Product development
Co-processing of alternate fuels
Published
4 years agoon
By
admin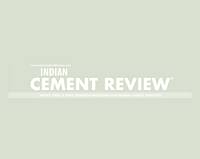
The absence of necessary infrastructure to support co-processing is one of the main reasons of its slow growth in India. There is thus, an urgent need for stakeholders to come together and evolve a national strategy and a time bound programme for building up the infrastructure, writes SP Deolalkar.
The Indian cement industry, Number Two in the world, is modern technology-wise, and efficient in terms of energy consumption. It is consciously taking steps to bring down CO2 emissions. As a part of this effort, India has taken up co-processing of Alternate Fuels (AF) but the overall rate of substitution is very low, just about one per cent. Technologies for using various types of AFs are available and have been successfully used elsewhere with substitution rates as high 30 – 40 per cent in European countries. Absence of necessary infrastructure to support co processing is the main reason of its slow growth in India.
Volume of AFs required
Installed capacity for and actual production of cement in India is 330 and 250 mtpa respectively. About 75 per cent cements produced are blended cements. With a clinker/cement ratio of ~ 0.72, clinker production would be ~ 180 mtpa requiring 38 – 40 mtpa of raw coal. If only ten per cent of it is replaced by AF, requirement of AF would be say 3.5 – 4 mtpa. Thus, there is tremendous scope for development of AFs as a viable industry in itself. Various aspects of co-processing AFs have been brought out in the author’s book ‘Designing Green Cement Plants in Section 4, devoted to AFR.
Need for infrastructure
The simple reason for the need for infrastructure is to create an environment where wastes with potential as fuels (AFs) would be continuously available to cement companies preferably in ready to use form. Incidentally, using coal also requires infrastructure and processing to be able to fire it in kilns and calciners. Historically, cement companies have taken on themselves this responsibility.
In contrast to coal, AFs come from a vast number of sources, are spread over a wide territory and differ greatly in properties and availability. Identified as wastes till now, it is necessary to begin at the beginning when planning to convert them into fuels and using them. Processing required to be done varies greatly from one type of AF to the other.
Co-processing replaces fossil fuel by say, a maximum 40 per cent. A cement plant is therefore required to process two types of fuels- sometimes three – if it is required to use two types of AFs as their continuous availability is not assured as of now. Hence investments in machinery and buildings for processing AFs are considered risky. For these reasons, cement companies would prefer buying the AF that can be delivered on their doorstep in ready to use form. This in turn implies outsourcing of this activity which is a new feature. Creating such supporting facilities means creating infrastructure. An appropriate example of an infrastructure created to meet the needs of the society is ‘AMUL’.
Infrastructure required for AFs
The concept of using wastes on a large scale itself being new, there is not much information on their properties, sources and locations. Infrastructure would therefore comprise of:
- Compilation of data in the form of a directory of wastes and potential AFs among them.
- Testing the more promising among them for determining various aspects of burning them as fuels. Pilot plant tests on the selected AFs.
- Setting up agencies which would do handling and processing of AFs and would supply them on a commercial scale to cement (or any other) industry continuously.
Directory of wastes and their potential
The first step in the build-up of infrastructure would be to collect categorical data on wastes that could be AFs. Such data would classify wastes and other non conventional sources of fuel according to their properties, heat value, sources, locations, availability and volume/ quantity.
Such data supplemented by maps showing locations would be very useful to potential users.
Refer to the map which is similar to maps of Geological Survey of India for mineral wealth of the country.
Often this is the starting point for location of a green field cement plant. Such data should be collected on a national level and should be available for all industries and for uses other than burning also.
Research on wastes as fuels
The next step on a national scale would be to have a fuel research institute that would carry out detailed research on every aspect of combustion of likely AFs such as products of combustion, gases emitted and ashes produced. In making cement, ashes enter clinker produced. Some wastes give away harmful compounds like NOx , dioxins, heavy metals. It is important to know about them before beginning to use them on a large scale. The Central Fuel Research Institute can be one such institute and should play an important role. If not equipped now, it should be strengthened and expanded by opening branches to serve the country as a whole.
Pilot plant tests
The next step in use of AFs would be to carry out pilot plant tests in a set up that simulates actual operating conditions. All aspects of co-processing that would influence regular operation and quality of product and emissions into the environment should be carefully observed and monitored. The tests would bring out aspects like efficiency of combustion, and the extent to which AF could replace fossil fuel. They would be the basis for designing of the system for co-processing in a real plant.
Such pilot plant tests assume great significance as their results would be the basis for approval and permission for co-processing on commercial scale continuously, by government agencies like Bureau of Indian Standards and Pollution Control Boards who would be invited to witness the tests. There are only a limited number of institutions that are equipped to carry out such pilot plant tests like for example NCCBM and CRS of ACC.
Since the requirements of pilot tests would increase with number of users and types of AFs, facilities in these institutes should be made available to other cement companies, say at cost. It should not be necessary to invent the wheel every time. Tests carried out on a given type of AF, if successful should be acceptable for that type as such.
Infrastructure for bringing AFs in ready to use form
This would be regional and product-wise. It has two main constituents:
- Collection and transport of wastes to the processor and transport of processed AF to users like cement companies.
- Processors of wastes who receive, store, blend and process wastes as per the requirements of users.
Transport can be within a state or interstate. Transporters may specialise in transporting specific types of AFs like, sludges, hazardous wastes, MSW, etc. That is because the transporting vehicles would have to be designed to suit wastes and AFs carried. Wastes occur all over the country but certain types of waste are predominant in specific regions. Their volume could also be large enough. In that case there can be more than one Intermediate Service Provider (ISP) or processor for one type of AF. It can be the other way round also; depending on relative locations of, processors and users, supply of processed AF can be within state or interstate. A processor may prefer to deal with one or say up to three types of wastes as different wastes require different facilities for handling, storing and processing for turning them into ready for use AFs.
A very important aspect of service to be rendered as supplier of AFs is the control on quality. It begins at the origin. Only those wastes which conform to the representative character established in research stations would be lifted. At the processor’s premises, it will be necessary to blend wastes as they may be from different sources from time to time or would differ in quality from same source to ensure uniformity of quality.
The processor has therefore to equip himself with necessary testing equipment to satisfy himself and his clients about the quality. He should have equipment that would do pre blending.
If the processor is thus equipped with facilities for testing at all stages of processing, the users do not have to duplicate them in their respective factory premises.
Processors will maintain stocks of wastes for processing and also stocks of processed AFs to be able to maintain continuity of supply of AFs to clients. That such an infrastructure is feasible and is beneficial to all stakeholders has been amply demonstrated by Gujarat Environment Protection Industries (GEPIL) located at Surat. There is an urgent need for many more Processors / ISPs like them if co-processing is to be speeded up.
Advantages of infrastructure
The availability of infrastructure/s as explained above has several advantages. Wastes having potential as AFs would be removed as and when generated. Societies would have cleaner environment. Processors contribute greatly in creating value for wastes by converting them into AFs and AFs would most certainly be cheaper than fossil fuels. The cement industry would thus save fossil fuels and bring down CO2 emissions further.
Conclusion
There is an urgent need for stakeholders to come together and evolve a national strategy and a time- bound programme for building up infrastructure. Generators and users can come together to form sister companies or subsidiaries that could be the processors or ISPs.
Consultants and machinery designers should join to evolve tailor made systems for co-processing different types of AFs. Once the infrastructure is in position, MoEF can stipulate minimum per cent of AF by way of co-processing.
You may like
Concrete
Conveyor belts are a vital link in the supply chain
Published
3 weeks agoon
June 16, 2025By
admin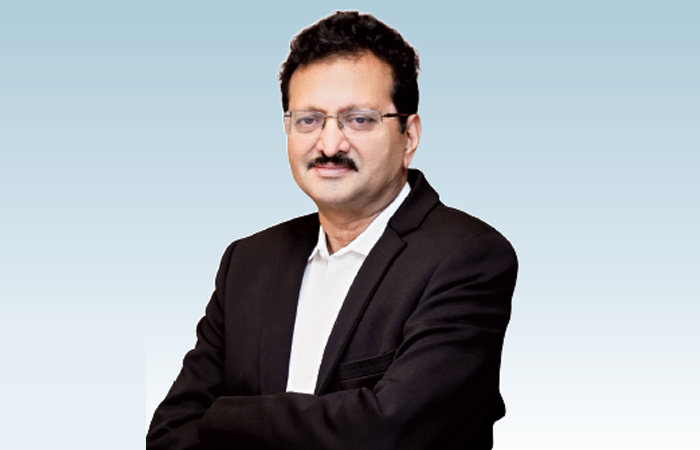
Kamlesh Jain, Managing Director, Elastocon, discusses how the brand delivers high-performance, customised conveyor belt solutions for demanding industries like cement, mining, and logistics, while embracing innovation, automation, and sustainability.
In today’s rapidly evolving industrial landscape, efficient material handling isn’t just a necessity—it’s a competitive advantage. As industries such as mining, cement, steel and logistics push for higher productivity, automation, and sustainability, the humble conveyor belt has taken on a mission-critical role. In this exclusive interview, Kamlesh Jain, Managing Director, Elastocon, discusses how the company is innovating for tougher terrains, smarter systems and a greener tomorrow.
Brief us about your company – in terms of its offerings, manufacturing facilities, and the key end-user industries it serves.
Elastocon, a flagship brand of the Royal Group, is a trusted name in the conveyor belt manufacturing industry. Under the brand name ELASTOCON, the company produces both open-end and endless belts, offering tailor-made solutions to some of the most demanding sectors such as cement, steel, power, mining, fertiliser, and logistics. Every belt is meticulously engineered—from fabric selection to material composition—to ensure optimal performance in tough working conditions. With advanced manufacturing facilities and strict quality protocols, Elastocon continues to deliver high-performance conveyor solutions designed for durability, safety, and efficiency.
How is the group addressing the needs for efficient material handling?
Efficient material handling is the backbone of any industrial operation. At Elastocon, our engineering philosophy revolves around creating belts that deliver consistent performance, long operational life, and minimal maintenance. We focus on key performance parameters such as tensile strength, abrasion resistance, tear strength, and low elongation at working tension. Our belts are designed to offer superior bonding between plies and covers, which directly impacts their life and reliability. We also support clients
with maintenance manuals and technical advice, helping them improve their system’s productivity and reduce downtime.
How critical are conveyor belts in ensuring seamless material handling?
Conveyor belts are a vital link in the supply chain across industries. In sectors like mining, cement, steel, and logistics, they facilitate the efficient movement of materials and help maintain uninterrupted production flows. At Elastocon, we recognise the crucial role of belts in minimising breakdowns and increasing plant uptime. Our belts are built to endure abrasive, high-temperature, or high-load environments. We also advocate proper system maintenance, including correct belt storage, jointing, roller alignment, and idler checks, to ensure smooth and centered belt movement, reducing operational interruptions.
What are the key market and demand drivers for the conveyor belt industry?
The growth of the conveyor belt industry is closely tied to infrastructure development, increased automation, and the push for higher operational efficiency. As industries strive to reduce labor dependency and improve productivity, there is a growing demand for advanced material handling systems. Customers today seek not just reliability, but also cost-effectiveness and technical superiority in the belts they choose. Enhanced product aesthetics and innovation in design are also becoming significant differentiators. These trends are pushing manufacturers to evolve continuously, and Elastocon is leading the way with customer-centric product development.
How does Elastocon address the diverse and evolving requirements of these sectors?
Our strength lies in offering a broad and technically advanced product portfolio that serves various industries. For general-purpose applications, our M24 and DINX/W grade belts offer excellent abrasion resistance, especially for RMHS and cement plants. For high-temperature operations, we provide HR and SHR T2 grade belts, as well as our flagship PYROCON and PYROKING belts, which can withstand extreme heat—up to 250°C continuous and even 400°C peak—thanks to advanced EPM polymers.
We also cater to sectors with specialised needs. For fire-prone environments like underground mining, we offer fire-resistant belts certified to IS 1891 Part V, ISO 340, and MSHA standards. Our OR-grade belts are designed for oil and chemical resistance, making them ideal for fertiliser and chemical industries. In high-moisture applications like food and agriculture, our MR-grade belts ensure optimal performance. This diverse range enables us to meet customer-specific challenges with precision and efficiency.
What core advantages does Elastocon offer that differentiate it from competitors?
Elastocon stands out due to its deep commitment to quality, innovation, and customer satisfaction. Every belt is customised to the client’s requirements, supported by a strong R&D foundation that keeps us aligned with global standards and trends. Our customer support doesn’t end at product delivery—we provide ongoing technical assistance and after-sales service that help clients maximise the value of their investments. Moreover, our focus on compliance and certifications ensures our belts meet stringent national and international safety and performance standards, giving customers added confidence.
How is Elastocon gearing up to meet its customers’ evolving needs?
We are conscious of the shift towards greener and smarter manufacturing practices. Elastocon is embracing sustainability by incorporating eco-friendly materials and energy-efficient manufacturing techniques. In parallel, we are developing belts that seamlessly integrate with automated systems and smart industrial platforms. Our vision is to make our products not just high-performing but also future-ready—aligned with global sustainability goals and compatible with emerging technologies in industrial automation and predictive maintenance.
What trends do you foresee shaping the future of the conveyor belt industry?
The conveyor belt industry is undergoing a significant transformation. As Industry 4.0 principles gain traction, we expect to see widespread adoption of smart belts equipped with sensors for real-time monitoring, diagnostics, and predictive maintenance. The demand for recyclable materials and sustainable designs will continue to grow. Furthermore, industry-specific customisation will increasingly replace standardisation, and belts will be expected to do more than just transport material—they will be integrated into intelligent production systems. Elastocon is already investing in these future-focused areas to stay ahead of the curve.

Advertising or branding is never about driving sales. It’s about creating brand awareness and recall. It’s about conveying the core values of your brand to your consumers. In this context, why is branding important for cement companies? As far as the customers are concerned cement is simply cement. It is precisely for this reason that branding, marketing and advertising of cement becomes crucial. Since the customer is unable to differentiate between the shades of grey, the onus of creating this awareness is carried by the brands. That explains the heavy marketing budgets, celebrity-centric commercials, emotion-invoking taglines and campaigns enunciating the many benefits of their offerings.
Marketing strategies of cement companies have undergone gradual transformation owing to the change in consumer behaviour. While TV commercials are high on humour and emotions to establish a fast connect with the customer, social media campaigns are focussed more on capturing the consumer’s attention in an over-crowded virtual world. Branding for cement companies has become a holistic growth strategy with quantifiable results. This has made brands opt for a mix package of traditional and new-age tools, such as social media. However, the hero of every marketing communication is the message, which encapsulates the unique selling points of the product. That after all is crux of the matter here.
While cement companies are effectively using marketing tools to reach out to the consumers, they need to strengthen the four Cs of the branding process – Consumer, Cost, Communication and Convenience. Putting up the right message, at the right time and at the right place for the right kind of customer demographic is of utmost importance in the long run. It is precisely for this reason that regional players are likely to have an upper hand as they rely on local language and cultural references to drive home the point. But modern marketing and branding domain is exponentially growing and it would be an interesting exercise to tabulate and analyse its impact on branding for cement.
Concrete
Indian cement industry is well known for its energy and natural resource efficiency
Published
3 years agoon
November 18, 2022By
admin
Dr Hitesh Sukhwal, Deputy General Manager – Environment, Udaipur Cement Works Limited (UCWL) takes us through the multifaceted efforts that the company has undertaken to keep emissions in check with the use of alternative sources of energy and carbon capture technology.
Tell us about the policies of your organisation for the betterment of the environment.
Caring for people is one of the core values of our JK Lakshmi Cement Limited. We strongly believe that we all together can make a difference. In all our units, we have taken measures to reduce carbon footprint, emissions and minimise the use of natural resources. Climate change and sustainable development are major global concerns. As a responsible corporate, we are committed with and doing consistent effort small or big to preserve and enrich the environment in and around our area of operations.
As far as environmental policies are concerned, we are committed to comply with all applicable laws, standards and regulations of regulatory bodies pertaining to the environment. We are consistently making efforts to integrate the environmental concerns into the mainstream of the operations. We are giving thrust upon natural resource conservation like limestone, gypsum, water and energy. We are utilising different kinds of alternative fuels and raw materials. Awareness among the employees and local people on environmental concerns is an integral part of our company. We are adopting best environmental practices aligned with sustainable development goals.
Udaipur Cement Works Limited is a subsidiary of the JK Lakshmi Cement Limited. Since its inception, the company is committed towards boosting sustainability through adopting the latest art of technology designs, resource efficient equipment and various in-house innovations. We are giving thrust upon renewable and clean energy sources for our cement manufacturing. Solar Power and Waste Heat Recovery based power are our key ingredients for total power mix.
What impact does cement production have on the environment? Elaborate the major areas affected.
The major environmental concern areas during cement production are air emissions through point and nonpoint sources due to plant operation and emissions from mining operation, from material transport, carbon emissions through process, transit, noise pollution, vibration during mining, natural resource depletion, loss of biodiversity and change in landscape.
India is the second largest cement producer in the world. The Indian cement industry is well known for its energy and natural resource efficiency worldwide. The Indian cement industry is a frontrunner for implementing significant technology measures to ensure a greener future.
The cement industry is an energy intensive and significant contributor to climate change. Cement production contributes greenhouse gases directly and indirectly into the atmosphere through calcination and use of fossil fuels in an energy form. The industry believes in a circular economy by utilising alternative fuels for making cement. Cement companies are focusing on major areas of energy efficiency by adoption of technology measures, clinker substitution by alternative raw material for cement making, alternative fuels and green and clean energy resources. These all efforts are being done towards environment protection and sustainable future.
Nowadays, almost all cement units have a dry manufacturing process for cement production, only a few exceptions where wet manufacturing processes are in operation. In the dry manufacturing process, water is used only for the purpose of machinery cooling, which is recirculated in a closed loop, thus, no polluted water is generated during the dry manufacturing process.
We should also accept the fact that modern life is impossible without cement. However, through state-of-the-art technology and innovations, it is possible to mitigate all kinds of pollution without harm to the environment and human beings.
Tell us about the impact blended cement creates on the environment and emission rate.
Our country started cement production in 1914. However, it was introduced in the year 1904 at a small scale, earlier. Initially, the manufacturing of cement was only for Ordinary Portland Cement (OPC). In the 1980s, the production of blended cement was introduced by replacing fly ash and blast furnace slag. The production of blended cement increased in the growth period and crossed the 50 per cent in the year 2004.
The manufacturing of blended cement results in substantial savings in the thermal and electrical energy consumption as well as saving of natural resources. The overall consumption of raw materials, fossil fuel such as coal, efficient burning and state-of-the-art technology in cement plants have resulted in the gradual reduction of emission of carbon dioxide (CO2). Later, the production of blended cement was increased in manifolds.
If we think about the growth of blended cement in the past few decades, we can understand how much quantity of , (fly ash and slag) consumed and saved natural resources like limestone and fossil fuel, which were anyhow disposed of and harmed the environment. This is the reason it is called green cement. Reduction in the clinker to cement ratio has the second highest emission reduction potential i.e., 37 per cent. The low carbon roadmap for cement industries can be achieved from blended cement. Portland Pozzolana Cement (PPC), Portland Slag Cement (PSC) and Composite Cement are already approved by the National Agency BIS.
As far as kilogram CO2 per ton of cement emission concerns, Portland Slag Cement (PSC) has a larger potential, other than PPC, Composite Cement etc. for carbon emission reduction. BIS approved 60 per cent slag and 35 per cent clinker in composition of PSC. Thus, clinker per centage is quite less in PSC composition compared to other blended cement. The manufacturing of blended cement directly reduces thermal and process emissions, which contribute high in overall emissions from the cement industry, and this cannot be addressed through adoption of energy efficiency measures.
In the coming times, the cement industry must relook for other blended cement options to achieve a low carbon emissions road map. In near future, availability of fly ash and slag in terms of quality and quantity will be reduced due to various government schemes for low carbon initiatives viz. enhance renewable energy sources, waste to energy plants etc.
Further, it is required to increase awareness among consumers, like individual home builders or large infrastructure projects, to adopt greener alternatives viz. PPC and PSC for more sustainable
resource utilisation.
What are the decarbonising efforts taken by your organisation?
India is the world’s second largest cement producer. Rapid growth of big infrastructure, low-cost housing (Pradhan Mantri Awas Yojna), smart cities project and urbanisation will create cement demand in future. Being an energy intensive industry, we are also focusing upon alternative and renewable energy sources for long-term sustainable business growth for cement production.
Presently, our focus is to improve efficiency of zero carbon electricity generation technology such as waste heat recovery power through process optimisation and by adopting technological innovations in WHR power systems. We are also increasing our capacity for WHR based power and solar power in the near future. Right now, we are sourcing about 50 per cent of our power requirement from clean and renewable energy sources i.e., zero carbon electricity generation technology. Usage of alternative fuel during co-processing in the cement manufacturing process is a viable and sustainable option. In our unit, we are utilising alternative raw material and fuel for reducing carbon emissions. We are also looking forward to green logistics for our product transport in nearby areas.
By reducing clinker – cement ratio, increasing production of PPC and PSC cement, utilisation of alternative raw materials like synthetic gypsum/chemical gypsum, Jarosite generated from other process industries, we can reduce carbon emissions from cement manufacturing process. Further, we are looking forward to generating onsite fossil free electricity generation facilities by increasing the capacity of WHR based power and ground mounted solar energy plants.
We can say energy is the prime requirement of the cement industry and renewable energy is one of the major sources, which provides an opportunity to make a clean, safe and infinite source of power which is affordable for the cement industry.
What are the current programmes run by your organisation for re-building the environment and reducing pollution?
We are working in different ways for environmental aspects. As I said, we strongly believe that we all together can make a difference. We focus on every environmental aspect directly / indirectly related to our operation and surroundings.
If we talk about air pollution in operation, every section of the operational unit is well equipped with state-of-the-art technology-based air pollution control equipment (BagHouse and ESP) to mitigate the dust pollution beyond the compliance standard. We use high class standard PTFE glass fibre filter bags in our bag houses. UCWL has installed the DeNOx system (SNCR) for abatement of NOx pollution within norms. The company has installed a 6 MW capacity Waste Heat Recovery based power plant that utilises waste heat of kiln i.e., green and clean energy source. Also, installed a 14.6 MW capacity solar power system in the form of a renewable energy source.
All material transfer points are equipped with a dust extraction system. Material is stored under a covered shed to avoid secondary fugitive dust emission sources. Finished product is stored in silos. Water spraying system are mounted with material handling point. Road vacuum sweeping machine deployed for housekeeping of paved area.
In mining, have deployed wet drill machine for drilling bore holes. Controlled blasting is carried out with optimum charge using Air Decking Technique with wooden spacers and non-electric detonator (NONEL) for control of noise, fly rock, vibration, and dust emission. No secondary blasting is being done. The boulders are broken by hydraulic rock breaker. Moreover, instead of road transport, we installed Overland Belt Conveying system for crushed limestone transport from mine lease area to cement plant. Thus omit an insignificant amount of greenhouse gas emissions due to material transport, which is otherwise emitted from combustion of fossil fuel in the transport system. All point emission sources (stacks) are well equipped with online continuous emission monitoring system (OCEMS) for measuring parameters like PM, SO2 and NOx for 24×7. OCEMS data are interfaced with SPCB and CPCB servers.
The company has done considerable work upon water conservation and certified at 2.76 times water positive. We installed a digital water flow metre for each abstraction point and digital ground water level recorder for measuring ground water level 24×7. All digital metres and level recorders are monitored by an in-house designed IoT based dashboard. Through this live dashboard, we can assess the impact of rainwater harvesting (RWH) and ground water monitoring.
All points of domestic sewage are well connected with Sewage Treatment Plant (STP) and treated water is being utilised in industrial cooling purposes, green belt development and in dust suppression. Effluent Treatment Plant (ETP) installed for mine’s workshop. Treated water is reused in washing activity. The unit maintains Zero Liquid Discharge (ZLD).
Our unit has done extensive plantations of native and pollution tolerant species in industrial premises and mine lease areas. Moreover, we are not confined to our industrial boundary for plantation. We organised seedling distribution camps in our surrounding areas. We involve our stakeholders, too, for our plantation drive. UCWL has also extended its services under Corporate Social Responsibility for betterment of the environment in its surrounding. We conduct awareness programs for employees and stakeholders. We have banned Single Use Plastic (SUP) in our premises. In our industrial township, we have implemented a solid waste management system for our all households, guest house and bachelor hostel. A complete process of segregated waste (dry and wet) door to door collection systems is well established.
Tell us about the efforts taken by your organisation to better the environment in and around the manufacturing unit.
UCWL has invested capital in various environmental management and protection projects like installed DeNOx (SNCR) system, strengthening green belt development in and out of industrial premises, installed high class pollution control equipment, ground-mounted solar power plant etc.
The company has taken up various energy conservation projects like, installed VFD to reduce power consumption, improve efficiency of WHR power generation by installing additional economiser tubes and AI-based process optimisation systems. Further, we are going to increase WHR power generation capacity under our upcoming expansion project. UCWL promotes rainwater harvesting for augmentation of the ground water resource. Various scientifically based WHR structures are installed in plant premises and mine lease areas. About 80 per cent of present water requirement is being fulfilled by harvested rainwater sourced from Mine’s Pit. We are also looking forward towards green transport (CNG/LNG based), which will drastically reduce carbon footprint.
We are proud to say that JK Lakshmi Cement Limited has a strong leadership and vision for developing an eco-conscious and sustainable role model of our cement business. The company was a pioneer among cement industries of India, which had installed the DeNOx (SNCR) system in its cement plant.

Hindalco Buys US Speciality Alumina Firm for $125 Million

Star Cement launches ‘Star Smart Building Solutions’

Nuvoco Vistas reports record quarterly EBITDA

UltraTech Cement increases capacity by 1.4Mt/yr

Shree Cement reports 2025 financial year results

Hindalco Buys US Speciality Alumina Firm for $125 Million

Star Cement launches ‘Star Smart Building Solutions’

Nuvoco Vistas reports record quarterly EBITDA

UltraTech Cement increases capacity by 1.4Mt/yr
