Environment
Reaping Twin Benefits
Published
7 years agoon
By
admin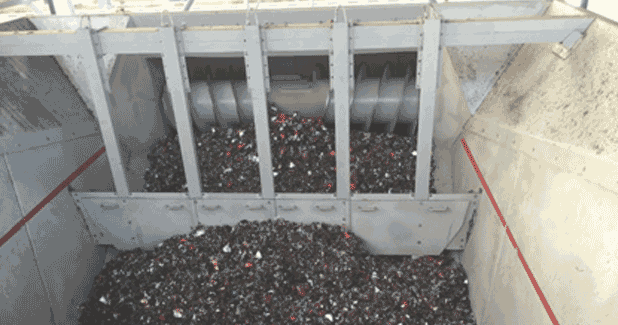
Use of alternative fuels in cement kilns can create a win-win situation for cement companies and urban local bodies by promoting better waste management practices.
Though there are many ways through which cost advantage of a cement company could be improved, increasing the use of alternative fuels and raw materials (AFR) is one of the important means to achieve the goal. Since the fuel costs have shown an upward trend over last few years, affecting the total manufacturing cost at their plants, the focus on AFR substitution rates have increased in the cement manufacturing process.
The use of AFR reduces carbon emissions that result from using fossil fuels and reduce the overall environmental impact of cement manufacturing process and will help in achieving industry and national emission targets.
The Indian cement industry has set voluntary and ambitious emission reduction targets to reduce 45 per cent of its carbon emissions intensity by 2050 from the 2010 levels. As one of the global leaders in energy efficiency, the Indian cement industry has also committed to reduce 377 – 485 PJ of energy in 2050 compared to business-as-usual (BAU) scenario. Moreover, the Government has committed to reduce emissions intensity of its Gross Domestic Product (GDP) by 33 to 35 per cent by 2030 from 2005 level.
"The potential to reduce emissions from cement is significant, since a one per cent increase in thermal substitution rate (TSR) will result in reduction of 2-3 kg carbon (CO) reduction/ tonne of cement," says Milind Murumkar, Advisor & Consultant for AFRM.
Usage pattern
Alternative fuel use (thermal substitution rate or TSR) increased from 0.6 per cent in 2010 to 3.7 per cent in 2015 and then dropped to 2.7 per cent in 2017, according to the report Low Carbon Technology Roadmap (LCTR) for the Indian Cement Sector: Status Review 2018 released by World Business Council for Sustainable Development (WBCSD).
The upward trend in alternative fuel use tapered off in 2016 and 2017 due to the comparative increase in prices of certain alternative fuels, making them uncompetitive to use instead of conventional fuels. This trend is expected to reverse and climb in the years to come due to improved economics, WBCSD exuded hope. More than 60 cement plants in India have reported continual use of alternative fuels. The sector consumed more than 1.5 million tonnes of alternative fuels in 2015. Biomass is 24 per cent of the total alternative fuel consumed.
Over the years, petcoke consumption has increased steadily in the Indian cement industry, mainly owing to the cost advantage it offers. Coal use (Indian and imported) has been declining over the years, and petcoke and alternative fuels are gradually replacing it. In 2017 the share of coal was 41 per cent while that of petcoke was 56 per cent and alternative fuels was 3 per cent. Changes in the fuel mix have lowered carbon intensity by 2 kgCO2/t cement. The overall emissions factor (for coal and petcoke) decreased to 94.1 kgCO2/GJ in 2017 from 94.7 kgCO2/GJ in 2010.
While terming the TSR in Indian cement industry as remarkably low when compared to the standards of Europe where the AFR substitution rate is more than 40 per cent, Ashok Kumar Dembla, Managing Director & President, Sita Ram Sharma, Head – Parts & Services, both from Humboldt Wedag India say, "There is huge scope for improving the figures that we are clocking today. It needs continuous support from Government and associated bodies. A critically reviewed vision plan to be laid out involving all the stakeholders to target the TSR levels of developed nations."
Picking up pace The concept of co-processing of waste in the cement kilns has been catching up over a period of last 3-4 years. Murumkar attributes this rising use of AFR to the continuously increasing cost of fossil fuels, severely affecting the operating margins of the cement manufacturers, and the regulatory initiatives taken during the recent years.
Regulatory drivers have also accelerated the co-processing of waste by cement companies. The Ministry of Environment Forests and Climate Change (MoEFCC) issued its Solid Waste Management Rules in 2016. These rules give preferential status to the co-processing of waste as a management option. Some state pollution control boards (SPCBs) have approved inter-state transportation of hazardous waste to encourage co-processing. "Together, these have resulted in increasing alternative fuel use," says WBCSD report.
India’s cement sector, being one of the eight core energy intensive sectors, is a part of PAT scheme (Perform, Achieve and Trade), launched under the National Mission to Enhance Energy Efficiency (NMEEE). The cement industry has been one of the major contributors to energy reductions in PAT Cycle 1, having surpassed its targets by more than 80 per cent. "Considering that latest technologies for energy reduction including waste heat recovery systems (WHRS), grinding systems etc., which are being widely adopted, one of the main levers to achieve PAT targets in the future is increasing AFR substitution in cement kilns," says Murumkar.
Waste management
In a BAU scenario, India will require a landfill area of 8,800 hectares by 2050. This is equivalent to the size of the city of New Delhi. By using 25 per cent AFR by 2050 (as per the objectives of the LCTR), the cement industry can contribute to a 26 per cent reduction in the space required for landfilling. About 80 per cent of the estimated 62 million tonnes of MSW generated in India is indiscriminately disposed of in dump sites.
Cement industries can certainly play a key role in promoting better waste management practices and create a win-win situation by working with urban local bodies on waste segregation and management of municipal solid waste. Indian cement plants have used different types of waste as alternative fuels. Solid waste is 73 per cent of total alternative fuel use. The major types of solid waste used are carbon black, tire chips, refuse-derived fuel (RDF), captive power plant (CPP) bed ash and dolachar. Substantial fractions of industrial, commercial, domestic and other wastes contain materials that have the potential for use as an alternative raw material or as a supplementary fuel for energy recovery in cement kilns.
The basic reasons for low TSR can be broadly assigned to lack of knowledge on AFR usage in Indian cement industry in the early years, especially on usage of industrial waste, lack of skilled persons for handling and usage of industrial wastes, lack of proper infrastructure for storage and feeding of AFR materials to cement kilns, lack of proper understanding on the permitting process in regulatory bodies and above all, the will to receive and use the waste materials in cement plants, says Murumkar. In the last two years, remarkable transformation has been noticed on all the above aspects with dramatic changes in the mindset of regulatory bodies, the plant operating professionals and also of waste generators who are shifting to co-processing as a better option over landfilling and incineration as it provides a cost-effective option to them, Murumkar adds.
Improving use
AFR can be used alone also as fuel in cement kilns. A proper understanding of the processes, raw material characteristics and the waste compositions are the key factors that need to be assessed before use of AFR in a particular kiln system… Actions by all stakeholders are critical for realisation of the vision to become reality. The government and industry must take collaborative action to create a favourable framework for accelerating and implementation of AFR usage in cement plants. "The government should create and enable level playing field for the AFR users by providing interim financial stimulus packages that compensate and provide an edge in pricing pressures. Also, the government should take initiatives to establish the state-of-art waste treatment plants, crop waste processing units etc., in collaboration with cement plants in that particular cluster to supply segregated and treated alternative fuels," say authors of an article for ICR from Humboldt Wedag India.
The main technical barrier is the adverse impact created on kiln production and specific energy consumption. The companies are in the process of developing a complete understanding of the impacts of minor constituents and what effects they might have on long-term cement performance.
For putting latest and innovative technol- ogical change into action, Humboldt Wedag India suggests that all stakeholders should intensify collaborative action to increase the implementation of the state-of-the-art technologies and share best operating practices. "The governments and industry should ensure sustained funding and supportive risk-mitigating mechanisms to promote the development and demonstration of new technologies and processes that offer increase in AFR utilisation."
Way forward
It has been proven beyond doubt that, in a cement kiln, the organic constituents of fuel are completely destroyed and the inorganic constituents combine with the raw materials and exit as part of the cement clinker without generating solid residues, thus providing the best solution for waste management, says Murumkar.
So, AFR offers twin benefits of benefiting cement companies on one side and managing huge quantities of waste on the other. The government must provide incentives for the use of RDF derived from municipal solid waste and biomass to promote high-volume use of these AFRs for deriving the maximum social benefit.
The industry has set for itself to achieve a 25 per cent TSR target by 2050. For Indian cement plants to increase TSR by 25 per cent (in 2050), a major barrier is cost of material sourcing and acquisition, says WBCSD.
The cost of sourcing the material should be regulated by applying "polluter pays principle" by imbibing the principle among waste generating industries. Higher fuel substitution will take place if waste legislation restricts landfilling and dedicated incineration and allows controlled collection and treatment of alternative fuels. Thus, it is imperative to know that co-processing can offer a local and desired route to manage wastes with minimum liability and environmental impact addressing all the requirements of sustainable development and help reducing our energy demand from natural resources.
– BS SRINIVASALU REDDY
Concrete
India donates 225t of cement for Myanmar earthquake relief
Published
3 months agoon
June 17, 2025By
admin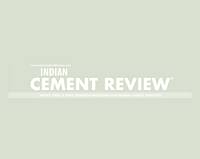
On 23 May 2025, the Indian Navy ship UMS Myitkyina arrived at Thilawa (MITT) port carrying 225 tonnes of cement provided by the Indian government to aid post-earthquake rebuilding efforts in Myanmar. As reported by the Global Light of Myanmar, a formal handover of 4500 50kg cement bags took place that afternoon. The Yangon Region authorities managed the loading of the cement onto trucks for distribution to the earthquake-affected zones.
Concrete
Reclamation of Used Oil for a Greener Future
Published
3 months agoon
June 16, 2025By
admin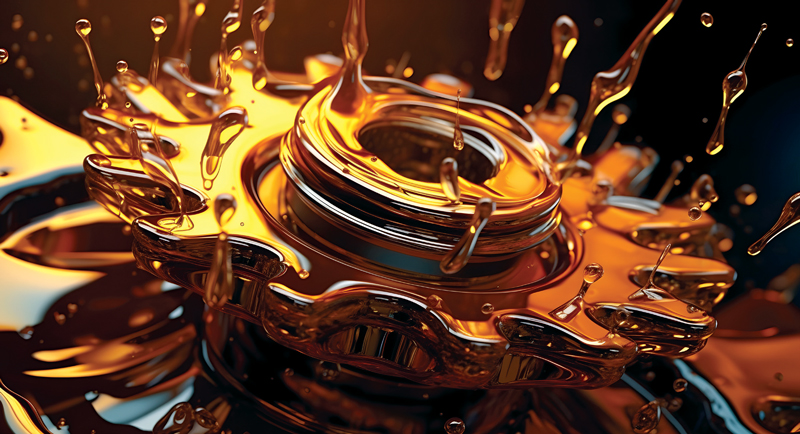
In this insightful article, KB Mathur, Founder and Director, Global Technical Services, explores how reclaiming used lubricants through advanced filtration and on-site testing can drive cost savings, enhance productivity, and support a greener industrial future. Read on to discover how oil regeneration is revolutionising sustainability in cement and core industries.
The core principle of the circular economy is to redefine the life cycle of materials and products. Unlike traditional linear models where waste from industrial production is dumped/discarded into the environment causing immense harm to the environment;the circular model seeks to keep materials literally in continuous circulation. This is achievedthrough processes cycle of reduction, regeneration, validating (testing) and reuse. Product once
validated as fit, this model ensures that products and materials are reintroduced into the production system, minimising waste. The result? Cleaner and greener manufacturing that fosters a more sustainable planet for future generations.
The current landscape of lubricants
Modern lubricants, typically derived from refined hydrocarbons, made from highly refined petroleum base stocks from crude oil. These play a critical role in maintaining the performance of machinery by reducing friction, enabling smooth operation, preventing damage and wear. However, most of these lubricants; derived from finite petroleum resources pose an environmental challenge once used and disposed of. As industries become increasingly conscious of their environmental impact, the paramount importance or focus is shifting towards reducing the carbon footprint and maximising the lifespan of lubricants; not just for environmental reasons but also to optimise operational costs.
During operations, lubricants often lose their efficacy and performance due to contamination and depletion of additives. When these oils reach their rejection limits (as they will now offer poor or bad lubrication) determined through laboratory testing, they are typically discarded contributing to environmental contamination and pollution.
But here lies an opportunity: Used lubricants can be regenerated and recharged, restoring them to their original performance level. This not only mitigates environmental pollution but also supports a circular economy by reducing waste and conserving resources.
Circular economy in lubricants
In the world of industrial machinery, lubricating oils while essential; are often misunderstood in terms of their life cycle. When oils are used in machinery, they don’t simply ‘DIE’. Instead, they become contaminated with moisture (water) and solid contaminants like dust, dirt, and wear debris. These contaminants degrade the oil’s effectiveness but do not render it completely unusable. Used lubricants can be regenerated via advanced filtration processes/systems and recharged with the use of performance enhancing additives hence restoring them. These oils are brought back to ‘As-New’ levels. This new fresher lubricating oil is formulated to carry out its specific job providing heightened lubrication and reliable performance of the assets with a view of improved machine condition. Hence, contributing to not just cost savings but leading to magnified productivity, and diminished environmental stress.
Save oil, save environment
At Global Technical Services (GTS), we specialise in the regeneration of hydraulic oils and gear oils used in plant operations. While we don’t recommend the regeneration of engine oils due to the complexity of contaminants and additives, our process ensures the continued utility of oils in other applications, offering both cost-saving and environmental benefits.
Regeneration process
Our regeneration plant employs state-of-the-art advanced contamination removal systems including fine and depth filters designed to remove dirt, wear particles, sludge, varnish, and water. Once contaminants are removed, the oil undergoes comprehensive testing to assess its physico-chemical properties and contamination levels. The test results indicate the status of the regenerated oil as compared to the fresh oil.
Depending upon the status the oil is further supplemented with high performance additives to bring it back to the desired specifications, under the guidance of an experienced lubrication technologist.
Contamination Removal ? Testing ? Additive Addition
(to be determined after testing in oil test laboratory)
The steps involved in this process are as follows:
1. Contamination removal: Using advanced filtration techniques to remove contaminants.
2. Testing: Assessing the oil’s properties to determine if it meets the required performance standards.
3. Additive addition: Based on testing results, performance-enhancing additives are added to restore the oil’s original characteristics.
On-site oil testing laboratories
The used oil from the machine passes through 5th generation fine filtration to be reclaimed as ‘New Oil’ and fit to use as per stringent industry standards.
To effectively implement circular economy principles in oil reclamation from used oil, establishing an on-site oil testing laboratory is crucial at any large plants or sites. Scientific testing methods ensure that regenerated oil meets the specifications required for optimal machine performance, making it suitable for reuse as ‘New Oil’ (within specified tolerances). Hence, it can be reused safely by reintroducing it in the machines.
The key parameters to be tested for regenerated hydraulic, gear and transmission oils (except Engine oils) include both physical and chemical characteristics of the lubricant:
- Kinematic Viscosity
- Flash Point
- Total Acid Number
- Moisture / Water Content
- Oil Cleanliness
- Elemental Analysis (Particulates, Additives and Contaminants)
- Insoluble
The presence of an on-site laboratory is essential for making quick decisions; ensuring that test reports are available within 36 to 48 hours and this prevents potential mechanical issues/ failures from arising due to poor lubrication. This symbiotic and cyclic process helps not only reduce waste and conserve oil, but also contributes in achieving cost savings and playing a big role in green economy.
Conclusion
The future of industrial operations depends on sustainability, and reclaiming used lubricating oils plays a critical role in this transformation. Through 5th Generation Filtration processes, lubricants can be regenerated and restored to their original levels, contributing to both environmental preservation and economic efficiency.
What would happen if we didn’t recycle our lubricants? Let’s review the quadruple impacts as mentioned below:
1. Oil Conservation and Environmental Impact: Used lubricating oils after usage are normally burnt or sold to a vendor which can be misused leading to pollution. Regenerating oils rather than discarding prevents unnecessary waste and reduces the environmental footprint of the industry. It helps save invaluable resources, aligning with the principles of sustainability and the circular economy. All lubricating oils (except engine oils) can be regenerated and brought to the level of ‘As New Oils’.
2. Cost Reduction Impact: By extending the life of lubricants, industries can significantly cut down on operating costs associated with frequent oil changes, leading to considerable savings over time. Lubricating oils are expensive and saving of lubricants by the process of regeneration will overall be a game changer and highly economical to the core industries.
3. Timely Decisions Impact: Having an oil testing laboratory at site is of prime importance for getting test reports within 36 to 48 hours enabling quick decisions in critical matters that may
lead to complete shutdown of the invaluable asset/equipment.
4. Green Economy Impact: Oil Regeneration is a fundamental part of the green economy. Supporting industries in their efforts to reduce waste, conserve resources, and minimise pollution is ‘The Need of Our Times’.
About the author:
KB Mathur, Founder & Director, Global Technical Services, is a seasoned mechanical engineer with 56 years of experience in India’s oil industry and industrial reliability. He pioneered ‘Total Lubrication Management’ and has been serving the mining and cement sectors since 1999.
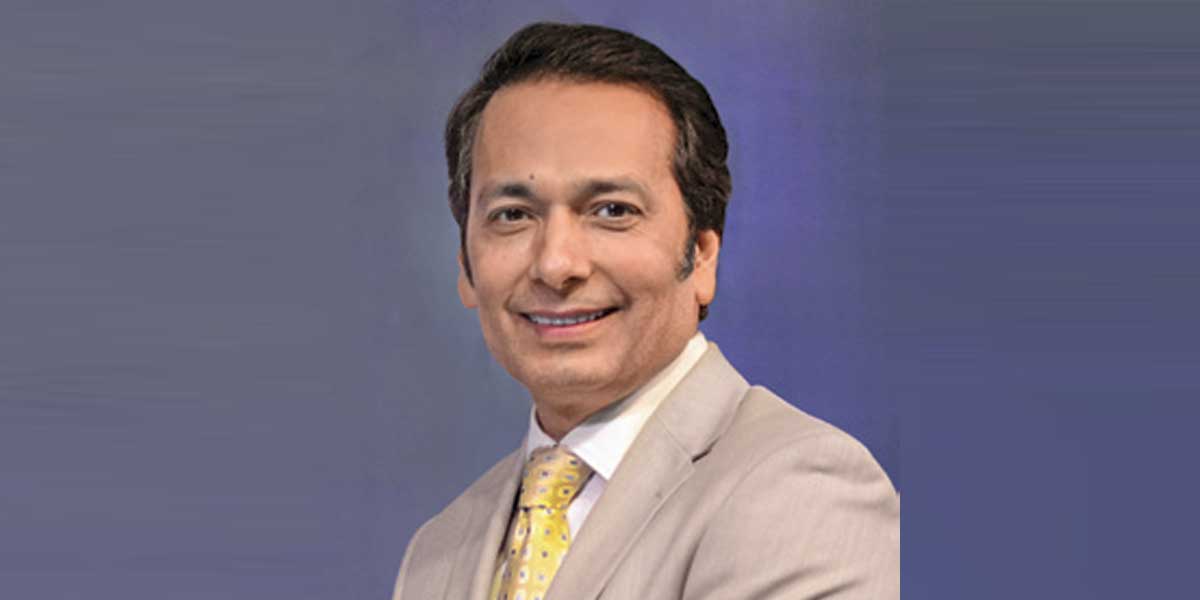
The Indian cement industry has reached a critical juncture in its sustainability journey. In a landmark move, the Ministry of Environment, Forest and Climate Change has, for the first time, announced greenhouse gas (GHG) emission intensity reduction targets for 282 entities, including 186 cement plants, under the Carbon Credit Trading Scheme, 2023. These targets, to be enforced starting FY2025-26, are aligned with India’s overarching ambition of achieving net zero emissions by 2070.
Cement manufacturing is intrinsically carbon-intensive, contributing to around 7 per cent of global GHG emissions, or approximately 3.8 billion tonnes annually. In India, the sector is responsible for 6 per cent of total emissions, underscoring its critical role in national climate mitigation strategies. This regulatory push, though long overdue, marks a significant shift towards accountability and structured decarbonisation.
However, the path to a greener cement sector is fraught with challenges—economic viability, regulatory ambiguity, and technical limitations continue to hinder the widespread adoption of sustainable alternatives. A major gap lies in the lack of a clear, India-specific definition for ‘green cement’, which is essential to establish standards and drive industry-wide transformation.
Despite these hurdles, the industry holds immense potential to emerge as a climate champion. Studies estimate that through targeted decarbonisation strategies—ranging from clinker substitution and alternative fuels to carbon capture and innovative product development—the sector could reduce emissions by 400 to 500 million metric tonnes by 2030.
Collaborations between key stakeholders and industry-wide awareness initiatives (such as Earth Day) are already fostering momentum. The responsibility now lies with producers, regulators and technology providers to fast-track innovation and investment.
The time to act is now. A sustainable cement industry is not only possible—it is imperative.