Concrete
Where concrete roads can take us
Published
11 years agoon
By
admin
India has the second largest network of roads in the world. The 4,689,842 km network of roads in India, second only to and USA (6,586,610 km), is long enough to go around the Earth 117 times! The Earth has a circumference of 40,075 km, and perhaps that should give readers a perspective of the size of this mammoth network. Building and maintaining this crucial infrastructure is a huge task for the government. And the choice between concrete and bitumen for road pavements will be one of the most critical decisions that the government has to take.
The recently published white-paper on road infrastructure in India by the Ministry of Road Transport and Highways clearly underlines the huge challenge faced by the country. Of the total road tracks in the country, 1277791 km of roads in India (roughly 30 per cent) are yet to be surfaced. India has more than fifty-three National highways, but the total length constitutes only 1.5 per cent of the total road network in India. The short stretch carries nearly 40 per cent of the total road traffic, most of which is of heavy vehicles. The country has abysmal length of expressways. If India has to keep up with the growing traffic, the government will have to construct around 15,000 km of expressways in the next ten years. 25 per cent of villages in India still have poor road links. India also has the lowest kilometre lane road density per 100,000 people among G-27 countries leading to traffic congestion. The government has to give priority to upgrading road infrastructure if it envisages any sort of economic growth. There is a long way to go ahead.
No significant steps were taken in building this critical infrastructure during the last three decades. The rate of new highway construction across India accelerated after 1999, but had slowed later to the extent of total neglect in past few years. Policy delays and regulatory blocks reduced the rate of highway construction awards to just 500 kilometres of new road projects in 2013. The new government at the Centre realises the importance of good road network and has chalked out an ambitious plan to relay the road to development. After all, the national network carries over 65 per cent of freight and about 85 per cent of passenger traffic. Indian transportation sector contributes 4.7 per cent towards India?s gross domestic product.
In a country that is so immensely rich in its mineral resources, connecting the resources to the industry, and the industry to the end consumer is extremely necessary for the economic development of the nation. According to 2009 estimates by Goldman Sachs, a leading global investment banking, securities and investment management firm, India will need to invest US$1.7 trillion on infrastructure projects before 2020 to meet its economic needs. A major part of this investment should be in upgrading India?s road network.
The last three decades have seen the country slipping into a service-based economy while the manufacturing sector took the backseat. Now with the government focusing on reviving the manufacturing sector, road building and infrastructural support automatically becomes its top priority, since the infrastructure has to be in place before the manufacturing and distribution of the produce can be kick started. Apart from building more roads the government will have to start with the upgradation of the existing network. Only 2 per cent of the existing network is surfaced with concrete. Now that the government is looking at ways to better the existing infrastructure, it is of crucial importance that it moves in the right direction to tackle the challenge. While the most popular approach would be to lay bitumen on mud, it would be a much more sensible decision if the government opts for concrete pavements. The benefits of concrete road over bitumen road are well established and well known (also elaborated in Part I and Part II of this story published respectively in the July 2014 and August 2014 issues of ICR).
India was one of the earliest countries in the world to start building concrete roads. The first concrete road in India was built in Madras (Chennai) in 1914, which remained pot-hole free for a very long time despite the heavy rains in the region. The results encouraged engineers at that time to construct the Dehradun-Mussoorie Highway that had perennial problems of roads getting damaged due to extreme weather conditions. Soon the trend picked up and more and more concrete roads were laid in India. The original Delhi-Agra (NH2), Bombay-Poona (NH4) and Bangalore-Mysore roads were all built of concrete. Then in 1939, about 120 km of the Bombay-Poona road (present NH-4) and 110 km of the Bombay-Nashik road (present NH-3) were concreted. In the same year, Mumbai?s Marine Drive was constructed out of cement concrete. Marine Drive is still giving excellent service, even in its sixtieth year. The road has stood the test of time and the onslaught of saline sea water and humid climate. It is a perfect example of the value offered by concrete roads over bitumen. The Cement Manufacturers Association has communicated several benefits to the governmental bodies on plenty of occasions. If nothing, the potholes on the bitumen road alone are sufficient to convince the case of concrete over bitumen.
India?s annual expenditure on the road sector is around Rs 20,000-30,000 crore, 70 per cent of funds of which are spent on just maintaining the existing roads. This is a sheer wastage of the tax payers? money when better and well established technologies for building concrete roads are readily available. The country has both the raw material and the necessary expertise to build such roads ready at hand. Why should then tar roads be built by importing costly bitumen?
Those in favour of bitumen road often point to the initial cost of laying concrete roads, which is apparently 15 per cent higher than that of bitumen road. But with the rising cost of crude oil in the market, the gap is fast getting narrow and the difference now is negligible. The life cost advantage of concrete road far exceeds the initial cost difference between the two types. When it comes to cost comparison, the directive issued by Bureau of Indian Standards states that whenever an asset has to be created or built, and competing technologies/methods/materials for building the assets are available, the technology/method/material which gives the lowest life-cycle cost will be selected. Initial cost will not be the guiding factor. And in life-cycle cost, concrete roads with their low maintenance requirements, invariably turn out to be cheaper than bituminous ones. Today with fibre and steel fillers reinforced concrete available, the life cycle cost of the concrete roads may extend way beyond 60 – 70 years. Fly ash can substitute 30 per cent of cement in the concrete mix and can bring down the material cost dramatically. Cost is no longer an issue with concrete roads. On the other hand the maintenance of tar roads is expensive because they need to be resurfaced once every three years.
Having better roads built using indigenous raw material has its own benefits, but the merits go far below the surface performance of the pavement. One rough estimate is that even if only 50 per cent of the highways in India were to be resurfaced with concrete, it would engage the unused capacities of cement plants at least for the next decade. That will give a big boost to the sluggish cement sector which is currently struggling to raise a rupee in its cost per Kg just to stay afloat. In-fact the government may very well negotiate a mutually agreeable price with the cement companies and start rolling out cement-concrete highways. A long-term deal can help reduce the cost per of a bag of cement, which costs upwards of Rs 270 – Rs 300 a bag , by Rs 100 a bag, which is a discount of over 33 – 37 per cent.
With the assured business in hand, the industry can invest in plant upgradation, capacity building and employment generation. The industry today has 40 per cent of its installed capacity lying idle. The demand of cement and concrete will allow optimum utilisaton of the installed capacities. Imagine the domino effect of concrete road building activity on employment generation. Generally, every one- million-tonnes per annum (1 MTPA) of cement production requires around 400 skilled technical workers. The additional 40 per cent capacity utilisation will create employment for around 6000 skilled technicians in cement industry alone. It is estimated that the cement industry will require a total of 43,000 skilled technical workers for about 108 million tonnes of greenfield expansion, 17,000 for about 42 million tonnes of brownfield expansion and 6, 000 for 3000 MW captive power plant operation in this sector.
Consequent project upgradation will lead to employment of additional hands by the equipment manufacturing plants, component manufacturing units, concrete manufacturer and suppliers, logistics service providers, etc. Additionally the increased logistical needs of transporting raw material and the cement and concrete will boost employment for truck drivers. And finally the activity will perhaps create largest employment opportunity for the daily wage workers engaged in the concrete road building activity.
These new roads will open investment opportunities for new real estate projects, smart cities and industrial corridors along the new roadways and would infuse the growth cycle with new energy.
Road building is a longterm investment and a lot depends on the performance of these roads. It is imperative that as we commit to better infrastructure we do so in a well informed manner, that we derive value for hard earned tax payers? money. Yes we can look at our neighbours, USA, China, Russia and can take cues from them. Cement and concrete today is omnipresent and their is no reason to move in traditional fashion of building tar roads, tolerating potholes and then laying them with concrete on top.
The technology of laying bitumen road is fairly simple, at least for the way in which these roads are laid in India. And for precisely this reason, this sector is filled with unorganised and often unprofessional contractors who grab projects based on factors other than their technological merits. Laying concrete roads on the other hand requires significant technical expertise and creates a barrier for unprofessionals to enter. Shifting to concrete roads will offer a clean slate to begin with, where the babu-contractor nexus will come to an end, and where the government too will be able to present a corruption free road building authority to the public.
Looking over the merits of concrete over bitumen as a construction material and as a technology, which was discussed in the last two issues of ICR and also considering the social implications of the shift to concrete, it is clear that concrete roads will take us toward economic growth.
Why Concrete?
Durability and maintenance free life
Concrete roads have a rated service life of twenty five to thirty years (more in reality), whereas asphalt roads theo- cratically last for ten years at the most.
Frequent repair and associated costs
Concrete road do not require frequent repair or patching work like asphalt roads.
Vehicles consume less fuel
Vehicles on concrete roads, consumes 15-20% less fuel than that on asphalt roads since, a concrete road does not get deflected under the wheels of loaded trucks.
Inert nature
Concrete roads do not get damaged by the leaking oils from the vehicles or by the extreme weather conditions like excess rain or extreme heat.
Greener construction process
Bitumen produces lots of highly polluting gases at the time of melting it for paving. Also, less fuel consumption by the vehicle running on a concrete road means less pollution.
Conserves natural resources
Bitumen is produced from imported petroleum, a non renewable resource. On the other hand, concrete (cement) is produced from abundantly available limestone. Precious foreign exchange is saved if we opt for concrete pavements.
Durability
Heavy rain and other extreme weather conditions damage the asphalt road, and the roads need to be repaired frequently.
Light reflectivity
Concrete reflects light better than the black coloured bitumen road. As a result the requirement for road lighting is reduced by half saving electrical energy and giving better visibility at night.
You may like
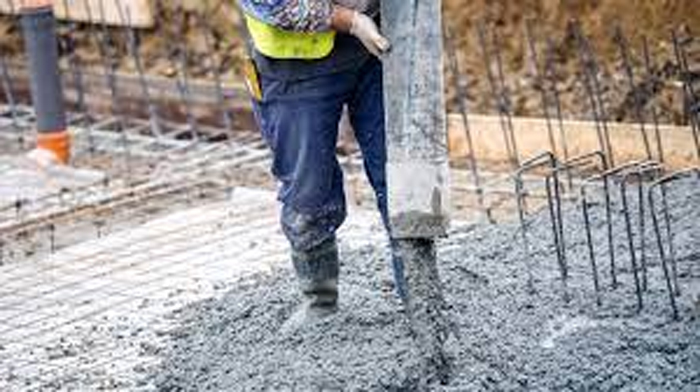
Tamil Nadu is set to host one of India’s five national carbon capture and utilisation (CCU) testbeds, aimed at reducing CO2 emissions in the cement industry as part of the country’s 2070 net-zero goal, as per a news report. The facility will be based at UltraTech Cement’s Reddipalayam plant in Ariyalur, supported by IIT Madras and BITS Pilani. Backed by the Department of Science and Technology (DST), the project will pilot an oxygen-enriched kiln capable of capturing up to two tonnes of CO2 per day for conversion into concrete products. Additional testbeds are planned in Rajasthan, Odisha, and Andhra Pradesh, involving companies like JK Cement and Dalmia Cement. Union Minister Jitendra Singh confirmed that funding approvals are underway, with full implementation expected in 2025.
Image source:https://www.heavyequipmentguide.ca/
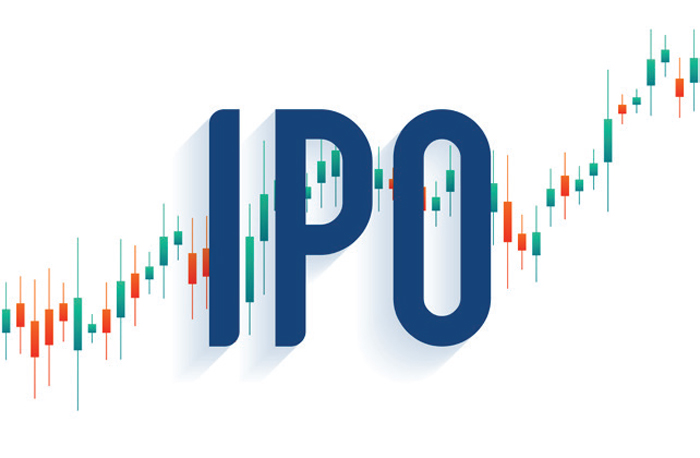
JSW Cement has set the price range for its upcoming initial public offering(IPO) at US$1.58 to US$1.67 per share, aiming to raise approximately US$409 million. As reported in the news, around US$91 million from the proceeds will be directed towards partially financing a new integrated cement plant in Nagaur, Rajasthan. Additionally, the company plans to utilise US$59.2 million to repay or prepay existing debts. The remaining capital will be allocated for general corporate purposes.
Concrete
Cement industry to gain from new infrastructure spending
Published
1 month agoon
July 24, 2025By
admin
As per a news report, Karan Adani, ACC Chair, has said that he expects the cement industry to benefit from the an anticipated US$2.2tn in new public infrastructure spending between 2025 and 2030. In a statement he said that ACC has crossed the 100Mt/yr cement capacity milestone in April 2025, propelling the company to get closer to its ambitious 140Mt/yr target by the 2028 financial year. The company’s capacity corresponds to 15 per cent of an all-India installed capacity of 686Mt/yr.
Image source:https://cementplantsupplier.com/cement-manufacturing/emerging-trends-in-cement-manufacturing-technology/