Environment
Shree Cement: An environment conscious, value driven organization
Published
14 years agoon
By
admin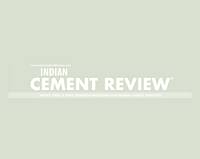
Shree Cement was the first Indian and the third Asian cement company to join the Cement Sustainability Initiative (CSI) of the World Business Council for Sustainable Development, Switzerland. With the achievement of this honor, the company has joined the league of the seven nations comprising the Asia Pacific Partnership on Clean Development & Climate Change with member countries like USA, Australia, China, Korea, Japan, Canada and India.Shree Cement is the largest cement manufacturer in Northern India and is ranked among the top five cement manufacturing groups in the country. The company has always believed in measuring its performance against the benchmarks of economical, social and environmental benefits. The company has received various awards and recognition at the national and international level for excellence in energy efficiency, environment management and sustainability. The company has also encouraged correct HR initiative which employ right systems and processes for appropriate manpower planning, recruitment, orientation, training & development and employee benefits. These initiatives have created a workforce that is happy and driven to continually improve upon their standard of performance.Plant LocationThe company operates cement plants at Beawar, Ras, Khushkhera, Jobner and Suratgarh in Rajasthan and Laksar (Roorkee) in Uttarakhand. In the last 5 years, the company has more than trebled its cement capacity to achieve the present capacity rate of 13.5 million tons per annum.The company has a power generation capacity of 260 MW with plants located at Beawar and Ras in Rajasthan, including waste heat recovery power plants of 46 MW capacity, which is the largest such capacity in the global cement industry excluding China. The company is further expanding its power capacity by setting up a 300 MW (2 x 150MW) power plant at Beawar. This will be taking the company’s overall power generation capacity to 560 MW.The company achieved a world record by setting up a 1 million ton clinkerisation unit at Bangur city, Ras, Rajasthan in 330 days as compared to an industry average of 630 days during 2010-2011. In building this facility, the company broke its own world record of 367 days made earlier in 2009. A clinker grinding unit of 1.5 mtpa was also commissioned by the company at Jobner near Jaipur. The company is also in plans to set up cement plants in Chhatisgarh with split grinding units to be set up in other parts of eastern India. Pre-project activities have also been initiated for a cement plant in Karnataka.BrandsIn a highly competitive industry which is evolving continuously with changes in branding and marketing strategies of different companies, the company has always believed in building brands which are aligned to the customer’s needs. The company has been able to realize a larger sales quantum, better realizations and increased competitiveness through extensive brand promotions and opening of new strategic markets.Shree UltraThe company’s flagship brand is Shree Ultra which contributes to more than half of its sales volumes. This brand is a perfect example of the company’s strategic shift from commodity to brand marketing. The two variants of Shree Ultra, Shree Ultra OPC and Shree Ultra Jung Rodhak Cement have been distinctly positioned, keeping in view the market demand. A high acceptance level has been observed for Shree Ultra Jung Rodhak Cement among brand influencers such as masons due to its unique rust prevention properties. The value of the brand can be gauged from the fact that alongwith a high demand level in highly educated markets like Delhi, it has enhanced its presence in the interior markets of Madhya Pradesh, Uttarakhand, Uttar Pradesh and Punjab.Bangur CementBangur Cement has been positioned as a premium brand in the market. It has been conceived to cater to the high end market segment. The unique tagline of the brand "Sasta Nahin, Sabse Achcha" has given it the status of ‘top of the market’ value brand.Rockstrong CementRockstrong Cement is the latest addition to the product portfolio of Shree Cement. The brand has recorded the highest YoY growth amongst the three brands of Shree in 2009-10. The unique position of this brand has been attributed to its promise of high performance and the ability to withstand exceptionally harsh environment conditions. Promotions for the brand are undertaken through a series of witty hoardings designed on current topics.AwardsAs a company which has always kept customer focus and compliance with environmental objectives at the forefront of its business strategies, Shree Cement has been honoured with several awards, reaffirming its commitment to a healthy and competitive business agenda. It has been awarded the CII-ITC sustainability award for nurturing innovation, promoting excellence, building trust and contribution towards sustainable future for all. The company has also won the ICC Sustainability Vision Award 2010 – 11 by Indian Chamber of Commerce for "CSR contributing inclusive growth". It has been awarded the Golden Peacock Award by the Institute of Directors for Climate Security. The company has also won the FE-EVI Green Business Leadership Award by Financial Express & Emergent Ventures India for Green Business Practices.It has also been awarded the National Award for Excellence in Energy Management – 2010 by Confederation of Indian Industry (CII). The company has won the National Award in Excellence in Cost Management-2009 by the Institute of Cost & Works Accountants of India (ICWAI). It has also been awarded the Greentech HR Excellence Silver Award in best Strategy – 2010 as well as the Best Employer Award by the Employers Association of Rajasthan.Corporate Social ResponsibilityAs part of its corporate social responsibility, the company has undertaken several measures with a view to empower the environment and making community life sustainable. It has undertaken grass root development in two districts of Ajmer and Pali, covering 20 villages. The company has formed the "Shree Rural Foundation Society" with a view to formalizing community engagement and developmental initiatives. A lot of prevailing issues in the society can be solved and answered through the effective spread of formal education, Understanding the importance of education, the company is providing assistance to a senior secondary school located within its premises. It has also been making contributions for meeting infrastructural requirements which help children gain better access to education. Shree Cement has also undertaken various literacy projects for non-school going girls, education development schemes for students wanting to pursue ITI and computer education for rural youth.The company also organizes various health camps like polio vaccination and eye camps. Mobile dispensaries are dispatched by the company in nearby villages for weekly health check up camps. Various awareness programs are also undertaken for their trucker’s community for combating diseases like HIV/AIDS. Recognizing the importance of family as an important and valuable unit of society, family welfare programs are also undertaken by the company. One such program is the MAMTA project which has been able to reach out and provide benefits to pregnant women as well as infants upto 1 year of age. Vaccination programs for protecting children against diseases like Hepatits – B and Typhoid have been organized. Awareness drives against use of tobacco, liquor have also been carried out. In order to spread the benefits to as many community members as possible, we also provide assistance to the government in their health programs by way of donations, mobility support and material supportEnvironmental complianceShree Cement has always believed in the amalgamation of business practices and compliance with environmental obligations. The company’s thoughts, planning and implementation contains at its core, environmental improvement and people betterment to ensure a sustainable growth. The company’s commitment towards ensuring protection and nurturing of the environment is reflected through some of its initiatives like setting up of Green Power Plants, manufacturing of synthetic gypsum and use of Air Cooled Condensers (ACCs).A deep concern has been expressed by the company towards the ecosystem and it is aware of the dependency of the surrounding communities on it. It has introduced various measures in our processes to ensure reduced emissions for the preservation of the environment. While the company’s clinker production has increased, it has brought down the SPM (Kg/ton of clinker) through its conservation measures like improving the efficiency of ESP and Dust Collectors.Reduced Dust LoadThe company is deeply concerned about our ecosystem and are aware of the dependency of our surrounding communities on it. It has introduced various measures in our processes to ensure reduced emissions for the preservation of the environment. While its clinker production has increased, it has brought down the SPM (Kg/ton of clinker) through conservation measures like improving the efficiency of ESP and Dust Collectors.Fly Ash Consumption and CO2 ReductionFly Ash is a waste-product of thermal power plants which is discarded as landfills. Shree Cement has increased the utilization of this waste-product in the process of cement manufacturing which has led to a decrease in the consumption of clinker. This in turn has helped in the conservation of limestone. As a result, the company has achieved CO reduction of 18.33 lakh ton in 09-10 and 14.09 lakh ton in 08-09.Reduction of CO Emission in Heavy Earth Moving Machines (H.E.M.M.)The company monitors the CO emission in all H.E.M.M. on regular intervals with Fuel Gas Analyzer. By analyzing the data, the company took corrective measures i.e. ensuring proper burning of the fuel (tappet setting), proper fuel injection (injector calibration) and thereby maintained the CO level within limits. Even with increased load on these machines, these steps have enabled the company to reduce the fuel consumption, increase the engine life and contribute towards the eco-system.Green for GoodThe company is committed to protect the environment and has taken measures to address global challenges such as climate change. It green power projects and increased use of fly ash in cement production is a step in this direction. Besides, the company’s dedicated focus towards the ‘green cause’ saw an increase in the number of trees planted. The overall greenery level of the plant area was 34% on 2009. Solar lights and heaters in have been installed by the company in its premises and LED based lights in its plants. Commenting on the company’s energy conservation efforts, it was stated by the World Economic Forum, "faced with limited access to low-cost energy, Shree Cement developed the world’s most energy-efficient process for making its products. The company has become the global benchmark: leading cement companies from around the world visit Shree to learn from its innovations."The company celebrates World Environment Day on 5th June to create awareness about environment safety. The company organizes workshops and distributes booklets emphasizing on environment protection.Prudent Water ManagementThe company is committed to conservation, recycling and recharging. One of the major steps towards conservation of water has been the replacement of the Conventional Water Cooling System with Air Cooled Condensing System. Another initiative in this direction was installation of Waste Heat Recovery Boilers (WHRB). In the absence of WHRBs, the waste hot gases had to be conditioned by spraying of water to bring it down to ambient temperature before releasing the gases. The installation of WHRBs has eliminated the need for conditioning of gases thereby resulting in considerable water savings. A new sewage treatment plant has been installed for the treatment and reuse of domestic waste water generated from our housing colony. This water is reused for purposes like irrigation, quenching and water spray. The company is also engaged in constructing various rain water harvesting structures like check dams, open and injection wells etc. It has adopted unique approaches like utilizing sites of abandoned mines to harvest rain water and Roof Rain Water Harvesting System. For the State at large, the company also provides assistance to the government for rejuvenation of local water bodies.New Sustainability ChampionThe sustainability paradigm has been accepted whole heartedly by Shree Cement. The company has always pursued a holistic program with an emphasis on three bottomlines of corporate performance-economic, social and environmental. Economic performance brings out the Company’s contribution to production and profit; social performance highlights its contribution to community; environmental performance brings out the contribution to conserving the environment.The World Economic Forum and the Boston Consulting Group (BCG) chalked out a program for seeking out unconventional, practical solutions to the current challenges of growth, aiming to identify and support key business practices, and to relay them to the global community. This project deliberately did not look to governments, environmental organizations or multinational corporations from advanced economies. Instead, it went to agents who deal with a wide range of constraints in their daily business: rapidly growing companies originating and operating in the emerging markets, where economic prosperity and populations are growing fastest, and where environmental constraints and stresses are often highest.Towards the end of a rigorous research process, the project identified and assessed 16 emerging market-based companies that share a unique mindset and set of best practices: these are the New Sustainability Champions. Based in countries such as Brazil, Costa Rica, Egypt and Kenya, these companies provide inspiring examples for any corporation around the world interested in tackling the challenges of performance, innovation, growth and sustainability.Shree Cement was the first Indian and the third Asian cement company to join the Cement Sustainability Initiative (CSI) of the World Business Council for Sustainable Development, Switzerland. With the achievement of this honor, the company has joined the league of the seven nations comprising the Asia Pacific Partnership on Clean Development & Climate Change with member countries like USA, Australia, China, Korea, Japan, Canada and India.Prashant Bangur, Joint executive President, Shree Cement, elucidates his views on sustainability practices, "We believe that sustainability is continual process and it is not something which was founded by nature. So we ensure sustainability in our day to day operations and adopted it as a habit. Sustainability should be understood as a multi dimensional approach wherein the focus should just not be upon profit, but the business should be integrated with energy conservation, natural resource conservation, healthy stake-holders dialogue, employee satisfaction, community at large and transparency.Through sheer dedication, innovation and creativity we have achieved a safe platform where we can hold a comfortable stand comparatively, yet there is long way to go. We have grown at a pace faster than the industry average with various thoughts and ideas. All our thoughts and ideas are not essentially contributing to our profit, but they are giving us a steady base to cement a green future. One natural way of ensuring sustainability is transparency about our practices, principles and thoughts as transparency is an outshoot; it’s a prerequisite of united, prosperous and sustainable organization."Prudent Business LeaderThrough the adoption of best business practices, a deep concern for the environment and continuous progress through constant application of contemporary technological methods, the company has managed to be a prudent business leader and a leading cement manufacturer.
You may like
Concrete
India donates 225t of cement for Myanmar earthquake relief
Published
3 months agoon
June 17, 2025By
admin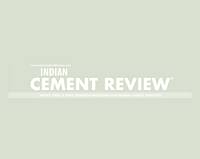
On 23 May 2025, the Indian Navy ship UMS Myitkyina arrived at Thilawa (MITT) port carrying 225 tonnes of cement provided by the Indian government to aid post-earthquake rebuilding efforts in Myanmar. As reported by the Global Light of Myanmar, a formal handover of 4500 50kg cement bags took place that afternoon. The Yangon Region authorities managed the loading of the cement onto trucks for distribution to the earthquake-affected zones.
Concrete
Reclamation of Used Oil for a Greener Future
Published
3 months agoon
June 16, 2025By
admin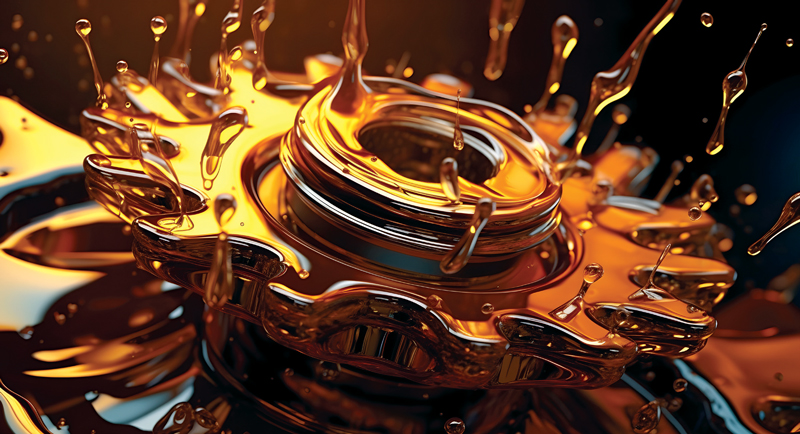
In this insightful article, KB Mathur, Founder and Director, Global Technical Services, explores how reclaiming used lubricants through advanced filtration and on-site testing can drive cost savings, enhance productivity, and support a greener industrial future. Read on to discover how oil regeneration is revolutionising sustainability in cement and core industries.
The core principle of the circular economy is to redefine the life cycle of materials and products. Unlike traditional linear models where waste from industrial production is dumped/discarded into the environment causing immense harm to the environment;the circular model seeks to keep materials literally in continuous circulation. This is achievedthrough processes cycle of reduction, regeneration, validating (testing) and reuse. Product once
validated as fit, this model ensures that products and materials are reintroduced into the production system, minimising waste. The result? Cleaner and greener manufacturing that fosters a more sustainable planet for future generations.
The current landscape of lubricants
Modern lubricants, typically derived from refined hydrocarbons, made from highly refined petroleum base stocks from crude oil. These play a critical role in maintaining the performance of machinery by reducing friction, enabling smooth operation, preventing damage and wear. However, most of these lubricants; derived from finite petroleum resources pose an environmental challenge once used and disposed of. As industries become increasingly conscious of their environmental impact, the paramount importance or focus is shifting towards reducing the carbon footprint and maximising the lifespan of lubricants; not just for environmental reasons but also to optimise operational costs.
During operations, lubricants often lose their efficacy and performance due to contamination and depletion of additives. When these oils reach their rejection limits (as they will now offer poor or bad lubrication) determined through laboratory testing, they are typically discarded contributing to environmental contamination and pollution.
But here lies an opportunity: Used lubricants can be regenerated and recharged, restoring them to their original performance level. This not only mitigates environmental pollution but also supports a circular economy by reducing waste and conserving resources.
Circular economy in lubricants
In the world of industrial machinery, lubricating oils while essential; are often misunderstood in terms of their life cycle. When oils are used in machinery, they don’t simply ‘DIE’. Instead, they become contaminated with moisture (water) and solid contaminants like dust, dirt, and wear debris. These contaminants degrade the oil’s effectiveness but do not render it completely unusable. Used lubricants can be regenerated via advanced filtration processes/systems and recharged with the use of performance enhancing additives hence restoring them. These oils are brought back to ‘As-New’ levels. This new fresher lubricating oil is formulated to carry out its specific job providing heightened lubrication and reliable performance of the assets with a view of improved machine condition. Hence, contributing to not just cost savings but leading to magnified productivity, and diminished environmental stress.
Save oil, save environment
At Global Technical Services (GTS), we specialise in the regeneration of hydraulic oils and gear oils used in plant operations. While we don’t recommend the regeneration of engine oils due to the complexity of contaminants and additives, our process ensures the continued utility of oils in other applications, offering both cost-saving and environmental benefits.
Regeneration process
Our regeneration plant employs state-of-the-art advanced contamination removal systems including fine and depth filters designed to remove dirt, wear particles, sludge, varnish, and water. Once contaminants are removed, the oil undergoes comprehensive testing to assess its physico-chemical properties and contamination levels. The test results indicate the status of the regenerated oil as compared to the fresh oil.
Depending upon the status the oil is further supplemented with high performance additives to bring it back to the desired specifications, under the guidance of an experienced lubrication technologist.
Contamination Removal ? Testing ? Additive Addition
(to be determined after testing in oil test laboratory)
The steps involved in this process are as follows:
1. Contamination removal: Using advanced filtration techniques to remove contaminants.
2. Testing: Assessing the oil’s properties to determine if it meets the required performance standards.
3. Additive addition: Based on testing results, performance-enhancing additives are added to restore the oil’s original characteristics.
On-site oil testing laboratories
The used oil from the machine passes through 5th generation fine filtration to be reclaimed as ‘New Oil’ and fit to use as per stringent industry standards.
To effectively implement circular economy principles in oil reclamation from used oil, establishing an on-site oil testing laboratory is crucial at any large plants or sites. Scientific testing methods ensure that regenerated oil meets the specifications required for optimal machine performance, making it suitable for reuse as ‘New Oil’ (within specified tolerances). Hence, it can be reused safely by reintroducing it in the machines.
The key parameters to be tested for regenerated hydraulic, gear and transmission oils (except Engine oils) include both physical and chemical characteristics of the lubricant:
- Kinematic Viscosity
- Flash Point
- Total Acid Number
- Moisture / Water Content
- Oil Cleanliness
- Elemental Analysis (Particulates, Additives and Contaminants)
- Insoluble
The presence of an on-site laboratory is essential for making quick decisions; ensuring that test reports are available within 36 to 48 hours and this prevents potential mechanical issues/ failures from arising due to poor lubrication. This symbiotic and cyclic process helps not only reduce waste and conserve oil, but also contributes in achieving cost savings and playing a big role in green economy.
Conclusion
The future of industrial operations depends on sustainability, and reclaiming used lubricating oils plays a critical role in this transformation. Through 5th Generation Filtration processes, lubricants can be regenerated and restored to their original levels, contributing to both environmental preservation and economic efficiency.
What would happen if we didn’t recycle our lubricants? Let’s review the quadruple impacts as mentioned below:
1. Oil Conservation and Environmental Impact: Used lubricating oils after usage are normally burnt or sold to a vendor which can be misused leading to pollution. Regenerating oils rather than discarding prevents unnecessary waste and reduces the environmental footprint of the industry. It helps save invaluable resources, aligning with the principles of sustainability and the circular economy. All lubricating oils (except engine oils) can be regenerated and brought to the level of ‘As New Oils’.
2. Cost Reduction Impact: By extending the life of lubricants, industries can significantly cut down on operating costs associated with frequent oil changes, leading to considerable savings over time. Lubricating oils are expensive and saving of lubricants by the process of regeneration will overall be a game changer and highly economical to the core industries.
3. Timely Decisions Impact: Having an oil testing laboratory at site is of prime importance for getting test reports within 36 to 48 hours enabling quick decisions in critical matters that may
lead to complete shutdown of the invaluable asset/equipment.
4. Green Economy Impact: Oil Regeneration is a fundamental part of the green economy. Supporting industries in their efforts to reduce waste, conserve resources, and minimise pollution is ‘The Need of Our Times’.
About the author:
KB Mathur, Founder & Director, Global Technical Services, is a seasoned mechanical engineer with 56 years of experience in India’s oil industry and industrial reliability. He pioneered ‘Total Lubrication Management’ and has been serving the mining and cement sectors since 1999.
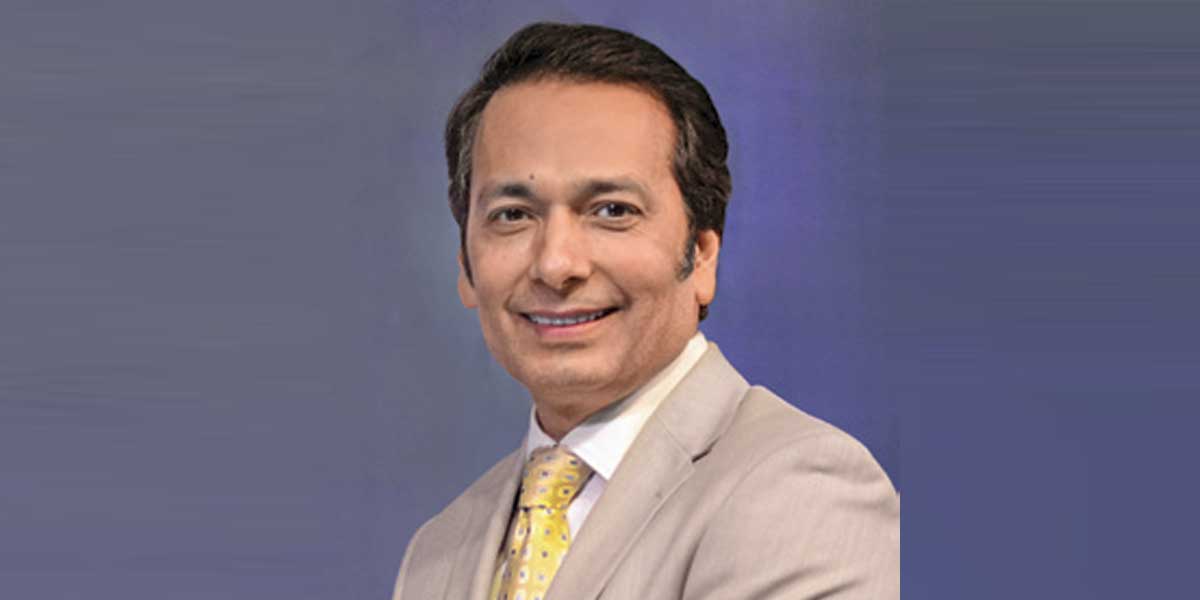
The Indian cement industry has reached a critical juncture in its sustainability journey. In a landmark move, the Ministry of Environment, Forest and Climate Change has, for the first time, announced greenhouse gas (GHG) emission intensity reduction targets for 282 entities, including 186 cement plants, under the Carbon Credit Trading Scheme, 2023. These targets, to be enforced starting FY2025-26, are aligned with India’s overarching ambition of achieving net zero emissions by 2070.
Cement manufacturing is intrinsically carbon-intensive, contributing to around 7 per cent of global GHG emissions, or approximately 3.8 billion tonnes annually. In India, the sector is responsible for 6 per cent of total emissions, underscoring its critical role in national climate mitigation strategies. This regulatory push, though long overdue, marks a significant shift towards accountability and structured decarbonisation.
However, the path to a greener cement sector is fraught with challenges—economic viability, regulatory ambiguity, and technical limitations continue to hinder the widespread adoption of sustainable alternatives. A major gap lies in the lack of a clear, India-specific definition for ‘green cement’, which is essential to establish standards and drive industry-wide transformation.
Despite these hurdles, the industry holds immense potential to emerge as a climate champion. Studies estimate that through targeted decarbonisation strategies—ranging from clinker substitution and alternative fuels to carbon capture and innovative product development—the sector could reduce emissions by 400 to 500 million metric tonnes by 2030.
Collaborations between key stakeholders and industry-wide awareness initiatives (such as Earth Day) are already fostering momentum. The responsibility now lies with producers, regulators and technology providers to fast-track innovation and investment.
The time to act is now. A sustainable cement industry is not only possible—it is imperative.