Environment
Over 1.5 billion people do not have access to safe water
Published
4 years agoon
By
admin
Bhaskar Bhattar, Director, Vexl Environ Projects Pvt Ltd
Water is rarely given the required attention in our country except when we face a drought situation. Bhaskar Bhattar, a water consultant, shares his views on the management of this critical commodity.
Tell us something about water which is generally not known to its users….
Water is a limited resource. Per capita availability of water is reducing at an alarming rate as the population is increasing and we humans are polluting our fresh /good water resources. Irrigation takes consumes over 90 per cent of the available water; water for human consumption is about 3-4 per cent and 5-6 per cent is the industrial water requirement. The water availability should be in excess of 2,000 cum/capita/annum for a province to be called a water-safe province. In India, at most places, we are in the range of 900-1,200 cum/capita/annum and are thus in a severe water scare province. Water efficiency has to be increased i.e., yield per drop of water has to be increased in all sectors and that is the only way ahead.
Almost 71 per cent of Earth is covered with water. The oceans hold about 96.5 per cent of all Earth?s water. Water also exists in the air in the form of vapour, in rivers and lakes, in icecaps and glaciers, in the ground as soil moisture and in aquifers, and even in our body. So we all have a misconception over why water is a scarce resource, when it is present in ample amount.
Around 97 per cent of the water on Earth is saltwater, which cannot be consumed directly without processing and only 3 per cent is fresh water; slightly over two-thirds of this is frozen in glaciers and polar ice caps. Only 0.3 per cent is available to us as surface water, which can be consumed directly. So considering this percentage, water becomes scarce though we have plenty of water on Earth.
Over 1.5 billion people do not have access to clean, safe water. Almost 4 million people die each year from water-related diseases.
What has been the general approach of our people towards water as a natural resource?
Natural resources again are limited resources and have to be used in an appropriate manner. Not only that, we cannot discharge or throw anything and everything into our water bodies. This could lead to their damage, making them unfit for human and other usage. We should protect our natural resources and also use them meaningfully. There are two major factors which give rivers their unique ability for holy water.
1. The presence of bacteriophages which gives the water its anti-bacterial nature. 2. An unusual ability to retain dissolved oxygen from the atmosphere.
Due to these two technical reasons, the water of the Ganges river is considered to be holy water. Further, every water body has self-cleansing properties. If any de-gradable pollutant is added to the water body, river, stream or lake, etc., the same will get decomposed over a period of time. The other aspect is the dilution owing to a large quantum of water, if available. In case the pollution load on the water bodies exceeds their self sustainable levels, the water bodies get polluted. If you observe, clean water bodies are getting contaminated owing to uncontrolled discharge of pollutants.
Water storage
Water is potable for weeks or months as long as it hasn?t been polluted by external sources like dirty fingers/hand or spit which is full of bacteria.
Very few pathogenic bacteria can survive in clean water. After a while they will simply die out, so stored water is safe.
What is water audit? How is it carried out?
A water audit is an accounting procedure. The purpose of a water audit is to accurately determine the amount of unaccounted water in a water distribution system.
Reasons for carrying out a water audit:
1. Understanding the water distribution process
2. Installing water meters for measurement of actual water consumed
3. Preparing water balance
4. Accounting for water losses
5. Taking steps to rectify the leakages
6. Verifying the water balance.
Water audits of residential and industrial areas are carried out differently, but the concept behind it is the same.
What is the concept of being ?water positive??
The basic concept of being water positive is using water efficiently and reducing water consumption, focussing on water conservation and recycling more and more water, and making rainwater harvesting mandatory for all citizens.
For instance, if a cement plants uses ?X? cum/day of raw water (from any available source like rivers, mines, municipal, etc.,) and shows that it is reusing treated wastewater of ?A? quantity and recharging rainwater of ?B? quantity, these two (A+B) are more than the water that they use (X) and they are thus water positive. The plant also concentrates on most optimal use of ?X?.
What are the highlights of the audit you carry out at cement plants in general?
- Installing water meters at raw water intake source and other distribution points
- Daily water balancing
- Quantifying the water per metric tonne of product
- Identifying and rectifying the water leakages
- Identifying underground water leaks
- Reduction in water consumption per tonne of product
- Efficient recycling of water
- Installation of automatic water-saving urinals
- Installation of water sensors in washbasins
- Reusing 100 per cent STP-treated water.
How sensitive is the cement industry about using water? Can you give some examples?
The cement industry is not a water-intensive industry as dry cement technology is used worldwide for manufacturing of cement. Water is used only in cooling towers for cooling of gearboxes and sprinkling on hot clinker for temperature reduction. Practically, for the cement industry, production is the prime focus of the plants, but water and wastewater issues become sensitive only when they directly affect production or legal compliances. Things are mostly attended to at the breakdown stages which leads to improper implementation and heavy investments which otherwise can be optimised by correct designing.
Is there any data available on how much of water is used by a million tonne cement plant?
Water is consumed in manufacturing of cement as per the approximate figures given below, based on a study done on life-cycle of cement:
- 0.288KL/ton of cement
- 0.003208KL/kWh of electricity
- 0.099KL/ton of limestone
Tell us something on recycling of water. How important is it for us?
Water recycling is reusing treated wastewater for beneficial purposes such as agricultural irrigation, industrial processes, toilet flushing, and replenishing a ground water basin.
Recycling of water directly saves this natural resource and is very beneficial as polluted water can be again used and fresh water is saved for future use, which promotes environment sustainability.
How do we sensitise people on the subject of water?
The following measures can be taken:
- By imparting trainings and creating awareness in people for water conservation
- By conducting programmes for households, to use water efficiently (recycling the water of washing machine, recycling the water of basins in flushes)
- By displaying banners and posters on water conservation
- By interacting with youth about the water footprint and importance of fresh water in life
- These measures should be at the governmental level and many corporates can take it up as a CSR initiative. Industry-specific training on water management is the key.
You may like
Concrete
India donates 225t of cement for Myanmar earthquake relief
Published
4 weeks agoon
June 17, 2025By
admin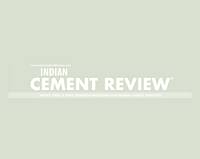
On 23 May 2025, the Indian Navy ship UMS Myitkyina arrived at Thilawa (MITT) port carrying 225 tonnes of cement provided by the Indian government to aid post-earthquake rebuilding efforts in Myanmar. As reported by the Global Light of Myanmar, a formal handover of 4500 50kg cement bags took place that afternoon. The Yangon Region authorities managed the loading of the cement onto trucks for distribution to the earthquake-affected zones.
Concrete
Reclamation of Used Oil for a Greener Future
Published
4 weeks agoon
June 16, 2025By
admin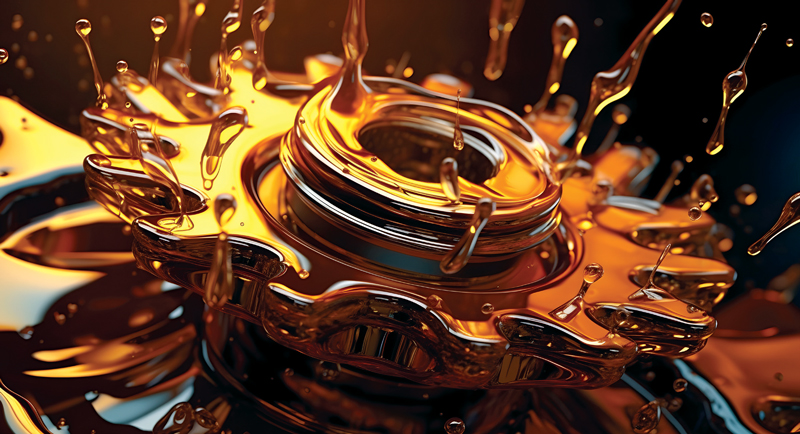
In this insightful article, KB Mathur, Founder and Director, Global Technical Services, explores how reclaiming used lubricants through advanced filtration and on-site testing can drive cost savings, enhance productivity, and support a greener industrial future. Read on to discover how oil regeneration is revolutionising sustainability in cement and core industries.
The core principle of the circular economy is to redefine the life cycle of materials and products. Unlike traditional linear models where waste from industrial production is dumped/discarded into the environment causing immense harm to the environment;the circular model seeks to keep materials literally in continuous circulation. This is achievedthrough processes cycle of reduction, regeneration, validating (testing) and reuse. Product once
validated as fit, this model ensures that products and materials are reintroduced into the production system, minimising waste. The result? Cleaner and greener manufacturing that fosters a more sustainable planet for future generations.
The current landscape of lubricants
Modern lubricants, typically derived from refined hydrocarbons, made from highly refined petroleum base stocks from crude oil. These play a critical role in maintaining the performance of machinery by reducing friction, enabling smooth operation, preventing damage and wear. However, most of these lubricants; derived from finite petroleum resources pose an environmental challenge once used and disposed of. As industries become increasingly conscious of their environmental impact, the paramount importance or focus is shifting towards reducing the carbon footprint and maximising the lifespan of lubricants; not just for environmental reasons but also to optimise operational costs.
During operations, lubricants often lose their efficacy and performance due to contamination and depletion of additives. When these oils reach their rejection limits (as they will now offer poor or bad lubrication) determined through laboratory testing, they are typically discarded contributing to environmental contamination and pollution.
But here lies an opportunity: Used lubricants can be regenerated and recharged, restoring them to their original performance level. This not only mitigates environmental pollution but also supports a circular economy by reducing waste and conserving resources.
Circular economy in lubricants
In the world of industrial machinery, lubricating oils while essential; are often misunderstood in terms of their life cycle. When oils are used in machinery, they don’t simply ‘DIE’. Instead, they become contaminated with moisture (water) and solid contaminants like dust, dirt, and wear debris. These contaminants degrade the oil’s effectiveness but do not render it completely unusable. Used lubricants can be regenerated via advanced filtration processes/systems and recharged with the use of performance enhancing additives hence restoring them. These oils are brought back to ‘As-New’ levels. This new fresher lubricating oil is formulated to carry out its specific job providing heightened lubrication and reliable performance of the assets with a view of improved machine condition. Hence, contributing to not just cost savings but leading to magnified productivity, and diminished environmental stress.
Save oil, save environment
At Global Technical Services (GTS), we specialise in the regeneration of hydraulic oils and gear oils used in plant operations. While we don’t recommend the regeneration of engine oils due to the complexity of contaminants and additives, our process ensures the continued utility of oils in other applications, offering both cost-saving and environmental benefits.
Regeneration process
Our regeneration plant employs state-of-the-art advanced contamination removal systems including fine and depth filters designed to remove dirt, wear particles, sludge, varnish, and water. Once contaminants are removed, the oil undergoes comprehensive testing to assess its physico-chemical properties and contamination levels. The test results indicate the status of the regenerated oil as compared to the fresh oil.
Depending upon the status the oil is further supplemented with high performance additives to bring it back to the desired specifications, under the guidance of an experienced lubrication technologist.
Contamination Removal ? Testing ? Additive Addition
(to be determined after testing in oil test laboratory)
The steps involved in this process are as follows:
1. Contamination removal: Using advanced filtration techniques to remove contaminants.
2. Testing: Assessing the oil’s properties to determine if it meets the required performance standards.
3. Additive addition: Based on testing results, performance-enhancing additives are added to restore the oil’s original characteristics.
On-site oil testing laboratories
The used oil from the machine passes through 5th generation fine filtration to be reclaimed as ‘New Oil’ and fit to use as per stringent industry standards.
To effectively implement circular economy principles in oil reclamation from used oil, establishing an on-site oil testing laboratory is crucial at any large plants or sites. Scientific testing methods ensure that regenerated oil meets the specifications required for optimal machine performance, making it suitable for reuse as ‘New Oil’ (within specified tolerances). Hence, it can be reused safely by reintroducing it in the machines.
The key parameters to be tested for regenerated hydraulic, gear and transmission oils (except Engine oils) include both physical and chemical characteristics of the lubricant:
- Kinematic Viscosity
- Flash Point
- Total Acid Number
- Moisture / Water Content
- Oil Cleanliness
- Elemental Analysis (Particulates, Additives and Contaminants)
- Insoluble
The presence of an on-site laboratory is essential for making quick decisions; ensuring that test reports are available within 36 to 48 hours and this prevents potential mechanical issues/ failures from arising due to poor lubrication. This symbiotic and cyclic process helps not only reduce waste and conserve oil, but also contributes in achieving cost savings and playing a big role in green economy.
Conclusion
The future of industrial operations depends on sustainability, and reclaiming used lubricating oils plays a critical role in this transformation. Through 5th Generation Filtration processes, lubricants can be regenerated and restored to their original levels, contributing to both environmental preservation and economic efficiency.
What would happen if we didn’t recycle our lubricants? Let’s review the quadruple impacts as mentioned below:
1. Oil Conservation and Environmental Impact: Used lubricating oils after usage are normally burnt or sold to a vendor which can be misused leading to pollution. Regenerating oils rather than discarding prevents unnecessary waste and reduces the environmental footprint of the industry. It helps save invaluable resources, aligning with the principles of sustainability and the circular economy. All lubricating oils (except engine oils) can be regenerated and brought to the level of ‘As New Oils’.
2. Cost Reduction Impact: By extending the life of lubricants, industries can significantly cut down on operating costs associated with frequent oil changes, leading to considerable savings over time. Lubricating oils are expensive and saving of lubricants by the process of regeneration will overall be a game changer and highly economical to the core industries.
3. Timely Decisions Impact: Having an oil testing laboratory at site is of prime importance for getting test reports within 36 to 48 hours enabling quick decisions in critical matters that may
lead to complete shutdown of the invaluable asset/equipment.
4. Green Economy Impact: Oil Regeneration is a fundamental part of the green economy. Supporting industries in their efforts to reduce waste, conserve resources, and minimise pollution is ‘The Need of Our Times’.
About the author:
KB Mathur, Founder & Director, Global Technical Services, is a seasoned mechanical engineer with 56 years of experience in India’s oil industry and industrial reliability. He pioneered ‘Total Lubrication Management’ and has been serving the mining and cement sectors since 1999.
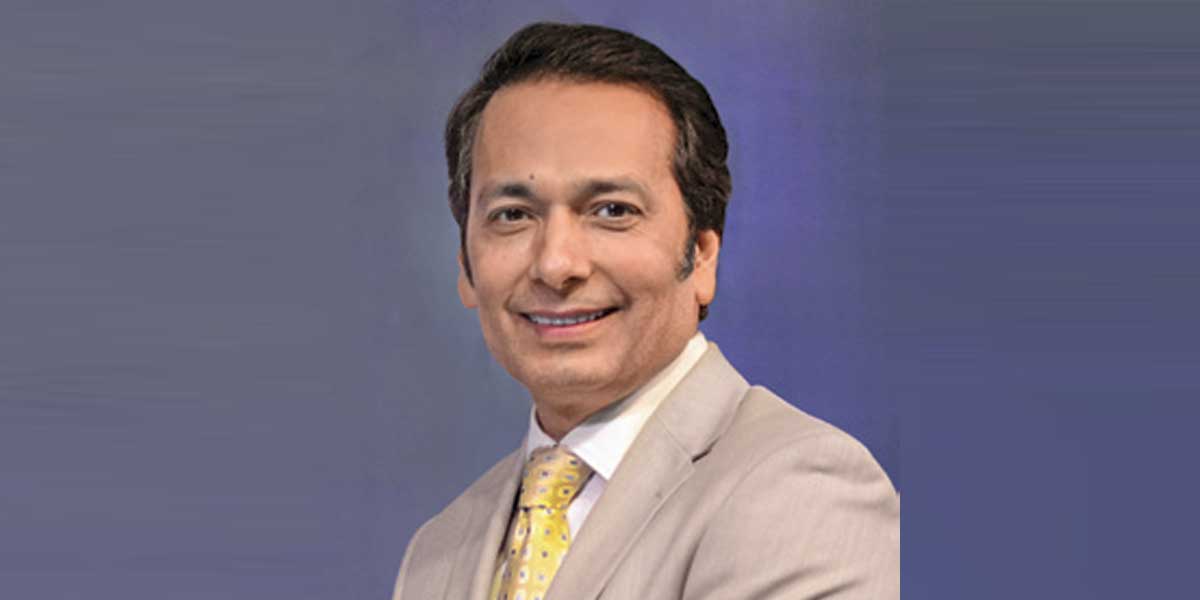
The Indian cement industry has reached a critical juncture in its sustainability journey. In a landmark move, the Ministry of Environment, Forest and Climate Change has, for the first time, announced greenhouse gas (GHG) emission intensity reduction targets for 282 entities, including 186 cement plants, under the Carbon Credit Trading Scheme, 2023. These targets, to be enforced starting FY2025-26, are aligned with India’s overarching ambition of achieving net zero emissions by 2070.
Cement manufacturing is intrinsically carbon-intensive, contributing to around 7 per cent of global GHG emissions, or approximately 3.8 billion tonnes annually. In India, the sector is responsible for 6 per cent of total emissions, underscoring its critical role in national climate mitigation strategies. This regulatory push, though long overdue, marks a significant shift towards accountability and structured decarbonisation.
However, the path to a greener cement sector is fraught with challenges—economic viability, regulatory ambiguity, and technical limitations continue to hinder the widespread adoption of sustainable alternatives. A major gap lies in the lack of a clear, India-specific definition for ‘green cement’, which is essential to establish standards and drive industry-wide transformation.
Despite these hurdles, the industry holds immense potential to emerge as a climate champion. Studies estimate that through targeted decarbonisation strategies—ranging from clinker substitution and alternative fuels to carbon capture and innovative product development—the sector could reduce emissions by 400 to 500 million metric tonnes by 2030.
Collaborations between key stakeholders and industry-wide awareness initiatives (such as Earth Day) are already fostering momentum. The responsibility now lies with producers, regulators and technology providers to fast-track innovation and investment.
The time to act is now. A sustainable cement industry is not only possible—it is imperative.

Hindalco Buys US Speciality Alumina Firm for $125 Million

Star Cement launches ‘Star Smart Building Solutions’

Nuvoco Vistas reports record quarterly EBITDA

UltraTech Cement increases capacity by 1.4Mt/yr

Shree Cement reports 2025 financial year results

Hindalco Buys US Speciality Alumina Firm for $125 Million

Star Cement launches ‘Star Smart Building Solutions’

Nuvoco Vistas reports record quarterly EBITDA

UltraTech Cement increases capacity by 1.4Mt/yr
