Process
Key Considerations for Cooler Retrofit
Published
4 years agoon
By
admin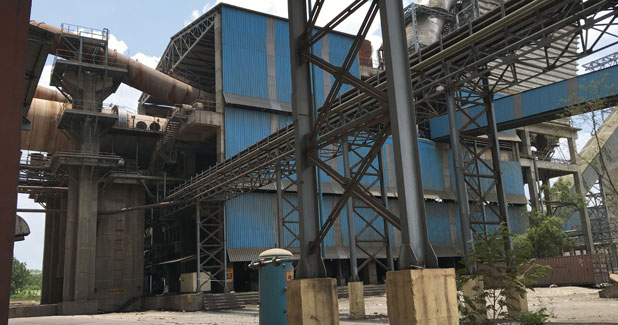
The need of the hour is to get the best performance from a cooler. When the kiln capacity goes up, one needs to understand the design considerations and what best can be done under the changed conditions.
The cement manufacturing process is highly energy intensive and consumes between 700 to 780 kcal/kg clinker of thermal energy in a dry type process with inline calciner. Cooler losses contribute to about 105-115 kcal/kg clinker for a modern fourth/fifth generation cooler. In order to get a better perspective on the basic engineering revolving around coolers, this article discusses some of the fundamental principles behind the working of the cooler as well as the design considerations that become paramount while upgrading coolers.
Clinker Cooler Basics
The clinker cooler is the part of the pyro-process where the solid reaction mass is quenched on exiting the kiln. The cooler is basically a heat exchanger which cools the hot clinker from the kiln while transferring this heat to the ambient air and consists of two zones. The clinker first enters the heat recuperation zone where the heat from the clinker is transferred to optimised amount of cooling air, so that the requisite amount of secondary and tertiary air can be obtained for combustion at the maximum possible temperature. The second zone is the cooling zone where the rest of the air is supplied to cool the clinker and the heat from the vent air can be recovered by drying of coal in coal mill or by waste heat recovery boilers.
The efficiency of the cooler depends on its ability to recover the heat from the clinker entering the cooler, and cooling the clinker. The cooler also fulfils the key role of transporting the clinker away from the kiln in a reliable manner.
Cooler design would include some of the following requirements: low capital cost; optimum cooling rate for good clinker quality; low clinker discharge temperature; least possible impact upon the environment; high heat recovery; low power consumption; low wear and maintenance cost, operational reliability, causing minimal downtime; ease of control so that it delivers a steady flow of combustion air at an unvarying temperature to the kiln and calciner.
Leading manufacturers of coolers today are FLSmidth, IKN (Ingenieurbnro Knhlerbau Neustadt), CemProTec, Claudius Peters, KHD Humboldt Wedag, ThyssenKrupp Polysius AG, FONS technology, etc. The coolers designed by these vendors have undergone significant modifications over the years. The major differences lie in the manner in which material is conveyed over the grates, the mode of aeration and the solid-gas heat exchange, the type and presence of self-regulating valves for airflow and the hydraulic system for moving parts.
With advancement in clinker cooler technology, the requirement of cooling air has gradually gone down from about 3.5 kg/kg clinker to 2.2 kg air /kg clinker (1.6-1.8 Nm3/kg clinker) in new fifth generation clinker coolers and the specific cooler area has gone up from 20 tpd/m2 to around 45 tpd/m2. The operating efficiency hovers around 70 ? 74 per cent in modern coolers (based on coal as fuel). Various developments have taken place with respect to the mode of aeration of grates, the mechanism of forward movement of the clinker as well as with the protection of the wear parts at the high operating temperatures. The issue of segregation of fine and coarse particles of clinker as received from the kiln on the bed of the cooler, causing maldistribution of cooling air flow through the bed is also to be prevented by the mechanism of transport within the cooler. Cooler manufacturers have developed various techniques to overcome issues of bypass of cooling air, red river formation as well as snow man formation at cooler inlet which have brought down the cooler power requirement to around 3-3.6 kWh/t of clinker from earlier design grate coolers which consumed around 6-7 kWh/t of clinker cooled.
The clinker cooler auxiliary system is generally similar in most modern coolers, where the cooling air enters through multiple fans and the positive pressure of the fan being controlled by the height of clinker bed on the cooler grate. The height of the bed is controlled by the grate speed or the speed at which crossbars push the material out of the cooler with an automatic closed loop control system. The vent air circuit usually consists of a heat exchanger, and baghouse or an ESP and a fan before the stack. In some designs the cooler has individual under-grate compartments, each being supplied with air from their respective cooler fans. For control of the air through the grate plates within the individual compartment, each cooler grate plate has a flow regulating device. Nowadays, cooler fans are also provided with variable drives so that the specific power consumption can be reduced in case the kiln is operated for prolonged periods at varying capacity levels. Some vendors provide circuits that can recycle the cooler vent air back to the cooler inlet, reducing the overall heat loss. This may be advantageous in the case a mid-tapping is taken at the cooler for a waste heat recovery boiler and the vent air after the boiler is at a low temperature of around 100-110?C.
A clinker crusher is usually provided after the cooler grades to ensure that any oversize lumps are broken down. The clinker discharges from the cooler across a grizzly to a hammer mill or hydraulic roll crusher located in the cooler outlet. The crusher may be sometimes installed in the middle of the cooler, before the last grate, to break up lumps and large clinker, and to ensure their efficient cooling.
Cooler operation issues Ideally, the cooler is designed to cool the clinker which enters at 1,300oC to around 100oC (ambient +65?C). When a cooler runs at an optimised level, the secondary air temperature is around 1,050oC, the tertiary air leaving the cooler is at 950oC and the vent air is at 250-300oC. Sometimes a mid-tapping from the cooler may be taken to the coal mill and/or to waste heat recovery boilers. Temperatures at such mid-tapping outlets are around 450-500oC. A typical mass balance for the cooler would be thus: of the cooling air of around 2.2 kg air/kg clinker that enters the cooler, around 1 kg air/kg clinker leaves as secondary and tertiary air for combustion, and the rest could be vented as exhaust. In case of a mid-tapping around 0.35 kg air/kg clinker may be removed (depends on coal moisture) and the rest 0.85 kg air/kg clinker is vented at lower temperatures of 150 to 200?C. Cooler disruptions may occur once in a while, however, most coolers are designed to handle higher temperatures or higher volumes of vent air for short periods (30 mins), and during such periods the coolers can be brought under manual control without major disruptions.
Ercom personnel have come across real plant situations where coolers perform at sub-par levels.
Considerations for cooler upgrades
Ercom has been able to solve most of the problems by studying the operation of the coolers and optimising the operating parameters. However for a given make, model and age of cooler, there will be a limit to the improvements that can be gained by tweaking operations alone. The cooler may become a bottleneck after capacity enhancement of the preheater-precalciner is carried out.
Ercom typically carries out a baseline audit to determine the above and then the project proceeds along the following lines:
1.Comparison of available cooler technologies to determine the best fit for the upgrade.
2.The choice of technology can be made for upgradation, on the following points: a.Possibility to reuse the existing cooler building/foundation. Constraints due to existing layout and possibility of increasing cooling modules have to be evaluated.
b.Existence of other pyro-lines and hence reduction of spares cost by installing similar coolers. Improvement in the maintenance requirement by incorporation of new design.
c.Modifications required to the cooler hood, burner assembly, etc.
d.Requirement of new cooler fans or reuse of existing ones. 3.Basic engineering is carried out keeping in mind that the main reason for installing the upgrade is to reduce the specific heat consumption of the pyro process, by reducing cooler losses and to also match higher clinker production level achieved from optimising the kiln operation. In this context, it is important to mention that a waste heat boiler for cooler exhaust gases should be designed on the basis of efficient operation of the cooler after upgrade. Any design that increases the power rating of the waste heat recovery system by reducing the heat recuperation to the kiln, thereby causing more fuel consumption, would not be a sustainable design (unless the cement plant was paid for burning fuel).
4.In a retrofit project, lead delivery times and hook-up times will play an important role in selection of vendors.
5.Since access to plant areas will be restricted in an operational project, project planning and execution will have to be carried out efficiently so that there are minimum hurdles to the movement of men and materials while maintaining a safe working condition at all times.
6.The enhanced requirement of certain utilities as well as necessity of automation upgrades when modifying the cooler should be studied upfront so that there will be fewer surprises during site installation and commissioning.
Ercom has been involved in cooler retrofitting projects both in India and the Middle East. Typically for upgradation from the cooler alone, say from 4,000 t/d to 5000 t/d, the cost of the project (retrofitting of existing cooler) is between Rs 6-9 crore depending on the extent of modifications required. However, the same may substantially vary on a case-to-case basis.
Upgradation of coolers in cement plants will be successful only when the entire project is conceived with an in-depth study of techno-economic feasibility and executed with adept and experienced engineering and project management. With assistance from partners like Ercom, all stakeholders will come out with positive outputs that will help the sustainability of both the environment and the cement business.
Some of the typical problems faced by many users are:
The cooler is unable to cool the clinker. Hot clinker at 150- 200?C leaves the cooler and is subsequently sprayed with water. In such cases it is found that the vent gas is also at high temperature, around 350?C.
1.The design of cooler or the installation of the cooler is such that quenching action does not happen at the immediate cooler inlet at the stationary grate section. This will lead to lower secondary and tertiary air temperatures, thus affecting the kiln operation.
2.The raw meal chemistry and the subsequent burning in the kiln may result in higher proportion of fines. If the cooler is not designed to handle fines there may be insufficient heat exchange, red rivers formation, carryover of material in the TA duct to cause blockages in cyclones, etc.
3.Snowman formation in the cooler could occur due to inefficient kiln operation with excessive fines, fall of clinker coating and due to the deficiency in number and locations of air blasters.
4.In some cases, the temperatures that were expected from cooler mid-tapping for coal mills or waste heat recovery systems are not achieved.
5.Higher power consumption in cooler drives occurs, which could be a result of coolers handling greater than design loads.
6.Frequent stoppages of cooler could take place due to failure of mechanical parts or high temperatures in gear box lubrication systems. Maintenance issues may also arise due to designs in which hot clinker falls out of the grate plates, and jamming of plates are frequent.
A cooler upgradation will have to be carried out based on the following parameters:
1.A design basis based on any envisaged upgradation in clinker capacity, plans to use alternate fuels (may affect the burner assembly), and plans to install waste heat recovery systems.
2.The specific heat consumption at baseline level should be determined along with existing cooler efficiency levels. This should be compared against industrial benchmarks for similar systems. Any changes in raw mix and clinker chemistry should also be considered.
3.An analysis of cooler downtime over the last two-three years will give a good idea of the failure mechanisms of the cooler. This will highlight the mechanical/electrical or automation related deficiencies in the existing installation.
(This article has been authored by S Bhattacharya, P K Ghosh and S Chatterjee, Ercom Engineers Pvt Ltd, New Delhi)
Process
Price hikes, drop in input costs help cement industry to post positive margins: Care Ratings
Published
4 years agoon
October 21, 2021By
admin
Region-wise,the southern region comprises 35% of the total cement capacity, followed by thenorthern, eastern, western and central region comprising 20%, 18%, 14% and 13%of the capacity, respectively.
The cement industry is expected to post positive margins on decent price hikes over the months, falling raw material prices and marked drop in overall production costs, said an analysis of Care Ratings.
Wholesale and retail prices of cement have increased 11.9% and 12.4%, respectively, in the current financial year. As whole prices have remained elevated in most of the markets in the months of FY20, against the corresponding period of the previous year.
Similarly, electricity and fuel cost have declined 11.9% during 9M FY20 due to drop in crude oil prices. Logistics costs, the biggest cost for cement industry, has also dropped 7.7% (selling and distribution) as the Railways extended the benefit of exemption from busy season surcharge. Moreover, the cost of raw materials, too, declined 5.1% given the price of limestone had fallen 11.3% in the same aforementioned period, the analysis said.
According to Care Ratings, though the overall sales revenue has increased only 1.3%, against 16% growth in the year-ago period, the overall expenditure has declined 3.2% which has benefited the industry largely given the moderation in sales.
Even though FY20 has been subdued in terms of production and demand, the fall in cost of production has still supported the cement industry by clocking in positive margins, the rating agency said.
Cement demand is closely linked to the overall economic growth, particularly the housing and infrastructure sector. The cement sector will be seeing a sharp growth in volumes mainly due to increasing demand from affordable housing and other government infrastructure projects like roads, metros, airports, irrigation.
The government’s newly introduced National Infrastructure Pipeline (NIP), with its target of becoming a $5-trillion economy by 2025, is a detailed road map focused on economic revival through infrastructure development.
The NIP covers a gamut of sectors; rural and urban infrastructure and entails investments of Rs.102 lakh crore to be undertaken by the central government, state governments and the private sector. Of the total projects of the NIP, 42% are under implementation while 19% are under development, 31% are at the conceptual stage and 8% are yet to be classified.
The sectors that will be of focus will be roads, railways, power (renewable and conventional), irrigation and urban infrastructure. These sectors together account for 79% of the proposed investments in six years to 2025. Given the government’s thrust on infrastructure creation, it is likely to benefit the cement industry going forward.
Similarly, the Pradhan Mantri Awaas Yojana, aimed at providing affordable housing, will be a strong driver to lift cement demand. Prices have started correcting Q4 FY20 onwards due to revival in demand of the commodity, the agency said in its analysis.
Industry’s sales revenue has grown at a CAGR of 7.3% during FY15-19 but has grown only 1.3% in the current financial year. Tepid demand throughout the country in the first half of the year has led to the contraction of sales revenue. Fall in the total expenditure of cement firms had aided in improving the operating profit and net profit margins of the industry (OPM was 15.2 during 9M FY19 and NPM was 3.1 during 9M FY19). Interest coverage ratio, too, has improved on an overall basis (ICR was 3.3 during 9M FY19).
According to Cement Manufacturers Association, India accounts for over 8% of the overall global installed capacity. Region-wise, the southern region comprises 35% of the total cement capacity, followed by the northern, eastern, western and central region comprising 20%, 18%, 14% and 13% of the capacity, respectively.
Installed capacity of domestic cement makers has increased at a CAGR of 4.9% during FY16-20. Manufacturers have been able to maintain a capacity utilisation rate above 65% in the past quinquennium. In the current financial year due to the prolonged rains in many parts of the country, the capacity utilisation rate has fallen from 70% during FY19 to 66% currently (YTD).
Source:moneycontrol.com
Process
Wonder Cement shows journey of cement with new campaign
Published
4 years agoon
October 21, 2021By
admin
The campaign also marks Wonder Cement being the first ever cement brand to enter the world of IGTV…
ETBrandEquity
Cement manufacturing company Wonder Cement, has announced the launch of a digital campaign ‘Har Raah Mein Wonder Hai’. The campaign has been designed specifically to run on platforms such as Instagram, Facebook and YouTube.
#HarRaahMeinWonderHai is a one-minute video, designed and conceptualised by its digital media partner Triature Digital Marketing and Technologies Pvt Ltd. The entire journey of the cement brand from leaving the factory, going through various weather conditions and witnessing the beauty of nature and wonders through the way until it reaches the destination i.e., to the consumer is very intriguing and the brand has tried to showcase the same with the film.
Sanjay Joshi, executive director, Wonder Cement, said, "Cement as a product poses a unique marketing challenge. Most consumers will build their homes once and therefore buy cement once in a lifetime. It is critical for a cement company to connect with their consumers emotionally. As a part of our communication strategy, it is our endeavor to reach out to a large audience of this country through digital. Wonder Cement always a pioneer in digital, with the launch of our IGTV campaign #HarRahMeinWonderHai, is the first brand in the cement category to venture into this space. Through this campaign, we have captured the emotional journey of a cement bag through its own perspective and depicted what it takes to lay the foundation of one’s dreams and turn them into reality."
The story begins with a family performing the bhoomi poojan of their new plot. It is the place where they are investing their life-long earnings; and planning to build a dream house for the family and children. The family believes in the tradition of having a ‘perfect shuruaat’ (perfect beginning) for their future dream house. The video later highlights the process of construction and in sequence it is emphasising the value of ‘Perfect Shuruaat’ through the eyes of a cement bag.
Tarun Singh Chauhan, management advisor and brand consultant, Wonder Cement, said, "Our objective with this campaign was to show that the cement produced at the Wonder Cement plant speaks for itself, its quality, trust and most of all perfection. The only way this was possible was to take the perspective of a cement bag and showing its journey of perfection from beginning till the end."
According to the company, the campaign also marks Wonder Cement being the first ever cement brand to enter the world of IGTV. No other brand in this category has created content specific to the platform.
Process
In spite of company’s optimism, demand weakness in cement is seen in the 4% y-o-y drop in sales volume. (Reuters)
Published
4 years agoon
October 21, 2021By
admin
Cost cuts and better realizations save? the ?day ?for ?UltraTech Cement, Updated: 27 Jan 2020, Vatsala Kamat from Live Mint
Lower cost of energy and logistics helped Ebitda per tonne rise by about 29% in Q3
Premiumization of acquired brands, synergistic?operations hold promise for future profit growth Topics
UltraTech Cement
India’s largest cement producer UltraTech Cement Ltd turned out a bittersweet show in the December quarter. A sharp drop in fuel costs and higher realizations helped drive profit growth. But the inherent demand weakness was evident in the sales volumes drop during the quarter.
Better realizations during the December quarter, in spite of the 4% year-on-year volume decline, minimized the pain. Net stand-alone revenue fell by 2.6% to ?9,981.8 crore.
But as pointed out earlier, lower costs on most fronts helped profitability. The chart alongside shows the sharp drop in energy costs led by lower petcoke prices, lower fuel consumption and higher use of green power. Logistics costs, too, fell due to lower railway freight charges and synergies from the acquired assets. These savings helped offset the increase in raw material costs.
The upshot: Q3 Ebitda (earnings before interest, tax, depreciation and amortization) of about ?990 per tonne was 29% higher from a year ago. The jump in profit on a per tonne basis was more or less along expected lines, given the increase in realizations. "Besides, the reduction in net debt by about ?2,000 crore is a key positive," said Binod Modi, analyst at Reliance Securities Ltd.
Graphic by Santosh Sharma/Mint
What also impressed analysts is the nimble-footed integration of the recently merged cement assets of Nathdwara and Century, which was a concern on the Street.
Kunal Shah, analyst (institutional equities) at Yes Securities (India) Ltd, said: "The company has proved its ability of asset integration. Century’s cement assets were ramped up to 79% capacity utilization in December, even as they operated Nathdwara generating an Ebitda of ?1,500 per tonne."
Looks like the demand weakness mirrored in weak sales during the quarter was masked by the deft integration and synergies derived from these acquired assets. This drove UltraTech’s stock up by 2.6% to ?4,643 after the Q3 results were declared on Friday.
Brand transition from Century to UltraTech, which is 55% complete, is likely to touch 80% by September 2020. A report by Jefferies India Pvt. Ltd highlights that the Ebitda per tonne for premium brands is about ?5-10 higher per bag than the average (A cement bag weighs 50kg). Of course, with competition increasing in the arena, it remains to be seen how brand premiumization in the cement industry will pan out. UltraTech Cement scores well among peers here.
However, there are road bumps ahead for the cement sector and for UltraTech. Falling gross domestic product growth, fiscal slippages and lower budgetary allocation to infrastructure sector are making industry houses jittery on growth. Although UltraTech’s management is confident that cement demand is looking up, sustainability and pricing power remains a worry for the near term.