Process
Smart Solution for Smart Buildings
Published
10 years agoon
By
admin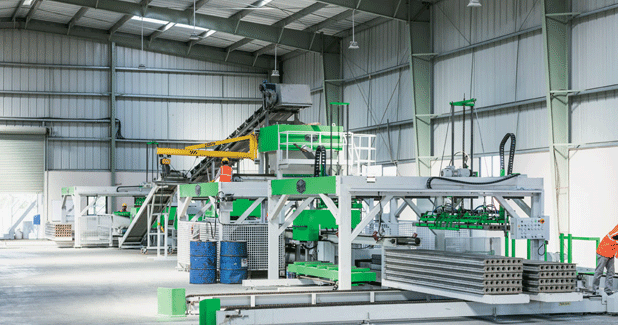
Fast, profitable and high-quality technology for light non-load bearing partition wall panels.
India?s housing shortage is offering huge opportunities for pre-cast technology suppliers as the country sets to modernise its construction sector. The government has set ambitious targets of 50 million affordable new homes by 2020; however, it is struggling to keep up with the speed of its building work, thanks to lack of proper technology and appropriate construction methods. To be able to achieve the targets, the country needs technology as well as pre-cast building construction know-how. ?The market for precast technology is growing fast in India. Our technology is being noticed more and we have the advantage of being early to market to make most of the growth, India is growing to become one of the most significant markets for our technology. The acceptance of pre-cast housing is already there, and our customers are realising the benefits of our technology,? says Chander Dutta, Managing Director, Elematic India. In the past few years, Elematic has put a significant effort in developing their capacity to serve the Indian precast customers. The company has established a sales and services unit in New Delhi as well as recently opened their own local manufacturing unit focusing on molds. Today the company can now offer whole precast production plants including well-priced, reliable batching and mixing plants.
Technology
Elematic, a leading manufacturer of precast concrete plants and production lines, has launched new technology level choices to their Acotec wall production lines. Acotec line is meant for manufacturing of light, non-load bearing, room-high precast partition wall panels. The new technology levels are called SEMI, PRO and EDGE, and they differ by the degree of automation and capacity as well as the required investment size. All the lines are quick and simple to install, run and maintain and require only very limited land area.
The new technology levels are launched in order to meet the varying customer needs. The SEMI line, with a production capacity of 80 sq m per hour, is the simplest of them all and is an excellent choice for anyone starting up in the business. It features a smart combined restacker handler and automation only for the key processes. The PRO line offers a higher capacity of 100 sq m per hour with automated functions for all main processes: sawing, trimming, stacking, restacking, cleaning & oiling, plate handling and pallet circulation. The fully-automatic Acotec EDGE offers a top-rate capacity of 120 sq m per hour and needs only two operators to run.
According to Dutta all the lines – Semi, Pro and Edge – feature new advanced production control system. Thanks to the system, a simple, modern user interface shows detailed data on every function in the whole process. Various reports on production rate, running hours and more are generated automatically. Modular structure of the lines and their integrated electricity with ETHERCAT bus system guarantee short installation and start up time of all lines, and the line can also be installed in existing production facilities. The production process is environmentally-friendly as it is silent and non-vibrating, and the raw material can be recycled so no waste is created. Low energy consumption of the line keeps the production costs on a low level as well.
For a semi automatic operation which is suitable for our country, minimum area to be constructed is 100,000 sq m. Normally, the working is about 10-12 hours in a day, according to Dutta.
BN Precast Group is one of the pioneers in the country using the Acotec technology in partition walls. For the production of the slabs, the company has chosen the original production technology from the Finnish pre-cast technology supplier Elematic and its Acotec line with a stationary extruder. ?For our customers, Acotec walls increase productivity massively, reduce costs and guarantee quality,? says Nishant S Patel, Director, BN Precast. The company?s clients are also getting a great deal of benefits from faster installation speed as construction with Acotec walls can be up to six times faster than with brickwork and twice as fast as block work.
Advantage Acotec
Speaking about the advantages of using Acotec Dutta avers, ?The Acotec wall panels are fast, easy and safe to install – building work proceeds up to six times faster when compared with traditional brickwork and even two times faster than block work. The panels have exact dimensions and completely even surface so no plastering is needed. In addition, their thin structure leaves more floor space for other purposes in a building. Despite the thinness, Acotec walls are strong and successfully used in seismic areas, too.
?The walls enable extremely fast installation of up to 40 sq ft per hour whereas traditional brickwork proceeds at a pace of 10 sq ft per hour before plastering is done. And we only need 5 workers to install these walls,? according to Patel. He further adds, ?The fact that only small amount of production space, only about 900 sq m, and low manpower is needed to use the Acotec line, create further benefits to the developers. The line is simple to install, run and maintain too – and its energy consumption is very low, only 55 kWh per hour. ?For us, the advantages are also obvious: high quantum production, low maintenance and high degree of quality control due to automation.?
Application areas
Acotec provides wide range of application for non-structural partition wall system in an environmentally friendly way, making it a truly a solution for the future. They suit for a wide variety of purposes such as bath rooms, kitchens and showers, thanks to the moisture resistance of the material. Acotec walls also offer excellent sound insulation, meaning that apartment buildings, schools and hotels benefit from these type of partition walls.
Challenges
Speaking about the challenges Dutta had this to say. Very few player in prefab have structural design capabilities to support the requirements of clients, there are very few good examples to showcase. There is apprehension in adopting new technologies. There is a misconception that precast is confined to only low cost housing. Any building can be made using precast concrete technology. Our customers in India are making luxury houses, villas, super specialty hospitals, stadiums etc using this technology. Beautiful architectural finishes, results can be achieved by using coloured or graphic concrete and giving form liner finishes.
According to Dutta, despite there is no specific data available as per our estimation is in India there is currently at least 5 million sq ft under construction with precast concrete technology. Dutta sums up on a high note. He says, ?A lot of projects are in the pipeline and this number can easily go up 50-100 million sq ft in the next 4-5 years.?
Some of the latest precast projects
- Tata Peenya, 4 million Sq. ft residential buildings, Bangalore
- Provident Sunworth, 5,900 apartments, Bangalore
- Amrapali Developers, 35 million sq ft Greater Noida
- BG Shirke, 27,000 apartments, Narela, New Delhi
- Supertech, 5 million sq ft, Noida
- Sobha Developers, 8 million sq ft, Bangalore
- BCC Developers, 2 million sq ft/annum
?In India we have produced more than 30,000 elements in the local units.?
– Chander Dutta, Managing Director, Elematic India
Elematic Oyj is the leading supplier of precast, prefab concrete technology worldwide. It has operations in over 100 countries. They are into supply of machinery, from supply of a single production line and to a complete precast plant. In a freewheeling with ICR, Chander Dutta, Managing Director, Elematic, sheds light on the technology and advantages. Excerpts from the interview…
Brief us about your company.
As a company, we are Finland-based and hold around 50-60 percent market share of precast business in the country. Worldwide we have 60 per cent market share in hollow core slab business and 40 per cent in plant and machinery. We provide machinery and technical solutions for making all types of precast elements required in any building construction. Climatic conditions in Finland are adverse. They have severe cold for about six months and in remaining period there is reasonable climate. Outside work can be carried out only during six months and remaining months are devoted for inside work. We started in the year 1950, when Finland was going through the same problems like that of ours. There was pressure of urbanisation that compelled the company to undertake technological developments. The government also supported the private players to develop the technology further. Even today 80-90 per cent of construction in Scandinavian countries is prefab.
In India we had few companies like Hindustan Prefab who have not been very successful in precast. What can be the reasons?
I am aware of the case of Hindustan Prefab. The technology was sourced from Russia. However Russia has failed mainly because they did not develop further with time, specifically the joints done in the precast, prefab jobs and the earth quake resistant designs. That may the reason for luke worm response to both these companies in popularising the concept of precast and prefab.
How are you able to provide better quality of constructions?
We have in house design team to support our manufacturing activity. Considering the bottlenecks faced by the clients, we have to guide them and suggest suitable product design. For the last five years we are promoting this technology and while doing so we realised that we must have a design team to support our initiative. For the success of prefab major requirement is planning, planning and only planning. Planning is extremely important part of prefab.
Can you give us more details on concrete being used?
We use M35 or M40 for walls, M 50 slabs. Concrete mix design is specialised job. The mix should perform well. No hair line cracks or micro cracks are acceptable. It has to be cured properly. In a factory environment, a workman produces one elements 10 times in a day. Because of repetition, he does a perfect job. Precast buildings have less maintenance; and life cycle cost is low; structures are more durable and more sustainable.
What is your take on the general perception that precast structures are monotonous?
To me whole of Mumbai looks like high rise slums. Many of the buildings there face a problem of poor quality of plaster. Buildings are very fancy from outside but inside, the scene is very bad. The buildings made with precast elements can be made earth quake resistant and yet more beautiful. One can use precast facade or coloured concrete. We must understand that because of repetition of elements, the cost in precast buildings comes down. In precast buildings you can have a balance of beauty and quality.
Name some of your projects under construction
BG Shirke is constructing a 14-storyed building for 20,000 homes in Delhi. With Amrapali group we are constructing 30-storyed building, and we are also working with Jindal University at Sonepat to construct a hostel for 200 students.
You may like
Process
Price hikes, drop in input costs help cement industry to post positive margins: Care Ratings
Published
4 years agoon
October 21, 2021By
admin
Region-wise,the southern region comprises 35% of the total cement capacity, followed by thenorthern, eastern, western and central region comprising 20%, 18%, 14% and 13%of the capacity, respectively.
The cement industry is expected to post positive margins on decent price hikes over the months, falling raw material prices and marked drop in overall production costs, said an analysis of Care Ratings.
Wholesale and retail prices of cement have increased 11.9% and 12.4%, respectively, in the current financial year. As whole prices have remained elevated in most of the markets in the months of FY20, against the corresponding period of the previous year.
Similarly, electricity and fuel cost have declined 11.9% during 9M FY20 due to drop in crude oil prices. Logistics costs, the biggest cost for cement industry, has also dropped 7.7% (selling and distribution) as the Railways extended the benefit of exemption from busy season surcharge. Moreover, the cost of raw materials, too, declined 5.1% given the price of limestone had fallen 11.3% in the same aforementioned period, the analysis said.
According to Care Ratings, though the overall sales revenue has increased only 1.3%, against 16% growth in the year-ago period, the overall expenditure has declined 3.2% which has benefited the industry largely given the moderation in sales.
Even though FY20 has been subdued in terms of production and demand, the fall in cost of production has still supported the cement industry by clocking in positive margins, the rating agency said.
Cement demand is closely linked to the overall economic growth, particularly the housing and infrastructure sector. The cement sector will be seeing a sharp growth in volumes mainly due to increasing demand from affordable housing and other government infrastructure projects like roads, metros, airports, irrigation.
The government’s newly introduced National Infrastructure Pipeline (NIP), with its target of becoming a $5-trillion economy by 2025, is a detailed road map focused on economic revival through infrastructure development.
The NIP covers a gamut of sectors; rural and urban infrastructure and entails investments of Rs.102 lakh crore to be undertaken by the central government, state governments and the private sector. Of the total projects of the NIP, 42% are under implementation while 19% are under development, 31% are at the conceptual stage and 8% are yet to be classified.
The sectors that will be of focus will be roads, railways, power (renewable and conventional), irrigation and urban infrastructure. These sectors together account for 79% of the proposed investments in six years to 2025. Given the government’s thrust on infrastructure creation, it is likely to benefit the cement industry going forward.
Similarly, the Pradhan Mantri Awaas Yojana, aimed at providing affordable housing, will be a strong driver to lift cement demand. Prices have started correcting Q4 FY20 onwards due to revival in demand of the commodity, the agency said in its analysis.
Industry’s sales revenue has grown at a CAGR of 7.3% during FY15-19 but has grown only 1.3% in the current financial year. Tepid demand throughout the country in the first half of the year has led to the contraction of sales revenue. Fall in the total expenditure of cement firms had aided in improving the operating profit and net profit margins of the industry (OPM was 15.2 during 9M FY19 and NPM was 3.1 during 9M FY19). Interest coverage ratio, too, has improved on an overall basis (ICR was 3.3 during 9M FY19).
According to Cement Manufacturers Association, India accounts for over 8% of the overall global installed capacity. Region-wise, the southern region comprises 35% of the total cement capacity, followed by the northern, eastern, western and central region comprising 20%, 18%, 14% and 13% of the capacity, respectively.
Installed capacity of domestic cement makers has increased at a CAGR of 4.9% during FY16-20. Manufacturers have been able to maintain a capacity utilisation rate above 65% in the past quinquennium. In the current financial year due to the prolonged rains in many parts of the country, the capacity utilisation rate has fallen from 70% during FY19 to 66% currently (YTD).
Source:moneycontrol.com
Process
Wonder Cement shows journey of cement with new campaign
Published
4 years agoon
October 21, 2021By
admin
The campaign also marks Wonder Cement being the first ever cement brand to enter the world of IGTV…
ETBrandEquity
Cement manufacturing company Wonder Cement, has announced the launch of a digital campaign ‘Har Raah Mein Wonder Hai’. The campaign has been designed specifically to run on platforms such as Instagram, Facebook and YouTube.
#HarRaahMeinWonderHai is a one-minute video, designed and conceptualised by its digital media partner Triature Digital Marketing and Technologies Pvt Ltd. The entire journey of the cement brand from leaving the factory, going through various weather conditions and witnessing the beauty of nature and wonders through the way until it reaches the destination i.e., to the consumer is very intriguing and the brand has tried to showcase the same with the film.
Sanjay Joshi, executive director, Wonder Cement, said, "Cement as a product poses a unique marketing challenge. Most consumers will build their homes once and therefore buy cement once in a lifetime. It is critical for a cement company to connect with their consumers emotionally. As a part of our communication strategy, it is our endeavor to reach out to a large audience of this country through digital. Wonder Cement always a pioneer in digital, with the launch of our IGTV campaign #HarRahMeinWonderHai, is the first brand in the cement category to venture into this space. Through this campaign, we have captured the emotional journey of a cement bag through its own perspective and depicted what it takes to lay the foundation of one’s dreams and turn them into reality."
The story begins with a family performing the bhoomi poojan of their new plot. It is the place where they are investing their life-long earnings; and planning to build a dream house for the family and children. The family believes in the tradition of having a ‘perfect shuruaat’ (perfect beginning) for their future dream house. The video later highlights the process of construction and in sequence it is emphasising the value of ‘Perfect Shuruaat’ through the eyes of a cement bag.
Tarun Singh Chauhan, management advisor and brand consultant, Wonder Cement, said, "Our objective with this campaign was to show that the cement produced at the Wonder Cement plant speaks for itself, its quality, trust and most of all perfection. The only way this was possible was to take the perspective of a cement bag and showing its journey of perfection from beginning till the end."
According to the company, the campaign also marks Wonder Cement being the first ever cement brand to enter the world of IGTV. No other brand in this category has created content specific to the platform.
Process
In spite of company’s optimism, demand weakness in cement is seen in the 4% y-o-y drop in sales volume. (Reuters)
Published
4 years agoon
October 21, 2021By
admin
Cost cuts and better realizations save? the ?day ?for ?UltraTech Cement, Updated: 27 Jan 2020, Vatsala Kamat from Live Mint
Lower cost of energy and logistics helped Ebitda per tonne rise by about 29% in Q3
Premiumization of acquired brands, synergistic?operations hold promise for future profit growth Topics
UltraTech Cement
India’s largest cement producer UltraTech Cement Ltd turned out a bittersweet show in the December quarter. A sharp drop in fuel costs and higher realizations helped drive profit growth. But the inherent demand weakness was evident in the sales volumes drop during the quarter.
Better realizations during the December quarter, in spite of the 4% year-on-year volume decline, minimized the pain. Net stand-alone revenue fell by 2.6% to ?9,981.8 crore.
But as pointed out earlier, lower costs on most fronts helped profitability. The chart alongside shows the sharp drop in energy costs led by lower petcoke prices, lower fuel consumption and higher use of green power. Logistics costs, too, fell due to lower railway freight charges and synergies from the acquired assets. These savings helped offset the increase in raw material costs.
The upshot: Q3 Ebitda (earnings before interest, tax, depreciation and amortization) of about ?990 per tonne was 29% higher from a year ago. The jump in profit on a per tonne basis was more or less along expected lines, given the increase in realizations. "Besides, the reduction in net debt by about ?2,000 crore is a key positive," said Binod Modi, analyst at Reliance Securities Ltd.
Graphic by Santosh Sharma/Mint
What also impressed analysts is the nimble-footed integration of the recently merged cement assets of Nathdwara and Century, which was a concern on the Street.
Kunal Shah, analyst (institutional equities) at Yes Securities (India) Ltd, said: "The company has proved its ability of asset integration. Century’s cement assets were ramped up to 79% capacity utilization in December, even as they operated Nathdwara generating an Ebitda of ?1,500 per tonne."
Looks like the demand weakness mirrored in weak sales during the quarter was masked by the deft integration and synergies derived from these acquired assets. This drove UltraTech’s stock up by 2.6% to ?4,643 after the Q3 results were declared on Friday.
Brand transition from Century to UltraTech, which is 55% complete, is likely to touch 80% by September 2020. A report by Jefferies India Pvt. Ltd highlights that the Ebitda per tonne for premium brands is about ?5-10 higher per bag than the average (A cement bag weighs 50kg). Of course, with competition increasing in the arena, it remains to be seen how brand premiumization in the cement industry will pan out. UltraTech Cement scores well among peers here.
However, there are road bumps ahead for the cement sector and for UltraTech. Falling gross domestic product growth, fiscal slippages and lower budgetary allocation to infrastructure sector are making industry houses jittery on growth. Although UltraTech’s management is confident that cement demand is looking up, sustainability and pricing power remains a worry for the near term.

Star Cement launches ‘Star Smart Building Solutions’

Nuvoco Vistas reports record quarterly EBITDA

UltraTech Cement increases capacity by 1.4Mt/yr

Shree Cement reports 2025 financial year results

Rekha Onteddu to become director at Sagar Cements

Star Cement launches ‘Star Smart Building Solutions’

Nuvoco Vistas reports record quarterly EBITDA

UltraTech Cement increases capacity by 1.4Mt/yr

Shree Cement reports 2025 financial year results
