Technology
Logistics management in post-Covid-19 era
Published
6 years agoon
By
admin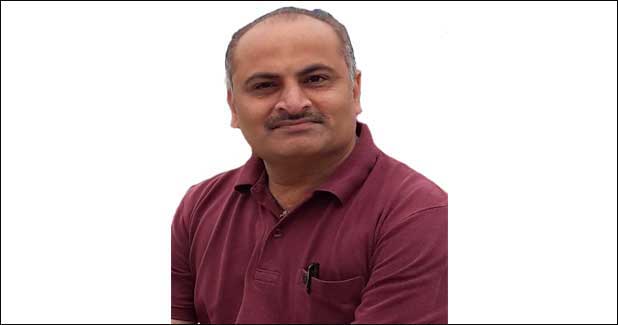
Most supply chain professionals are still in the reactive phase of how to deal with this pandemic. That includes combating fear and uncertainty around shortages and gauging the overall impact the coronavirus will have on supply chain and logistics operations.
Logistics management is the backbone of any country’s economy. Logistics is unique, It never stops?.! Logistics is happening around the globe, 24×7. Logistics is concerned with getting products and services where they are needed when they are desired. It is very difficult to visualise any marketing or manufacturing without logistics support. Logistics has been performed since the beginning of civilisation. It’s hardly new.
Logistics involves the integration of information, transportation, inventory, warehousing, material handling and packaging. In any individual firms, logistics expenditure typically ranges from 5 to 35 per cent of sales depending on the type of business, geographical area of the operation and volume ratio of product and materials. Logistics typically accounts for one of the highest costs of doing business, second only to materials in manufacturing or cost of goods sold in wholesaling or retailing.
Logistics is the art and science of managing and controlling the flow of goods, energy, information and other resources like products, services and people from the source of production to the market. It involves the integration of information, transportation, inventory, warehousing, material handling and packaging.
The main objectives of logistics is to achieve "7 Rs" – "The right product, in right quantity, in right condition, at the right time and Right place for the right customer, at the right cost."
The global logistics market size is estimated to be $2,734 billion in 2020 and projected to reach $3,215 billion by 2021, at a YoY growth of 17.6 per cent. In our cement industry, the logistics cost is approximately Rs 39,000 crore (23 to 25 per cent of total cement sales). Logistics mode mix of road (71 per cent), rail (27 per cent) and coastal (2 per cent). Bagged cement with 80 per cent and bulk cement with 20 per cent.
Covid-19 and Indian logistics industry
Asia Pacific is expected to have the largest logistics market size as the region has taken stringent and quite early measures to contain the Coronavirus outspread. China has started to recover from the COVID-19 pandemic faster than any other country.
The World Health Organization (WHO) has appreciated India’s control over the spread of the pandemic. This has allowed the logistics and supply chain companies to meet consumer demands during the pandemic situation. During the lockdown, only essential people and commodities are permitted by the authorities. The list of essential people and commodities must be continuously revised to minimise the adverse impact on people’s lives and the spread of the pandemic. Thus, the Asia-Pacific region is expected to show positive signs soon as the supply chain industry recovers gradually.
About 50 per cent of the 12.5 million heavy, medium, and small commercial vehicles have shut their engines because of coronavirus. There are no drivers, no loaders, and no unloaders to support the $200 billion logistics industry. Fifty per cent of India’s organised trucking fleet is now without drivers, who have gone home.
The entire supply chain is being impacted. From raw materials and packaging material supply to manpower at manufacturing plants (to load/unload/operate) to logistics, and transport to retail. the entire value chain in logistics right from transportation to warehousing would be adversely impacted, entities with asset-heavy business model will see a greater impact owing to high fixed costs.
There has been a significant drop in volumes at all facilities. As the volumes fall, it will take several months before they get back to normalcy – ports are highly capital-intensive in nature. The standing cost of assets is very high, running into millions of rupees.
As per research on behavioural science, it takes more than two months before a new behaviour becomes a habit or culture. We are in a lockdown of 68 days, it is a significant time period to impact consumer behaviour. We can also expect that post lockdown.
The Covid-19 pandemic is challenging businesses to think in unique and different ways. The disruptions caused by the virus outbreak have left deep impacts on consumer behaviour and preferences. Customers are now increasingly exercising caution on what, where, and how they buy.
The cumulative loss estimate is as high as Rs 50,000 crore with the highest loss coming from the aviation sector, followed by the Roadways, in terms of lost toll taxes, goods wasted on the road due to a sudden lockdown and halt numbers of fully loaded trucks.
Most supply chain professionals are still in the reactive phase of how to deal with this pandemic. That includes combating fear and uncertainty around shortages and gauging the overall impact the coronavirus will have on supply chain and logistics operations.
Logistics management in post coronavirus era
Role of logistics management: The major role of the logistics management function as given below:
- Demand planning and forecasting along with production function
- Sourcing and procurement of raw materials/goods and services required to run the manufacturing operation and its customers’ needs
- Managing the inflow and outflow of the inventory – be it the raw material required or making the product or pushing them to market along with sales and marketing functions
- Putting agreements in place to ensure safety for the organisations
- Managing supplier relationships by driving SLAs and KPIs in supplies
Impact of Covid-19 on logistics management function: When the factories/offices/markets are shut, the factories producing essentials are the only ones allowed to operate, the customer base of the organisation is working from home, the impact is on both sides – demand and supply. With reduced demand, the suppliers who were looking for new buyers for their products were impacted. On the other hand, buyers who were getting supplies from their supplier/vendor base got impacted because of no supplies from them.
Covid-19’s safety and compliance guidelines were put into place for the organisations as well as the individuals. From social distancing to be followed in the factories and workplace to ensure employees and workers are equipped with PPE kits, things have changed in recent times.
Scarcity of raw materials supplies, indirect material supplies and the higher lead time is another problem that happened to result in higher prices, limited availability and increased logistics cost to the companies.
The buyers and suppliers lost chance to meet each other face to face and negotiate on table. Almost everyone was working virtually and some of the buyers/suppliers who were not familiar with collaboration tools faced difficulties in executing negotiations effectively. In short, virtual meetings were done for decision making.
While a lot of changes have happened at organisation level in various functions in last few months, the Supply management function has changed too. The pressures being placed on supply chain professionals around the world by Covid-19 are leading to a reassessment of how supply chains function. They are also likely to accelerate the process of digital transformation as a means of overcoming weaknesses and vulnerabilities. There are several ways in which businesses can go about creating resilient supply chains in a post-Covid world.
There is an urgent need to reduce dependency on physical labour in areas such as transportation, logistics and warehousing. This can be achieved through the introduction of automation/technologies such as the Internet of Things (IoT) and artificial intelligence (AI) and machine learning.
The factories which can modularise production and adapt lines in line with demand changes will become the norm. They will be backed by supply networks capable of communicating intelligently with one another, thereby increasing their effectiveness and agility.
It is the time when instead of having dependency on one supplier or a couple of suppliers, organisation need to have a base of supplier who are ready to serve it when needed. To keep the relationship going, it is advised to keep procuring small quantities from time to time from additional suppliers.
Covid-19 has taught many things to almost everyone, so the sourcing and procurement function should remain ready for surprises going forward too. Plan for short term and long term is not enough. There is a need to start planning for near ? short term too, which can be in the next 24 hours. There is enough data points organisations sit on. The need is to utilise the data science tools to predict daily than monthly, quarterly or annual plans.
The supply chain technologies are emerging that dramatically improve visibility across the end-to-end supply chain, and support companies’ ability to resist such shocks. The traditional linear supply chain model is transforming into digital supply networks (DSNs), where functional silos are broken down and organisations become connected to their complete supply network to enable end-to-end visibility, collaboration, agility and optimisation.
Leveraging advanced technologies such as the IoT, AI, robotics, and 5G, DSNs are designed to anticipate and meet future challenges.
The key elements that will emerge in the logistics management of a post-Covid world include:
- Intelligent procurement to help organisations understand where and when to source using advanced machine learning algorithms based on factors such as past purchases and commodity pricing
- Data management with intelligent automation and analytics that will deliver end-to-end information management and provide supply chain partners with insights around diagnostics, market intelligence and risk management
- Supplier risk management to help organisations model cost structures and keep abreast of any supply disruptions and secure capacity
- Supply chain simulation involving modelling new strategies based on changes to business or operating models which helps to validate and identify the most cost-efficient supply chain design
Covid-19 warns that rare events may disrupt the logistics management. Greater agility, adoption to changing contexts and ability to redesign the supply chain in the situations of rare events will help organisations to prevent damages caused by pandemics in general particularly Covid-19.
In last one decade due to digitalisation era, IT has created the big changes in entire trucking industry and their productivity and efficiency. Driven by the IIoT (Industrial Internet of Things), the manufacturing sector is a major transformation. Automation has been gaining traction in the logistics industry as well with the continuous adoption of IoT.
Intelligent process flows: The supply chain responsive to rare events such as Covid-19 is not easy as the systems are not trained to absorb the shocks provided by such situation. One of the ways to make the supply chain responsive is to transform the supply chain processes to intelligent process flow. A company can transform all verticals into an intelligent process flow starting from demand planning and manufacturing execution to order orchestration and fulfillment. This will allow the processes, people, and technology to interact – bridging the current gap in a company’s ability to understand the changes in the environment.
Digital technology: Company needs to leverage the power of AI and other emerging technologies. Such dependencies on advanced technologies can help companies navigate through the supply chain vulnerabilities caused by Covid-19 and assist in business continuity amid disruption and uncertainty. Including automation, Blockchain, IoT, and edge computing in its supply chain design and management may help company turn unanticipated into the envisioned.
IT system-based order punching to order allotment: In this current digital India, the use of Computers / Smart Phones is very common for all of us. We have to develop a very strong IT system in that we can manage real time automated punching of our marketing orders through CRM Software to orders’ allotment to transporters, trucks’ confirmation, online lorry receipt generation, e-invoicing, e-way bill and e-PoD from Customers etc. It will help to marketing, logistics and transporters touch free work environment and social distancing for protecting from Covid-19.
GPS based trucking/logistics management: In view of the Covid-19, transporter has hesitancy to interact with multiple agencies (like gate security, logistics officers, WB operator, packing plant supervisor, truck loading workers, etc.). We have to develop strong RFID/GPS system based trucking management and monitoring system. The GPS will provide real-time visibility into the specific location and movement of vehicles.
GPS solutions provide real-time tracking of fleet and workforce from the first mile to long haul to the last mile. Logistics and Technology have become synonymous. It is strictly followed that driver should remain inside his truck and the activities such as security in-out, weighment of truck will do automatic with the help of RFID-based system and Automation of Weighbridge integration. This will help minimum interaction of drivers with security, logistics officers, weigh bridge operation and packing plant workers. In order to enhance driver’s experience, despatch related information can now be shared on his mobile with the help of the GPS System, so that he do not have to interact with logistics, transporters and packing plant operators.
Usually, drivers use to wait for long time to get the delivery instructions, Invoice papers and e-way bill, etc. at cement plant. But with the use of GPS system, automatic weighbridge, SAP integration process and IT -based logistics management applications, automation of packing plant operation and the print of DI, invoice, E-way bill can generate automatically and handed over to drivers while truck goes out and driver remain seated in his truck.
GPS system will help to monitoring real time truck transit time, halt during travelling, expected time of reaching at customer site, reaching at delivery point, delivery confirmation through e-PoD from customers etc touch free work environment and without human intervention.
Technological advancements now enable businesses to build end-to-end supply chain solutions that speed up processes and avoid bottlenecks in the supply chain. Business intelligence tools have helped to improve forecasting and identify areas of concern without any major time lag. The entire system is touch free work environment and social distancing for protecting from Covid-19.
Logistics central monitoring cell: Given the constantly evolving scenario, it is vital for consumer goods/commodity companies, retailers and brands to establish a cross-functional empowered Central Monitoring cell to take decisions fluidly. Given the current volatility in consumer behaviour and internal operating chain, it is critical to establish the guiding principles and core objectives for the monitoring cell while providing the decision-making authority to decide and implement initiatives on the go.
Conclusion
The supply chain is the backbone of any country’s economy as a majority of goods and services flow through the supply chain partners. Supply chains have become highly sophisticated and vital to the competitiveness of many companies. A decades-long focus on supply chain optimisation to minimise costs, reduce inventories, and drive up asset utilisation has removed buffers and flexibility to absorb delays and disruptions. The effect of Covid-19 on the supply chain that leads to issues in manufacturing, distribution, and retailing has exposed the dire need for proactive strategies. As companies move through the current crisis, firms will realise the value of intelligent process flows, self-correcting and smart supply chain, implications of AI and augmented techniques, and a forward-looking strategic approach.
Several technological advances have been made in recent times to ensure optimum utilisation of resources, tracking of consignments and seamless distribution of cargo such as Automatic Identification and Data Capture (AIDC) Technology, Quick response (QR) code, real-time locating systems and RFID. Adoption of Warehouse Management System (WMS) and other IT-driven solutions are becoming effective in increasing the competitiveness of the warehousing industry.
The entire digitalisation system will help overall productivity, efficiency, proper and efficient fleet utilisation resulting huge cost saving in logistics management in cement industry. The future successful company will be the one that has a dynamically optimised supply chain network with preparation and readiness to address the next disruption whether the next wave of Covid-19 or a new threat to business practices.
Footnote: The article is authored by Dr Girish Mehta.
You may like
Economy & Market
Hindalco Buys US Speciality Alumina Firm for $125 Million
Published
2 months agoon
June 25, 2025By
admin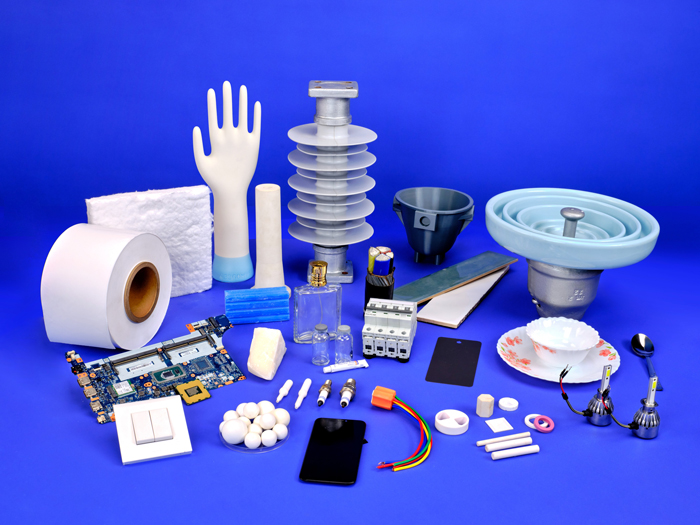
This strategic acquisition marks a significant investment in speciality alumina, a key step by Aditya Birla Group’s metals flagship towards becoming future-ready by scaling its high-value, technology-led materials portfolio.
Hindalco Industries, the world’s largest aluminium company by revenue and the metals flagship of the $28 billion Aditya Birla Group, has announced the acquisition of a 100 per cent equity stake in US-based AluChem Companies—a prominent manufacturer of speciality alumina—for an enterprise value of $125 million. The transaction will be executed through Aditya Holdings, a wholly owned subsidiary.
This acquisition represents a pivotal investment in speciality alumina and advances Hindalco’s strategy to expand its high-value, technology-led materials portfolio.
Hindalco’s speciality alumina business, a key pillar of its value-added strategy, has delivered consistent double-digit growth in recent years. It has emerged as a high-growth, high-margin vertical within the company’s portfolio. As speciality alumina finds expanding applications across electric mobility, semiconductors, and precision ceramics, the deal positions Hindalco further up the innovation curve, enabling next-generation alumina solutions and value-accretive growth.
Kumar Mangalam Birla, Chairman of Aditya Birla Group, called the acquisition an important step in their global strategy to build a leadership position in value-added, high-tech materials.
“Our strategic foray into the speciality alumina space will not only accelerate the development of future-ready, sustainable solutions but also open new pathways to pursue high-impact growth opportunities. By integrating advanced technologies into our value chain, we are reinforcing our commitment to self-reliance, import substitution, and building scale in innovation-led businesses.”
Ronald P Zapletal, Founder, AluChem Companies, said the partnership with Hindalco would provide AluChem the ability and capital to scale up faster and build scale in North America.
“AluChem will benefit from their world-class sustainability and safety standards and practices, access to integrated operations and a consistent, reliable raw material supply chain. Their ability to leverage R&D capabilities and a talented workforce adds tremendous value to our innovation pipeline, helping drive market expansion beyond North America.”
An Eye on the Future
The global speciality alumina market is projected to grow significantly, with rising demand for tailored solutions in sectors such as ceramics, electronics, aerospace, and medical applications. Hindalco currently operates 500,000 tonnes of speciality alumina capacity and aims to scale this up to 1 million tonnes by FY2030.
Commenting on the development, Satish Pai, Managing Director, Hindalco Industries, said the deal reinforced their commitment to innovation and global expansion.
“As alumina gains increasing relevance in critical and clean-tech sectors, AluChem’s advanced chemistry capabilities will significantly enhance our ability to serve these fast-evolving markets. Importantly, it deepens our high-value-added portfolio with differentiated products that drive profitability and strengthen our global competitiveness.”
AluChem adds a strong North American presence to Hindalco’s portfolio, with an annual capacity of 60,000 tonnes across three advanced manufacturing facilities in Ohio and Arkansas. The company is a long-standing supplier of ultra-low soda calcined and tabular alumina, materials prized for their thermal and mechanical stability and widely used in precision engineering and high-performance refractories.
Saurabh Khedekar, CEO of the Alumina Business at Hindalco Industries, said the acquisition unlocked immediate synergies, including market access and portfolio diversification.
“Hindalco plans to work with AluChem’s high performance technology solutions and scale up production of ultra-low soda alumina products to drive a larger global market share.”
The transaction is expected to close in the upcoming quarter, subject to customary closing conditions and regulatory approvals.

As India’s cement industry heads for unprecedented growth, the importance of smart, sustainable and strategic lubrication is gaining ground. From reducing downtime and enhancing energy efficiency to enabling predictive maintenance, lubricants are transforming plant performance. ICR explores how advanced lubrication solutions are becoming critical enablers of reliability, resilience and environmental stewardship in the cement sector.
The Indian cement industry, a cornerstone of the nation’s infrastructure development, is experiencing significant growth. In 2023, India’s cement production reached 374.55 million tonnes, marking a 6.83 per cent year-on-year growth. Projections indicate that the market size will expand from 3.96 billion tonnes in 2023 to 5.99 billion tonnes by 2032, reflecting a compound annual growth rate (CAGR) of 4.7 per cent during 2024-32. This expansion underscores the increasing demand for efficient and sustainable operations within the sector.
In cement manufacturing, equipment such as kilns, crushers, vertical mills, ball mills, conveyors and fans operate under extreme temperatures, heavy loads and high dust exposure. These demanding conditions make proper lubrication not just essential, but mission-critical. Selecting the right type of lubricant and maintaining an effective lubrication regime can drastically improve machine uptime, reduce maintenance costs, and enhance plant safety. In many cases, lubricant-related failures account for a significant proportion of unplanned downtime, underscoring the value of a well-structured lubrication strategy.
The Indian cement sector is also undergoing a technological transformation, with increasing emphasis on automation, predictive maintenance and energy efficiency. In this evolving landscape, lubricants are no longer just consumables—they are enablers of performance, longevity and sustainability. With the growing availability of advanced lubricants and condition-monitoring technologies, Indian cement plants have the opportunity to optimise their lubrication practices in line with global standards. Additionally, tightening environmental regulations and sustainability goals are driving the shift toward eco-friendly lubricants and responsible usage practices, making lubrication management a key factor in both operational and environmental performance.
As the industry moves forward, there is a growing realisation that lubrication excellence can be a competitive differentiator. This article explores the critical role of lubricants in cement manufacturing, the latest technological advancements, the environmental considerations shaping lubricant use, and the challenges and opportunities for cement producers in India aiming to maximise equipment reliability and operational efficiency.
The role of lubricants in cement manufacturing
Cement manufacturing involves heavy-duty machinery operating under extreme conditions—high temperatures, heavy loads and continuous operations. Lubricants are essential in minimising friction, reducing wear and tear, and preventing equipment failures. Proper lubrication ensures that components such as kilns, crushers and grinding mills function optimally, thereby reducing downtime and maintenance costs.
Moreover, the integration of advanced lubrication technologies has enabled predictive maintenance strategies. By monitoring lubricant conditions, operators can anticipate equipment issues before they escalate, allowing for timely interventions and uninterrupted production cycles.
“Lubricants play a crucial role in enhancing the efficiency and reliability of cement plant operations. High-performance lubricants reduce friction and wear in critical machinery such as crushers, kilns, mills, and conveyors, ensuring smoother operation and extending equipment life. By minimising mechanical breakdowns and unplanned downtime, they contribute to consistent production and lower maintenance costs. Additionally, specialised lubricants designed to withstand high temperatures, heavy loads, and dusty environments help maintain optimal performance under demanding conditions. Proper lubrication also improves energy efficiency by reducing power loss due to friction. In essence, the right lubrication strategy not only enhances equipment reliability and operational uptime but also supports overall cost-effectiveness and productivity in cement manufacturing,” says Hiten Ved, Sales Head, Royal Petro Specialities.
In addition to enhancing equipment longevity, lubricants are pivotal in ensuring uninterrupted production cycles. Cement manufacturing is a 24/7 operation, and any unexpected downtime due to mechanical failure can lead to significant financial losses. Lubricants with high thermal stability and oxidation resistance prevent the breakdown of oil films under intense heat, especially in applications like rotary kilns, vertical roller mills and clinker coolers. By reducing the likelihood of equipment seizures or breakdowns, these lubricants act as silent enablers of plant reliability and uptime.
Gaurav Mathur, Director and Chief Executive Officer, Global Technical Services, says, “Wall paintings in tombs show workers using water to move statues, indicating early recognition of lubrication. By 1400 BC, animal fat was used to lubricate chariot axles, ever since then mankind has been relentlessly working to improvise the efficiency of lubricants. Tribological advancements have propelled industrialisation in the world. Machines working in demanding environment need better performance, however merely just better lubricant that is made from highly refined base oils is not good enough. Mineral and synthetic base oils and advanced additives chemistry have given birth to advanced lubricants. These lubricants have better performance characteristics and longer service life.”
“However, the way lubrication is done is more critical and if lubrication is not performed in a proper way, highest performing lubricants would also under perform compared to the lowest specification product. Total Lubrication Management has to be implemented for better machine reliability, equipment availability and lower down time. Implementation of TLM has paid rich dividends in the industry. Pillars of TLM being, contamination free lubrication, regular testing of lubricants to access the lubricant and machine condition and regeneration of lubricants,” he adds.
Lubricants contribute directly to energy efficiency. Friction losses within rotating equipment can account for up to 30 per cent of the total energy consumption in certain plant areas. Advanced synthetic lubricants, with low traction coefficients and superior film strength, reduce this internal resistance, thus improving mechanical efficiency and lowering the plant’s overall energy footprint. As Indian cement plants pursue energy benchmarking and ISO 50001 certifications, the use of high-performance lubricants becomes an integral strategy in achieving energy conservation goals.
“The cement industry has many lubrication points that require NLGI Grade 2 grease that can be used in high temperature applications. These may include bearings on vibrating screens and roller mills; rotating joints on grinding units; and various shafts, pivots, and metal to metal contact points found throughout the plant. CorrLube™ VpCI® Lithium EP Grease has a dropping point of 360 °F (182 °C), allowing it to be used in a broad range of temperatures. For areas that need a slightly harder grease of NLGI Grade 3, EcoLine® Biobased Grease offers a
similar dropping point of 365 °F (185 °C), explain Julie Holmquist, Marketing Content Writer,
Cortec Corporation.
Market dynamics: growth and trends
The Indian industrial lubricants market was valued at $13.05 billion in 2024 and is projected to reach $ 20.72 billion by 2033, growing at a CAGR of 4.12 per cent. This growth is driven by the expanding industrial sector, increased mechanisation, and the adoption of advanced machinery requiring specialised lubricants.
In the cement sector specifically, the demand for high-performance lubricants is rising. The lubricants for cement market are estimated to be $ 2.5 billion in 2024 and is expected to reach $ 3.9 billion by 2033, at a CAGR of 5.3 per cent from 2026 to 2033. This surge is attributed to the need for lubricants that can withstand harsh operating conditions and enhance equipment reliability.
Advancements in lubrication technology
Recent years have witnessed significant advancements in lubrication technology tailored for the cement industry. Synthetic lubricants, known for their superior thermal stability and longer service life, are increasingly being adopted. These lubricants perform effectively under extreme temperatures and heavy loads, common in cement manufacturing processes.
Additionally, the development of bio-based lubricants offers environmentally friendly alternatives without compromising performance. These lubricants, derived from renewable sources, reduce the environmental footprint and align with global sustainability goals. Their biodegradability and low toxicity make them suitable for applications where environmental considerations are paramount.
Smart lubrication systems are another breakthrough in the cement industry. These systems use IoT-enabled sensors and controllers to monitor lubricant condition in real time—tracking parameters such as viscosity, temperature, contamination levels and usage. This data is integrated into plant maintenance software to automate lubricant replenishment and alert operators to potential failures. Predictive lubrication ensures that each component receives the right amount of lubricant at the right time, minimising waste, reducing manual intervention, and extending machinery life.
“Many VpCI® products can be applied to surfaces with minimal pre-cleaning, and the protective VpCI® layer typically does not need to be removed before equipment is put back into service. VpCI® ‘s save significant labor, time, and associated costs compared to methods that require extensive surface preparation (e.g., sandblasting) and post-application cleaning or degreasing. This allows for faster startup after maintenance,” elaborates Ana Juraga, Content Writer, Cortec Corporation.
Furthermore, Original Equipment Manufacturers (OEMs) and lubricant suppliers are collaborating to develop application-specific lubricants tailored to the unique operating conditions of cement manufacturing units. For example, gear oils designed for high-load kilns or open gear systems now come with superior Extreme Pressure (EP) additives and anti-wear properties to cope with shock loading and variable speed operations. These co-developed solutions not only enhance mechanical reliability but also ensure compatibility with diverse materials used in modern cement equipment, ensuring peak performance in both greenfield and brownfield plants.
Sustainability and environmental considerations
The cement industry is under increasing pressure to reduce its environmental impact. Lubricants contribute to this goal by enhancing energy efficiency and reducing emissions. High-quality lubricants decrease friction, leading to lower energy consumption and, consequently, reduced greenhouse gas emissions.
Furthermore, the use of long-life lubricants minimises the frequency of oil changes, thereby reducing waste generation and disposal issues. The shift towards bio-based and recyclable lubricants also supports circular economy principles, promoting resource efficiency and environmental stewardship.
A report by Klüber Lubrication India suggests that sustainability continues to be a key focus for industries, the Securities and Exchange Board of India (SEBI) has mandated Business Responsibility and Sustainability Reporting (BRSR) for the top 1,000 listed companies. This framework requires organisations to disclose their environmental, social and governance (ESG) initiatives, including energy conservation, emission reductions and resource optimisation. Beyond compliance, BRSR reporting allows companies to showcase their sustainability leadership and build investor confidence. Organisations that proactively address sustainability challenges are better positioned to attract long-term investors, secure financing, and maintain a competitive advantage in an evolving regulatory landscape.
The report also states that their high-performance synthetic lubricants play a crucial role in helping cement manufacturers meet these regulatory requirements by enhancing energy efficiency and reducing CO2 emissions in critical machinery such as vertical roller mills (VRMs) and main gearboxes. By adopting our energy-efficient solutions, companies can strengthen their BRSR compliance while achieving tangible operational benefits.
An emerging trend in the lubricant industry is the formulation of biodegradable lubricants specifically tailored for heavy industries like cement manufacturing. These eco-friendly alternatives are made from renewable base stocks and are designed to degrade naturally without leaving behind harmful residues. In environmentally sensitive zones or operations with high spill risk, such as open gear applications or hydraulic systems exposed to the elements, biodegradable lubricants offer a sustainable solution that aligns with stricter environmental regulations and the growing emphasis on corporate social responsibility (CSR) in India’s industrial sector.
KB Mathur, Founder and Director, Global Technical Services, says, “In the world of industrial machinery, lubricating oils while essential; are often misunderstood in terms of their life cycle. When oils are used in machinery, they don’t simply ‘DIE’. Instead, they become contaminated with moisture (water) and solid contaminants like dust, dirt and wear debris. These contaminants degrade the oil’s effectiveness but do not render it completely unusable. Used lubricants can be regenerated via advanced filtration processes/systems and recharged with the use of performance enhancing additives hence restoring them. These oils are brought back to ‘As-New’ levels. This new fresher lubricating oil is formulated to carry out its specific job providing heightened lubrication and reliable performance of the assets with a view of improved machine condition. Hence, contributing to not just cost savings but leading to magnified productivity, and diminished environmental stress.”
Lubricant manufacturers are increasingly focusing on circular economy principles, offering oil analysis, filtration and recycling services that extend lubricant life and minimise waste. Used oil regeneration programs not only reduce disposal costs but also help cement plants meet regulatory norms under the Hazardous Waste Management Rules of India. This closed-loop approach not only lowers the environmental burden but also enhances economic efficiency—making sustainability a dual benefit for operational and ecological performance. As cement companies work towards science-based targets and carbon neutrality, lubricant selection and management play a more strategic role in meeting these broader sustainability commitments.
Challenges and opportunities
Despite the benefits, the adoption of advanced lubricants in the Indian cement industry faces challenges. These include the higher initial costs of synthetic and bio-based lubricants and a lack of awareness about their long-term benefits. Additionally, the integration of lubrication management systems requires investment in training and infrastructure.
However, these challenges present opportunities for innovation and collaboration. Manufacturers
can work closely with lubricant suppliers to develop customised solutions that meet specific operational needs. Moreover, government incentives and regulatory frameworks promoting sustainable practices can accelerate the adoption of advanced lubrication technologies.
Another key challenge is the limited awareness and technical training available at the plant level regarding proper lubrication practices. Many maintenance teams still rely on outdated methods such as manual greasing or fixed-interval lubrication schedules, which often lead to over-lubrication, under-lubrication or lubricant contamination. This results in premature equipment wear and higher operating costs. There is a growing need for skill development programmes and collaboration with lubricant suppliers to train technicians on best practices, condition-based monitoring, and the use of smart lubrication systems.
“Oil in the machine is like blood in the human body. There is no rotating machine that works without lubricants (liquid, semi liquid or solid). Based on the machine component, type of lubricant is used to minimise the mechanical changes in the machine. Lubricant being the product that separates two or more materials under movement. With modern machines being more and more sophisticated and tolerances being finer than before, cleanliness of Lubricants is critical, would the source of contamination be internal wear or external contamination. These contaminations rupture and compromises lubricant film, contamination particles when come in-between the fine tolerances, become cause of catastrophic failure,” expounds Gaurav Mathur.
At the same time, the industry is witnessing an opportunity to leverage digitalisation in lubrication management. Advanced lubrication tracking tools, coupled with ERP and maintenance software, can now offer real-time visibility into lubricant consumption, scheduling and health diagnostics. Integration of AI-powered analytics helps predict equipment failure based on lubricant data, enabling a shift from reactive to predictive maintenance. For Indian cement manufacturers aiming to digitise plant operations as part of Industry 4.0, lubrication is an ideal entry point that delivers immediate ROI and long-term gains in efficiency, asset life and sustainability.
Conclusion
As the Indian cement industry continues its trajectory of growth, the role of high-performance lubricants in ensuring operational reliability, energy efficiency and cost savings cannot be overstated. From kilns and crushers to ball mills and gearboxes, modern lubrication solutions are critical in
reducing downtime and maximising equipment lifespan. With rising demand and increased production pressures, cement plants must adopt a proactive approach to lubrication management—viewing it not as a routine maintenance task, but as a strategic pillar of plant performance.
Recent advancements in lubricant technology, such as synthetic formulations, nano-additives, and smart dispensers, have opened new avenues for boosting equipment efficiency and longevity. Digital tools and IoT-based systems now allow plant operators to monitor lubricant condition in real time, enabling predictive maintenance and minimising the risk of failure. As cement manufacturers increasingly pursue digital transformation and automation under Industry 4.0 frameworks, lubrication systems must be seamlessly integrated into broader asset management strategies.
At the same time, sustainability imperatives are reshaping lubrication choices. There is growing emphasis on biodegradable lubricants, optimised lubricant consumption, and environmentally responsible disposal practices. Overcoming challenges such as limited awareness, inconsistent maintenance practices, and cost sensitivity will require collaboration between lubricant manufacturers, OEMs and cement producers. The opportunities, however, are substantial—by aligning lubrication strategies with efficiency, digitalisation and sustainability goals, the Indian cement industry can significantly enhance its competitiveness and resilience in the years ahead.
– Kanika Mathur
Concrete
We consistently push the boundaries of technology
Published
5 months agoon
April 18, 2025By
admin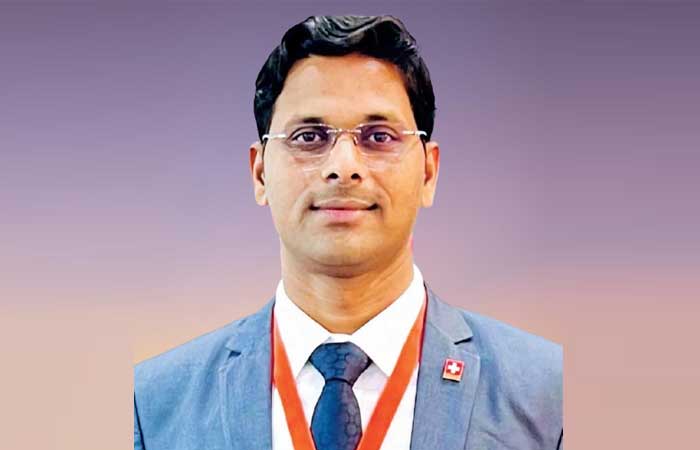
Swapnil Jadhav, Director, SIDSA Environmental, discusses transforming waste into valuable resources through cutting-edge technology and innovative process solutions.
SIDSA Environmental brings decades of experience and expertise to the important niche of waste treatment and process technologies. As a global leader that is at the forefront of sustainable waste management, the company excels in recycling, waste-to-energy solutions and alternative fuel production. In this conversation, Swapnil Jadhav, Director, SIDSA Environmental, shares insights into their advanced shredding technology, its role in RDF production for the cement industry and emerging trends in waste-to-energy solutions.
Can you give us an overview of SIDSA Environmental’s role in waste treatment and process technologies?
SIDSA is a leading innovator in the field of waste treatment and process technologies, dedicated to delivering sustainable solutions that address the growing challenges of waste management.
SIDSA is a more than 52-year-old organisation with worldwide presence and has successfully realised over 1100 projects.
Our expertise is in the engineering and development of cutting-edge systems that enable the conversion of waste materials into valuable resources. This includes recycling technologies, waste-to-energy (W2E) systems, and advanced methods for producing alternative fuels such as refuse derived fuel (RDF). The organisation prioritises environmental stewardship by integrating energy-efficient processes and technologies, supporting industrial sectors—including the cement industry—in reducing their carbon footprint. Through our comprehensive approach, we aim to promote a circular economy where waste is no longer a burden but a resource to be harnessed.
How does SIDSA Environmental’s shredding technology contribute to the cement industry, especially in the production of RDF?
SIDSA’s shredding technology is pivotal in transforming diverse waste streams into high-quality RDF. Cement kilns require fuel with specific calorific values and uniform composition to ensure efficient combustion and operational stability, and this is where our shredding systems excel. In India, we are segment leaders with more than 30 projects including over 50 equipment of varied capacity successfully realised. Some of the solutions were supplied as complete turnkey plants for high capacity AFR processing. Our esteemed client list comprises reputed cement manufacturers and chemical industries. Our technology processes various types of waste—such as plastics, textiles and industrial residues—breaking them down into consistent particles suitable for energy recovery.
Key features include:
- High efficiency: Ensures optimal throughput for large volumes of waste.
- Adaptability: Handles mixed and heterogeneous waste streams, including contaminated or complex materials.
- Reliability: Reduces the likelihood of operational disruptions in RDF production. By standardising RDF properties, our shredding technology enables cement plants to achieve greater energy efficiency while adhering to environmental regulations.
What are the key benefits of using alternative fuels like RDF in cement kilns?
The adoption of RDF and other alternative fuels offers significant advantages across environmental, economic and social dimensions:
- Environmental benefits: Cement kilns using RDF emit fewer greenhouse gases compared to those reliant on fossil fuels like coal or petroleum coke. RDF also helps mitigate the issue of overflowing landfills by diverting waste toward energy recovery.
- Economic savings: Alternative fuels are often more cost-effective than traditional energy sources, allowing cement plants to reduce operational expenses.
- Sustainability and resource efficiency: RDF facilitates the circular economy by repurposing waste materials into energy, conserving finite natural resources.
- Operational flexibility: Cement kilns designed to use RDF can seamlessly switch between different fuel types, enhancing adaptability to market conditions.
What innovations have been introduced in waste-to-energy (W2E) and recycling solutions?
SIDSA’s machinery is meticulously engineered to handle the complex requirements of processing hazardous and bulky waste.
This includes:
- Robust construction: Our equipment is designed to manage heavy loads and challenging waste streams, such as industrial debris, tires and large furniture.
- Advanced safety features: Intelligent sensors and automated controls ensure safe operation when dealing with potentially harmful materials, such as chemical waste.
- Compliance with standards: Machinery is built to adhere to international environmental and safety regulations, guaranteeing reliability under stringent conditions.
- Modular design: Allows for customisation and scalability to meet the unique needs of various waste management facilities.
How does your organisation customised solutions help cement plants improve sustainability and efficiency?
We consistently push the boundaries of technology to enhance waste management outcomes.
General innovations and new product development focus on:
- Energy-efficient shredders: These machines consume less power while maintaining high throughput, contributing to lower operational costs.
- AI-powered sorting systems: Utilise advanced algorithms to automate waste classification, increasing material recovery rates and minimising errors.
- Advanced gasification technologies: Convert waste into syngas (a clean energy source) while minimising emissions and residue.
- Closed-loop recycling solutions: Enable the extraction and repurposing of materials from waste streams, maximising resource use while reducing environmental impact.
What future trends do you foresee in waste management and alternative fuel usage in the cement sector?
Looking ahead, several trends are likely to shape the future of waste management and alternative fuels in the cement industry:
- AI integration: AI-driven technologies will enhance waste sorting and optimise RDF production, enabling greater efficiency.
- Bio-based fuels: Increased use of biofuels derived from organic waste as a renewable and low-carbon energy source.
- Collaborative approaches: Strengthened partnerships between governments, private industries and technology providers will facilitate large-scale implementation of sustainable practices.
- Circular economy expansion: The cement sector will increasingly adopt closed-loop systems, reducing waste and maximising resource reuse.
- Regulatory evolution: More stringent environmental laws and incentives for using alternative fuels will accelerate the transition toward sustainable energy solutions.
(Communication by the management of the company)