Environment
CSR initiative for truck drivers
Published
6 years agoon
By
admin
Road transport has a sizable share in the logistics chain of cement business. The vital and important link of road transport is vehicle drivers. The author takes a close look considering the sustainability of the chain and how CSR can bring in meaningful change.
Today, the entire world is in the grips of an unprecedented crisis of a magnitude which no one had anticipated – the Covid-19 pandemic. This has shaken the fabric of the global society, which was already facing innumerable challenges. Amongst them, in the Indian context, is the issue concerning the well-being and training of our business partners in the road transport industry – the community of truck drivers who are a vital part of our supply chain to keep our economy rolling.
The fates of our business and the road transport industry are closely interdependent, with healthy growth of the cement industry directly correlated with the growth of the road transportation infrastructure. And the backbone of this infrastructure are the millions of truck drivers who on a daily basis move the manufactured produce from one end of the supply chain to the other. Corporates can benefit themselves only by benefiting society, which also includes the large truckers’ community.
Background – Importance of road transport in India
Road transport is considered to be the most cost effective and preferred transportation mode for freight, keeping in view its level of penetration into populated areas, easy availability, adaptability to individual needs and cost savings. No wonder that road transport has emerged as the dominant segment in India’s transportation sector and accounts for about 60 percent of freight traffic movement in the country. Road transport also acts as a secondary feeder service to goods transported by railways.
For cement, too, the major transport mode is road, accounting for almost 65 percent of total outbound cement despatches, and around 20 million tonnes of cement is transported by road every month through an estimated 2.5 lakh trucks. In addition, an equivalent number of trucks and bulkers are deployed to move the inbound raw materials like coal, flyash and gypsum to the manufacturing plants. Transit mixers for RMC further add to the total number of vehicles engaged in the cement industry.
At 5.9 million km, India has the second largest road network in the world (next to USA’s 6.9 million km) and the Ministry of Road Transport and Highways (MoRTH) is planning to add 60,000 km of roads over the next five years. Under the Make in India program of the Government of India launched in 2014, Roads and Highways was identified as one of the key focus sectors under the National Infrastructure Pipeline (NIP) for expansion, including the iconic Bharatmala Pariyojana. Rural road network is also being augmented under the Pradhan Mantri Gram Sadak Yojana (PMGSY). With the expansion of the road network in the country, it is anticipated that road transportation of goods will further increase in the foreseeable future.
Human manpower behind the wheels on the road
According to All India Motor Transport Congress (AIMTC) – the apex body of transporters – there are 9.3 million goods vehicles in India, including multi axle/articulated vehicles, smaller trucks, lorries, LMVs and tankers. As per industry estimates, India had a truck to driver ratio of about 1:1.3 in the early 90s which is estimated to have dropped to 1:0.75 today, and expected to drop further to an alarmingly low 1:0.60 over the next decade!
Hence, the total number of goods vehicle drivers would be around 7.0 million, with nearly 2.3 million trucks idling due to shortage of drivers. Last year MoRTH has removed the minimum education requirement (of Class 8) for obtaining a commercial vehicle driving license to improve employment opportunities, particularly for the underprivileged skilled persons.
Reasons for driver shortage
Despite their hard work, the truck drivers in India have never got the respect they deserve. In fact, one of the least respected professions in our society is that of the truck driver. They have not been accorded any position of dignity, largely owing to their absence in the routine social life of their families and communities. Often, they become a truck driver because they can find no other job and are looked upon with open disdain. In addition, the lifestyle practices and habits (and often even the character) of a truck driver are perceived negatively by society.
And remuneration to the truck drivers is one of most neglected areas of logistics operations in India. The average earning of a truck driver is around Rs 15,000 to 20,000 per month (including daily allowance or bhatta). 85 percent of the road transport industry is from the unorganised sector, or small fleet operators, and the drivers do not have any fixed working hours, benefit of minimum wages, and a defined rest period. The truck drivers are deprived of benefits like ESI, PF, bonus and leave. The majority of the drivers are uneducated and often learn driving on the job while working as a helper or cleaner and do not have any formal defensive driving training. Added to this is the larger problem of the typical driver having a "macho" attitude and a firm belief that all accidents are not preventable – "what has to happen, will happen". Hence, he may scorn away advice relating to speed limit or wearing of seat belt.
Very few young persons want to join this profession now. Unlike other developed countries, it is rare for an Indian truck driver’s son aspiring to be a truck driver. Often this is due to the driver’s children being better educated and hence exposed to more job opportunities which are better paying without the hardships faced by their father. Many young persons prefer employment in the industrial or service sectors or, in the rural areas, may even opt to earn a living under the Government’s MNREGA scheme whilst searching for a regular job.
Hardships faced by Indian truck drivers
An Indian truck driver is on the road almost every day of the month. His is a 24×7 job which involves driving long distances across various states. The truck is virtually his "home away from home" on the road. Surveys have revealed that almost 53 percent truck drivers suffer from a health issue, 23 percent battle sleep deprivation, about 18 percent face physical stress and 12 percent mental stress.
According to MoRTH, around 1.50 lakh people are killed in road crashes annually. As per a study conducted by the Central Road Research Institute (CRRI) exhausted and sleep deprived drivers account for nearly 40 percent of road crashes.
Of the 4.65 lakh road crashes every year, a quarter are linked to truck drivers with a fatality rate of around 25 percent. Also, 50 percent of the mishaps happen between sunset and sunrise as drivers prefer to drive in the night to escape police and RTO harassment during the day. This position has changed during COVID-19 as short and medium haul drivers (covering upto 400 km in a day) are not keen to eat out or spend time in roadside dhabas and want to be with their family by night time and have dinner at home.
As per road safety experts’ recommendations, drivers should not driver for more than 8 to 10 hours in a day and take regular breaks at least every 2 hours so that they stay alert. However, goods vehicle drivers in India often drive more than 10 to 12 hours a day. Whilst an average Indian driver may "rest" for 8 to 10 hours, he effectively sleeps for only 3 to 4 hours. (these figures have also changed during the pandemic, with drivers being on the road for shorter periods).
And many of them have to make do with sleeping in their uncomfortable truck cabin or even under their truck, often in the grueling heat during summers, for fear of getting robbed of diesel, cash or the goods in their vehicles. It is also not uncommon to find a driver cooking his meal under his truck or inside the cabin using a kerosene stove, with a complete disregard to his and others’ safety. Consequently, truck drivers are under physical and mental stress that results in accidents as they often doze off whilst driving.
CSR initiatives for truck drivers
A major component of the RSIP covered softer aspects relating to the driver community like their physical, mental and behavioural health, work-life balance and time for family, personal hygiene, cleanliness and habits, lifestyle and eating habits, literacy and education, and issues relating to self-esteem, dignity and respect. These were taken up across all plants under the CSR umbrella with positive and beneficial outcomes. Some of the major initiatives taken are enumerated below:
Health camps: Truck drivers are a highly vulnerable working population due to several health risk factors including poor eyesight and hearing loss, hypertension, fatigue, obstructive sleep apnea and sleep deprivation, and insufficient physical activity. Other risk factors are exposure to diesel exhaust and risk of developing lung cancer, poor diet, obesity, and other metabolic disorders. Furthermore, they are prone to risky behaviors and lifestyles such as smoking, tobacco/gutka chewing, drinking, substance abuse, and having casual sexual contacts. These can have an adverse impact on their health with a consequent risk of traffic accidents and health problems.
What started as occasional eyesight checking camps at ACC plant locations soon turned into a comprehensive health and medical check-up program as a regular on-going activity. These are usually organised by the medical staff of the plant hospital and often doctors from nearby towns are also called in. The primary aim of the health camps is to cover the following:
Vision: At least 65 percent of our truck drivers have some vision problem, mild or acute. The younger drivers may have myopia and may require their first pair of spectacles. The older drivers also need to be checked for signs of color blindness, cataract or glaucoma and may either need to replace their old specs or get reading glasses. Thousands of drivers have been covered in the eyesight camps and hundreds of drivers provided with free prescription spectacles, mostly on the spot. It is advisable for drivers to have their vision tested at least once every 2 years.
Hearing: Hearing loss can have the most significant impact on a truck driver’s ability to do his job. The occupational conditions of truck drivers may have bilateral, symmetrical harmful effect on hearing threshold sense in all frequencies, but mainly at a frequency of 4000 Hz. Periodic medical examinations are vital for pre-diagnosing and prevention of any possible impairment.
Blood pressure: Considered a silent ailment, as there may be no symptoms of the condition, uncontrolled BP can lead to serious health problems such as heart attack and stroke. Drivers found to be having higher than normal BP are generally advised to exercise, reduce salt in their food, drink lots of water, stop smoking and drinking alcohol, and get plenty of sleep. In fact sleep deprivation is a major reason for drivers having high BP.
HIV/AIDS: Truck drivers are at increased risk of HIV/AIDS infection and of contracting other STD diseases. As Ashok Alexander, who headed Avahan (an initiative by the Bill and Melinda Gates Foundation for HIV prevention in India) states in his book A Stranger Truth, HIV prevalence among truckers ranged from 3 to 7 per cent. Avahan’s research showed that long-distance truckers were the ones most at risk; the short-haul truckers got home every night. Health camps for drivers create awareness about HIV/AIDS and counselling for prevention.
Alcohol addiction and substance abuse (tobacco, drugs, etc): Drunk driving is responsible for approximately 20 to 30 percent of crash fatalities and injuries. Alcohol can seriously impair brake reaction time, steering responsiveness, and lane control. It also increases the tendency of over-speeding and other high risk driving behaviors. Health camps have special counselling sessions to make the drivers aware of the dangers of drinking and driving as well as the legal consequences and the disastrous impact on the driver’s family. Some of our plants came up with an interesting idea of putting the driver’s family photo in the driver cabin to serve as a reminder not to risk his life for the sake of his family who wait for him to come back home safely.
Personal accident and health Insurance: As part of the HSE program and keeping in view the high risk job nature of driving on company’s business, ACC introduced a Group Personal Accident Insurance policy for third-party truck drivers to ensure their safety and wellbeing. The policy covers accidental death and total or partial disability and serves to provide a secured life and future to the driver and his dependents.
It is heartening to note that the All India Transporters Welfare Association (AITWA) launched a mega project named "Highway Heroes" for the welfare of the truck driver community on 14th November 2019. The multi-dimensional welfare scheme includes provisions like free accident insurance, hospitalisation expenses, education help to children of drivers, training, and safety and a centralised national 24×7 helpline for access in case of an emergency like an accident, attack by criminals, theft or any other harassment.
The National Health Authority (NHA) also signed an MoU with AITWA on 14th November 2019 to provide healthcare services to truck drivers under the "Ayushman Bharat – Pradhan Mantri Jan Arogya Yojana" (PM-JAY) scheme. Under this partnership, the NHA and AITWA will work together to identify truck drivers and employees of transport companies who could be eligible beneficiaries of the scheme.
Respect and dignity: In India the truck drivers appear at the bottom of the pyramid when it comes to respect and historically have been privy to lack of praise and dignity. They rarely receive respect from civic authorities like RTO, police personnel and check-post officials and one frequently hears reports of discriminatory behavior and harassment to truckers. Most drivers do not have the educational background or knowledge to deal with legal complications.
It is unfortunate that the driver’s job in India has a social disrespect and stigma attached to it. A large number of drivers find it difficult to get married as people are reluctant to marry their daughter to a driver. The driver’s children do not want to become drivers and drivers themselves have a low self-esteem.
Regular interactive sessions with drivers at ACC’s plants (often in the form of Driver Chaupals) have helped to instill and reinforce self-confidence and dignity in the drivers. They are briefed on the role as being beyond that of a mere driver to that of a brand ambassador and the customer’s first point-of contact with the company. Some of our plants have taken innovative steps like providing laundry service, toilets with bathing facility and even hair-cutting saloons in their parking yards so that drivers can freshen themselves before commencing their trip and look presentable and clean when they reach their customer. Cleanliness, hygiene and grooming also helps to increase the driver’s self-confidence and self-respect. ACC’s Thondebhavi plant in Karnataka was the first to install a full length mirror in the driver rest facility so that he can see how others view him!
ACC’s Chanda plant (near Nagpur) was the first plant in the Indian cement industry to construct a state-of-the-art fully concrete parking yard of 4.5 acres for trucks, with safety features like fishbone parking, one-way movement, no reversing, adequate illumination and separate entrance and exit gates. The parking facility (designed by the renowned Arun Das Associates) has a specially designed resting facility for the drivers with beds, toilets with showers, restaurant, clean drinking water, TV, and recreational and games facilities. The facility had a marked impact on the drivers. Truckers now wanted to visited the plant to pick up loads as they looked forward to a comfortable stay and rest whilst they waited for their turn to be called to roll the truck inside the plant for loading. Proper food, shower and rest ensured an absence of fatigue and safe driving!
Work-life balance: One of the underlying themes of our CSR initiatives is aimed at providing the driver community with adequate work-life balance. This has been achieved through a multipronged strategy of
- providing a financial security net through personal health and accident insurance policy
- more efficient route planning and scheduling of trucks using Fleet Management
- System supported by GPS truck tracking from "Gate Out to Gate In" (GOGI) and RFID for streamlining the "Gate In to Gate Out"(GIGO) flow of trucks inside the plant which help in optimising the truck transit time, thereby enabling drivers to spend less time on the road. The drivers can enjoy more time with their family, eat meals with them more frequently, and sleep better.
Rewarding safe drivers: ACC installed GPS based real time truck tracking systems (IVMS) in all third party dedicated vehicles (in a phased manner) to monitor and analyse driver performance using metrics like over-speeding, route deviation, sudden acceleration, harsh braking, harsh manoeuvring and power disconnection of IVMS.
The MIS is used to develop a monthly "Performance Report Card" of each driver as well as each Road Transport Contractor and the drivers with high performance scores are felicitated and rewarded for at functions attended by their family members (wives, children and sometimes even parents). Many drivers share personal experiences about driving safety and take a pledge to extend this message across the community. In many instances, the company has also sponsored their children’s education as a safe driving reward.
These award functions serve the twin purpose of motivating other drivers to drive safely and instilling a sense of pride and self confidence in them as well as their family members. The drivers also feel that they have earned the respect of the Management when they are called upon the stage to receive their awards. Some plants have even displayed life size photographs of drivers with good safety record in their plants to motivate them.
Driver Chaupal and toolbox talks: Plants have been organising "toolbox" safety talks for drivers as informal group discussions that focus on a particular safety issue (like driving in monsoon, or risk associated with worn out tyres, importance of rest and breaks, benefits of using seat belts, safe way of tarpaulin tying, use of PPE, danger of using mobile phones whilst driving, etc). These talks are used daily to promote a safety culture as well as to facilitate health and safety discussions, often with the help of a nukkad natak.
A unique initiative taken by some ACC plants was organising a "Driver Chaupal" on a weekly basis, attended by all drivers present in the parking yard on the particular day. These are typically like corporate "town halls" where drivers get an opportunity to voice their opinions on matters affecting them like plant amenities (drinking water, canteen facility etc) and the senior management can take quick action to redress any genuine grievances.
Seat belt usage: Very few truck drivers in India have a habit of wearing a seat belt, except at police check posts to escape being fined. A bigger concern is the absence of a proper driver seat and 3 Point retractable seat belts in the older truck models. Ideally, a driver’s seat needs to be with a head restraint, adjustable and fold-down backrest, vertical and fore-aft adjustment, adjustable lumbar support and adjustable seat angle. Many of the older trucks’ driver seats do not have these features and there is no provision for fitting a retractable seat belt. Often the trucks were found to have just a common belt strap with a buckle which the drivers will tighten across their stomach to escape from penalties or fines. Many drivers carried a belief that wearing a seat belt may put them at a greater risk as they may not be able to jump out in case the truck rolls over a hill. It took painstaking effort and scores of meetings with drivers and road transport contractors to dispel this wrong notion. We also impressed upon our road transport contractors to retrofit proper seat and seat belt.
ACC also launched a "Suraksha Kavach" ("security armour") drive at plants to successfully introduce the use of a Seat Belt Convincer to demonstrate the importance of wearing a seat belt whilst driving. The Seat Belt Convincer is a crash simulator training device that simulates a low impact vehicle collision (within a speed range of 8 to 15 kmph) to reinforce the benefits of wearing a seat belt whenever the vehicle is in motion.
Truck Simulators with adjustable virtual traffic, weather conditions and road layouts were also used to train drivers and manoeuvre the vehicles in different weather conditions and terrains. The simulator allows possibility of encountering dangerous driving conditions without subjecting the driver to physical risk.
Self-cooking facility: A majority of truck drivers do their own cooking using a kerosene stove and essential utensils. It is not uncommon to find the driver and helper lighting up a stove under their truck or inside the cabin, ignoring the immense fire and explosion hazard. Both as a CSR and safety initiative ACC created kitchen facilities near the drivers’ rest rooms, equipped with running water for cleaning utensils, drinking water and cooking gas stove. The drivers were delighted with this (free of charge) facility which reduced their hardship and provided a clean, hygienic, convenient and safe place to cook their meals. It also encouraged camaraderie amongst the drivers.
Conclusion
Though our CSR and Logistics Safety Excellence journey is a decade old, we realise we have a lot of ground to cover and, to quote Robert Frost, "have promises to keep and miles to go’. We also realise that it is not enough to pursue driver community issues as a side activity. Rather, uplifting the drivers" lives needs to be an integral part of our core business strategy. Through our initiatives we help our driver partners to earn a sustainable livelihood and live a life of self-respect, dignity and pride.
Foonote:
ABOUT THE AUTHOR:
Rajesh Seth, Director Logistics (Retd), ACC. He is IIM Ahmadabad, alumnus and has held many executive positions during his association with ACC Ltd. Today he is a visiting faculty and advisor on logistics.
BOX:
ACC’s road safety improvement programme
To tackle some of the above issues, ACC embarked on a Logistics Safety Excellence journey in 2011 with a holistic Road Safety Improvement Programme (RSIP) with a "Zero Harm" vision spanning across all the seventeen cement plants and its subsidiary Bulk Cement Corporation (India) at Kalamboli (in Navi Mumbai). RSIP had a clear, well-defined objective focusing on People, Vehicles and Processes. The program was designed in a modular format in two phases -Phase 1 covering 8 easy-to-implement steps ("low hanging fruits") and Phase 2 covering 16 steps (requiring a longer period for implementation). There was a strong emphasis on knowledge sharing and replication of best practices across all plants.
The RSIP essentially focused on:
People/Partners – defensive driving training and CSR initiatives for drivers
Vehicles – their maintenance, adherence to a 30-point checklist and road worthiness, and
Processes – traffic management, hazard identification-cum-mitigation, Journey Risk Mapping (JRM) and Driver Management Centers (DMCs).
- The DMCs were set up at all plant locations to provide valuable support like
- Defensive Driving Induction training (DDI) for new drivers,
- Defensive Driving Courses for all drivers,
- Training through truck simulators,
- In-cab assessment, and
- JRM briefings and debriefings
- Driver performance assessment using "In Vehicle Monitoring System" (IVMS) and GPS
A Transport Control Tower (TCT) was set up in 2018 as a nodal point to monitor the driving patterns of the drivers and provide them counselling on safe driving. The installation of IVMS brought more vehicles within the ambit of TCT monitoring and counselling. In-camera counselling for drivers was also launched across all plants. Anti-toppling devices were fitted in transit mixers to prevent accidents caused by roll-over of mixers.
Another unique initiative was the introduction of "driver passport" for each driver (certifying his fitness to drive on company’s work) and a "Vehicle Passport" for each vehicle (certifying its road worthiness to ply on company’s business. These were earlier manual, but later changed to an electronic format. Around 30,000 vehicles and drivers (outbound and inbound) belonging to over 250 Authorised Road Transport Contractors were covered under the program. This practice was also shared with the Cement Sustainability Initiative (Task Force 3 for Driving and Contractor Safety) of the global CEO-led World Business Council for Sustainable Development (WBCSD) and adopted by other CSI member companies in the Indian cement industry.
You may like
-
Bridge Collapse Spurs Focus on Stainless Steel
-
Protection, Promotion & Projection
-
Core sector contracts by 38.1% in April 2020
-
Terex MPS plant aids limestone production for JSW in Middle East
-
Highways, shipping surge ahead on the back of infrastructure push
-
Gadkari flags off two cargo vessels from Varanasi
Concrete
India donates 225t of cement for Myanmar earthquake relief
Published
3 months agoon
June 17, 2025By
admin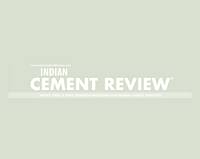
On 23 May 2025, the Indian Navy ship UMS Myitkyina arrived at Thilawa (MITT) port carrying 225 tonnes of cement provided by the Indian government to aid post-earthquake rebuilding efforts in Myanmar. As reported by the Global Light of Myanmar, a formal handover of 4500 50kg cement bags took place that afternoon. The Yangon Region authorities managed the loading of the cement onto trucks for distribution to the earthquake-affected zones.
Concrete
Reclamation of Used Oil for a Greener Future
Published
3 months agoon
June 16, 2025By
admin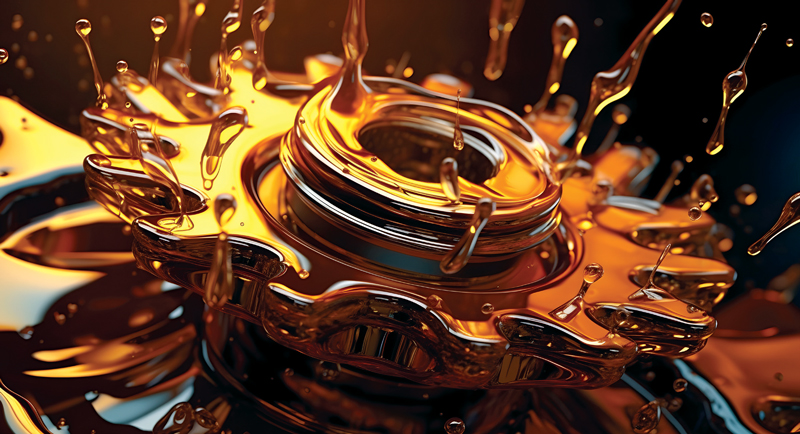
In this insightful article, KB Mathur, Founder and Director, Global Technical Services, explores how reclaiming used lubricants through advanced filtration and on-site testing can drive cost savings, enhance productivity, and support a greener industrial future. Read on to discover how oil regeneration is revolutionising sustainability in cement and core industries.
The core principle of the circular economy is to redefine the life cycle of materials and products. Unlike traditional linear models where waste from industrial production is dumped/discarded into the environment causing immense harm to the environment;the circular model seeks to keep materials literally in continuous circulation. This is achievedthrough processes cycle of reduction, regeneration, validating (testing) and reuse. Product once
validated as fit, this model ensures that products and materials are reintroduced into the production system, minimising waste. The result? Cleaner and greener manufacturing that fosters a more sustainable planet for future generations.
The current landscape of lubricants
Modern lubricants, typically derived from refined hydrocarbons, made from highly refined petroleum base stocks from crude oil. These play a critical role in maintaining the performance of machinery by reducing friction, enabling smooth operation, preventing damage and wear. However, most of these lubricants; derived from finite petroleum resources pose an environmental challenge once used and disposed of. As industries become increasingly conscious of their environmental impact, the paramount importance or focus is shifting towards reducing the carbon footprint and maximising the lifespan of lubricants; not just for environmental reasons but also to optimise operational costs.
During operations, lubricants often lose their efficacy and performance due to contamination and depletion of additives. When these oils reach their rejection limits (as they will now offer poor or bad lubrication) determined through laboratory testing, they are typically discarded contributing to environmental contamination and pollution.
But here lies an opportunity: Used lubricants can be regenerated and recharged, restoring them to their original performance level. This not only mitigates environmental pollution but also supports a circular economy by reducing waste and conserving resources.
Circular economy in lubricants
In the world of industrial machinery, lubricating oils while essential; are often misunderstood in terms of their life cycle. When oils are used in machinery, they don’t simply ‘DIE’. Instead, they become contaminated with moisture (water) and solid contaminants like dust, dirt, and wear debris. These contaminants degrade the oil’s effectiveness but do not render it completely unusable. Used lubricants can be regenerated via advanced filtration processes/systems and recharged with the use of performance enhancing additives hence restoring them. These oils are brought back to ‘As-New’ levels. This new fresher lubricating oil is formulated to carry out its specific job providing heightened lubrication and reliable performance of the assets with a view of improved machine condition. Hence, contributing to not just cost savings but leading to magnified productivity, and diminished environmental stress.
Save oil, save environment
At Global Technical Services (GTS), we specialise in the regeneration of hydraulic oils and gear oils used in plant operations. While we don’t recommend the regeneration of engine oils due to the complexity of contaminants and additives, our process ensures the continued utility of oils in other applications, offering both cost-saving and environmental benefits.
Regeneration process
Our regeneration plant employs state-of-the-art advanced contamination removal systems including fine and depth filters designed to remove dirt, wear particles, sludge, varnish, and water. Once contaminants are removed, the oil undergoes comprehensive testing to assess its physico-chemical properties and contamination levels. The test results indicate the status of the regenerated oil as compared to the fresh oil.
Depending upon the status the oil is further supplemented with high performance additives to bring it back to the desired specifications, under the guidance of an experienced lubrication technologist.
Contamination Removal ? Testing ? Additive Addition
(to be determined after testing in oil test laboratory)
The steps involved in this process are as follows:
1. Contamination removal: Using advanced filtration techniques to remove contaminants.
2. Testing: Assessing the oil’s properties to determine if it meets the required performance standards.
3. Additive addition: Based on testing results, performance-enhancing additives are added to restore the oil’s original characteristics.
On-site oil testing laboratories
The used oil from the machine passes through 5th generation fine filtration to be reclaimed as ‘New Oil’ and fit to use as per stringent industry standards.
To effectively implement circular economy principles in oil reclamation from used oil, establishing an on-site oil testing laboratory is crucial at any large plants or sites. Scientific testing methods ensure that regenerated oil meets the specifications required for optimal machine performance, making it suitable for reuse as ‘New Oil’ (within specified tolerances). Hence, it can be reused safely by reintroducing it in the machines.
The key parameters to be tested for regenerated hydraulic, gear and transmission oils (except Engine oils) include both physical and chemical characteristics of the lubricant:
- Kinematic Viscosity
- Flash Point
- Total Acid Number
- Moisture / Water Content
- Oil Cleanliness
- Elemental Analysis (Particulates, Additives and Contaminants)
- Insoluble
The presence of an on-site laboratory is essential for making quick decisions; ensuring that test reports are available within 36 to 48 hours and this prevents potential mechanical issues/ failures from arising due to poor lubrication. This symbiotic and cyclic process helps not only reduce waste and conserve oil, but also contributes in achieving cost savings and playing a big role in green economy.
Conclusion
The future of industrial operations depends on sustainability, and reclaiming used lubricating oils plays a critical role in this transformation. Through 5th Generation Filtration processes, lubricants can be regenerated and restored to their original levels, contributing to both environmental preservation and economic efficiency.
What would happen if we didn’t recycle our lubricants? Let’s review the quadruple impacts as mentioned below:
1. Oil Conservation and Environmental Impact: Used lubricating oils after usage are normally burnt or sold to a vendor which can be misused leading to pollution. Regenerating oils rather than discarding prevents unnecessary waste and reduces the environmental footprint of the industry. It helps save invaluable resources, aligning with the principles of sustainability and the circular economy. All lubricating oils (except engine oils) can be regenerated and brought to the level of ‘As New Oils’.
2. Cost Reduction Impact: By extending the life of lubricants, industries can significantly cut down on operating costs associated with frequent oil changes, leading to considerable savings over time. Lubricating oils are expensive and saving of lubricants by the process of regeneration will overall be a game changer and highly economical to the core industries.
3. Timely Decisions Impact: Having an oil testing laboratory at site is of prime importance for getting test reports within 36 to 48 hours enabling quick decisions in critical matters that may
lead to complete shutdown of the invaluable asset/equipment.
4. Green Economy Impact: Oil Regeneration is a fundamental part of the green economy. Supporting industries in their efforts to reduce waste, conserve resources, and minimise pollution is ‘The Need of Our Times’.
About the author:
KB Mathur, Founder & Director, Global Technical Services, is a seasoned mechanical engineer with 56 years of experience in India’s oil industry and industrial reliability. He pioneered ‘Total Lubrication Management’ and has been serving the mining and cement sectors since 1999.
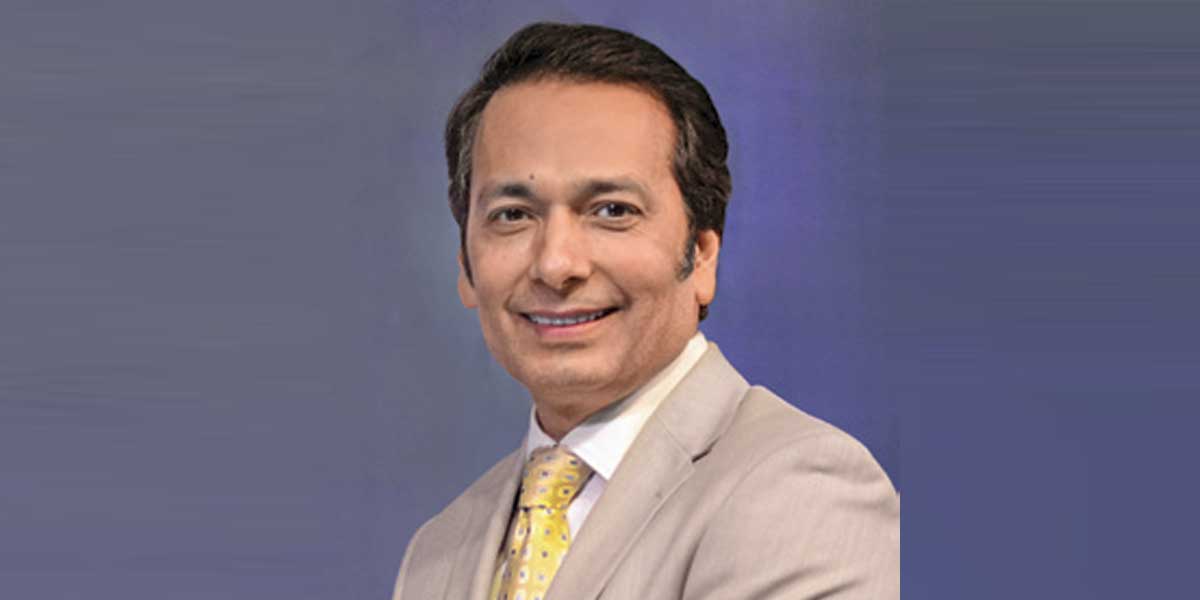
The Indian cement industry has reached a critical juncture in its sustainability journey. In a landmark move, the Ministry of Environment, Forest and Climate Change has, for the first time, announced greenhouse gas (GHG) emission intensity reduction targets for 282 entities, including 186 cement plants, under the Carbon Credit Trading Scheme, 2023. These targets, to be enforced starting FY2025-26, are aligned with India’s overarching ambition of achieving net zero emissions by 2070.
Cement manufacturing is intrinsically carbon-intensive, contributing to around 7 per cent of global GHG emissions, or approximately 3.8 billion tonnes annually. In India, the sector is responsible for 6 per cent of total emissions, underscoring its critical role in national climate mitigation strategies. This regulatory push, though long overdue, marks a significant shift towards accountability and structured decarbonisation.
However, the path to a greener cement sector is fraught with challenges—economic viability, regulatory ambiguity, and technical limitations continue to hinder the widespread adoption of sustainable alternatives. A major gap lies in the lack of a clear, India-specific definition for ‘green cement’, which is essential to establish standards and drive industry-wide transformation.
Despite these hurdles, the industry holds immense potential to emerge as a climate champion. Studies estimate that through targeted decarbonisation strategies—ranging from clinker substitution and alternative fuels to carbon capture and innovative product development—the sector could reduce emissions by 400 to 500 million metric tonnes by 2030.
Collaborations between key stakeholders and industry-wide awareness initiatives (such as Earth Day) are already fostering momentum. The responsibility now lies with producers, regulators and technology providers to fast-track innovation and investment.
The time to act is now. A sustainable cement industry is not only possible—it is imperative.