Process
Waste to Wealth – Optimising AFR Utilisation
Published
10 years agoon
By
admin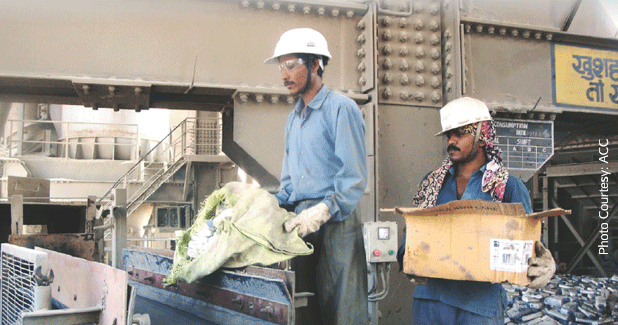
Despite various technological barriers and absence of proper regulation and enabling policy framework this is an opportune time for the Indian cement industry to focus all its efforts on increasing co-processing.
While developed countries have successfully achieved a TSR rate over 40 per cent, in certain cases even up to 80 per cent, in India it is around a meager one per cent; and the target set for 2020 is just 5 per cent. What the industry needs is specific policy and regulatory framework that help enhance the AFR utlisation.
Cement plants can dispose different kinds of wastes in an environmentally sound manner, without any residue for further treatment and disposal. Co-processing offers an environment-friendly waste solution that is superior to land filling or incineration. Cement kiln co-processing facilitates zero waste future having no concern or liability of the generated waste. While disposing wastes, cement kiln recovers the energy and recycle raw material in it, thereby reducing the use of traditional renewable fuels and raw materials.
The global scenario
Some of the energy-intensive industries when became unviable due to very high cost of energy have been able to transform themselves into viable industries by co-processing waste as an alternate fuel. Tracking the history of AFR usage Axel Pieters, Head, Geocycle India, says, ?About 25 years ago, Geocycle Belgium initiated the use of waste as alternative fuel. This plant turned from a low profit to a high profit plant. Over a period, investments of the order of $30 million were made to develop state-of-the-art facilities to move to a significant TSR percentage in this plant.? According to Pieters 80 TSR is considered to be a remarkable achievement. In some developed countries, where the waste markets are mature and legislation and enforcement are in place, these numbers can be achieved. Here, the society at large is ready to invest in a clean environment.
Legislation – the enabler
What kind of legislation is there in developed countries for the industry to make long term investments to reach very high levels of TSR like 60-80 per cent? Pieters sheds some light. Countries like Germany, Belgium, France, Switzerland and Norway have already reached the figures of 60-90 per cent of TSR in many cases. A part of Eastern European countries, which moved to European Union later on, are raising their investments now. European Union has a policy to reduce 40 per cent landfill area by 2020 as compared to what it was in 1998, otherwise these countries will get penalties. Therefore, there is a mandatory drive to implement the landfill directive. There is a big strive in Eastern Europe to raise TSR levels.
Says Shashank Jain, Programme Manager (Industry), Shakti Sustainable Energy Foundation, ?Cement kilns, in-fact, in the developed countries are seen as an effective option for disposing industrial and urban waste. Enabling policy and regulatory environment has helped these countries manage the waste as a resource.
Indian scenario
According to Jain TSR in Indian cement industry varies in great range. Few leading plants have achieved high figures in the range 15-20 per cent but most operate below three per cent of substitution. Jain is however optimistic. He says, ?AFR usage in cement industry is rising slowly but steadily since last few years. Pollution Control Boards (PCBs) have also become more concerned and acting proactively in terms of speeding up the clearance processes. We are very positive on this and expect TSR to be above five per cent by 2020.?
Policy framework, a must
What is the present policy framework in India for utilisation of waste and what amendments are needed? According to Pieters high values of TSR indicate that the industry has made investments because there is a conducive policy framework which infuses investments. Plans have to be made in feeding installations and preprocessing installations which are to the tune of $10 million. If one plans to use RDF derived out of municipal solid waste that contains 0.8 per cent of chlorine gas, one has to implement the chlorine by-pass system beyond a certain TSR level. A chlorine by-pass system typically costs about $8 million. In India, the installation of a chlorine by-pass is blocked due to legal limitations.?
? At Geocycle India, we have made investments for implementing co-processing solution for the wastes and expect a reasonable return on investment for the same. However, in the Indian set up, the legislation is politically influenced. It is blocking the co-processing of waste by favouring dumping and land filling. It thus becomes difficult for the cement industry to compete. For the environmental protection of the country as such, the policy framework is lagging behind compared to the other countries,? avers Pieters.
Ulhas Parlikar, Deputy Head, External Affairs, R&D, Geocycle India explains it further. According to him most countries are adopting environment-friendly technologies for waste management and co-processing technology has been recognised as one of the preferred technologies in their policy framework. Different kinds of wastes are diverted in these countries to cement kilns for co-processing because co-processing, being a recovery process, is higher in waste management hierarchy over landfill or incineration. In India, co-processing technology has started receiving its deserved recognition now and the policies are getting aligned towards the same. The current permitting process consists of waste-by-waste clearance through an elaborate trial burn process. In India, as of now more than 75 trial burns of different kinds of wastes have been implemented successfully and all have been approved as acceptable by Central Pollution Control Board (CPCB) and State Pollution Control Boards (SPCBs). These wastes ranged from non-hazardous wastes to most dangerous Persistent Organic Pollutants (POPs). Now, therefore, there is a need to move the legislation from waste-by-waste permitting process to infrastructure and emission monitoring-based permitting system.?
According to Rajnish Kapur, Business Head (Grey Cement Division), JK Cement, the time taken to get the approval from the respective authorities for use of AFRs is too long. With the implementation of online monitoring systems the online data is transferred to the concerned board. Hence the board should now issue open clearance system for all the AFRs which have been used in various cement manufacturing units. He adds,?Automatic open clearance system for all cement plants for waste co-incineration is to be given, if the trial has been conducted successfully for that class of material in any cement plant.?
Says KN Rao, Director-Energy & Environment, ACC Ltd, ?Co-processing of alternative fuels in place of fossil fuels and use of non-carbonaceous raw material are aligned to the company climate change mitigation strategy. ACC has deployed huge amount of technical resources and also made huge investments for pre-processing facilities and feeding system in various plants of ACC for use of alternative fuels and raw materials in cement manufacturing process.?
The 2020 target
Action plan has already been drawn up by the Institute of Industrial Productivity (IIP) for Indian cement industry by which the target is to reach five per cent of TSR by the year 2020. According to Kamalkumar, Chief General Manager, Holtec today TSR is less than 1 per cent for the whole of industry. UltraTech is around 0.45 per cent, ACC is 0.6 per cent, My Home is 0.3 per cent. Achieving the target of five per cent of TSR itself seems to be a Herculean task. He says, ?In fact, we have the technical capability to reach the target of five per cent TSR and manufacturers are ready and taking initiatives to achieve the stipulated target. But there has to be a collective mechanism in place. Suppose today one invests in creating a facility to use RDF and in future RDF is not made available to him that is going to create enough trouble. Vikram Cement at Khor has invested in the facility and it is working fine. On the flip side JP cement in HP has invested, however they are not getting RDF.? He adds, ?In short everybody including CMA, SPCB, CPCB are working hard to put the system in place, make it happen. Facilities are being created and we can reach the target in the near future.?
For Parlikar to achieve the target there is an urgent need to implement necessary policy level reforms that are emission monitoring and infrastructure based. Further, there is a need for the cement industry to implement necessary facilities for waste handling, storing, pre-processing and feeding in the kiln. There is also investment required for creating facilities for monitoring and control of emissions. Further, the legislative process needs to bring the material in the market. For example, although, large quantities of tyres are replaced every year in the country, the same is not visible in the waste market. This is because there is no defined regulatory system in place to collect and divert them in the waste market. Once they become visible in the waste market, they will be available to cement industry for disposal through co-processing.
He further points out, ?Similarly, about 60 million tonne of municipal solid waste is generated every year. About 30 per cent of this is non-compostable and non-recyclable combustible fraction which can be converted into Refuse Derived Fuel (RDF). If proper policy framework is put in place, about 10 million tonne of this combustible waste can be disposed as RDF in an environmentally friendly manner through co-processing in the cement kilns. It is also important that the ?polluter pays? principle has to be embedded in the policy framework. This will facilitate generation of enough funds for the proper management of wastes?
Challenges
Inter-state movement: According to KamalKumar the industry is comfortable in using agri waste but when it comes to industrial waste there are issues. When waste moves from one state to another state there are many issues involved. Transportation hurdles is the main bottleneck. Even moving from one district to another is a problem. He quips, ?Cement plants are the best and the most economic solution for waste management. There are challenges which collectively we have to overcome.? Says Kapur ?In case of interstate movement of wastes, permission of both state pollution control board is required. This needs time and efforts. One policy related with movement can be made across the country to promote AFR use, and there is also a need to introduce GPS tracking system for controlling the end use.? Says Jain, ?Permitting inter-state movement of waste will definitely help enhance the use of AFR. However, having clearly defined responsibility of each stakeholder in collection, packaging, transportation, handling and storage, etc will support the decision makers. Similarly, development of operational guidelines with built-in safety features for the earlier mentioned sub-activities will ensure safe and environmentally sound co-processing.?
Speaking about the on-ground reality Parlikar says, ?This is because of the NIMBY syndrome. The receiving state has the concern of owning the liability of the waste that is received for disposal in their incineration or landfill facility. Their additional concern is about quicker depletion of the available disposal capacity of the state through the disposal of waste from other states. Hence, the receiving state has a tendency to oppose the transfer.
However, if it is transferred for implementing co-processing, the waste conserves the natural resources used in that state and also reduces the GHG emissions. Further, being a zero-waste technology, co-processing does not leave any waste footprint in the state and also does not utilise the available capacity of the landfills. In fact, it enhances the available capacity of the existing landfills due to diversion of the landfill material for co-processing. Hence, transfer of wastes across the state is beneficial to the receiving state and should be encouraged.?
Pieters adds, ?This system is practised in different parts of the world successfully. In the entire Europe, waste moves from one country to another. There are well-defined processes in place in Basel Convention that are practiced successfully in these country to country transfers. These processes can be easily adapted for transfer of wastes across the states in India and the Basel convention is already signed by India years ago.?
Cost impact: According to Jain suitable technologies are available for converting MSW to cement grade RDF, which are financially viable also. He says, ?Use of alternate fuels for TSR is a financial viable intervention with very good IRR. It also depends on the type of waste proposed for usage and technical intervention. Many Indian cement plants have successfully implemented these options and substituted fossil fuel significantly. The payback period generally varies between 2-4 years.?
Consistent quality supply: Says Kapur, ?The consistent supply and uniform quality are main constraints in utilising AFRs – for example, tyre carbon black. The cost of the carbon black depends upon the cost of waste tyres in the market/import conditions. Due to high demand for waste tyre, the cost of carbon black is increasing and hence its adulteration too.? He suggests, ?There should be long term agreement with the manufacturers directly with clear quality parameters, thereby the traders can be avoided and can sustain the supply as well as quality. However, the essence of the agreement shall be the price factor with regards to the coal price. Regulatory authorities need to standardise all waste for stream line the market operations.? Speaking about the current emission norms Kapur had this to say. ?There is no existing standard for NOx from kiln. Only SPM standard is 50 mg/Nm3 for new plants and 100 mg/Nm3 for old plants. NO2 standard from 1-1-2016 and SPM standard from 1-6-2016 for cement kiln will be 800 mg/Nm3 and 30 mg/Nm3 respectively. Online monitoring system has been installed and commissioned in plants stacks for monitoring SPM, SO2 and NOx. The online monitoring system has already started. It will help us in controlling emissions while firing different type of AFRs.?
According to Rao the government is gearing up to release regulatory norms for these emissions. ACC has already installed the required measuring systems for these emissions. We are aware of the base line emissions which are very well below the expected norms in majority of their plants. In respect of a few exceptions, the required corrective actions are initiated to address these emissions.
Long way to go
Enhanced AFR usage in kilns will help even exceed energy consumption reduction targets under the Perform- Achieve- Trade (PAT) scheme. We still have a long way to go. There is huge potential for use of AFR.
Kapur sums it up. AFR mission has to be encouraged by government, society, business entities and individuals. Let us not forget cement plants are best disposal of hazardous wastes. It serves mother earth, humanity at large and therefore economical in long run and has to be achieved in collaboration of all stakeholders. Waste to wealth – and that is the way to go.
Agith G Antony
THRUST AREAS TO PROMOTE THE USE OF RDF
- Declare waste to energy as a renewable source of energy
- Amendment in MSW and HWM rules and inclusion of co-processing in cement kilns as a preferred disposal option
- Development of operational guidelines for transportation, storage, and handling of waste
- Suitable market mechanism for promotion of co-processing
- Creation and formalisation of waste hierarchy to direct waste with good heating values for co-processing
- Promote waste segregation and pre-processing
- Develop collaboration between local municipal corporation and cement plants, regular supply of MSW for RDF, capacity building of municipal corporations.
- Information on availability and quality of waste
Reducing the CO2 Footprint – The Road Map
India is the world?s fastest growing cement market with increasing demands giving rise to fast pace infrastructure development. The Indian cement industry has made strong efforts to reduce its carbon footprint being the most efficient in the world. Yet, because the manufacturing process relies on the burning of limestone (calcium carbonate), it produced 137 mt of carbon dioxide (CO2) in 2010 – approximately 7 per cent of India?s total man-made CO2 emissions.
To further reduce CO2 emissions and achieve sustainability, International Energy Agency (IEA) and Cement Sustainability Initiative (CSI) in collaboration with the Confederation of Indian Industry (CII) and the National Council for Cement and Building Materials (NCB) have developed a low carbon technology roadmap specifically for the Indian cement industry as part of their global initiative.
Under this new roadmap, Indian cement industry has set a target of halving its carbon emissions to 0.35 tonnes (t) of CO2/t cement in 2050, about 45 per cent lower than current levels to support the global goal. The roadmap development was spear-headed by the three co-chair companies, ACC, Shree Cement and UltraTech, who committed extensive resources and expertise from across their companies to lead the project.
Key Findings
- Reduction of total CO2 emissions to an industrial average of 0.719 tonne (t) of CO2/t cement in 2010 from a substantially higher level of 1.12 t CO2/t cement in 1996
- CO2 emissions are projected to reach between 488 mt CO2 and 835 mt CO2 by 2050 if suitable technologies and measures are not adopted. This represents a 255 per cent to 510 per cent increase compared to current emissions
- The technologies, policy frameworks and investment needs outlined in this roadmap could reduce CO2 intensity in the Indian cement industry by about 45 per cent by 2050, from the 2010 level
- The milestones for the Indian cement industry set out in this roadmap would enhance energy security by saving between 377 petajoules (PJ) and 485 PJ of energy in 2050 compared to a business-as-usual scenario
- The additional investment required in the Indian cement industry (based on net present value) to achieve the CO2 emissions reduction set out in this roadmap is between $29 billion and $50 billion (`145,000 crore and `250,000 crore), or 15 to 25 per cent higher than in a business-as-usual scenario
- The roadmap also outlines key levers to attain energy efficiency by increasing use of blended cements, alternative fuels and raw materials, widespread implementation of waste heat recovery (WHR) systems, alternative energy sources, research and development, etc.
Courtesy: KN Rao, Director-Energy & Environment, ACC Ltd
POLICY MATTERS
- Implement ?polluters to pay? principle
- Waste has to have hierarchy as per Basel Convention
- Align the regulation with internationally existing codes like Basel Convention
- Encourage segregation at source
- Tax dumping of waste on land
- For inter-state transportation GPS and documentation in electronic form
- Waste for recycling and for dumping needs different treatment in the laws
- Recognise the status of intermediate facilitators
- Time bound clearance for proposals
INITIATIVES TAKEN BY ACC
- A formal policy framework to promote the use of alternative fuels and raw materials
- Pre-processing platform and feeding system in different plants of ACC for different categories of waste with necessary safety system
- Each of the plant has been mapped for its AFR profile
- Installation of machinery and equipment for AFR feeding wherever required
- AFR awareness programs are conducted in all plants
- Establishment of Regional Sustainable Development Federations (RSDF) in north, east and southwest India.
- Identification of wastes generated by other industries across the country to examine the feasibility for co-processing these wastes in our kilns, dryers and captive power plants.
- Testing of hazardous waste samples to assess the scope of their usage as AFR
- ACC?s AFR team is working closely with government, central and state pollution control boards to help popularise co processing of waste in cement kilns.
- ACC?s AFR team is represented on the Technical team of India?s 11th Five Year Plan which will consider AFR as a national initiative.
Process
Price hikes, drop in input costs help cement industry to post positive margins: Care Ratings
Published
4 years agoon
October 21, 2021By
admin
Region-wise,the southern region comprises 35% of the total cement capacity, followed by thenorthern, eastern, western and central region comprising 20%, 18%, 14% and 13%of the capacity, respectively.
The cement industry is expected to post positive margins on decent price hikes over the months, falling raw material prices and marked drop in overall production costs, said an analysis of Care Ratings.
Wholesale and retail prices of cement have increased 11.9% and 12.4%, respectively, in the current financial year. As whole prices have remained elevated in most of the markets in the months of FY20, against the corresponding period of the previous year.
Similarly, electricity and fuel cost have declined 11.9% during 9M FY20 due to drop in crude oil prices. Logistics costs, the biggest cost for cement industry, has also dropped 7.7% (selling and distribution) as the Railways extended the benefit of exemption from busy season surcharge. Moreover, the cost of raw materials, too, declined 5.1% given the price of limestone had fallen 11.3% in the same aforementioned period, the analysis said.
According to Care Ratings, though the overall sales revenue has increased only 1.3%, against 16% growth in the year-ago period, the overall expenditure has declined 3.2% which has benefited the industry largely given the moderation in sales.
Even though FY20 has been subdued in terms of production and demand, the fall in cost of production has still supported the cement industry by clocking in positive margins, the rating agency said.
Cement demand is closely linked to the overall economic growth, particularly the housing and infrastructure sector. The cement sector will be seeing a sharp growth in volumes mainly due to increasing demand from affordable housing and other government infrastructure projects like roads, metros, airports, irrigation.
The government’s newly introduced National Infrastructure Pipeline (NIP), with its target of becoming a $5-trillion economy by 2025, is a detailed road map focused on economic revival through infrastructure development.
The NIP covers a gamut of sectors; rural and urban infrastructure and entails investments of Rs.102 lakh crore to be undertaken by the central government, state governments and the private sector. Of the total projects of the NIP, 42% are under implementation while 19% are under development, 31% are at the conceptual stage and 8% are yet to be classified.
The sectors that will be of focus will be roads, railways, power (renewable and conventional), irrigation and urban infrastructure. These sectors together account for 79% of the proposed investments in six years to 2025. Given the government’s thrust on infrastructure creation, it is likely to benefit the cement industry going forward.
Similarly, the Pradhan Mantri Awaas Yojana, aimed at providing affordable housing, will be a strong driver to lift cement demand. Prices have started correcting Q4 FY20 onwards due to revival in demand of the commodity, the agency said in its analysis.
Industry’s sales revenue has grown at a CAGR of 7.3% during FY15-19 but has grown only 1.3% in the current financial year. Tepid demand throughout the country in the first half of the year has led to the contraction of sales revenue. Fall in the total expenditure of cement firms had aided in improving the operating profit and net profit margins of the industry (OPM was 15.2 during 9M FY19 and NPM was 3.1 during 9M FY19). Interest coverage ratio, too, has improved on an overall basis (ICR was 3.3 during 9M FY19).
According to Cement Manufacturers Association, India accounts for over 8% of the overall global installed capacity. Region-wise, the southern region comprises 35% of the total cement capacity, followed by the northern, eastern, western and central region comprising 20%, 18%, 14% and 13% of the capacity, respectively.
Installed capacity of domestic cement makers has increased at a CAGR of 4.9% during FY16-20. Manufacturers have been able to maintain a capacity utilisation rate above 65% in the past quinquennium. In the current financial year due to the prolonged rains in many parts of the country, the capacity utilisation rate has fallen from 70% during FY19 to 66% currently (YTD).
Source:moneycontrol.com
Process
Wonder Cement shows journey of cement with new campaign
Published
4 years agoon
October 21, 2021By
admin
The campaign also marks Wonder Cement being the first ever cement brand to enter the world of IGTV…
ETBrandEquity
Cement manufacturing company Wonder Cement, has announced the launch of a digital campaign ‘Har Raah Mein Wonder Hai’. The campaign has been designed specifically to run on platforms such as Instagram, Facebook and YouTube.
#HarRaahMeinWonderHai is a one-minute video, designed and conceptualised by its digital media partner Triature Digital Marketing and Technologies Pvt Ltd. The entire journey of the cement brand from leaving the factory, going through various weather conditions and witnessing the beauty of nature and wonders through the way until it reaches the destination i.e., to the consumer is very intriguing and the brand has tried to showcase the same with the film.
Sanjay Joshi, executive director, Wonder Cement, said, "Cement as a product poses a unique marketing challenge. Most consumers will build their homes once and therefore buy cement once in a lifetime. It is critical for a cement company to connect with their consumers emotionally. As a part of our communication strategy, it is our endeavor to reach out to a large audience of this country through digital. Wonder Cement always a pioneer in digital, with the launch of our IGTV campaign #HarRahMeinWonderHai, is the first brand in the cement category to venture into this space. Through this campaign, we have captured the emotional journey of a cement bag through its own perspective and depicted what it takes to lay the foundation of one’s dreams and turn them into reality."
The story begins with a family performing the bhoomi poojan of their new plot. It is the place where they are investing their life-long earnings; and planning to build a dream house for the family and children. The family believes in the tradition of having a ‘perfect shuruaat’ (perfect beginning) for their future dream house. The video later highlights the process of construction and in sequence it is emphasising the value of ‘Perfect Shuruaat’ through the eyes of a cement bag.
Tarun Singh Chauhan, management advisor and brand consultant, Wonder Cement, said, "Our objective with this campaign was to show that the cement produced at the Wonder Cement plant speaks for itself, its quality, trust and most of all perfection. The only way this was possible was to take the perspective of a cement bag and showing its journey of perfection from beginning till the end."
According to the company, the campaign also marks Wonder Cement being the first ever cement brand to enter the world of IGTV. No other brand in this category has created content specific to the platform.
Process
In spite of company’s optimism, demand weakness in cement is seen in the 4% y-o-y drop in sales volume. (Reuters)
Published
4 years agoon
October 21, 2021By
admin
Cost cuts and better realizations save? the ?day ?for ?UltraTech Cement, Updated: 27 Jan 2020, Vatsala Kamat from Live Mint
Lower cost of energy and logistics helped Ebitda per tonne rise by about 29% in Q3
Premiumization of acquired brands, synergistic?operations hold promise for future profit growth Topics
UltraTech Cement
India’s largest cement producer UltraTech Cement Ltd turned out a bittersweet show in the December quarter. A sharp drop in fuel costs and higher realizations helped drive profit growth. But the inherent demand weakness was evident in the sales volumes drop during the quarter.
Better realizations during the December quarter, in spite of the 4% year-on-year volume decline, minimized the pain. Net stand-alone revenue fell by 2.6% to ?9,981.8 crore.
But as pointed out earlier, lower costs on most fronts helped profitability. The chart alongside shows the sharp drop in energy costs led by lower petcoke prices, lower fuel consumption and higher use of green power. Logistics costs, too, fell due to lower railway freight charges and synergies from the acquired assets. These savings helped offset the increase in raw material costs.
The upshot: Q3 Ebitda (earnings before interest, tax, depreciation and amortization) of about ?990 per tonne was 29% higher from a year ago. The jump in profit on a per tonne basis was more or less along expected lines, given the increase in realizations. "Besides, the reduction in net debt by about ?2,000 crore is a key positive," said Binod Modi, analyst at Reliance Securities Ltd.
Graphic by Santosh Sharma/Mint
What also impressed analysts is the nimble-footed integration of the recently merged cement assets of Nathdwara and Century, which was a concern on the Street.
Kunal Shah, analyst (institutional equities) at Yes Securities (India) Ltd, said: "The company has proved its ability of asset integration. Century’s cement assets were ramped up to 79% capacity utilization in December, even as they operated Nathdwara generating an Ebitda of ?1,500 per tonne."
Looks like the demand weakness mirrored in weak sales during the quarter was masked by the deft integration and synergies derived from these acquired assets. This drove UltraTech’s stock up by 2.6% to ?4,643 after the Q3 results were declared on Friday.
Brand transition from Century to UltraTech, which is 55% complete, is likely to touch 80% by September 2020. A report by Jefferies India Pvt. Ltd highlights that the Ebitda per tonne for premium brands is about ?5-10 higher per bag than the average (A cement bag weighs 50kg). Of course, with competition increasing in the arena, it remains to be seen how brand premiumization in the cement industry will pan out. UltraTech Cement scores well among peers here.
However, there are road bumps ahead for the cement sector and for UltraTech. Falling gross domestic product growth, fiscal slippages and lower budgetary allocation to infrastructure sector are making industry houses jittery on growth. Although UltraTech’s management is confident that cement demand is looking up, sustainability and pricing power remains a worry for the near term.