Process
Ready for a quality mix
Published
13 years agoon
By
admin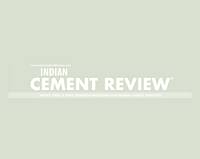
ICR studies the concrete equipment manufacturing industry, threat posed by the Chinese equipment industry and the reasons affecting the quality of concrete in India.
Infrastructure development works as a strong catalyst for a country’s economic growth, and India, hoping to be a global economic leader, has many such projects in the pipeline. With the Government of India launching multi-billion infrastructure projects, the demand for construction equipment has risen manifold. The government sector alone has an estimate of USD 716.33 billion to spend on infrastructure in the near future. Many private sector players and real estate industrialists have also enlarged the size of the construction market in recent years and with fast track execution being the order of the day, equipment is increasingly playing a crucial role. Hans Fuchs, CEO and Managing Director, ACC Concrete, elaborates the market size of RMC in the construction industry. "The total size of RMC in India is approximately 60 mio cum. However, the RMC produced from commercial RMC supplies is approximately 22 mio cum. The reason for this is that a lot of on-site production takes place and is actually increasing. This is backward Integration market (contractors and builders erecting and operating their own plants From our statistics and forecast we expect the residential segment to account for about 29 per cent of the demand while Infrastructure (roads, powers, railways, airports etc) and commercial construction (commercial complexes, retail stores etc) segments are likely to constitute about 33 per cent and 38 per cent respectively."
Concrete equipment industry
Indian concrete equipment industry has been growing at a rapid pace in recent years owing to high demand for sophisticated equipment. Entry of various foreign players in Indian market provides an indication of the potential of the Indian concrete equipment market, which is expected to grow at a CAGR of – 20.0 per cent over the next five years.
Segment such as concrete equipments have witnessed notable market growth and housing sector developments will further enable it to register 18.8 per cent CAGR growth during FY 2011 – FY 2014.
Despite a fall in 2009, the concrete equipment market is recovering strongly. Various real estate projects along with focus on affordable housing will create huge demand for concrete equipment in the country. Besides, various government and private housing development projects have been already launched and are currently in the development phase. It is anticipated that the trend will prevail in coming years also, which will boost the demand for concrete equipment in the country.
Apart from concrete equipment, several other segments such as, earth moving equipment, material handling equipment and road building have also been showing tremendous growth for the past few years. Based on various market drivers and trends as discussed and analysed in report, these segments are all set to witness rapid market expansion during our forecast period (FY 2011-14). Commenting on the current scenario of the concrete equipment, SA Reddy, Ex Deputy Managing Director, Gammon, said, "Most of the structures in the country are constructed in concrete rather than structural steel due to competitive economic advantages. The concrete construction industry is relatively better developed. The structural steel available in the country is of dated specifications; the rolled sections manufactured in the country do not conform to those in the developed countries, obsolete by decades. Thus approximately more than 100 million tonne of cement is used every year in the manufacture of concrete in the country. However, most of the concrete is being produced in the small and medium scale sectors using tilting drum mixers and volumetric batching. The Indian Standard Code of Practice IS 456 mandates that concrete shall be produced by weigh batching except for low grades of concrete. Nominal mix concrete may be used for concrete of M20 or lower. The code also specifies that design mix concrete is preferred to nominal mix, but in most of the cases this is not being followed. Consequently, the development and production of concrete construction equipment in India remains stunted, barring exceptions." Siddharth Shah, Managing Diretor, Cosmos Sales, said, "Curren?tly there has been a drastic change in people who have started understanding the quality of concrete. Initially people never understood concrete as a whole in terms of quality and output which has changed in last two years. The change in understanding has resulted into better quality machines." Considering the current financial slump in the market for the first two quarters, he further exclaims that it was due to certain factors like the stoppages, governmental issues and policies which had just been introduced, however remaining optimistic, he said that the situation has started improving.
Nevertheless, Dr JD Bapat, an independent consultant, is very much positive when it comes to sharing his views on the current scenario of the equipment industry. "In my opinion the concrete industry in India is still at a very nascent stage and is still developing. We might have not yet reached the stage wherein we have all the modern technologies, hence the development has been happening rapidly, since the manufactures are willingly accepting the new technologies launched in the market. We have been adopting a lot of technologies in concrete pumps from Germany". The manufacturers are leaving no stone unturned in order to combat the current market situation and are introducing newer technologies and equipment have a leading edge over others.
Supreme Infra has signed a deal worth Rs 107 crore out of which, they have got concrete equipment worth Rs 56 crore which includes crushing equipment. Manish Kumar Sharma, Head of Plant and Machinery, emphasises on the need of introducing new products. "Being a construction company we need to buy a lot of concrete equipment, thus have purchased boom pumps, batching plants which have cut down on the number of days required for the projects."
Similarly, Cosmos Sales will be launching a simple plug and play mobile batching plant for the upcoming bC India 2013. The equipment will be easy to handle and will be operating on the concept of a twin shaft mixer with the output of 25 cu m the control panel of the plant will have has PLC’s or a printout system which helps us monitor which kind of concrete is the customer opting for. The best part of this equipment is that it is just plug and play. No erections or site preparations are needed for the same.
Commenting on the technological progress TR Badarinarayan, CEO, Sany India, said, "Technological change is a continuous process and since the company has now been acquired by Putzmiester, they now have a complete range of concrete equipment including transit mixers and batching plants. Thus the batching plants have become more economical and accurate with the introduction of computerised technologies." Also the transit mixers, the capacity of 6 cu m is now the basic requirement and having a capacity of 8 cu m is now a luxury. Due to these technological changes, the mixers have become fuel efficient and since the imports are larger in volume, the prices have balanced. In terms of the cosmetic change in transit mixers, there is a small improvement in terms of the hydraulic pumps and motors used and have become neater, which makes them look appealing.
SA Reddy, feels that the technological improvements relate to moisture control integrated with PLC, use of elaborate PLC programs in Batching Plants and obligatory use of either Pan Mixers or turbo mixers with single or twin horizontal shafts. All operations in batch plants are PLC controlled both for quality and quantity. Moisture in aggregates is automatically measured by moisture probes fitted in the sand bins and fed to the PLC for appropriate adjustments. Expressing his view on the boom pumps he exclaimed, "Boom pumps are manufactured in India for up to about 40 m reach compared to reach up to 100 m elsewhere. Self climbing placer booms are definitely required in high rise construction. Concrete pipelines are required to be manufactured with high grade steel. Such pipes are still being imported as high grade steel is not manufactured in the country."
Hans Fauchs highlights the need of the technological progress required in the RMC equipment industry. "With increasing usage of high quality RMC for normal to critical projects, equipment manufacturers are building many customised and innovative products-mobile plants, small-sized plants/ small foundation, long boom pumps etc."
Government intervention
On the policy level all the major equipment manufacturers feel that the government needs to reduce the burden of taxes imposed on the manufacturers. According to SA Reddy, easing norms for import would be the key step. He goes a step further to explain how China poses a threat to the Indian economy by being technologically advanced. "Till about the year 2000, manufacture of concrete pumps was confined to some European Countries, notably Germany. In the last 12 years China has emerged as a serious competitor in producing and offering concrete pumps of quality. Recently they have ended up by purchasing a well known German Concrete Pump manufacturer. For the construction of the nearly completed 330 m tall Palais Royale Residential Tower, the Chinese Company had supplied a high pressure concrete pump to pump concrete from ground level for the full height in single stage," he explained.
Apart from reducing the burden of taxes Manish Kumar also elaborates on how the manufactures run into losses by undertaking government projects. "The construction industry depends on the government for a couple of things one is the cost of the sort of raw materials like cement, bitumen and the other is the taxation part. When we undertake government projects, quoted prices is unchangeable after the tender is assigned. Nevertheless, the prices of these raw materials keep on increasing and we end up in losses."
TR Badarinarayan, on the other hand believes that the first quarter of the year 2013, will be very crucial and suggests a few steps for the government in order to avoid losing out on global competition. "I am very hopeful for the year 2013 since post slouch; the cycle is expected to move upwards, if it does not we shall be out of the global race. Thus the government needs to have the budget in place and a lot of homework needs to be done. Also we need to see what does the government have to offer in the budget, hence the first quarter is expected to be the most important phase, wherein we will come to know where do we stand."
Apart from the reduction in taxes, Siddharth Shah senses the need of trained labour in the industry." We would to be a part of various training centre wherein we can train people when it comes to operating equipment and would like the government to assist us for the same." Also Shah suggests the need of better quotes offered by the government. He explained, "The existing quotes have been introduced a long time ago and have remained unchanged. Also we would require help from the government when it comes to reduction of taxes since it’s not us the companies who’s making money out of all this but also the Government."
Challenges
The major hurdle for the RMC equipment industry is the lack of standard products. Especially post China entering the Indian market the quality of the equipment has deteriorated. With the market almost flooded with sub standard products, Manish comments on how the customers are drifting away, and in the long run, are running into losses. "Although the customer has a lot of choices and the commercially oriented customer will obviously opt for the equipment of a lower price which has made the market is very competitive. There is no denial of the fact that with increased choices and the existing market scenario the customer will be benefitted. But the products offered are of a lower grade. Thus, minimum standards should be set for the same. I see a lot of other countries entering the Indian market, but the quality is not up to the mark and at the end of the day it’s the customers who bear the brunt, since none of the Chinese equipment manufactures guarantee after sales services nor do they lay emphasis on the quality."
Whilst, Siddharth Shah feels that the if the customer starts understanding the difference between sub standard and standard equipment, no foreign market entering India can pose a threat to the industry. We cannot stop anyone from coming to India, but if the customers are wise enough, we wouldn’t have a problem. Accentuating on the quality, he further goes on to say that if the manufacturers in India offer standard equipment, the consumer will automatically be directed to us, since consistency in quality is always economical in the long run."
Advantages of RMC over site mix concrete
??The RMC plant involves an automated and computerised process to manufacture a quality product by exercising control over every step and on mixing of all ingredients (quality raw materials). In case of site mix concrete (SMC), there is lack of control on mixing of input materials, which may result in a poor quality output.
??SMC operations typically run into 2-3 kg wastage per 50 kg cement due to poor storage of raw materials, which is not the case for RMC.
??SMC is a labour-intensive operation and managing labour is a hectic task. Use of RMC lowers dependency on labour and this also benefits developers through optimisation of costs.
??Production at the RMC plant ensures faster production. While production output from site mixed operation requires 8/12 mixer to produce 4-5 cu m per hour a single RMC plant (60 cu m per hourr) can generate output of around 45 cu m per hour. Thus, RMC offers ten times better yield than SMC, resulting in optimisation of time and costs for clients.
??Usage of RMC is eco-friendly, as the raw materials are mixed at the plant, which reduces air pollution in and around the worksite.
Comparing the international standard for maintaining quality of equipment produced, SA Reddy said that developing countries strictly follow the "Two Hours Rule. In case the available space is restricted, tower batching plants are used, requiring less space. The aggregates and cement storage does not require any space at all at the ground level. The materials supplied continuously and directly loaded into the radial bins of the tower by bucket conveyors. Such tower batching plants can find space within the city or at the project sites in the city. The Quality Assurance Section of the Project does not enforce the two hour rule and succumb to pressure from RMC suppliers. In many cases the RMC Suppliers takes advantage of retarding admixtures to justify long time interval between mixing and placing concrete. In general retarders are not meant for short circuiting the codal requirements."
Explaining the scenario in India, he further said, "The RMC Industry in India is not equipped to design economical concrete mixes compared to the developed world. In general about 30 per cent extra cement is used in the RMC and the cost is passed on to the buyer. It is not only the extra cost. Extra cement in the mix beyond the limits mentioned in IS 456 generates more heat in concrete during the early ages resulting in undesirable effects including cracks."
Like Shah, even Reddy senses an urgent need of trained labour in the industry.
Development of precast and prestressed concrete
With time being a major factor, in the construction industry, precast and prestressed concrete have gained importance. Although the usage of concrete has been boosted due to these technologies, the precast concrete of standard sections produced in factories similar to rolled steel girders is practically non existent in India. In some cases products are precast in casting yards attached to the project. There is no precast pretensioned girder factory in India but common in the developed world contributing to the economy and speed of construction.
Changes required
Although the equipment manufacturing industry has shown signs of improvement and is on track for the same, India needs to adhere to the international standards to come into terms of the international ones. The concrete batching plants and pumps of lower capacity are required with provision of moisture probes in batching plants.
Also there is a need to update Indian Standards for Construction Equipment and fine tune the weighing tolerances. Also curing tanks require temperature control devices and the placer booms needs to be with longer reaches. Medium height construction needs self erecting tower crane of lower capacity and trucks mounted with tower cranes and telehandlers.
Only a few Indian Manufacturers with foreign tie-up offer batching plants fitted with Pan Mixers. It is necessary that from quality point of view, Pan Mixers are used. For quality concrete production, Program Logic Controllers (PLC) are used as standard equipment in the batching plant which enables automated control of quality of concrete once the parameters are set for each grade and mix of concrete. A wide variety of options are available. However in India, the buyers opt for the basic minimum only, restricting production of quality concrete.
PLC’s facilitate printouts for each batch of concrete; these printouts are essential Quality Assurance tools. However, many batching plants in India do not use this facility. Even when used, the printout clubs together six batches and the average of six batches is used for QA purposes. This is not correct. As per the IS code each batch coming out of the batching plant is required to be evaluated for the weighing tolerance.
Truck Mixers in the International markets are available in the range of 2 to 12 cu m capacity, whereas in India only 6 cu m capacity is generally available, thus restricting economic utilisation. For small and medium projects, it is more competitive to use concrete dumpers of one to two tonne capacity, with four wheeled drive for travelling on rough terrain without need for service roads. In India, some manufacturers offer concrete dumpers, but barring exceptions, the quality is not satisfactory and their use is limited. Elsewhere such dumpers are also fitted with agitators to ensure quality concrete at the delivery point; such equipment is not available in India.
Concrete Pumps are manufactured in India only for high end use, starting from about 25 cu m capacity per hour. Most of the medium and small projects require pumps in the range of 10 to 15 cu m per hour capacity. Thus the available pumps are grossly under utilised. Another cost effective alternative to pumping concrete is to useMobile Concrete Placers with belt conveyors such as Morgen placers. Though some Indian Manufacturers offer such equipment the qualityis not satisfactory and they are not popular with users. Gammon India has used 60 cu m per hour capacity for the Libyan Power Station contract about thirty five years ago very profitably. Boom Placers are used to support the pipeline of the concrete pump. Majority of them are truck mounted with limited ranges.
With mushrooming of High Rise Construction in India there is need for self climbing boom placers. These are available in limited cases, mostly imported. Overall if we see, the equipment manufactured by the Indian companies are good, but somewhere down the line, constant check has be kept since the quality of concrete might be getting deteriorated due to the poor practices followed by the contractors.
Leading players in RMC equipment market
Schwing Stetter: Promoted by Gerhard Schwing, the company pioneers in manufacturing transit mixers and concrete batching plant. The company is based in Tamil Nadu.
Sany India: After recently being acquired by Putzmeister, the company jointly manufactures batching plants, boom pumps, transit mixers and all the major concrete equipment.
Putzmeister: Based in Goa, Putzmeister, jointly manufactures batching plants, boom pumps, transit mixers and all the major concrete equipment.
Aquarius Engineers: One of the leading manufacturers of boom and concrete pumps, concrete batching plants, stationary boom placer, slipform pavers, concrete recycling, the company offers wide range of equipment for the domestic as well as international market.
Universal Construction Equipment: Within the three decades of its evolution, Universal has become more than just being one of lndia’s largest engineering companies. The company offers wide rang of concrete solutions including concrete mixer, batching plant concrete pump and boom placer.
Ajax Fiori: Ajax Fiori, located in Bengaluru, manufactures a wide range of equipment for the construction industry, including self loading mobile concrete mixers, batching plants and site dumpers.
Process
Price hikes, drop in input costs help cement industry to post positive margins: Care Ratings
Published
4 years agoon
October 21, 2021By
admin
Region-wise,the southern region comprises 35% of the total cement capacity, followed by thenorthern, eastern, western and central region comprising 20%, 18%, 14% and 13%of the capacity, respectively.
The cement industry is expected to post positive margins on decent price hikes over the months, falling raw material prices and marked drop in overall production costs, said an analysis of Care Ratings.
Wholesale and retail prices of cement have increased 11.9% and 12.4%, respectively, in the current financial year. As whole prices have remained elevated in most of the markets in the months of FY20, against the corresponding period of the previous year.
Similarly, electricity and fuel cost have declined 11.9% during 9M FY20 due to drop in crude oil prices. Logistics costs, the biggest cost for cement industry, has also dropped 7.7% (selling and distribution) as the Railways extended the benefit of exemption from busy season surcharge. Moreover, the cost of raw materials, too, declined 5.1% given the price of limestone had fallen 11.3% in the same aforementioned period, the analysis said.
According to Care Ratings, though the overall sales revenue has increased only 1.3%, against 16% growth in the year-ago period, the overall expenditure has declined 3.2% which has benefited the industry largely given the moderation in sales.
Even though FY20 has been subdued in terms of production and demand, the fall in cost of production has still supported the cement industry by clocking in positive margins, the rating agency said.
Cement demand is closely linked to the overall economic growth, particularly the housing and infrastructure sector. The cement sector will be seeing a sharp growth in volumes mainly due to increasing demand from affordable housing and other government infrastructure projects like roads, metros, airports, irrigation.
The government’s newly introduced National Infrastructure Pipeline (NIP), with its target of becoming a $5-trillion economy by 2025, is a detailed road map focused on economic revival through infrastructure development.
The NIP covers a gamut of sectors; rural and urban infrastructure and entails investments of Rs.102 lakh crore to be undertaken by the central government, state governments and the private sector. Of the total projects of the NIP, 42% are under implementation while 19% are under development, 31% are at the conceptual stage and 8% are yet to be classified.
The sectors that will be of focus will be roads, railways, power (renewable and conventional), irrigation and urban infrastructure. These sectors together account for 79% of the proposed investments in six years to 2025. Given the government’s thrust on infrastructure creation, it is likely to benefit the cement industry going forward.
Similarly, the Pradhan Mantri Awaas Yojana, aimed at providing affordable housing, will be a strong driver to lift cement demand. Prices have started correcting Q4 FY20 onwards due to revival in demand of the commodity, the agency said in its analysis.
Industry’s sales revenue has grown at a CAGR of 7.3% during FY15-19 but has grown only 1.3% in the current financial year. Tepid demand throughout the country in the first half of the year has led to the contraction of sales revenue. Fall in the total expenditure of cement firms had aided in improving the operating profit and net profit margins of the industry (OPM was 15.2 during 9M FY19 and NPM was 3.1 during 9M FY19). Interest coverage ratio, too, has improved on an overall basis (ICR was 3.3 during 9M FY19).
According to Cement Manufacturers Association, India accounts for over 8% of the overall global installed capacity. Region-wise, the southern region comprises 35% of the total cement capacity, followed by the northern, eastern, western and central region comprising 20%, 18%, 14% and 13% of the capacity, respectively.
Installed capacity of domestic cement makers has increased at a CAGR of 4.9% during FY16-20. Manufacturers have been able to maintain a capacity utilisation rate above 65% in the past quinquennium. In the current financial year due to the prolonged rains in many parts of the country, the capacity utilisation rate has fallen from 70% during FY19 to 66% currently (YTD).
Source:moneycontrol.com
Process
Wonder Cement shows journey of cement with new campaign
Published
4 years agoon
October 21, 2021By
admin
The campaign also marks Wonder Cement being the first ever cement brand to enter the world of IGTV…
ETBrandEquity
Cement manufacturing company Wonder Cement, has announced the launch of a digital campaign ‘Har Raah Mein Wonder Hai’. The campaign has been designed specifically to run on platforms such as Instagram, Facebook and YouTube.
#HarRaahMeinWonderHai is a one-minute video, designed and conceptualised by its digital media partner Triature Digital Marketing and Technologies Pvt Ltd. The entire journey of the cement brand from leaving the factory, going through various weather conditions and witnessing the beauty of nature and wonders through the way until it reaches the destination i.e., to the consumer is very intriguing and the brand has tried to showcase the same with the film.
Sanjay Joshi, executive director, Wonder Cement, said, "Cement as a product poses a unique marketing challenge. Most consumers will build their homes once and therefore buy cement once in a lifetime. It is critical for a cement company to connect with their consumers emotionally. As a part of our communication strategy, it is our endeavor to reach out to a large audience of this country through digital. Wonder Cement always a pioneer in digital, with the launch of our IGTV campaign #HarRahMeinWonderHai, is the first brand in the cement category to venture into this space. Through this campaign, we have captured the emotional journey of a cement bag through its own perspective and depicted what it takes to lay the foundation of one’s dreams and turn them into reality."
The story begins with a family performing the bhoomi poojan of their new plot. It is the place where they are investing their life-long earnings; and planning to build a dream house for the family and children. The family believes in the tradition of having a ‘perfect shuruaat’ (perfect beginning) for their future dream house. The video later highlights the process of construction and in sequence it is emphasising the value of ‘Perfect Shuruaat’ through the eyes of a cement bag.
Tarun Singh Chauhan, management advisor and brand consultant, Wonder Cement, said, "Our objective with this campaign was to show that the cement produced at the Wonder Cement plant speaks for itself, its quality, trust and most of all perfection. The only way this was possible was to take the perspective of a cement bag and showing its journey of perfection from beginning till the end."
According to the company, the campaign also marks Wonder Cement being the first ever cement brand to enter the world of IGTV. No other brand in this category has created content specific to the platform.
Process
In spite of company’s optimism, demand weakness in cement is seen in the 4% y-o-y drop in sales volume. (Reuters)
Published
4 years agoon
October 21, 2021By
admin
Cost cuts and better realizations save? the ?day ?for ?UltraTech Cement, Updated: 27 Jan 2020, Vatsala Kamat from Live Mint
Lower cost of energy and logistics helped Ebitda per tonne rise by about 29% in Q3
Premiumization of acquired brands, synergistic?operations hold promise for future profit growth Topics
UltraTech Cement
India’s largest cement producer UltraTech Cement Ltd turned out a bittersweet show in the December quarter. A sharp drop in fuel costs and higher realizations helped drive profit growth. But the inherent demand weakness was evident in the sales volumes drop during the quarter.
Better realizations during the December quarter, in spite of the 4% year-on-year volume decline, minimized the pain. Net stand-alone revenue fell by 2.6% to ?9,981.8 crore.
But as pointed out earlier, lower costs on most fronts helped profitability. The chart alongside shows the sharp drop in energy costs led by lower petcoke prices, lower fuel consumption and higher use of green power. Logistics costs, too, fell due to lower railway freight charges and synergies from the acquired assets. These savings helped offset the increase in raw material costs.
The upshot: Q3 Ebitda (earnings before interest, tax, depreciation and amortization) of about ?990 per tonne was 29% higher from a year ago. The jump in profit on a per tonne basis was more or less along expected lines, given the increase in realizations. "Besides, the reduction in net debt by about ?2,000 crore is a key positive," said Binod Modi, analyst at Reliance Securities Ltd.
Graphic by Santosh Sharma/Mint
What also impressed analysts is the nimble-footed integration of the recently merged cement assets of Nathdwara and Century, which was a concern on the Street.
Kunal Shah, analyst (institutional equities) at Yes Securities (India) Ltd, said: "The company has proved its ability of asset integration. Century’s cement assets were ramped up to 79% capacity utilization in December, even as they operated Nathdwara generating an Ebitda of ?1,500 per tonne."
Looks like the demand weakness mirrored in weak sales during the quarter was masked by the deft integration and synergies derived from these acquired assets. This drove UltraTech’s stock up by 2.6% to ?4,643 after the Q3 results were declared on Friday.
Brand transition from Century to UltraTech, which is 55% complete, is likely to touch 80% by September 2020. A report by Jefferies India Pvt. Ltd highlights that the Ebitda per tonne for premium brands is about ?5-10 higher per bag than the average (A cement bag weighs 50kg). Of course, with competition increasing in the arena, it remains to be seen how brand premiumization in the cement industry will pan out. UltraTech Cement scores well among peers here.
However, there are road bumps ahead for the cement sector and for UltraTech. Falling gross domestic product growth, fiscal slippages and lower budgetary allocation to infrastructure sector are making industry houses jittery on growth. Although UltraTech’s management is confident that cement demand is looking up, sustainability and pricing power remains a worry for the near term.

Hindalco Buys US Speciality Alumina Firm for $125 Million

Star Cement launches ‘Star Smart Building Solutions’

Nuvoco Vistas reports record quarterly EBITDA

UltraTech Cement increases capacity by 1.4Mt/yr

Shree Cement reports 2025 financial year results

Hindalco Buys US Speciality Alumina Firm for $125 Million

Star Cement launches ‘Star Smart Building Solutions’

Nuvoco Vistas reports record quarterly EBITDA

UltraTech Cement increases capacity by 1.4Mt/yr
