Environment
Can demand catch up with capacity expansion?
Published
14 years agoon
By
admin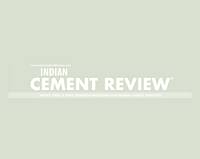
India, the second largest producer of cement, is now one of the fastest growing economies in the world. The country ranks next only to China in cement production with a total capacity of 280 million tonne per annum (mtpa). The Indian cement industry is on a roll, driven by a booming housing sector, and increased activity in infrastructure development like roads, ports and bridges. It has outpaced itself, ramping up production capacity, attracting the top global cement companies to spark off a spate of mergers and acquisitions. The government’s continued thrust on infrastructure and the 12th Five-Year Plan coming up with doubling of allocation to infrastructure will expedite the booming cement sector. An analysis by A Mohankumar.Twenty years have passed, since the industry was de-licensed in 1991-92, and the cement capacity has increased six times, close to 300 mt. During this 20-year period, the industry has flourished, on government’s continuous use of cements for infrastructure development, construction of roads and ports and the boom in real estate also saw the industry scaling new heights. The main consumer of cement is the housing sector, which contributes to almost 60 per cent of cement sale. The last 20 years the industry has witnessed spate of mergers and acquisitions Vicat SA acquiring stake in Hyderabad-based Sagar Cement, Holcim increasing its hold on Ambuja Cement and increasing its stake in ACC Cement, Italcementi Group acquired KK Birla promoted Zuari Industries’ cement business, the the French cement major Lafarge acquired the cement plants of Raymond and Tisco. There were also major consolidations like India Cement taking over Raasi Cement and Sri Vishnu Cement; and Grasim acquiring the cement business of L&T, Indian Rayon’s cement division, and Sri Digvijay Cements.2011 and beyond-Capacity expansion projects lined upDalmia Bharat Enterprises plans to invest $554.32 mn to set up two greenfield cement plants in Karnataka and Meghalaya.Bharathi Cement plans to double its production capacity by expanding its plant in Andhra Pradesh, with an investment of $149.97 mn.Madras Cements plans to invest $178.4 mn to increase the manufacturing capacity of its Ariyalur plant in Tamil Nadu to 4.5 mt from 2 mt.My Home Industries plans to increase cement production capacity from the existing 5 mtpa to 15 mtpa at a cost of $1 bn.Shree Cement plans to invest $97.13 mn to set up a 1.5 mn mt clinker and grinding unit in Rajasthan. The company will also set up a cement manufacturing unit and power plant in Karnataka with a total investment of $423.6 million.Jaiprakash Associates plans to invest $640 mn to increase its cement capacity.Swiss cement company Holcim plans to invest $ 1 bn in setting up two to three greenfield manufacturing plants in India in the next five years to serve the rising domestic demand. Anjani Portland Cement wll invest Rs 350 crore on a cement plant in Karnataka, which will increase the total cement production capacity to 2.2 mtpa.JK Cement will increase its grey cement capacity by 2.2 mt and will set up 5,000 tonne per day (tpd) production capacity in Mangrol, Rajasthan.Gujarat plans to triple its cement production capacity in 3-5 years. These are the major projects which will add to the existing cement capacities. In India, it has been noticed that growth in cement consumption is in correlation to the growth in gross domestic product (GDP), irrespective of its sectoral composition. Based on an expected GDP growth of 7-8 per cent over the next decade, conservative estimates place a cement consumption growth of 9-10 per cent over the same period.Demand drivers: The majors factors that will act as a propeller for demand will be the buoyant real estate market and housing sector, increased infrastructure spending, through various governmental programmes like Indiramma Housing Scheme, Kalaignar Housing Scheme, low-cost housing in urban and rural areas under schemes like Jawaharlal Nehru National Urban Renewal Mission (JNNURM) and Indira Aawas Yojana. The other factors that will add to the growth will be the accelerating rate of urbanisation, easy availability of housing credit, tax benefits for house building and purchasing, etc.Obstacles: The first major constraint will be availability of land. Over the years, land prices have increased astronomically. Cement plants are primarily located where raw material is available in abundance, there are good infrastructure facilities, and logistics to reach the market. Despite India being a very large country, the dwindling number of locations that meet acceptable standards for this criteria, and the large number of small private land holdings involved, makes land acquisition, for future greenfield units, an increasingly cumbersome and time-consuming pre-project activity. The next in order is the fuel. Coal being the primary fuel, is fast depleting. A shortage of 200 mn is estimated. To meet the shortfal, India has to import coal from Indonesia, South Africa, China, Australia and Russia. The advantages of imported coal are its relatively high calorific value, low ash content, low moisture and the availability of credit at international rates. The other alternative to coal can be gas. Gas as a principal fuel, has been rarely used. A two mt pa cement plant is estimated to require about 4 mmscmd (mio standard m3/day) of gas. With new gas discoveries in the Krishna Godavari basin (in the order of 5 trillion standard m3/day), it is foreseen that at least some cement plants in the southern states switching over to gas. Due to the worsening power situation in the country, cement plants are increasingly relying on captive generation to meet their entire power needs. Wind power has been used in some southern plants, tidal power is also under consideration by cement companies.Poor water management is a cause of concern. The industry currently uses approximately 61 mn m3 of water, annually. Despite selecting water-conserving plant equipment, the industry’s requirement for water is expected to grow. The industry usually depends on natural water bodies and groundwater and in some places RO based desalination plants have been installed. Recyling of water can also help to a certain extend.Logistic is a major deterrent. The transport of cement is mainly through railways and roadways. The bulk of the transport both inbound and outbound, accounts for almost 50 per cent of the cost of delivered cement. For cement dispatches, railway is a preferred mode of transport. A rise in freight charges, increases the price of cement and it is passed to the end user. Likewise, rise in petroleum or diesel, increases the price. To conserve transport costs and improve delivery time, split locating grinding capacity, proximate to blending material sources and markets, and creation of bulk terminals at coastal locations, would become more common.Capacity expansion vs raw materialThe main raw materials used in the cement manufacturing process are limestone, sand, shale, clay, and iron ore. The main material, limestone, is usually mined on site while the other minor materials may be mined either on site or in nearby quarries. For manufacturing 1 tonne of cement, a quantity of 1.5 tonne of limestone is required. The cement grade limestone available in India is approximately 15 bn tonne. India is endowed with large deposits of limestone, however given the expected industry growth rate and its current utilisation pattern of limestone. There is a possibility of limestone being fully consumed. This can be curtailed to some extent by scouting and exploration of new deposits; active exploration of the use of calcareous industrial waste as a substitute for limestone and conversion of the industry’s product mix to 100 per cent blended cement will add few more years.Pozzolanic and slag are the two main blending materials. Flyash, India’s primary source of pozzolana is mainly derived from thermal power plants (TPPs). TPPs currently generate about 100 mtpa of flyash, out of which 21 mt is used by the cement industry. Other than flyash, laboratory trials have shown alternate pozzolanic materials such as rice husk, bamboo dust, calcined clay, etc, to have acceptable cementitious properties. After flyash, slag, produced as a waste material by steel plants, is the next most popular blending material. Against a expected availability of 17 mtpa, the usage is 10 mt. Due to the pressing need to dispose slag, there are recent moves by steel producers to enter the cement industry, either through a joint venture with an existing cement player, or independently.EnvironmentCapacity expansion will depend mostly on environment clearance. Cement industry is the major contributor to CO2 emissions. Recently there was news about lower agricultural produce due to cement plants in the vicinity. In future, there would be an increasing demand for environmental clearance. The operations would be dominated by environmental considerations with issues such as more demanding emission levels, conservation of scarce natural resources, lower human dependency, etc. The industry causes environmental impacts at all stages of the process. These include emissions of airborne pollution in the form of dust, gases, noise and vibration when operating machinery and during blasting in quarries. Environmental norms are likely to get more stringent. Greenhouse gas emission in India, at a per capita level, is far lesser than the permissible limit allowed under the Kyoto protocol; hence, India, is exempted from the framework of the treaty.Equipment to reduce dust emissions during quarrying and manufacture of cement is widely used, and equipment to trap and separate exhaust gases are coming up in a big way. Environmental protection also includes the re-integration of quarries into the countryside after they have been closed down by returning them to nature or re-cultivating them. Technology development and acquisition would need to keep pace, eg, lowering of dust emission norms, from 50 mg/Nm3 to 10 mg/Nm3 may result in the increased adoption of hybrid filters; the pressure to reduce CO2 emission could unleash a variety of clean technologies and practices such as cogeneration of power using waste heat, incineration in cement kilns of waste materials to meet the dual objectives of waste disposal and cost reduction, separation of CO2 from kiln exhaust gas and its utilisation in value products, etc.Alterative fuelsCement companies are looking for an alternative to coal. In many plants in Gujarat, Rajasthan and south India, companies mainly use pet coke, imported coal and lignite. Lignite being a poor cousin, the use of lignite in the times ahead would remain restricted, mainly on account of its low calorific value and difficulties in storage. The next alternative to coal is pet coke. Pet coke is a by-product obtained during refining of heavy crude oil. Pet coke is characterised as high grade fuel with a high calorific value of more than 8,000 Kcal per kg, having low ash content and low volatile matter but high sulphur content as up to 7 per cent. Due to higher calorific value compared to coal, less quantity of pet coke needs to be moved from source to plant site, which reduces the cost of transport.The increase in capacity would be better if there is increasing use of surface miners. The utilisation of marginal grade limestone by employing flotation processes to reduce silica and adding calcareous industrial waste for enriching lime and improved drilling and blasting operations through better drilling geometry and explosive technology will help improve the capacity. Availability of larger crushers capable of handling 1.9 x 1.9 m boulder sizes; throughputs exceeding 2,000 tph for a product size of 75 mm which is technologically advanced, and raw grinding system will be an added advantage. For raw grinding adoption of larger and more energy efficient vertical roller mills with longer roller, table lives and improved material bed development should be adopted.Other areas of plant technology and operation, that could see significant changes, include: automation, instrumentation & plant control systems aimed at reducing human intervention, automated maintenance (eg lubrication) and better process measurement and control. This includes new technologies such as intelligent MCCs, serial bus architecture, satellite communications, etc. There would also be a requirement for material handling systems targeted towards achieving higher capacity, smaller area requirements and lower wear rates.Packing and despatch: To meet increased demands, increased adoption of 240 tph, twin discharge, 16 spout packers are likely; to address variable market demands and despatch modes, flexibility in the despatch section would need to be significantly enhanced through appropriate automation.ManpowerWith increase in capacity, there would be increase in plant and equipment sizes, higher levels of automation, and an additional headcount of 14,000-15,000 by the end of 2015. The industry would see diminishing export demands for cements in neighbouring and MENA countries. because of the increase in capacities in MENA countries and large discoveries of limestone. There would be less demand for cement from the neighbouring countries as it would be far more economical for them to export it from other cement rich countries, since cement from India is high due to high cost of raw material, fuels and taxes.ConclusionThe demand for cement is expected to grow at 9-10 per cent per annum. Industry leaders and regional players will spearhead the country’s expansions. Many foreign players are also likely to enter the market as the industry would require enormous amount to finance the projects. In the coming years, there would be major consolidation in the market, in the form of mergers and acquisitions, or a joint venture or major expansion by regional players. Many players would compete for a pan-India presence. The industry would also see improvement in machinery and equipment, and would streamline their production for better results. Capacity addition will also put pressures on input resources like land, limestone, fuel and manpower. Industry would thus compete, not only in the market, but also in attaining strategic control over input resources.The cement industry usually follows a cycle. It starts when demand for cement picks up and companies start enjoying high margins and growth. As the business is lucrative, additional cement capacity comes up both from the incumbents and the new players. However, the capacity addition outpaces demand, and the cement manufacturer starts losing pricing power, resulting in lower profitability. Thereafter, the capacity addition slows down until the demand catches up, and this completes one cycle.However, the current cycle has boosters from a strong economy both from demand for infrastructure and housing and from supply due to increased investment capacity. The current year will therefore see a challanging economic balance.
You may like
Concrete
India donates 225t of cement for Myanmar earthquake relief
Published
3 weeks agoon
June 17, 2025By
admin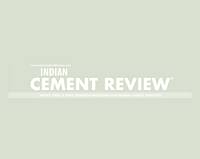
On 23 May 2025, the Indian Navy ship UMS Myitkyina arrived at Thilawa (MITT) port carrying 225 tonnes of cement provided by the Indian government to aid post-earthquake rebuilding efforts in Myanmar. As reported by the Global Light of Myanmar, a formal handover of 4500 50kg cement bags took place that afternoon. The Yangon Region authorities managed the loading of the cement onto trucks for distribution to the earthquake-affected zones.
Concrete
Reclamation of Used Oil for a Greener Future
Published
3 weeks agoon
June 16, 2025By
admin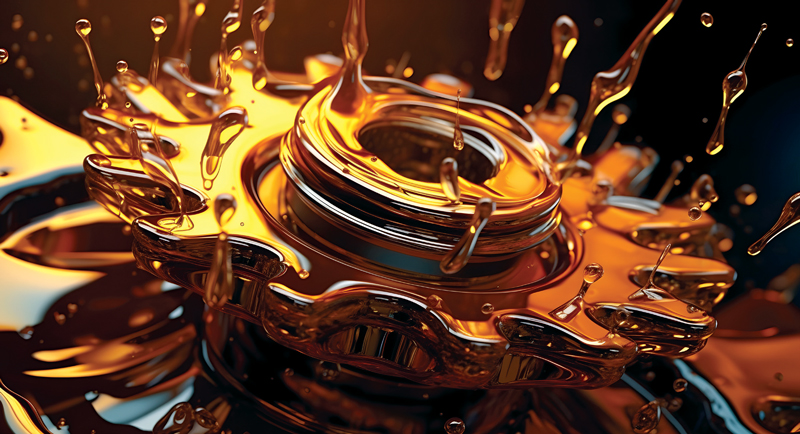
In this insightful article, KB Mathur, Founder and Director, Global Technical Services, explores how reclaiming used lubricants through advanced filtration and on-site testing can drive cost savings, enhance productivity, and support a greener industrial future. Read on to discover how oil regeneration is revolutionising sustainability in cement and core industries.
The core principle of the circular economy is to redefine the life cycle of materials and products. Unlike traditional linear models where waste from industrial production is dumped/discarded into the environment causing immense harm to the environment;the circular model seeks to keep materials literally in continuous circulation. This is achievedthrough processes cycle of reduction, regeneration, validating (testing) and reuse. Product once
validated as fit, this model ensures that products and materials are reintroduced into the production system, minimising waste. The result? Cleaner and greener manufacturing that fosters a more sustainable planet for future generations.
The current landscape of lubricants
Modern lubricants, typically derived from refined hydrocarbons, made from highly refined petroleum base stocks from crude oil. These play a critical role in maintaining the performance of machinery by reducing friction, enabling smooth operation, preventing damage and wear. However, most of these lubricants; derived from finite petroleum resources pose an environmental challenge once used and disposed of. As industries become increasingly conscious of their environmental impact, the paramount importance or focus is shifting towards reducing the carbon footprint and maximising the lifespan of lubricants; not just for environmental reasons but also to optimise operational costs.
During operations, lubricants often lose their efficacy and performance due to contamination and depletion of additives. When these oils reach their rejection limits (as they will now offer poor or bad lubrication) determined through laboratory testing, they are typically discarded contributing to environmental contamination and pollution.
But here lies an opportunity: Used lubricants can be regenerated and recharged, restoring them to their original performance level. This not only mitigates environmental pollution but also supports a circular economy by reducing waste and conserving resources.
Circular economy in lubricants
In the world of industrial machinery, lubricating oils while essential; are often misunderstood in terms of their life cycle. When oils are used in machinery, they don’t simply ‘DIE’. Instead, they become contaminated with moisture (water) and solid contaminants like dust, dirt, and wear debris. These contaminants degrade the oil’s effectiveness but do not render it completely unusable. Used lubricants can be regenerated via advanced filtration processes/systems and recharged with the use of performance enhancing additives hence restoring them. These oils are brought back to ‘As-New’ levels. This new fresher lubricating oil is formulated to carry out its specific job providing heightened lubrication and reliable performance of the assets with a view of improved machine condition. Hence, contributing to not just cost savings but leading to magnified productivity, and diminished environmental stress.
Save oil, save environment
At Global Technical Services (GTS), we specialise in the regeneration of hydraulic oils and gear oils used in plant operations. While we don’t recommend the regeneration of engine oils due to the complexity of contaminants and additives, our process ensures the continued utility of oils in other applications, offering both cost-saving and environmental benefits.
Regeneration process
Our regeneration plant employs state-of-the-art advanced contamination removal systems including fine and depth filters designed to remove dirt, wear particles, sludge, varnish, and water. Once contaminants are removed, the oil undergoes comprehensive testing to assess its physico-chemical properties and contamination levels. The test results indicate the status of the regenerated oil as compared to the fresh oil.
Depending upon the status the oil is further supplemented with high performance additives to bring it back to the desired specifications, under the guidance of an experienced lubrication technologist.
Contamination Removal ? Testing ? Additive Addition
(to be determined after testing in oil test laboratory)
The steps involved in this process are as follows:
1. Contamination removal: Using advanced filtration techniques to remove contaminants.
2. Testing: Assessing the oil’s properties to determine if it meets the required performance standards.
3. Additive addition: Based on testing results, performance-enhancing additives are added to restore the oil’s original characteristics.
On-site oil testing laboratories
The used oil from the machine passes through 5th generation fine filtration to be reclaimed as ‘New Oil’ and fit to use as per stringent industry standards.
To effectively implement circular economy principles in oil reclamation from used oil, establishing an on-site oil testing laboratory is crucial at any large plants or sites. Scientific testing methods ensure that regenerated oil meets the specifications required for optimal machine performance, making it suitable for reuse as ‘New Oil’ (within specified tolerances). Hence, it can be reused safely by reintroducing it in the machines.
The key parameters to be tested for regenerated hydraulic, gear and transmission oils (except Engine oils) include both physical and chemical characteristics of the lubricant:
- Kinematic Viscosity
- Flash Point
- Total Acid Number
- Moisture / Water Content
- Oil Cleanliness
- Elemental Analysis (Particulates, Additives and Contaminants)
- Insoluble
The presence of an on-site laboratory is essential for making quick decisions; ensuring that test reports are available within 36 to 48 hours and this prevents potential mechanical issues/ failures from arising due to poor lubrication. This symbiotic and cyclic process helps not only reduce waste and conserve oil, but also contributes in achieving cost savings and playing a big role in green economy.
Conclusion
The future of industrial operations depends on sustainability, and reclaiming used lubricating oils plays a critical role in this transformation. Through 5th Generation Filtration processes, lubricants can be regenerated and restored to their original levels, contributing to both environmental preservation and economic efficiency.
What would happen if we didn’t recycle our lubricants? Let’s review the quadruple impacts as mentioned below:
1. Oil Conservation and Environmental Impact: Used lubricating oils after usage are normally burnt or sold to a vendor which can be misused leading to pollution. Regenerating oils rather than discarding prevents unnecessary waste and reduces the environmental footprint of the industry. It helps save invaluable resources, aligning with the principles of sustainability and the circular economy. All lubricating oils (except engine oils) can be regenerated and brought to the level of ‘As New Oils’.
2. Cost Reduction Impact: By extending the life of lubricants, industries can significantly cut down on operating costs associated with frequent oil changes, leading to considerable savings over time. Lubricating oils are expensive and saving of lubricants by the process of regeneration will overall be a game changer and highly economical to the core industries.
3. Timely Decisions Impact: Having an oil testing laboratory at site is of prime importance for getting test reports within 36 to 48 hours enabling quick decisions in critical matters that may
lead to complete shutdown of the invaluable asset/equipment.
4. Green Economy Impact: Oil Regeneration is a fundamental part of the green economy. Supporting industries in their efforts to reduce waste, conserve resources, and minimise pollution is ‘The Need of Our Times’.
About the author:
KB Mathur, Founder & Director, Global Technical Services, is a seasoned mechanical engineer with 56 years of experience in India’s oil industry and industrial reliability. He pioneered ‘Total Lubrication Management’ and has been serving the mining and cement sectors since 1999.
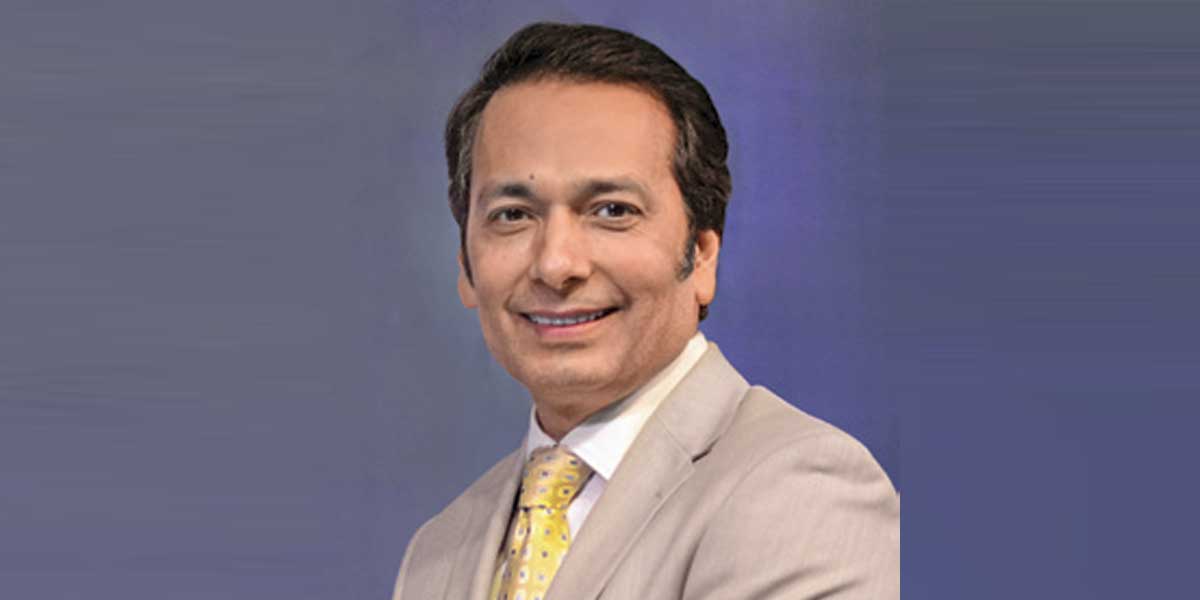
The Indian cement industry has reached a critical juncture in its sustainability journey. In a landmark move, the Ministry of Environment, Forest and Climate Change has, for the first time, announced greenhouse gas (GHG) emission intensity reduction targets for 282 entities, including 186 cement plants, under the Carbon Credit Trading Scheme, 2023. These targets, to be enforced starting FY2025-26, are aligned with India’s overarching ambition of achieving net zero emissions by 2070.
Cement manufacturing is intrinsically carbon-intensive, contributing to around 7 per cent of global GHG emissions, or approximately 3.8 billion tonnes annually. In India, the sector is responsible for 6 per cent of total emissions, underscoring its critical role in national climate mitigation strategies. This regulatory push, though long overdue, marks a significant shift towards accountability and structured decarbonisation.
However, the path to a greener cement sector is fraught with challenges—economic viability, regulatory ambiguity, and technical limitations continue to hinder the widespread adoption of sustainable alternatives. A major gap lies in the lack of a clear, India-specific definition for ‘green cement’, which is essential to establish standards and drive industry-wide transformation.
Despite these hurdles, the industry holds immense potential to emerge as a climate champion. Studies estimate that through targeted decarbonisation strategies—ranging from clinker substitution and alternative fuels to carbon capture and innovative product development—the sector could reduce emissions by 400 to 500 million metric tonnes by 2030.
Collaborations between key stakeholders and industry-wide awareness initiatives (such as Earth Day) are already fostering momentum. The responsibility now lies with producers, regulators and technology providers to fast-track innovation and investment.
The time to act is now. A sustainable cement industry is not only possible—it is imperative.

Hindalco Buys US Speciality Alumina Firm for $125 Million

Star Cement launches ‘Star Smart Building Solutions’

Nuvoco Vistas reports record quarterly EBITDA

UltraTech Cement increases capacity by 1.4Mt/yr

Shree Cement reports 2025 financial year results

Hindalco Buys US Speciality Alumina Firm for $125 Million

Star Cement launches ‘Star Smart Building Solutions’

Nuvoco Vistas reports record quarterly EBITDA

UltraTech Cement increases capacity by 1.4Mt/yr
