Product development
The Opportunity in Water
Published
4 years agoon
By
admin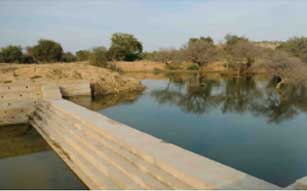
Taking a three-pronged approach, ACF commenced work to better equip the community with the resources to deal with the harsh climatic conditions ??working closely with the local people there to drive harvesting of water and groundwater recharge, creating year-round access to drinking water and promoting the judicious use of water within the community, particularly in the ??hirsty??agricultural sector, writes Pearl Tiwari of ACF.
Cement and other manufacturing companies often get a bad rap for being big consumers of water ??criticised for their consumption, and for the resulting negative impact they have on local community water resources.
But Ambuja Cements has managed to do exactly the opposite and in 2019 was an eight times water positive company ??a result of an emphasis on initiatives to both conserve water in plant operations and harvest water in communities ??eyond the fence??
Nowhere are the outcomes of this more dramatically seen, than in Rabriyawas, Rajasthan, where the once stark, arid landscape now flourishes with an abundant agricultural sector which generates prosperity for farmers, their families, and local economies.
How then, has the Indian cement giant managed to transform the region and harness the power of water as an opportunity not only for the company, but for the broader Rabriyawas region and the 63,000 people who live there?
??utside the Fence??Investment
When Ambuja Cement?? founder, Narotam Sekhsaria, took the first steps to kickstart the company in 1986, he decided to start investing in the local communities that surrounded the plant site ??in fact even before the plant itself had come up. A visionary, he knew that it was of vital importance for the community to grow and flourish alongside the company – not only would it provide licence to operate, but it would support the company?? long term sustainability agenda, build the reputation in the community as a responsible company and generate lots of goodwill along the way.
So when ACL mooted a plant in Rabriyawas in 2002, Ambuja Cement Foundation (ACF)??he company?? CSR arm??obilised to conduct a needs assessment of the area to generate ??utside the fence??strategies, and there were no surprises when water emerged as the most pressing need of the hour.
Located on the edge of the Thar Desert in Rajasthan, Rabriyawas is home to a particularly hostile climate with temperatures often skyrocketing above 50 degrees Celsius; erratic and often deficit rainfall sees the region face harsh drought every four to five years; and famine hits the region once every 50 years, causing mass migration. Despite the fragile ecosystem, acute drinking water scarcity and vulnerable livelihoods, it is still the most densely populated desert in India.
Taking a three-pronged approach, ACF commenced work to better equip the community with the resources to deal with the harsh climatic conditions ??working closely with the local people there to drive harvesting of water and groundwater recharge, creating year-round access to drinking water and promoting the judicious use of water within the community, particularly in the ??hirsty??agricultural sector. Blending both traditional techniques and modern technologies in their approach, ACF rolled up its sleeves and got to work.
Rainwater harvesting & groundwater recharge
One of the most ancient and traditional structures for rainwater harvesting in the dry desert state are ponds. In Rajasthan, it is estimated that there are about 83,000 ponds. However, the changing social milieu has meant that many of these water bodies have fallen into disrepair due to improper maintenance and the advent of modern forms of water supply. Across communities, ponds seep water, have become polluted and are full of silt, which has reduced the quality and volume of water available in ponds.
In 2003-04, ACF decided to start their work by reviving four ponds in Rabriyawas, Pali district, with the idea of making the project sustainable by involving the local community to ensure ??hey embrace and manage each pond for future generations??
Work started with the local community of Balada (Pali district) where ACF committed to the supply of machinery for de-silting of ponds. The huge manpower and transportation required for the removal of silt from the site however, was provided by the community. This soil was high in nutrients and provided a great resource to add topsoil to farmer fields and build farm bunds to trap and channel water.
Together they revived the ponds, resulting in an additional 1,25,800 cubic meters water storage capacity in Balada through multiple times deepening in the past 15 years. And the ripple effect in the community was unbelievable. Farmers were able to bring 120 acres more land under cultivation, 80 wells near the Balada pond were recharged and soil fertility improved. There was a 66 per cent decrease in dependency on piped water and 57 per cent decrease in tanker water resulting in a shift of water source especially for drinking purposes. Expenditure on water reduced 14 per cent and expenditure on health reduced by 22 per cent. And this was just the beginning.
As time passed and work scaled up, ACF has worked with communities in a similar fashion and a total of 191 village ponds have been deepened for increasing their storage capacity in the last 15 years. Of course, this was not the only intervention and a variety of other harvesting strategies were adopted, including construction of 35 khadins, 47 farm ponds, 44 check dams, one earthen dam and the widespread promotion of Roof Rainwater Harvesting Structure (RRWHS) at household and community level.
The beauty of water harvesting is that it not only captures rain as it falls for community use, but it also recharges the ground water aquifers as well ??vital to an area like Rabriyawas. According to the Central Ground Water guidelines, Rabriyawas falls under the ??ark zone??category ??one of the most serious as far as ground water availability is concerned. With no major surface water bodies like rivers lakes or canals in the area, groundwater was the principal source to fulfil demand for domestic, agriculture and industrial purposes in Rabriyawas.
With this scenario in place, ACL was concerned about water sustainability and knew it had to look well beyond its own fence and work with the entire area around its manufacturing plant to ensure an increase in the water table.
So, the recharge of groundwater became a key strategy for ACF in its efforts to transform the area and was value added by building a series of 17 subsurface dykes (subsurface barriers in sandy riverbeds.)
Subsurface dykes are a unique feature of the project area in Pali district and are an example of groundwater conservation technique for rivers having sandy beds in the arid and semi-arid regions of Rajasthan. The success story of the sub-surface dykes has demonstrated that it is one of the most feasible methods for the conservation and exploitation of the ground water resources.
Drinking water
With the average rate of depletion of the groundwater table in the Pali district more than 0.4 m per year, the over abstraction of groundwater had led to severe problems in the quality of water with a high presence of fluoride and salinity ??making it unfit for human consumption. Between 1996 and 2001, the number of villages suffering due to poor quality of drinking water in Pali went up from 13.3 per cent to 66.2 per cent.
ACF started to monitor groundwater quality to track changes due to the extensive work done on water harvesting and groundwater recharge. In 2010, total dissolvable solids were 2992 but by 2018, TDS had reduced to 808.
Meanwhile, ACF set a target to ensure water sufficiency for each household in core villages in Rabriyawas and set about supporting 2690 families for the construction of RRWHS (average capacity of 12,000 litres) in the area to meet the potable water requirements at household level. The tanks were enough to meet the year-round requirement of families in the area and had a dramatic impact on health indicators. For example, there was a reduction in the prevalence of fluoride and kidney stones among the population and 98.04 per cent of beneficiaries highlighted a positive influence on their health, due to improvements in drinking water quality.
Improving water use efficiency in agriculture
A key issue that needed to be addressed was the inefficient use of water in the area, particularly within the agricultural sector, as water demand management is vital in order for local people to manage and conserve the water they have available. The productivity of water is improved through the promotion of water efficient irrigation methods and by creating awareness among farmers of necessary behaviour change.
ACF?? approach was to demonstrate the use of micro irrigation (drip and sprinkler systems) and promote its benefits. This was necessary as the adoption of this technology requires a significant investment by farmers. Slowly as a few farmers came forward to adopt it, others witnessed the resultant increase in yield, saving of water, reduced energy consumption, and reduced labour requirement and cost, and followed suit. Over time, a total of 510 farmers have adopted micro irrigation saving 2.78 million cubic meters (mcm) of water in the process.
Today there is an increase in crop intensity from a single crop per year, to double and triple crops by using micro irrigation and farm ponds. Once barren land has been transformed thanks to irrigation and soil treatment and is now being utilised by farmers. About 97 per cent of farmers have increased crop yields due to the availability of water.
Community impacts
In Rabriyawas, with a total investment of Rs 8.2 crore over 15 years of work, ACF has impacted 65,000 people, increased groundwater levels by 2 to 12 m, and generated over 16.33 mcm additional water storage. Water availability at household level reduced women drudgery and saved time with a value ranging from one to four hours per day in the project area.
Additionally, an independent study indicated a five times social return on every rupee invested in water resource management in Rabriyawas, as the ripple effect of water generated positive impacts on other areas of community life like health, education, and employment.
??nside the Fence??strategies
Although ACL uses a dry process of cement production which uses minimal water, water conservation and its sustainability remains on a high pedestal in the company?? overall Sustainable Development plan with aspirational targets for 2030.
??nside of the fence??at Rabriyawas, ACL employs many strategies to recycle, reuse and reduce its use of water in its operations. Several water efficiency measures have been put in place, like the installation of waste heat recovery, roller press, dip tube in lower stage cyclone, raw water storage tank (10,000 KL), and air cooled air compressors and dryers. The plant recycles about 70,000 cubic meters of water (14 per cent of water withdrawal) which is helping the plant to reduce its overall water withdrawal.
On site there is a revival of water harvesting which saw the connection of water-logged area to main drainage lines. There is also a sewage treatment plant installed and all the waste water discharged from the plant and colonies are directed to this treatment plant, which in turn is used for horticulture purposes in the plant areas.
Even the employees have gotten involved. Work is being done to motivate and reward employees for playing a role in water conservation and there is a number of water awareness campaigns run throughout the year at the plant and in the Ambuja colonies. A water management committee was formed which takes care of the level of water used, efficiency and conservation. Frequent water talks and seminars are organised for the employees and a ??ater Hero Award??is granted every year to that department who has made sufficient efforts to reduce the use of water for its work in the plant. World Water Day is also celebrated at the plant.
The culmination of all these strategies has made the Rabriyawas plant one of the most efficient plants at Ambuja Cements and today it is almost 34 times water positive.
Of course much more is being done at a national level within the company, and innovative products and services have been developed to reduce the consumption of water at customer end. Modular curing solutions (MCS) is a unique curing application which does not require extra water flooding after roof slab casting for curing. MCS enhances the hydration process by preventing moisture evaporation from concrete and thus typically saves about 12,000 litres of water in curing 1,000 square feet of slab surface.
In 2019, ACL across locations, enabled customers for water saving of around 223 million litres at the customer front where its Technical Services team provided water optimisation in concrete mix proportions at 43433 sites (saving about 54 million litres of water onsite), modular curing solutions (MCS) at 7,714 sites (saving about 93 million litres of water onsite) and rain water harvesting (RWH) solutions at 893 sites (harvesting about 76 million litres of rain water). These were construction sites on the customer side of the supply chain in many parts of the country where often water availability and quality were a challenge.
Conclusion
Water is a critical need for most regions in India and has emerged as a single common agenda among several locations where Ambuja Cements has spread its wings over the last two decades. As a shared resource locally, this lever creates business value by leveraging strategic social investment to address water related risks in the community around plant operations. By harnessing both inside and outside the fence strategies, ACF has developed a significant water positive status, which continues to grow year after year.
The work by ACF in Rabriyawas is just one example of how that opportunity presents a win-win for all stakeholders and its success was integral to the awarding of the Jal Shakti Ministry?? annual National Water Mission Awards under the category ??ocused attention to vulnerable areas including over-exploited areas??to ACF in 2019.
It also highlights how, by tackling this important issue and optimising water for both business and community, today and for the future, water presents an exciting opportunity to industries that rely on it as a core resource for their business.
ABOUT THE AUTHOR:
Pearl Tiwari, Director & CEO, Ambuja Cement Foundation. Tiwari is a social development professional having worked in this area across diverse academic, NGO and CSR roles. A post-graduate from Tata Institute of Social Sciences (TISS) with 37 years of experience in the development sector.
You may like
Concrete
Conveyor belts are a vital link in the supply chain
Published
3 months agoon
June 16, 2025By
admin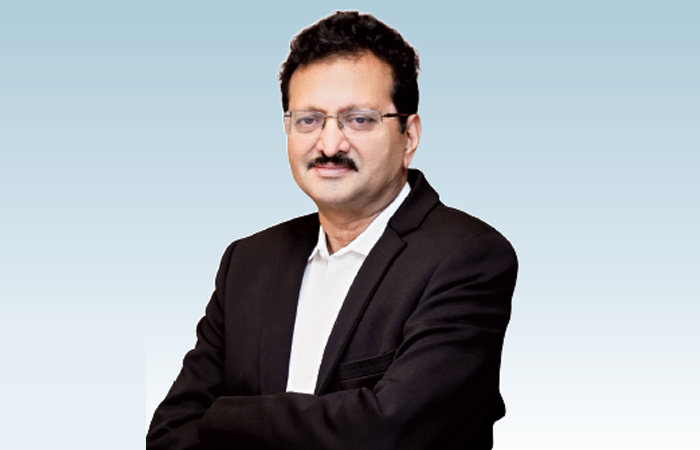
Kamlesh Jain, Managing Director, Elastocon, discusses how the brand delivers high-performance, customised conveyor belt solutions for demanding industries like cement, mining, and logistics, while embracing innovation, automation, and sustainability.
In today’s rapidly evolving industrial landscape, efficient material handling isn’t just a necessity—it’s a competitive advantage. As industries such as mining, cement, steel and logistics push for higher productivity, automation, and sustainability, the humble conveyor belt has taken on a mission-critical role. In this exclusive interview, Kamlesh Jain, Managing Director, Elastocon, discusses how the company is innovating for tougher terrains, smarter systems and a greener tomorrow.
Brief us about your company – in terms of its offerings, manufacturing facilities, and the key end-user industries it serves.
Elastocon, a flagship brand of the Royal Group, is a trusted name in the conveyor belt manufacturing industry. Under the brand name ELASTOCON, the company produces both open-end and endless belts, offering tailor-made solutions to some of the most demanding sectors such as cement, steel, power, mining, fertiliser, and logistics. Every belt is meticulously engineered—from fabric selection to material composition—to ensure optimal performance in tough working conditions. With advanced manufacturing facilities and strict quality protocols, Elastocon continues to deliver high-performance conveyor solutions designed for durability, safety, and efficiency.
How is the group addressing the needs for efficient material handling?
Efficient material handling is the backbone of any industrial operation. At Elastocon, our engineering philosophy revolves around creating belts that deliver consistent performance, long operational life, and minimal maintenance. We focus on key performance parameters such as tensile strength, abrasion resistance, tear strength, and low elongation at working tension. Our belts are designed to offer superior bonding between plies and covers, which directly impacts their life and reliability. We also support clients
with maintenance manuals and technical advice, helping them improve their system’s productivity and reduce downtime.
How critical are conveyor belts in ensuring seamless material handling?
Conveyor belts are a vital link in the supply chain across industries. In sectors like mining, cement, steel, and logistics, they facilitate the efficient movement of materials and help maintain uninterrupted production flows. At Elastocon, we recognise the crucial role of belts in minimising breakdowns and increasing plant uptime. Our belts are built to endure abrasive, high-temperature, or high-load environments. We also advocate proper system maintenance, including correct belt storage, jointing, roller alignment, and idler checks, to ensure smooth and centered belt movement, reducing operational interruptions.
What are the key market and demand drivers for the conveyor belt industry?
The growth of the conveyor belt industry is closely tied to infrastructure development, increased automation, and the push for higher operational efficiency. As industries strive to reduce labor dependency and improve productivity, there is a growing demand for advanced material handling systems. Customers today seek not just reliability, but also cost-effectiveness and technical superiority in the belts they choose. Enhanced product aesthetics and innovation in design are also becoming significant differentiators. These trends are pushing manufacturers to evolve continuously, and Elastocon is leading the way with customer-centric product development.
How does Elastocon address the diverse and evolving requirements of these sectors?
Our strength lies in offering a broad and technically advanced product portfolio that serves various industries. For general-purpose applications, our M24 and DINX/W grade belts offer excellent abrasion resistance, especially for RMHS and cement plants. For high-temperature operations, we provide HR and SHR T2 grade belts, as well as our flagship PYROCON and PYROKING belts, which can withstand extreme heat—up to 250°C continuous and even 400°C peak—thanks to advanced EPM polymers.
We also cater to sectors with specialised needs. For fire-prone environments like underground mining, we offer fire-resistant belts certified to IS 1891 Part V, ISO 340, and MSHA standards. Our OR-grade belts are designed for oil and chemical resistance, making them ideal for fertiliser and chemical industries. In high-moisture applications like food and agriculture, our MR-grade belts ensure optimal performance. This diverse range enables us to meet customer-specific challenges with precision and efficiency.
What core advantages does Elastocon offer that differentiate it from competitors?
Elastocon stands out due to its deep commitment to quality, innovation, and customer satisfaction. Every belt is customised to the client’s requirements, supported by a strong R&D foundation that keeps us aligned with global standards and trends. Our customer support doesn’t end at product delivery—we provide ongoing technical assistance and after-sales service that help clients maximise the value of their investments. Moreover, our focus on compliance and certifications ensures our belts meet stringent national and international safety and performance standards, giving customers added confidence.
How is Elastocon gearing up to meet its customers’ evolving needs?
We are conscious of the shift towards greener and smarter manufacturing practices. Elastocon is embracing sustainability by incorporating eco-friendly materials and energy-efficient manufacturing techniques. In parallel, we are developing belts that seamlessly integrate with automated systems and smart industrial platforms. Our vision is to make our products not just high-performing but also future-ready—aligned with global sustainability goals and compatible with emerging technologies in industrial automation and predictive maintenance.
What trends do you foresee shaping the future of the conveyor belt industry?
The conveyor belt industry is undergoing a significant transformation. As Industry 4.0 principles gain traction, we expect to see widespread adoption of smart belts equipped with sensors for real-time monitoring, diagnostics, and predictive maintenance. The demand for recyclable materials and sustainable designs will continue to grow. Furthermore, industry-specific customisation will increasingly replace standardisation, and belts will be expected to do more than just transport material—they will be integrated into intelligent production systems. Elastocon is already investing in these future-focused areas to stay ahead of the curve.

Advertising or branding is never about driving sales. It’s about creating brand awareness and recall. It’s about conveying the core values of your brand to your consumers. In this context, why is branding important for cement companies? As far as the customers are concerned cement is simply cement. It is precisely for this reason that branding, marketing and advertising of cement becomes crucial. Since the customer is unable to differentiate between the shades of grey, the onus of creating this awareness is carried by the brands. That explains the heavy marketing budgets, celebrity-centric commercials, emotion-invoking taglines and campaigns enunciating the many benefits of their offerings.
Marketing strategies of cement companies have undergone gradual transformation owing to the change in consumer behaviour. While TV commercials are high on humour and emotions to establish a fast connect with the customer, social media campaigns are focussed more on capturing the consumer’s attention in an over-crowded virtual world. Branding for cement companies has become a holistic growth strategy with quantifiable results. This has made brands opt for a mix package of traditional and new-age tools, such as social media. However, the hero of every marketing communication is the message, which encapsulates the unique selling points of the product. That after all is crux of the matter here.
While cement companies are effectively using marketing tools to reach out to the consumers, they need to strengthen the four Cs of the branding process – Consumer, Cost, Communication and Convenience. Putting up the right message, at the right time and at the right place for the right kind of customer demographic is of utmost importance in the long run. It is precisely for this reason that regional players are likely to have an upper hand as they rely on local language and cultural references to drive home the point. But modern marketing and branding domain is exponentially growing and it would be an interesting exercise to tabulate and analyse its impact on branding for cement.
Concrete
Indian cement industry is well known for its energy and natural resource efficiency
Published
3 years agoon
November 18, 2022By
admin
Dr Hitesh Sukhwal, Deputy General Manager – Environment, Udaipur Cement Works Limited (UCWL) takes us through the multifaceted efforts that the company has undertaken to keep emissions in check with the use of alternative sources of energy and carbon capture technology.
Tell us about the policies of your organisation for the betterment of the environment.
Caring for people is one of the core values of our JK Lakshmi Cement Limited. We strongly believe that we all together can make a difference. In all our units, we have taken measures to reduce carbon footprint, emissions and minimise the use of natural resources. Climate change and sustainable development are major global concerns. As a responsible corporate, we are committed with and doing consistent effort small or big to preserve and enrich the environment in and around our area of operations.
As far as environmental policies are concerned, we are committed to comply with all applicable laws, standards and regulations of regulatory bodies pertaining to the environment. We are consistently making efforts to integrate the environmental concerns into the mainstream of the operations. We are giving thrust upon natural resource conservation like limestone, gypsum, water and energy. We are utilising different kinds of alternative fuels and raw materials. Awareness among the employees and local people on environmental concerns is an integral part of our company. We are adopting best environmental practices aligned with sustainable development goals.
Udaipur Cement Works Limited is a subsidiary of the JK Lakshmi Cement Limited. Since its inception, the company is committed towards boosting sustainability through adopting the latest art of technology designs, resource efficient equipment and various in-house innovations. We are giving thrust upon renewable and clean energy sources for our cement manufacturing. Solar Power and Waste Heat Recovery based power are our key ingredients for total power mix.
What impact does cement production have on the environment? Elaborate the major areas affected.
The major environmental concern areas during cement production are air emissions through point and nonpoint sources due to plant operation and emissions from mining operation, from material transport, carbon emissions through process, transit, noise pollution, vibration during mining, natural resource depletion, loss of biodiversity and change in landscape.
India is the second largest cement producer in the world. The Indian cement industry is well known for its energy and natural resource efficiency worldwide. The Indian cement industry is a frontrunner for implementing significant technology measures to ensure a greener future.
The cement industry is an energy intensive and significant contributor to climate change. Cement production contributes greenhouse gases directly and indirectly into the atmosphere through calcination and use of fossil fuels in an energy form. The industry believes in a circular economy by utilising alternative fuels for making cement. Cement companies are focusing on major areas of energy efficiency by adoption of technology measures, clinker substitution by alternative raw material for cement making, alternative fuels and green and clean energy resources. These all efforts are being done towards environment protection and sustainable future.
Nowadays, almost all cement units have a dry manufacturing process for cement production, only a few exceptions where wet manufacturing processes are in operation. In the dry manufacturing process, water is used only for the purpose of machinery cooling, which is recirculated in a closed loop, thus, no polluted water is generated during the dry manufacturing process.
We should also accept the fact that modern life is impossible without cement. However, through state-of-the-art technology and innovations, it is possible to mitigate all kinds of pollution without harm to the environment and human beings.
Tell us about the impact blended cement creates on the environment and emission rate.
Our country started cement production in 1914. However, it was introduced in the year 1904 at a small scale, earlier. Initially, the manufacturing of cement was only for Ordinary Portland Cement (OPC). In the 1980s, the production of blended cement was introduced by replacing fly ash and blast furnace slag. The production of blended cement increased in the growth period and crossed the 50 per cent in the year 2004.
The manufacturing of blended cement results in substantial savings in the thermal and electrical energy consumption as well as saving of natural resources. The overall consumption of raw materials, fossil fuel such as coal, efficient burning and state-of-the-art technology in cement plants have resulted in the gradual reduction of emission of carbon dioxide (CO2). Later, the production of blended cement was increased in manifolds.
If we think about the growth of blended cement in the past few decades, we can understand how much quantity of , (fly ash and slag) consumed and saved natural resources like limestone and fossil fuel, which were anyhow disposed of and harmed the environment. This is the reason it is called green cement. Reduction in the clinker to cement ratio has the second highest emission reduction potential i.e., 37 per cent. The low carbon roadmap for cement industries can be achieved from blended cement. Portland Pozzolana Cement (PPC), Portland Slag Cement (PSC) and Composite Cement are already approved by the National Agency BIS.
As far as kilogram CO2 per ton of cement emission concerns, Portland Slag Cement (PSC) has a larger potential, other than PPC, Composite Cement etc. for carbon emission reduction. BIS approved 60 per cent slag and 35 per cent clinker in composition of PSC. Thus, clinker per centage is quite less in PSC composition compared to other blended cement. The manufacturing of blended cement directly reduces thermal and process emissions, which contribute high in overall emissions from the cement industry, and this cannot be addressed through adoption of energy efficiency measures.
In the coming times, the cement industry must relook for other blended cement options to achieve a low carbon emissions road map. In near future, availability of fly ash and slag in terms of quality and quantity will be reduced due to various government schemes for low carbon initiatives viz. enhance renewable energy sources, waste to energy plants etc.
Further, it is required to increase awareness among consumers, like individual home builders or large infrastructure projects, to adopt greener alternatives viz. PPC and PSC for more sustainable
resource utilisation.
What are the decarbonising efforts taken by your organisation?
India is the world’s second largest cement producer. Rapid growth of big infrastructure, low-cost housing (Pradhan Mantri Awas Yojna), smart cities project and urbanisation will create cement demand in future. Being an energy intensive industry, we are also focusing upon alternative and renewable energy sources for long-term sustainable business growth for cement production.
Presently, our focus is to improve efficiency of zero carbon electricity generation technology such as waste heat recovery power through process optimisation and by adopting technological innovations in WHR power systems. We are also increasing our capacity for WHR based power and solar power in the near future. Right now, we are sourcing about 50 per cent of our power requirement from clean and renewable energy sources i.e., zero carbon electricity generation technology. Usage of alternative fuel during co-processing in the cement manufacturing process is a viable and sustainable option. In our unit, we are utilising alternative raw material and fuel for reducing carbon emissions. We are also looking forward to green logistics for our product transport in nearby areas.
By reducing clinker – cement ratio, increasing production of PPC and PSC cement, utilisation of alternative raw materials like synthetic gypsum/chemical gypsum, Jarosite generated from other process industries, we can reduce carbon emissions from cement manufacturing process. Further, we are looking forward to generating onsite fossil free electricity generation facilities by increasing the capacity of WHR based power and ground mounted solar energy plants.
We can say energy is the prime requirement of the cement industry and renewable energy is one of the major sources, which provides an opportunity to make a clean, safe and infinite source of power which is affordable for the cement industry.
What are the current programmes run by your organisation for re-building the environment and reducing pollution?
We are working in different ways for environmental aspects. As I said, we strongly believe that we all together can make a difference. We focus on every environmental aspect directly / indirectly related to our operation and surroundings.
If we talk about air pollution in operation, every section of the operational unit is well equipped with state-of-the-art technology-based air pollution control equipment (BagHouse and ESP) to mitigate the dust pollution beyond the compliance standard. We use high class standard PTFE glass fibre filter bags in our bag houses. UCWL has installed the DeNOx system (SNCR) for abatement of NOx pollution within norms. The company has installed a 6 MW capacity Waste Heat Recovery based power plant that utilises waste heat of kiln i.e., green and clean energy source. Also, installed a 14.6 MW capacity solar power system in the form of a renewable energy source.
All material transfer points are equipped with a dust extraction system. Material is stored under a covered shed to avoid secondary fugitive dust emission sources. Finished product is stored in silos. Water spraying system are mounted with material handling point. Road vacuum sweeping machine deployed for housekeeping of paved area.
In mining, have deployed wet drill machine for drilling bore holes. Controlled blasting is carried out with optimum charge using Air Decking Technique with wooden spacers and non-electric detonator (NONEL) for control of noise, fly rock, vibration, and dust emission. No secondary blasting is being done. The boulders are broken by hydraulic rock breaker. Moreover, instead of road transport, we installed Overland Belt Conveying system for crushed limestone transport from mine lease area to cement plant. Thus omit an insignificant amount of greenhouse gas emissions due to material transport, which is otherwise emitted from combustion of fossil fuel in the transport system. All point emission sources (stacks) are well equipped with online continuous emission monitoring system (OCEMS) for measuring parameters like PM, SO2 and NOx for 24×7. OCEMS data are interfaced with SPCB and CPCB servers.
The company has done considerable work upon water conservation and certified at 2.76 times water positive. We installed a digital water flow metre for each abstraction point and digital ground water level recorder for measuring ground water level 24×7. All digital metres and level recorders are monitored by an in-house designed IoT based dashboard. Through this live dashboard, we can assess the impact of rainwater harvesting (RWH) and ground water monitoring.
All points of domestic sewage are well connected with Sewage Treatment Plant (STP) and treated water is being utilised in industrial cooling purposes, green belt development and in dust suppression. Effluent Treatment Plant (ETP) installed for mine’s workshop. Treated water is reused in washing activity. The unit maintains Zero Liquid Discharge (ZLD).
Our unit has done extensive plantations of native and pollution tolerant species in industrial premises and mine lease areas. Moreover, we are not confined to our industrial boundary for plantation. We organised seedling distribution camps in our surrounding areas. We involve our stakeholders, too, for our plantation drive. UCWL has also extended its services under Corporate Social Responsibility for betterment of the environment in its surrounding. We conduct awareness programs for employees and stakeholders. We have banned Single Use Plastic (SUP) in our premises. In our industrial township, we have implemented a solid waste management system for our all households, guest house and bachelor hostel. A complete process of segregated waste (dry and wet) door to door collection systems is well established.
Tell us about the efforts taken by your organisation to better the environment in and around the manufacturing unit.
UCWL has invested capital in various environmental management and protection projects like installed DeNOx (SNCR) system, strengthening green belt development in and out of industrial premises, installed high class pollution control equipment, ground-mounted solar power plant etc.
The company has taken up various energy conservation projects like, installed VFD to reduce power consumption, improve efficiency of WHR power generation by installing additional economiser tubes and AI-based process optimisation systems. Further, we are going to increase WHR power generation capacity under our upcoming expansion project. UCWL promotes rainwater harvesting for augmentation of the ground water resource. Various scientifically based WHR structures are installed in plant premises and mine lease areas. About 80 per cent of present water requirement is being fulfilled by harvested rainwater sourced from Mine’s Pit. We are also looking forward towards green transport (CNG/LNG based), which will drastically reduce carbon footprint.
We are proud to say that JK Lakshmi Cement Limited has a strong leadership and vision for developing an eco-conscious and sustainable role model of our cement business. The company was a pioneer among cement industries of India, which had installed the DeNOx (SNCR) system in its cement plant.