Environment
Cement industry has become more cost effective and efficient by implementing environmental regulation.
Published
6 years agoon
By
admin
Wonder Cement is a cement manufacturing company, enriched with the heritage of R.K. Marble, a leading name in the marble industry. The cement plant is located in Nimbahera, District Chittorgarhin Rajasthan, with three production lines, has a capacity of producing 9.50 Million Tons Per Annum (MTPA) of clinker. With the commencement of grinding unit in Dhule, Maharashtra and Bhadnawar, Madhya Pradesh, with the capacity of 2 MTPA each, it’s cement manufacturing capacity has increased to 11MTPA. Now, the company is going to commission its third grinding unit in Jhajjar, Haryana so as to facilitate an increase in combined production capacity of 13 MTPA by January, 2021.
Interview with Vivek Patni, Director, Wonder Cement
1.How do you see the year ahead in terms of sale and capacity utilization post pandemic of Covid-19? How about the revival of construction sector?
We see the demand revival from October – December 2020 quarter. We see capacity utilization to be in the range from 65% to 70% on all India basis However, in North region, where we are working, capacity utilization will be in the range of 75%.
2.How has environmental regulation affected the cement industry in the past one decade and how do you expect it to influence it over the next decade?
The Cement Industry has responded to environment regulation very positively. The industry has become more clean and green in last two decade. The industry under its responsibility towards environment has implemented the regulation very effectively. I feel that industry has become more cost effective and efficient by implementing environmental regulation.
The Industry is continuously working on reduction of Greenhouses Gases.
3.What impact you think this will have on the competitiveness of the cement industry, the cost of production, product quality and profitability?
The Cement Industry has become more cost effective by implementing stringent environment regulations. The carbon foot print has reduced by increasing blended Cement, WHRS installation and uses of alternate fuels and Raw materials. These measures not only made industry more environmentally friendly but it reduces the Cost of Production and also improves its efficiency parameters.
4.What are the chances of climate change groups directly or indirectly influencing the Indian cement industry in terms of limiting capacity additions, affecting the choice of fuels, influencing the product mix, etc? What are likely to be the future drivers?
The climate change groups are becoming more and more active. These groups will ask for reduction of CO2 and Nox (both are greenhouses gases). With the new development in technologies and research going, CO2 capturing will be possible. With changes in Cement manufacturing process, Nox reduction is also very much possible. However, the new technology of CO2 capturing and Nox reduction becoming technically and commercially viable may take some time but it will be possible to reduce/minimize the impact on climate change by technology adoption.
The real challenges on capacity addition/size of plant are from the land owners in the context of cement industry. With the new regulations of land acquisition, it is becoming very difficult to acquire the mining and plant land. Therefore, I see bigger challenges from Environmentalist on account of land acquisition and rehabilitation of project affected area.
5.How has the implementation of the latest environmental norms in the cement industry fared so far and how do you see it faring in the future, in terms of the ease or difficulty in the actual implementation of the environmental norms, financial impact, technical difficulties, etc. and do you think these norms need any re-visit?
The implementation of latest regulations of Environment did not pose big challenge. The industry has adopted and implemented regulations upto great extent. The new regulations of SPM of 30 mg/NM3 are very well adopted by industry. The Indian Cement Industry is working on controlling NOx as prescribed by regulating authorities.
Achieving the latest regulations on NOx has been a challenge for industry. The industry is in process of installing SCNR and also re-designing the process to minimize NOx generations.
The regulations of Land Acquisition and rehabilitation are bigger challenges. The land acquisition is delayed the project implementations.
The other challenges for industry are drawing of underground water. Because of NGT orders, it has become very difficult to get permission/renewal ground water withdrawal. However, industry is switching over to technology where water consumption can be minimized/eliminated. One such example is the raw material grinding in roll press. Grate cooler is designed without water spray. The ESP is being replaced with Bag filters to avoid uses of water.
6.What is your expectation in the availability and pricing of coal in India over the next decade? Is there a likelihood of environmental groups effectively dissuading the industry from using coal? What alternatives are likely to arise?
I do not see availability of Coal for manufacturing Cement will be a constraint during next decade. However, the Industry focus will be there to reduce uses of Fossil Fuel. Following will be the drives:
(i)Increase uses of Alternate Fuel like Industrial Waste and Bio Mass.
(ii)Reduction of specific power and fuel consumption.
(iii)More and more uses of Power Generated from Waste Heat.
(iv)Increase of share of Renewal Energy
(v)The present TSR (Thermal Substitution Rate) in Indian Cement Industry is around 3 to 5%. However, industry is now putting of equipment and machinery gearing upto use all type of Waste material generated by industrial units. The Bio mass is already being utilized in Cement Kiln and Power Plants.
7.What has been the extent of Alternative Fuels & Raw Materials (AFR) usage in the cement industry in general and your cement plants in particular in the past and how much Thermal Substitution Rate (TSR) do you think we can achieve over the next decade?
The present TSR in Cement Industry is around 5%. With growing awareness about disposal of waste in Cement Kilns, I am very sure that TSR is going to increase in days to come.
The Cement Industry is gearing up to dispose of any type of waste material in their Kilns by installing waste handling and processing Equipment.
We at Wonder Cement have started working on uses of AFR. The Capex has been sanctioned. The installation work is in progress. We expect to start using AFR by 2021.
I feel by next decade, the Industry will have minimum TSR of 25%. The challenges in increasing the uses of AFR are getting clearance of Pollution Board.
8.How has information technology impacted the cement industry in the past two decades and how do you expect it to change over the next decade? What are likely to be the future drivers?
The IT had played key role in the manufacturing process of Cement. More and more processes are being automated. In coming year, Industry will adopt many tools to monitor sales and will strengthen sales force to improve their sales, generate leads and convert leads to sales. IT will have bigger role in controlling logistic cost by way optimizing whereas locations, distributions from plant and warehouses, it will also optimizing fleet size. The Industry is moving paper less operations.
9.How the deteriorating limestone quality in future will have impact on cement manufacturing in next 10 years. What type of innovations in equipment or Process Technology do you foresee to tackle this problem?
Lime stone beneficiation will be the key to use low grade lime stone quality. Lot of R & D work is being done for beneficiation of Lime Stone. Wonder Cement is also working on such project for beneficiation.
Vivek Patni is the young member of Patni family and Director of Wonder Cement.
You may like
Concrete
India donates 225t of cement for Myanmar earthquake relief
Published
4 weeks agoon
June 17, 2025By
admin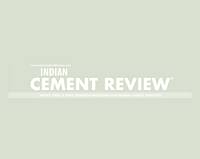
On 23 May 2025, the Indian Navy ship UMS Myitkyina arrived at Thilawa (MITT) port carrying 225 tonnes of cement provided by the Indian government to aid post-earthquake rebuilding efforts in Myanmar. As reported by the Global Light of Myanmar, a formal handover of 4500 50kg cement bags took place that afternoon. The Yangon Region authorities managed the loading of the cement onto trucks for distribution to the earthquake-affected zones.
Concrete
Reclamation of Used Oil for a Greener Future
Published
4 weeks agoon
June 16, 2025By
admin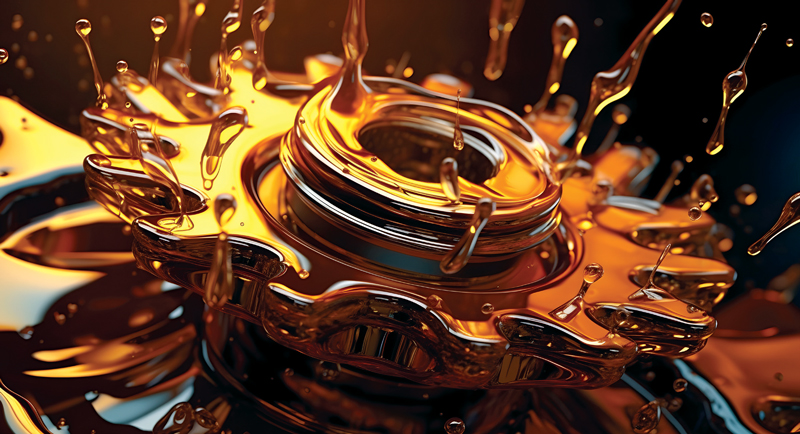
In this insightful article, KB Mathur, Founder and Director, Global Technical Services, explores how reclaiming used lubricants through advanced filtration and on-site testing can drive cost savings, enhance productivity, and support a greener industrial future. Read on to discover how oil regeneration is revolutionising sustainability in cement and core industries.
The core principle of the circular economy is to redefine the life cycle of materials and products. Unlike traditional linear models where waste from industrial production is dumped/discarded into the environment causing immense harm to the environment;the circular model seeks to keep materials literally in continuous circulation. This is achievedthrough processes cycle of reduction, regeneration, validating (testing) and reuse. Product once
validated as fit, this model ensures that products and materials are reintroduced into the production system, minimising waste. The result? Cleaner and greener manufacturing that fosters a more sustainable planet for future generations.
The current landscape of lubricants
Modern lubricants, typically derived from refined hydrocarbons, made from highly refined petroleum base stocks from crude oil. These play a critical role in maintaining the performance of machinery by reducing friction, enabling smooth operation, preventing damage and wear. However, most of these lubricants; derived from finite petroleum resources pose an environmental challenge once used and disposed of. As industries become increasingly conscious of their environmental impact, the paramount importance or focus is shifting towards reducing the carbon footprint and maximising the lifespan of lubricants; not just for environmental reasons but also to optimise operational costs.
During operations, lubricants often lose their efficacy and performance due to contamination and depletion of additives. When these oils reach their rejection limits (as they will now offer poor or bad lubrication) determined through laboratory testing, they are typically discarded contributing to environmental contamination and pollution.
But here lies an opportunity: Used lubricants can be regenerated and recharged, restoring them to their original performance level. This not only mitigates environmental pollution but also supports a circular economy by reducing waste and conserving resources.
Circular economy in lubricants
In the world of industrial machinery, lubricating oils while essential; are often misunderstood in terms of their life cycle. When oils are used in machinery, they don’t simply ‘DIE’. Instead, they become contaminated with moisture (water) and solid contaminants like dust, dirt, and wear debris. These contaminants degrade the oil’s effectiveness but do not render it completely unusable. Used lubricants can be regenerated via advanced filtration processes/systems and recharged with the use of performance enhancing additives hence restoring them. These oils are brought back to ‘As-New’ levels. This new fresher lubricating oil is formulated to carry out its specific job providing heightened lubrication and reliable performance of the assets with a view of improved machine condition. Hence, contributing to not just cost savings but leading to magnified productivity, and diminished environmental stress.
Save oil, save environment
At Global Technical Services (GTS), we specialise in the regeneration of hydraulic oils and gear oils used in plant operations. While we don’t recommend the regeneration of engine oils due to the complexity of contaminants and additives, our process ensures the continued utility of oils in other applications, offering both cost-saving and environmental benefits.
Regeneration process
Our regeneration plant employs state-of-the-art advanced contamination removal systems including fine and depth filters designed to remove dirt, wear particles, sludge, varnish, and water. Once contaminants are removed, the oil undergoes comprehensive testing to assess its physico-chemical properties and contamination levels. The test results indicate the status of the regenerated oil as compared to the fresh oil.
Depending upon the status the oil is further supplemented with high performance additives to bring it back to the desired specifications, under the guidance of an experienced lubrication technologist.
Contamination Removal ? Testing ? Additive Addition
(to be determined after testing in oil test laboratory)
The steps involved in this process are as follows:
1. Contamination removal: Using advanced filtration techniques to remove contaminants.
2. Testing: Assessing the oil’s properties to determine if it meets the required performance standards.
3. Additive addition: Based on testing results, performance-enhancing additives are added to restore the oil’s original characteristics.
On-site oil testing laboratories
The used oil from the machine passes through 5th generation fine filtration to be reclaimed as ‘New Oil’ and fit to use as per stringent industry standards.
To effectively implement circular economy principles in oil reclamation from used oil, establishing an on-site oil testing laboratory is crucial at any large plants or sites. Scientific testing methods ensure that regenerated oil meets the specifications required for optimal machine performance, making it suitable for reuse as ‘New Oil’ (within specified tolerances). Hence, it can be reused safely by reintroducing it in the machines.
The key parameters to be tested for regenerated hydraulic, gear and transmission oils (except Engine oils) include both physical and chemical characteristics of the lubricant:
- Kinematic Viscosity
- Flash Point
- Total Acid Number
- Moisture / Water Content
- Oil Cleanliness
- Elemental Analysis (Particulates, Additives and Contaminants)
- Insoluble
The presence of an on-site laboratory is essential for making quick decisions; ensuring that test reports are available within 36 to 48 hours and this prevents potential mechanical issues/ failures from arising due to poor lubrication. This symbiotic and cyclic process helps not only reduce waste and conserve oil, but also contributes in achieving cost savings and playing a big role in green economy.
Conclusion
The future of industrial operations depends on sustainability, and reclaiming used lubricating oils plays a critical role in this transformation. Through 5th Generation Filtration processes, lubricants can be regenerated and restored to their original levels, contributing to both environmental preservation and economic efficiency.
What would happen if we didn’t recycle our lubricants? Let’s review the quadruple impacts as mentioned below:
1. Oil Conservation and Environmental Impact: Used lubricating oils after usage are normally burnt or sold to a vendor which can be misused leading to pollution. Regenerating oils rather than discarding prevents unnecessary waste and reduces the environmental footprint of the industry. It helps save invaluable resources, aligning with the principles of sustainability and the circular economy. All lubricating oils (except engine oils) can be regenerated and brought to the level of ‘As New Oils’.
2. Cost Reduction Impact: By extending the life of lubricants, industries can significantly cut down on operating costs associated with frequent oil changes, leading to considerable savings over time. Lubricating oils are expensive and saving of lubricants by the process of regeneration will overall be a game changer and highly economical to the core industries.
3. Timely Decisions Impact: Having an oil testing laboratory at site is of prime importance for getting test reports within 36 to 48 hours enabling quick decisions in critical matters that may
lead to complete shutdown of the invaluable asset/equipment.
4. Green Economy Impact: Oil Regeneration is a fundamental part of the green economy. Supporting industries in their efforts to reduce waste, conserve resources, and minimise pollution is ‘The Need of Our Times’.
About the author:
KB Mathur, Founder & Director, Global Technical Services, is a seasoned mechanical engineer with 56 years of experience in India’s oil industry and industrial reliability. He pioneered ‘Total Lubrication Management’ and has been serving the mining and cement sectors since 1999.
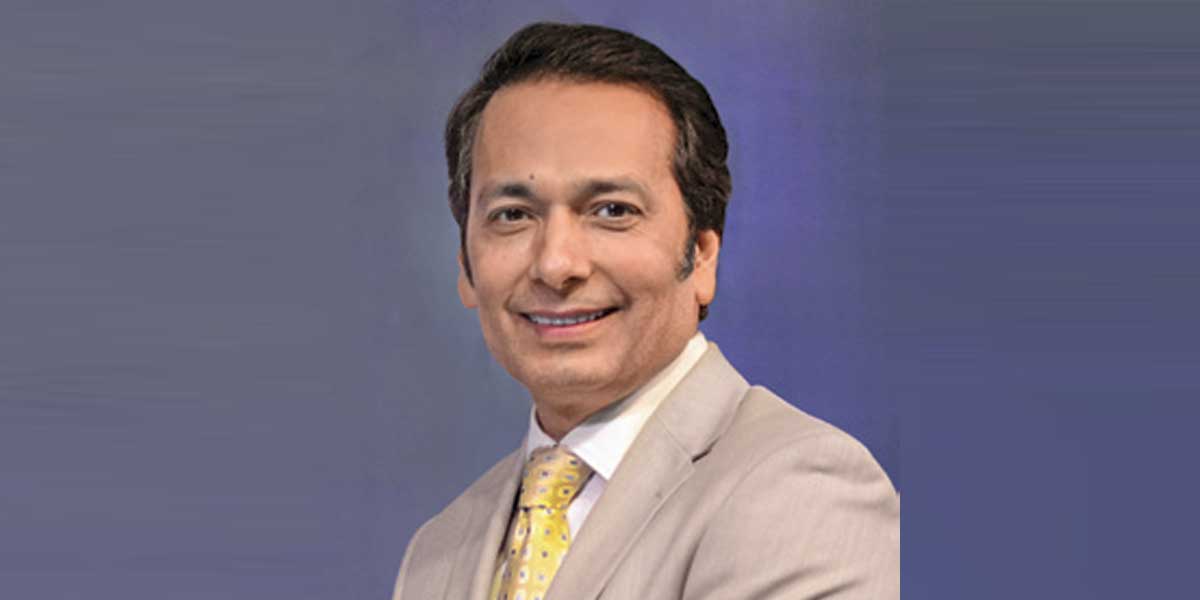
The Indian cement industry has reached a critical juncture in its sustainability journey. In a landmark move, the Ministry of Environment, Forest and Climate Change has, for the first time, announced greenhouse gas (GHG) emission intensity reduction targets for 282 entities, including 186 cement plants, under the Carbon Credit Trading Scheme, 2023. These targets, to be enforced starting FY2025-26, are aligned with India’s overarching ambition of achieving net zero emissions by 2070.
Cement manufacturing is intrinsically carbon-intensive, contributing to around 7 per cent of global GHG emissions, or approximately 3.8 billion tonnes annually. In India, the sector is responsible for 6 per cent of total emissions, underscoring its critical role in national climate mitigation strategies. This regulatory push, though long overdue, marks a significant shift towards accountability and structured decarbonisation.
However, the path to a greener cement sector is fraught with challenges—economic viability, regulatory ambiguity, and technical limitations continue to hinder the widespread adoption of sustainable alternatives. A major gap lies in the lack of a clear, India-specific definition for ‘green cement’, which is essential to establish standards and drive industry-wide transformation.
Despite these hurdles, the industry holds immense potential to emerge as a climate champion. Studies estimate that through targeted decarbonisation strategies—ranging from clinker substitution and alternative fuels to carbon capture and innovative product development—the sector could reduce emissions by 400 to 500 million metric tonnes by 2030.
Collaborations between key stakeholders and industry-wide awareness initiatives (such as Earth Day) are already fostering momentum. The responsibility now lies with producers, regulators and technology providers to fast-track innovation and investment.
The time to act is now. A sustainable cement industry is not only possible—it is imperative.

Hindalco Buys US Speciality Alumina Firm for $125 Million

Star Cement launches ‘Star Smart Building Solutions’

Nuvoco Vistas reports record quarterly EBITDA

UltraTech Cement increases capacity by 1.4Mt/yr

Shree Cement reports 2025 financial year results

Hindalco Buys US Speciality Alumina Firm for $125 Million

Star Cement launches ‘Star Smart Building Solutions’

Nuvoco Vistas reports record quarterly EBITDA

UltraTech Cement increases capacity by 1.4Mt/yr
