Process
We have used more than 80, 000 tonnes of fly ash without any problem
Published
4 years agoon
By
admin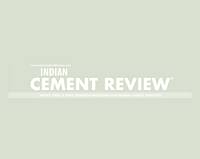
Cyrus Pithawalla, Director Engineering, Hiranandani Constructions
Concrete mixing has evolved as an art mastered by the few to a precise scientific process that can be replicated anywhere. The key is knowing what to look for during its preparation. Cyrus Pithawalla, Director Engineering, Hiranandani Constructions shares his insights with ICR. Excerpts from the interaction.
Tell us about cement grades suitable for concrete production.
Cement comes in different grades and based on that, its applications vary. In foreign countries, cement is categorised as Class-A, Class-B, Class-C etc (API classifications). That cement cannot be used in India as the climatic conditions here are very different. If we try to use that here, then we will have cracks in structures called shrinkage cracks. Here in India, cement comes in 33, 43, 53, and also 63 grade. Of these 43 and 53 grade are very popular, 43 grade is good for plastering work, and 53 grade should be for making concrete.
There is a big difference in quality and strength of 43 and 53 grade cement. One has to be very careful if both 43 and the 53 grade cement are stocked in the same godown. If workers mistakenly take 43 grade cement instead of 53 grade for mixing in concrete, then the results will be disastrous. Both materials look the same. Mixing fly ash in 53 grade cement serves as a good visual demarcation and helps avoiding such confusion. Now that the cost difference between 43 grade cement and the 53 grade cement has become negligible, it is possible to use 53 grade cement for both plastering as well as for concrete manufacturing. As we go ahead, we will see only 53 grade being used everywhere; 43 grade cement is becoming less available due to its decreasing demand.
What is the role of aggregates and how does one pick the right material?
The basic components of concrete are coarse aggregates (CA), sand and cement. Aggregates are classified as CA-1 and CA-2 based on size. CA-1 is about 15 – 10 mm in diameter while CA-2 is about 25-30 mm in diameter. In India our quarries are supplying 15 mm CA-1 and 30 mm CA-2 aggregates. An ideal concrete mix would have CA1 of 10 mm diameter and CA2 of 20 mm diameter. In concrete, the better the particle packing, the higher the strength. CA-1 fills the gap between the CA-2 aggregates. Sand fills the void between the CA-1 aggregates and then finally, cement fills the voids between the sand particles and holds the entire mixture in place. Another most important ingredient is the water and its quantity is critical to concrete’s strength.
Today river sand is being replaced with manufactured sand. How well does that work?
Now river sand is no longer available. The supply has completely stopped. In this scenario, we have to turn to manufactured sand. Unfortunately, very few realise that in several cases, what is being sold as manufactured sand is nothing but crusher dust. There is a huge difference between crusher dust (also called crushed sand) and manufactured sand. The manufactured sand goes through various processes and the product that you get at the end has uniformity in size and good homogeneity while crusher dust is nothing but quarry waste, the fine dust that is generated during the aggregate crushing process. This waste product of the quarry is laden with fine dust and is often sold to unsuspecting buyers. This impacts the quality of concrete and one must avoid buying crusher dust/crushed sand. Also, in the monsoon, crusher dust powder comes along with CA1 as it is stuck to the material due to high moisture in the material. So, extra care must be taken while procuring aggregates in monsoon season.
How open is the industry to using fly ash?
Fly ash so far, has been considered taboo. Some people may have doubts about using it as there are several misunderstandings surrounding it. We have been using fly ash without any problem for a long time. We have used more than 80, 000 tonnes of fly ash without any problem at all.
What care do you take in the selection of fly ash?
You must first understand that fly ash comes as different types. The quality varies depending on the source that it is obtained from and also most importantly, with regards to its fineness. We have identified one such supplier who supplies the fly ash as per our specifications. The company has separate classifiers to collect flyash of different particle size.
In case of fly ash, the quality in terms of the fineness and the consistency in size is very important as it is difficult to make out the variation in fly ash quality on the site where mixing is taking place. And you can`t afford to have one batch of concrete poured differently from another. So fineness and particle size uniformity is very important.
Are there any grades of fly ash that are more suitable for concrete manufacture?
Yes, there are grades of fly ash but very few people are aware of it. Fly ash is a waste product of the thermal power industry and so far, the cost associated is the cost of transporting it. There is as such, no processing that happens once fly ash is generated from a thermal plant. The fly ash is collected from precipitators and separated / classified to obtain a product with uniform mesh size. The first chamber separates the coarse material, the second picks up finer quality fly ash and the third chamber collects the finest material at the end. So the fly ash available is graded as 60 , 63, 80, etc, depending on the mesh size. The finer the fly ash, the better it is. We prefer the one that you get at the end of the classification process as the grade is really good there.
And how much fly ash can we add to concrete?
You can add from 20 – 30 per cent. You can even go up to 40 per cent, depending on the end result you are looking at. According to our experience, 29 per cent is the highest that we can go.
With newer materials and additives available, higher grades of concrete are becoming available. How high can we go?
Concrete strength on a global scale, is measured in terms of N/mm2. So a M30 grade concrete means the compressive strength it acquires after 28 days will be 30 N/mm2. So there is M30, M40, M60, etc. Now note that the concrete strength depends on the water- to- binder ratio or the ratio of water to the fines in it. If you are adding only cement, then it is ratio of water to cement, and if fly ash is added, then you must consider both cement plus fly ash while calculating the ratio. The ratio can be as low as 0.31 at the most. If you try to formulate concrete to say, M100 or anything above, then there is a problem. In such cases, the ratio can drop to ~ 0.22 or lower. At this water binder ratio, autogenous shrinkage will occur in the concrete and micro cracks will start developing in the structure. These micro cracks are not visible to the naked eye but I would certainly worry about such cracks. So the water binder ratio caps the strength limit up to which we can safely go.
Can the addition of polymers help prevent such cracking?
No, polymers are anyway added to concrete in today`s modern process. Despite these polymers, there could be cracks.
How do delays affect the RMC quality and what more can be done at the technical level?
Today, there are plasticisers available that help tweak the slump characteristics and setting properties of concrete. If you are expecting a delay, then you can dose extra before dispatch. However, if the dosage is extra, then the setting time too, is extended. One can always fix things if it is under-dosed. Extra dosage can be added at site. This however, is done manually and there is an element of uncertainty in the process.
Which are the latest materials that excite you?
I am excited about the new age super plasticisers. They help in achieving the target slump. You must understand that the slump requirement will vary from application to application. The column will require concrete with a different slump than that required by the concrete in slab. The third generation super plasticisers available today are highly customisable, and some leading companies are making custom polymers available tailor-made just for your needs. That is very exciting.
Process
Price hikes, drop in input costs help cement industry to post positive margins: Care Ratings
Published
4 years agoon
October 21, 2021By
admin
Region-wise,the southern region comprises 35% of the total cement capacity, followed by thenorthern, eastern, western and central region comprising 20%, 18%, 14% and 13%of the capacity, respectively.
The cement industry is expected to post positive margins on decent price hikes over the months, falling raw material prices and marked drop in overall production costs, said an analysis of Care Ratings.
Wholesale and retail prices of cement have increased 11.9% and 12.4%, respectively, in the current financial year. As whole prices have remained elevated in most of the markets in the months of FY20, against the corresponding period of the previous year.
Similarly, electricity and fuel cost have declined 11.9% during 9M FY20 due to drop in crude oil prices. Logistics costs, the biggest cost for cement industry, has also dropped 7.7% (selling and distribution) as the Railways extended the benefit of exemption from busy season surcharge. Moreover, the cost of raw materials, too, declined 5.1% given the price of limestone had fallen 11.3% in the same aforementioned period, the analysis said.
According to Care Ratings, though the overall sales revenue has increased only 1.3%, against 16% growth in the year-ago period, the overall expenditure has declined 3.2% which has benefited the industry largely given the moderation in sales.
Even though FY20 has been subdued in terms of production and demand, the fall in cost of production has still supported the cement industry by clocking in positive margins, the rating agency said.
Cement demand is closely linked to the overall economic growth, particularly the housing and infrastructure sector. The cement sector will be seeing a sharp growth in volumes mainly due to increasing demand from affordable housing and other government infrastructure projects like roads, metros, airports, irrigation.
The government’s newly introduced National Infrastructure Pipeline (NIP), with its target of becoming a $5-trillion economy by 2025, is a detailed road map focused on economic revival through infrastructure development.
The NIP covers a gamut of sectors; rural and urban infrastructure and entails investments of Rs.102 lakh crore to be undertaken by the central government, state governments and the private sector. Of the total projects of the NIP, 42% are under implementation while 19% are under development, 31% are at the conceptual stage and 8% are yet to be classified.
The sectors that will be of focus will be roads, railways, power (renewable and conventional), irrigation and urban infrastructure. These sectors together account for 79% of the proposed investments in six years to 2025. Given the government’s thrust on infrastructure creation, it is likely to benefit the cement industry going forward.
Similarly, the Pradhan Mantri Awaas Yojana, aimed at providing affordable housing, will be a strong driver to lift cement demand. Prices have started correcting Q4 FY20 onwards due to revival in demand of the commodity, the agency said in its analysis.
Industry’s sales revenue has grown at a CAGR of 7.3% during FY15-19 but has grown only 1.3% in the current financial year. Tepid demand throughout the country in the first half of the year has led to the contraction of sales revenue. Fall in the total expenditure of cement firms had aided in improving the operating profit and net profit margins of the industry (OPM was 15.2 during 9M FY19 and NPM was 3.1 during 9M FY19). Interest coverage ratio, too, has improved on an overall basis (ICR was 3.3 during 9M FY19).
According to Cement Manufacturers Association, India accounts for over 8% of the overall global installed capacity. Region-wise, the southern region comprises 35% of the total cement capacity, followed by the northern, eastern, western and central region comprising 20%, 18%, 14% and 13% of the capacity, respectively.
Installed capacity of domestic cement makers has increased at a CAGR of 4.9% during FY16-20. Manufacturers have been able to maintain a capacity utilisation rate above 65% in the past quinquennium. In the current financial year due to the prolonged rains in many parts of the country, the capacity utilisation rate has fallen from 70% during FY19 to 66% currently (YTD).
Source:moneycontrol.com
Process
Wonder Cement shows journey of cement with new campaign
Published
4 years agoon
October 21, 2021By
admin
The campaign also marks Wonder Cement being the first ever cement brand to enter the world of IGTV…
ETBrandEquity
Cement manufacturing company Wonder Cement, has announced the launch of a digital campaign ‘Har Raah Mein Wonder Hai’. The campaign has been designed specifically to run on platforms such as Instagram, Facebook and YouTube.
#HarRaahMeinWonderHai is a one-minute video, designed and conceptualised by its digital media partner Triature Digital Marketing and Technologies Pvt Ltd. The entire journey of the cement brand from leaving the factory, going through various weather conditions and witnessing the beauty of nature and wonders through the way until it reaches the destination i.e., to the consumer is very intriguing and the brand has tried to showcase the same with the film.
Sanjay Joshi, executive director, Wonder Cement, said, "Cement as a product poses a unique marketing challenge. Most consumers will build their homes once and therefore buy cement once in a lifetime. It is critical for a cement company to connect with their consumers emotionally. As a part of our communication strategy, it is our endeavor to reach out to a large audience of this country through digital. Wonder Cement always a pioneer in digital, with the launch of our IGTV campaign #HarRahMeinWonderHai, is the first brand in the cement category to venture into this space. Through this campaign, we have captured the emotional journey of a cement bag through its own perspective and depicted what it takes to lay the foundation of one’s dreams and turn them into reality."
The story begins with a family performing the bhoomi poojan of their new plot. It is the place where they are investing their life-long earnings; and planning to build a dream house for the family and children. The family believes in the tradition of having a ‘perfect shuruaat’ (perfect beginning) for their future dream house. The video later highlights the process of construction and in sequence it is emphasising the value of ‘Perfect Shuruaat’ through the eyes of a cement bag.
Tarun Singh Chauhan, management advisor and brand consultant, Wonder Cement, said, "Our objective with this campaign was to show that the cement produced at the Wonder Cement plant speaks for itself, its quality, trust and most of all perfection. The only way this was possible was to take the perspective of a cement bag and showing its journey of perfection from beginning till the end."
According to the company, the campaign also marks Wonder Cement being the first ever cement brand to enter the world of IGTV. No other brand in this category has created content specific to the platform.
Process
In spite of company’s optimism, demand weakness in cement is seen in the 4% y-o-y drop in sales volume. (Reuters)
Published
4 years agoon
October 21, 2021By
admin
Cost cuts and better realizations save? the ?day ?for ?UltraTech Cement, Updated: 27 Jan 2020, Vatsala Kamat from Live Mint
Lower cost of energy and logistics helped Ebitda per tonne rise by about 29% in Q3
Premiumization of acquired brands, synergistic?operations hold promise for future profit growth Topics
UltraTech Cement
India’s largest cement producer UltraTech Cement Ltd turned out a bittersweet show in the December quarter. A sharp drop in fuel costs and higher realizations helped drive profit growth. But the inherent demand weakness was evident in the sales volumes drop during the quarter.
Better realizations during the December quarter, in spite of the 4% year-on-year volume decline, minimized the pain. Net stand-alone revenue fell by 2.6% to ?9,981.8 crore.
But as pointed out earlier, lower costs on most fronts helped profitability. The chart alongside shows the sharp drop in energy costs led by lower petcoke prices, lower fuel consumption and higher use of green power. Logistics costs, too, fell due to lower railway freight charges and synergies from the acquired assets. These savings helped offset the increase in raw material costs.
The upshot: Q3 Ebitda (earnings before interest, tax, depreciation and amortization) of about ?990 per tonne was 29% higher from a year ago. The jump in profit on a per tonne basis was more or less along expected lines, given the increase in realizations. "Besides, the reduction in net debt by about ?2,000 crore is a key positive," said Binod Modi, analyst at Reliance Securities Ltd.
Graphic by Santosh Sharma/Mint
What also impressed analysts is the nimble-footed integration of the recently merged cement assets of Nathdwara and Century, which was a concern on the Street.
Kunal Shah, analyst (institutional equities) at Yes Securities (India) Ltd, said: "The company has proved its ability of asset integration. Century’s cement assets were ramped up to 79% capacity utilization in December, even as they operated Nathdwara generating an Ebitda of ?1,500 per tonne."
Looks like the demand weakness mirrored in weak sales during the quarter was masked by the deft integration and synergies derived from these acquired assets. This drove UltraTech’s stock up by 2.6% to ?4,643 after the Q3 results were declared on Friday.
Brand transition from Century to UltraTech, which is 55% complete, is likely to touch 80% by September 2020. A report by Jefferies India Pvt. Ltd highlights that the Ebitda per tonne for premium brands is about ?5-10 higher per bag than the average (A cement bag weighs 50kg). Of course, with competition increasing in the arena, it remains to be seen how brand premiumization in the cement industry will pan out. UltraTech Cement scores well among peers here.
However, there are road bumps ahead for the cement sector and for UltraTech. Falling gross domestic product growth, fiscal slippages and lower budgetary allocation to infrastructure sector are making industry houses jittery on growth. Although UltraTech’s management is confident that cement demand is looking up, sustainability and pricing power remains a worry for the near term.