Environment
Waste to Energy to Wealth
Published
6 years agoon
By
admin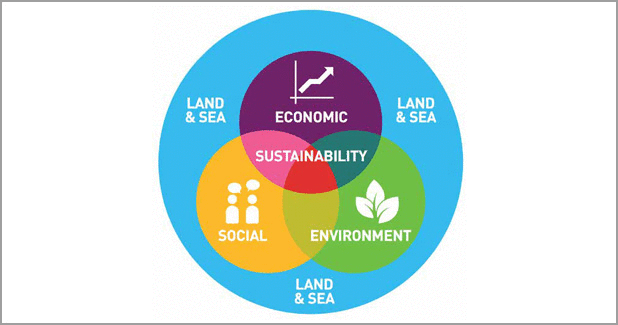
Handling of waste; be it hazardous, industrial or domestic was never so challenging in the earlier years. However cement industry offers an easy solution with minimal cost that needs to be utilised fully.
Rapid urbanisation and industrialisation and increasing household income are leading to higher waste volumes in India. The safe and effective disposal of this increasing level of waste generation is a key concern for authorities at local, State and Government level. One way forward is the promotion of large-scale co-processing in the cement industry, and to create a more conducive regulatory environment.
The increased use of waste as alternative fuel and raw material (AFR) in cement kilns can make a considerable contribution to effective and safe waste disposal efforts. In addition, this will not only help with the Indian cement industry become more competitive on a global stage, but is also in line with Prime Minister Modi’s "Swachh Bharat Abhiyan"(Clean India campaign), which has been launched throughout the country as a national movement. It has become necessary in the present situation of Covid-19 pandemic, we revisit "Swachh Bharat Abhiyan."
While the domestic cement industry has made significant strides in terms of enhancing energy efficiency and optimising productivity, the use of AFR is still a major area that can be developed. Thermal substitution of coal remains low compared to the European average of 40 per cent and varies dramatically from plant to plant. While some leading facilities report substitution rates of between 15 to 20 per cent, most achieve less than three per cent.
Challenges faced by Indian cement industry
The slow pace of revision of waste management rules to keep pace with current advancements in waste management approaches-i.e. co-processing and the absence of a proper waste hierarchy that recognises waste stream suited for co-processing?has been a long-standing barrier for co-processing in the country. Limited waste availability,the level of co-processing depends on the plant location and available surrounding waste market.
At present, obtaining a regular supply of homogeneous waste is asignificant challenge for cement plants as detailed information on quality, quantity and the type of waste generated is not readily available in the public domain. Since data on the quantity and quality of waste is minimal or outdated, cement producers have to spend a considerable amount of time and resources in exploring the availability of different types of AFR, thus weakening the business case for waste utilisation.
Lengthy permit process
The long permit processes further compounds the issue. To initiate co-processing, cement plants must conduct trial runs to obtain clearances from local and pollution control authorities, which is not only a lengthy process but also cost intensive. Although state regulatory bodies are working to simplify procedures, an approach based on the infrastructure, and measuring, reporting and verification (MRV) system in place at co-processing sites would be more appropriate than a trial-based one. Moreover, the inter-state movement of waste (except agricultural waste) comes with its own challenges.
The inter-State movement of hazardous waste in India is not usually encouraged, requires additional permissions and is marred by the lack of certified transporters who can safely move materials from waste generators to cement plants. Permitting the inter-state movement of waste would certainly support the uptake of waste utilisation in the cement industry. However, clearly-defined responsibilities for each stakeholder in terms of collection, packaging, transportation, handling and storage, etc would go some way to helping authorities in their decision-making process. Similarly, the development of operational guidelines with built-in safety features for the aforementioned associated-activities will aid safe and environmentally sound co-processing.
The expert group is also examining various kinds of incentives that can be accorded to both waste generators and waste users that pursue co-processing opportunities. Incentives could be, for instance, financial, government recognition, or faster approval process, etc. The co-processing movement has received further stimulus from the Clean India Mission, as the government is currently working on the revision of various waste management rules.
The initiative recognises co-processing as one of the approaches for waste management, as well as emphasises the importance of segregation of waste at source which will help ensure the homogeneous supply of waste for co-processing. Though India still has a long way to go in terms of forming a comprehensive co-processing system, now is an opportune time for domestic cement industry to focus on how co-processing can help increase its competitiveness on a global stage, and assist with the disposal of the country’s every-increasing volumes of waste.
What is the circular economy?
Taking as an example the cyclical nature pattern, circular economy is presented as a system of resources utilisation where reduction, reuse and recycling of elements prevails: minimise production to a bare minimum, and when it’s necessary to use the product, go for the reuse of the elements that cannot return to the environment.
That is, the circular economy promotes the use of as many biodegradable materials as possible in the manufacture of products -biological nutrients- so they can get back to nature without causing environmental damage at the end of their useful life. When it is not possible to use eco-friendly materials-technical nutrients: electronics, hardware, batteries-the aim is to facilitate a simple uncoupling to give them a new life by reintroducing them into the production cycle and compose a new piece. When this is not possible, it will be recycled in a respectful way with the environment.
Circular economy is a substantial improvement common to both businesses and consumers. Companies that have implemented this system are proving that reusing resources is much more cost effective than creating them from scratch. As a result, production prices are reduced, so that the sale price is also lowered, thereby benefiting the consumer; not only economically, but also in social and environmental aspects.
The main objective of the circular economy is to make economic systems and industrial processes more environmentally friendly and sustainable. Shifting to a circular economy is not a straight forward process and requires substantial changes in the value chain, such as; adapted design, better waste and water management, greater recycling and re-use of products. European Union has done much more work than any other such body.
Based on the data of 2015, turning waste into a resource – only around one-third was recycled and the rest incinerated or landfilled. Estimated additional potential for reuse/recycling is up to 600 MT. If this material is lost then growth, job creation and competitiveness will be compromised and negative environmental impacts generated. The main objective is to recycle more in order to have more "waste" which can be used as a resource. Recycling is a pre-condition for the circular economy.
However, it is important to be aware that there are two problems connected to the topic:
The "legal" base is missing: Currently, there is an action plan which is still under discussion at the EU commission. Final recycling targets are still to be fixed, as well as the methods of calculation to be used. It will take some time until the action plan has been formally finalised by the EU and it will require more time to transfer the amended EU laws into national laws- However, we should remain prepared as these implementations are clearly approaching.
The comparison of data from the different countries has not proved easy so far; with each EU country applying different methods for the counting of waste streams and the calculation of recycling targets, which has rendered the data from different countries more or less incomparable. One target of a circular economy is to harmonise these methods of definition and calculation.
Are we in India prepared for a circular economy?
– VIKAS DAMLE
You may like
Concrete
India donates 225t of cement for Myanmar earthquake relief
Published
3 weeks agoon
June 17, 2025By
admin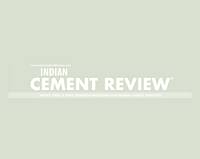
On 23 May 2025, the Indian Navy ship UMS Myitkyina arrived at Thilawa (MITT) port carrying 225 tonnes of cement provided by the Indian government to aid post-earthquake rebuilding efforts in Myanmar. As reported by the Global Light of Myanmar, a formal handover of 4500 50kg cement bags took place that afternoon. The Yangon Region authorities managed the loading of the cement onto trucks for distribution to the earthquake-affected zones.
Concrete
Reclamation of Used Oil for a Greener Future
Published
3 weeks agoon
June 16, 2025By
admin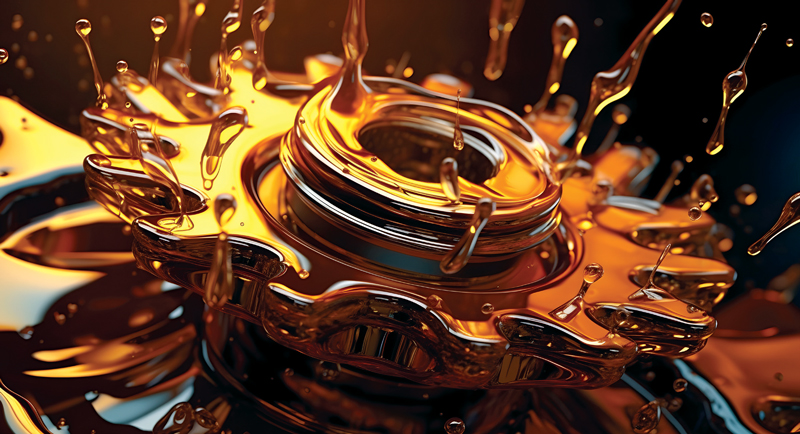
In this insightful article, KB Mathur, Founder and Director, Global Technical Services, explores how reclaiming used lubricants through advanced filtration and on-site testing can drive cost savings, enhance productivity, and support a greener industrial future. Read on to discover how oil regeneration is revolutionising sustainability in cement and core industries.
The core principle of the circular economy is to redefine the life cycle of materials and products. Unlike traditional linear models where waste from industrial production is dumped/discarded into the environment causing immense harm to the environment;the circular model seeks to keep materials literally in continuous circulation. This is achievedthrough processes cycle of reduction, regeneration, validating (testing) and reuse. Product once
validated as fit, this model ensures that products and materials are reintroduced into the production system, minimising waste. The result? Cleaner and greener manufacturing that fosters a more sustainable planet for future generations.
The current landscape of lubricants
Modern lubricants, typically derived from refined hydrocarbons, made from highly refined petroleum base stocks from crude oil. These play a critical role in maintaining the performance of machinery by reducing friction, enabling smooth operation, preventing damage and wear. However, most of these lubricants; derived from finite petroleum resources pose an environmental challenge once used and disposed of. As industries become increasingly conscious of their environmental impact, the paramount importance or focus is shifting towards reducing the carbon footprint and maximising the lifespan of lubricants; not just for environmental reasons but also to optimise operational costs.
During operations, lubricants often lose their efficacy and performance due to contamination and depletion of additives. When these oils reach their rejection limits (as they will now offer poor or bad lubrication) determined through laboratory testing, they are typically discarded contributing to environmental contamination and pollution.
But here lies an opportunity: Used lubricants can be regenerated and recharged, restoring them to their original performance level. This not only mitigates environmental pollution but also supports a circular economy by reducing waste and conserving resources.
Circular economy in lubricants
In the world of industrial machinery, lubricating oils while essential; are often misunderstood in terms of their life cycle. When oils are used in machinery, they don’t simply ‘DIE’. Instead, they become contaminated with moisture (water) and solid contaminants like dust, dirt, and wear debris. These contaminants degrade the oil’s effectiveness but do not render it completely unusable. Used lubricants can be regenerated via advanced filtration processes/systems and recharged with the use of performance enhancing additives hence restoring them. These oils are brought back to ‘As-New’ levels. This new fresher lubricating oil is formulated to carry out its specific job providing heightened lubrication and reliable performance of the assets with a view of improved machine condition. Hence, contributing to not just cost savings but leading to magnified productivity, and diminished environmental stress.
Save oil, save environment
At Global Technical Services (GTS), we specialise in the regeneration of hydraulic oils and gear oils used in plant operations. While we don’t recommend the regeneration of engine oils due to the complexity of contaminants and additives, our process ensures the continued utility of oils in other applications, offering both cost-saving and environmental benefits.
Regeneration process
Our regeneration plant employs state-of-the-art advanced contamination removal systems including fine and depth filters designed to remove dirt, wear particles, sludge, varnish, and water. Once contaminants are removed, the oil undergoes comprehensive testing to assess its physico-chemical properties and contamination levels. The test results indicate the status of the regenerated oil as compared to the fresh oil.
Depending upon the status the oil is further supplemented with high performance additives to bring it back to the desired specifications, under the guidance of an experienced lubrication technologist.
Contamination Removal ? Testing ? Additive Addition
(to be determined after testing in oil test laboratory)
The steps involved in this process are as follows:
1. Contamination removal: Using advanced filtration techniques to remove contaminants.
2. Testing: Assessing the oil’s properties to determine if it meets the required performance standards.
3. Additive addition: Based on testing results, performance-enhancing additives are added to restore the oil’s original characteristics.
On-site oil testing laboratories
The used oil from the machine passes through 5th generation fine filtration to be reclaimed as ‘New Oil’ and fit to use as per stringent industry standards.
To effectively implement circular economy principles in oil reclamation from used oil, establishing an on-site oil testing laboratory is crucial at any large plants or sites. Scientific testing methods ensure that regenerated oil meets the specifications required for optimal machine performance, making it suitable for reuse as ‘New Oil’ (within specified tolerances). Hence, it can be reused safely by reintroducing it in the machines.
The key parameters to be tested for regenerated hydraulic, gear and transmission oils (except Engine oils) include both physical and chemical characteristics of the lubricant:
- Kinematic Viscosity
- Flash Point
- Total Acid Number
- Moisture / Water Content
- Oil Cleanliness
- Elemental Analysis (Particulates, Additives and Contaminants)
- Insoluble
The presence of an on-site laboratory is essential for making quick decisions; ensuring that test reports are available within 36 to 48 hours and this prevents potential mechanical issues/ failures from arising due to poor lubrication. This symbiotic and cyclic process helps not only reduce waste and conserve oil, but also contributes in achieving cost savings and playing a big role in green economy.
Conclusion
The future of industrial operations depends on sustainability, and reclaiming used lubricating oils plays a critical role in this transformation. Through 5th Generation Filtration processes, lubricants can be regenerated and restored to their original levels, contributing to both environmental preservation and economic efficiency.
What would happen if we didn’t recycle our lubricants? Let’s review the quadruple impacts as mentioned below:
1. Oil Conservation and Environmental Impact: Used lubricating oils after usage are normally burnt or sold to a vendor which can be misused leading to pollution. Regenerating oils rather than discarding prevents unnecessary waste and reduces the environmental footprint of the industry. It helps save invaluable resources, aligning with the principles of sustainability and the circular economy. All lubricating oils (except engine oils) can be regenerated and brought to the level of ‘As New Oils’.
2. Cost Reduction Impact: By extending the life of lubricants, industries can significantly cut down on operating costs associated with frequent oil changes, leading to considerable savings over time. Lubricating oils are expensive and saving of lubricants by the process of regeneration will overall be a game changer and highly economical to the core industries.
3. Timely Decisions Impact: Having an oil testing laboratory at site is of prime importance for getting test reports within 36 to 48 hours enabling quick decisions in critical matters that may
lead to complete shutdown of the invaluable asset/equipment.
4. Green Economy Impact: Oil Regeneration is a fundamental part of the green economy. Supporting industries in their efforts to reduce waste, conserve resources, and minimise pollution is ‘The Need of Our Times’.
About the author:
KB Mathur, Founder & Director, Global Technical Services, is a seasoned mechanical engineer with 56 years of experience in India’s oil industry and industrial reliability. He pioneered ‘Total Lubrication Management’ and has been serving the mining and cement sectors since 1999.
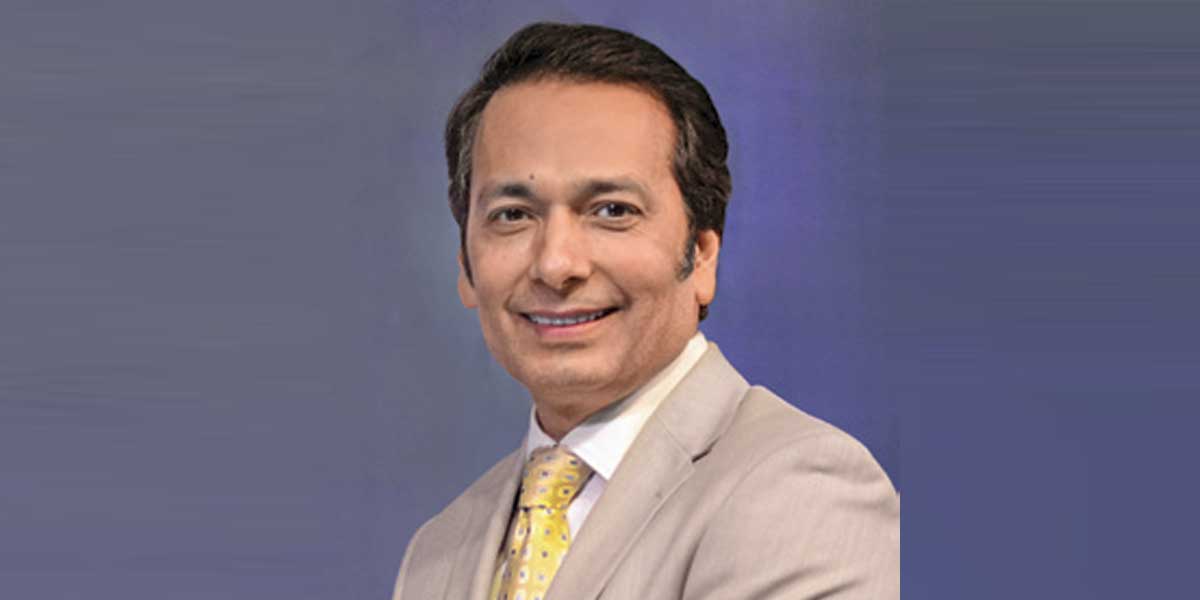
The Indian cement industry has reached a critical juncture in its sustainability journey. In a landmark move, the Ministry of Environment, Forest and Climate Change has, for the first time, announced greenhouse gas (GHG) emission intensity reduction targets for 282 entities, including 186 cement plants, under the Carbon Credit Trading Scheme, 2023. These targets, to be enforced starting FY2025-26, are aligned with India’s overarching ambition of achieving net zero emissions by 2070.
Cement manufacturing is intrinsically carbon-intensive, contributing to around 7 per cent of global GHG emissions, or approximately 3.8 billion tonnes annually. In India, the sector is responsible for 6 per cent of total emissions, underscoring its critical role in national climate mitigation strategies. This regulatory push, though long overdue, marks a significant shift towards accountability and structured decarbonisation.
However, the path to a greener cement sector is fraught with challenges—economic viability, regulatory ambiguity, and technical limitations continue to hinder the widespread adoption of sustainable alternatives. A major gap lies in the lack of a clear, India-specific definition for ‘green cement’, which is essential to establish standards and drive industry-wide transformation.
Despite these hurdles, the industry holds immense potential to emerge as a climate champion. Studies estimate that through targeted decarbonisation strategies—ranging from clinker substitution and alternative fuels to carbon capture and innovative product development—the sector could reduce emissions by 400 to 500 million metric tonnes by 2030.
Collaborations between key stakeholders and industry-wide awareness initiatives (such as Earth Day) are already fostering momentum. The responsibility now lies with producers, regulators and technology providers to fast-track innovation and investment.
The time to act is now. A sustainable cement industry is not only possible—it is imperative.

Hindalco Buys US Speciality Alumina Firm for $125 Million

Star Cement launches ‘Star Smart Building Solutions’

Nuvoco Vistas reports record quarterly EBITDA

UltraTech Cement increases capacity by 1.4Mt/yr

Shree Cement reports 2025 financial year results

Hindalco Buys US Speciality Alumina Firm for $125 Million

Star Cement launches ‘Star Smart Building Solutions’

Nuvoco Vistas reports record quarterly EBITDA

UltraTech Cement increases capacity by 1.4Mt/yr
