
But here lies an opportunity: Used lubricants can be regenerated and recharged, restoring them to their original performance level. This not only mitigates environmental pollution but also supports a circular economy by reducing waste and conserving resources.
Circular economy in lubricants
In the world of industrial machinery, lubricating oils while essential; are often misunderstood in terms of their life cycle. When oils are used in machinery, they don’t simply ‘DIE’. Instead, they become contaminated with moisture (water) and solid contaminants like dust, dirt, and wear debris. These contaminants degrade the oil’s effectiveness but do not render it completely unusable. Used lubricants can be regenerated via advanced filtration processes/systems and recharged with the use of performance enhancing additives hence restoring them. These oils are brought back to ‘As-New’ levels. This new fresher lubricating oil is formulated to carry out its specific job providing heightened lubrication and reliable performance of the assets with a view of improved machine condition. Hence, contributing to not just cost savings but leading to magnified productivity, and diminished environmental stress.
Save oil, save environment
At Global Technical Services (GTS), we specialise in the regeneration of hydraulic oils and gear oils used in plant operations. While we don’t recommend the regeneration of engine oils due to the complexity of contaminants and additives, our process ensures the continued utility of oils in other applications, offering both cost-saving and environmental benefits.
Regeneration process
Our regeneration plant employs state-of-the-art advanced contamination removal systems including fine and depth filters designed to remove dirt, wear particles, sludge, varnish, and water. Once contaminants are removed, the oil undergoes comprehensive testing to assess its physico-chemical properties and contamination levels. The test results indicate the status of the regenerated oil as compared to the fresh oil.
Depending upon the status the oil is further supplemented with high performance additives to bring it back to the desired specifications, under the guidance of an experienced lubrication technologist.
Contamination Removal ? Testing ? Additive Addition
(to be determined after testing in oil test laboratory)
The steps involved in this process are as follows:
1. Contamination removal: Using advanced filtration techniques to remove contaminants.
2. Testing: Assessing the oil’s properties to determine if it meets the required performance standards.
3. Additive addition: Based on testing results, performance-enhancing additives are added to restore the oil’s original characteristics.
On-site oil testing laboratories
The used oil from the machine passes through 5th generation fine filtration to be reclaimed as ‘New Oil’ and fit to use as per stringent industry standards.
To effectively implement circular economy principles in oil reclamation from used oil, establishing an on-site oil testing laboratory is crucial at any large plants or sites. Scientific testing methods ensure that regenerated oil meets the specifications required for optimal machine performance, making it suitable for reuse as ‘New Oil’ (within specified tolerances). Hence, it can be reused safely by reintroducing it in the machines.
The key parameters to be tested for regenerated hydraulic, gear and transmission oils (except Engine oils) include both physical and chemical characteristics of the lubricant:
- Kinematic Viscosity
- Flash Point
- Total Acid Number
- Moisture / Water Content
- Oil Cleanliness
- Elemental Analysis (Particulates, Additives and Contaminants)
- Insoluble
The presence of an on-site laboratory is essential for making quick decisions; ensuring that test reports are available within 36 to 48 hours and this prevents potential mechanical issues/ failures from arising due to poor lubrication. This symbiotic and cyclic process helps not only reduce waste and conserve oil, but also contributes in achieving cost savings and playing a big role in green economy.
Conclusion
The future of industrial operations depends on sustainability, and reclaiming used lubricating oils plays a critical role in this transformation. Through 5th Generation Filtration processes, lubricants can be regenerated and restored to their original levels, contributing to both environmental preservation and economic efficiency.
What would happen if we didn’t recycle our lubricants? Let’s review the quadruple impacts as mentioned below:
1. Oil Conservation and Environmental Impact: Used lubricating oils after usage are normally burnt or sold to a vendor which can be misused leading to pollution. Regenerating oils rather than discarding prevents unnecessary waste and reduces the environmental footprint of the industry. It helps save invaluable resources, aligning with the principles of sustainability and the circular economy. All lubricating oils (except engine oils) can be regenerated and brought to the level of ‘As New Oils’.
2. Cost Reduction Impact: By extending the life of lubricants, industries can significantly cut down on operating costs associated with frequent oil changes, leading to considerable savings over time. Lubricating oils are expensive and saving of lubricants by the process of regeneration will overall be a game changer and highly economical to the core industries.
3. Timely Decisions Impact: Having an oil testing laboratory at site is of prime importance for getting test reports within 36 to 48 hours enabling quick decisions in critical matters that may
lead to complete shutdown of the invaluable asset/equipment.
4. Green Economy Impact: Oil Regeneration is a fundamental part of the green economy. Supporting industries in their efforts to reduce waste, conserve resources, and minimise pollution is ‘The Need of Our Times’.
About the author:
KB Mathur, Founder & Director, Global Technical Services, is a seasoned mechanical engineer with 56 years of experience in India’s oil industry and industrial reliability. He pioneered ‘Total Lubrication Management’ and has been serving the mining and cement sectors since 1999.
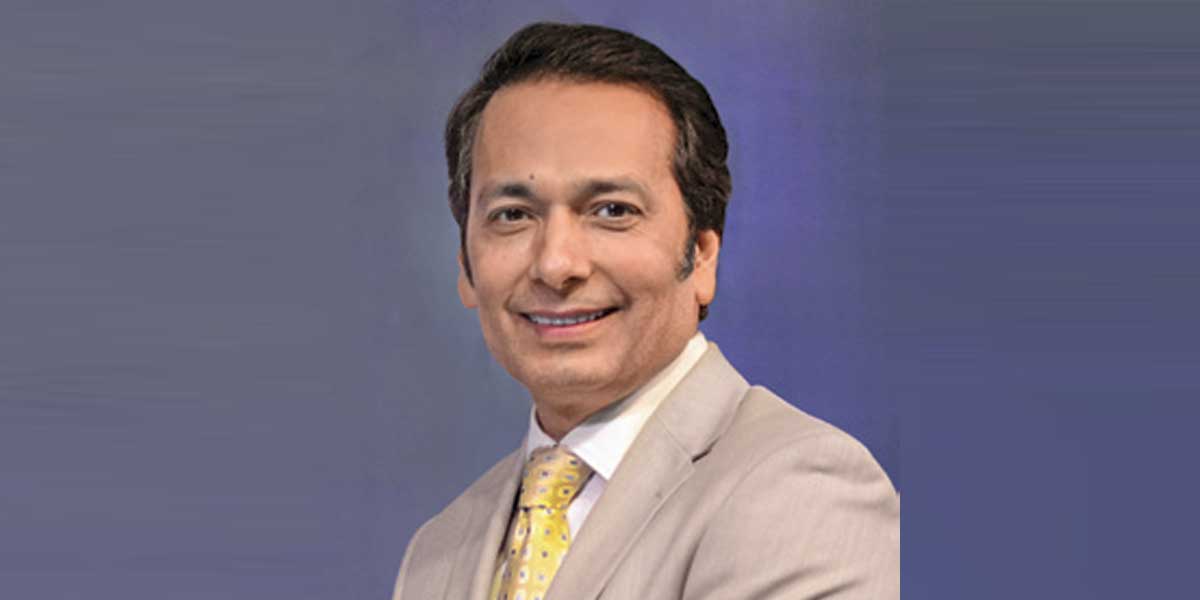
The Indian cement industry has reached a critical juncture in its sustainability journey. In a landmark move, the Ministry of Environment, Forest and Climate Change has, for the first time, announced greenhouse gas (GHG) emission intensity reduction targets for 282 entities, including 186 cement plants, under the Carbon Credit Trading Scheme, 2023. These targets, to be enforced starting FY2025-26, are aligned with India’s overarching ambition of achieving net zero emissions by 2070.
Cement manufacturing is intrinsically carbon-intensive, contributing to around 7 per cent of global GHG emissions, or approximately 3.8 billion tonnes annually. In India, the sector is responsible for 6 per cent of total emissions, underscoring its critical role in national climate mitigation strategies. This regulatory push, though long overdue, marks a significant shift towards accountability and structured decarbonisation.
However, the path to a greener cement sector is fraught with challenges—economic viability, regulatory ambiguity, and technical limitations continue to hinder the widespread adoption of sustainable alternatives. A major gap lies in the lack of a clear, India-specific definition for ‘green cement’, which is essential to establish standards and drive industry-wide transformation.
Despite these hurdles, the industry holds immense potential to emerge as a climate champion. Studies estimate that through targeted decarbonisation strategies—ranging from clinker substitution and alternative fuels to carbon capture and innovative product development—the sector could reduce emissions by 400 to 500 million metric tonnes by 2030.
Collaborations between key stakeholders and industry-wide awareness initiatives (such as Earth Day) are already fostering momentum. The responsibility now lies with producers, regulators and technology providers to fast-track innovation and investment.
The time to act is now. A sustainable cement industry is not only possible—it is imperative.