Environment
April price hikes indicative of improved profitability | Analysts
Published
8 years agoon
By
admin
According to a few analysts and industry watchers, the hikes in the prices of cement by various cement manufacturers are an indication of a possible growth in volumes and probable profitable for cement makers during the current quarter. A recent report released by analyst firm Edelweiss says that cement prices have picked up u on an average – during the month of April.
‘Average all-India prices rose 6.7 per cent month-on-month led by (the) western and southern markets where price jumped in double digits, followed by the eastern market (up 6 per cent month-on-month) and other regions,’ the report said. The report claims that cement off-take was ‘robust’ in the eastern region of India, ‘stable’ in the north and ‘marginally weak’ in Uttar Pradesh.
PhillipCapital India said in a 27th April report that despite assuming flat volume growth for the sector, Q1 earnings are likely to surprise positively, driven by prices hikes. ‘Given a favourable demand scenario, we understand cement prices have been raised across pockets by about 10 per cent and further price hikes of 3-5 per cent cannot be ruled out in May 2017. After the monsoon arrives, cement prices are unlikely to be increased until the end of H1FY18,’ the report said.
Vijayawada builders to import cement to combat cartelisation
Alleging that cement companies were engaging in cartelisation, builders’ associations in Vijayawada have decided to import cement from Sri Lanka, China, Bangladesh, Malaysia and Korea.
According to estimates from these builders, the import of cement from the countries indicated above would reduce the price per bag by around Rs 30, which will eventually benefit consumers as construction prices will come down.
The Vijayawada chapters of the Confederation of Real Estate Developers’ Associations of India (CREDAI), Andhra Pradesh Real Estate Developers Association (APREDA) and Capital Region Builders Association (CRBA) have formed a joint action committee (JAC) to oppose the alleged cement cartel.
Concrete admixtures chemical market may touch $16,324 million
According to a new report published by Allied Market Research, Concrete Admixtures Construction Chemical Market: Global Opportunity Analysis and Industry Forecast, 2015-2023, the global concrete admixtures construction chemical market is projected to reach $16,324 million by 2022. This translates into a CAGR of 5.7 per cent from 2017 to 2023 (the market was valued at $11,027 million in 2016).
Concrete admixtures construction chemical are ingredients other than water, aggregates and cement, which are used to modify the properties such as, heat of hydration, accelerate or retard setting time, workability, water reduction, dispersion and air-entrainment, impermeability, and durability factors. Concrete admixtures are available as mineral and chemical admixtures.
The rapid growth of the construction industry due to change in lifestyle patterns in emerging countries such as China, India, Brazil, Middle East, and Africa, owing to the rapid economic development and increase in disposable income has fueled the growth of concrete admixtures market. Moreover, fast adoption of latest manufacturing standards globally is expected to increase the penetration level of concrete admixtures.
Andhra Pradesh asks cement companies to drop prices
A Group of Ministers (GoM), constituted by the Andhra Pradesh government to look into the issue of rising cement prices has held talks with representatives of various cement companies. The government has directed cement companies to slash prices ‘immediately’, but these firms have said that they would ‘revert on the issue’ in two days.
According to the cement companies, they would face an approximate tax incidence of around Rs 40 per bag after the new Goods and Services Tax (GST) comes into force. But the GoM does not want the cement companies to hike prices before the new tax regime is rolled out.
The Andhra Pradesh government is now arguing that it already gives the state’s cement companies ‘many concessions and benefits’, so the GoM has maintained that the cement firms cannot hike prices unilaterally, placing a burden on the common man.
Orient Cement is member of Cement Sustainability Initiative
Orient Cement Limited will become part of the Cement Sustainability Initiative (CSI), a CEO-led business initiative. The entity operates under the umbrella of the World Business Council for Sustainable Development (WBCSD), an effort by global cement majors towards sustainable development.
Orient Cement expects membership of this initiative to give further impetus to its efforts to create a safe and ecologically favourable environment, and is in line with its vision to be the employer of choice and the neighbour of choice in the geographies where it operates.
After the announcement, Deepak Khetrapal, Managing Director and Chief Executive Officer, Orient Cement said, ‘We are delighted to be a part of the global mission to make our industry shoulder the responsibility for global sustainability. We thank the WBCSD and the CSI for partnering with us in our journey. We expect to contribute to and benefit from our participation in the various working groups of this initiative, and look forward to a very engaging and fulfilling journey ahead. We accept this membership with a deep sense of responsibility and intend to play our role to the utmost extent in this noble mission.’
Sanghipuram joins progressive ‘Less Cash’ township league
Taking forward the vision of Prime Minister Narendra Modi, Sanghipuram, home to Sanghi Industries‘ employees and their families based in Kutch, Gujarat, has moved towards a ‘less cash’ township model with almost 90 per cent of monetary transactions being carried out digitally. In order to promote digital payment systems, shops and existing business entities at the town are equipped with Point of Sale (PoS) machines, major online wallet options and interface apps like Unified Payments Interface (UPI) and Bharat Interface for Money (BHIM).
The efforts have clearly made a mark, as Sanghipuram was launched as one of the ‘less-cash’ townships of India by Prime Minister Modi at Nagpur a few days back. With a population of around 2,500 people, Sanghipuram is a self-reliant town with businesses, shops, hospitals, schools and other infrastructure facilities required for an integrated township.
Aditya Sanghi, Director of Sanghi Industries, said, ‘Our company believes in following the best practices initiated by the Government of India. Not only have we implemented this less cash initiative in our township, we have further extended it to our dealer network in Gujarat as well as other states where Sanghi Cement is sold. About 90 per cent of monetary transactions in Sanghipuram have now turned cashless and digital.’ As a result of these efforts, the number of daily cashless transactions has increased to 140 as compared to 75 prior to the start of the cashless transaction campaign.
Sanghi Industries Limited is a major cement player in western India. The company’s 4 million tonnes per annum capacity plant in Abdasa taluka of Kutch in Gujarat is ranked as one of the largest cement plants at a single location in India. It is one of the top three players in Gujarat, and is now extending its presence to Maharashtra and Rajasthan.
CREDAI protests cement price hike, seeks Centre’s intervention
The Confederation of Real Estate Developers’ Association of India (CREDAI) has sought government intervention to check rising cement prices. The entity said that the spike could ‘create unnecessary roadblocks and impediments’ in achieving the goal of ‘Housing for All’ by 2022. Cement prices have witnessed a sudden jump of 20-40 per cent over the past two months across the country, says CREDAI.
‘We are pained by complaints of unjustifiable and collusive jacking up of cement prices by manufacturers across India, which have the potential to create unnecessary roadblocks and impediments in ensuring ?Housing for All’ by 2022, said CREDAI Vice-President Sushil Mohta. He said the Competition Commission of India, on earlier occasions, had pulled up cement manufacturers for ‘collusive pricing’ and had imposed hefty fines on them.
Seaborne cementitious trade increases globally; Asia-Pacific absorbs over 50% of total trade
According to the latest update of the World Cement, Clinker & Slag Sea-Based Trade Report from CW Research, more than 174 million tonnes (MT) of cementitious materials were traded by sea-going vessels in 2016. The trade volumes grew 1.3 per cent compared to the 171.9 MT of cementitious materials traded by sea in 2015.
CW Research’s latest research shows that seaborne cementitious trade has benefited from low shipping rates. Moreover, the increase in imports in some key markets where cement production has leveled out (such as the US), has also motivated higher seaborne cementitious trade volumes in 2016, compared to 2015
Raluca Cercel, CW Research’s Lead Analyst for the report, stresses that, in the seaborne global trade context, ‘About 2 to 3 per cent of total cement consumption is traded internationally, and two-thirds of the total trade is performed by sea-going vessels’.
In the worldwide seaborne cementitious trade, gray cement continues to be the most traded cementitious commodity by sea. In 2016, more than half of the sea-based cementitious trade, comprising gray cement, white cement, slag, clinker, and fly ash, was made up of gray cement. Clinker (including both white and gray) accounted for 33 per cent of total seaborne cementitious trade in 2016, followed by ground blast furnace slag, with a 12 per cent share of the trade.
Far less traded, white cement and fly ash made for 3 per cent and for less than 2 per cent, respectively, of total seaborne trade of cementitious materials.
According to CW Research, on the main trade routes and regions, the Asia Pacific region absorbs 51 per cent of the total seaborne trade of cementitious materials. Due to proximity and pricing considerations, the largest volumes of cementitious materials were traded within this region, with almost 90 MT shipped in 2016.
Global companies LafargeHolcim, HC Trading and Cemex together control about 30 per cent of the cement trading market. The two largest Asian cement traders (Taiheyo and Tong Yang Cement) together control around 10 per cent of the market.
Worldwide, there are more than 900 cement terminals, more than 100 waterside grinding plants (slag and clinker) and almost 140 waterside integrated cement plants. Most of the cement terminals are located in Far East Asia, followed by the Med Basin and the Black Sea. In terms of waterside integrated plants (used as export facilities), the Far East has a total of 51 plants, while 46 integrated waterside plants are located in the Med Basin and Black Sea region.
The presence of these facilities in the Asia Pacific region favors the trade of cementitious materials, therefore explaining the large volumes that were shipped in the area.
Utilisation of cement carriers has currently reached almost 100 per cent u and is a forecasted to grow in the coming years (mostly concentrated in Far East Asia, India, Northern and the Baltic Sea). In terms of the specialised cement carrier market, there are currently more than 300 cement carriers used for seaborne distribution of cementitious materials. An additional 200 cement carriers under the 1,000 dwt allow for environmental friendly, speedy and weather independent cement distribution.
Driven in particular by production shortages and supply chain optimization efforts, CW forecasts that the total traded volume of cementitious materials will exceed 200 MT, increasing at a CAGR of more than 3 per cent between 2016 and 2021.
Cement trading ensures that surplus and shortages of cementitious materials are ironed out across markets. More than that, maintaining utilisation rates weighs heavily in the future of traded cement volumes. These are only two of the factors that balance the scale in favour of increased sea-trade volumes in the next five years.
Hindering factors are potential fuel-related restrictions on the shipping industry, as well as new capacity additions in traditional import markets, will counterbalance positive drivers,: emphasises Raluca Cercel, CW Research’s Lead Analyst for the report. In conclusion, seaborne cementitious trade volumes increased globally between 2015 and 2016. That was largely due to consumption in the Asia Pacific region, which absorbed more than half of the total seaborne trade of cementitious materials. Even though fuel usage regulations in maritime shipping and local autonomy in cement production may condition the promising numbers, the outlook for seaborne cementitious trade volumes remains optimistic.
Cement firm reportedly drills Rs.350-cr hole in IndusInd, Yes Bank profits Exposure to a single cement company has made a Rs 350-crore dent in the net profits of IndusInd Bank and Yes Bank, private lenders otherwise known to have better control on asset quality.
IndusInd Bank and Yes Bank had to make provisions of Rs 122 crore and Rs 227.9 crore, respectively, towards their exposure to this account in compliance with a Reserve Bank notification. Both the banks stressed the reverses are ‘temporary’ in nature, underlining that the cement company in question is all set to be acquired by a better performing city-based company soon and once the deal fructifies, there will be a write back.
Even though the bank managements did not name the company, sources said this relates to the exposure to Jaypee Cements, which is all set to be acquired by UltraTech in a Rs 16,200-crore deal.
To ensure greater transparency and promote better discipline, the RBI has said that it will be flagging divergences in asset recognition to the bank, ask them to make extra provisions or re-classification of the account and instructed lenders to disclose the same in quarterly statements, starting with that for FY2016-17.
Cement demand likely to pick up: Sharekhan
Analyst firm Sharekhan believes that, barring the southern cement players (due to drought-like conditions in key southern states), cement demand is likely to improve on account of diminishing effects of demonetisation and an uptick in government spending on infrastructure development and housing projects. However, the key monitorables going ahead would be the guidance for the upcoming southwest monsoon season (which currently is below normal), and the sustainability of price hikes taken by cement companies during April 2017 (pan-India players have taken Rs 20 per bag month-on-month (m-o-m) hike, while Andhra Pradesh and Telangana cement companies are looking for Rs 50-60 per bag hike (m-o-m).
The firm says that cement stocks have largely factored in better earnings growth for FY2018 due to the impending improvement in the demand outlook and a sustained pricing discipline. However, the drought-like conditions prevailing in south India and a weak southwest monsoon can play spoilsport in FY2018. Consequently, Sharekhan remains selective at present and has a ?Hold’ recommendation on cement stocks under its active coverage.
Bone cement mixer devices’ market to grow during 2017-2021
Technavio market research analysts have forecast that the global bone cement mixer devices market will grow at a CAGR of more than 4 per cent during the forecast period. The market study covers the present scenario and growth prospects of the global bone cement mixer devices market for 2017-2021. The report also lists bench-top bone cement mixer devices, and portable and hand-held bone cement mixer devices, of which the portable and hand-held devices accounted for more than 65 per cent of the market share in 2016.
Technavio healthcare and life sciences analysts highlight the following three market drivers that are contributing to the growth of the bone cement mixer devices:
- Growing prevalence of orthopaedic disorders
- Increased use of bone cement in interventional procedures
- High demand for automated bone cement mixers
- Asia-Pacific to continue driving global cement industry growth
- According to a latest report, the global cement & concrete additive market has seen positive growth over the past few years and as per analysis, the global market will experience a remarkable growth during the forecast period.
Globally, the cement & concrete additive market has completely driven the rising demand for residential and non-residential properties. As per the data, the construction business is likely to increase in the near future, which in turn will escalate the demand for cement & concrete additives. Geographically, Asia-Pacific is expected to be the largest market owing to the rising construction and infrastructure investments in China, India, Indonesia and other countries as well.
The report, ‘Global Cement & Concrete Additive Market’ comprises extensive primary research along with detailed analysis of qualitative as well as quantitative aspects by various industry experts, and key opinion leaders, to gain deeper insight into the market and industry performance. The report gives a clear picture of the current market scenario which includes historical and projected market size in terms of value and volume, technological advancements, macro-economical and governing factors in the market. The report provides detailed information and strategies of the key players in the industry. The report also gives a broad study of the different market segments and regions.
Note-ban, polls impact cement companies’ Q4 bottom-line, says India Ratings Cement production would have shrunk in the March quarter primarily due to the base effect coupled with the note-ban-induced cash crunch and polls in many states during the period, says a report. ‘The lagged impact of cash crunch and state polls will take a toll on cement production in Q4. Latest data showed cement volumes in February 2017 declined the most in over a decade by 15.8 per cent y-o-y. Volumes also declined by 5 per cent on (a) month-on-month basis,’ says an India Ratings report. The report notes the decline in cement production growth is also on account of a high base last year, as in the March 2016, quarter production grew by 9.2, 13.5 and 11.9 per cent respectively.
On the prices front, the wholesale price index of grey cement and slag cement has shown a softening trend through November 2016-January 2017. Cement players got some respite on the cost front, with pet coke and coal prices showing moderation in January and February 2017, after pet coke prices almost doubled since March 2016, the report said.
Volumes of national players in Q3 contracted by 5 per cent y-o-y; while for central and north-based players fell by 3 per cent and 6 per cent respectively. The southern region, in contrast, showed strong volume growth of 21 per cent. Growth in the southern region is led by an increase in government expenditure in Andhra Pradesh and Telangana.
On the policy front, due to the recent measures announced by the Railways Ministry that require long term agreements/contracts for industries like cement, steel and fertilisers, cement companies may see improvement in demand.
As per the policy, the Ministry will provide a minimum guaranteed volume linked discount, on the basis of incremental growth in gross freight revenue, in return for a commitment to provide a minimum guaranteed quantity of traffic. The discounts will range from 1.5 to 35 per cent, as per the incremental growth in gross freight revenue.
You may like
-
In spite of company’s optimism, demand weakness in cement is seen in the 4% y-o-y drop in sales volume. (Reuters)
-
Earnings of cement firms may recover from September
-
Siam Cement to lift capacity by 4.5 mta
-
igus’ roller links
-
Coal India’s e-auction prices for coal rise
-
Tata Steel launches GGBS in Bhubaneswar
Concrete
India donates 225t of cement for Myanmar earthquake relief
Published
2 months agoon
June 17, 2025By
admin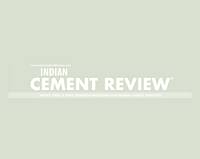
On 23 May 2025, the Indian Navy ship UMS Myitkyina arrived at Thilawa (MITT) port carrying 225 tonnes of cement provided by the Indian government to aid post-earthquake rebuilding efforts in Myanmar. As reported by the Global Light of Myanmar, a formal handover of 4500 50kg cement bags took place that afternoon. The Yangon Region authorities managed the loading of the cement onto trucks for distribution to the earthquake-affected zones.
Concrete
Reclamation of Used Oil for a Greener Future
Published
2 months agoon
June 16, 2025By
admin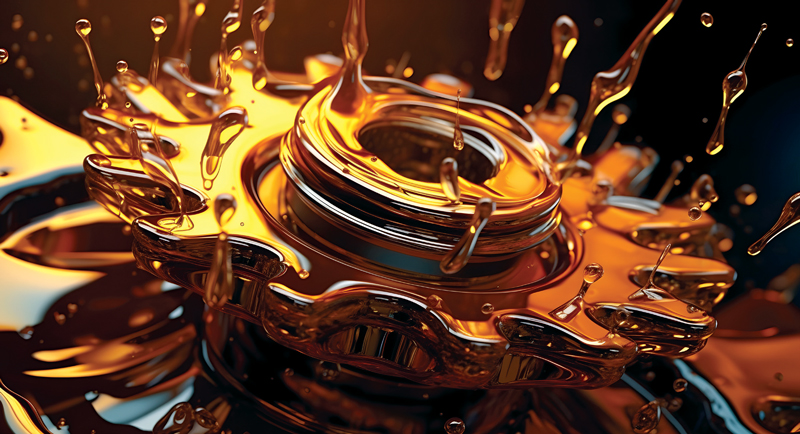
In this insightful article, KB Mathur, Founder and Director, Global Technical Services, explores how reclaiming used lubricants through advanced filtration and on-site testing can drive cost savings, enhance productivity, and support a greener industrial future. Read on to discover how oil regeneration is revolutionising sustainability in cement and core industries.
The core principle of the circular economy is to redefine the life cycle of materials and products. Unlike traditional linear models where waste from industrial production is dumped/discarded into the environment causing immense harm to the environment;the circular model seeks to keep materials literally in continuous circulation. This is achievedthrough processes cycle of reduction, regeneration, validating (testing) and reuse. Product once
validated as fit, this model ensures that products and materials are reintroduced into the production system, minimising waste. The result? Cleaner and greener manufacturing that fosters a more sustainable planet for future generations.
The current landscape of lubricants
Modern lubricants, typically derived from refined hydrocarbons, made from highly refined petroleum base stocks from crude oil. These play a critical role in maintaining the performance of machinery by reducing friction, enabling smooth operation, preventing damage and wear. However, most of these lubricants; derived from finite petroleum resources pose an environmental challenge once used and disposed of. As industries become increasingly conscious of their environmental impact, the paramount importance or focus is shifting towards reducing the carbon footprint and maximising the lifespan of lubricants; not just for environmental reasons but also to optimise operational costs.
During operations, lubricants often lose their efficacy and performance due to contamination and depletion of additives. When these oils reach their rejection limits (as they will now offer poor or bad lubrication) determined through laboratory testing, they are typically discarded contributing to environmental contamination and pollution.
But here lies an opportunity: Used lubricants can be regenerated and recharged, restoring them to their original performance level. This not only mitigates environmental pollution but also supports a circular economy by reducing waste and conserving resources.
Circular economy in lubricants
In the world of industrial machinery, lubricating oils while essential; are often misunderstood in terms of their life cycle. When oils are used in machinery, they don’t simply ‘DIE’. Instead, they become contaminated with moisture (water) and solid contaminants like dust, dirt, and wear debris. These contaminants degrade the oil’s effectiveness but do not render it completely unusable. Used lubricants can be regenerated via advanced filtration processes/systems and recharged with the use of performance enhancing additives hence restoring them. These oils are brought back to ‘As-New’ levels. This new fresher lubricating oil is formulated to carry out its specific job providing heightened lubrication and reliable performance of the assets with a view of improved machine condition. Hence, contributing to not just cost savings but leading to magnified productivity, and diminished environmental stress.
Save oil, save environment
At Global Technical Services (GTS), we specialise in the regeneration of hydraulic oils and gear oils used in plant operations. While we don’t recommend the regeneration of engine oils due to the complexity of contaminants and additives, our process ensures the continued utility of oils in other applications, offering both cost-saving and environmental benefits.
Regeneration process
Our regeneration plant employs state-of-the-art advanced contamination removal systems including fine and depth filters designed to remove dirt, wear particles, sludge, varnish, and water. Once contaminants are removed, the oil undergoes comprehensive testing to assess its physico-chemical properties and contamination levels. The test results indicate the status of the regenerated oil as compared to the fresh oil.
Depending upon the status the oil is further supplemented with high performance additives to bring it back to the desired specifications, under the guidance of an experienced lubrication technologist.
Contamination Removal ? Testing ? Additive Addition
(to be determined after testing in oil test laboratory)
The steps involved in this process are as follows:
1. Contamination removal: Using advanced filtration techniques to remove contaminants.
2. Testing: Assessing the oil’s properties to determine if it meets the required performance standards.
3. Additive addition: Based on testing results, performance-enhancing additives are added to restore the oil’s original characteristics.
On-site oil testing laboratories
The used oil from the machine passes through 5th generation fine filtration to be reclaimed as ‘New Oil’ and fit to use as per stringent industry standards.
To effectively implement circular economy principles in oil reclamation from used oil, establishing an on-site oil testing laboratory is crucial at any large plants or sites. Scientific testing methods ensure that regenerated oil meets the specifications required for optimal machine performance, making it suitable for reuse as ‘New Oil’ (within specified tolerances). Hence, it can be reused safely by reintroducing it in the machines.
The key parameters to be tested for regenerated hydraulic, gear and transmission oils (except Engine oils) include both physical and chemical characteristics of the lubricant:
- Kinematic Viscosity
- Flash Point
- Total Acid Number
- Moisture / Water Content
- Oil Cleanliness
- Elemental Analysis (Particulates, Additives and Contaminants)
- Insoluble
The presence of an on-site laboratory is essential for making quick decisions; ensuring that test reports are available within 36 to 48 hours and this prevents potential mechanical issues/ failures from arising due to poor lubrication. This symbiotic and cyclic process helps not only reduce waste and conserve oil, but also contributes in achieving cost savings and playing a big role in green economy.
Conclusion
The future of industrial operations depends on sustainability, and reclaiming used lubricating oils plays a critical role in this transformation. Through 5th Generation Filtration processes, lubricants can be regenerated and restored to their original levels, contributing to both environmental preservation and economic efficiency.
What would happen if we didn’t recycle our lubricants? Let’s review the quadruple impacts as mentioned below:
1. Oil Conservation and Environmental Impact: Used lubricating oils after usage are normally burnt or sold to a vendor which can be misused leading to pollution. Regenerating oils rather than discarding prevents unnecessary waste and reduces the environmental footprint of the industry. It helps save invaluable resources, aligning with the principles of sustainability and the circular economy. All lubricating oils (except engine oils) can be regenerated and brought to the level of ‘As New Oils’.
2. Cost Reduction Impact: By extending the life of lubricants, industries can significantly cut down on operating costs associated with frequent oil changes, leading to considerable savings over time. Lubricating oils are expensive and saving of lubricants by the process of regeneration will overall be a game changer and highly economical to the core industries.
3. Timely Decisions Impact: Having an oil testing laboratory at site is of prime importance for getting test reports within 36 to 48 hours enabling quick decisions in critical matters that may
lead to complete shutdown of the invaluable asset/equipment.
4. Green Economy Impact: Oil Regeneration is a fundamental part of the green economy. Supporting industries in their efforts to reduce waste, conserve resources, and minimise pollution is ‘The Need of Our Times’.
About the author:
KB Mathur, Founder & Director, Global Technical Services, is a seasoned mechanical engineer with 56 years of experience in India’s oil industry and industrial reliability. He pioneered ‘Total Lubrication Management’ and has been serving the mining and cement sectors since 1999.
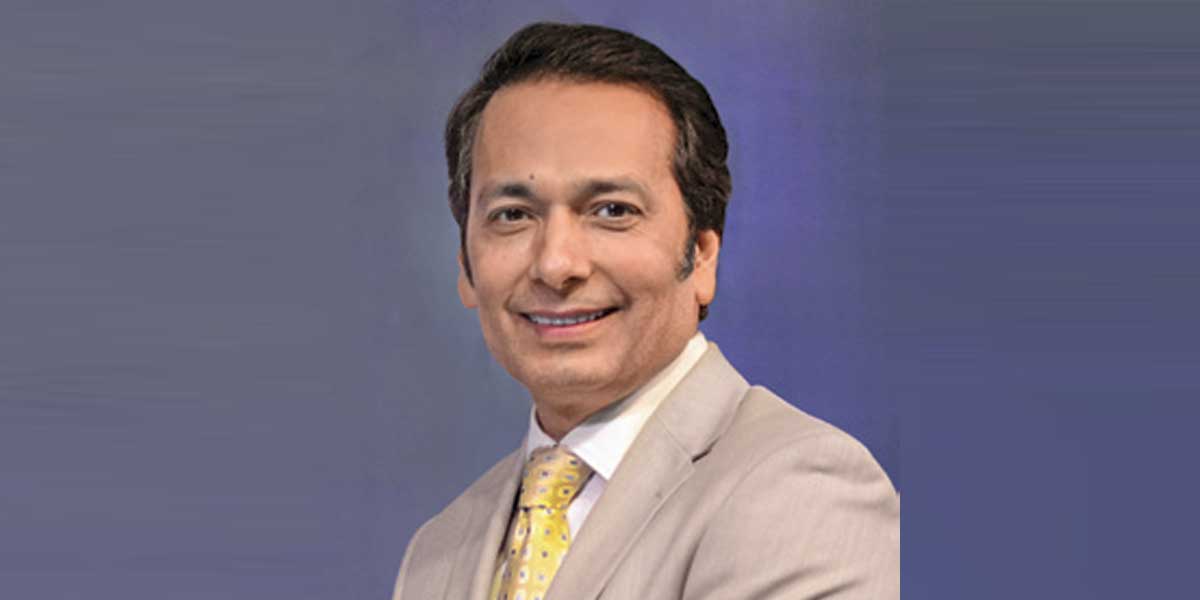
The Indian cement industry has reached a critical juncture in its sustainability journey. In a landmark move, the Ministry of Environment, Forest and Climate Change has, for the first time, announced greenhouse gas (GHG) emission intensity reduction targets for 282 entities, including 186 cement plants, under the Carbon Credit Trading Scheme, 2023. These targets, to be enforced starting FY2025-26, are aligned with India’s overarching ambition of achieving net zero emissions by 2070.
Cement manufacturing is intrinsically carbon-intensive, contributing to around 7 per cent of global GHG emissions, or approximately 3.8 billion tonnes annually. In India, the sector is responsible for 6 per cent of total emissions, underscoring its critical role in national climate mitigation strategies. This regulatory push, though long overdue, marks a significant shift towards accountability and structured decarbonisation.
However, the path to a greener cement sector is fraught with challenges—economic viability, regulatory ambiguity, and technical limitations continue to hinder the widespread adoption of sustainable alternatives. A major gap lies in the lack of a clear, India-specific definition for ‘green cement’, which is essential to establish standards and drive industry-wide transformation.
Despite these hurdles, the industry holds immense potential to emerge as a climate champion. Studies estimate that through targeted decarbonisation strategies—ranging from clinker substitution and alternative fuels to carbon capture and innovative product development—the sector could reduce emissions by 400 to 500 million metric tonnes by 2030.
Collaborations between key stakeholders and industry-wide awareness initiatives (such as Earth Day) are already fostering momentum. The responsibility now lies with producers, regulators and technology providers to fast-track innovation and investment.
The time to act is now. A sustainable cement industry is not only possible—it is imperative.